丰田之生产模式(TPS)-目视化管理 ss
TPS(ToyotaProductionSystem)丰田模式的14项原则

TPS(ToyotaProductionSystem)丰田模式的14项原则原则1:管理决策以长期理念为基础,即使因此牺牲短期财务目标也在所不惜。
1)企业的目标应该有长期目标,永续经营比短期财务目标更加重要。
不能看到短期利润率而忽视长期盈利能力和生存能力,必须牺牲短期利益而追求长远利益,这样企业才能生存长久;2)管理决策的关注点(focus)应该是顾客(包含外部和内部顾客)与社会。
企业必须使顾客满意才能生存,必须符合社会和相关方的期望,要满足法律法规要求,要不断提高社会责任形象;评估公司每个部门为顾客和社会创造价值的能力;4)要有责任感。
努力决定自己的命运,依靠自己,相信自己的能力。
对自己的行为以及保持并提高创造价值的技能等负起责任。
原则2:建立连续的作业流程以使问题浮现。
1)重新设计工作流程,使其变成创造高附加价值的连续流程(one flow一个流)。
尽力把所有计划中闲置或等候他人的工作时间减少到零(七大浪费)。
2)建立快速输送材料与信息的流程,使流程与人员紧密地联结在一起,以便立即浮现问题(SMED快速换模)。
3)使整个企业文化重视流程,这是促成真正的持续改善及员工发展的关键(改善Kaizen)。
原则3:使用拉动式生产方式以避免生产过剩(pull system)。
1)在生产流程下游的顾客需求的时候,供应给他们正确数量的正确产品。
材料的补充应该由消耗量决定,这是准时生产的基本原则(just-in-time)。
2)使在制品及仓库存货减少至最少,每项产品只维持少量存货,根据顾客实际领取的数量,经济地补充存货。
按顾客每天的需求来变化,而不是事后来分析和追踪浪费的存货。
原则4:生产均衡化(balance)。
使工作负荷平均,像龟兔赛跑中的乌龟一样均衡。
1)杜绝浪费只是实现精益所必须做的1/3,避免员工与设备的工作负荷过重,这与避免生产安排的不均匀同等重要(7种浪费)。
2)尽量使所有制造与服务流程的工作负荷平均化(生产节拍Takt Time),以取代大多数公司实行的批量生产方法中经常启动、停止的做法。
TPS丰田生产方式
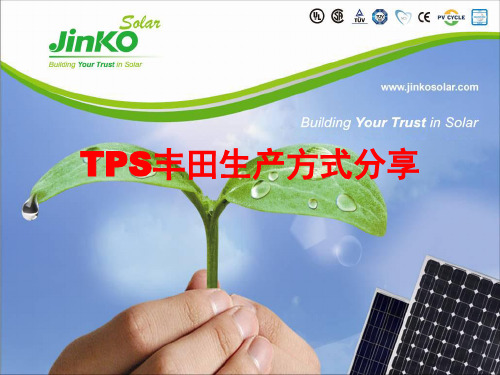
17:建立接力区 游泳当中的接力,快的人、慢的人都要负责同 样的距离。田径接力的话, 快的人可以在接 力区照顾慢的人。在生产线作业当中也希望是 田径接力的方式。为了提高生产线的效率,基 层管理人员建立接力区是很重要的事情。
3
3:我去丰田这次给各位带回了什么?
A world’s Leading Vertically-integrated PV Manufacturer
4
有很多公司都套用丰田联生产模式,的确它有独特的管理方 式,在每个环节中变通使用也是受益非浅.想知道各位的看法.
