中型优质H 型钢LF 精炼工艺优化实践
含铝钢LF精炼渣成分优化及造渣制度改进
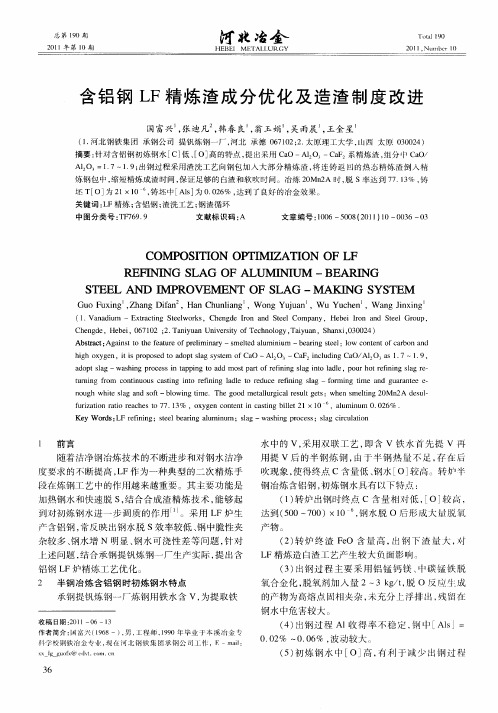
一
在 统计转 炉 下渣 量 基 础 上 , 终 渣 总量 和成 分 要 求 按 可粗 略计 算 出各种 造渣 材料 用量 , 过取样 分 析 、 经 修 正, 就能 得到 合理 的造 渣材 料用 量及 配 比 。 另外 , 效利 用 从 连 铸 回转 台下 来 的热 态 精 炼 有 渣, 可减 少造 渣料 的加 入 , 降低 因渣料 熔化 带来 的热
XX
—
I g , x 【 It C f . I g u , @ ‘ v . OT C] f ( I
—
( ) 炼 钢 水 中 [ 高 , 利 于 减 少 出钢 过 5初 0] 有
36
21 0 1年 第 1 0期
钢 水 吸 N, 免大 幅度 增 N。 避
3 L F炉 常用精 炼 渣 系
S TEEI ,AND 皿 OVEM匣NT OF LAG — M A KD S TE S G YS
Gu u ig ,h n fn , a h ni g , n uun , ce WagJ xn oF xn Z a gDi H nC u l n Wo gY ja WuYuh n , n i ig a a n
( . n du —E tat g S el r s 1 Va a im xr ci tewok ,Ch n d r n a d Se lCo a y,He e Io n te Gru n e g e Io n te mp n b i r n a d Se l o p, C eg e h n d ,He e , 6 1 2 ; . ny a ies yo e h oo y, iu n h n i0 0 2 b i 0 7 0 2 Ta iun Unv ri fT c n lg Tay a ,S a x ,3 0 4) t
h型钢生产工艺
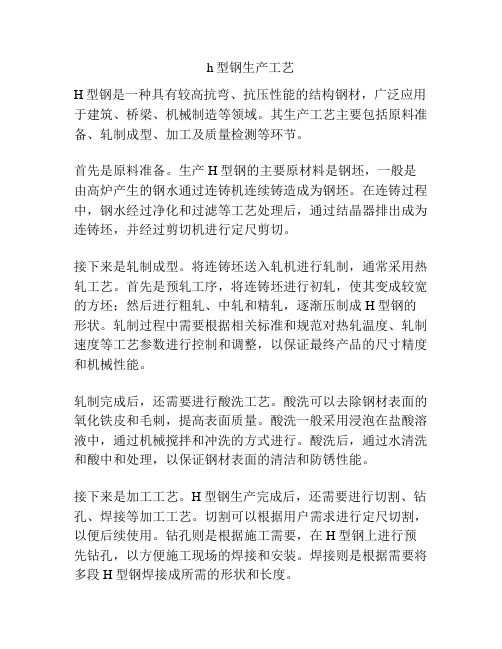
h型钢生产工艺H型钢是一种具有较高抗弯、抗压性能的结构钢材,广泛应用于建筑、桥梁、机械制造等领域。
其生产工艺主要包括原料准备、轧制成型、加工及质量检测等环节。
首先是原料准备。
生产H型钢的主要原材料是钢坯,一般是由高炉产生的钢水通过连铸机连续铸造成为钢坯。
在连铸过程中,钢水经过净化和过滤等工艺处理后,通过结晶器排出成为连铸坯,并经过剪切机进行定尺剪切。
接下来是轧制成型。
将连铸坯送入轧机进行轧制,通常采用热轧工艺。
首先是预轧工序,将连铸坯进行初轧,使其变成较宽的方坯;然后进行粗轧、中轧和精轧,逐渐压制成H型钢的形状。
轧制过程中需要根据相关标准和规范对热轧温度、轧制速度等工艺参数进行控制和调整,以保证最终产品的尺寸精度和机械性能。
轧制完成后,还需要进行酸洗工艺。
酸洗可以去除钢材表面的氧化铁皮和毛刺,提高表面质量。
酸洗一般采用浸泡在盐酸溶液中,通过机械搅拌和冲洗的方式进行。
酸洗后,通过水清洗和酸中和处理,以保证钢材表面的清洁和防锈性能。
接下来是加工工艺。
H型钢生产完成后,还需要进行切割、钻孔、焊接等加工工艺。
切割可以根据用户需求进行定尺切割,以便后续使用。
钻孔则是根据施工需要,在H型钢上进行预先钻孔,以方便施工现场的焊接和安装。
焊接则是根据需要将多段H型钢焊接成所需的形状和长度。
最后是质量检测。
对生产的H型钢进行质量检测,包括外观质量、尺寸精度和机械性能等方面。
外观质量检测主要是检查钢材表面是否有明显缺陷和损伤;尺寸精度检测主要是检查钢材的横截面尺寸、直线度和弯曲度等;机械性能检测则是通过拉伸、弯曲和冲击等试验,来确定钢材的强度、硬度和韧性等机械性能参数。
