AOI自动光学检测
一分钟了解自动光学检测(AOI)技术
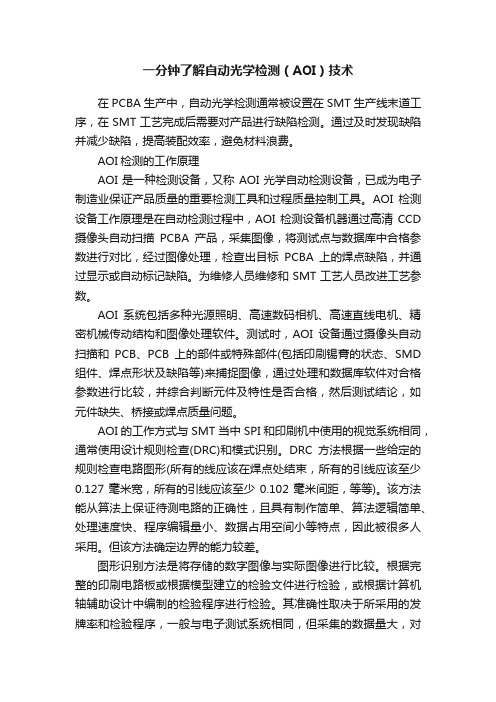
一分钟了解自动光学检测(AOI)技术在PCBA生产中,自动光学检测通常被设置在SMT生产线末道工序,在SMT工艺完成后需要对产品进行缺陷检测。
通过及时发现缺陷并减少缺陷,提高装配效率,避免材料浪费。
AOI检测的工作原理AOI是一种检测设备,又称AOI光学自动检测设备,已成为电子制造业保证产品质量的重要检测工具和过程质量控制工具。
AOI检测设备工作原理是在自动检测过程中,AOI检测设备机器通过高清CCD 摄像头自动扫描PCBA产品,采集图像,将测试点与数据库中合格参数进行对比,经过图像处理,检查出目标PCBA上的焊点缺陷,并通过显示或自动标记缺陷。
为维修人员维修和SMT工艺人员改进工艺参数。
AOI系统包括多种光源照明、高速数码相机、高速直线电机、精密机械传动结构和图像处理软件。
测试时,AOI设备通过摄像头自动扫描和PCB、PCB上的部件或特殊部件(包括印刷锡膏的状态、SMD 组件、焊点形状及缺陷等)来捕捉图像,通过处理和数据库软件对合格参数进行比较,并综合判断元件及特性是否合格,然后测试结论,如元件缺失、桥接或焊点质量问题。
AOI的工作方式与SMT当中SPI和印刷机中使用的视觉系统相同,通常使用设计规则检查(DRC)和模式识别。
DRC方法根据一些给定的规则检查电路图形(所有的线应该在焊点处结束,所有的引线应该至少0.127毫米宽,所有的引线应该至少0.102毫米间距,等等)。
该方法能从算法上保证待测电路的正确性,且具有制作简单、算法逻辑简单、处理速度快、程序编辑量小、数据占用空间小等特点,因此被很多人采用。
但该方法确定边界的能力较差。
图形识别方法是将存储的数字图像与实际图像进行比较。
根据完整的印刷电路板或根据模型建立的检验文件进行检验,或根据计算机轴辅助设计中编制的检验程序进行检验。
其准确性取决于所采用的发牌率和检验程序,一般与电子测试系统相同,但采集的数据量大,对数据的实时处理要求较高。
模式识别方法利用实际设计数据代替DRC 中已建立的设计原则,具有明显的优势。
aoi检测步骤
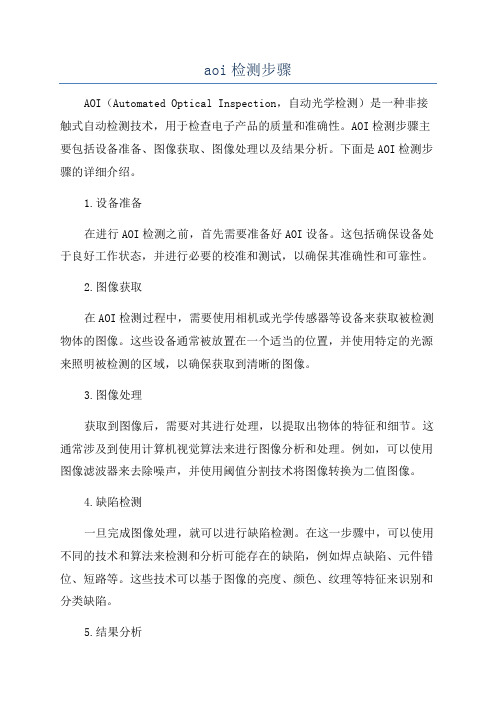
aoi检测步骤AOI(Automated Optical Inspection,自动光学检测)是一种非接触式自动检测技术,用于检查电子产品的质量和准确性。
AOI检测步骤主要包括设备准备、图像获取、图像处理以及结果分析。
下面是AOI检测步骤的详细介绍。
1.设备准备在进行AOI检测之前,首先需要准备好AOI设备。
这包括确保设备处于良好工作状态,并进行必要的校准和测试,以确保其准确性和可靠性。
2.图像获取在AOI检测过程中,需要使用相机或光学传感器等设备来获取被检测物体的图像。
这些设备通常被放置在一个适当的位置,并使用特定的光源来照明被检测的区域,以确保获取到清晰的图像。
3.图像处理获取到图像后,需要对其进行处理,以提取出物体的特征和细节。
这通常涉及到使用计算机视觉算法来进行图像分析和处理。
例如,可以使用图像滤波器来去除噪声,并使用阈值分割技术将图像转换为二值图像。
4.缺陷检测一旦完成图像处理,就可以进行缺陷检测。
在这一步骤中,可以使用不同的技术和算法来检测和分析可能存在的缺陷,例如焊点缺陷、元件错位、短路等。
这些技术可以基于图像的亮度、颜色、纹理等特征来识别和分类缺陷。
5.结果分析最后一步是对检测结果进行分析和评估。
根据检测到的缺陷数量和类型,可以判断被检测物体是否合格。
通常会将检测结果显示在计算机屏幕上或以报告的形式输出。
此外,还可以将结果与预先设定的标准或要求进行比较,以确定产品是否符合要求。
总结起来,AOI检测步骤包括设备准备、图像获取、图像处理以及结果分析。
