注塑件成型与设计
第6章 注塑模具结构及设计(4)-成型零件设计

一、分型面的形式
二、分型面的选择 选择分型面的原则是: 1、分型面应选择在塑件外形最大轮廓处 当初步确定塑件的分型方向后,分型面应选在塑件外形最大 轮廓处,即通过该方向上塑件的截面积最大,否则塑件无法从 型腔中脱出。 2、应尽量减少塑件(型腔)在分型面上的投影面积 注塑机都规定其相应模具所允许的最大成型面积以及额定锁 模力,注射成型过程中,当塑件(包括浇注系统)在分型面上 的投影面积超过允许的最大成型面积时,将会出现涨模溢料现 象,这时注射成型所需的合模力也会超过额定锁模力。因此, 选择分型面时,应考虑对成型面积的影响。(教材P67图4-34)
6、3、2 结构设计 成型零件主要包括型腔、型芯、镶拼件、各种成型杆与成 型环。
塑件生产对成型零件的要求: 足够的强度、刚度、硬度(HRC30以上)、耐磨性; 足够的精度和适当的表面粗糙度(一般Ra<0.4μm);
一定的耐热疲劳性和耐腐蚀性,生产腐蚀性塑料还要特 别防护(选耐蚀材料或电镀硬铬)。
7、无损塑件外观 图示塑件,底部带有环形支撑面,若分型面 按图(a)中方案设计,会在环形支撑面处留下毛 边痕迹。如果改为图(b)中方案、毛边产生在塑 件端面,去除后对塑件外观无损。
8、对侧向抽芯的影响 一般注塑模的侧向抽芯,都是借助模具打开时的开模运 动。通过模具的抽芯机构进行抽芯,在有限的开模行程内, 完成的抽芯距离有限制。因此,对于带有互相垂直的两个 方向都有孔或凹槽的塑件,应避免长距离抽芯。
2、镶拼型芯结构 为便于加工,形状复杂的型芯可采用镶拼组合式结构, 如图所示。
采用组合式行行行可大大改善加工和热处理的工艺性。 但设计和制造这类型芯时,必须注意结构的合理性,应 保证型芯和小型芯镶块的强度、防止热处理变形,应避 免尖角与薄壁。
注塑成型工艺流程及工艺参数
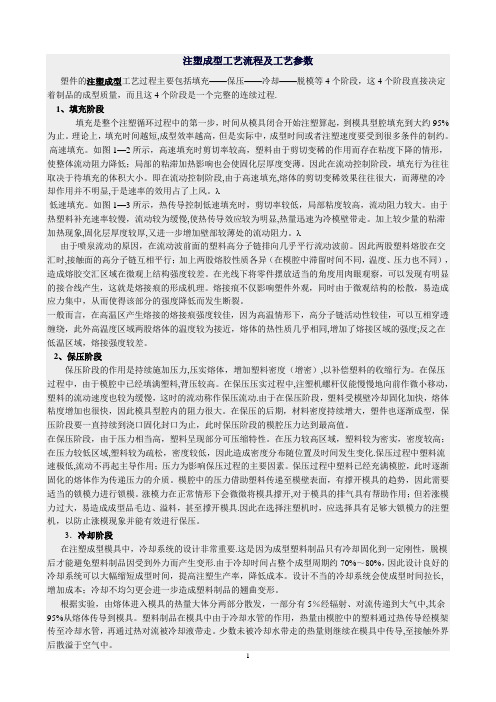
注塑成型工艺流程及工艺参数塑件的注塑成型工艺过程主要包括填充——保压——冷却——脱模等4个阶段,这4个阶段直接决定着制品的成型质量,而且这4个阶段是一个完整的连续过程.1、填充阶段填充是整个注塑循环过程中的第一步,时间从模具闭合开始注塑算起,到模具型腔填充到大约95%为止。
理论上,填充时间越短,成型效率越高,但是实际中,成型时间或者注塑速度要受到很多条件的制约。
高速填充。
如图1—2所示,高速填充时剪切率较高,塑料由于剪切变稀的作用而存在粘度下降的情形,使整体流动阻力降低;局部的粘滞加热影响也会使固化层厚度变薄。
因此在流动控制阶段,填充行为往往取决于待填充的体积大小。
即在流动控制阶段,由于高速填充,熔体的剪切变稀效果往往很大,而薄壁的冷却作用并不明显,于是速率的效用占了上风。
λ低速填充。
如图1—3所示,热传导控制低速填充时,剪切率较低,局部粘度较高,流动阻力较大。
由于热塑料补充速率较慢,流动较为缓慢,使热传导效应较为明显,热量迅速为冷模壁带走。
加上较少量的粘滞加热现象,固化层厚度较厚,又进一步增加壁部较薄处的流动阻力。
λ由于喷泉流动的原因,在流动波前面的塑料高分子链排向几乎平行流动波前。
因此两股塑料熔胶在交汇时,接触面的高分子链互相平行;加上两股熔胶性质各异(在模腔中滞留时间不同,温度、压力也不同),造成熔胶交汇区域在微观上结构强度较差。
