加氢裂化脱硫系统
加氢裂化循环氢气脱硫工艺液力循环泵新技术的研究与开发

专题论述
加复裂化循环氢号腑硫 工 艺 液力循环泵新技术的酮穷与开发
中国石化 集 团南京工程 公 司 陈幼 军 石 家庄 海 阔捷 能科技 有 限公 司 杨 守智
[ 要] 摘 本文分析循 环氢气溶液法脱硫 工艺中的能量损耗 , 新性地提 出高压富液与低压贫液能量直接转换全新技术 方案 , 绍液 创 介 力循环泵 工作原理和研 究实验情 况。现场试验表 明 , 采用液力循环泵新装备可降低循环 氢脱硫溶液 泵动 力消耗 7%r上 , 0 X 节能效 果 十分显著。 [ 关键词] 循环氢气 脱硫
22液力循环泵工作原理 .
脱硫塔 顶部进入加氢裂 化工序 , 其所携带 的动能与压缩机 泵人时气体 所携带 的动能基本相 当。吸收硫化氢等有害气体 的富液从脱硫塔底部 流 出, 但富胺液再生不需要高压 , 因此流 出脱硫塔 的富胺液要经多级减 压, 富胺液所携带 的动能转化成热能 。当然 , 脱硫塔 内的循环氢气在逆 流而上 的过程 中存在着 液体摩擦阻力损 失等能量消耗 , 经过计算和 但 实 际观察 , 能量损 耗是泵人贫胺 液所携带动能 的 1 %。根 据能量守恒 0
1 引 言 .
液 力循环泵
贫富液压力 能交换是在压 力交换液缸 内完成 的 , 压力 交换 液缸 主 要 由缸体 、 活塞 、 活塞杆 、 活塞杆密封填料 盒等 附件 组成 。图 1 中右 图 为压力交换液缸吸液示意图 , 液缸下腔与闪蒸罐低压富液联通 , 由压 力 缓冲罐来的 中压贫液进入压力交换液缸的上部有杆腔 , 推动活塞下行 , 把压力交换液缸无杆下腔 内做完功后的低压富胺液经换 向分配器压 出 至富胺液 闪蒸罐 。图 1中右 图为压力交换 液缸排液示 意图 , 液缸下腔 与吸收塔高压富液联通 , 富液进人压力交换液缸 的下部无杆腔 , 推动 活 塞上行 , 把压力交换液缸有 杆上腔 内的低 压贫胺液增压 后经排液单 向
加氢硫化氢脱硫塔的工作原理

加氢硫化氢脱硫塔的工作原理
加氢硫化氢脱硫塔的工作原理是利用加氢和氧化还原反应将硫化氢转化为硫和水。
在脱硫塔中,氢气和硫化氢在催化剂的作用下发生加氢反应,将硫化氢转化为硫和水。
同时,氧化还原反应将硫化物氧化为硫和水,从而实现脱硫的目的。
具体来说,加氢硫化氢脱硫塔的工作原理可以分为以下几个步骤:
1. 预处理:将原料气中的杂质去除,如水、烃类化合物等,以避免对催化剂造成影响。
2. 加氢反应:在催化剂的作用下,氢气和硫化氢发生加氢反应,将硫化氢转化为硫和水。
这个反应是放热反应,需要控制温度以避免过热。
3. 氧化还原反应:在催化剂的作用下,硫化物被氧化为硫和水,从而实现脱硫的目的。
这个反应也是放热反应,需要控制温度以避免过热。
4. 产品气处理:将脱硫后的气体进行进一步处理,如去除剩余的氢气、硫等杂质,得到纯净的天然气。
加氢硫化氢脱硫塔的优点包括高脱硫率、低能耗、环保等。
但是,它也存在着一些缺点,如需要使用高纯度的氢气、催化剂易失活等。
因此,在实际应用中需要根据具体情况选择适合的脱硫技术。
加氢裂化工艺流程介绍
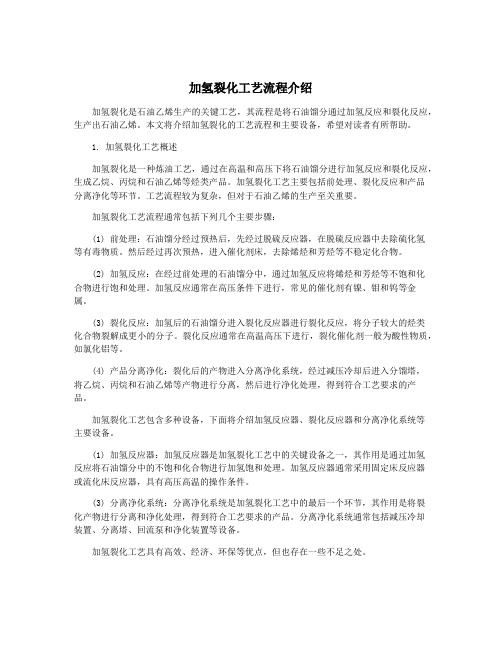