综上所述,H型钢的生产工艺包括原料准备、轧制成型、加工及质量检测等环节。
通过科学的工艺控制和质量检测手段,可以生产出符合标准和规范要求的高质量H型钢产品。
LF钢包精炼技术
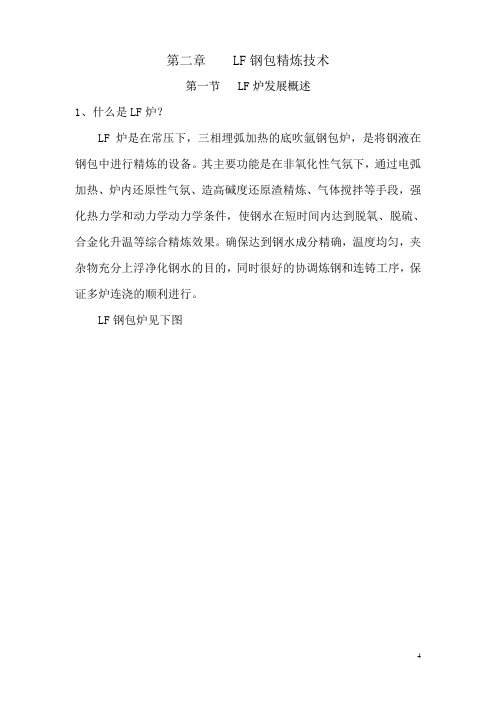
第二章 LF钢包精炼技术第一节L F炉发展概述1、什么是LF炉?LF炉是在常压下,三相埋弧加热的底吹氩钢包炉,是将钢液在钢包中进行精炼的设备。
其主要功能是在非氧化性气氛下,通过电弧加热、炉内还原性气氛、造高碱度还原渣精炼、气体搅拌等手段,强化热力学和动力学动力学条件,使钢水在短时间内达到脱氧、脱硫、合金化升温等综合精炼效果。
确保达到钢水成分精确,温度均匀,夹杂物充分上浮净化钢水的目的,同时很好的协调炼钢和连铸工序,保证多炉连浇的顺利进行。
LF钢包炉见下图2、LF炉发展过程简述LF炉精炼方法是由日本特殊钢公司在1971年开发研制的,早先以精炼处理特殊钢为主,是一种以电弧加热、氩气搅拌和渣精炼为核心的钢包精炼炉生产技术。
由于LF炉法具有多种冶金功能和使用中的灵活性,在普钢生产厂也得到广泛的应用。
目前世界钢包炉的总数中,最多的是LF 炉。
在我国,随着连铸比的大幅度提高,LF炉所处理的钢种几乎涉及从特钢到普钢的所有钢种。
LF炉法设备较为简单,投资不大。
生产中可视质量控制的需要,采用多种不同的工艺操作制度;设计中可按产品需要进行不同的配套组合,满足最终产品质量控制的要求3、LF炉的处理效果经过LF炉处理的钢可以达到很高的质量水平:(1)脱硫率可达50%~70%,可生产出硫含量<=0.01%的钢。
如果处理时间充分,甚至可达硫含量0.005%的水平。
(2)可以生产高纯度钢,钢中夹杂物总量可降低50%,大颗粒夹杂物几乎全部能去除;钢中含氧量可达到20ppm~30ppm。
(3)钢水升温速度可达到3℃/min~5℃/min。
(4)温度控制精度±3℃~5℃。
(5)成分控制精度高,可以生产出诸如[C]±0.01%、[S i]±0.02%、[Mn]±0.02%等元素含量范围很窄的钢。
4、工序组合优化目的:增强企业整体竞争力。
而竞争力主要体现在两个方面,一是能够提供其它企业无法生产的钢种;二是能在成本相同的条件下提供质量要求更优的产品,或以更低廉的成本供应质量相当的产品。
BOF LF CC(EMS)生产65Mn的冶炼实践
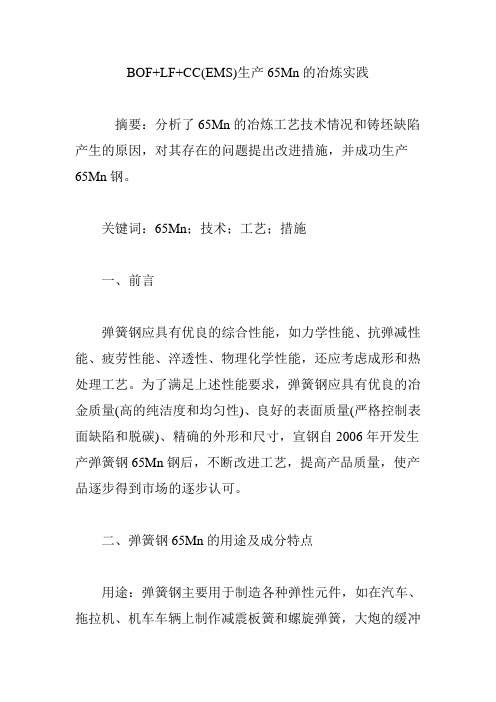
BOF+LF+CC(EMS)生产65Mn的冶炼实践摘要:分析了65Mn的冶炼工艺技术情况和铸坯缺陷产生的原因,对其存在的问题提出改进措施,并成功生产65Mn钢。
关键词:65Mn;技术;工艺;措施一、前言弹簧钢应具有优良的综合性能,如力学性能、抗弹减性能、疲劳性能、淬透性、物理化学性能,还应考虑成形和热处理工艺。
为了满足上述性能要求,弹簧钢应具有优良的冶金质量(高的纯洁度和均匀性)、良好的表面质量(严格控制表面缺陷和脱碳)、精确的外形和尺寸,宣钢自2006年开发生产弹簧钢65Mn钢后,不断改进工艺,提高产品质量,使产品逐步得到市场的逐步认可。
二、弹簧钢65Mn的用途及成分特点用途:弹簧钢主要用于制造各种弹性元件,如在汽车、拖拉机、机车车辆上制作减震板簧和螺旋弹簧,大炮的缓冲弹簧,钟表的发条等。
三、弹簧钢的冶炼生产实践(一)炼钢工艺改进1、终点碳控工艺的改进高拉碳补吹法和低拉碳增碳法两种方式,宣钢传统生产采用低拉碳增碳法。
低拉碳工艺能保证较低的出钢磷、合适的出钢温度和相对稳定的出钢碳,其工艺较为稳定,通常将钢水一次拉碳到W[c]O.10%%~0.15%,但是该工艺熔池终点[0]含量高,存在着钢铁料消耗高、脱氧合金化产生的氧化物夹杂及复合物夹杂含量高、炉衬受侵蚀严重等不足:该工艺出钢后增碳量达到0.5%以上,精炼到站碳控极不稳定,大量增碳出钢过程钢水沸腾温降幅度大。