通过这些步骤,可以快速准确地检测电子产品的质量和准确性,提高生产效率,降低人为错误的风险。
不过,值得注意的是,不同的产品和应用可能需要不同的参数和算法来进行检测,因此在实际应用中需要进行一定的定制和调整。
aoi自动光学检测机工作原理

AOI自动光学检测机工作原理AOI(Automatic Optical Inspection)自动光学检测机是一种采用自动光学检测技术,用于对电子元器件、印刷电路板(PCB)等进行缺陷检测的设备。
它可以在制造过程中实时检测产品的质量,帮助提高生产效率和产品质量。
本文将详细介绍AOI自动光学检测机的工作原理。
1. AOI自动光学检测机的组成AOI自动光学检测机通常由以下几个主要部分组成:1.光源:提供光照条件,使被测物体可以清晰地被相机拍摄到。
2.相机:用于拍摄被测物体的图像,并将图像转化为数字信号。
3.图像处理系统:接收相机传输的图像信号,进行图像处理,如增强图像对比度、降噪等。
4.缺陷检测算法:对处理后的图像进行缺陷检测和分析,通常使用特定的图像处理算法和机器学习技术。
5.控制系统:控制整个系统的运行和参数设置,并对检测结果进行处理和分析。
6.传送系统:将待检测的产品传送到检测区域,如传送带、机械臂等。
2. AOI自动光学检测机的工作流程AOI自动光学检测机的工作流程通常包括以下几个步骤:1.产品传送:待检测的产品通过传送系统进入检测区域。
2.光源照射:光源照射被测物体,为相机拍摄提供足够的光照条件。
3.图像采集:相机对被测物体进行拍摄,得到一张或多张图像,并将图像转化为数字信号。
4.图像处理:图像处理系统对相机采集到的图像进行预处理,如增强对比度、降噪等,以提高后续缺陷检测的准确性。
5.缺陷检测:采用缺陷检测算法对处理后的图像进行缺陷检测和分析。
检测算法通常包括形状分析、颜色分析、边缘检测等。
6.检测结果分析:根据检测算法的结果,判断被测物体是否存在缺陷,如脏污、划痕、错位等。
7.控制与处理:控制系统根据检测结果进行判定,对有缺陷的产品进行处理,如剔除、标记等。
8.数据记录与分析:检测系统可以将每次检测的结果进行记录,并进行统计和分析,以便制定后续的生产改进方案。
3. AOI自动光学检测机的基本原理AOI自动光学检测机的基本原理是通过光学技术对被测物体进行图像采集和处理,再结合缺陷检测算法,判断是否存在缺陷。
自动光学检查(AOI)
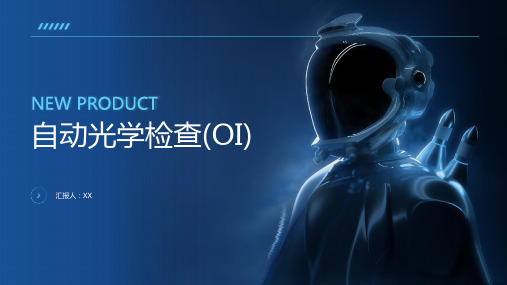
技术进步:更高精度、更快速 度、更智能的OI设备
应用领域:拓展到更多行业, 如半导体、电子、汽车等
市场竞争:国内外企业竞争加 剧,推动技术升级和创新
环保要求:满足绿色制造和可 持续发展的要求,降低能耗和 污染
感谢您的观看
汇报人:XX
OI可以大大提高生产效率,减少人 工检查的错误率。
添加标题
添加标题
添加标题
添加标题
OI主要用于检测电子产品的表面缺 陷、焊点质量、元件放置等。
OI广泛应用于电子制造行业,如 PCB、SMT等领域。
自动光学检查 (OI)是一种 通过光学手段 对电子元件进 行自动检查的
技术。
OI系统通常包 括一个摄像头, 一个光源和一 个图像处理系
统。
工作原理:摄像 头拍摄电子元件 的图像,光源提 供均匀的照明, 图像处理系统分 析图像,检测出
缺陷和异常。
OI的优点:速 度快,准确度 高,可以检测 出人工检查难 以发现的缺陷。
电子行业:用于检测电路板、半导 体等电子元件的缺陷和故障
航空航天行业:用于检测机、卫 星等航空航天设备的缺陷和故障
准备阶段:确定检测目标和标准, 准备检测设备和工具
分析阶段:对检测数据进行分析和 处理,找出存在的问题和缺陷
添加标题
添加标题
添加标题
添加标题
检测阶段:按照预定的流程和标准 进行检测,获取检测数据