加氢裂化工艺流程介绍加氢裂化是石油乙烯生产的关键工艺,其流程是将石油馏分通过加氢反应和裂化反应,生产出石油乙烯。
本文将介绍加氢裂化的工艺流程和主要设备,希望对读者有所帮助。
1. 加氢裂化工艺概述加氢裂化是一种炼油工艺,通过在高温和高压下将石油馏分进行加氢反应和裂化反应,生成乙烷、丙烷和石油乙烯等烃类产品。
加氢裂化工艺主要包括前处理、裂化反应和产品分离净化等环节。
工艺流程较为复杂,但对于石油乙烯的生产至关重要。
加氢裂化工艺流程通常包括下列几个主要步骤:(1) 前处理:石油馏分经过预热后,先经过脱硫反应器,在脱硫反应器中去除硫化氢等有毒物质。
然后经过再次预热,进入催化剂床,去除烯烃和芳烃等不稳定化合物。
(2) 加氢反应:在经过前处理的石油馏分中,通过加氢反应将烯烃和芳烃等不饱和化合物进行饱和处理。
加氢反应通常在高压条件下进行,常见的催化剂有镍、钼和钨等金属。
(3) 裂化反应:加氢后的石油馏分进入裂化反应器进行裂化反应,将分子较大的烃类化合物裂解成更小的分子。
裂化反应通常在高温高压下进行,裂化催化剂一般为酸性物质,如氯化铝等。
(4) 产品分离净化:裂化后的产物进入分离净化系统,经过减压冷却后进入分馏塔,将乙烷、丙烷和石油乙烯等产物进行分离,然后进行净化处理,得到符合工艺要求的产品。
加氢裂化工艺包含多种设备,下面将介绍加氢反应器、裂化反应器和分离净化系统等主要设备。
(1) 加氢反应器:加氢反应器是加氢裂化工艺中的关键设备之一,其作用是通过加氢反应将石油馏分中的不饱和化合物进行加氢饱和处理。
加氢反应器通常采用固定床反应器或流化床反应器,具有高压高温的操作条件。
(3) 分离净化系统:分离净化系统是加氢裂化工艺中的最后一个环节,其作用是将裂化产物进行分离和净化处理,得到符合工艺要求的产品。
分离净化系统通常包括减压冷却装置、分离塔、回流泵和净化装置等设备。
加氢裂化工艺具有高效、经济、环保等优点,但也存在一些不足之处。
汽油加氢处理工艺流程

汽油加氢处理工艺流程是一种利用氢气对汽油进行加氢反应的工艺,以提高汽油的质量和性能。
汽油加氢处理主要是通过加氢裂化、加氢脱硫、加氢脱氮和加氢脱芳等工艺来提高汽油的辛烷值、减少硫、氮等杂质的含量,提高汽油的清洁度和燃烧效率。
汽油加氢处理工艺流程通常包括以下几个主要步骤:1. 精制汽油原料的准备:首先需要将原油经过初步的精制处理得到催化裂化汽油或者石化汽油。
这些原料汽油包含大量的不饱和烃、硫、氮和芳烃等杂质,需要通过加氢处理来改善其性能。
2. 加氢裂化:将精制汽油原料与氢气混合,并通过加热至一定温度、压力下进行加氢处理,使得其中的不饱和烃(烯烃、芳烃)和饱和烃发生加氢反应,生成高辛烷值、低芳烃含量的汽油。
加氢裂化是汽油加氢处理的核心步骤。
3. 加氢脱硫:经过加氢裂化处理后的汽油还含有一定量的硫化物,需要进行加氢脱硫处理。
加氢脱硫过程中,硫化物与氢气在催化剂的作用下发生反应,生成硫化氢并得到脱硫汽油。
4. 加氢脱氮:加氢处理后的汽油可能还含有一定量的氮杂质,影响汽油的清洁度和燃烧效率。
因此,需要进行加氢脱氮处理,将氮杂质也去除。
5. 加氢脱芳:芳烃是汽油中的一种重要成分,但过多的芳烃含量会影响汽油的清洁度和辛烷值。
因此,需要通过加氢反应将部分芳烃转化成饱和烃或环烷烃,以提高汽油的品质。
