结合多种工艺.注塑转移成型
多工位级进模的工艺特征

多工位级进模的工艺特征
多工位级进模是一种用于生产复杂零件的成型工艺。
它有以下的特征:
1. 多工位:级进模有多个工位,每个工位可以完成不同的操作,如注塑、挤压、剪切、冲孔等。
2. 级进:模具在进行工件成型时,通过连续推动工件,将工件移至下一个工位进行下一道工序,直到制成完整的零件。
3. 精度高:多工位级进模可以一次完成多道复杂的加工工序,工艺流程简单,能够保证工件的精度和质量。
4. 自动化程度高:多工位级进模的生产过程可以实现全自动化,提高了生产效率和生产质量。
5. 适用范围广:级进模可以用于制造各种复杂的零部件,如汽车零部件、电子产品、家用电器等。
6. 设计难度大:由于级进模的复杂性,它的设计和制造难度都比较大。
需要考虑到多个工位之间的转移、定位、夹持等问题。
几种常用塑料的成型工艺
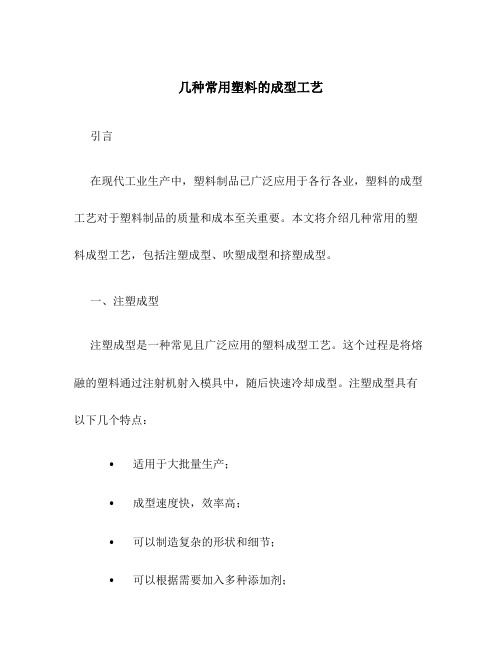
几种常用塑料的成型工艺引言在现代工业生产中,塑料制品已广泛应用于各行各业,塑料的成型工艺对于塑料制品的质量和成本至关重要。
本文将介绍几种常用的塑料成型工艺,包括注塑成型、吹塑成型和挤塑成型。
一、注塑成型注塑成型是一种常见且广泛应用的塑料成型工艺。
这个过程是将熔融的塑料通过注射机射入模具中,随后快速冷却成型。
注塑成型具有以下几个特点:•适用于大批量生产;•成型速度快,效率高;•可以制造复杂的形状和细节;•可以根据需要加入多种添加剂;•成本相对较低。
注塑成型主要有以下几个步骤:1.塑料原料进料:将塑料颗粒通过注塑机的料斗输送到加热筒中,进行熔融。
2.制作模具:根据产品的形状和尺寸,制作适当的模具。
3.射入模具:将熔融的塑料注入模具中。
4.冷却成型:通过冷却系统,使塑料迅速冷却成型。
5.取出成品:将成品从模具中取出。
注塑成型应用广泛,常见的产品包括塑料杯、塑料盒、零部件等。
二、吹塑成型吹塑成型是一种常用的塑料成型工艺,适用于制造中空物体,如瓶子、容器、玩具等。
吹塑成型具有以下几个特点:•适用于大中批量生产;•可以制造中空物体;•成型速度较快;•成本相对较低。
吹塑成型主要有以下几个步骤:1.塑料颗粒预热:将塑料颗粒通过加热系统进行预热,使其变软且易于塑性变形。
2.吹塑成型:将预热的塑料颗粒放入吹塑机中,通过高压气体将其吹塑成模具中的形状。
3.冷却固化:通过冷却系统,使塑料迅速冷却固化。
4.修整:将成品从模具中取出,并进行修整、修剪等处理。
吹塑成型广泛应用于食品包装、化妆品容器等领域。
三、挤塑成型挤塑成型是一种将熔融的塑料挤出成型的工艺,适用于制造具有恒定截面形状的长条状成品,如管道、线缆等。
挤塑成型具有以下几个特点:•适用于大批量生产;•可以制造长条状成品;•成型速度较快;•成本相对较低。
挤塑成型主要有以下几个步骤:1.塑料预处理:将塑料颗粒或粉末进行预处理,使其达到适合挤塑的熔融状态。
2.加热熔融:将预处理的塑料通过加热系统加热熔融。
注塑机工艺流程注塑成型工艺过程详解
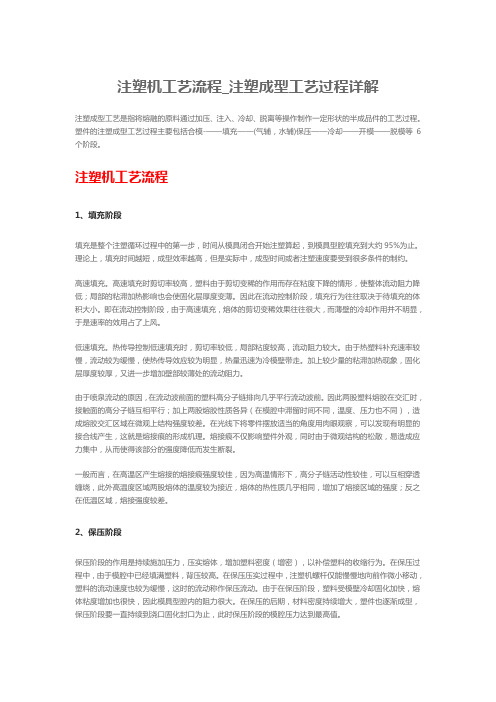
注塑机工艺流程_注塑成型工艺过程详解注塑成型工艺是指将熔融的原料通过加压、注入、冷却、脱离等操作制作一定形状的半成品件的工艺过程。
