轴承基础知识(翻译)
轴承基础知识

润滑脂保留
速度能力Βιβλιοθήκη 轴承的组成 密封件Shield 防尘盖
代号 Z/2Z or ZZ Made from sheet steel 薄钢板制造 High running speed 适合高速 Unsuitable of heavy contamination and water 不适合重污染物及有水分的环境
Ball 滚珠
Symmetric spherical roller 对称球面滚子
Asymmetric 非对称滚子
Needle滚针 滚针
Tapper roller 圆锥滚子
滚动体与滚道的接触
Contact Surface
Ball and raceway —point contact 球与滚道的接触—点接触 球与滚道的接触 点接触 High speed 高转速 Low load 低载荷 低载荷 Eg: DGBB,TBB,ACBB
Rolling elements 滚动体
Separate inner and outer ring, transmit load 分隔内外圈,传递 分隔内外圈 传递 载荷 Change slipping friction to rolling friction 滑动摩擦转换为滚 动摩擦 Cylindrical roller 圆柱滚子
Bearing clearance after mounting 轴承的安装游隙
Inner ring interference fit with shaft 轴承内圈与轴过盈配合,内 轴承内圈与轴过盈配合, 圈膨胀
Outer ring transition fit with box
外圈与箱体过渡配合, 外圈与箱体过渡配合,外圈 紧缩
3 用于球轴承 10/3用于滚子轴承 用于滚子轴承 1) 系数 n 代表失败可能性 代表失败可能性, 例如: 例如:即区别在必须可靠 性和100 % 之间。 之间。 性和
轴承基础知识

Speed capability
什么是润滑
Lubricant film
Lubrication - prevents direct metallic contacts between the bearing components - prevents wear - protects against corrosion
Y-轴承单元
- 能适应初始的不同心误差 - 可实现经济的轴承排列方式 - 安装简便 - 可以安装密封件
平面轴承(滑动轴承)
球面滑动轴承与关节轴承
® GLYCODUR dry sliding bearings
Suitable where regular tilting movements or oscillations occur at relatively low sliding velocities
承载能力
相同内径、外径不同类型轴承的承载能力
影响速度的因素 什么是润滑?
提高转速 m 载荷小 m 高精度 m 正确的游隙 m 最优化的润滑 m 有效的冷却 降低转速 m 大载荷 m 精度低 m 过渡润滑 m 润滑不足 m 润滑粘度太高 m 冷却不良
轴承选择的主要考虑的几个方面
有效空间 对中
速度
TVN
PDN
SNL SOFN
SD
SDG
SDR
关于SKF的型号
基本型号表示:
• 产品类型 • 标准设计 • 尺寸
补充型号表示:
• 其它设计(变化) • 轴承组件 • 特殊轴承的类型
滚动轴承型号标识
轴承类型
径向轴承, 宽度 (B,T)
推力轴承, 高度 (H)
外径 (D) to 内径 (d)
轴承基础知识

轴承基础知识轴承的定义轴承是一个支撑轴的零件,它可以引导轴的旋转,也可以承受轴上空转的零件,轴承可分为滚动轴承和滑动轴承,一般来说的轴承指的是滚动轴承。
一、滚动轴承的定义将运转的轴与轴座之间的滑动摩擦变为滚动摩擦,从而减少摩擦损失的一种精密的机械元件,叫滚动轴承。
1、滚动轴承的结构及分类1.1结构滚动轴承(以下简称轴承)一般由内圈、外圈、滚动体和保持架组成。
(如图1.1)内圈与外圈之间装有若干个滚动体,由保持架使其保持一定的间隔以免相互接触和碰撞,从而进行圆滑的滚动。
轴承按照滚动体的列数,可以分为单列、双列和多列。
1)、内圈、外圈和滚动体内圈、外圈上滚动体滚动的部分称作滚动面。
球轴承套圈的滚动又称作沟道。
一般来说,内圈的内径、外圈的外径在安装时分别与轴和外壳有适当的配合。
推力轴承的内圈、外圈分别称作轴圈和座圈。
2)、滚动体滚动体分为球和滚子两大类,滚子根据其形状又分为圆柱滚子、圆锥滚子、球面滚子和滚针。
3)、保持架保持架将滚动体部分包围,使其在圆周方向保持一定的间隔。
保持架按工艺不同可分为冲压保持架、车制保持架、成形保持架和销式保持架。
按照材料不同可分为钢保持架、铜保持架、尼龙保持架及酚醛树脂保持架。
1.2分类轴承受负荷时作用于滚动面与滚动体之间的负荷方向与垂直于轴承中心线的平面内所形成的角度称作接触角,接触角小于45°主要承受径向负荷称为向心轴承,在45°~90°之间主要承受轴向负荷称为推力轴承,根据接触角和滚动体的不同,通用轴承分类如下:深沟球轴承(单、双列)向心球轴承角接触球轴承(单、双列)四点接触球轴承调心球轴承向心圆柱滚子轴承(单、双、四列)轴向心滚子轴承圆锥滚子轴承(单、双、四列)滚承滚针轴承(单、双列)动调心滚子轴承轴承推力球轴承推力球轴承(单、双列)推力角接触球轴承(单、双向)推力推力圆柱滚子轴承轴推力滚子轴承推力圆锥滚子轴承承推力滚针轴承推力调心滚子轴承2、滚动轴承的主要尺寸与基本代号方法2.1滚动轴承基本尺寸对于轴承的主要尺寸,国际标准化组织(ISO)为保证国际上的互换性和生产中的经济性,已制定了统一的国际标准[ISO15、ISO355、ISO104],分别对向心轴承、圆锥滚子、推力轴承的主要外形尺寸作了相应的规定,即对轴承的内径、外径宽度以及倒角尺寸进行了系列化、标准化,我国标准也等效采用了ISO 标准的规定。
轴承外文翻译

BEARING LIFE ANALYSISABSTRACTNature works hard to destroy bearings, but their chances of survival can be improved by following a few simple guidelines. Extreme neglect in a bearing leads to overheating and possibly seizure or, at worst, an explosion. But even a failed bearing leaves clues as to what went wrong. After a little detective work, action can be taken to avoid a repeat performance.1 .WHY BEARINGS FAILAn individual bearing may fail for several reasons; however, the results of an endurance tes t series are only meaningful when the test bearings fail by fatigue-related mechanisms. The experimenter must control the test process to ensure that this occurs. Some of the other failure modes that can be experienced are discussed in detail by Tallian [19.2]. The following paragraphs deal with a few specific failure types that can affect the conduct of a life test sequence.In Chapter 23, the influence of lubrication on contact fatigue life is discussed from the standpoint of EHL film generation. There ar e also other lubrication-related effects that can affect the outcome of the test series. The first is particulate contaminants in the lubricant. Depending on bearing size, operating speed, and lubricant rheology, the overall thickness of the lubricant film developed at the rolling element-raceway contacts may fall between 0.05 and 0.5 