6. 分离和提纯:经过加氢处理后的汽油通过冷却、分离等步骤,将其中产生的硫化氢、氨和其它杂质分离,最终得到高质量、清洁的汽油产品。
7. 催化剂再生:加氢处理中用到的催化剂随着时间的延长会受到积碳、中毒等影响,影响催化剂的活性和寿命。
因此,需要对催化剂进行再生处理,以恢复催化剂的活性和延长使用寿命。
总的来说,汽油加氢处理工艺流程是一种重要的汽油炼制技术,可以有效提高汽油的品质和性能,满足现代汽车对清洁高效燃料的需求。
在石油加工行业中有着广泛的应用和良好的市场前景。
加氢裂化装置循环氢脱硫系统改造运行比较分析

月毕 业 于 江苏 工 业 学 院 化学 工 程 与 工艺 专 业 石 油 加 工 方 向 , 同年 7 进 人 中 石 化 上 海 高 桥 分 公 司 炼 油 事 业 部 工 作 。现 为 炼 油 作 月
业 五 区工 艺 员 。
3 0
高
Байду номын сангаас
桥
石
化
差 降低 。
2 运行 比较分 析
2 1 改 造 对 操 作 条 件 的 影 响 .
影响 , 出 改造 过 程 中存 在 的 问 题 , 提 出 相 应 的解 决 方 案 。 找 并
关键词 氢裂化 加 循环氢脱 硫改鑫 操作 节能 条件
加 氢裂化装 置能使 高凝点 的重油转化 成优质
的航空煤 油 、 凝 点柴 油 和高 粘度 的润 滑 油 基础 低 油, 并且 具有 原料 油 馏分 宽 、 产方 案 灵活 性 大 、 生
注: 由于 改 造 后该 加 氢 裂化 装 置 2 0 0 8年 正 常 生产 的 日期 为 6月 1 日 ~3 0 0日 , 20 而 0 5年 6月 份 正 常 生 产 的 日期 为 6月 1日~ 1 5
日, 为增 加 数 据 的可 比性 , 取两 年 6月份 的 1 日~1 0 5日的 数据 。
l5 6
消了低 分油 与高分气换 热 流程 的情 况下 ,0 8年 20 热高 分 进 口平 均 温度 较 2 0 0 5年 低 1 . ℃ ; 造 06 改
10 6
15 5
后 混合氢 和高分气换 热器 0 1增加为两 台 , 换热器
O 1出 口的 温 度 较 改 造 前 低 l .℃ , 是 由 于 改 造 02 但
设备 。
加 循环氢 脱硫系统 , 同时对部 分相关 管线 、 备 的 设
加氢裂化工艺流程概述
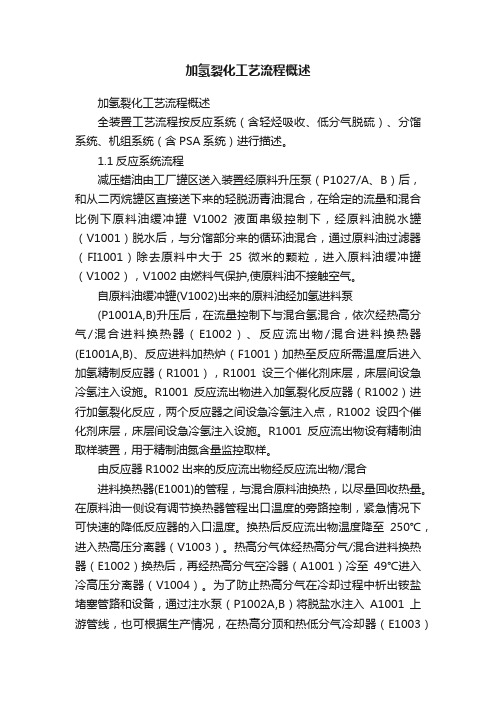
加氢裂化工艺流程概述加氢裂化工艺流程概述全装置工艺流程按反应系统(含轻烃吸收、低分气脱硫)、分馏系统、机组系统(含PSA系统)进行描述。
1.1反应系统流程减压蜡油由工厂罐区送入装置经原料升压泵(P1027/A、B)后,和从二丙烷罐区直接送下来的轻脱沥青油混合,在给定的流量和混合比例下原料油缓冲罐V1002液面串级控制下,经原料油脱水罐(V1001)脱水后,与分馏部分来的循环油混合,通过原料油过滤器(FI1001)除去原料中大于25微米的颗粒,进入原料油缓冲罐(V1002),V1002由燃料气保护,使原料油不接触空气。