高拉碳出钢工艺w[c]≥0.30%,可弥补上述低拉碳工艺的不足,采用高碳出钢工艺后,熔池终点W([0])可由约400PPm降至IOOPPm左右;高拉碳操作须双渣法冶炼,冶炼操作难度大,终点温度较低,但可实现0.010%以下的出钢磷。
将高碳低磷出钢工艺应用到65Mn钢转炉生产中后,为避免磷高事故的发生,制定了该钢种的750s倒炉成分要求(见表2),明确规定如倒炉磷超过表2要求,则750s后采用低拉碳工艺,确保出钢磷受控。
该工艺推广应用后,取得了很好的效果,转炉吹炼过程及终点基本受控,在实际生产中,出钢碳w[c]≥O.30%成功率达95%以上。
h钢生产工艺
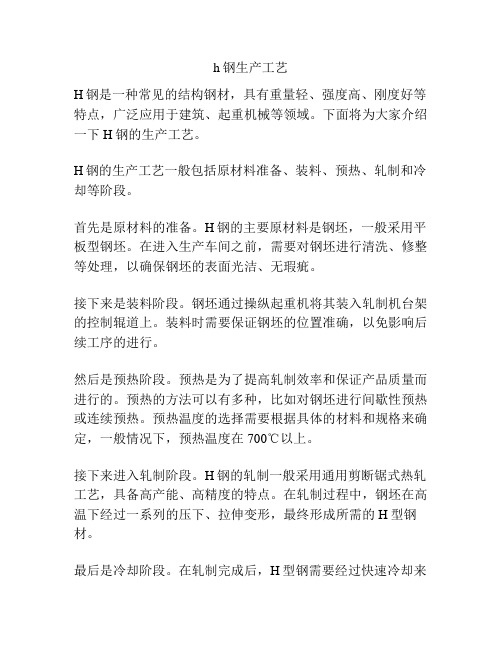
h钢生产工艺H钢是一种常见的结构钢材,具有重量轻、强度高、刚度好等特点,广泛应用于建筑、起重机械等领域。
下面将为大家介绍一下H钢的生产工艺。
H钢的生产工艺一般包括原材料准备、装料、预热、轧制和冷却等阶段。
首先是原材料的准备。
H钢的主要原材料是钢坯,一般采用平板型钢坯。
在进入生产车间之前,需要对钢坯进行清洗、修整等处理,以确保钢坯的表面光洁、无瑕疵。
接下来是装料阶段。
钢坯通过操纵起重机将其装入轧制机台架的控制辊道上。
装料时需要保证钢坯的位置准确,以免影响后续工序的进行。
然后是预热阶段。
预热是为了提高轧制效率和保证产品质量而进行的。
预热的方法可以有多种,比如对钢坯进行间歇性预热或连续预热。
预热温度的选择需要根据具体的材料和规格来确定,一般情况下,预热温度在700℃以上。
接下来进入轧制阶段。
H钢的轧制一般采用通用剪断锯式热轧工艺,具备高产能、高精度的特点。
在轧制过程中,钢坯在高温下经过一系列的压下、拉伸变形,最终形成所需的H型钢材。
最后是冷却阶段。
在轧制完成后,H型钢需要经过快速冷却来提高其机械性能。
冷却的方法可以有多种,比如自然冷却、水冷遭、风冷等,具体选择需要根据钢材的使用要求来确定。
H钢的生产工艺中还包括一些辅助工序,比如钢材切割、修整、成品检验等。
切割可以根据需要对H型钢进行定尺切割,修整则是对钢材进行矫直、修边等处理,以确保其外观美观。
成品检验则是对H型钢进行各项性能指标的测试,确保其符合国家标准要求。
总的来说,H钢的生产工艺包括原材料准备、装料、预热、轧制和冷却等阶段。
通过科学合理的工艺流程和严格的质量控制,可以保证生产出高质量、高性能的H型钢材,满足不同行业对结构材料的需求。
莱钢LF快速精炼生产优质H型钢实践
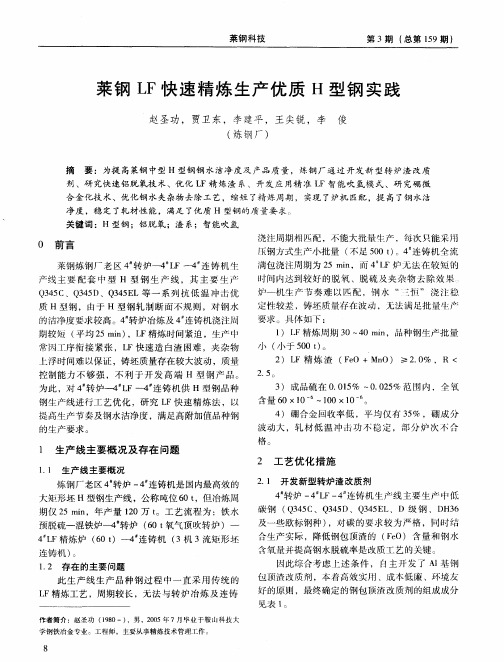
2 1 开发 新型转 炉渣 改质 剂 .
4转 炉 一 F一 铸机 生 产 线 主要 生 产 中低 4L 4连
碳 钢 ( 35 Q 4 C、Q 4 D、Q 4 E 35 3 5 L、D 级 钢 、D 3 H6
莱 钢科 技
第 3期 ( 总第 1 9期 ) 5
莱钢 L F快 速 精 炼 生 产 优 质 H 型 钢 实 践
赵圣功 ,贾卫东 ,李建平 ,王尖锐 ,李 俊
高 莱钢 中型 H型 钢钢 水 洁 净度 及 产 品质 量 ,炼 钢厂 通 过 开发 新 型转 炉 渣 改质
相 C O ・ A 2 3 a ・ A 2 3 a ・ I0 a 6 10 、C O 2 1 、C O A2 3而生 0
包顶部 ,参 考加 入 量 5 0—10 k/ 次 ,在 钢包 到 0 s炉
达4 号吹氩位采用氩气搅拌 ,保证改质剂 的充分熔 化和有效地参加反应 ,对钢水提前进行预脱氧 、 脱