m . Solid particles and damage the raceway and rolling element surfaces, leading to substantially shortened endurances. This has been amply demonstrated by Sayles and MacPherson [19.6] and others.Therefore, filtration of the lubricant to the desired level is necessary to ensure meaningful test result. The desired level is determined by the application which the testing purports to approximate. If thi s degree of filtration is not provided, effects of contamination must be considered when evaluating test results. Chapter 23 discusses the effect of various degrees of particulate contamination, and hence filtration, on bearing fatigue life.The moisture content in the lubricant is another important consideration. It has long been apparent that quantities of free water in the oil cause corrosion of the rolling contact surfaces and thus have a detrimental effect on bearing life. It has been further shown b y Fitch[19.7] and others, however, that water levels as low as 50-100 parts per million(ppm) may also have a detrimental effect, even with no evidence of corrosion. This is due to hydrogen embrittlement of the rolling element and raceway material. See als o Chapter 23. Moisture control in test lubrication systems is thus a major concern, and the effect of moisture needs to be considered during the evaluation of life test results. A maximum of 40 ppm is considered necessary to minimize life reduction effects.The chemical composition of the test lubricant also requires consideration. Most commercial lubricants contain a number of proprietary additives developed for specific purposes; for example, to provide antiwear properties, to achieve extreme pressure and/or thermal stability, and to provide boundary lubrication in case of marginal lubricant films. These additives can also affect the endurance of rolling bearings, either immediately or after experiencing time-related degradation. Care must be taken to ensu re that the additives included in the test lubricant will not suffer excessive deterioration as a result of accelerated life test conditions. Also for consistency of results and comparing life test groups, it is good practice to utilize one standard test lubricant from a particular producer for the conduct of all general life tests.The statistical nature of rolling contact fatigue requires many test samples to obtain a reasonable estimate of life. A bearing life test sequence thus needs a long time. A majo r job of the experimentalist is to ensure the consistency of the applied test conditions throughout the entire test period. This process is not simple because subtle changes can occur during the test period. Such changes might be overlooked until their effects become major. At that time it is often too late to salvage the collected data, and the test must be redone under better controls.For example, the stability of the additive packages in a test lubricant can be a source of changing test conditions. Some lubricants have been known to suffer additive depletion after an extended period of operation. The degradation of the additive package can alter the EH L conditions in the rolling content, altering bearing life. Generally, the normal chemical tests used to evaluate lubricants do not determine the conditions of the additive content. Therefore if a lubricant is used for endurance testing over a long time, a sample of the fluid should be returned to the producer at regular intervals, say annually, for a detailed evaluation of its condition.Adequate temperature controls must also be employed during the test. The thickness of the EHL film is sensitive to the contact temperature. Most test machines are located in standard industrial environments where rather wide fluctuations in ambient temperature are experienced over a period of a year. In addition, the heat generation rates of individual bearings can vary as a result of