生产过程关键控制点记录
灌装车间关键控制点记录

、无悬浮物、无沉淀、无
4
灯检 异物,封口严实。
2. 瓶体、瓶口、瓶身无油
污
1.旋盖压合平整、无脱落
现象。
5
封口 2.倒立检漏试验,桶口无
渗漏、无渗透现象。
记录:
灌装车间生产过程关键控制点记录
年 月日
实测结果
时分
时分
时分
时分
编号:
异常情况处置
责任人 验证人
山西晋粮植物油库
序号 关键控制点
工艺要求及 控制参数
1、检查滤网(滤布)干净
1
过滤
完好 2、运行中检查压力保持在
0.2~0.5Βιβλιοθήκη pa1、检查手持汽枪口是否通
畅。
2
净瓶 2、对每个瓶进行除尘、净
化。
1、认真按照《灌装机操作
规程》操作
3
灌装 2、定期清理灌装管路、消
毒擦拭设备,保持出油嘴
洁净。
1. 油品透亮、无明显杂渣
重要工序质量控制及关键工序控制点
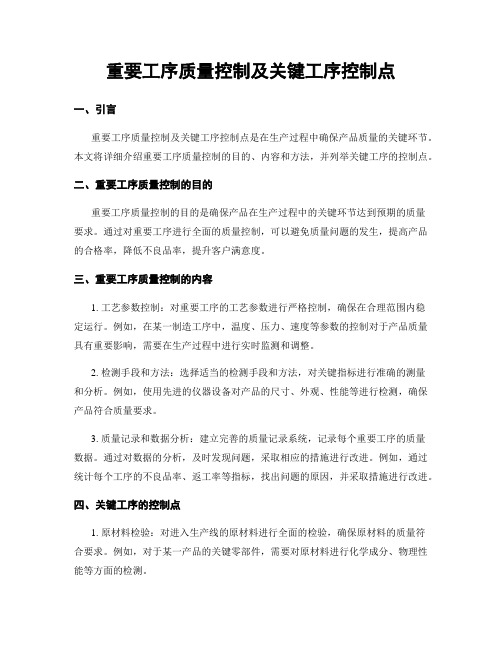
重要工序质量控制及关键工序控制点一、引言重要工序质量控制及关键工序控制点是在生产过程中确保产品质量的关键环节。
本文将详细介绍重要工序质量控制的目的、内容和方法,并列举关键工序的控制点。
二、重要工序质量控制的目的重要工序质量控制的目的是确保产品在生产过程中的关键环节达到预期的质量要求。
通过对重要工序进行全面的质量控制,可以避免质量问题的发生,提高产品的合格率,降低不良品率,提升客户满意度。
三、重要工序质量控制的内容1. 工艺参数控制:对重要工序的工艺参数进行严格控制,确保在合理范围内稳定运行。
例如,在某一制造工序中,温度、压力、速度等参数的控制对于产品质量具有重要影响,需要在生产过程中进行实时监测和调整。
2. 检测手段和方法:选择适当的检测手段和方法,对关键指标进行准确的测量和分析。
例如,使用先进的仪器设备对产品的尺寸、外观、性能等进行检测,确保产品符合质量要求。
3. 质量记录和数据分析:建立完善的质量记录系统,记录每个重要工序的质量数据。
通过对数据的分析,及时发现问题,采取相应的措施进行改进。
例如,通过统计每个工序的不良品率、返工率等指标,找出问题的原因,并采取措施进行改进。
四、关键工序的控制点1. 原材料检验:对进入生产线的原材料进行全面的检验,确保原材料的质量符合要求。
例如,对于某一产品的关键零部件,需要对原材料进行化学成分、物理性能等方面的检测。
2. 制造工艺控制:在生产过程中,对关键工艺进行严格的控制,确保产品的质量稳定。
例如,在某一制造工序中,需要对温度、压力、时间等参数进行精确控制。
3. 检测环节控制:在产品生产过程中设置关键的检测环节,对产品进行全面的检测。
例如,在某一制造工序中,需要对产品的尺寸、外观、性能等进行检测,确保产品符合质量要求。
4. 过程监控和反馈:建立完善的过程监控系统,及时监测工艺参数和产品质量指标,并进行反馈。
例如,通过实时监测工艺参数的变化,及时调整工艺参数,确保产品质量的稳定。
生产作业流程关键管控点
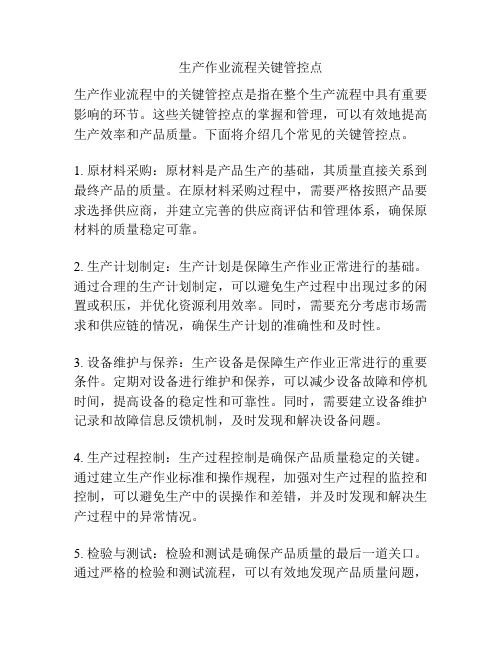