A world’s Leading Vertically-integrated PV Manufacturer 18
15:「流动作业」与「传送作业」 「流动作业」指产品在流动当中,各工序对其 加工被附加了价值。如果只是使用传送带传送 产品的话,这就不是「流动作业」,而是「传 送作业」。 作为丰田生产方式的基本条件,我们提出要使 生产现场「流动化」,当然这是指建立「流动 作业」。
A world’s Leading Vertically-integrated PV Manufacturer 6
2:Just-In-Time 如果能够在所需要的时候,按所需数量,获取 所需要的东西,那么就可以消除生产现场的浪 费;不均;不合理,提高生产效率。该思想的开 山鼻祖是丰田汽车的创始人-丰田喜一郎,其 后继者将此思想展开,概括成为了一个生产体 系。不单是in time, 而是just in time, 这是一个重要的关键。 「Just-In-Time」 和下面的「自働化」共同形成丰田生产方式的 两大支柱。
解读丰田生产模式(TPS)

解读丰田生产模式(TPS)作者:佚名文章来源:ISOYES收集点击数:4668 更新时间:2006-9-17 19:13:34通过此次赴日对丰田叉车日本总部的参观考察,笔者对这一在全世界广受瞩目的生产模式有了更进一步的了解与认识,在此愿提出来与大家共享。
丰田生产模式(ToyotaProductionSystem TPS)对国内读者来说并不陌生,它产生于日本丰田公司,是“为实现企业对员工、社会和产品负责的目的,以彻底杜绝浪费的思想为目标,在连续改善的基础上,采用准时化与自动化方式与方法,追求制造产品合理性的一种生产方式”。
通过此次赴日对丰田叉车日本总部的参观考察,笔者对这一在全世界广受瞩目的生产模式有了更进一步的了解与认识,在此愿提出来与大家共享。
一、丰田生产模式(TPS)源自丰田的基本理念要解读丰田生产模式(TPS),首先得对丰田的基本理念有一个了解。
丰田的基本理念是:“为客户提供更好的产品”。
在这里,“更好的产品”包含了两层意思,一是要“提供给客户高品质的产品”;二是要以“满意的价格”为客户提供产品。
为了确保实现以上两点,丰田公司在生产中便采取了一系列措施,从而形成了现今我们所熟知的丰田生产模式(TPS)。
其采取的措施主要包括以下两点;一是采用不使次品流入到下一个流程的系统,各个流程均保证产品质量,从而保证得到高品质的产品。
二是通过不断改善(排除不必要的程序),以降低产品成本,确保产品拥有一个顾客满意的价格。
这两点可以说便是丰田生产模式(TPS)的精髓之所在。
二、全面质量管理,确保丰田产品的高品质如何做到不使次品流入到下一个流程,从而确保丰田产品的品质?丰田公司采用了全面质量管理(TQM),它强调质量是生产出来的而非检验出来的,由生产中的质量管理来保证产品的最终品质。
在每道工序进行时均注意质量的检测与控制,保证及时发现质量问题,培养每位员工的质量意识。
如果发现问题,立即停止生产,直到解决,从而保证不出现对不合格产品的失效加工和有问题产品流入下一个流程。
丰田式生产模式TPS名词讲解
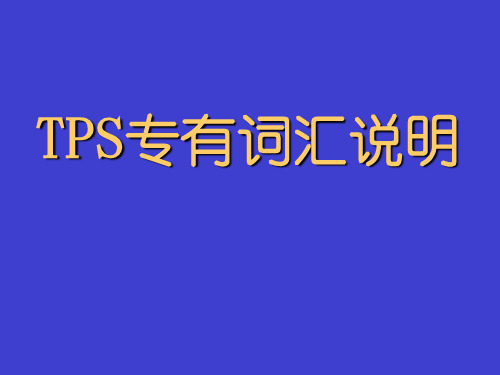
1).丰田式的制造方法:
生产现场作成物的流动
过去
1人1机
车床 车床 车床
分
铣床 铣 床 铣 床
别
集
钻床 钻床 钻床
中
现在 车 床 铣 床 钻 床 提高生
产力
依制造过程一个流为原则的方式
2). 实行『刚好及时』生产
(1)依据上述方法,以看板为手段。
(2)看板扮演了物品之『领取情报』或 『运搬指示情报』,或作为生产工程内 之作业指示情报。
1971本社/元町工厂 冲床换模时间(3分)
1950目视管理的 灯号方式(在引 擎装配线采用)
1955本社工厂装配 线生产方式(灯号、 停止钮、混载搬运)
1962机械采用总 量限制 机械防呆装置
1961元町工厂装 配场设置灯号
1966上乡 工厂完成 自动线
1.丰田生产方式
(TOYOTA Production System)
a)生产线正常运转:绿色 b)设备异常:红色
6.看板(Kanban)
1)『看板』就是为了实现丰田生产方式第一支 柱刚好及时的管理道具
2) 多半用小纸片放入四角型的塑料袋中 3) 纸片上显示着:
a)要领取什么?多少?