the combined effects of normal manufacturing tolerances. Both of these conditions produce variations in operating temperature levels in a lot of bearings and affect the validity of the life data. A means must be provided to monitor and control the operating temperature level of each bearing to achieve a degree of consistency. A tolerance level of 3C is normally considered adequate for the endurance test process.The deterioration of the condition of the mounting hardware used with the bearings is another area requiring constant monitoring. The heavy loads used for life te sting require heavy interference fits between the bearing inner rings and shafts. Repeated mounting and dismounting of bearings can produce damage to the shaft surface, which in turn can alter the geometry of a mounted ring. The shaft surface and the bore of the housing are also subject to deterioration from fretting corrosion. Fretting corrosion results from the oxidation of the fine wear particlesgenerated by the vibratory abrasion of the surface, which is accelerated by the heavy endurance test loading.This mechanism can also produce significant variations in the geometry of the mounting surfaces, which can alter the internal bearing geometry. Such changes can have a major effect in reducing bearing test life.The detection of bearing failure is also a major consideration in a life test series. The fatigue theory considers failure as the initiation of the first crack in the bulk material. Obviously there is no way to detect this occurrence in practice. To be detectable the crack must propagate to the surface and produce a spall of sufficient magnitude to produce a marked effect on an operating parameter of the bearing: for example, noise, vibration, and/or temperature. Techniques exit for detecting failures in application systems. The ability of these sys tems to detect earl y signs of failure varies with the complexity of the test system, the type of bearing under evaluation, and other test conditions. Currentl y no single system exists that can consistently provide the failure discrimination necessary for a ll types of bearing life tests. It is then necessary to select a system that will repeatedl y terminate machine operation with a consistent minimal degree of damage.The rate of failure propagation is therefore important. If the degree of damage at test ter mination is consistent among test elements, the only variation between the experimental and theoretical lives is the lag in failure detection. In standard through-hardened bearing steels the failure propagation rate is quite rapid under endurance test cond itions, and this is not a major factor, considering the t ypical dispersion of endurance test data and the degree of confidence obtained from statistical analysis. This may not, however, be the case with other experimental materials or with surface-hardened steels or steels produced by experimental techniques. Care must be used when evaluating these latter results and particularl y when comparing theexperimental lives with those obtained from standard steel lots.The ultimate means of ensuring that an endura nce test series was adequately controlled is the conduct of a post-test analysis. This detailed examination of all the tested bearings uses high-magnification optical inspection, higher-magnification scanning electron microscopy, metallurgical and dimensio nal examinations, and chemicalevaluations as required. The characteristics of the failures are examined to establish their origins and the residual surface conditions are evaluated for indications of extraneous effects that may have influenced the bearin g life. This technique allows the experimenter to ensure that the data are indeed valid. The “Damage Atlas” compiled by Tallian et al. [19.8] containing numerous black and white photographs of the various bearing failure modes can provide