生产作业流程关键管控点生产作业流程中的关键管控点是指在整个生产流程中具有重要影响的环节。
这些关键管控点的掌握和管理,可以有效地提高生产效率和产品质量。
下面将介绍几个常见的关键管控点。
1. 原材料采购:原材料是产品生产的基础,其质量直接关系到最终产品的质量。
在原材料采购过程中,需要严格按照产品要求选择供应商,并建立完善的供应商评估和管理体系,确保原材料的质量稳定可靠。
2. 生产计划制定:生产计划是保障生产作业正常进行的基础。
通过合理的生产计划制定,可以避免生产过程中出现过多的闲置或积压,并优化资源利用效率。
同时,需要充分考虑市场需求和供应链的情况,确保生产计划的准确性和及时性。
3. 设备维护与保养:生产设备是保障生产作业正常进行的重要条件。
定期对设备进行维护和保养,可以减少设备故障和停机时间,提高设备的稳定性和可靠性。
同时,需要建立设备维护记录和故障信息反馈机制,及时发现和解决设备问题。
4. 生产过程控制:生产过程控制是确保产品质量稳定的关键。
通过建立生产作业标准和操作规程,加强对生产过程的监控和控制,可以避免生产中的误操作和差错,并及时发现和解决生产过程中的异常情况。
5. 检验与测试:检验和测试是确保产品质量的最后一道关口。
通过严格的检验和测试流程,可以有效地发现产品质量问题,并及时采取纠正措施,避免次品产品流入市场。
同时,需要建立完善的检验和测试记录,以便追溯和分析问题的原因。
以上是生产作业流程中的几个关键管控点。
通过对关键管控点的严格管理和有效掌握,可以提高生产效率和产品质量,降低生产成本,增强企业竞争力。
因此,企业应重视关键管控点的管理,建立相应的制度和机制,确保生产作业流程的稳定性和可持续发展。
药品生产过程中的关键控制点

药品生产过程中的关键控制点药品生产过程中的关键控制点是指在制药过程中具有重要作用的步骤或环节,对药品质量的稳定性与安全性具有决定性的影响。
本文将着重介绍药品生产过程中的几个关键控制点。
一、原材料的选择与采购在药品生产过程中,选择和采购合格的原材料是第一个关键控制点。
原材料的质量直接影响着最终药品的质量。
因此,在进行原材料采购时,药品生产企业必须建立健全的供应商评估和选择机制,确保供应商具备优质原材料的供应能力。
同时,对原材料的质量进行全面的检验,确保原材料符合国家和企业的标准要求。
二、工艺参数的控制工艺参数的控制是药品生产过程中的另一个关键控制点。
这包括药品的配方、反应温度、反应时间、搅拌速度等参数的控制。
合理的工艺参数设置可以确保药品生产过程中的关键步骤得到有效的控制,从而保证药品的质量稳定性。
药品生产企业应该根据药品的特性和生产设备的情况,制定合适的工艺参数,并严格按照标准操作程序进行操作。
三、生产设备的维护与验证生产设备的维护与验证是药品生产过程中的另一个关键控制点。
设备的正常运行状态对于药品的质量控制至关重要。
药品生产企业需要定期对生产设备进行维护和保养,确保设备处于良好的工作状态。
同时,还需要进行设备验证,验证设备的性能是否符合规范要求,保证药品生产过程中的各个步骤得到有效的控制。