硫 ,缩 短精炼 前期 成渣 时 间。 22 L . F单 次 集中快 速铝脱 氧技 术 的研 究 22 1 单次集 中铝 脱氧 机理 .. 氧气顶 吹转 炉 出钢钢水 自由氧含 量较高 ,采 用 由表 2可 看 出 ,C O和 A , a 1 生成 五个 中间相 0 性 质差 异较大 ,应 控制 钢 中钙 含量 ,避 免生成 中问
预脱硫 一混 铁 炉_4转 炉 (0t _ 6 氧气 顶 吹转 炉 )一
4L F精炼 炉 ( 0t - 6 )-4 连铸 机 ( - 3机 3流矩 形坯
连铸 机 ) 。
《LF精炼培训课件》PPT课件
喂丝速度
1~8 m/s(可调)
主机行走速度 14 m/min
导线管升角 30°
2021/6/10
15
2.3.13 供电系统 高压供电 低压供电 低压设备装机容量 2.3.14 合金加料系统 储料仓几何容积14m3 储料仓几何容积 6m3 称量料斗几何容积 振动给料器给料能力 称量精度
35 KV( 50Hz) AC380/AC220/DC24 V ~350 KW
2021/6/10
4
LF精炼工艺流程: 转炉炼钢→挡渣出钢→钢包吊到钢包车上→进准备位→测 温→预吹氩→钢包入加热位→测温、定氧、取样→加热、造 渣→调成份→取样、测温、定氧→钢包入等待位→喂丝、软 吹氩→加保温剂→连铸。
2021/6/10
5
2.2 LF精炼主要设备组成及功能 2.2.1 LF精炼炉主要设备组成
一般0-3kg/t,要控制萤石用量。
(7) 要求精炼操作尽快化渣,快速造白渣,白渣保持时间
≥15min,品种钢根据钢种要求适当增加白渣保持时间。炉渣控
制要求:R≥2.5,FeO+MnO≤1.5%。
(8) 脱氧剂加入原则:勤加、少加、散加。
2021/6/10
18
(9) 软吹前炉渣粘度调整合适,保证软吹过程中炉渣不板结。
l一电极;2—合金料斗;3一还原气氛; 4一钢水;5一透气砖;6一滑动水口;7一炉渣
2021/6/10
6
LF精炼炉由以下主要设备组成 (1) 机械设备:精炼钢包、精炼钢包车、炉盖及升降机构、 电极横臂及升降装置、电极横臂旋转装置、电极夹持器、喂丝 机、电极连接站、加料系统设备和吹氩装置等. (2) 除尘系统设备:管道、阀门等。 (3) 供电和电控系统设备:精炼变压器、高低压电控柜、操 作箱(台)等。 (4) 仪表和计算机设备。 (5) 液压系统设备:液压站和液压缸等。
LF精炼过程钢中显微夹杂物及工艺优化
第 3 3卷
L F精 炼 后 期 经 过 喂 丝 , 水 中 主 要 是 球 形 氧 化 物 夹 杂 , 它 氧 化 物 和 硫 化 物 夹 杂 尺 寸 较 小 , 中钙 铝 酸 钢 其 其
盐 和 钙 硅 酸 盐 较 多 。其 形 貌 和 能 谱 分 析 如 图 4和 表 3所 示 。
宅于图像 1
43. 4
理后显 微夹 杂物 数 量为 7 . 5 2个 / m。 比 L a r , F处 理 中 多 3. 1 8个/ mm2 升高 了 7 . 。 , 33 用 体积率 法对 2 g钢 中 显微 夹 杂 物粒 度 进行 统 0
计 , 图 6所 示 。 由 图 可 知 , F精 炼 过 程 钢 液 中 显 微 如 L
3 2 显 微 夹 杂 形 貌 与 能谱 分 析 .
扫 描 电 镜 分 析 钢 中显 微 夹 杂 物 知 , F精 炼 中 期 钢 液 中 沿 晶 硫 化 物 较 多 , 有 三 处 聚 集 状 铝 氧 化 物 , 杂 L 且 夹
物形 貌及 能谱 分 析如 图 2 图 3和表 l 表 2所示 。 、 、
系 , F精 炼 末期 弱 氩 气 软 吹 , L 以促 使 粒 径 < l 夹 杂 上 浮 。 0m
中图分类 号 : F 3 . 文献 标志 码 : T 734 A