guidance for thes e types of determinations. This work was subsequently updated by Tallian [19.9], now including color photographs as well.The post-test analysis is, by definition, after the fact. To provide control throughout the test series and to eliminate all quest ionable areas, the experimenter should conduct a preliminary study whenever a bearing is removed from the test machine. In this portion of the investigation each bearing is examined optically at magnifications up to 30 for indications of improper or out-of-control test parameters. Examples of the types of indications that can be observed are given in Figs. 19.2-19.6.Figure 19.2 illustrates the appearance of a typical fatigue-originated spall on a ball bearing raceway. Figure 19.3 contains a spalling failure on the raceway of a roller bearing that resulted from bearing misalignment, and Fig. 19.4 contains a spalling failure on the outer ring of a ball bearing produced by fretting corrosion on the outer diameter. Figure 19.5 illustr ates a more subtle form of test alteration, `where the spalling failure originated from the presence of a debris denton the surface. Figure 19.6 gives an example of a totally different failure mode produced by the loss of internal bearing clearance due to thermal unbalance of the system.The last four failures are not valid fatigue spalls and indicate the need to correct the test methods. Furthermore, these data points would need to be eliminated from the failure data to obtain a valid estimate of the experimental bearing life.2 .AVOIDING FAILURESThe best way to handle bearing failures is to avoid them.This can be done in the selection process by recognizing critical performance characteristics.These include noise,starting and running torque,stiffness,non-repetitive run out,and radial and axial play.In some applications, these items are so critical that specifying an ABEC level alone is not sufficient.Torque requirements are determined by the lubricant,retainer,raceway quality(roundness cross curvature a nd surface finish),and whether seals or shields are used.Lubricant viscosity must be selected carefull y because inappropriate lubricant,especially in miniature bearings,causes excessive torque.Also,different lubricants have varying noise characteristics th at should be matched to the application. For example,greases produce more noise than oil.Non-repetitive run out(NRR)occurs during rotation as a random eccentricit y between the inner and outer races,much like a cam action.NRR can be caused by retainer tole rance or eccentricities of theraceways and balls.Unlike repetitive run out, no compensation can be made for NRR.NRR is reflected in the cost of the bearing.It is common in the industry to provide different bearing types and grades for specific applications.For example,a bearing with an NRR of less than 0.3um is used when minimal run out is needed,such as in disk—drive spindle motors.Similarly,machine—tool spindles tolerate only minimal deflections to maintain precision cuts.Consequently, bearings are manufactured with low NRR just for machine-tool applications.Contamination is unavoidable in many industrial products,and shields and seals are commonly used to protect bearings from dust and dirt.However,a perfect bearing seal is not possible because of the movement between inner and outer races.Consequently,lubrication migration and contamination are always problems.Once a bearing is contaminated, its lubricant deteriorates and operation becomes noisier.If it overheats,the bearing can seize.At the very least,contamination causes wear as it works between balls and the raceway,becoming imbedded in the races and acting as an abrasive between metal surfaces.Fending off dirt with seals and shields illustrates some methods for controlling contamination.Noise is as an indicator of bearing quality.Various noise grades have been developed