b)『制造什么产品?怎样去制造?』
4)看板的类型: a)领取看板或搬运看板:后工程到前工程去 领取,其间作为『领取情报』或『搬运指 示情报』来联系的。 b)工程内看板:为使前工程只制造被取用数 量而指示生产的。
2)标准作业的三大要素: (1)表示必须以几分几秒制造一台或一个的 『节拍时间』
(2)随着时之经过而进行作业的『作业顺序』
(3)为能顺利进行作业,工程内所须的最少 制品,亦即『标准在制品』量。
详细讲解丰田精益生产管理模式

引取看板信箱
②
FED
① 组装生产线
ABC ④
工程间看板
③
信箱
⑤
A
B
ABC加工生产线
原 料
C 完成品
D
E
DEF加工生产线
原 料
F
领回かんばん
部品箱
工程内かんばん㌃
TTMC
④搬运到组装生产线的部品箱,要带着看板一同放在组装部品的放 置场所(绝对不许搬运没有看板的部品)
引取看板信箱
②
FED
① 组装生产线
目的:外注部品的引取
TTMC
(かんばん例)
所番地
703 0-1
K-2-1-7
トヨタ自動車株式会社
アイシン高岡
90153-11020
S5 収容数
326
6-4.看板的流程和规则
TTMC
①在拿取部品的第一个部品或达到规定的部品量时取下看板
引取看板信箱 ②
FED
① 组装生产线
ABC ④
工程间看板
③
信箱
⑤
A
70
70
70
70 平准化流程
60
60
60
60
秒
50
50
50
50
C AB C AB C AB C AB
3-3 节拍时间
TTMC
一日的负荷时间 节拍时间=
1日的生产必要数(个or台)
将1个部品或1台的量在多长的时间内进行生产的时间值 (负荷时间:定时(没有加班) 可动率:按100%计算)
例题
※ 1日的生产必要台数为200台,负荷时间为8小时 (460分钟),此时的节拍时间是多少?