报告阶段:将检测结果和分析结果 整理成报告,提供给相关人员和部 门
检测结果分为合格和不合格两种
不合格结果表示产品不符合标准要 求,需要返修或报废
添加标题
添加标题
添加标题
添加标题
合格结果表示产品符合标准要求, 可以继续生产
AOI检测机及检测方法
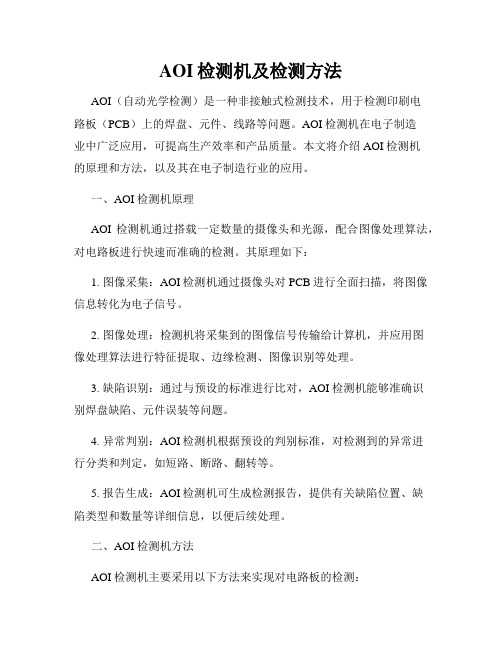
AOI检测机及检测方法AOI(自动光学检测)是一种非接触式检测技术,用于检测印刷电路板(PCB)上的焊盘、元件、线路等问题。
AOI检测机在电子制造业中广泛应用,可提高生产效率和产品质量。
本文将介绍AOI检测机的原理和方法,以及其在电子制造行业的应用。
一、AOI检测机原理AOI检测机通过搭载一定数量的摄像头和光源,配合图像处理算法,对电路板进行快速而准确的检测。
其原理如下:1. 图像采集:AOI检测机通过摄像头对PCB进行全面扫描,将图像信息转化为电子信号。
2. 图像处理:检测机将采集到的图像信号传输给计算机,并应用图像处理算法进行特征提取、边缘检测、图像识别等处理。
3. 缺陷识别:通过与预设的标准进行比对,AOI检测机能够准确识别焊盘缺陷、元件误装等问题。
4. 异常判别:AOI检测机根据预设的判别标准,对检测到的异常进行分类和判定,如短路、断路、翻转等。
5. 报告生成:AOI检测机可生成检测报告,提供有关缺陷位置、缺陷类型和数量等详细信息,以便后续处理。
二、AOI检测机方法AOI检测机主要采用以下方法来实现对电路板的检测:1. 外观检测:AOI检测机能够检测焊盘的缺失、损坏、氧化、短路等问题,以及元件的位置偏移、误装、缺陷等。
2. 高精度定位:通过像素级别的图像处理算法,AOI检测机能够精确定位焊盘和元件的位置,以及线路的走向。
3. 缺陷检测:AOI检测机可针对常见的电路板缺陷,如误焊、漏焊、短路等,进行智能化检测和判定。
4. 通信检测:AOI检测机可以通过通信接口与上位系统进行数据传输,实现实时监控和远程配置。
5. 大数据分析:AOI检测机可将检测结果和数据与其他生产数据进行关联分析,为制造商提供数据决策支持。
三、AOI检测机在电子制造业的应用AOI检测机在电子制造业中得到了广泛的应用,主要体现在以下几个方面:1. 提高产品质量:AOI检测机能够快速、准确地检测电路板上的缺陷和问题,提高产品质量和可靠性。
PCB线路自动光学检查AOI原理介绍
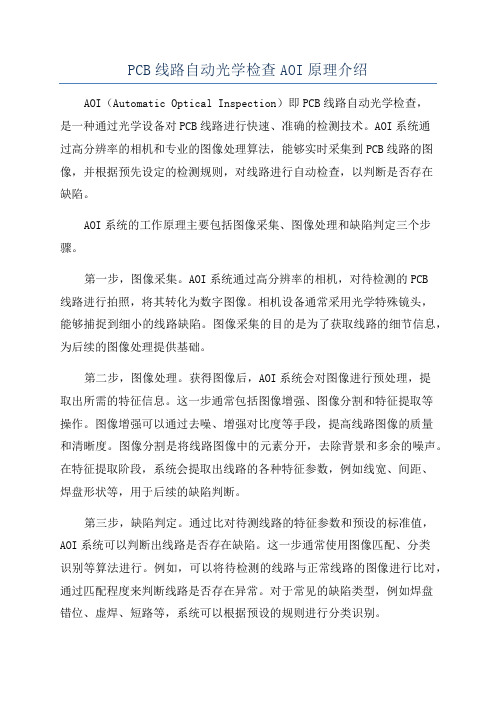
PCB线路自动光学检查AOI原理介绍AOI(Automatic Optical Inspection)即PCB线路自动光学检查,是一种通过光学设备对PCB线路进行快速、准确的检测技术。
AOI系统通过高分辨率的相机和专业的图像处理算法,能够实时采集到PCB线路的图像,并根据预先设定的检测规则,对线路进行自动检查,以判断是否存在缺陷。
AOI系统的工作原理主要包括图像采集、图像处理和缺陷判定三个步骤。
第一步,图像采集。
AOI系统通过高分辨率的相机,对待检测的PCB线路进行拍照,将其转化为数字图像。
相机设备通常采用光学特殊镜头,能够捕捉到细小的线路缺陷。
图像采集的目的是为了获取线路的细节信息,为后续的图像处理提供基础。
第二步,图像处理。
获得图像后,AOI系统会对图像进行预处理,提取出所需的特征信息。
这一步通常包括图像增强、图像分割和特征提取等操作。
图像增强可以通过去噪、增强对比度等手段,提高线路图像的质量和清晰度。
图像分割是将线路图像中的元素分开,去除背景和多余的噪声。
在特征提取阶段,系统会提取出线路的各种特征参数,例如线宽、间距、焊盘形状等,用于后续的缺陷判断。
第三步,缺陷判定。
通过比对待测线路的特征参数和预设的标准值,AOI系统可以判断出线路是否存在缺陷。
这一步通常使用图像匹配、分类识别等算法进行。
