论文箱体零件加工及加工工艺
箱体零件的机械加工工艺及夹具设计
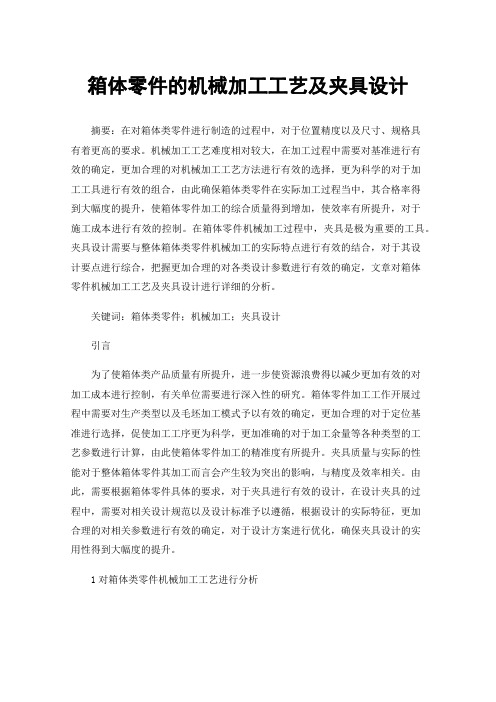
箱体零件的机械加工工艺及夹具设计摘要:在对箱体类零件进行制造的过程中,对于位置精度以及尺寸、规格具有着更高的要求。
机械加工工艺难度相对较大,在加工过程中需要对基准进行有效的确定,更加合理的对机械加工工艺方法进行有效的选择,更为科学的对于加工工具进行有效的组合,由此确保箱体类零件在实际加工过程当中,其合格率得到大幅度的提升,使箱体零件加工的综合质量得到增加,使效率有所提升,对于施工成本进行有效的控制。
在箱体零件机械加工过程中,夹具是极为重要的工具。
夹具设计需要与整体箱体类零件机械加工的实际特点进行有效的结合,对于其设计要点进行综合,把握更加合理的对各类设计参数进行有效的确定,文章对箱体零件机械加工工艺及夹具设计进行详细的分析。
关键词:箱体类零件;机械加工;夹具设计引言为了使箱体类产品质量有所提升,进一步使资源浪费得以减少更加有效的对加工成本进行控制,有关单位需要进行深入性的研究。
箱体零件加工工作开展过程中需要对生产类型以及毛坯加工模式予以有效的确定,更加合理的对于定位基准进行选择,促使加工工序更为科学,更加准确的对于加工余量等各种类型的工艺参数进行计算,由此使箱体零件加工的精准度有所提升。
夹具质量与实际的性能对于整体箱体零件其加工而言会产生较为突出的影响,与精度及效率相关。
由此,需要根据箱体零件具体的要求,对于夹具进行有效的设计,在设计夹具的过程中,需要对相关设计规范以及设计标准予以遵循,根据设计的实际特征,更加合理的对相关参数进行有效的确定,对于设计方案进行优化,确保夹具设计的实用性得到大幅度的提升。
1对箱体类零件机械加工工艺进行分析箱体类零件在实际加工过程中,对于各种类型的机械加工工艺具有着更高的要求。
具体而言,需要进一步的对相应的加工工艺进行详细的分析,相应的工艺可从以下几个角度进行探究。
1.1对箱体类零件生产类型进行分析箱体类零件在实际加工过程中,需要依照其实际的生产进度、产量等诸多情况,对于平均废品率以及备品率进行有效的分析,合理对箱体零件其生产类型进行有效的确定。
减速器箱体的加工工艺及夹具毕业设计论文
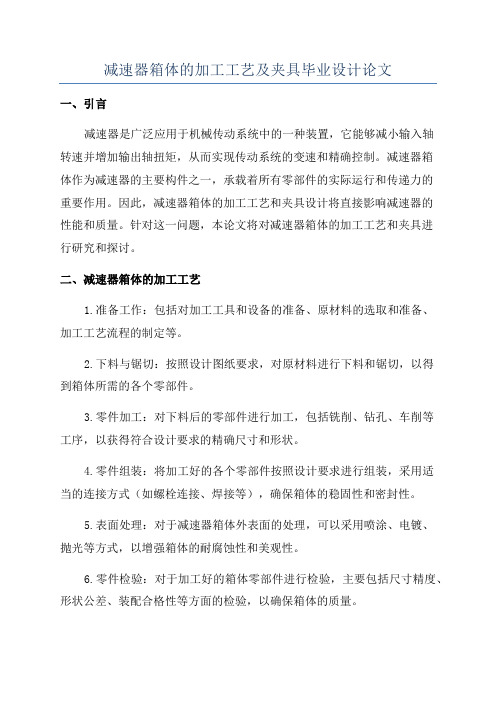
减速器箱体的加工工艺及夹具毕业设计论文一、引言减速器是广泛应用于机械传动系统中的一种装置,它能够减小输入轴转速并增加输出轴扭矩,从而实现传动系统的变速和精确控制。
减速器箱体作为减速器的主要构件之一,承载着所有零部件的实际运行和传递力的重要作用。
因此,减速器箱体的加工工艺和夹具设计将直接影响减速器的性能和质量。
针对这一问题,本论文将对减速器箱体的加工工艺和夹具进行研究和探讨。
二、减速器箱体的加工工艺1.准备工作:包括对加工工具和设备的准备、原材料的选取和准备、加工工艺流程的制定等。
2.下料与锯切:按照设计图纸要求,对原材料进行下料和锯切,以得到箱体所需的各个零部件。
3.零件加工:对下料后的零部件进行加工,包括铣削、钻孔、车削等工序,以获得符合设计要求的精确尺寸和形状。
4.零件组装:将加工好的各个零部件按照设计要求进行组装,采用适当的连接方式(如螺栓连接、焊接等),确保箱体的稳固性和密封性。
5.表面处理:对于减速器箱体外表面的处理,可以采用喷涂、电镀、抛光等方式,以增强箱体的耐腐蚀性和美观性。
6.零件检验:对于加工好的箱体零部件进行检验,主要包括尺寸精度、形状公差、装配合格性等方面的检验,以确保箱体的质量。
7.最终组装和调试:将经过检验合格的零部件进行最终组装,并进行调试和测试,确保减速器箱体的性能和功能达到设计要求。
三、减速器箱体加工工艺中的夹具设计夹具是加工工艺中的重要辅助工具,它能够固定工件、定位、限制运动和提高加工稳定性。
在减速器箱体加工过程中,夹具的设计对于保证加工质量和提高生产效率起到关键作用。
以下是减速器箱体加工工艺中常用的夹具设计方法:1.定位夹具:定位夹具主要用于将待加工的零部件正确的位置上,确保加工精度和减小误差。
常用的定位夹具有平行销、固定块、定位板等。
2.夹持夹具:夹持夹具用于将工件固定在加工设备上,以保证加工过程的稳定性和安全性。
常用的夹持夹具有机械夹具、液压夹具、气动夹具等。
箱体类零件的加工工艺
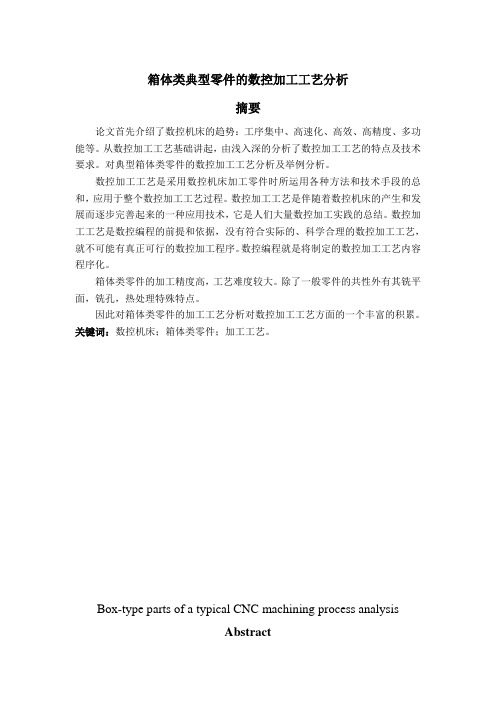
箱体类典型零件的数控加工工艺分析摘要论文首先介绍了数控机床的趋势:工序集中、高速化、高效、高精度、多功能等。