在光线下将零件摆放适当的角度用肉眼观察,可以发现有明显的接合线产生,这就是熔接痕的形成机理。
熔接痕不仅影响塑件外观,同时由于微观结构的松散,易造成应力集中,从而使得该部分的强度降低而发生断裂。
一般而言,在高温区产生熔接的熔接痕强度较佳,因为高温情形下,高分子链活动性较佳,可以互相穿透缠绕,此外高温度区域两股熔体的温度较为接近,熔体的热性质几乎相同,增加了熔接区域的强度;反之在低温区域,熔接强度较差。
2、保压阶段保压阶段的作用是持续施加压力,压实熔体,增加塑料密度(增密),以补偿塑料的收缩行为。
注塑模具的设计及制造

注塑模具的设计及制造注塑模具是用于注塑成型的模具,它的设计和制造直接关系到产品质量和生产效率。
本文将从设计和制造两个方面介绍注塑模具的相关知识。
一、注塑模具的设计1.产品设计分析:在进行注塑模具设计之前,首先要对即将生产的产品进行分析。
了解产品的形态尺寸、材料特性、注塑工艺和生产要求等,为模具设计提供依据。
2.模具结构设计:根据产品要求和注塑工艺,设计模具的结构。
包括模具的开合方式、定位方式、注塑道设计和冷却系统设计等。
合理的结构设计可以提高模具使用寿命和生产效率。
3.模具零件设计:根据模具结构设计,对各个零件进行详细设计。
比如模具芯、模具腔、滑块、顶出机构、定位销和定位套等。
零件设计要考虑到材料选择、加工工艺和装配要求等。
4.模具标准件选用:在模具设计过程中,可以选用一些标准件,如模具基础板、导向套和注塑嘴等。
合理选用标准件不仅可以减少设计工作量,还可以提高模具加工精度和降低成本。
5.注塑模具的通气设计:在注塑过程中,模具内会产生大量的气体,如果不能有效排出,会导致产品缺陷。
所以,在模具设计中要合理设置通气孔和排气槽,以确保注塑过程的质量。
二、注塑模具的制造1.模具材料选择:注塑模具常用的材料有优质合金钢和工具钢,比如P20、718、2738等。
材料的选择要根据产品要求、生产批量和制造成本等因素综合考虑。
2.模具加工工艺:注塑模具的加工工艺包括铣削、镗削、磨削、电火花和线切割等。
不同的加工工艺需要选用不同的设备和工装,操作人员要熟悉模具加工过程和技术要求。
3.模具热处理:模具在使用过程中需要经过热处理,以提高材料的硬度和耐磨性。
常见的热处理方法有淬火、回火和表面处理等,要根据模具材料和要求选择适当的热处理方法。
4.模具组装和调试:在模具制造完成后,需要对各个零部件进行组装和调试。
确保模具各部件的精度和配合度,在注塑生产前进行试模和修正,以保证产品质量。
总之,注塑模具的设计和制造对于提高注塑产品的质量和生产效率至关重要。
塑料成型工艺与模具设计
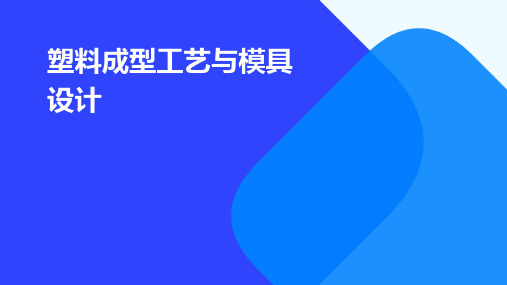
采用新型螺杆设计、优化口模结构等 方法,提高制品尺寸精度和表面质量。
05
模具设计的创新与实践
智能化模具设计
1
智能化模具设计是指利用先进的信息技术、人工 智能和大数据分析,实现模具设计的自动化、智 能化和精细化。
2
通过智能化设计,可以大大提高模具设计的效率 和精度,减少人工干预和误差,降低生产成本, 提高产品质量。
案例概述
本案例介绍了智能化技术在塑料成型工 艺与模具设计中的应用,以提高模具设