塑件的注塑成型工艺过程主要包括合模-——填充——(气辅,水辅)保压——冷却——开模——脱模等6个阶段。
注塑机工艺流程1、填充阶段填充是整个注塑循环过程中的第一步,时间从模具闭合开始注塑算起,到模具型腔填充到大约95%为止。
理论上,填充时间越短,成型效率越高,但是实际中,成型时间或者注塑速度要受到很多条件的制约。
高速填充。
高速填充时剪切率较高,塑料由于剪切变稀的作用而存在粘度下降的情形,使整体流动阻力降低;局部的粘滞加热影响也会使固化层厚度变薄。
因此在流动控制阶段,填充行为往往取决于待填充的体积大小。
即在流动控制阶段,由于高速填充,熔体的剪切变稀效果往往很大,而薄壁的冷却作用并不明显,于是速率的效用占了上风。
低速填充。
热传导控制低速填充时,剪切率较低,局部粘度较高,流动阻力较大。
由于热塑料补充速率较慢,流动较为缓慢,使热传导效应较为明显,热量迅速为冷模壁带走。
加上较少量的粘滞加热现象,固化层厚度较厚,又进一步增加壁部较薄处的流动阻力。
由于喷泉流动的原因,在流动波前面的塑料高分子链排向几乎平行流动波前。
因此两股塑料熔胶在交汇时,接触面的高分子链互相平行;加上两股熔胶性质各异(在模腔中滞留时间不同,温度、压力也不同),造成熔胶交汇区域在微观上结构强度较差。
在光线下将零件摆放适当的角度用肉眼观察,可以发现有明显的接合线产生,这就是熔接痕的形成机理。
熔接痕不仅影响塑件外观,同时由于微观结构的松散,易造成应力集中,从而使得该部分的强度降低而发生断裂。
一般而言,在高温区产生熔接的熔接痕强度较佳,因为高温情形下,高分子链活动性较佳,可以互相穿透缠绕,此外高温度区域两股熔体的温度较为接近,熔体的热性质几乎相同,增加了熔接区域的强度;反之在低温区域,熔接强度较差。
2、保压阶段保压阶段的作用是持续施加压力,压实熔体,增加塑料密度(增密),以补偿塑料的收缩行为。
注塑成型工艺介绍
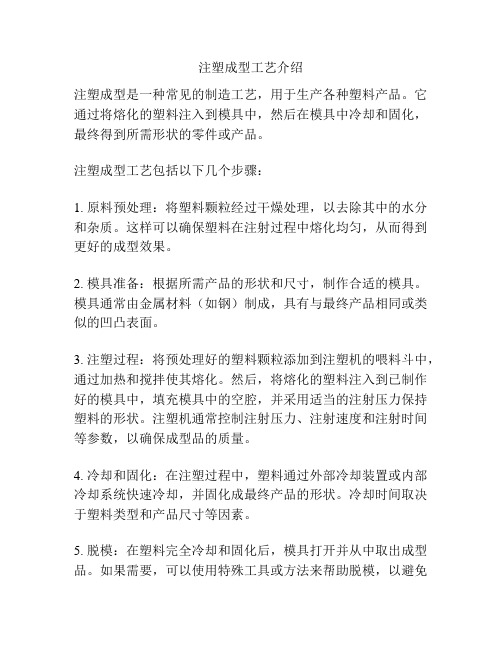
注塑成型工艺介绍注塑成型是一种常见的制造工艺,用于生产各种塑料产品。
它通过将熔化的塑料注入到模具中,然后在模具中冷却和固化,最终得到所需形状的零件或产品。
注塑成型工艺包括以下几个步骤:1. 原料预处理:将塑料颗粒经过干燥处理,以去除其中的水分和杂质。
这样可以确保塑料在注射过程中熔化均匀,从而得到更好的成型效果。
2. 模具准备:根据所需产品的形状和尺寸,制作合适的模具。
模具通常由金属材料(如钢)制成,具有与最终产品相同或类似的凹凸表面。
3. 注塑过程:将预处理好的塑料颗粒添加到注塑机的喂料斗中,通过加热和搅拌使其熔化。
然后,将熔化的塑料注入到已制作好的模具中,填充模具中的空腔,并采用适当的注射压力保持塑料的形状。
注塑机通常控制注射压力、注射速度和注射时间等参数,以确保成型品的质量。
4. 冷却和固化:在注塑过程中,塑料通过外部冷却装置或内部冷却系统快速冷却,并固化成最终产品的形状。
冷却时间取决于塑料类型和产品尺寸等因素。
5. 脱模:在塑料完全冷却和固化后,模具打开并从中取出成型品。
如果需要,可以使用特殊工具或方法来帮助脱模,以避免损坏或变形。
6. 后处理:根据产品的要求,可能需要进行后处理工艺,如修边、打磨、修整等,以获得最终的产品质量和外观效果。