例如,可以将待检测的线路与正常线路的图像进行比对,通过匹配程度来判断线路是否存在异常。
对于常见的缺陷类型,例如焊盘错位、虚焊、短路等,系统可以根据预设的规则进行分类识别。
AOI系统的优点是速度快、准确度高和自动化程度高。
相比传统的人工检查方法,AOI系统可以大大提高检查的效率和准确度。
而且由于其全自动化的特点,可以适用于大批量生产,并能够检测到人眼难以察觉的线路缺陷。
不过,AOI系统也存在一些局限性。
例如,对于非透明的线路或者多层线路的检测,可能会受到光照条件等因素的限制。
此外,AOI系统也无法检测到一些隐蔽的缺陷,例如线路的电性能或者可靠性等方面的问题,需要借助其他测试方法进行检测。
aoi检测原理
aoi检测原理
AOI(自动光学检测)是一种利用光学设备进行电子元件、印
刷电路板(PCB)和其他光学组装的自动检测技术。
其主要原理是通过摄像仪和光源对待检测物体表面进行扫描,然后通过计算机算法对采集到的图像进行分析和处理,从而实现快速、高精度的检测。
AOI检测主要包括以下步骤:
1. 目标定位:通过电脑辅助设计(CAD)数据或已知的特征,确定待检测物体的位置和方向。
这可以通过在AOI系统中预
先加载CAD数据或使用计算机视觉算法(如边缘检测、阈值
处理等)来实现。
2. 光学扫描:使用高分辨率的摄像仪和恰当的光源对待检测物体进行扫描。
光源的选择根据被检测物体的表面特性和缺陷类型而定。
扫描可以是单向的,也可以是多方向的,以确保对整个物体表面的覆盖。
3. 图像采集:摄像仪将扫描到的图像传输到计算机中进行采集和存储。
为了提高检测效果,图像采集的速度和分辨率需要根据被检测物体的特性进行优化。
4. 图像分析与缺陷检测:采集到的图像通过计算机视觉算法进行分析。
这些算法可以包括边缘检测、图像过滤、颜色分析、形状匹配等。
通过设定合适的阈值和规则,算法可以检测出图像中的缺陷,如焊点缺失、焊盘变形、元件位置偏移等。
5. 缺陷分类和报警:检测到的缺陷根据其类型和严重程度进行分类,并根据预设的标准判定是否报警。
报警通常以声音、光信号或计算机界面的形式呈现,以便操作人员能够及时采取措施修复缺陷,并确保产品质量。
总之,AOI检测利用光学设备和计算机视觉算法实现对待检测物体进行快速、精确的缺陷检测,广泛应用于电子制造、PCB 生产、半导体等行业中。
AOI光学自动检测技术基本原理与设备构成
AOI光学自动检测技术基本原理与设备构成AOI(Automated Optical Inspection)光学自动检测技术是一种通过光学设备对电子产品表面进行快速高效的检测和检查的技术。
其基本原理是通过光学成像和图像处理技术,对待测物体的表面图像进行采集、分析和比对,从而检测出表面缺陷、错误贴装、焊接质量等问题。
1.光源系统:光源系统是AOI设备的核心部分,用于提供光源来照明待测物体。
常见的光源有LED光源和激光光源。
LED光源发出的光线均匀、稳定,适用于大面积的表面检测;而激光光源则具有较高的光斑亮度和聚焦能力,适用于小尺寸物体的检测。
2.图像采集系统:图像采集系统使用摄像机或CCD等设备来采集待测物体的图像。
采集到的图像需要具有较高的分辨率、色彩还原度和鲁棒性,以确保后续图像处理的准确性和稳定性。
3.图像处理系统:图像处理系统对采集到的图像进行处理,提取出关键信息并进行分析。
常见的图像处理算法包括图像滤波、边缘检测、图像增强和特征提取等。
这些算法可以帮助检测系统识别表面缺陷、贴装错误等。
4.比对系统:比对系统是AOI检测的关键部分,用于将采集到的图像与标准图像或数据库中储存的模板进行比对。
通过比对,可以检测出待测物体的与标准不符之处,如缺陷、偏移、错位等。
5.控制系统:控制系统对整个AOI设备进行控制和调整。
它可以控制光源的亮度和方向、摄像机的曝光时间和位置等参数,以保证检测的准确性和稳定性。