四、生产过程的记录与监控记录与监控是药品生产过程中的另一个关键控制点。
药品生产企业需要建立完善的记录体系,将生产过程中的各项数据进行记录,以便追溯和分析。
同时,还需要对药品生产过程进行实时的监控,及时发现并解决潜在的问题,确保药品质量的稳定性和可靠性。
五、质量控制体系的建立与实施质量控制体系的建立与实施是药品生产过程中的最后一个关键控制点。
药品生产企业需要建立健全的质量管理体系,确保质量控制的全过程有效执行。
这包括药品质量标准的建立、质量检验的实施、不合格品的处理和质量风险的管理等方面。
只有建立和实施全面、严格的质量控制体系,才能够保证药品的质量稳定性和安全性。
关键工序质量控制点
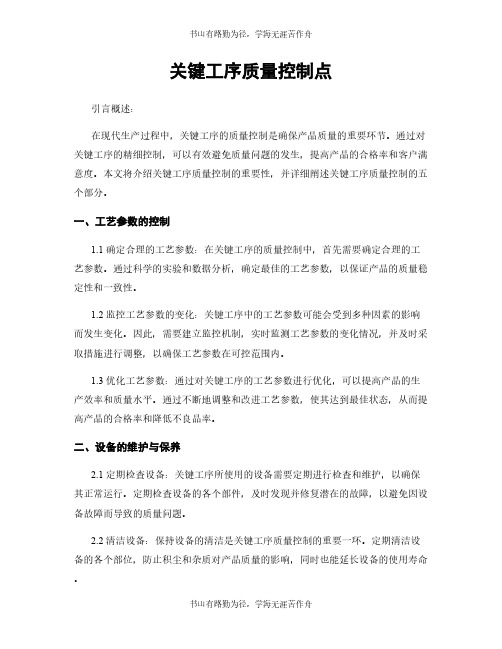
关键工序质量控制点引言概述:在现代生产过程中,关键工序的质量控制是确保产品质量的重要环节。
通过对关键工序的精细控制,可以有效避免质量问题的发生,提高产品的合格率和客户满意度。
本文将介绍关键工序质量控制的重要性,并详细阐述关键工序质量控制的五个部分。
一、工艺参数的控制1.1 确定合理的工艺参数:在关键工序的质量控制中,首先需要确定合理的工艺参数。
通过科学的实验和数据分析,确定最佳的工艺参数,以保证产品的质量稳定性和一致性。
1.2 监控工艺参数的变化:关键工序中的工艺参数可能会受到多种因素的影响而发生变化。
因此,需要建立监控机制,实时监测工艺参数的变化情况,并及时采取措施进行调整,以确保工艺参数在可控范围内。
1.3 优化工艺参数:通过对关键工序的工艺参数进行优化,可以提高产品的生产效率和质量水平。
通过不断地调整和改进工艺参数,使其达到最佳状态,从而提高产品的合格率和降低不良品率。
二、设备的维护与保养2.1 定期检查设备:关键工序所使用的设备需要定期进行检查和维护,以确保其正常运行。
定期检查设备的各个部件,及时发现并修复潜在的故障,以避免因设备故障而导致的质量问题。
2.2 清洁设备:保持设备的清洁是关键工序质量控制的重要一环。
定期清洁设备的各个部位,防止积尘和杂质对产品质量的影响,同时也能延长设备的使用寿命。
2.3 更新设备:随着科技的进步,设备的更新换代是关键工序质量控制的必要措施。
及时更新设备,引入更先进的技术和设备,可以提高生产效率和产品质量水平。
三、操作规程的制定与执行3.1 制定详细的操作规程:关键工序的操作规程应该详细而清晰,包括每个步骤的具体要求和操作方法。
制定操作规程时,要考虑到各种可能的情况和变化,并提供相应的应对措施。
3.2 培训操作人员:关键工序的操作人员需要经过专业的培训,熟悉操作规程和工艺要求。
通过培训,操作人员可以掌握正确的操作方法和技巧,提高操作的准确性和稳定性。
3.3 监督执行情况:制定好的操作规程需要得到严格的执行。
HACCP在食品生产中的关键控制点及监测方法

HACCP在食品生产中的关键控制点及监测方法在食品生产中,食品安全一直是一个重要的关注点。
为了确保食品质量和安全,HACCP(危害分析和关键控制点)系统被广泛应用于食品行业。