注塑成型工艺的优点在于可以生产复杂形状的产品,并具有良好的尺寸稳定性和表面质量。
此外,注塑成型可以批量生产,提高生产效率和降低成本。
然而,注塑成型也存在一些限制,如模具制作成本较高、制作周期长、塑料材料的选择受限等。
因此,在进行注塑成型之前,需要仔细评估产品设计和成本效益,以确保工艺的可行性。
总而言之,注塑成型是一种常用、高效且灵活的制造工艺,广泛应用于各个行业,从电子产品到家具、汽车零部件等。
它为生产高质量和复杂形状的塑料产品提供了可靠的解决方案。
注塑成型是一种常见的制造工艺,广泛应用于各个行业。
它能够生产出各种形状复杂、尺寸稳定的塑料制品,包括塑料壳体、容器、零部件、玩具等。
注塑多段成型原理

背压的形成、作用与调校一、背压的形成在塑料熔融、塑化过程中,熔料不断移向料筒前端(计量室内),且越来越多,逐渐形成一个压力,推动螺杆向后退。
为了阻止螺杆后退过快,确保熔料均匀压实,需要给螺杆提供一个反方向的压力,这个反方向阻止螺杆后退的压力称为背压。
背压亦称塑化压力,它的控制是通过调节注射油缸之回油节流阀实现的。
预塑化螺杆注塑机注射油缸后部都设有背压阀,调节螺杆旋转后退时注射油缸泄油的速度,使油缸保持一定的压力(如下图所示);全电动机的螺杆后移速度(阻力)是由 AC 伺服阀控制的。
二、适当调校背压的好处1、能将炮筒内的熔料压实,增加密度,提高射胶量、制品重量和尺寸的稳定性。
2、可将熔料内的气体“ 挤出”,减少制品表面的气花、内部气泡、提高光泽均匀性。
减慢螺杆后退速度,使炮筒内的熔料充分塑化,增加色粉、色母与熔料的混合均匀度,避免制品出现混色现象。
3、减慢螺杆后退速度,使炮筒内的熔料充分塑化,增加色粉、色母与熔料的混合均匀度,避免制品出现混色现象。
4、适当提升背压,可改善制品表面的缩水和产品周边的走胶情况。
5、能提升熔料的温度,使熔料塑化质量提高,改善熔料充模时的流动性,制品表面无冷胶纹。
三、背压太低时,易出现下列问题1、背压太低时,螺杆后退过快,流入炮筒前端的熔料密度小(较松散),夹入空气多。
2、会导致塑化质量差、射胶量不稳定,产品重量、制品尺寸变化大。
3、制品表面会出现缩水、气花、冷料纹、光泽不匀等不良现象。
4、产品内部易出现气泡,产品周边及骨位易走不满胶。
四、过高的背压 ,易出现下列问题1、炮筒前端的熔料压力太高、料温高、粘度下降,熔料在螺杆槽中的逆流和料筒与螺杆间隙的漏流量增大,会降低塑化效率(单位时间内塑化的料量).2、对于热稳定性差的塑料(如:PVC、POM等)或着色剂,因熔料的温度升高且在料筒中受热时间增长而造成热分解,或着色剂变色程度增大,制品表面颜色/光泽变差。
3、背压过高,螺杆后退慢,预塑回料时间长,会增加周期时间,导致生产效率下降。
日用陶瓷主要成型工艺

日用陶瓷主要成型工艺日用陶瓷是我们日常生活中常见的物品,它们的制作过程经历了多种成型工艺。
本文将介绍几种常见的日用陶瓷成型工艺,包括手工成型、模具成型和注塑成型。
手工成型是最古老也是最原始的陶瓷成型工艺之一。
在手工成型过程中,陶工使用手工技艺将陶泥按照设计的形状逐渐塑造出来。
这种工艺需要陶工具有丰富的经验和技艺,因为他们需要准确掌握陶泥的质感和形状,以确保最终成品的完美。
手工成型的优点是可以根据需求进行个性化设计和调整,制作出独一无二的陶瓷作品。