4. 自働化
丰田式生产模式
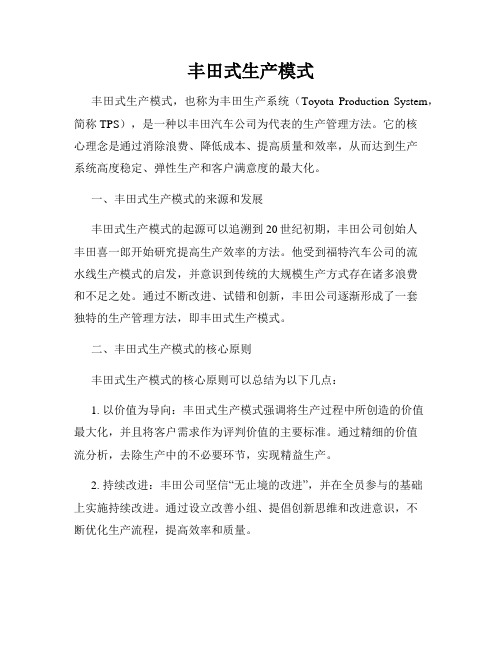
丰田式生产模式丰田式生产模式,也称为丰田生产系统(Toyota Production System,简称TPS),是一种以丰田汽车公司为代表的生产管理方法。
它的核心理念是通过消除浪费、降低成本、提高质量和效率,从而达到生产系统高度稳定、弹性生产和客户满意度的最大化。
一、丰田式生产模式的来源和发展丰田式生产模式的起源可以追溯到20世纪初期,丰田公司创始人丰田喜一郎开始研究提高生产效率的方法。
他受到福特汽车公司的流水线生产模式的启发,并意识到传统的大规模生产方式存在诸多浪费和不足之处。
通过不断改进、试错和创新,丰田公司逐渐形成了一套独特的生产管理方法,即丰田式生产模式。
二、丰田式生产模式的核心原则丰田式生产模式的核心原则可以总结为以下几点:1. 以价值为导向:丰田式生产模式强调将生产过程中所创造的价值最大化,并且将客户需求作为评判价值的主要标准。
通过精细的价值流分析,去除生产中的不必要环节,实现精益生产。
2. 持续改进:丰田公司坚信“无止境的改进”,并在全员参与的基础上实施持续改进。
通过设立改善小组、提倡创新思维和改进意识,不断优化生产流程,提高效率和质量。
3. 流程标准化:丰田式生产模式注重流程标准化和作业标准化。
通过制定明确的工作标准和工作方法,确保每一个员工都能按照标准操作,消除误差和浪费。
4. 在根本上解决问题:丰田公司倡导解决问题的根本原因,而不仅仅解决表面问题。
通过推行“5W1H”(即:What、Why、When、Where、Who、How)的问题分析方法,找出问题产生的根源,并采取相应的措施予以解决。
5. 灵活性和弹性生产:丰田式生产模式注重生产系统的灵活性和弹性。
为了响应市场需求的变化,丰田公司采用“拉动生产”模式,即按需生产,避免库存浪费和滞销。
三、丰田式生产模式的实践和效果丰田式生产模式在实践中取得了显著的效果和成就。
丰田公司通过改变传统的大规模批量生产方式,转向小规模、多品种的柔性生产模式,成功地提高了生产效率、降低了生产成本、缩短了交货周期。
丰田式生产管理(TPS)
丰田式生产管理(TPS)丰田式生产管理又称丰田生产体系(ToyotaProduction System,TPS)由日本丰田汽车公司的副社长大野耐一创建,是丰田公司的一种独具特色的现代化生产方式。
它顺应时代的发展和市场的变化,经历了20多年的探索和完善,逐渐形成和发展成为今天这样的包括经营理念、生产组织、物流控制、质量管理、成本控制、库存管理、现场管理和现场改善等在内的较为完整的生产管理技术与方法体系。
丰田生产方式又称精细生产方式或精益生产方式。
一、丰田生产方式的起源和理念TPS的灵感来自美国,而不是来自丰田自己的汽车生产过程。
丰田的代表团到美国访问,研究美国的企业。
他们首先参观了福特汽车公司位于美国密歇根州的汽车厂。
尽管当时福特汽车是行业的领导者,丰田代表团发现福特使用的很多生产方法,并不是很有效率。
令代表团最为震惊的是大量的库存,和在大部日子,工厂各部门的工作量并不平均。
不过,他们在访问Piggly Wiggly超级市场时,看到Piggly Wiggly只会在顾客购买货品之后,才重新进货,代表团从而得到启示。