同时,控制系统也可以收集和处理采集到的图像数据,并进行结果的展示和分析。
总结起来,AOI光学自动检测技术基于光学成像和图像处理技术,通过光源系统提供照明,图像采集系统采集图像,图像处理系统进行处理,比对系统进行比对,控制系统实现整个检测过程的自动化控制。
这样的设备构成有效地实现了电子产品表面缺陷和错误贴装等问题的自动检测和检查。
aoi自动光学检测机工作原理
aoi自动光学检测机工作原理AOI自动光学检测机是一种高精度、高效率的检测设备,广泛应用于电子、半导体、汽车等行业中。
其工作原理是通过光学成像技术和图像处理算法,对印刷电路板(PCB)、芯片等进行非接触式的自动检测。
一、 AOI自动光学检测机的基本构成AOI自动光学检测机主要由以下几个部分组成:1. 光源系统:提供光源,照亮被测试物体。
2. 成像系统:将被测试物体的图像转换为数字信号。
3. 图像处理系统:对数字信号进行处理和分析,提取出需要的信息。
4. 控制系统:控制整个设备的运行。
5. 传输系统:将被测试物体从一个位置传输到另一个位置。
二、 AOI自动光学检测机的工作流程AOI自动光学检测机的工作流程如下:1. 准备工作:在测试前需要对设备进行预热和校准,确保设备正常运行。
2. 加载PCB或芯片:将待测试的PCB或芯片放置于传输带上,并通过传输带将其送入设备内部。
3. 光源照射:在进入成像系统前,被测试物体会先经过光源系统的照射,使其表面得到充分的照明。
4. 成像:被测试物体经过光源照射后,进入成像系统。
成像系统利用透镜、CCD等元件将被测试物体的图像转换为数字信号,并传送到图像处理系统中。
5. 图像处理:图像处理系统对数字信号进行处理和分析,提取出需要的信息。
这些信息可能包括线路连接情况、元器件位置、焊点质量等。
6. 判定:根据预设的检测标准和算法,对提取出来的信息进行判定。
如果检测结果符合要求,则将其发送到下一步操作;否则将其标记为不良品并发送到设备外部进行处理。
7. 卸载PCB或芯片:检测完成后,将PCB或芯片从传输带上卸载,并送至下一步操作或退出设备。
三、 AOI自动光学检测机的优势1. 高精度:AOI自动光学检测机采用高精度成像技术和图像处理算法,能够对PCB、芯片等进行高精度、高速度的自动检测。
2. 高效率:AOI自动光学检测机能够实现非接触式的自动检测,避免了传统手工检测的繁琐和低效率。
AOI作业指导书 (2)
AOI作业指导书一、概述AOI(Automated Optical Inspection)自动光学检测是一种利用光学技术对印刷电路板(PCB)进行自动检测的方法。
本作业指导书旨在提供详细的操作步骤和注意事项,以确保在进行AOI作业时能够准确、高效地完成检测任务。
二、设备准备1. AOI设备:确保AOI设备处于正常工作状态,连接电源和数据线。
2. 检测样品:准备待检测的PCB样品,确保其完整无损。
3. 操作系统:确保AOI设备上的操作系统已经正确安装并更新至最新版本。
三、操作步骤1. 打开AOI设备:按下电源按钮,启动AOI设备,确保屏幕显示正常。
2. 登录系统:根据设备要求,输入用户名和密码,登录到AOI系统界面。
3. 创建新任务:点击界面上的“新建任务”按钮,进入任务创建页面。
4. 输入任务信息:根据实际需求,填写任务名称、任务描述等相关信息,并选择待检测的PCB样品。
5. 配置检测参数:根据PCB的特性和检测要求,设置合适的检测参数,包括光源亮度、暴光时间、分辨率等。
6. 调整视觉系统:根据PCB的尺寸和布局,调整视觉系统的位置和焦距,确保能够全面、清晰地检测整个PCB表面。
7. 开始检测:点击界面上的“开始检测”按钮,AOI设备将开始自动检测PCB样品。
8. 检测结果分析:等待检测完成后,系统将自动生成检测结果报告。
根据报告中的缺陷信息,分析并判断是否存在问题。