0 引 言
某钢 厂为适 应市场形势发展 的需要 , 拓展企业生存发展 空 间, 转炉冶 炼配备 了 L 为 F精炼 , 以达 到脱氧 、 脱
1 LF精 炼 工 艺
L F精 炼 前 后 的 工 艺 流 程 是 : 转 炉 出钢 一 钢 包 底 吹 氩 一 L F吹 氩 搅 拌 一 通 电 升 温 一 造 渣 脱 氧 、 硫 一 喂 丝 一 软 吹 一 连 铸 。转 炉 出钢 过 脱
低碳含铝钢LF炉精炼工艺及精炼渣的优化
低碳含铝钢LF炉精炼工艺及精炼渣的优化发表时间:2019-04-28T09:05:25.827Z 来源:《基层建设》2019年第6期作者:季世安[导读] 摘要:LF炉精炼是目前重庆钢铁公司高级品种钢生产的关键技术之一,目前重钢LF 炉使用的精炼渣配方单一,限制了LF炉在高级品种钢生产中优势作用的充分发挥,不能满足品种钢生产的需要。
河钢集团承钢分公司河北省承德市 067001摘要:LF炉精炼是目前重庆钢铁公司高级品种钢生产的关键技术之一,目前重钢LF 炉使用的精炼渣配方单一,限制了LF炉在高级品种钢生产中优势作用的充分发挥,不能满足品种钢生产的需要。
近年来许多钢厂采用LF炉生产低碳含铝钢,如08Al、ML08Al钢种,常反映出钢水脱硫效率较低、铸坯夹杂总量较高、脆性夹杂较多、钢水增氮较多等问题,但是,要充分发挥精炼渣的作用,必须针对不同的钢种,合理设计精炼渣成分,并且在精炼渣的加入制度、LF精炼炉操作工艺方面协调配合,才能达到预期效果。
关键词:LF 精炼; 含铝钢; 渣洗工艺随着洁净钢冶炼技术的不断进步和对钢水洁净度要求的不断提高,LF 作为一种典型的二次精炼手段在炼钢工艺中的作用越来越重要。
其主要功能是加热钢水和快速脱S,结合合成渣精炼技术,能够起到对初炼钢水进一步调质的作用。
采用LF 炉生产含铝钢,常反映出钢水脱S 效率较低、钢中脆性夹杂较多、钢水增N 明显、钢水可浇性差等问题,结合承钢提钒炼钢一厂生产实际,提出含铝钢LF 炉精炼工艺优化。
一、含铝钢粗钢水特点08Al 或ML08Al 是最典型的低碳含铝钢,成品钢[C]= 0.06%∼0.08% (质量分数) ,钢中酸溶铝[Al]=0.02%∼0.06%,而16MnR、A36 等钢种,虽然[C]=0.15%∼0.18%,而酸溶铝含量也在上述范围内.这些钢中含有一定量的酸溶铝,主要是为了细化晶粒、提高韧性采用转炉冶炼这些钢种,出钢时的粗钢水具有以下特点:(1) 转炉出钢钢水[C]含量较低,[O]含量较高,常达到500×10−6∼800×10−6.要将钢水氧脱至较低的水平,则需脱除的氧多,生成的脱氧产物量也多.(2) 转炉终渣FeO 高,若下渣量过大则对后续精炼造白渣工艺带来很大的危害.(3) 在允许增碳量很少的限制下,出钢过程或LF 炉内很少采用电石、碳化硅脱氧,主要采用铝锰铁、钢芯铝、铝块等脱氧,部分钢种允许较高硅含量则采用硅铁或硅锰合金脱氧.若脱氧剂配置不当,使脱氧反应生成的脱氧产物为高熔点固相夹杂,未充分上浮排除,则残留在钢水中危害较大。
LF精炼炉除尘灰的毒化机理和资源化利用工艺
Po i s oni ng Me c han i s m a nd t he Re s o ur c e Ut i l i z a ion t Pr o c e s s o f LF As h Re mo va l
LI ANG J u n
( No .2 S t e e l ma k i n g P l a n t o f B a y i I r o n a n d S t e e l C o .L t d . , U r u mq i 8 3 0 0 2 2 ,C h i n a )
a s h r e mo va 1 .