to classify bearing performance capabilities.Noise anal ysis is done with an Ander-on-meter, which is used forquality control in bearing production and also when failed bearings ar e returned for anal ysis. A transducer is attached to the outer ring and the inner race is turned at 1,800rpm on an air spindle. Noise is measured in andirons, which represent ball displacement in μm/rad.With experience, inspectors can identify the smalles t flaw from their sound. Dust, for example, makes an irregular crackling. Ball scratches make a consistent popping and are the most difficult to identify. Inner-race damage is normally a constant high-pitched noise, while a damaged outer race makes an inte rmittent sound as it rotates.Bearing defects are further identified by their frequencies. Generally, defects are separated into low, medium, and high wavelengths. Defects are also referenced to the number of irregularities per revolution.Low-band noise is the effect of long-wavelength irregularities that occur about 1.6 to 10 times per revolution. These are caused by a variety of inconsistencies, such as pockets in the race. Detectable pockets are manufacturing flaws and result when the race is mounted too tightly in multiple jaw chucks.Medium-hand noise is characterized by irregularities that occur 10 to 60 times per revolution. It is caused by vibration in the grinding operation that produces balls and raceways. High-hand irregularities occur at 60 to 300 times per revolution and indicate closely spaced chatter marks or widely spaced, rough irregularities.Classifying bearings by their noise characteristics allows users to specify a noise grade in addition to the ABEC standards used by most manufacturers. ABEC defines physical tolerances such as bore, outer diameter, and run out. As the ABEC class number increase (from 3 to 9), tolerances are tightened. ABEC class, however, does not specify other bearing characteristics such as raceway quality, finish, or noise. Hence, a noise classification helps improve on the industry standard.(come from Lu,Zhengran . Study of the bearing capacity of fastener steel tube full hall formwork support using the theory ofstability of pressed pole with three-point rotation restraint[J] . China Civil Engineering Journal 2012-5 )轴承寿命分析摘要自然界苛刻的工作条件会导致轴承的失效,但是如果遵循一些简单的规则,轴承正常运转的机会是能够被提高的。
bearing翻译

bearing翻译
bearing翻译
bearing是英文中的一个常用词,它在机械领域里特别常见,其中包含了很多重要的概念。
其中,"bearing"的意思就是"轴承",这是一种机械零件,可以在机械系统中支撑或者传动其他部件。
轴承是一种精密的部件,其目的是减少摩擦和支撑传动机构中的转动部件。
它们通常由内部轴承和外部轴承组成,内部轴承使物体能够转动,而外部轴承则支撑物体不受外力影响。
轴承可以用于支撑、旋转或移动物体,因此在工程中有着重要的作用。
轴承通常由两个部分组成:内圈轴承和外圈轴承。
内圈轴承由一个圆筒形的金属套筒和一个内表面的滚子组成,圆筒形的金属套筒起着保护滚子的作用,而滚子则支撑物体不受外力影响,使物体能够转动或移动。
外圈轴承则由一个圆筒形的金属套筒和弹性滚珠组成,滚珠支撑物体不受外力影响,使物体能够转动或移动。
轴承的材料也是非常重要的,一般来说,轴承的材料选择应根据使用环境来确定。
一般来说,轴承的材料选择应当考虑其承受压力的大小、温度、摩擦系数等。
轴承的型号也是很重要的,它的型号可根据轴承的尺寸、材料、承载能力、应用等因素来确定。
常见的轴承型号有滚动轴承、调心滚子轴承、深沟球轴承、滚针轴承、圆柱滚子轴承、滑动轴承等。
综上所述,bearing翻译为轴承,是一种机械零件,由内圈轴承和外圈轴承组成,用于支撑、旋转或移动物体,材料选择应根据使用环境来确定,型号可根据尺寸、材料、承载能力、应用等因素来确定。
轴承基础知识介绍
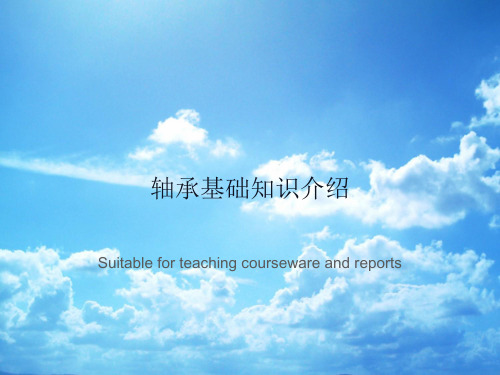
①前置代号字母
∣ 轴 承 分 部 件 代 号
②基本代号数字、字母 ③后置代号字母+数字
五 四 三 二一
∣ ∣∣
∣
类 宽直 内
型 度径 径
代 系系 代 号 列列 号
代代
号号
∣ ∣∣ ∣ ∣ ∣ ∣
密保 特 公内游 其 封持 殊 差部隙 他 与架 轴 等结代 代 防及 承 级构号 号 尘材 材 代代 代料 料 号号 号代 代
• 工作时滚动体在内外圈间滚
动保持架将滚动体均匀地隔 开以减少滚动体之间的摩擦 和磨损
滚子的类型
滚珠
球面滚柱 对称型
球面滚柱 不对称型
圆柱滚子
针形滚子
锥形滚子
几种常见的轴承形式
滚珠轴承
滚柱轴承
滚柱和滚珠与滚道的接触形式
1、圆柱滚子轴承2、深沟球轴承 3、圆锥滚子轴承 4、双列深沟球轴承 5、角接触轴承 6、调心滚子轴 承
难的运转部位
图片
• 滑动轴承图片
五、轴承的安装与拆卸
1、轴承的安装环境: 轴承的安装要在干燥、清洁的环境中进
行
安装前的准备工作:
· 应准备好所必需的部件、工具及设备; · 应仔细检查轴和外壳的配合表面的加工
质量;
· 应清除毛刺保持安装表面清洁
注意:在安装准备工作没有完成前不要拆开 轴承包装以免使轴承受到污染
用油箱加热轴承时在距箱底一定距离处应有 一网栅或者用钩子吊着轴承轴承不能放到箱底上以 防沉杂质进入轴承内或不均匀的加热油箱中必须有 温度计严格控制油温不得超过100℃以防止发生回 火效应使套圈的硬度降低用于过盈配合
加热轴承一定要掌握好温度切不可加热到 100 ℃以上否则 轴承会发生回火现象致使套圈硬度 和精度降低影响轴承的使用寿命
轴承基础知识
INA 和FAG 的滚动轴承能够满足疲劳强度、耐磨性、 硬度、韧性和结构稳定性的要求。用于套圈和滚动体 的材料一般是低合金,高纯净度的淬透铬钢材。对承 受大的冲击载荷和交变应力的轴承,也可用渗碳钢( 协 议供货)。
内圈:1、安装在设备的轴上,通常是转动的部分。 2、内孔有圆柱形和圆锥形两种。 3、外表面是滚道,形状取决于滚动体
K(1:12)
K30(1:30)