9. 问题处理:根据检测结果报告,对于存在的缺陷进行分类和处理,可以选择修复、返工或者报废。
10. 完成任务:根据实际情况,点击界面上的“完成任务”按钮,将任务标记为已完成。
四、注意事项1. 操作规范:在进行AOI作业时,操作人员应遵守相关的操作规范,确保操作的准确性和稳定性。
2. 设备维护:定期对AOI设备进行维护保养,包括清洁光源、调整视觉系统、检查电源和数据线等,以确保设备的正常工作。
3. 校准检测参数:根据实际需求,定期校准检测参数,以保证检测的准确性和可靠性。
- 1、下载文档前请自行甄别文档内容的完整性,平台不提供额外的编辑、内容补充、找答案等附加服务。
- 2、"仅部分预览"的文档,不可在线预览部分如存在完整性等问题,可反馈申请退款(可完整预览的文档不适用该条件!)。
- 3、如文档侵犯您的权益,请联系客服反馈,我们会尽快为您处理(人工客服工作时间:9:00-18:30)。
AOI的全称是Automatic Optic Inspection(自动光学检测),是基于光学原理来对焊接生产中遇到的常见缺陷进行检测的设备。
AOI是近几年才兴起的一种新型测试技术,但发展迅速,目前很多厂家都推出了AOI测试设备。
当自动检测时,机器通过摄像头自动扫描PCB,采集图像,测试的焊点与数据库中的合格的参数进行比较,经过图像处理,检查出PCB上缺陷,并通过显示器或自动标志把缺陷显示/标示出来,供维修人员修整。
编辑摘要目录1 什么是AOI2 什么是AOI测试技术3 AOI的主要目标4 针对AOI检查的PCB优化设计5 新一代自动光学检测技术(AOI):内嵌式检测技术自动光学检查(AOI, Automated Optical Inspection)一、定义运用高速高精度视觉处理技术自动检测PCB板上各种不同帖装错误及焊接缺陷.PCB板的范围可从细间距高密度板到低密度大尺寸板,并可提供在线检测方案,以提高生产效率,及焊接质量 .通过使用AOI作为减少缺陷的工具,在装配工艺过程的早期查找和消除错误,以实现良好的过程控制.早期发现缺陷将避免将坏板送到随后的装配阶段,AOI将减少修理成本将避免报废不可修理的电路板.二、主要特点1)高速检测系统与PCB板帖装密度无关2)快速便捷的编程系统- 图形界面下进行-运用帖装数据自动进行数据检测-运用元件数据库进行检测数据的快速编辑3)运用丰富的专用多功能检测算法和二元或灰度水平光学成像处理技术进行检测4)根据被检测元件位置的瞬间变化进行检测窗口的自动化校正,达到高精度检测5)通过用墨水直接标记于PCB板上或在操作显示器上用图形错误表示来进行检测电的核对三、AOI 检查与人工检查的比较人工检查AOI检查pcb<18*20及千个pad以下人重要辅助检查时间正常正常持续性因人而异好可靠性因人而异较好准确性因人而异误点率高pcb<18*20及千个pad以上人重要辅助检查时间长短持续性差好可靠性差较好准确性因人而异误点率高AOI是近几年才兴起的一种新型测试技术,但发展较为迅速,目前很多厂家都推出了AOI测试设备。
当自动检测时,机器通过摄像头自动扫描PC B,采集图像,测试的焊点与数据库中的合格的参数进行比较,经过图像处理,检查出PCB上缺陷,并通过显示器或自动标志把缺陷显示/标示出来,供维修人员修整。
1、实施目标:实施AOI有以下两类主要的目标:(1)最终品质(End quality)。
对产品走下生产线时的最终状态进行监控。
当生产问题非常清楚、产品混合度高、数量和速度为关键因素的时候,优先采用这个目标。
AOI通常放置在生产线最末端。
在这个位置,设备可以产生范围广泛的过程控制信息。
(2)过程跟踪(Process tracking)。
使用检查设备来监视生产过程。
典型地包括详细的缺陷分类和元件贴放偏移信息。
当产品可靠性很重要、低混合度的大批量制造、和元件供应稳定时,制造商优先采用这个目标。