从数控加工工艺基础讲起,由浅入深的分析了数控加工工艺的特点及技术要求。
对典型箱体类零件的数控加工工艺分析及举例分析。
数控加工工艺是采用数控机床加工零件时所运用各种方法和技术手段的总和,应用于整个数控加工工艺过程。
数控加工工艺是伴随着数控机床的产生和发展而逐步完善起来的一种应用技术,它是人们大量数控加工实践的总结。
数控加工工艺是数控编程的前提和依据,没有符合实际的、科学合理的数控加工工艺,就不可能有真正可行的数控加工程序。
数控编程就是将制定的数控加工工艺内容程序化。
箱体类零件的加工精度高,工艺难度较大。
除了一般零件的共性外有其铣平面,铣孔,热处理特殊特点。
因此对箱体类零件的加工工艺分析对数控加工工艺方面的一个丰富的积累。
关键词:数控机床;箱体类零件;加工工艺。
Box-type parts of a typical CNC machining process analysisAbstractPaper introduces the trend of CNC machine tools: process focus, high-speed, high efficiency, high precision, multi-function, such as. From talking about the basisof numerical control processing, easy-to-digest analysis of the characteristics of CNC machining technology and technical requirements. The typical box-type parts on the CNC machining process analysisand example analysis.CNC machining process is the use of CNC machining parts by using various methods and techniques of the sum of the means applied to the entire CNC machining process. CNC machining process is accompanied by the emergence of CNC machine tools and development with a gradual improvement of application technology, it is the practice of a large number of CNC machining summary. CNC Machining NC programming process is the prerequisite and basis for, not in line with the practical, scientific and rational CNC machining process, there can be no real NC machining process possible. NC programming is to formulate the contents of the NC processing program.Box-type high-precision machining, process more difficult. In addition to the general common parts outside the plane of its milling, hole milling, heat treatment of special features.Box-type parts on the process of analysis of the aspects of CNC machining process to a rich accumulation.Keywords: CNC machine tools; box components; processing technology.目录第1章概述 (3)1.1 数控加工技术的发展和趋势 (3)1.2 数控加工的定义 (5)1.3数控加工工艺的定义 (5)1.4数控加工工艺的特点 (5)第2章数控加工工艺基础 (6)2.1 数控加工工艺分析 (6)2.2零件图的分析审查 (8)2.3零件机械加工工艺规程的制定 (9)第3章数控机床加工箱体类零件的工艺分析 (13)3.1箱体类零件的结构及特点 (13)3.2箱体类零件的材料及毛胚 (14)3.3箱体类零件的主要技术要求 (15)3.4箱体零件的加工工艺分析 (15)第4章分离式齿轮箱体加工工艺过程及其分析 (21)4.1 分离式箱体的主要技术要求 (21)4.2 分离式箱体的工艺特点 (22)第5章总结 (25)参考文献 (26)答谢词 (27)第1章概述1.1 数控加工技术的发展和趋势1.1.1数控机床的发展美国麻省理工学院于1952年成功地研制出世界上第一台的数控铣床。