Ke y wo r d s :L F a s h r e mo v a l ;p o i s o n i n g me c h ni a s m ;t a k e a d v a n t a g e o f
某炼钢 厂 ( 以下简称该厂)的 2 # L F精炼炉,其 除尘 器为独立的设置,与其他工艺点 的除尘器不连通 ,每天
冶炼 的钢 种:中厚 板用钢 、管线钢 、容器钢 、热轧
用钢等 ;
除尘灰的卸灰温度;<5 0℃。
收稿 日期 :2 0 1 3 - 0 6 — 2 4 ;修 回 日期 :2 0 1 3 — 0 7 — 0 5
作 者简 介 :梁
军( 1 9 6 4 一) ,男,本科 ,工 程师 ,研 究方 向为炼 钢
5 6
童
加 熟
2 0 1 3年 第 4 2卷 第 6期
v O1 . 42 N O. 6 201 3
I NDUSTRI AL HEATI NG
D OI :1 0 . 3 9 6 9  ̄ .i s s n .1 0 0 2 — 1 6 3 9 . 2 0 1 3 . 0 6 . 0 1 8
- 1、下载文档前请自行甄别文档内容的完整性,平台不提供额外的编辑、内容补充、找答案等附加服务。
- 2、"仅部分预览"的文档,不可在线预览部分如存在完整性等问题,可反馈申请退款(可完整预览的文档不适用该条件!)。
- 3、如文档侵犯您的权益,请联系客服反馈,我们会尽快为您处理(人工客服工作时间:9:00-18:30)。
中型优质H型钢LF精炼工艺优化实践赵圣功(山东钢铁股份有限公司莱芜分公司,莱芜;271104)摘要:为提高莱钢中型H型钢钢水洁净度及产品质量,炼钢厂通过开发新型转炉渣改质剂、研究快速铝脱氧技术、优化LF精炼渣系、研究硼微合金化技术、优化钢水夹杂物去除工艺,缩短了精炼周期,实现了炉机匹配,满足了优质H型钢的质量要求,提高了钢水洁净度,稳定了轧材性能。
关键词:H型钢;铝脱氧;渣系0 前言莱钢炼钢厂老区4号转炉—4号LF炉—4号连铸机生产线,主要配套中型H型钢生产,如Q345C、Q345D、Q345EL等一系列抗低温冲击优质H型钢。
由于H型钢轧制断面不规则,对钢水的洁净度要求较高。
4号转炉冶炼及4号连铸机浇注周期较短(平均25min),LF 精炼时间紧迫,生产中常因工序衔接紧张,LF快速造白渣困难,夹杂物上浮时间难以保证,铸坯质量波动较大,质量控制能力不够强,不利于开发高端H型钢产品。
为此,莱钢炼钢厂对供H型钢品种钢的4号转炉—4号LF炉—4号连铸机生产线进行工艺优化,研究LF 快速精炼法,以提高生产节奏及钢水洁净度,满足高附加值品种钢的生产要求,从而提升公司利润上升空间。
1 生产线主要概况及存在问题1.1 生产线主要概况炼钢厂老区4号转炉—4号LF炉—4号连铸机是国内最高效的大矩形坯H型钢生产线,公称吨位60t,但冶炼周期仅25min,年产量120万t。
工艺流程为:铁水预脱硫—混铁炉—4号转炉(60t氧气顶吹转炉)—4号LF精炼炉(60t)—4号连铸机(3机3流矩形坯连铸机)。
1.2 存在的主要问题此生产线在生产品种钢过程中,由于传统的LF精炼工艺周期较长,无法与转炉冶炼及连铸浇注周期相匹配,不能大批量生产,因此每次只能采用压钢方式进行小批量(不足500t)生产。
4号连铸机全流满包浇注周期为25min,而4号LF精炼炉无法在较短的时间内达到较好的脱氧、脱硫及夹杂物去除效果。
炉—机生产节奏难以匹配,钢水“三恒”浇注稳定性较差,铸坯质量波动,无法满足批量生产要求。
具体如下:1)LF精炼周期30~40min,品种钢生产批量小(小于500t)。
2)LF精炼渣(FeO+MnO)≥2.0%,R<2.5。
3)成品硫在0.015%~0.025%,全氧含量60~100ppm。
4)硼合金回收率低,平均仅有35%,硼成分波动大,轧材低温冲击功不稳定,部分炉次不合格。
2 工艺优化措施2.1 开发新型转炉渣改质剂供中型H型钢4号转炉—4号LF炉—4号连铸机生产线主要生产中低碳钢(Q345C、Q345D、Q345EL、D级钢、DH36及一些欧标钢种),对碳的要求较为严格。