本文将重点讨论HACCP在食品生产过程中的关键控制点及其监测方法。
1. 概述HACCP系统HACCP系统是一种基于科学原理的食品安全管理系统,旨在通过分析食品加工过程中的危害和控制点,预防、消除和减轻食品中潜在的危险物质。
它是一个连续的监控系统,包括以下七个原则:危害分析、确定关键控制点、确定监测方法、建立纠正措施、建立监测程序、建立记录系统和建立验证程序。
2. 关键控制点(CCP)关键控制点是食品生产过程中必须严格控制的步骤,以确保消除或减轻危害物质的存在。
确定关键控制点的方法包括风险评估和决策树。
一般来说,关键控制点包括接收原料、储存和运输、加工、包装和交付等环节。
(1)接收原料在接收原料的过程中,可能存在一些潜在的危险物质,如细菌、化学物质或异物等。
因此,建立关键控制点以确保原料的质量和安全非常重要。
监测方法包括对原料进行检验和实施供应商审查的程序。
(2)储存和运输储存和运输过程中,温度、湿度和保鲜度是需要控制的关键因素。
为了确保食品的质量和安全,建立关键控制点可以包括定期对冷链进行监测,确保温度符合要求,以及实施原料和成品的合理储存和运输。
(3)加工加工是食品生产中最重要的环节之一。
关键控制点一般包括烹饪温度、杀菌时间或处理程序,以及对加工设备的良好维护和清洁。
监测方法可以包括温度计测量、时间记录、设备维护日志和卫生检查。
(4)包装和交付在包装和交付的过程中,关键控制点包括包装质量、包装材料的适用性和交付方式的卫生要求等。
监测方法可以包括包装检验、交货时间的记录和交付条件的监测。
3. 监测方法为了确保在关键控制点上采取的控制措施有效,需要建立相应的监测方法。
这些方法可以包括物理测量、化学分析、细菌检测、传感器监测等。
食品生产流程中的关键控制点
食品生产流程中的关键控制点在食品生产过程中,关键控制点(Critical Control Points,简称CCPs)是指需要严格控制和监测的环节,以确保食品安全和质量。
CCPs是食品安全管理体系中的核心要素,其正确的识别和管理对于食品生产企业而言至关重要。
本文将介绍食品生产流程中的关键控制点,并探讨如何有效地管理这些CCPs,以确保食品的安全性和合规性。
一、原料采购原料采购是食品生产过程中的第一个关键控制点。
在选择供应商时,企业应该进行严格的筛选,确保供应商具有良好的信誉和合规记录。
此外,企业还应对原料进行必要的检验和测试,以确保其符合食品安全和质量标准。
二、加工过程控制在食品加工过程中,有几个关键控制点需要特别注意。
首先是温度控制。
许多食品在加热过程中需要达到一定的温度才能消灭微生物和其他有害物质。
因此,准确控制加热温度并监测温度变化是确保食品安全的关键因素之一。
其次是时间控制。
不同的食品加工过程需要不同的时间才能达到安全标准。
食品生产企业应该严格控制加工时间,确保食品在加工过程中得到充分处理。
此外,对于一些特殊的食品加工过程,如发酵、腌制等,企业还需要控制发酵或腌制的时间和条件,以确保食品的质量和安全。
三、卫生和清洁控制卫生和清洁是食品生产过程中最重要的关键控制点之一。