毕业设计(论文)-曲轴箱箱体的工艺及工装[管理资料]
![毕业设计(论文)-曲轴箱箱体的工艺及工装[管理资料]](https://img.taocdn.com/s3/m/b9c285bae45c3b3566ec8b98.png)
东华理工大学长江学院毕业设计题目曲轴箱箱体的工艺及工装英文题目Crancase technology and tooling cabinet学生姓名:学号:专业:机械制造及自动化系别:机械工程系指导教师:职称:副教授二零一二年六月摘要曲轴箱是一种典型的箱体零件,它的作用是容纳和支承其内的所有零部件,保证它们相互间的正确位置,使彼此之间能协调地运转和工作。
曲轴箱的分割面与轴承孔,箱盖左右两侧缸孔精度要求较高,因此在安排工艺过程时,就需要把各主要表面及孔的粗精加工工序分开。
在制定曲轴箱工艺过程中,还确定了切削参数,工时定额,并填写了工序卡片。
分别设计了一套钻联接孔的钻模与镗轴承孔的镗模,并进行了定位误差分析。
关键词:工艺过程;切削用量;工时定额;曲轴箱箱体;专用夹具;定位误差分析ABSTRACTCrankcase is a typical box part, its role is to hold and all the parts inside the bearing to ensure the correct position between them, so that better coordination to operate and work. Split the crankcase and the bearing bore surface, the to major rough surface and hole finishing operations separately. In the development process card. Were designed a drill hole jig join bearing hole boring and boring model, and location error analysis out.Key words: Process;cutting the amount of fixed working hours;special fixtures;positioning error analysis目录绪论 (1)1曲轴箱结构特点分析 (2) (2) (2) (2) (3) (3)2拟定箱体加工工艺路线 (4) (4) (4) (4) (5) (5)3毛坯尺寸、机械加工余量和工序尺寸的确定 (6): (6) (7) (7)4确定切削参数和工时定额的计算 (8) (8) (10) (13)×Φ18MM孔,锪4×Φ40MM凸台 (15)×Φ16MM孔,锪12×Φ32MM凸台平面 (18),钻、攻3×M6MM螺纹 (21) (24).0+, (25)0350 + (26).00350 + (27).0035×160MM (28)、攻箱盖缸孔6×M8螺孔 (30)、攻轴承孔端面6×M8螺孔 (33)5专用夹具的设计 (37) (37) (37)结论 (42)致谢 (43)参考文献 (44)绪论箱体类零件是箱体类零部件装配时的基础零件,它的作用是容纳和支承其内的所有零部件,并保证它们相互间的正确位置,使彼此之间能协调地运转和工作。
箱体零件的加工工艺

箱体零件的加工工艺【箱体零件的加工工艺】一、箱体零件加工工艺的历史其实啊,箱体零件的加工工艺有着相当长的历史。
在工业发展的早期,人们制造箱体零件的方法非常原始和简单。
那时候可没有现在这么先进的机床和工具,加工精度和效率都很低。
比如说,早期可能就是用手工打造,一点点地敲敲打打,把金属材料塑造成大致的箱体形状。
这就好比是在捏泥巴,只不过材料从泥巴变成了金属,而且难度要大得多。