因此改质剂选择要避免增碳。
同时结合生产实际,认为降低钢包顶渣的(FeO)含量和钢水含氧量并提高钢水脱硫率是改质工艺的关键。
综合考虑上述条件,自主开发了Al基钢包顶渣改质剂,本着高效实用、成本低廉、环境友好的原则,最终确定钢包顶渣改质剂的组成成分,见表1。
在出钢脱氧合金化完毕后,将改质剂加入到钢包顶部,参考加入量50~100kg/炉次,在钢包到达4号吹氩位采用氩气搅拌,保证改质剂的充分熔化和有效地参加反应,对钢水提前进行预脱氧、脱硫,缩短精炼前期成渣时间。
2.2 LF单次集中快速铝脱氧技术的研究2.2.1 单次集中铝脱氧机理氧气顶吹转炉出钢钢水自由氧含量较高,采用铝脱氧如果以一批方式加入钢液,主要形成Al2O3簇夹杂物,这些夹杂物尺寸大,碰撞结合力大,很容易浮出进入渣中,只有少量紧密簇状物和单个Al2O3颗粒滞留在钢液中,其尺寸小于30μm。
如果以两批或多批方式加入,会出现一些板型Al2O3夹杂物,夹杂物颗粒小,尺寸在5~20μm,上浮去除较为困难,所以加入铝时应尽可能快地单次集中加入,以减少小的有害Al2O3夹杂物的数量。
2.2.2 铝脱氧方式改变以往的硅钙钡、硅铝钙钡脱氧,采用铝质脱氧剂脱氧。
尽管铝有很强的脱氧能力,但在高氧位时,因其密度小,在出钢过程中加入易在钢水表面燃烧,利用率极低,加之其价格高,因此并不经济。
所以选择在出钢完毕钢水到达吹氩位时,在低氧位条件下加入(顶渣改质后的钢水氧位变低),采用钢包喂铝线法可使铝迅速溶于钢液,显著提高铝回收率,脱氧效果良好。
为缩短精炼时间,确保含铝夹杂物充分排除,在精炼进站前一次性喂入一定量的铝线(Φ12mm,Al≥98%,米重330g/m)进行强脱氧,以减少难以去除的板型Al2O3夹杂的产生。
2.3 钙处理工艺2.3.1 钙处理机理经铝脱氧的钢液中存在的Al2O3夹杂物多数熔点很高,在连铸温度下呈固态,很容易在中间包水口处聚积引起堵塞,因此向铝脱氧的钢液中加入钙,能够改变铝氧化物夹杂的形态。
钙是强脱氧剂且沸点低,进入钢液后很快成为蒸汽,在上浮过程中与钢中氧作用生成钙的氧化物。
钙处理过程中,随着夹杂物中钙的增加,夹杂物将沿着Al2O3-CaO·6Al2O3-CaO·2Al2O3-12CaO·7Al2O3-CaO·Al2O3-3CaO·Al2O3的路线改变性质[1]。
各钙铝酸盐夹杂物的性质,见表2。
根据表2可以看出,CaO和Al2O3生成的五个中间相性质差异较大,应控制钢中钙含量,避免生成中间相CaO·6Al2O3、CaO·2Al2O3、CaO·Al2O3而生成液相12CaO·7Al2O3,有利于夹杂物上浮,12CaO·7Al2O3熔点很低(1415℃),而且密度小,在钢液中集聚上浮排入炉渣,就可以使大量的这类脱氧产物在进入中间包之前从钢液中上浮去除,不仅可以减轻中间包水口堵塞问题,保证连铸顺利进行,改善钢液的浇铸性能,而且可以提高钢水清洁度、改善钢的质量。
2.3.2 钙处理方式1)为有效减少粉剂包芯线(硅钙线、钙铁线)中有害元素(S、P、C、Si)带入钢液,提高钙回收率,降低生产成本,同时满足脱氧、脱硫、改变夹杂形态、促进夹杂物上浮、净化钢液的目的,采用实芯纯钙线(理化指标见表3)对钢液进行钙处理。
2)根据钢水中[Al]与[Ca]的含量关系进行钙化处理,要求[Ca]/[Al]为0.10~0.15,使钢中铝夹杂物形成12CaO·7Al2O3并聚合上浮,达到去除夹杂物的目的,保证连铸顺利浇注。
按照铝回收率30%、钙回收率30%确定钢水中的[Ca]/[A1]在合适范围,由此确定喂硅钙线标准。
3)钙处理前要求钢水溶解氧含量低于10ppm,硫含量低于0.010%,顶渣为泡沫黄白渣,为减轻喂钙线过程钢水翻腾严重,喂线速度1.2~1.7m/s,钙处理完毕采用智能吹氩模式(流量控制在20~50NL/min)进行软吹,软吹过程采用碳花稻壳覆盖钢液面,要求钢液面微动不裸漏,时间不低于10min。
