126拉深件常见缺陷
拉深加工的质量缺陷分析及对策

? " / / A
图1 压边 圈不平所 产生的制件缺 陷
圈
一处
图3 凸模中心线与凹模平面不垂直时所产生的制件缺陷
对策 :检查 凸 凹模轴 心 线 是 否 由于长 期振 动 而 不 重 合 ,压 边 圈螺 钉是 否 长短 不 一 ,凹模 几 何形 状
2 . 拉深件 表面 出现起皱 、裂纹或破裂现象
圆筒 件 边 缘 褶 皱 ( 见 图4 ) 。原 因分 析 :凹 模 圆角半 径 太大 ,在拉 深 过程 的 末 阶段 ,脱离 了压边 圈 ,但 尚未超 过 凹模 圆角 材料 ,压边 圈压不 到 ,起
皱 后被 继 续拉 入 凹模 ,形 成边 缘 褶皱 。对 策 :减 小
半 径 ,使 之 保持 均 匀 。 ( 3 )制 件 侧 壁 高 低 不 一 ,薄 厚 不 一 。原 因分 析 :模具 定 位部 分 产 生偏 差 或板 料 定 位板 的 中心 与
凹模 中 心不 重 合 。对 策 :检 查 凸凹模 中心 线 是 否共
凹模 圆角半 径 或采 用 弧形 压边 固。
部位 即凹模的圆角部位 。 原 因分析 :在 拉深 中 ,凹模 圆角部位压 力很
图5 工件壁部拉 毛
大 ,因而 滑 动面 的摩 擦 阻 力很 大 ,会产 生 可能 达 到
( 2 )检查 凸凹模是否 存在间隙不均匀 ,或研
配不 好 、导 向不 良等 问 题造 成 局 部 压料 力增 高 ,使 侧 面 产 生局 部 接 触 划 痕 或变 薄 性 质 的擦 伤 。对 策 : 调 整 凸 凹模 间 隙使 其 均 匀 ,保 证 凸凹模 工作 部 位 的 研 配 质量 ,保证 凸 凹模 工 作表 面 低 的表 面 粗 糙 度 值 和 尺 寸 的一 致 性 。
不锈钢薄板拉深时出现的问题及对策

不锈钢薄板拉深时出现的问题及对策不锈钢薄板拉深是通用冲压成形工艺中最常用的一种薄板冲压成形方式。
不锈钢薄板拉深工艺具有板料利用率高、深度比较大、拉深成型比较方便等优点。
然而,不锈钢薄板拉深过程中也出现一些问题,这些问题的出现不仅会影响产品的外观和功能性能,而且也影响到生产的效率。
针对不锈钢薄板拉深过程中出现的问题,有必要对其进行深入的研究,并采取恰当的对策,以达到质量的要求。
一、不锈钢薄板拉深时出现的问题1、形变问题。
不锈钢薄板在拉深过程中,板料容易发生形变,尤其是拉深深度达到几十毫米以上时,形变比较严重。
如果板料不正确,可能会造成节点变形,导致拉深效果不理想。
2、剪切纹问题。
不锈钢薄板拉深过程中,剪切纹也是一个经常出现的问题。
如果剪切纹过大,拉深效果不佳,严重的会影响金属的加工性能,并影响最终成型的质量。
3、拉深模具问题。
不锈钢薄板拉深过程中,拉深模具的加工精度和寿命对拉深质量至关重要。
如果拉深模具加工精度较低,拉深时会出现不良痕迹,影响拉深效果,同时会长期损害拉深模具,把模具的寿命大幅度缩短。
4、焊接问题。
焊接是不锈钢薄板拉深工艺中一个重要环节,也是容易出现问题的环节,如果焊接不当会使焊接处的精度受到影响,同时还会影响到不锈钢薄板的外观和功能。
二、不锈钢薄板拉深时的对策1、选用合适的板料。
焊接前,应根据拉深工艺要求选用合适的不锈钢薄板,将其硬度、拉伸度和刚度调整到最佳状态,以确保板料在拉深过程中能够获得最佳形变效果。
2、调整拉深模具的加工精度。
拉深模具的加工精度是不锈钢薄板拉深质量的重要保证,应使用非标准精密加工技术,加工出复杂抛光表面,以提高薄板拉深工艺质量。
3、精确控制焊接参数。