自原料油缓冲罐(V1002)出来的原料油经加氢进料泵(P1001A,B)升压后,在流量控制下与混合氢混合,依次经热高分气/混合进料换热器(E1002)、反应流出物/混合进料换热器(E1001A,B)、反应进料加热炉(F1001)加热至反应所需温度后进入加氢精制反应器(R1001),R1001设三个催化剂床层,床层间设急冷氢注入设施。
R1001反应流出物进入加氢裂化反应器(R1002)进行加氢裂化反应,两个反应器之间设急冷氢注入点,R1002设四个催化剂床层,床层间设急冷氢注入设施。
R1001反应流出物设有精制油取样装置,用于精制油氮含量监控取样。
由反应器R1002出来的反应流出物经反应流出物/混合进料换热器(E1001)的管程,与混合原料油换热,以尽量回收热量。
在原料油一侧设有调节换热器管程出口温度的旁路控制,紧急情况下可快速的降低反应器的入口温度。
换热后反应流出物温度降至250℃,进入热高压分离器(V1003)。
热高分气体经热高分气/混合进料换热器(E1002)换热后,再经热高分气空冷器(A1001)冷至49℃进入冷高压分离器(V1004)。
为了防止热高分气在冷却过程中析出铵盐堵塞管路和设备,通过注水泵(P1002A,B)将脱盐水注入A1001上游管线,也可根据生产情况,在热高分顶和热低分气冷却器(E1003)前进行间歇注水。
催化裂化 加氢裂化吸收稳定系统流程及优化

催化裂化加氢裂化吸收稳定系统流程及优化1. 引言1.1 概述催化裂化和加氢裂化是石油炼制领域中常用的重要工艺,主要用于石油原料的转化和提纯。
通过催化裂化和加氢裂化技术,可以将重质石油馏分转变为更高附加值的产品,如汽油、柴油、润滑油等。
这些工艺的关键在于稳定系统流程的运行,以确保产品质量的稳定性、生产效率的提高和设备寿命的延长。
本文目的在于深入探讨催化裂化和加氢裂化吸收稳定系统流程,并提出优化方案以改善工艺效果。
首先概述了本文将要讨论的内容和结构,然后介绍了引言部分的目标。
1.2 文章结构本文主要分为五个部分进行描述。
第一部分是引言,简要介绍了本文内容和结构。
第二、三和四部分则详细讨论了催化裂化系统流程、加氢裂化系统流程以及吸收系统流程优化。
最后一部分是结论与展望,总结了已经探讨过的内容,并对未来进行展望。
1.3 目的本文的目的是深入探讨催化裂化和加氢裂化吸收稳定系统流程,并提出优化方案以改善工艺效果。
通过对系统组成、工艺概述和问题解决方案的介绍,旨在帮助工程师和研究人员更好地理解这些重要工艺,并为实践中的流程优化提供指导。
同时,本文还将对未来的研究方向进行展望,为相关领域提供新的思路和建议。
通过深入分析和讨论,我们期望能够推动催化裂化和加氢裂化技术的进一步发展和优化。
以上就是引言部分的内容,在接下来的文章中,我们将逐一探讨催化裂化系统流程、加氢裂化系统流程以及吸收系统流程优化。
这些内容将有助于读者更好地理解相关工艺,并为实践中的问题解决和优化提供参考。
最后,我们将对已经探讨过的内容进行总结,并展望未来该领域研究方向。
以下内容不属于引言部分。
2. 催化裂化系统流程:2.1 系统组成:催化裂化系统主要由反应器、催化剂输送装置、分离装置和再生装置组成。
其中,反应器是催化裂化过程中最重要的组件,它用于将原料油在催化剂的作用下发生裂解反应。
催化剂输送装置用于将新鲜催化剂及再生后的催化剂注入反应器中。
分离装置则用于将裂解产物进行分离和提纯,包括汽油分离塔、液-液萃取塔等。