企业应该建立严格的卫生和清洁程序,并培训员工遵守这些程序。
这包括设备、工具和生产场所的清洁和消毒,员工个人卫生和手部卫生的管理,以及废物处理的控制等。
卫生和清洁控制是预防食品污染和交叉感染的重要手段。
四、检测和监测食品生产过程中的关键控制点需要定期检测和监测。
这可以通过临时抽样和实验室测试进行。
通过检测和监测,企业可以及时了解食品生产过程中的问题,并采取相应的措施进行纠正。
检测和监测还可以帮助企业评估食品生产过程中风险的变化,并及时调整控制措施,保证食品的安全性和合规性。
五、记录和文档管理记录和文档管理是食品生产过程中的另一个重要关键控制点。
关键工序质量控制点记录
监控要点
名称
控制要点
控制内容、
地 点
结 果
频次
检查人签名
制剂
物料交接
检验报告书、合格证
□符合,有
□不符合,无
每批
称量
一人称量,一人复核
□是
□否
定期
操作过程
执行标准操作
程序情况
□遵守
□违反
定时
操作过程的状态标识,重量与实物相符
□标识正确,相符
□标识不正确,不符合
随机
随机
按标准检验,有检验合格报告单
□按标准检验,合格 □不合格
生产偏差
执行偏差处理工作程序,并有记录
□执行,有
□不执行,无
原始记录
填写符合要求,无提前记或追记,准确、及时、真实、完整
□符合规定
□不符合规定
人员卫生
内外环境卫生
设施卫生
工艺卫生
物品定置要求
□遵守 □违反
□遵守 □违反
□遵守 □违反
□遵守 □违反
□遵守□违反
□遵守□违反
随机
物料平衡
□偏差在的[控制范围内□偏差偏离控制范围
每批
中间产品容器状态标识、标签
□与实物相符
□与实物有偏差
每批
中间产品抽验结果
□符合规定
□不符合规定
每批
生产偏差
执行偏差处理工作程序,并有记录
□执行,有记录
□违反,记录不全
每批
原始记录
填写完整、正确
□符合要求
□不符合要求
每批
生产结束
中间产品容器状态标识、标签
□与实物相符
□与实物有偏差
生产过程关键控制点记录(暂不记录)
原料验收
原料验收标准
熟制
温度:105℃
时间:50min
计量热灌装
温度:80-100℃
原料验收
原料验收标准
熟制
温度:105℃
时间:50min
计量热灌装
温度:80-100℃
原料验收
原料验收标准
熟制
温度:105℃
时间:50min
计量热灌装
温度:80-100℃
原料验收
原料验收标准
熟制
温度:105℃
时间:50min
实际
结果
质量控制
运行情况
异常情况
处置措施
处置时间
处置结果
责任人
原料验收
原料验收标准
熟制
温度:105℃
时间:50min
计量热灌装
温度:80-100℃
原料验收
原料验收标准
熟制
温度:105℃
时间:50min
计量热灌装
温度:80-100℃
原料验收
原料验收标准
熟制
温度:105℃
时间:50min
计量热灌装
温度:80-100℃
蘸碟生产过程关键控制点记录
日期
时间
关键控制点名称
工艺要求
及控制参数
实际
结果
质量控制
运行情况
异常情况
处置措施
处置时间
处置结果
责任人
原料验收