对于不锈钢薄板拉深工艺中的焊接工序,应根据不锈钢薄板的材质和厚度,精确控制焊接参数,以确保焊接精度,并尽可能降低焊接缺陷出现的几率。
4、采用有效的检测手段。
除了提高拉深过程中的加工精度外,还可以采用有效的检测手段,对不锈钢薄板进行拉深全过程的检查,以确保拉深质量。
Cr12MoV钢拉深模失效分析及工艺改进
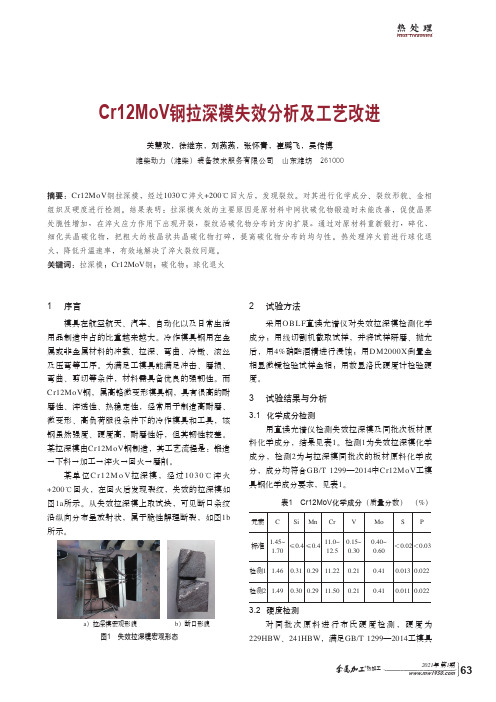
2021年 第1期热加工63热处理Heat TreatmentCr12MoV 钢拉深模失效分析及工艺改进关慧欢,徐继东,刘燕燕,张怀青,崔鹏飞,吴传博潍柴动力(潍柴)装备技术服务有限公司 山东潍坊 261000摘要:Cr12MoV 钢拉深模,经过1030℃淬火+200℃回火后,发现裂纹。
对其进行化学成分、裂纹形貌、金相组织及硬度进行检测。
结果表明:拉深模失效的主要原因是原材料中网状碳化物锻造时未能改善,促使晶界处脆性增加,在淬火应力作用下出现开裂,裂纹沿碳化物分布的方向扩展。
通过对原材料重新锻打,碎化、细化共晶碳化物,把粗大的枝晶状共晶碳化物打碎,提高碳化物分布的均匀性。
热处理淬火前进行球化退火,降低升温速率,有效地解决了淬火裂纹问题。
关键词:拉深模;Cr12MoV 钢;碳化物;球化退火1 序言模具在航空航天、汽车、自动化以及日常生活用品制造中占的比重越来越大。
冷作模具钢用在金属或非金属材料的冲载、拉深、弯曲、冷镦、滚丝及压弯等工序。
为满足工模具能满足冲击、磨损、弯曲、剪切等条件,材料需具备优良的强韧性。
而Cr12MoV 钢,属高铬微变形模具钢,具有很高的耐磨性、淬透性、热稳定性,经常用于制造高耐磨、微变形、高负荷服役条件下的冷作模具和工具,该钢虽然强度、硬度高,耐磨性好,但其韧性较差。
某拉深模由Cr12MoV 钢制造,其工艺流程是:锻造→下料→加工→淬火→回火→磨削。
某单位C r12M o V 拉深模,经过1030℃淬火+200℃回火,在回火后发现裂纹,失效的拉深模如图1a 所示。
从失效拉深模上取试块,可见断口条纹沿纵向分布呈放射状,属于脆性解理断裂,如图1b 所示。
2 试验方法采用OBLF 直读光谱仪对失效拉深模检测化学成分;用线切割机截取试样,并将试样研磨、抛光后,用4%硝酸酒精进行浸蚀;用DM2000X 倒置金相显微镜检验试样金相;用数显洛氏硬度计检验硬度。
3 试验结果与分析3.1 化学成分检测用直读光谱仪检测失效拉深模及同批次板材原料化学成分,结果见表1。
拉深件常见质量问题及预防措施
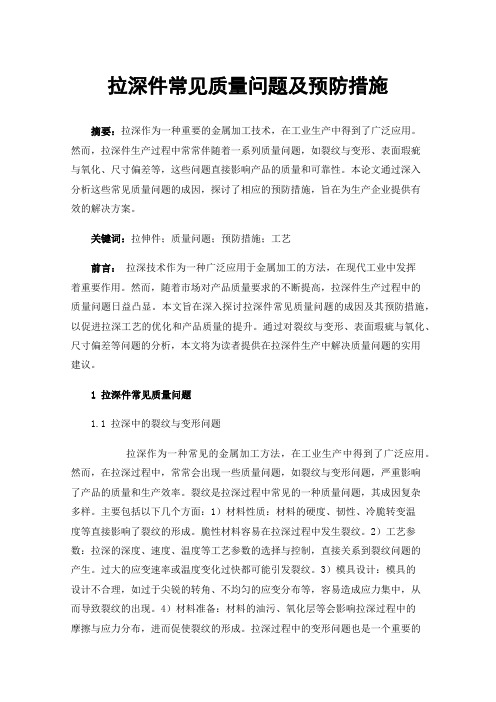
拉深件常见质量问题及预防措施摘要:拉深作为一种重要的金属加工技术,在工业生产中得到了广泛应用。
然而,拉深件生产过程中常常伴随着一系列质量问题,如裂纹与变形、表面瑕疵与氧化、尺寸偏差等,这些问题直接影响产品的质量和可靠性。
本论文通过深入分析这些常见质量问题的成因,探讨了相应的预防措施,旨在为生产企业提供有效的解决方案。
关键词:拉伸件;质量问题;预防措施;工艺前言:拉深技术作为一种广泛应用于金属加工的方法,在现代工业中发挥着重要作用。
然而,随着市场对产品质量要求的不断提高,拉深件生产过程中的质量问题日益凸显。
本文旨在深入探讨拉深件常见质量问题的成因及其预防措施,以促进拉深工艺的优化和产品质量的提升。
通过对裂纹与变形、表面瑕疵与氧化、尺寸偏差等问题的分析,本文将为读者提供在拉深件生产中解决质量问题的实用建议。
1拉深件常见质量问题1.1 拉深中的裂纹与变形问题拉深作为一种常见的金属加工方法,在工业生产中得到了广泛应用。