随着工业革命的推进,蒸汽机的出现带动了机械制造业的发展。
慢慢地,出现了一些简单的机床,像车床、铣床等。
这时候加工箱体零件就有了一定的进步,但还是比较粗糙。
到了 20 世纪,随着科技的飞速发展,数控机床、加工中心等先进设备逐渐问世,箱体零件的加工工艺也迎来了巨大的变革。
加工精度、效率和质量都有了显著的提高。
二、箱体零件加工工艺的制作过程1. 设计与规划说白了就是在开始加工之前,得先想好要做个什么样的箱体零件。
这就像你要盖房子,得先有个设计图纸,知道房子的大小、形状、结构等等。
要考虑箱体的用途、尺寸、材料等因素,制定出详细的加工方案。
比如说,一个用于汽车发动机的箱体零件,和一个用于电脑主机的箱体零件,那要求肯定是不一样的。
2. 材料准备根据设计要求选择合适的材料。
常见的有铸铁、铝合金、钢等。
这就好比做饭选食材,得选对了才能做出好吃的菜。
不同的材料有不同的性能,比如强度、硬度、耐磨性等。
3. 毛坯制造有了材料,接下来就是制造毛坯。
毛坯可以通过铸造、锻造、焊接等方法获得。
比如说铸造,就像是做个大的金属“沙模”,把熔化的金属液体倒进去,冷却后就得到了一个初步的形状。
4. 粗加工先把毛坯进行初步的加工,去掉多余的部分,让它大致接近箱体零件的最终形状。
这个过程就像是在雕刻一块大石头,先把多余的石头凿掉,露出大致的轮廓。
5. 半精加工在粗加工的基础上,进一步提高精度和表面质量。
比如说,把一些面磨得更平,把孔钻得更准。
6. 精加工这是最后的关键步骤,要达到设计要求的精度和表面质量。
箱体类零件的加工工艺分析
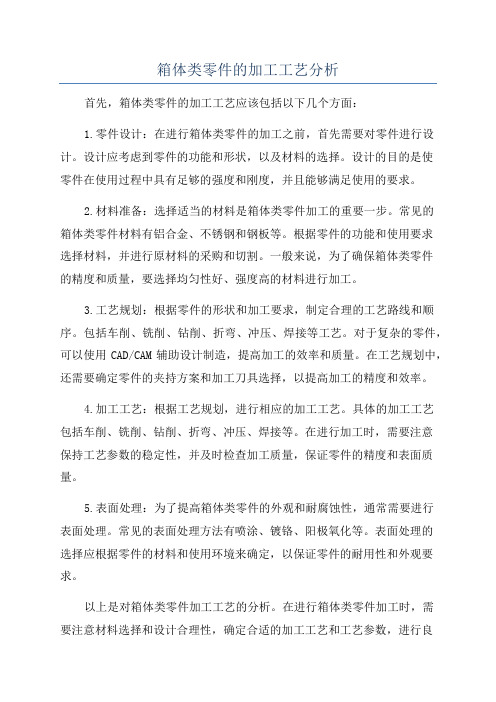
箱体类零件的加工工艺分析首先,箱体类零件的加工工艺应该包括以下几个方面:1.零件设计:在进行箱体类零件的加工之前,首先需要对零件进行设计。
设计应考虑到零件的功能和形状,以及材料的选择。
设计的目的是使零件在使用过程中具有足够的强度和刚度,并且能够满足使用的要求。
2.材料准备:选择适当的材料是箱体类零件加工的重要一步。
常见的箱体类零件材料有铝合金、不锈钢和钢板等。
根据零件的功能和使用要求选择材料,并进行原材料的采购和切割。
一般来说,为了确保箱体类零件的精度和质量,要选择均匀性好、强度高的材料进行加工。
3.工艺规划:根据零件的形状和加工要求,制定合理的工艺路线和顺序。
包括车削、铣削、钻削、折弯、冲压、焊接等工艺。
对于复杂的零件,可以使用CAD/CAM辅助设计制造,提高加工的效率和质量。
在工艺规划中,还需要确定零件的夹持方案和加工刀具选择,以提高加工的精度和效率。
4.加工工艺:根据工艺规划,进行相应的加工工艺。
具体的加工工艺包括车削、铣削、钻削、折弯、冲压、焊接等。
在进行加工时,需要注意保持工艺参数的稳定性,并及时检查加工质量,保证零件的精度和表面质量。
5.表面处理:为了提高箱体类零件的外观和耐腐蚀性,通常需要进行表面处理。
常见的表面处理方法有喷涂、镀铬、阳极氧化等。
表面处理的选择应根据零件的材料和使用环境来确定,以保证零件的耐用性和外观要求。
以上是对箱体类零件加工工艺的分析。
在进行箱体类零件加工时,需要注意材料选择和设计合理性,确定合适的加工工艺和工艺参数,进行良好的加工控制和质量检查。
通过合理的加工工艺,可以保证箱体类零件的精度和质量,提高产品的竞争力和市场占有率。
箱体类零件的加工工艺过程
二 箱体类零件的主要技术要求
1、孔径精度及孔与孔的位置精度 2、孔与平面的位置精度 3、主要平面的精度 4、表面粗糙度
某车床主轴箱简图
三 箱体类零件的材料及毛坯
1、箱体类零件的材料
箱体铸铁材料采用最多的是各种牌号的灰铸铁:如 HT200、HT250、HT300等。对一些要求较高的箱体, 可采用耐磨合金铸铁,以提高铸件质量。
定位基准 — — —
Ⅰ孔与Ⅱ孔 顶面A及外形 顶面A及两工艺孔 顶面A及两工艺孔 导轨面B、C 顶面A及两工艺孔 顶面A及两工艺孔 顶面A及两工艺孔
— 顶面A及两工艺孔
— — —
某主轴箱小批生产工艺过程
序号 1 2 3
4
5 6 7 8 9 10 11 12 13
工序内容 铸造 时效 涂底漆 划线:考虑主轴孔有加工余量,并尽量均匀。划C、A及E、D面 加工线 粗、精加工顶面A 粗、精加工B、C面及侧面D 粗、精加工两端面E、F 粗、半精加工各纵向孔 精加工各纵向孔 粗、精加工横向孔 加工螺孔及各次要孔 清洗、去毛刺 检验
划线:考虑主轴孔有加工余量,并尽量均匀。
二 箱体(类零2件)的主加要技工术要阶求 段精、精分开
三 箱体类零件的材料及毛坯