1.1 正确的流程方能产生正确结果●建立无间断的作业流程以使问题浮现●使用「后拉式制度」以避免过度生产●平准化:工作负荷平均(工作要像龟兔赛跑中的乌龟,而不是兔子那样)●建立立即暂停以解决问题、一开始就重视品管的文化●职务工作的标准化是持续改善与授权员工的基础●使用视觉控管,使问题无从隐藏●使用可靠的、已经经过充分测试的技术以支持人员及流程1.2发展员工与事业伙伴,以为组织创造价值●栽培彻底了解并拥抱公司理念的员工成为领导者,并使他们能教导其他人●栽培与发展信奉公司理念的杰出人才与团队●重视公司的事业伙伴与供货商网络,挑战它们,并帮助它们改善1.3 持续解决根本问题是组织型学习的驱动力●现地现物:亲临现场查看以彻底了解情况●决策不急躁,要通过协商以共识为基础,彻底考虑所有可能选择,快速执行决策●透过不断地省思与持续改善,以变成一个学习型组织二、丰田式生产管理:不降低成本就无法提高利润成本中心型以计算或实际的成本为中心,加上预先设定好的利润而得出售价,其公式为:售价 = 成本+利润在供应< 销量时,在垄断产品时可以如此定价售价中心型在供应>销量时,以售价为中心,当市场售价降低时利润随之减少,其公式为:利润 = 售价-成本缺乏改善意识的企业属于此类型,市场好时有较高的利润,市场差时大幅度下降利润中心型在供应>销量时,以利润为中心,当市场售价降低时,成本也必须下降以获得的利润 (目标利润 ) 不会减少,其公式为:成本 = 售价-利润减少浪费--降低成本的主要手段什么是浪费?不增加价值的活动(如:生产过程改变零件尺寸、形状或功能,非价格) 是浪费;尽管是增加价值的活动,但所用资源超过了绝对最少的界限,也是浪费丰田式生产管理目的就是取消那些不增加产品价值的工作,即降低成本。
丰田精益生产模式介绍(TPS)
丰田精益生产模式介绍(TPS)丰田精益生产方式(TPS-Toyota Production System)是由日本丰田汽车公司的副社长大野耐一创建的,是丰田公司的一种独具特色的现代化生产方式。
它顺应了时代的发展和市场的变化,其间经历了20多年的探索和完善,逐渐形成和发展成为一套完整的生产管理技术与方法体系。
丰田生产方式使得丰田汽车在全世界获得成功。
通和认为:从更高的意义上说,丰田生产方式代表了一种崇尚创新的企业文化和企业精神,丰田生产方式是一场意识革命。
那么,中国企业就很有必要需要了解其TPS这种具有东方文化背景的管理模式的特点、核心、内涵等特征。
下面我们就主要从TPS精益生产模式和中国企业在推行TPS方面存在的显著问题、解决途径以及企业精益化之路等方面进行重点阐述,相信一定会对我国企业的现代化管理具有极强的参考和借鉴作用。
一、TPS由来的简单回顾20世纪后半期,世界汽车工业进入一个市场需求多样化的新阶段,而对质量的要求也越来越高,这就给制造业提出了这样一个新课题:只有有效地组织多品种、小批量生产,避免生产过剩所引起的设备、人员、库存、资金等一系列资源浪费,以保持企业竞争能力。
在这种历史背景下,从丰田相佐诘开始,经丰田喜一郎及大野耐一等人的共同努力,综合了单件生产和批量生产的特点和优点,创造了一种多品种、小批量混合生产条件下高质量、低消耗的生产方式,这就是精益生产,其核心是追求消灭包括库存在内的一切“浪费”。
二、TPS生产管理哲学的理论框架丰田式生产管理哲学的理论框架包含“一个目标”、“两大支柱”和“一大基础”。
“一个目标”是低成本、高效率、高质量地进行生产,最大限度地使顾客满意;“两大支柱”是准时化(JIT)与人员自觉化; “一大基础”是指改善,改善是丰田式生产管理的基础。
这里的改善是指这样的含义:(1)从局部到整体永远存在着改进与提高的余地。
(2)消除一切浪费。
(3)连续改善(Continuous Improvement)。
丰田生产方式及其十大根本特征