然而,手工成型的缺点是生产效率低,成本较高。
模具成型是一种较为常见的陶瓷成型工艺。
在模具成型过程中,陶工首先根据设计要求制作出一个模具,然后将陶泥放入模具中,经过一定的时间使其凝固和干燥,最后从模具中取出成品。
模具成型的优点是生产效率高,成本较低,适用于大规模生产。
然而,模具成型的缺点是成品的形状和质感相对固定,无法进行个性化设计和调整。
注塑成型是一种现代化的陶瓷成型工艺。
在注塑成型过程中,陶泥通过注射机注入模具中,通过压力和热力使其充分填充模具的空腔,然后冷却成型,最后从模具中取出成品。
注塑成型的优点是生产效率非常高,可以快速制作出大量一致的成品。
此外,注塑成型还可以实现复杂的形状和细节,使产品更加精细。
然而,注塑成型的缺点是设备和技术要求较高,成本相对较高。
日用陶瓷的主要成型工艺包括手工成型、模具成型和注塑成型。
每种工艺都有其独特的优点和局限性,可以根据需求选择合适的工艺。
无论是手工成型、模具成型还是注塑成型,陶瓷制作都需要陶工的经验和技艺,以及对陶泥和成型过程的精确掌握。
通过不同的工艺,我们可以制作出各种不同形状和风格的日用陶瓷,丰富我们的生活。
塑料制品生产工艺过程

塑料制品的生产工艺流程根据塑料的固有性能,使其成为具有一定形状和使用价值的塑料制品,是一个复杂而繁重的过程。
塑料制品工业生产中,塑料制品的生产系统主要是由塑料的成型、机械加工、装饰和装配四个连续的过程组成的。
在这四个过程中,塑料成型是塑料加工的关键。
成型的方法多达三十几种,主要是将各种形态的塑料(粉、粒料、溶液或分散体)制成所需形状的制品或坯件。
成型方法主要决定于塑料的类型(热塑性还是热固性)、起始形态以及制品的外形和尺寸。
塑料加工热塑性塑料常用的方法有挤出、注射成型、压延、吹塑和热成型等,塑料加工热固性塑料一般采用模压、传递模塑,也用注射成型。
层压、模压和热成型是使塑料在平面上成型。
上述塑料加工的方法,均可用于橡胶加工.此外,还有以液态单体或聚合物为原料的浇铸等。
在这些方法中,以挤出和注射成型用得最多,也是最基本的成型方法。
塑料制品生产之机械加工是借用金属和木材等的塑料加工方法,制造尺寸很精确或数量不多的塑料制品,也可作为成型的辅助工序,如挤出型材的锯切。
由于塑料的性能与金属和木材不同,塑料的热导性差,热膨胀系数、弹性模量低,当夹具或刀具加压太大时,易于引起变形,切削时受热易熔化,且易粘附在刀具上。
因此,塑料进行机械加工时,所用的刀具及相应的切削速度等都要适应塑料特点。
常用的机械加工方法有锯、剪、冲、车、刨、钻、磨、抛光、螺纹加工等.此外,塑料也可用激光截断、打孔和焊接。
塑料制品生产之接合塑料加工把塑料件接合起来的方法有焊接和粘接。
焊接法是使用焊条的热风焊接,使用热极的热熔焊接,以及高频焊接、摩擦焊接、感应焊接、超声焊接等.粘接法可按所用的胶粘剂,分为熔剂、树脂溶液和热熔胶粘接。
塑料制品生产表面修饰的目的是美化塑料制品表面,通常包括:机械修饰,即用锉、磨、抛光等工艺,去除制件上毛边、毛刺,以及修正尺寸等;涂饰,包括用涂料涂敷制件表面,用溶剂使表面增亮,用带花纹薄膜贴覆制品表面等;施彩,包括彩绘、印刷和烫印;镀金属,包括真空镀膜、电镀以及化学法镀银等.塑料加工烫印是在加热、加压下,将烫印膜上的彩色铝箔层(或其他花纹膜层)转移到制件上.许多家用电器及建筑制品、日用品等都用此法获得金属光泽或木纹等图案。