粗、精加(工两3端)面E工、F序间安排时效处理
同轴线上孔径的排列方式
2)大批(大量4生)产时粗,毛基坯精准度较的高。选择
1、不同批量箱体生产的共性 2、孔与平面的位置精度 四 箱体类零件的结构工艺性
某主轴箱大批生产工艺过程 二 箱体类零件的主要技术要求 同轴线上孔径的排列方式 三 箱体类零件的材料及毛坯 同轴线上孔径的排列方式 圆工作台铣床加工示意图 1)中小批生产时,由于毛坯精度较低一般采用划线装夹。 粗、精加工两端面E、F 单元三 平面加工方法和加工方案 2、孔与平面的位置精度 划C、A及E、D面加工线 三 箱体类零件的材料及毛坯 四 箱体类零件的结构工艺性 箱体毛坯制造方法有两种,一种是采用铸造,另一种是采用焊接。 圆工作台铣床加工示意图 (3)工序间安排时效处理 对金属切削机床的箱体,由于形状较为复杂,而铸铁具有成形容易、可加工性良好、并且吸振性好、成本低等优点,所以一般都采用 铸铁; 粗、精加工B、C面及侧面D 2、孔与平面的位置精度 二 典型箱体类零件加工工艺过程与分析
箱体零件的加工工艺及工艺装备设计
箱体零件的加工工艺及工艺装备设计
首先,箱体零件的材料选择是加工工艺及工艺装备设计的基础。
箱体
零件一般使用金属材料,如铝合金、钢材等。
在选择材料时,需要考虑箱
体零件的功能要求、强度要求、耐腐蚀性等因素。
根据不同的材料性质,
选择相应的加工方法和工艺装备。
其次,根据箱体零件的形状和加工要求,设计合理的加工工艺流程。
加工工艺流程应当包括工序的选择、先后顺序及工艺参数的确定等。
一般
情况下,箱体零件的加工工艺流程包括以下几个步骤:材料切割、表面处理、机械加工、装配等。
在确定加工工艺流程时,需要考虑成本、加工精度、效率和质量等因素,并与产品设计进行协调。
然后,根据加工工艺的要求,选择适当的工艺装备。
工艺装备的选择
应当符合箱体零件的加工特点和工艺流程要求。
常用的工艺装备包括数控
机床、冲压机、激光切割机等。
选择工艺装备时,需要考虑其加工规模、
加工精度、加工效率、稳定性和维护成本等因素。
最后,进行工艺装备布局设计。
工艺装备布局设计应当合理安排各个
工序的加工设备,使得加工流程顺畅、物料运输方便,并提高工作效率。
同时,还应当考虑人员活动空间、安全通道等因素。
综上所述,箱体零件的加工工艺及工艺装备设计是一个综合性的任务。
在设计过程中,需要综合考虑材料选择、加工工艺流程设计、工艺装备选
择和工艺装备布局设计等因素,以满足箱体零件的功能要求、质量要求、
成本要求等。
只有通过合理的设计,才能提高加工效率、降低成本,并保
证产品质量。
毕业设计(箱体零件工艺设计)
编号:沙洲工学院2008届毕业论文题目:对箱体零件加工工艺的分析及研究动力工程系数控技术专业班级:05数控技术学号: xxx姓名:xxx指导教师:xxx.2008年7 月摘要本文主要对箱体零件的加工方法的研究和说明,箱体类零件是机器及其部件的基础件,它将机器及其部件中的轴、轴承、套和齿轮等零件按一定的相互位置关系装配成一个整体,并按预定传动关系协调其运动。
因此,箱体的加工质量不仅影响其装配精度及运动精度,而且影响到机器的工作精度、使用性能和寿命。
关键词:加工工艺精度定位Abstract :This article mainly to the box body components' processing method's research and showing, the box body class components is the machine and part's foundation, it components and so on machine and part's axis, bearing, wrap and gear assembles according to certain mutual position relations a whole, and is coordinated its movement according to the predetermined transmission relations. Therefore, the box body's processing quality not only affects its assembly precision and the movement precision, moreover affects machine's work precision, the operational