然而,在拉深过程中,常常会出现一些质量问题,如裂纹与变形问题,严重影响了产品的质量和生产效率。
裂纹是拉深过程中常见的一种质量问题,其成因复杂多样。
主要包括以下几个方面:1)材料性质:材料的硬度、韧性、冷脆转变温度等直接影响了裂纹的形成。
脆性材料容易在拉深过程中发生裂纹。
2)工艺参数:拉深的深度、速度、温度等工艺参数的选择与控制,直接关系到裂纹问题的产生。
过大的应变速率或温度变化过快都可能引发裂纹。
3)模具设计:模具的设计不合理,如过于尖锐的转角、不均匀的应变分布等,容易造成应力集中,从而导致裂纹的出现。
4)材料准备:材料的油污、氧化层等会影响拉深过程中的摩擦与应力分布,进而促使裂纹的形成。
拉深过程中的变形问题也是一个重要的质量挑战,材料的弹性模量、塑性变形能力等直接影响了变形的程度。
材料越脆性,变形越容易导致失真,并且不均匀的应变分布会引发不均匀的变形,从而造成拉深件的形状不准确。
此外,模具刚度不足会导致变形过大,模具变形甚至破坏,进而影响拉深件的准确性,拉深过程中的温度、压力等工艺参数的控制不当,都会导致不良的变形。
拉伸件、弯曲件缺陷及消除

在凸模纵断面形状急骤变化部位产生的壁增厚折皱..................................................................21
反弯曲形、鞍形、葫芦形的壁减薄折皱............................................................................21
【纵弯曲折皱】
凸缘折皱 .....................................................................................................11
壁折皱 .......................................................................................................13
弯曲件缺陷及消除 .............................................................................................35
回 弹 .......................................................................................................35
扭曲 .........................................................................................................29
模子印痕 .....................................................................................................30
拉深各工艺的缺陷

拉深各工艺的缺陷
不同工艺在生产过程中都可能存在一些缺陷,以下是几种常见的工艺缺陷:
1. 焊接缺陷:在焊接过程中可能出现的缺陷包括焊接强度不足、焊接接头不牢固、焊接接头气孔等,这些缺陷会导致焊接件的质量下降,甚至影响到焊接结构的安全性。
2. 铸造缺陷:在铸造过程中可能出现气孔、夹渣、砂眼、缩孔等缺陷,这些缺陷会导致铸件的内在质量不合格,可能会引起铸件的破裂、变形等问题。