计的效率和精度。
快速原型制造
采用3D打印技术制作模具原型,缩短 了模具制作周期,降低了试模成本。
智能化技术应用
采用计算机辅助设计(CAD)软件进 行模具设计,利用仿真技术预测制品 成型过程和优化模具结构。
数据分析与优化
通过收集生产数据,分析制品缺陷和 模具问题,进一步优化模具设计和工 艺参数。
工艺特性要求
塑料成型工艺的特性决定了模具 设计的结构和尺寸,例如模具的 型腔、浇注系统、冷却系统等。
材料选择
塑料成型工艺对材料的要求也影 响了模具设计的选择,例如模具 材料的耐热性、耐磨性、耐腐蚀 性等。
模具设计对塑料成型工艺的制约
模具容量
模具的容量决定了能够成型的塑料制 品的大小和复杂程度。
模具温度控制
新材料选择
选用聚碳酸酯(PC)作为替代传统 聚乙烯(PE)的材料,具有更好的 强度、耐热性和透明性。
模具设计调整
针对新材料的特点,优化了模具结构 设计,如增加热流道、改进冷却系统 等。
工艺参数优化
根据新材料的特性,调整了注射温度、 注射压力、模具温度等工艺参数,提 高了成型效率和制品性能。
智能化模具设计实践案例
基于正交试验法的注塑件成型工艺参数优化设计

基于正交试验法的注塑件成型工艺参数优化设计引言注塑成型是一种常见的加工工艺,用于制造各种形状复杂的塑料制品。
在注塑件成型过程中,工艺参数的优化设计对于产品质量的提高和生产效率的提升具有至关重要的作用。
本文将介绍一种基于正交试验法的注塑件成型工艺参数优化设计方法。
正交试验法的概述正交试验法是一种在多因素影响下进行试验的方法,通过选择一组经过科学设计的试验方案,可以在尽量少的试验次数内获取最全面的试验数据。
该方法能够通过独立变量的选择、合理的试验方案和统计分析的方法,确定各个因素对结果的影响程度以及相互之间的关系。
正交试验法在注塑件成型工艺参数优化设计中的应用在注塑件成型过程中,有许多因素会影响最终产品的质量,如注塑温度、注射速度、保压时间等。
通过正交试验法,可以确定这些因素的最佳设置,以获得最佳的注塑件成型工艺参数。
步骤一:确定影响因素首先,我们需要确定影响注塑件成型的各个因素。
基于经验和相关文献,我们可以列出一些可能的影响因素,如注塑温度、注射速度、保压时间、模具温度等。
步骤二:选择试验水平在进行正交试验之前,我们需要确定每个因素的试验水平。
试验水平的选择应该满足设计要求并尽可能简化试验过程。
一般来说,我们可以选择每个因素的三个水平进行试验。
步骤三:设计试验方案基于已确定的因素和试验水平,我们可以使用正交试验表设计试验方案。
通过正交试验表的选择,我们可以避免冗余试验和测试过程的复杂性。
步骤四:进行实验根据设计的试验方案,我们可以开始进行实验。
在每个试验点上,我们需要记录各个因素的设置和相应的试验数据。
通过多次试验,我们可以获得一系列试验数据,进一步分析每个因素的影响。
步骤五:数据分析通过对实验数据的分析,我们可以得到不同因素之间的相对重要性和相互之间的关系。
常用的数据分析方法包括方差分析、回归分析等。
通过这些分析方法,可以确定最佳的注塑件成型工艺参数。
结论基于正交试验法的注塑件成型工艺参数优化设计方法能够帮助我们快速、有效地确定最佳的工艺参数。
注塑模具结构及设计-9设计实例改善及细节改进