九、轴承的代号
FAG型号: 635.2RSR、6207、7205B.MP、 B7215C.T.P4S.UL、 H、 QJ213.MPA、1220.K.M.C3、51218、 NU2234E.M1.C3、NN3010AS.K.M.SP、 32214.A、241/710B.K30.MB、 、29348E1
公差变小,精度等级提高
PN为普通精度等级,在轴承后缀未标注精度的情 况下,默认轴承精度为PN级。
六、轴承的使用温度
轴承的使用温度受轴承材质影响会有所不同。经过特殊 的热处理,轴承的使用温度会有提高。 S0 S1 S2 S3 S4
150℃
200℃
250℃
300℃ 350℃
没有特殊后缀的轴承使用温度一般不能超过120℃。
大连鸿辉贸易有限公司
轴承基础知识
一、轴承的含义及应用
轴承(bearing):用于确定旋转轴与 其他零件相对运动位置,起支承或导 向作用的零部件。
(在机械传动过程中起支撑导向,减小摩擦,承受 载荷的作用)
轴承的广泛应用于各个行业:航空工 业、汽车工业、各种机械设备、造纸 厂、水泥厂、发电厂等工厂。
径向游隙(Sr)轴向游隙(Sa)
轴承的游隙组(径向游隙组) C1 C2 C0/CN 游隙组增大 C3 C4 C5
轴承基础知识(中英对照)
一、轴承(一)滚动轴承总论1. 滚动轴承 rolling bearing ['rəuliŋ]2. 单列轴承 single row bearing [rau]3. 双列轴承 double row bearing4. 多列轴承 multi-row bearing ['mʌlti]5. 满装滚动体轴承 full complementbearing [ful] ['kɔmplimənt]6. 角接触轴承 angular contact bearing ['æŋɡjulə]7. 调心轴承 self-aligning bearing [ə‘lainiŋ]8. 可分离的轴承 separable bearing ['sepərəbl]9. 不可分离轴承 non-separable bearing10. 单列深沟球轴承是球轴承中最普通的种类,应用及其广泛。
Single row deep groove ball bearings are the most common type of rolling bearing and are used in a wide variety [və'raiəti] of applications.The moment of friction of high-speed grease-lubricated rolling bearing determines its power consumption and heatoutput,and the heat output has a direct effect on its temperature rise.在高速脂润滑滚动轴承中,摩擦力矩的大小决定了轴承的功率消耗和发热量的大小,发热量的大小直接影响轴承的温升失效。
轴承英语基础知识培训(二)(10.4.29)一、轴承(一)滚动轴承总论10. 英制轴承 inch bearing inch [intʃ]11. 开型轴承 open bearing open ['əupən]12. 密封圈轴承 sealed bearing sealed [si:ld]13. 防尘盖轴承 shielded bearing shielded ['ʃi:ldid]14. 闭型轴承 capped bearing15. 预润滑轴承 prelubricatedbearing [pri:‘ljubrikeitid]16. 仪器精密轴承 instrument precisionbearing ['instrumənt] [pri'siʒən]17. 组配轴承 matched bearingSealed bearing system reduces clamping pressure and increases bearing life.密封的轴承系统减少夹持力并增加轴承寿命。
轴承论文中英文资料外文翻译文献
中英文资料外文翻译文献EXTENDING BEARING LIFEAbstract:Nature works hard to destroy bearings, but their chances of survival can be improved by following a few simple guidelines. Extreme neglect in a bearing leads to overheating and possibly seizure or, at worst, an explosion. But even a failed bearing leaves clues as to what went wrong. After a little detective work, action can be taken to avoid a repeat performance.Keywords: bearings failures lifeBearings fail for a number of reasons,but the most common are misapplication,contamination,improper lubricant,shipping or handling damage,and misalignment. The problem is often not difficult to diagnose because a failed bearing usually leaves telltale signs about what went wrong.However,while a postmortem yields good information,it is better to avoid the process altogether by specifying the bearing correctly in The first place.To do this,it is useful to review the manufacturers sizing guidelines and operating characteristics for the selected bearing.Equally critical is a study of requirements for noise, torque, and runout, as well as possible exposure to contaminants, hostile liquids, and temperature extremes. This can provide further clues as to whether a bearing is right for a job.1 Why bearings failAbout 40% of ball bearing failures are caused by contamination from dust, dirt, shavings, and corrosion. Contamination also causes torque and noise problems, and is often the result of improper handling or the application environment.Fortunately, a bearing failure caused by environment or handling contamination is preventable,and a simple visual examination can easily identify the cause.Conducting a postmortem il1ustrates what to look for on a failed or failing bearing.Then,understanding the mechanism behind the failure, such as brinelling or fatigue, helps eliminate the source of the problem.Brinelling is one type of bearing failure easily avoided by proper handing andassembly. It is characterized by indentations in the bearing raceway caused by shock loading-such as when a bearing is dropped-or incorrect assembly. Brinelling usually occurs when loads exceed the