3. 锻造缺陷:在锻造过程中可能出现表面裂纹、内部裂纹、夹杂物等缺陷,这些缺陷会导致锻件的强度、韧性下降,甚至引起锻件的破损。
4. 喷涂缺陷:在喷涂过程中可能出现涂层厚度不均匀、涂层与基材结合不牢固等缺陷,导致喷涂件的防腐、耐磨性能下降。
5. 切削加工缺陷:在切削加工过程中可能出现刀具磨损、切削力过大、表面粗糙度不符合要求等缺陷,导致零件的加工精度和表面质量下降。
6. 粉末冶金缺陷:在粉末冶金过程中可能出现孔隙、裂纹、异物等缺陷,导致制品的密度、机械性能下降。
这些缺陷可能由不同的原因引起,例如材料质量不好、工艺参数调整不当、设备故障等,因此在生产过程中需要严格控制各个环节,以减少缺陷的产生。
拉深缺陷及解决措施2(DOC)
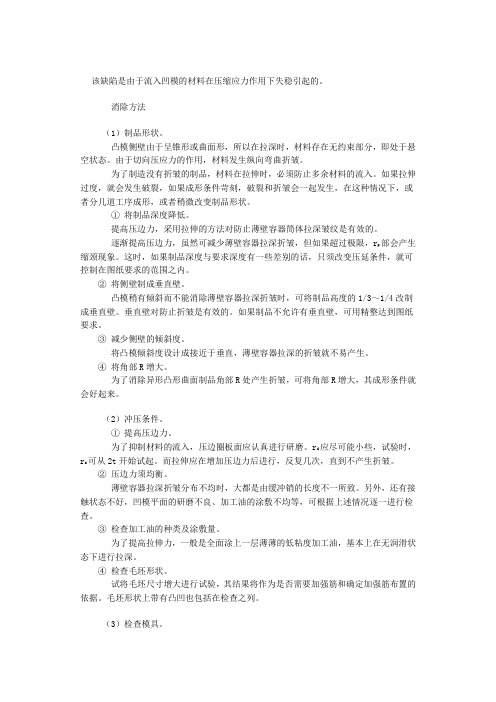
该缺陷是由于流入凹模的材料在压缩应力作用下失稳引起的。
消除方法(1)制品形状。
凸模侧壁由于呈锥形或曲面形,所以在拉深时,材料存在无约束部分,即处于悬空状态。
由于切向压应力的作用,材料发生纵向弯曲折皱。
为了制造没有折皱的制品,材料在拉伸时,必须防止多余材料的流入。
如果拉伸过度,就会发生破裂,如果成形条件苛刻,破裂和折皱会一起发生,在这种情况下,或者分几道工序成形,或者稍微改变制品形状。
① 将制品深度降低。
提高压边力,采用拉伸的方法对防止薄壁容器筒体拉深皱纹是有效的。
逐渐提高压边力,虽然可减少薄壁容器拉深折皱,但如果超过极限,r p部会产生缩颈现象。
这时,如果制品深度与要求深度有一些差别的话,只须改变压延条件,就可控制在图纸要求的范围之内。
② 将侧壁制成垂直壁。
凸模稍有倾斜而不能消除薄壁容器拉深折皱时,可将制品高度的1/3~1/4改制成垂直壁。
垂直壁对防止折皱是有效的。
如果制品不允许有垂直壁,可用精整达到图纸要求。
③ 减少侧壁的倾斜度。
将凸模倾斜度设计成接近于垂直,薄壁容器拉深的折皱就不易产生。
④ 将角部R增大。
为了消除异形凸形曲面制品角部R处产生折皱,可将角部R增大,其成形条件就会好起来。
(2)冲压条件。
① 提高压边力。
为了抑制材料的流入,压边圈板面应认真进行研磨。
r d应尽可能小些,试验时,r d可从2t开始试起。
而拉伸应在增加压边力后进行,反复几次,直到不产生折皱。
② 压边力须均衡。
薄壁容器拉深折皱分布不均时,大都是由缓冲销的长度不一所致。
另外,还有接触状态不好,凹模平面的研磨不良、加工油的涂敷不均等,可根据上述情况逐一进行检查。
③检查加工油的种类及涂敷量。
为了提高拉伸力,一般是全面涂上一层薄薄的低粘度加工油,基本上在无润滑状态下进行拉深。
④ 检查毛坯形状。
试将毛坯尺寸增大进行试验,其结果将作为是否需要加强筋和确定加强筋布置的依据。
毛坯形状上带有凸凹也包括在检查之列。
(3)检查模具。
① 加强拉伸的结构。
拉深引起的缺陷

凸模肩部相应部位裂纹由于材料的强度不够,当拉深载荷达到材料破断载荷时就会发生此缺陷。
缺陷部位产生于凸模肩R相应的部位(r p处),即比冲撞痕线更接近r p的部分。
破裂部分的冲撞痕线,因与其它部位不同,可以对下面几种情况进行观察检查:或者被延展;或者在凸缘的上下面有发亮的部分;或者产生折皱。
另外,在侧壁上有时也有发亮的部分。
初期横向破裂,呈舌状。
如图1。
图1 r p部破裂原因及消除方法(1)制品形状。
①拉深深度过大。
目前,圆筒、方筒深拉深的极限是在设计阶段确定的。
从而,在极限附近进行拉深时,要用表面光洁、平整的材料,综合模具配合和研磨,加工润滑油,缓冲压力,压力机精度等现场条件,进行试验拉深。
