炉渣在高炉生产中的作用
高炉炼铁原理第四章造渣和脱硫过程(全)
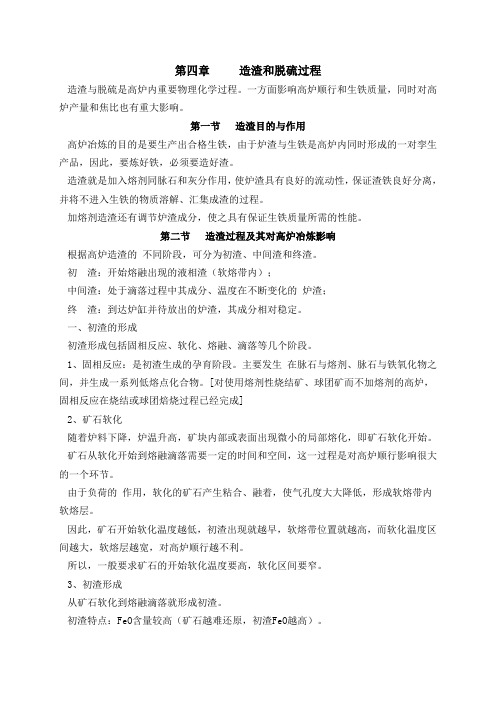
第四章造渣和脱硫过程造渣与脱硫是高炉内重要物理化学过程。
一方面影响高炉顺行和生铁质量,同时对高炉产量和焦比也有重大影响。
第一节造渣目的与作用高炉冶炼的目的是要生产出合格生铁,由于炉渣与生铁是高炉内同时形成的一对孪生产品,因此,要炼好铁,必须要造好渣。
造渣就是加入熔剂同脉石和灰分作用,使炉渣具有良好的流动性,保证渣铁良好分离,并将不进入生铁的物质溶解、汇集成渣的过程。
加熔剂造渣还有调节炉渣成分,使之具有保证生铁质量所需的性能。
第二节造渣过程及其对高炉冶炼影响根据高炉造渣的不同阶段,可分为初渣、中间渣和终渣。
初渣:开始熔融出现的液相渣(软熔带内);中间渣:处于滴落过程中其成分、温度在不断变化的炉渣;终渣:到达炉缸并待放出的炉渣,其成分相对稳定。
一、初渣的形成初渣形成包括固相反应、软化、熔融、滴落等几个阶段。
1、固相反应:是初渣生成的孕育阶段。
主要发生在脉石与熔剂、脉石与铁氧化物之间,并生成一系列低熔点化合物。
[对使用熔剂性烧结矿、球团矿而不加熔剂的高炉,固相反应在烧结或球团焙烧过程已经完成]2、矿石软化随着炉料下降,炉温升高,矿块内部或表面出现微小的局部熔化,即矿石软化开始。
矿石从软化开始到熔融滴落需要一定的时间和空间,这一过程是对高炉顺行影响很大的一个环节。
由于负荷的作用,软化的矿石产生粘合、融着,使气孔度大大降低,形成软熔带内软熔层。
因此,矿石开始软化温度越低,初渣出现就越早,软熔带位置就越高,而软化温度区间越大,软熔层越宽,对高炉顺行越不利。
所以,一般要求矿石的开始软化温度要高,软化区间要窄。
3、初渣形成从矿石软化到熔融滴落就形成初渣。
初渣特点:FeO含量较高(矿石越难还原,初渣FeO越高)。
高炉内初渣生成的区域称为软熔带。
根据高炉解体研究,在矿石完全熔化滴落以前,在软熔带内仍基本维持矿、焦分层状态,只是固态的矿石层变成了软熔层。
(见图)二、中间渣即处于软熔带以下、风口水平以上正在滴落过程的液相渣。
高Al2O3炉渣对高炉生产的影响

高Al2O3炉渣对高炉生产的影响随着我国钢铁产业的迅速发展,对炼铁原料的需求日益扩大,进口矿粉已占相当数量。
目前国内进口的矿粉主要是澳矿与印矿,这两种矿粉中Al2O3含量普遍偏高。
山东泰山钢铁集团(简称泰钢)高炉炉渣中Al2O3含量平均在18.2%左右,最高时可达到22%。
炉渣Al2O3含量高时炉渣的流动性和稳定性都将变差,易引起炉墙粘结与炉缸堆积,破坏高炉冶炼的正常进程,给高炉操作带来一系列的问题。
如不制定科学的操作方针与方法,将引起炉况不顺,影响产量与质量。
因此,Al2O3含量高的炉渣严重制约了高炉的正常生产。
2 Al2O3含量对炉渣性能的影响Al2O3属于中性,但在高炉冶炼中可认为是酸性物质,其熔点是2050℃,在高炉冶炼中与SiO2混合后仍产生高熔点(1545℃)的物质,使渣铁流动性差,分离困难。