material yield point(350,000 psi in SAE 52100 chrome steel).It may also be caused by improper assembly, Which places a load across the races.Raceway dents also produce noise,vibration,and increased torque.A similar defect is a pattern of elliptical dents caused by balls vibrating between raceways while the bearing is not turning.This problem is called false brinelling. It occurs on equipment in transit or that vibrates when not in operation. In addition, debris created by false brinelling acts like an abrasive, further contaminating the bearing. Unlike brinelling, false binelling is often indicated by a reddish color from fretting corrosion in the lubricant.False brinelling is prevented by eliminating vibration sources and keeping the bearing well lubricated. Isolation pads on the equipment or a separate foundation may be required to reduce environmental vibration. Also a light preload on the bearing helps keep the balls and raceway in tight contact. Preloading also helps prevent false brinelling during transit.Seizures can be caused by a lack of internal clearance, improper lubrication, or excessive loading. Before seizing, excessive, friction and heat softens the bearing steel. Overheated bearings often change color,usually to blue-black or straw colored.Friction also causes stress in the retainer,which can break and hasten bearing failure.Premature material fatigue is caused by a high load or excessive preload.When these conditions are unavoidable,bearing life should be carefully calculated so that a maintenance scheme can be worked out.Another solution for fighting premature fatigue is changing material.When standard bearing materials,such as 440C or SAE 52100,do not guarantee sufficient life,specialty materials can be recommended. In addition,when the problem is traced back to excessive loading,a higher capacity bearing or different configuration may be used.Creep is less common than premature fatigue.In bearings.it is caused by excessive clearance between bore and shaft that allows the bore to rotate on the shaft.Creep can be expensive because it causes damage to other components in addition to the bearing.0ther more likely creep indicators are scratches,scuff marks,or discoloration to shaft and bore.To prevent creep damage,the bearing housing and shaft fittings should be visually checked.Misalignment is related to creep in that it is mounting related.If races are misaligned or cocked.The balls track in a noncircumferencial path.The problem is incorrect mounting or tolerancing,or insufficient squareness of the bearing mounting site.Misalignment of more than 1/4·can cause an early failure.Contaminated lubricant is often more difficult to detect than misalignment or creep.Contamination shows as premature wear.Solid contaminants become an abrasive in the lubricant.In addition。
轴承基础知识_0002
大挡边采用采用优化 轮廓设计,并采用粗 磨、精磨和挡边超精 工艺,精心设计的轮 廓和精密加工保证了 轴承在工作时这一块 滑动区域的润滑油膜 的形成
圆柱滚子轴承
特点 承受大的径向负荷 •高速 •安装方便 •多种设计适合不同的应用 •适用于内外圈都采用过盈配合 •内部设计的特点适用于非定位轴承 缺点 承受角度对中误差的能力非常有限
农机圆锥滚子轴承
农机用圆锥滚子轴承应用特点: •低速 •重载
车桥主减、差速器,轮边
•同时承受轴向和径向负荷 •高的刚度要求
变 速 箱
PEER农机圆锥轴承特点
优化了套圈热处 理,保证滚道的 硬度 改善滚子球基面 的粗糙度有效地 保证了润滑油膜 的质量
优化了滚道轮 廓曲线减少了 边缘应力集中, 具有更大的承 载能力
轮系传动
行走支重轮、驱动轮…
农机用深沟球轴承应用特点: •低速
变 速 箱
•重载
•环境恶劣(泥水、粉尘、温度差异大) •使用维护不规范
PEER农机深沟球轴承特点
高密封性能的密封
高等级的钢材,锻打 成型工艺
宽温度范围的油脂和比 较大的填脂量 滚道超精+高精度等 级钢球,降低轴承的 旋转扭矩和温升
批量产品稳定
PEER BEARING COMPANY
轴承基础知识
Shanghai peer bearing co,. ltd
内容
• 滚动轴承的分类 • 滚动轴承的代号 • 滚动轴承的密封 • 滚动轴承保持架 • 滚动轴承的润滑 • 滚动轴承精度和游隙
1 2 3 4 5 6
滚动轴承的分类
• 滚动轴承的分类 • 滚动轴承的代号 • 滚动轴承的密封 • 滚动轴承保持架 • 滚动轴承的润滑 • 滚动轴承精度和游隙
- 1、下载文档前请自行甄别文档内容的完整性,平台不提供额外的编辑、内容补充、找答案等附加服务。
- 2、"仅部分预览"的文档,不可在线预览部分如存在完整性等问题,可反馈申请退款(可完整预览的文档不适用该条件!)。
- 3、如文档侵犯您的权益,请联系客服反馈,我们会尽快为您处理(人工客服工作时间:9:00-18:30)。
Seal
Rolling elements Inner ring Outer ring Cage Seal
Rolling elements name the bearing
Ball Spherical roller (symmetrical) Spherical roller (asymmetrical)
Suffix /C1 /C2 /CN /C3 /C4 /C5