加氢裂化循环氢脱硫操作规程

1401-C-101 温度循 环 氢 进 ℃ <551401-C-101 温度脱后循环气中的 H S 2 ppm <1000含量加氢裂化循环氢脱硫操作规程一、工艺原理由反响系统来的循环氢在脱硫塔内与甲基二乙醇胺溶 剂(MDEA)逆向接触,发生化学吸取反响。
由于 MDEA 对硫化氢具有很高的吸取率,同时又不易溶解循环氢中的其它组 分,所以能有效地从循环氢中将 H S 脱除。
2反响过程如下:C H O N+H S → C H O NH ++HS -5 13 2 2 5 13 2这个反响是在瞬间内完成的,所以能到达快速连续的脱硫效果。
同时,较高的压力及较低的温度有利于反响向右进 行。
二、正常操作条件1401-C-101 液位% 40~65 1401-C-101 胺液循环量t/h 64 贫 胺 液 进 ℃ 高于循环氢 5~6三、操作因素1.温度MDEA 溶液是一种弱有机碱,其碱性随温度上升而减弱,因此在较低的温度下有利于反响吸取,生成酸性硫化物。
在较高的温度下,MDEA 溶液又解吸脱附硫化氢。
因而,脱硫操作都是在低温下进展,而再生则在较高温度下进展。
1401-C-101 是气-液吸取塔,温度低,一则胺液碱性强,有利于化学吸取反响,二则会使贫液中酸气平衡分压降低,有利于气体吸取。
但是假设温度太低,会使原料气中的重烃组分冷凝,促使溶液发泡,破坏吸取塔的操作。
保持溶剂的入塔温度比原料气温度高出 5~6℃,以利于脱硫塔的稳定操作。
2.压力压力对吸取有直接影响。
压力高,有利于吸取脱硫的进行,但塔的操作压力受原料及设备设计压力的限制。
较高的压力对于 1401-C-101 ,有利于气 --液的溶解吸取效果。
1401-C-101 的操作压力由反响压力打算的。
3.溶剂循环量由于溶剂的设计浓度为 35%(w),所以操作变量主要是溶剂的循环量。
循环量过小,满足不了脱硫的化学需要量、导致吸取效果降低,会消灭脱后循环氢中H S 量过大,质量不2合格;而循环量过大,则塔负荷大,易发泡而影响吸取效果,动力消耗大。
- 1、下载文档前请自行甄别文档内容的完整性,平台不提供额外的编辑、内容补充、找答案等附加服务。
- 2、"仅部分预览"的文档,不可在线预览部分如存在完整性等问题,可反馈申请退款(可完整预览的文档不适用该条件!)。
- 3、如文档侵犯您的权益,请联系客服反馈,我们会尽快为您处理(人工客服工作时间:9:00-18:30)。
1脱硫系统操作法1.1工艺操作指标1.1.1气柜气(T201)脱硫塔塔顶温度℃40塔顶压力MPa(G) 0. 71.1.2液化气脱硫抽提塔塔顶温度℃40塔顶压力MPa(G) 1.51.1.3干气(T101)脱硫塔塔顶温度℃40塔顶压力MPa(G) 0.71.1.4MDEA分子式:C5H13NO2分子量:119.16沸点:247℃密度(20℃):1047.8kg/m3粘度(20℃):101 cp溶液浓度:~30 W%1.2操作因素分析1.2.1工艺原理干气、气柜气在脱硫塔内与甲基二乙醇胺溶剂(MDEA)逆向接触,发生化学吸附反应。
由于MDEA 对硫化氢具有较高的吸收率,同时又不易溶解原料气中的其它组分,所以能有效地从原料气中将硫化氢脱除,从而使干气、气柜气得到净化。