注塑成型技术

注塑成型技术注塑成型技术是一种常见的加工工艺,广泛应用于制造各种塑料制品。
它通过将熔化的塑料材料注入模具中,经过冷却和固化形成所需的产品。
本文将介绍注塑成型技术的工作原理、优势、应用领域以及未来发展方向等内容。
一、工作原理注塑成型技术主要由注射系统、模具系统、冷却系统、控制系统和辅助系统等组成。
首先,将塑料颗粒或粉末加热至熔化状态,然后通过注射系统将熔融的塑料注入到模具腔中。
随后,经过冷却和固化,将所需的产品从模具中取出。
在注塑成型过程中,需要注意控制以下因素:注塑压力、注塑速度、注射时间和冷却时间。
适当调节这些参数可以确保产品的质量和生产效率。
二、优势注塑成型技术具有许多优势,使其成为一种常用的塑料加工方法。
1. 生产效率高:注塑成型工艺可以实现连续生产,自动化程度高,生产效率较高。
2. 产品精度高:模具的设计和制造精度较高,可以生产出形状复杂、尺寸精确的产品。
3. 可塑性好:注塑成型工艺适用于各种不同类型的塑料材料,如聚丙烯、聚氯乙烯、聚苯乙烯等。
4. 成本低:由于注塑成型技术可以实现大规模连续生产,单个产品的生产成本相对较低。
5. 资源回收利用:废弃的塑料制品可以通过再次熔化和塑化再利用,降低了对资源的消耗。
三、应用领域注塑成型技术广泛应用于许多工业领域和日常生活中,以下是一些常见的应用领域:1. 电子电器:注塑成型技术可以用于生产各种电子设备外壳、插件、线束等。
2. 汽车工业:汽车零部件的生产通常采用注塑成型技术,如车灯、仪表盘、内饰件等。
3. 医疗器械:医用注射器、输液器和其他医疗器械都是通过注塑成型工艺制造的。
4. 家居用品:家具配件、塑料餐具、家用电器等都是使用注塑成型技术生产的。
5. 包装行业:塑料瓶、塑料桶、塑料盒等包装材料通常采用注塑成型工艺生产。
四、未来发展方向注塑成型技术在不断发展和创新的过程中,面临着一些挑战和机遇。
1. 环境友好型材料:随着环保意识的增强,未来的注塑成型技术可能会更加注重使用可降解和可回收的塑料材料。
- 1、下载文档前请自行甄别文档内容的完整性,平台不提供额外的编辑、内容补充、找答案等附加服务。
- 2、"仅部分预览"的文档,不可在线预览部分如存在完整性等问题,可反馈申请退款(可完整预览的文档不适用该条件!)。
- 3、如文档侵犯您的权益,请联系客服反馈,我们会尽快为您处理(人工客服工作时间:9:00-18:30)。
注塑成型新工艺
结合多种工艺
目前,很多成型商已采用了诸如三明治成型、注射压力成型以及气体或水的辅助成型工艺来生产超薄壁零件或玻纤增强的内表面光滑的中空零件。
塑料加工研究院的注塑成型和模具技术部门建议,如果将上述各种先进工艺组合起来,可以得到更高级的加工件,并能够降低成本,克服单一方法的局限性。
塑料加工研究院的注塑成型和模具技术部门评价说,将三明治成型、注射压力成型以及气体或水的辅助成型相结合,这种组合工艺完全是从在模具里成型“皮-芯-皮”的三明治结构开始的。
把三明治成型与注射压力成型相结合,加工的零件具有更均匀的芯-皮分布。
在注射压力成型工艺中,使用较低的注射或充模压力,不仅可以使加工件中的物料定向程度较低,减少收缩和变形,而且还可以降低对模腔的耐压要求。