丰田生产方式及其十大根本特征丰田生产方式(Toyota Production System,简称TPS)是丰田汽车公司所采用的一种管理生产方式。
TPS是丰田成功的关键之一,也是丰田汽车公司在汽车行业中取得重大竞争优势的基础。
以下是TPS的十大根本特征:1.按需生产:TPS通过精确的计划和预测市场需求,在最短的时间内生产出产品,并减少库存水平。
丰田不会生产超出市场需求的产品,以避免库存积压和浪费。
2.人性化管理:TPS注重员工的工作满意度和自主权,鼓励员工提出问题,并参与到问题解决的过程中。
丰田鼓励员工进行持续的改进,为员工提供培训和发展机会。
3.零缺陷:TPS追求零缺陷的目标,通过减少浪费和优化生产流程,确保产品质量的一致性和稳定性。
丰田强调每个员工都是质量控制的检查员。
4.超市式管理:TPS引进了“超市式”管理概念,即以产品的实际需求为基础,将物料和零件存放在相应的位置,并保持适当的库存水平。
这种方式可以提高生产效率和减少浪费。
5.紧凑型生产布局:TPS采用紧凑型生产布局,将生产设备和工作站安排在紧密相连的区域内。
这有助于减少运输时间和距离,提高生产效率。
6.持续改进:TPS鼓励员工参与到持续改进的过程中,通过提出问题和解决问题来改善生产流程和工作环境。
丰田鼓励员工进行小规模的试验和改进,以寻求更好的解决方案。
7.小批量生产:TPS倡导小批量生产,以减少库存和生产周期。
丰田通过精确的计划和协调供应链,实现了小批量生产的目标,提高了生产效率和灵活性。
8.快速响应:TPS要求整个生产过程实现快速响应,使得丰田能够及时地回应市场需求的变化。
通过减少交通和等待时间,优化生产流程,丰田能够在最短的时间内生产出产品。
9.节约资源:TPS重视节约资源的原则,通过减少浪费和优化生产流程,实现资源的最大化利用。
丰田鼓励员工提出节约资源的建议,并将其纳入到生产过程中。
10.长期稳定:TPS注重长期稳定和持续发展。
丰田生产系统管理工具
丰田生产系统管理工具丰田生产系统(Toyota Production System,简称TPS)是丰田汽车公司开发并成功实施的生产管理方法,其核心理念是以精益为导向,追求持续改进和高效率的生产方式。
在TPS中,有许多管理工具被广泛使用,以帮助企业实现精益生产。
一、五问法(5 Whys)是TPS中最常用的管理工具之一。
它的基本原理是通过连续反问为什么,将问题一层层分解,找到根本原因。
通过深入分析问题背后的本质原因,可以避免单纯解决表面问题的方法,从而实现持续改进。
二、流程图(Process Flow Diagram)是TPS中用于描述生产流程的图形工具。
它通过可视化生产过程中的各个环节、工序和资料流动,帮助员工更好地理解整个流程,并找到改进的机会。
流程图也可以帮助员工迅速发现操作中的瓶颈和浪费,从而提高效率。
三、标准作业(Standardized Work)是在TPS中广泛应用的管理工具之一。
通过清晰地规定生产过程中的每个步骤、时间和要求,能够确保每个员工按照同样的标准工作,从而提高稳定性和质量。
标准作业也为员工提供了一个参考框架,帮助他们更好地理解工作要求,并减少错误的发生。
四、Kanban(看板)是TPS中用于控制生产流程的一种视觉化管理工具。
通过设置看板,可以实时了解生产线上的物料和工序的状态,并及时调整生产进度。
看板还可以帮助员工识别缺货和过量生产的问题,从而避免浪费和效率低下。
五、持续改善(Continuous Improvement)是TPS的核心理念之一,也是一种管理工具。