反应过程如下:C5H13O2N + H2S C5H13O2NH+ + HS-这个反应是在瞬间内完成的,所以能达到迅速连续的脱硫效果。
同时,较高的压力及较低的温度有利于反应向右进行。
1.2.2温度对脱硫的影响MDEA的碱性随温度的变化而变化,即温度低,MDEA碱性强,脱硫性能好;温度高则有利于硫化物在富液中分解。
因而,脱硫操作都是在低温下进行,而再生则在较高的温度下进行。
对吸收塔(T101、T201)来说,温度低一则MDEA碱性强,有利于化学吸收反应,二则会使贫液中的酸性气平衡分压降低,有利于气体吸收;但如果温度过低,可能会导致进料气的一部分烃类在吸收塔内冷凝,导致MDEA溶液发泡而影响吸收效果。
1.2.3压力对脱硫的影响对吸收来说,如果压力高,使气相中酸气分压增大,吸收的推动力就增大,故高压有利于吸收。
相反,如果吸收压力低,同样道理会使吸收推动力减少不利于吸收。
实际操作中由于压力太高会使设备承受不了而造成安全阀跳,同时会导致部分烃类气体的冷凝,压力太低会降低吸收效率,故需要严格控制操作压力。
1.2.4胺循环量在一定的温度、压力下,MDEA的化学脱硫,溶解度是一定的,循环量过小,满足不了脱硫的化学需要量,导致吸收效果降低,会出现净化气中的H2S量过大,质量不合格;而循环量过大,则塔负荷大,能耗高。
所谓溶剂的酸气负荷是指吸收塔底富液中酸性气体(H2S)摩尔数与溶液中胺的摩尔数之比。
当MDEA浓度决定后,它直接影响溶剂循环量。
如果溶剂的酸气负荷选大了,由于一分子胺只能与0.5分子的H2S起反应,这样过多的H2S就会生成硫化氢胺盐对设备腐蚀不利,同时,还会降低吸收效果。
如果富液中酸气负荷上升,则要加大循环量,如果由于MDEA浓度低,吸收效果差,除了减少注水外,也可暂时考虑加大循环量,但根本的调节方法还是提高胺液浓度。
1.2.5液位吸收塔T101、T201的液位高低会直接影响正常操作以及整个系统的胺液平衡;液位过高则降低了吸收有效空间,液面低会引起吸收塔压空、串气,打乱整个操作。
一般按液面的50~75%控制。
1.2.6贫液温度贫液温度按国内经验一般控制在比原料气温度高4~5℃为适宜,这主要考虑到富液的烃含量问题。
1.2.7MDEA浓度本装置是按MDEA浓度为30%(重)设计的,如果浓度<20%单位体积中,富液中的酸性气浓度将变得较低,溶剂循环量必须加大,以便能更完全吸收原料气中H2S杂质。
相反,使用较高浓度的MDEA溶液,将允许减少循环量,但每单位体积溶液吸收的酸性气体量将增加,酸性气浓度过高的富溶剂腐蚀性更强。
1.2.8原料含硫量液化气以及干气是脱硫系统的原料,其含硫量与原油含硫量以及反应系统的操作有关,含硫量越高,脱硫难度越大。
1.3正常操作法1.3.1贫液缓冲罐V4011.3.1.1压力V407罐顶压力由PIC4010A/B控制,压力高时打开PV4010B阀,将多余气体放入火炬;压力低时打开PV4010A阀,将氮气补充进V407。
两阀通过压力控制器对其进行分程调节,当PIC4010阀位在0~50%时,PV4010A开度为100%~0%,PV4010B开度为0%;当PIC4010阀位在50~100%时,PV4010A 开度为0%,PV4010B开度为0%~100%。
压力控制0.1KPa。