这经常要求把检查设备放置到生产线上的几个位置,在线地监控具体生产状况,并为生产工艺的调整提供必要的依据。
2、放置位置虽然AOI可用于生产线上的多个位置,各个位置可检测特殊缺陷,但AOI检查设备应放到一个可以尽早识别和改正最多缺陷的位置。
有三个检查位置是主要的:(1)锡膏印刷之后。
如果锡膏印刷过程满足要求,那么ICT发现的缺陷数量可大幅度的减少。
典型的印刷缺陷包括以下几点:A.焊盘上焊锡不足。
B.焊盘上焊锡过多。
C.焊锡对焊盘的重合不良。
D.焊盘之间的焊锡桥。
在ICT上,相对这些情况的缺陷概率直接与情况的严重性成比例。
轻微的少锡很少导致缺陷,而严重的情况,如根本无锡,几乎总是在ICT造成缺陷。
焊锡不足可能是元件丢失或焊点开路的一个原因。
尽管如此,决定哪里放置AOI需要认识到元件丢失可能是其它原因下发生的,这些原因必须放在检查计划内。
这个位置的检查最直接地支持过程跟踪和特征化。
这个阶段的定量过程控制数据包括,印刷偏移和焊锡量信息,而有关印刷焊锡的定性信息也会产生。
(2)回流焊前。
检查是在元件贴放在板上锡膏内之后和PCB送入回流炉之前完成的。
这是一个典型地放置检查机器的位置,因为这里可发现来自锡膏印刷以及机器贴放的大多数缺陷。
在这个位置产生的定量的过程控制信息,提供高速片机和密间距元件贴装设备校准的信息。
这个信息可用来修改元件贴放或表明贴片机需要校准。
这个位置的检查满足过程跟踪的目标。
(3)回流焊后。
在SMT工艺过程的最后步骤进行检查,这是目前AOI最流行的选择,因为这个位置可发现全部的装配错误。
回流焊后检查提供高度的安全性,因为它识别由锡膏印刷、元件贴装和回流过程引起的错误。
为了便于检查,一块PCB能够在设计阶段就进行优化布局吗?答案当然是肯定的,我们在本文中提供了一些建议供参考。
每块PCB可以采用光学或者X-ray技术并运用适当的运算法则来进行检查。
基于图像检查的基本原理是:每个具有明显对比度的图像都是可以被检查的。
在AOI中存在的主要问题是,当一些检查对象是不可见的,或是在PCB上存在一些干扰使得图像变得模糊或隐藏起来了。
然而,实际经验和系统化测试都表明,这些影响是可以通过PCB的设计来预防甚至减少的。
为了推动这种优化设计,可以运用一些看上去很古老的附加手段(这些方法仍在很多领域被推崇),它的优点包括:• 减少编程时间• 最大限度地减少误报• 改善失效检查。
制定设计方针,可以有效地简化检查和显著地降低生产成本。
Viscom AG 和KIRRON GmbH &Co.KG 合作开发出一项特殊测试方案,目的是为了从根本上研究和证明这些设计在检查中产生的效果。
基于IPC-7350标准的PCB布局被推荐为针对这些测试的基准。
首先,为了探究每一种布局的检查效果,建议在大量PCB布局上采用这种基准;之后,再有意地利用PCB错误布局,使得它产生一些工艺中的缺陷,如立碑和引脚悬空等。
(图1)AOI针对AOI检查的布局建议• 针对AOI检查的PCB整体布局器件到PCB的边缘应该至少留有3mm(0.12”)的工艺边。
片式器件必须优先于圆柱形器件。
布局上建议考虑传感器技术,因为有时检查只能通过垂直(正交)角度,而其他时候又需要一个辅助的角度来进行。
• 元器件对一个稳定的工艺过程来说,一个重要的因素是元器件,这不仅与PCB上直接的器件布局有关,而且或多或少也与“工艺流程设计”有关。
目前元器件的采购趋势是尽可能地便宜,而不管它在颜色、尺寸等参数上的不同。
不幸的是,这些选择在日后对AOI或AXI检查过程中造成的影响往往被忽略了。
始终采用同样的材料和产品能够显著地减少检查时间和误报,而这些问题主要是通过元器件以及PCB的突然变化而出现的。
• 元器件尺寸IPC-7350标准描述了器件的尺寸,并对某些焊盘的尺寸提出了建议。
根据IPC标准,器件的长度和引脚的宽度可以有一个较大变化范围,相反,焊盘的尺寸却是相对固定的。