通过设立改善的目标、制定改善计划、实施改善措施和评估改善效果,可以不断推动生产过程的优化和创新。
持续改善还鼓励员工积极参与改进活动,发挥他们的创造力和提高意识,为企业创造更大的价值。
综上所述,丰田生产系统的管理工具是为了帮助企业实现精益生产,持续改进和高效率的生产方式。
通过运用这些工具,企业可以深入分析问题、优化流程、控制生产,并不断提高质量和效率,从而实现更高水平的竞争力和持续发展。
- 1、下载文档前请自行甄别文档内容的完整性,平台不提供额外的编辑、内容补充、找答案等附加服务。
- 2、"仅部分预览"的文档,不可在线预览部分如存在完整性等问题,可反馈申请退款(可完整预览的文档不适用该条件!)。
- 3、如文档侵犯您的权益,请联系客服反馈,我们会尽快为您处理(人工客服工作时间:9:00-18:30)。
5S推动职责
收集资料 文宣活动 改善推动
物
第4个S --时时保持美观、干净 清洁
第5个S
--使员工养成好习惯遵守规则
人
素养
18
5S的效益(特性要因图)
厂房
设备
新设备 有位置
扩大效用
有多余 空间
厂房较亮丽
走道畅通
地板 干净
提高 稼动率
降低故
障率
5S
的
异常立判
减少质量 不良
节省寻找时间
降低报废
心情 愉快
减少公伤 、公害
物品 降低仓库呆料
其它
归纳目视化系统的特性(三)
控制指标 → 完成计划指标中的过程控制型指标 各个控制机制可以采用防呆方法 各工序过程中也可以采用 侦错反馈来提醒或停机 颜色管理 让相关人员能有效辨识异常点 进而改善
(一)整理的认识1
整理(SEIRI)
定义:区分要与不要的东西,职场除了要用的东西
以外,一切都不放置;
丰田之生产模式(TPS)-目视 化管理
复习一下 JIT 的功能与特性
集结性的生产方式 后拉式生产方式 快速换模生产方式 以上种种 充分容易让生产过程中曝露出现场问题 因为有曝露才容易发现现场失控的水龙头
凸显现场问题的另一模式
目视化之现场管理系统
原意: 是将现场的种种管理 可以采用眼睛在最快速 的方式下 实时反映问题缺点
21
活动计划的建立
制订长期计划与公司整体计划(各部门); 制定小集团的活动计划(以部门别展开制定); 对计划的达成状况要跟催与确认; 务必尽量按计划时程实施,特别发表;
(1)竞赛办法 (2)区域划分 (3)评审小组成立 (4)定点公怖 (5)成绩公怖 (6)奖惩
22
全面展开
A1:采取对策 A2:修下计划
归纳目视化系统的特性(一)
最通俗 最常挂在嘴边 也是常做不到的事项 利用5S来显露现场的失控点 后段再详述
归纳目视化系统的特性(二)
计划指标 → 完成使命的最终指标值
改善的机制与过程 可以采用 (因) 与 (果) 来归纳
利用信息目标值的达成率来反映问题点状况 (当未达 到指标性的状况 便是代表有失控有问题 便可以利用 这些问题点来启动改善机制)
1、建立清扫责任区(室内、外) 2、开始一次全公司的大清扫
3、每个地方清洗干净
4、调查污染源,予以杜绝或隔离
12
清扫就是使职场成为没有垃圾,没 有脏污的状态,要的东西马上就能 取得,且能被正常的使用。这样状 态就是清扫的第一目的.
13
(四)清洁的认识1
清洁(SETKETSU)
定义:将上面3S实施的做法制度化,规范化,维持
目的:将“空间”腾出来活用,降低作业成本 .
1、 对工作场所(范围)全面简查,包括看得到和看不 到的; 2、制定[要]和[不要]的判别基准(见下页)
3、要的物品调查使用频度,决定日常用量
8
“要”与“不要”评定基准
9
因为不整理而发生的浪费…..