1.3.1.2液位V3017液位由贫液进口阀LIC4008控制,通过V3017液位控制器LT3502串级控制。
V3017是热贫液进装置缓冲罐,贫溶剂进入装置后,通过E3016加热,然后进入V3017,向循环氢脱硫塔T3005提供贫液,其流量也影响V3017的液位稳定。
正常生产中V3017的液位过低,则容易使T3005贫溶剂泵P3003抽空,V3017液位控制50~70%。
1.3.2地下溶剂罐V3035V3035设有液位控制器LT3503,控制地下溶剂泵P3029电机开关,液位高时启动P3029将收集的富液打回脱硫装置。
V3035液位控制50~85%。
1.3.3富胺液闪蒸罐V30241.3.3.1压力V3024罐顶压力由PV3503控制,压力高时打开PV3503阀,将多余气体放入火炬。
1.3.3.2液位V3024液位由底部出口控制阀FV3501控制,出装置的富胺液由流量累计计量FIQ3504、瞬时计量FT3504进行计量。
1.3.4循环氢脱硫塔T30051.3.4.1液位1.3.4.1.1塔底液位T3005塔底富液经过液力透平HT3002减压后送回脱硫装置,HT3002作为贫液进口泵P3003A的动力;液位太高可能引起液泛;液位太低,则容易使液力透平HT3002抽空,由于T3005压力达13.5MPa,容易引起串气;液位太高或太低均会影响操作稳定。
T3005塔底液位由阀LV3118A/B控制,LV3118A 是HT3002进口阀,LV3118B是HT3002旁路阀,通过液位控制器LICA3118分程控制,当LICA3118阀位在0~50%时,LV3118A开度为0%~100%,LV3118B开度为0%;当LICA3118阀位在50~100%时,LV3118A开度为100%,LV3118B开度为0%~100%,设有高低报警并带停车联锁。
贫液进料流量由P3003出口流量阀FV3135控制,由于P3003出口流量与HT3002转速有关,T3005塔底液位和压力也影响贫液进料流量。
正常生产时控制流量115.64m3/h。
正常生产时塔底液位控制在60~85%。
1.3.4.1.2循环氢压缩机进口分液罐V3007液位V3007液位由塔底富液排放阀LV3119控制,将分离出的富液通过富液总管排回脱硫装置。
正常生产时液位控制在60~75%。
该液位是C3001联锁系统动作原因之一,设有液位高高报警三个,其中两个报警时,联锁停C3001,装置紧急停车。
1.3.4.2塔顶压力T3005塔顶压力在正常生产时主要通过调节循环氢压缩机进口分液罐V3007罐顶废氢排放阀PV3127B通过控制废氢的排放量来控制,正常控制在13.5MPa。
V3007压力同时也是循环氢压缩机C3001进口压力,C3001的运转对T3005塔顶压力控制有较大的影响。
贫液进料流量由P3003出口流量阀FV3135控制,流量大时可导致塔顶压力下降,流量小则相反。
该阀同时也对塔顶温度有一定的影响。
1.3.4.3吸收温度在脱硫系统的操作中,吸收温度由吸收贫液温度决定,而贫液在进入装置后,在E3016壳程被管程的产品柴油加热,因此,调控E3016出口产品柴油温度的管程旁路阀TV3505对调控贫液温度有一定的影响。