②凸模半径(r p)过小。
a将r p修正到适当值。
b图纸上的r p过小时,首先按适当值进行拉深,然后再增加一道工序,成形所需尺寸。
③凹模尺寸(r d)过小。
a将r d修正到适当值。
b图纸上的r d过小时,首先用适当r d值进行拉深,然后再增加一道工序,成形到所需尺寸。
④方筒的角部半径(r c)过小。
a将拉深深度减小;b多增加一道拉深工序;c换成更高级的材料;d将板料厚度增加。
(2)冲压条件。
①压边力过大。
压边力过大时,在凸缘面上不会发生起皱。
防皱压板面粗糙度,模具配合,间隙,r p,r d,加工油的种类和涂敷条件,缓冲销造成的压边力分布等,都影响防皱压力。
如果有关拉深的上述这些条件都合适的话,压边力就会下降,在起皱之前,不会发生破裂。
压边力过大时,由于凸缘面会全面发亮,所以很容易判断。
②润滑不良。
拉深加工与润滑有极为密切的关系,特别是包含有减薄拉深加工时,必须控制制品温度的升高。
如果是条件好的拉深加工,润滑油的选择不成什幺问题;条件不好的拉深加工,如果润滑油选择不当,就会引起破裂。
③毛坯形状不良。
在试拉深阶段,决定毛坯形状是重要的工作之一。
必须将毛坯形状限制在最小尺寸。
当用方形毛坯进行圆筒拉深时,极限拉深率为0.58左右。
- 1、下载文档前请自行甄别文档内容的完整性,平台不提供额外的编辑、内容补充、找答案等附加服务。
- 2、"仅部分预览"的文档,不可在线预览部分如存在完整性等问题,可反馈申请退款(可完整预览的文档不适用该条件!)。
- 3、如文档侵犯您的权益,请联系客服反馈,我们会尽快为您处理(人工客服工作时间:9:00-18:30)。
拉深件厚度和硬度的分布
3、形状、尺寸超差
(1)直径
模具间隙较大时, 制件回弹比较明显。 口部直径要比凹模 工作部分略有增大, 口部与侧壁之间的 上口部分要比凹模 的有所减小。且间 隙越大越严重。
d凹=24.05 d凹=24.14
(2)高度
制件的实际高 度随间隙值的减 小而逐渐增大, 间隙值增大,制 件高度减小,甚 至低于理论高度。
2、拉裂
拉深时板料拉应力超过筒壁的抗拉强度。拉深 后得到工件的厚度沿底部向口部方向是不同的, 特别是靠近凸模圆角处变薄最严重。
措施:
(1)选冲压性能好的材料,如屈强比小、延伸 率大的;
(2)提高模具设备的技术状态(增加Hale Waihona Puke 模的表 面粗糙度、增加凸凹模圆角);
(3)适当调整压边力、间隙、拉深比,正确操 作并合理润滑。
模具间隙值与拉深件高度的关系
4、拉深件表面擦伤
引起拉深件表面擦伤的原因主要是制作 凹模的材料、凹模表面粗糙度及表面磨损 严重、拉深间隙过小、毛坯表面有砂和氧 化皮等引起材料在流动时表面被擦伤。
§12.6 拉深件常见工序
1、起皱
拉深过程中,如毛坯相对厚度较小,毛坯凸缘部分在 切向压力的作用下,很可能因为失稳而产生弯曲隆起的现 象,称为起皱。
影响起皱的因素: (1)凸缘部分材料的相对厚度: (2)切向压应力的大小:变形程度越大,需要转移的剩余
材料越多,加工硬化现象越严重,则σ 3越大,就越容易 起皱。 (3)材料的力学性能:板料的屈强比小,则屈服极限小, 变形区内的切向压应力也相对减小,因此板料不容易起皱。
(4)凹模工作部分的几何形状
筒形件防止拉深起皱的措施
(1)加压边圈并适当加大压边力; (2)取适当凹模直径(减小),可减少流
入凹模膛内的材料,消除皱纹; (3)保证压边力各处均匀,控制材料流向,
减少起皱; (4)坯料应厚度均匀,且相对厚度越大越
不易起皱; (5)选择拉深性能好的材料。