1、空间的浪费 2、使用棚架或柜橱的浪费 3、零件或产品变旧而不能使用的浪费 4、放置处变得窄小 5、连不要的东西也要管理的浪费 6、库存管理或盘点花时间的浪费
真的人 .
企业文化
1、表层文化:制定服装、臂章、工作帽等识别标准; 2、中层文化----制度层:制定公司规章制度; 3、深层文化:推行礼貌运动和推动各种激励活动等。
17
5S关连图
第1个S --区分“要用”与“不要用”的东西 整理
第2个S -将要用的东西 整 顿 定出位置放
第3个S --将不要用的 地 清 扫 东西清扫干净 、
工作气 氛好
效
感到较有制度
益
较认同 公司
人员 外宾参观有面子
19
二、5S推动体制与步骤
☆ 活动文件的建立 ☆ 活动计划的建立 ☆ 全面展开 ☆ 升华
20
活动文件的建立
没有规矩,不成方圆! 没有“法律”,谈何“法治”与“法制”! 成员其职责;(涵盖所有直接与间接单位) 活动方式与周期;(最好要附表) 评比的具体方式与周期; 奖惩的时施细节;
A
P1:分析5S现 状及问题点
P2:决定5S改善方案与目标
P3:提出5S实施计划(含订
定必要的5S作业标准等)
P
C
C.:定期召开检讨, 检查5S实施之过程与 结果是否与计划或与 目标吻合?
C2:分析异常原因
D
D1:成立推行体制 D2:展开文宣活动及教
育训练
D3:实施
23
升华
少
人
化
多 工 程 操 作
变 换 准 备
自
働 化
2
现
5
3
1
场
意 识 改 革
改 善 的 基 础
流 动 生 产
4
平 准 化
标 准 作 业
……..5S
广 告 牌
质 量 保 証
·
保 全 安 全
目视
管理
步骤1:意识改革
JIT 旧意识
抛弃
抛弃陈旧的意识,改用 JIT的想法.
步骤2: 5S 基础
步骤3:整流化生产
JIT改善的基础是整理、整顿停、止大批制造,让每 清扫、清洁、素养等5S. 一项工程都遵循着顺
其成果 ; 目的:通过制度化来维持成果,激励工作士气 .
相关标准
14
储位
入侧位 置表示 先进先 出,同 一部品 不要横 放,务 必纵向 放置, 由前方 取用
架号位置,取 出侧表示
15
储位案例
16
(五)素养的认识1
素养(SHITSUKE)
定义:培养文明礼貌习惯,按规定行事,养成良好
的工作习惯 ; 目的:提升“人的质量”,成为对任何工作都讲究认
10
(二)整顿的认识1
整顿(SEITON)
定义:要的东西依规定定位、定方法摆放整齐,明确
数量,明确标示 ; 目的:不浪费“时间”找东西,提高工作效率 .
新人也能 识别
11
(三)清扫的认识1
清扫(SEISO)
定义:清除职场内的脏污,并防止污染的发生 ;
目的:消除“脏污”,保持职场干净、明亮,提高工 作品质 .
25
三、5S推动要领
☆ 5S与日常管理结合 ☆ 5S推动干部职责 ☆ 5S推动员工职责 ☆ 简查要点
26
5S与日常管理结合
在质量解析与改善的体系中,实施问 题,改善对策一段时间后,要进行效果 确认,而确认对策有效,则要将改善对 策定着化,纳入作业标准,同时导入日 常管理架构中,作为例行管理活动。 5S 活动也一样
序来制造。
步骤4:平准化不可有落单式 Nhomakorabea产, 无论何时所生产的都 是均等的数量。
步骤5:标准作业
② ③
① ④
⑤
好不容易所完成的物 品流程,不可弄乱, 要牢计于心。
JIT
及 时 生 产
J IT
在必要的时候只生 产和搬运必要的量
24
执行要点
1、即使在远处,亦 可一看就知。 2、大家都能执行, 且使用方便执行。