performance and the life.Keywords :Processing craft precision Localization目录引言 (1)第1章企业概况 (2)第2章箱体零件加工工艺及案例分析 (2)第2.1节主轴箱加工工艺过程 (2)第2.2节箱体类零件加工工艺分析 (3)第3章分离式齿轮箱体加工工艺过程及其分析 (6)第3.1节分离式箱体的主要技术要求 (7)第3.2节分离式箱体的工艺特点 (8)第4章总结体会 (9)第4.1节概述 (9)第4.2节平面加工方法和平面加工方案 (12)参考文献 (21)引言箱体类零件通常作为箱体部件装配时的基准零件。
箱体类零件加工工艺
Equipment Manufacturing Technology No.11,2012作为机器的基础零件之一,箱体将机器里的各个零部件组装成一个整体,并让这个整体以正确的相对位置进行某些必要运动。
虽然不同机器的箱体也各不相同,但这些箱体都具有结构复杂、壁厚不均及内部腔形等共同点,箱体内壁上拥有形状各异的平面和数量众多的轴承,支撑孔及紧固孔,这些平面及孔都有较高的精度和较低的粗糙度要求。
因此,箱体加工品质的高低会对其各部件的装配精度、机器的性能及使用寿命等方面产生直接影响。
1箱体类零件的技术要求1.1表面粗糙度及孔的精度要求轴承孔必须具有较高尺寸精度及较低的表面粗糙度。
如果无法满足,就会导致轴承和箱体上的孔重合度不高,从而在工作过程中产生振动及噪音,尤其是机床主轴支撑孔会对主轴旋转精度产生直接影响,进而对机床加工工艺产生影响。
通常情况下,对主轴支撑孔的加工等级和粗糙度的要求分别为IT6 ̄7级和Ra1.6 ̄0.8μm[1]。
1.2孔距和位置精度要求在箱体中以齿轮啮合关系存在的相邻孔之间,必须具有较高的孔距尺寸精度和平行度,如果达不到要求就会对齿轮的啮合精度产生影响,从而箱体在工作时,因震动和噪音减少齿轮使用寿命。
传动齿轮副的中心距允差及轮啮合精度直接决定着孔距尺寸精度。
箱体同轴线上的孔必须具有较高同轴度。
一旦同轴度较低的话,不但会导致箱体装配不便,还会加剧轴承磨损度,使之温度上升,进而影响机器的正常工作和精度。
1.3主要平面精度要求箱体的主要平面必须具有较高的相互位置和形状精度以及较低的粗糙度。
通常箱体的主要平面为装配基面或加工定位面,其加工品质对箱体加工时的定位精度,以及箱体同其它零件进行总装时的相对位置精度和接触刚度都有直接影响,因此,对箱体主要平面粗糙度的要求较低,但平面度的要求较高[2]。
1.4孔对装配基面的精度要求箱体上支撑孔同装配基面之间必须具有较高的平行度和尺寸精度,同时还应对端面具有较高垂直度。
- 1、下载文档前请自行甄别文档内容的完整性,平台不提供额外的编辑、内容补充、找答案等附加服务。
- 2、"仅部分预览"的文档,不可在线预览部分如存在完整性等问题,可反馈申请退款(可完整预览的文档不适用该条件!)。
- 3、如文档侵犯您的权益,请联系客服反馈,我们会尽快为您处理(人工客服工作时间:9:00-18:30)。
箱体零件加工及加工工艺专业机械设计制造及其自动化年级 2013级姓名王婷指导教师李强2015年5月25日天津理工大学成人高等教育本科毕业设计(论文)任务书目录引言 (4)第1章零件图解析 (5)1.1箱体零件作用 (5)1.2箱体零件的材料及其力学性能 (5)1.3箱体零件的结构工艺分析 (5)第2章毛坯的分析 (5)2.1毛坯的选择 (5)2.2毛坯图的设计 (6)第3章工艺路线拟定 (6)3.1定位基准的选择 (6)3.2加工方法的确定 (6)第4章加工顺序的安排 (7)4.1工序的安排 (7)4.2工序划分的确定 (8)4.3热处理工序的安排 (8)4.4拟定加工工艺路线 (9)4.5加工路线的确定 (9)4.6加工设备的选择 (9)4.7刀具的选择 (10)4.8选择夹具及量具确定装夹方案 (10)第5章工艺设计 (10)5.1加工余量,工序尺寸,及其公差的确定 (10)5.2确定切削用量及功率的校核 (11)第6章数控加工路线的分析 (13)结论 .......................... 错误!未定义书签。
参考文献 ........................... 错误!未定义书签。
附表1 .............................. 错误!未定义书签。
附表2 .............................. 错误!未定义书签。