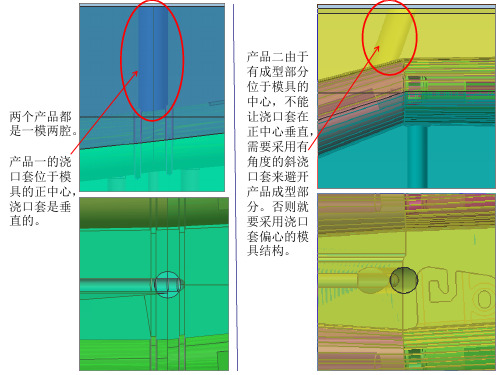
单独的垃圾钉
垃圾钉的位置要考虑顶出板和底板上的各零部件的情况,尽量做到均匀布置,受力平衡。
普通的浇口套的料把经常有拉丝的现象,可以在浇口套的中间加上 一个金属隔片来做成防拉丝的浇口套。
普通的浇口套
防拉丝的浇口套
防拉丝浇口套中间有镶件槽
金属隔片
锁模块
锁模块用在动,定模之间,可以锁紧动, 定模,防止吊装时模具分开产生事故。 通常在模具上是对称布置的。
由于两个滑块的抽芯 距都比较长,当两抽 芯合拢时头部容易产 生错位。
预防措施: 在两个抽 芯的头部 加上锥度 的定位。
两抽芯合拢时因 为有定位的作用, 可以防止错位。
因为有油缸, 所以模具必 须加上长支 腿才能平稳 放置。
支腿的固定 形式采用右 图时,模具 在翻转时螺 钉容易断裂。
支腿的固定 形式改为镶 入式后,模 具在翻转时 产生的剪切 力由镶入部 分承受,螺 钉不容易断 裂。
Z钩形
环槽形
倒锥形
对于型芯的碰穿面要留研配的余量, 尺寸应该标注正公差。
产品
型芯
正公差加在红 色的碰穿面上
从加工方面考虑,顶杆的布置遇到镶拼结构时,一般不允许顶杆 跨越镶拼线,如图1所示。扁顶杆、方顶设计在镶块中间时,成型 制品部分一般要在镶块的一侧。不得跨越两个镶块,如图2所示。
跨越镶拼线不允许
承压片
在模具的动,定模板之间,加上承压片 可以在研配时通过调整承压片的厚度方 便的调整动,定模板之间的间隙和分型 面上所受合模力的大小。 模板上开框
增加承压片
单独的承压片立体图
定模
动模 承压片
单独的带肩螺栓立体图 复位弹簧
带肩螺栓 带肩螺栓用在顶出板上时, 可以利用螺纹部分的拧入 来克服弹簧的预压缩力从 而方便拆装顶出板。
注塑模具设计和制造操作流程

注塑模具设计和制造操作流程注塑模具是在工业生产中广泛应用的一种工具,它用于制造各种形状的塑料零件。
在注塑模具设计和制造的操作流程中,需要经历多个步骤和环节,以确保最终的产品符合要求。
本文将详细介绍注塑模具设计和制造的操作流程。
1. 需求分析在开始注塑模具设计和制造之前,首先需要进行需求分析。
这包括与客户的沟通和了解客户对产品的要求。
在需求分析阶段,需要明确产品的尺寸、材料、颜色等方面的要求,以及产品将用途和预期使用寿命。
这些要求将为后续的模具设计和制造提供指导。
2. 设计草图在需求分析完成后,设计师将根据客户的要求和产品的特点绘制设计草图。
设计草图应准确反映产品的形状、结构和尺寸,并考虑到注塑成型的特点和要求。
在设计草图中,设计师通常会标注模具的尺寸、孔洞位置和活动部件的设计等重要信息。
3. 三维建模基于设计草图,设计师使用计算机辅助设计(CAD)软件进行三维建模。
三维建模可以更加直观地显示产品的形状和结构,同时可以进行尺寸调整和碰撞检测等操作。
设计师需要熟练掌握CAD软件的使用,以实现精确的模具设计。
4. 模具加工在完成三维建模后,进入模具加工环节。
模具加工通常包括数控加工、车铣加工、电火花加工等多个工艺。
根据设计要求,将选用合适的材料,并进行精密加工,以确保模具的尺寸和质量符合要求。
模具加工需要经验丰富的技术人员和高精度的加工设备的支持。
5. 组件装配模具加工完成后,需要进行各个零部件的组装。