2.4 CaO-Al2O3-SiO2精炼渣系快速生成技术研究在LF精炼过程中,为合理快速地造白泡沫渣,营造出炉内稳定的还原性气氛,达到深脱硫、脱氧的目的,以充分吸收钢水中的夹杂物并对夹杂物进行变性处理,综合考虑渣中各组分对造渣的影响,将精炼终渣的成分(%)设计为:CaO=50%~60%,SiO2=15%~25%,Al2O3=10%~20%,MgO=5%~10%,见表4。
2.5 硼微合金化技术的研究2.5.1 硼元素的性质及对钢性能的影响硼的熔点2300℃,沸点2550℃,硼在室温下比较稳定,即使在盐酸或氢氟酸中长期煮沸也不起作用。
硼能和卤族元素直接化合,形成卤化硼。
从各元素氧化性顺序(Re-Zr-Ca-Al-Ti-B-Si-C-P-Nb-V-Mn-Cr-W/Mo/Fe-Co-Ni-Cu)中可以看出,硼在钢中化学性质极其活泼,能与钢中的氧、氮、硫、磷发生化学反应,高温下硼还与许多金属和金属氧化物反应,形成金属硼化物。
这些化合物通常是高硬度:耐熔、高电导率和化学惰性的物质,常具有特殊的性质。
微量(≤0.005%)的硼可以大幅提高钢的淬透性,能够提高钢的热强性能,硼微合金化可以实现细化晶粒、降低屈服强度,提高深冲性能[2]。
2.5.2 硼微合金化方式鉴于硼元素化学性质极为活泼,极易与钢水中的氧、氮等发生反应,因此选择在LF精炼工序进行硼微合金化,合金化时机选择在精炼后期,钢水脱氧完全时采用喂硼铁线(硼含量18%,米重520g/m)的方式进行合金化。
2.6 钢水夹杂物去除工艺的优化2.6.1 优化碱性覆盖剂配方软吹过程采用碱性覆盖剂覆盖钢水表面,以提高吸收Al2O3夹杂物。
根据CaO-SiO2-Al2O3三元相图,优化碱性覆盖剂配方,成分如表5所示,使其吸收Al2O3夹杂能力明显优于酸性和中性覆盖剂,且吸收Al2O3夹杂后覆盖剂的熔点降低,尤其是表面张力降低70%,有利于钢液的进一步净化。
此碱性覆盖剂保温性能较好,吸附夹杂能力强。
工业应用表明,与酸性覆盖剂相比,平均温降仅为0.32℃/min,铸坯夹杂物含量降低约15%~25%,铸坯质量明显改善。
2.6.2 强化软吹时间为进一步缩短冶炼周期,实现炉—机匹配,充分利用LF精炼大包回转台设备功能,改进吹氩管路,在一炉钢精炼完毕后将钢包转出进行软吹,同时将下一炉钢水转至精炼位进行冶炼,从而可提高生产节奏5~8min,同时满足了软吹时间8~12min。
为进一步延长弱搅拌时间,促进微细夹杂物的上浮,增上连铸大包浇注过程软吹设备,在浇注前、中期对钢水进行软吹,有效促进夹杂物上浮。
3 工艺优化后效果1)通过LF快速精炼技术的研究应用,使纯精炼时间由原来的35~40min缩短至25min 以内,满足了炉—机匹配,实现了Q345C、Q345D、Q345EL、DH36、D级钢及欧标H型钢的大批量生产,由每批次不足500t提升至2000t以上,产品质量满足了用户要求,提升了利润空间。
2)通过开发新型Al基钢包渣改质剂,使其发挥了最佳的预脱氧、脱硫能力,降低了精炼进站钢水顶渣氧化性,缩短了精炼前期成渣时间,同时含有较多量的CaO有效防止了回磷。
顶渣改质前后效果对比情况,如表6所示。
3)研究LF炉单次集中快速铝脱氧技术,通过对不同的钢水进站情况确定合适的铝线喂入量标准,大幅度提高了深脱氧能力,控制合理的[Ca]/[Al],钢水洁净度进一步提高,轧材全氧含量稳定在50ppm以下。
4)通过研究CaO-Al2O3-SiO2精炼渣系快速生成技术,提高了钢水流动性及顶渣埋弧效果,促进了快速脱氧、脱硫及夹杂物的去除,成品硫稳定在0.010%以下。
5)优化硼合金化方式,制定精准硼合金化标准,稳定了硼回收率(70%左右)及硼成分,提高了各品种钢的低温冲击性能。
6)通过LF炉快速精炼技术的研究应用,缩短了精炼周期,精炼电极消耗由0.53kg/t 钢降低到0.35kg/t钢;精炼平均电耗由42kWh/t钢降低到28kWh/t钢。