1.3.4.4循环氢含硫量循环氢含硫量与原油含硫量以及反应系统的操作有关,含硫量越高,脱硫难度越大。
1.3.5液化气脱硫塔T3008T3008是液-液抽提塔,它的最基本条件是液相操作,若温度高,则液化气会汽化导致压力波动打乱操作,且C5以上沸点较高的化合物(操作波动时产生)在溶液中的积累速度增大,而直接影响吸收效果,所以,低温时对T3008操作有利。
但温度直接取决于塔的操作压力,对于达到同一效果而言,压力高温度可稍高,反之亦然。
影响T3008温度的因素有,进料温度、贫溶液温度、塔顶温度等。
1.3.5.1液位T3008是液-液抽提塔,其塔顶液位是指液态的液化气与溶液之间的交界。
1.3.5.1.1塔顶液位T3008塔底富液经过塔底流量阀FV3311送回脱硫装置,可由液位控制器LT3307串级控制,并设有高低报警;液位太高或太低均会影响操作稳定。
T3008贫液进料量对该液位也有影响。
由FV3310通过控制P3019出口的贫液量控制T3008贫液进料量。
正常生产时控制流量约10.04m3/h。
由于T3008是液-液抽提塔,因此液化气进料也会使该液位波动。
液化气进料与脱乙烷塔T3007塔底液位有关,由其底部出口流量控制阀FV3306控制。
正常生产时控制流量约4.87~8.509t/h。
正常生产时液位控制在60~85%。
1.3.5.1.2液态烃聚集器V3020液位V3020液位由塔底富液排放阀LV3308控制,将分离出的富液与T3008底部排出的富液一起排回脱硫装置。
正常生产时液位控制在60~85%。
1.3.5.2塔顶压力T3008塔顶压力通过控制液态烃聚集器V3020压力来控制。
在正常生产时主要通过调节V3020顶部液化气出口控制阀FV3312来控制,FV3312由压力控制器PV3305串级控制,正常控制在1.9MPa。
T3008顶部产品液化气流量对塔顶压力有较大的影响,流量大时可导致塔顶压力下降,流量小则相反。
1.3.6干气脱硫塔T30111.3.6.1液位1.3.6.1.1塔底液位T3011塔底富液经过塔底液位控制阀LV3408送回脱硫装置;液位太高可能引起液泛;液位太低,容易引起串气;液位太高或太低均会影响操作稳定。
T3011贫液进料量对塔底液位也有影响。
由FV3409通过控制P3019来的贫液量控制T3011进料量。
正常生产时控制流量约56.64m3/h。
正常生产时塔底液位控制在60~85%。
1.3.6.1.2干气分液罐V3016液位V3016液位由塔液位控制阀LV3407控制,将分离出的液体放空。
正常生产液位控制在40~60%。
1.3.6.2塔顶压力T3011塔顶压力通过压力控制阀P V3408来控制。
在正常生产时控制在0.6MPa。
T3011顶部石脑油进料量对塔顶压力有较大的影响,流量大时可导致塔顶压力下降,流量小则相反。
该阀同时也对塔顶温度有一定的影响。
1.3.6.3干气H2S含量超标的调节1.3.6.3.1原因:a、原料中酸性气含量增加。
b、原料气量增大。
c、贫液循环量不足、贫液再生不好或浓度低。
d、压力波动或溶液温度高。
e、溶液液面过低。
f、溶液发泡严重或溶液脏等造成吸收效果差。
1.3.6.3.2调节:a、增大贫液循环量。
b、反应系统平稳操作。
c、联系脱硫装置平稳操作,提高溶液浓度和再生度。