这包括模具的固定板、活动板、导柱、导套、顶针等部件的安装和调试。
组装过程需要严格按照设计要求进行,以确保模具的运行和操作的顺畅性。
6. 试模和调试模具组装完成后,进行试模和调试。
在试模过程中,将注入塑料材料,并观察成型情况,如产品的尺寸、表面质量等。
如果发现问题,需要进行相应的调整和修正,以使产品达到客户的要求。
试模和调试过程可能需要多次重复,直到达到符合要求的效果为止。
7. 批量生产完成试模和调试后,模具可以投入批量生产。
注塑模具结构及设计-4(成型零部件)

2)使型腔深度最浅 模具型腔深度的大小对模具结构与制造有如下三方面的影响: a)目前模具型腔的加工多采用电火花成型加工,型腔越深加工时间越 长,影响模具生产周期,同时增加生产成本。 b)模具型腔深度影响着模具的厚度。型腔越深,动、定模越厚。一方 面加工比较困难;另一方面各种注射机对模具的最大厚度都有一定的 限制,故型腔深度不宜过大。 c)型腔深度越深,在相同起模斜度时,同一尺寸上下两端实际 尺寸差值越大。若要控制规定的尺寸公差,就要减小脱模斜度, 可能导致塑件脱模困难。因此在选择分型面时应尽可能使型腔 深度最浅。
5)有侧向抽芯的分型,选择分型面时,参考下述原则: a)将侧型芯尽量设在动模上,便于抽芯,而若设在定模上,则抽芯较难, 模具结构会复杂。
b)将抽芯距离长的放在开模方向, 而将抽芯距离小的放在侧向,较为 合理。抽芯距越短,斜滑块移动的 距离和斜导柱长度就越短,可以缩 小模具的尺寸。也能减少塑件尺寸 误差和有利于脱模。如图6塑件中有 两个垂直的孔,把抽芯距离小的小 孔安排在侧向抽芯上就比把抽芯距 离大的大孔安排在侧向抽芯上合理。
模具成型部分的尺寸计算设计主要考虑便于调整和修改模具的尺寸, 保证产品的尺寸变化在公差的可控制范围内。 1,在成型部件上加脱模斜度时,凹模以大端为准,斜向小端; 凸模以小端为准,斜向大端。这样方便模具的修整。
不带脱模斜度的型腔尺寸
加脱模斜度后的型腔尺寸
2,型腔的尺寸必需考虑塑料的收缩率,要把塑料的收缩尺寸加进去。
4)尽量避免侧向抽芯
图3 分型面位置的选择
塑料注射模具,应尽可能避免采用侧向抽芯,因 为侧向抽芯模具结构复杂,并且直接影响塑件尺 寸、配合的精度,且耗时耗财,制造成本显著增 加,故在万不得己的情况下才能使用。如图4中 Ⅲ-Ⅲ、Ⅳ-Ⅳ分型面需要侧向抽芯,而选择Ⅰ-Ⅰ、 Ⅱ-Ⅱ分型面可以避免侧向抽芯。
- 1、下载文档前请自行甄别文档内容的完整性,平台不提供额外的编辑、内容补充、找答案等附加服务。
- 2、"仅部分预览"的文档,不可在线预览部分如存在完整性等问题,可反馈申请退款(可完整预览的文档不适用该条件!)。
- 3、如文档侵犯您的权益,请联系客服反馈,我们会尽快为您处理(人工客服工作时间:9:00-18:30)。
Flow Lines, Metal Flake Orientation
•
This section of metallic molded-in-color rocker molding show appearance defects caused by flow lines and metal flake alignments formed around the attaching hole pins.