致谢 .. (18)引言数控加工毕业设计是在学院机械制造工艺学(含机床夹具设计)和所有专业课之后进行的,是对所学各课程的一次深入的综合性的复习,也是理论联系实际的训练。
毕业设计的任务是根据所给定的箱体零件图,确定合适的加工机床、刀具、切削用量,合理的进给路线,制定经济高效的工艺方案;绘制箱体零件图一张、毛坯图一张、编制工艺过程卡,数控加工工序卡,数控刀具卡,编写数控加工程序,撰写设计说明书。
要求我们能综合运用机械制造工艺学中基本理论,并结合生产实习中学到的实践知识,独立的分析和解决工艺问题,初步具备了设计一个中等复杂箱体零件的工艺程度箱体零件的工艺规程的能力和运用夹具设计的基本原理和方法,拟定加工方案。
同时也是熟悉和运用有关手册、图表等技术资料及编写技术文件等基本技能的一次实践机会,为今后从事的工作打下良好基础。
加工目的:1、保证箱体零件加工质量;2、合适一般现场条件,能显著提高生产效率:3、降低生产成本,适宜性强:4、工艺合理,工艺资料齐全,说服力强。
第1章零件图解析1.1箱体零件作用该箱体零件为燃烧室支撑环,是内燃机内一种高温高压的起支撑作用的环。
1.2箱体零件的材料及其力学性能工件材料为1Cr18Ni9Ti是奥式体不锈钢,相对可切削性为0.3~0.5之间,是一种难切削的材料,其难加工性主要表现在以下几个方面:高温强度和高温硬度高,1Cr18Ni9Ti在700度时也不能降低其机械性能,故切削不易被切离,切削过程中切削力大,刀具易磨损。
塑性和韧性高,虽然1Cr18Ni9Ti的抗拉强度和硬度都不高,但综合性能很好,塑性和韧性高,它的延伸率、断面收缩率和冲击值都较高,切削变形所消耗的功能增多,所消耗的能量比切除相同体积的低碳钢约高50%,并且大部分能量转化为热能使切削温度升高。
1Cr18Ni9Ti的导热率低,散热差,有切削带走的热量少,大部分的热量被刀具吸收,致使刀具的温度升高,加剧刀具磨损,在一定的温度和压力下会产生粘附现象,在切削过程中,刀具易产生积削瘤,不易获得表面粗糙度高的加工表面。
加工硬化严重,1Cr18Ni9Ti强度一般为539Mpa,但室温冷加工时,由于加工硬化和变形会诱发马式体转变,使强度提高,这样大大增加了切削时的磨损。
1Cr18Ni9Ti具有优良的力学性能,良好的耐蚀能力,较突出的是冷变形能力,无磁性。
1.3箱体零件的结构工艺分析从箱体零件图上看,该箱体零件是典型的回转体箱体零件,结构比较简单,其主要加工的面有¢197.3的外圆柱面,¢187、¢171.08的内圆柱表面,以及内外轮廓。
该箱体零件在加工时主要考虑变形以及测量的问题,由于内外轮廓交界处壁太薄仅0.635的厚度,在切削过程中不易散热,刀具所带走的只是少量热量,加工硬化也很严重,塑性和韧性较高,所以要使工件恢复其应力再加工,采取相应的热处理去处内应力,减少其变形。
图中所给的尺寸精度并不高,在IT11~12级之间,但粗糙度都是1.6。
通过分析该箱体零件,其布局合理,方便加工,我们通过径向夹紧可保证其加工要求,整个图面清晰,尺寸完整合理,能够完整表达物体的形状和大小,符合要求。
第2章毛坯的分析毛坯的选择和拟定毛坯图是制定工艺规程的最初阶段工作之一,也是一个比较重要的阶段,毛坯的形状和特征(硬度,精度,金相组织等)对机械加工的难易,工序数量的多少有直接影响,因此,合理选择毛坯在生产占相当重要的位置,同样毛坯的加工余量的确定也是一个非常重要的问题。
2.1毛坯的选择毛坯种类的选择决定与箱体零件的实际作用,材料、形状、生产性质以及在生产中获得可能性,毛坯的制造方法主要有以下几种:1、型材2、锻造3、铸造4、焊接5、其他毛坯。
该箱体零件为燃烧室支撑环材料为1Cr18Ni9Ti,考虑到箱体零件本身的结构以及材料,结构简单,塑性和韧性高,所以推荐用型材或锻件,但从经济方面着想,如用型材中的棒料,加工余量太大,这样不仅浪费材料,而且还增加机床,刀具及能源等消耗,而短见具有较高的强度,冲击韧性常用于大载荷或冲击载荷下的工作箱体零件。
本箱体零件生产批量为中小批量,所以综上所叙选择锻件中的自由锻。
2.2毛坯图的设计毛坯(锻件)图是根据产品箱体零件设计的,经查《机械加工工艺手册》自由锻件中机械加工余量计算公式得:A=0.2*H^0.2*D^0.55=5.8mm,小孔0.75A=4.35mm,大孔0.5A=2.9mm,H=0.5A=2.9mm。
第3章工艺路线拟定3.1定位基准的选择工件在加工第一道或最初几道工序时,职能一毛坯上未加工的表面作为定位基准,这个是粗基准,该箱体零件选用¢171.08内孔作为粗基准来加工外圆柱面和左端面。