此外,有加压这个步骤,可以获得较小的皮厚或总壁厚。
塑料加工研究院的注塑成型和模具技术部门认为,利用“三明治成型+注射压力成型”工艺,可以生产出采用传统成型工艺根本无法实现的薄壁加工件。
采用传统的三明治注射成型工艺,可以实现的最薄的壁厚为1.5 mm,而采用三明治/压力工艺后,制作出的工件壁厚仅为1 mm。
当然,传统的三明治成型工艺允许用户把加工件里芯材的百分比加大。
塑料加工研究院的注塑成型和模具技术部门还进行了如下试验,即通过“三明治成型+水辅助成型”的组合工艺,用长玻纤PP和无填料PP来成型扶手。
根据以往的经验,用注水的办法会使短玻纤增强的尼龙66或长玻纤PP这类纤维增强材料形成空心,导致加工件内表面的质量很差,而且空心腔的尺寸也会发生偏差。
因此,塑料加工研究院的注塑成型和模具技术部门认为,玻纤填充树脂的流动特性使水辅助成型工艺很难或者无法实现。
因此,他们采用30%长玻纤增强PP作为表皮、无填料PP作为芯来进行三明治试验。
扶手模具的直径为30 mm,长度为500 mm。
通过注水,使无填料的物料形成空心。
这样,外层材料具有了刚性、韧性以及抗张力和迸裂强度,而内层材料具有了良好的阻隔性能,内表面也很光滑。
目前,这种方法已经被用于工业生产中。
注塑转移成型
一种被称作注塑转移成型(ITM)的新工艺不仅可以使多腔成型的热塑性塑料小零件获得很好的一致性,还可以得到更好的成型质量。
这种借鉴了热固性塑料转移成型工艺的新工艺是将热流道注塑和压力成型两者进行组合的工艺。
据塑料加工研究院的注塑成型和模具技术部门介绍,在传统的热流道注塑成型中,熔体进入多个腔室的温度和压力是不一样的,这意味着每个腔室具有不同的粘度、不同的填充量和不同的冷却状况,最终将导致零件的尺寸和性能也不相同。
此外,传统注塑模具的另一个局限性是,通常对热流道的设计都是针对具体的模具或物料,对于完全不同的模具或物料而言,这个热流道就不一定适用了。
为此,塑料加工研究院研制了一种模具。
在模具的固定侧采用了特殊的电加热,在热半模里有一个熔体转移室,用来储存来自螺杆的熔体,并借助于一个活塞/气缸系统把熔体转移到模腔里去;冷半模在移动压板一侧。
利用固定在半模里的隔热板来减少冷、热半模之间的热传导。
当模具的开模线合拢时,活塞/气缸系统对熔体转移室施压,通过短门,将物料直接推入模腔。
在这个系统里,注塑和
保压是由静止不动的模具而不是通过螺杆来实现的。
在保压阶段之后,转移室开始充填下一个周期的物料。
在这个过程中,主开模线(它的开与合都与转移室的动作互不相干)一直保持合拢,直到加工件充分冷却为止。
这种工艺具有许多好处。
模具的熔体转移部分与该部分的几何形状无关,因此无需为不同的模具而做相应的改变;由于注塑体积是由腔室的运动距离来决定的,所以可以降低多腔模具的造价,同时不需要再使用昂贵的热流道温度控制器;因为熔体的通道很短,而且熔体是直接从蓄集室的门进入模腔,所以所需要的压力比传统热流道可提供的压力更低,熔体完全能够均匀地充满所有模腔;作用在熔体上的剪切力和应力更小了,有利于长玻纤增强料或者瓷粉掺混料的成型,并使得加工件的收缩率和翘曲变形更小。
目前,塑料加工研究院已经使用了多达12个模腔的模具对长玻纤增强聚丙烯材料进行注塑成型试验,并取得了成功。
他们很快就会用超过100个模腔的模具来进一步测试这种工艺。