Molding Issues and Common Defects
Mold Expansion / Part Shrinkage
• Thermoplastics shrink as they cool and solidify during the molding process and after part ejection. • The mold cavity is machined larger than the final desired part size in order to compensate for part shrinkage as the part cools. • Mold shrinkage data for the specific plastic material can be used to calculate the amount of mold expansion needed. • Mold shrinkage units are expressed as length-per unitlength, or as a percentage, and is calculated using the following formula:
Injection Molding Press
The injection molding press operation includes a means to: Open and close and clamp the injection mold. Measure, melt, and inject the plastic resin. Cool the molten plastic in the mold. Eject the finished part from the mold. Computer control system.
Core with lifter
Cavity
Design Terminology
Part and Tool Design Terminology
Part and Tool Design Terminology
• • • • • • •
- Die Angles & Draft Angles, 拔模角 - A Surface, B Surface, etc. A 面, B 面 - Parting Lines, Lifter Lines, 分模线 - Doghouses, Ribs, Flanges 安装支座,加强筋,翻边 - True Holes, Molded Holes, 注塑孔 - Tooling Considerations, 注塑模考虑 ....
Traveling Angled Lifter
Forms rib with flange
*Actually, the cavity is stationary, and the core side moves to open the tool when mounted in the molding machine.
Hot Runner Manifold & Multiple Valve Gates
The manifold in a large mold heats and delivers the hot plastic from the molding machine to the gate locations on the part.
Injection Mold Components
• • • • • • • • •
Cavity Core Clamp Plates Ejector Plate & Pins Lifters Slides Water Lines Gates and Sprues Hot Runner System, etc
Injection Molding and Design 注塑成型与设计
• Injection Molding Process Overview • Part and Tool Design Terminology
• Common Molding Defects
• Molded Part Design Best Practices
We generally use minimum 3 degrees draft per side.
More draft is needed for grained surfaces.
Cavity 'A' surface vs. Core 'B' surface
Do you know the difference? Does your supplier and tool shop? Did you indicate it clearly in your math data file?
Revised Part, eliminate pins on A surface
Oops! Original Part, tooled wrong, core/cavity. Ejection pins on show surface (A surface).
Molding Issues and Common Defects
Injection Molding Process Overview
Injection Molding Process ew
• Injection molding is used to produce most of our complex plastic parts. • Injection molding is a process which involves forcing molten plastic into a machined mold cavity under high pressure.
Core With Slide
Cavity With Horn Pin
Cavity and Core with Lifter and Pin
Cam Operated Core Pin
Forms hole in flange
Cam
Plastic Part
Ejection Pin
Injection Sprue
Die Angle & Parting Line
Cavity
Part (2 cavity) Die Angle (Die Vector) Mold opening direction Parting Line – where the core, cavity, and part meet together. Core
Draft Angles
Parts must have open draft angles in the part geometry design. Part draft angle is measured relative to the die opening angle. If there is no draft angle, the part will cool and shrink onto the tool and will be difficult or impossible to remove without damage.
(mold dimension – part size) / mold dimension = Shrink Factor
Molding Issues and Common Defects
• Dimensional Size Errors (too long, too short, too thin, too thick, etc.) • Dimensional Warpage, Distortion, & Stress • Sink & Shrink Marks • Lifter Line Read-Through • Flow Lines, Weld (Knit) Lines • Metallic Flake Orientation • Porosity • Non-isotropic Behavior (different behavior in different directions)
Flow Line & Metal Flake Orientation
Gate
Flow Obstruction
Weld Lines (Knit Lines)
Weld (knit) lines are appearance and structural defects which are formed when the molten plastic must divide to go around an obstruction and then rejoin itself. We often find this problem on doghouses and also at attaching holes near a part edge.
Injection Mold
• The injection mold forms both the show (A) side and the back (B) side of the part. • The show side of the part is generally the cavity side of the tool, and the back side is the core side. • The interface between the cavity and core is the parting line. • The number of cavities is the number of parts produced per cycle.