以上选择符合粗基准的选择原则中的(如果必须保证箱体零件某些重要表面的加工余量分布均匀,就应该选择该表面做为粗基准,应该用毛坯的尺寸和位置可靠表面,而且平整具有足够大的面积做基准)在以后的工序中,则使用经过加工的表面作为定位基准,¢197.3的外圆柱面和左端面作为定位基准,着个基准就是精基准。
在选精基准时采用有基准重合,基准统一,互为基准,自为基准。
这样定位比较简单可靠,为以后加工重要表面做好准备。
3.2加工方法的确定在市场经济的前提下,一切都是为能创造出更多的财富和提高劳动率为目的,同样的加工方法的选择一般考虑的是在保证工件加工要求的前提下,译稿工件的加工效率和经济性,而在具体的选择上,一般根据机械加工资料和工人的经验来确定。
由于方法的多种多样,工人在选择时一般结合具体的工件和现场的加工条件来确定最佳的加工方案。
同样在该箱体零件的加工方法的选择中,我们考虑了工件的具体情况互我们学校的具体加工条件,一下是我们按加工顺序来阐述的加工方案:①¢197.3外圆柱面,精度为IT12,表面粗糙度为Ra1.6粗车(IT12~11,Ra25~12.5)-精车(IT8~7,Ra1.6~0.8)②¢187.48内圆柱表面, 精度为IT12,表面粗糙度为Ra1.6粗车(IT12~11,Ra25~12.5)-半精车(IT10~9,Ra6.3~3.2)- 精车(IT8~7,Ra1.6~0.8)③¢171.08内圆柱面,无精度要求, 表面粗糙度为Ra1.6粗车(IT12~11,Ra25~12.5)-精车(IT8~7,Ra1.6~0.8)④由R2.8,R12.7,R1.6,R20.07的圆弧组成的内外轮廓, 表面粗糙度为Ra1.6粗车(IT12~11,Ra25~12.5)-半精车(IT10~9,Ra6.3~3.2)- 精车(IT8~7,Ra1.6~0.8) 第1道工序分5个工步,加工3个要素。
工步1是装夹找正。
横向装夹时一要找正两磨削过的平面与车床的z轴平行,以保证车出的(侧)面与磨削过的面垂直;二要找正两磨过的面与夹盘的回转中心线对称。
工步2是车平面(工件的一个侧面)。
工步3是钻中心孔。
工步4是用φ18mm的钻头钻通孔。
工步5是用φ16mm粗的镗刀镗φ20mm和φ32mm阶梯孔。
第2道工序分2个工步,加工1个要素。
工步1是装夹找正。
在上工序的基础上翻180。
装夹,还是横向装夹。
装夹时一要找正到两磨过的平面与车床的Z 轴平行;二要找正到两磨削过的平面的对称线(面)距夹盘回转中心1±0.02mm之内。
工步2是用φ16mm粗的车刀车φ32mm偏心孔。
第3工序分3个工步,加工1个要素。
工步l是装夹找正。
纵向装夹,夹偏心孔偏向的那头装夹时一要找正到夹盘回转中心线与工序1加工的那个侧面垂直,二要找正到磨削过的两侧而与夹盘同转中心线对称.工步2是车端面。
工步3是打中心孔。
第4道工序分3个工步,加工为随后各工序找正用的找正槽。
工步1是装夹找正,夹的方向与上工序一样,只是比上工序少夹一段,右侧用回转顶尖顶上。
装夹时只要找正左侧,主要是找正磨削过的两侧面与夹盘回转中心线对称。
工步2是加上左找正槽,工步3是加工右找正槽。
第5道工序分5个工步,加工3个要素。
工步I是装夹找正、夹的方向与上工序一样,只是比上工序多一段。
装夹时找正夹盘回转中心线与两对侧面的对称平面的交线再合。
工步2是钻中心孔。
工步3是用φφ15.7mm的钻头钻通孔。
上步4是车φ16.8m通孔和锥孔。
工步5是车端面槽。
第6道上序分5个工步,加工4个要素。
工步1是装夹找正,是在上工序的基础上调头夹。
装夹时找正的要求与上工序相同,也就是要找正夹盘同转中心线与上工序加工的孔轴。
工步2是车端面u工步3是车正49mm孔和28.6mm孔。
工步4是车螺纹的锥底孔及其上的倒角。
工步5是车螺纹。
第7工序分3个工步,加工外回转型面。
工步1是装夹找正。
在上工序的基础调头,右端用回转顶尖顶上。
装夹时的找正要求同第5工序。
工步2车左半圆弧回转面和一段圆柱面。
工步3是车右半圆弧回转面和一段圆柱面。
在写刀路之前,将立体图画好后,要将图形中心移到坐标原点,最高点移到Z=0,方可以加工,铜公火花位可加工负预留量。
在加工前还要检查工件的装夹方向是否同电脑中的图形方向相同,在模具中的排位是否正确,装夹具是否妨碍加工,前后模的方向是否相配。
还要检查你所用的刀具是否齐全,校表分中的基准等。
加工铜公要注意的事项:火花位的确定,一般幼公(即精公)预留量为0.05~0.15,粗公0.2~0.5,具体火花位的大小可由做模师父定。