此外,PCB制造公差的影响相对于这些器件的变化来说也是是很小的。
• PCB的颜色和阻焊通常,设备能够检查出所有不同单板的颜色,尽管检查中的某些细节处理是不倚赖于颜色的。
例如,一块白色和一块绿色的PCB有着不同的对比度,因此设备需要一些特定的补偿。
在一种极端情况下,桥接在亮背景下呈现黑色,而在另一种极端情况下,桥接在黑背景下却是呈现出亮色。
这里我们建议使用无光泽的阻焊层。
在我们的实践中,焊盘间(甚至是细间距引脚)的区域也应该覆盖着阻焊层,这个建议也已经被焊料供应商所响应。
(图2)AOI• 印刷图案所有印有图案的PCB也是能够被检查的,例如,当元器件的边框或元器件本体上的字母单独出现在组件的某个区域从而干扰对其他部分的检查时,可以手工调整检查程序。
尽管如此,在生产允许的范围内,图案的印刷范围仍然有一个较大的选择,因此,减少非反射性标识印刷(黑或暗黄)值得加以考虑。
另外一个可能出现的情况是需要有选择地印刷标识:例如,当某些特定的器件(如霍尔传感器)正面向下时就必须印刷成白色;而另一种情况是印有极性标志的有倾斜角的钽电容器件;这样能使标识和背景形成鲜明的对比,使得检查的图像更加清晰。
(图3)AOI• 基准点设备可以检查所有类型的基准点,而且任何构件都可以被定义成一个基准点。
虽然三个基准点可以补偿一块单板的变形,但通常情况下只需要确定两个基准点就可以了。
每个基准点至少离单板边缘5mm(0.2”)。
十字形、菱形、星形等比较适用,并建议使用统一的黑背景。
此外,十字形的基准点特别有优势,他们在检测光下的图像十分稳定且可以被快速和容易地判定。
(图4)。
AOI• 确认坏板设备有能力检查所有已知类型的坏板标识。
板上的任何构件都可以被定义为坏板标识。
这里建议采用与上述基准点的判定相类似的方法,即在可能的情况下,首先通过检查整板或已完成组装的单板上的单个坏板标识来进行确认。
板上每个单独的坏板标识只有在整板的坏板标识检查失败后才会被逐一检查;整板的坏板标识应该定位于PCB的边上。
• 避免焊点反射焊点的形状和接触角是焊点反射的根源。
焊点的形成依赖于焊盘的尺寸、器件的高度、焊锡的数量和回流工艺参数。
为了防止焊接反射,应当避免器件对称排列。
• 波峰焊经过波峰焊后,焊点所有的参数会有很大的变化,这主要是由于焊炉内锡的老化导致焊盘反射特性从光亮到灰暗,因此,在检查时算法上必须要包含这些变化。
在波峰焊中,典型的缺陷是短路和焊珠。
当检测到短路时,假如印刷的图案或者无反射印刷这两种情况的减少以及应用阻焊层,就可以消除这些误报。
如果基准点没有被阻焊膜盖住而过波峰焊,可能会导致一个圆形基准点上锡成了一个半球,其内在的反射特性将会发生改变;应用十字型作为基准点或者用阻焊层覆盖基准点,可以防止这种情况的发生。
• 片式元件、MELF器件和C-leads 器件在片式元件和MELF器件上,弯月状的焊点必须被正确地识别出来;而在器件本体两侧下方的焊点由于焊锡无爬升,很难检查。
另外,焊盘边缘到焊端的间距Xc也需要注意(图5)。
Xc (焊盘的外侧间距)对Xi(焊盘的内侧间距)的比率应选择>1。
同样的规则也适用于C-leads器件的弯月型和器件本体两侧的焊盘设计。
这里,我们建议Xc对Xi的比率稍微大于1.5。
值得注意的是:任何元器件的长度变化也必须计算在内。
AOI• “鸥翼”型引脚器件通常,这类器件的判定标准可以通过对毛细效应在垂直方向的作用的分析中找到。
由于毛细力,焊锡从焊盘末端爬到引脚上形成焊点。
由于工艺波动和器件边缘的阻挡作用,导致不能完全形成一个完整的上半月型焊点。
尽管没有形成一个上半月型的焊点,但也可以被认为焊接得很好。
“鸥翼”型引脚焊锡的侧面爬升情况由于器件变化或焊盘设计的原因,并不是经常能够被检查出来,这是由于焊锡的爬升方向必须用同引脚方向垂直的角度去检查。