原料验收标准
烘炒
温度:160℃
时间:25min
原料验收
原料验收标准
烘炒
温度:160℃
时间:25min
原料验收
原料验收标准
烘炒
温度:160℃
HACCP在食品生产流程中的关键控制点
HACCP在食品生产流程中的关键控制点HACCP(Hazard Analysis and Critical Control Points)是一种食品安全管理系统,用于识别并管理食品生产过程中可能存在的危害物质及其控制点,以确保食品安全和质量。
以下是HACCP在食品生产流程中的关键控制点。
1. 原料接收与存储:在食品生产流程中,原料的接收与存储是非常重要的环节。
关键控制点包括确保原料的新鲜度、合规性和正确的温度控制。
必须确保原料没有受到任何污染,如细菌、霉菌或其他危害物质。
2. 预处理:预处理阶段包括清洗、去除杂质、切割等过程。
在这个阶段,关键的控制点包括清洗剂的正确使用和溶液的浓度、处理水的质量、杂质去除的有效性以及卫生程序的严格执行。
3. 烹调与杀菌:烹调和杀菌步骤是确保食品安全的重要步骤。
关键控制点包括确保达到适当的温度和时间,以确保熟透并杀灭细菌、寄生虫和病毒。
4. 冷却与储存:在食品生产过程中,适当的冷却和储存是确保食品安全和质量的关键控制点。
食品冷却和储存应在适当的温度下进行,以防止细菌滋生和传播。
5. 包装与标识:食品包装和标识是确保产品质量和安全的重要步骤。
关键控制点包括使用适当的包装材料、正确的封口方法和标签的准确性。
食品包装应该能够保护食品免受外界污染和变质。
6. 运输与配送:在运输和配送过程中,食品应该保持在适当的温度下,并避免与可能污染食品的物质接触。
关键控制点包括运输温度的监控、车辆卫生的维护和货物的正确装载。
7. 消费准备:在食品消费准备的环节,关键控制点包括确保员工操作规范和卫生程序的遵守,熟食与生食的分开储存,食品接触表面的卫生清洁,以及遵循适当的温度和时间要求。
8. 回访和监测:HACCP的一个重要环节是回访和监测建立的控制点。
关键控制点包括对食品安全计划和程序的定期评估,确保流程中的危害物质没有滋生或增加。
在食品生产流程中准确识别和管理关键控制点是实施HACCP的关键。
- 1、下载文档前请自行甄别文档内容的完整性,平台不提供额外的编辑、内容补充、找答案等附加服务。
- 2、"仅部分预览"的文档,不可在线预览部分如存在完整性等问题,可反馈申请退款(可完整预览的文档不适用该条件!)。
- 3、如文档侵犯您的权益,请联系客服反馈,我们会尽快为您处理(人工客服工作时间:9:00-18:30)。
长春市食品生产企业食品安全管理通用记录表(四)
食品安全管理人员:
生产过程关键控制点记录
企业名称:
长春市食品药品监督管理局制
生产过程关键控制点记录
第页
备注:1.根据产品特性、食品安全标准要求,合理确定企业生产过程中的关键环节控制点,如生产工序、设备管理、贮存、包装等关键环节,包括必要的半成品检验记录、温度控制、车间洁净度控制等;2.制定关键控制点的操作控制程序或作业指导书,并按照要求组织实施,如实做好记录。