clearance less than C2 less than Normal Normal greater than Normal greater than C3 greater than C4
Example: 6210/C3 = Deep groove ball bearing with clearance greater than Normal CN does not normally appear in the bearing designation
Rolห้องสมุดไป่ตู้er bearings
Cylindrical roller bearing Taper Needle roller roller bearing bearing Spherical roller bearing
Ball bearing properties
Deep groove ball bearing Angular contact Self-aligning ball bearing ball bearing
Spherical roller bearings
Symmetrical rollers for maximum life under any conditions Floating guide ring gives minimum friction and ensures reliable operation Window-type steel cages strong and tolerant to high temperatures
1950 1990
22322 Bearing size 22317 E Outside diameter (mm) 240 180 Mass (kg) 18,00 7,25 46,50 Load carrying 46,70
capacity (tonnes)
energy and lubricant savings through lower friction integrated functions e.g. attachment flanges and sensors
radial load carrying capacity
axial load carrying capacity
speed capability
can accdommodate misalignment
Taper roller bearings
optimized SKF design
- Logarithmic contact profile plus optimised surface finish increases service life - Improved roller end/flange contact greatly reduces friction - Optimum utilisation of cross section
Thrust bearings
Thrust ball bearing single direction
Thrust ball bearing single direction with sphered housing washer
Thrust ball bearing double direction
Cylindrical roller Needle roller
Taper roller
Radial rolling bearings Radial rolling bearings
Ball bearings
Deep groove Angular Self-aligning ball bearing contact ball bearing ball bearing
Load carrying capacity
Basic dynamic load rating C P P
The ISO life equation
Basic static load rating C 0 P
0
P
0
The static safety factor
L =
10
10
( )
C p P
s
0 0
What is friction?
Plain bearings sliding friction
m
m
Rolling bearings rolling friction
Bearing loads
Radial load
F
r
Combined load
Axial load
F
a
The components of a bearing
Bearing Basics 轴承基础知识
SKF轴承基础知识介绍
轴承是机械零件
轴承的设计目的 减少摩擦 承受载荷 引导运动
轴承的发展历史-永无止境
1794
1869
1100 B.C.
40 A.D.
3500 B.C. 1995
SKF的历史
1907 Sven Wingquist invented the self-aligning ball bearing Aktiebolaget Svenska Kullagerfabriken (SKF) founded in Gothenburg 1910 Sales offices opened in France and Germany 1911 SKF patented the spherical roller bearing The first SKF maufacturing plant outside Sweden started operations at Luton in England 1913Half the shares of Norma Compagnie GmbH, Bad Cannstatt, Germany, were acquired by SKF 1916 The first American factory was built 1920 SKF produced the first spherical roller bearings 1996 SKF is the world leader in bearings, has some 80 manufacturing facilities worldwide and is operating in more than 130 countries.
-
Bearing clearance
Radial clearance Axial clearance
Clearance
Normal clearance Reduced clearance because of tight fit Increased clearance because of temperature
Sven Wingquist, the inventor of the self-aligning ball bearing (1907) and the spherical roller bearing (1911)
SKF Quality Policy
"To market only products and services that will ensure customer satisfaction: Functionality Reliability Performance Availability Service"
s =
0
C
0
L = basic rating life, millions of revolutions C = basic dynamic load rating, N P = equivalent dynamic bearing load, N p = exponent of the life equation With the load P = C the L life will be 1 million revolutions
Continual improvements
Downsizing The improvements have led to
Bearings with longer service life higher reliability higher load carrying capacity higher speed capability higher precision quieter running
Cylindrical roller bearings
NU NJ NUP - more and larger rollers
- Logarithmic contact profile plus optimised surface finish
N NU+HJ NJ+HJ - Improved roller end/flange contact geometry - 3 cage variants: steel, polyamide, brass
Thrust ball bearing double direction with sphered housing washers
Cylindrical roller thrust bearing single direction