当加入碱性物质如CaO或MgO后,尽管CaO的熔点是2570℃,MgO熔点是2800℃,但与SiO2和 Al2O3结合后生成低熔点(低于1400℃)的物质,在高炉内熔化,形成流动性良好的炉渣,使渣铁分离,保证高炉正常生产。
2.1 Al2O3小于15%时能够改善炉渣的稳定性当Al2O3含量在5%~20%、MgO含量小于20%时,在CaO/SiO2约为1.0的区域里熔化温度较低;当Al2O3含量低时,随着碱度的增加,炉渣熔化温度增加较快;当Al2O3含量大于10%后,随碱度增加,熔化温度增高减缓,熔化温度区域扩大,炉渣粘度随碱度变化也减缓,炉渣稳定性增加。
可以认为Al2O3的存在削弱了CaO/SiO2变化的影响。
2.2 高Al2O3炉渣对高炉冶炼的不利影响Al2O3小于15%时能够改善炉渣的稳定性,有利于高炉操作,但炉渣中Al2O3含量一般在15%~18%,原因是高Al2O3炉渣难以熔化,并且粘度增大,流动性变差,会产生以下负面影响:(1)高Al2O3炉渣的初渣堵塞炉料间的空隙,使料柱透气性变差,增加煤气通过时的阻力。
高炉的工作原理

高炉的工作原理
高炉是一种用于炼化铁矿石的设备,它的工作原理可以概括为以下几个步骤:
1. 加料:将铁矿石、焦炭和石灰石按照一定比例放入高炉的上部。
矿石中的铁氧化物与焦炭中的碳反应生成一氧化碳,同时释放出大量的热量。
2. 熔化:在高炉内,温度逐渐升高,矿石中的铁氧化物被还原为液态铁,与石灰石中的杂质形成炉渣。
液态的铁会逐渐下沉到高炉的底部,而炉渣则浮在铁上。
3. 分层:由于液态铁的密度较高,它会在高炉的底部逐渐积累形成铁水层。
而轻质的炉渣则会浮在铁水上形成炉渣层。
4. 放铁:当高炉中的铁水层积累到一定程度时,可以通过开启铁口将铁水抽出。
这些铁水会被引向冷却设备,形成铁水块。
整个过程中,高炉的内部温度可以达到几千摄氏度,高炉顶部的热风会自下而上通过高炉,使得矿石、焦炭等材料被加热。
在高炉的反应过程中,除液态铁和炉渣外,还会产生一些有害气体和粉尘。
为了减少对环境的影响,高炉内通常设置有除尘设备和尾气处理系统,对气体进行捕捉和净化处理。
炉渣的分类
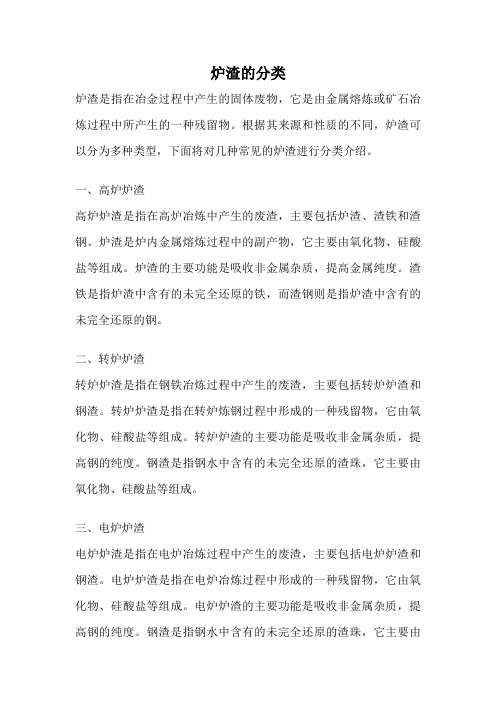
炉渣的分类炉渣是指在冶金过程中产生的固体废物,它是由金属熔炼或矿石冶炼过程中所产生的一种残留物。
根据其来源和性质的不同,炉渣可以分为多种类型,下面将对几种常见的炉渣进行分类介绍。
一、高炉炉渣高炉炉渣是指在高炉冶炼中产生的废渣,主要包括炉渣、渣铁和渣钢。
炉渣是炉内金属熔炼过程中的副产物,它主要由氧化物、硅酸盐等组成。
炉渣的主要功能是吸收非金属杂质,提高金属纯度。
渣铁是指炉渣中含有的未完全还原的铁,而渣钢则是指炉渣中含有的未完全还原的钢。
二、转炉炉渣转炉炉渣是指在钢铁冶炼过程中产生的废渣,主要包括转炉炉渣和钢渣。
转炉炉渣是指在转炉炼钢过程中形成的一种残留物,它由氧化物、硅酸盐等组成。
转炉炉渣的主要功能是吸收非金属杂质,提高钢的纯度。
钢渣是指钢水中含有的未完全还原的渣珠,它主要由氧化物、硅酸盐等组成。
三、电炉炉渣电炉炉渣是指在电炉冶炼过程中产生的废渣,主要包括电炉炉渣和钢渣。
电炉炉渣是指在电炉冶炼过程中形成的一种残留物,它由氧化物、硅酸盐等组成。
电炉炉渣的主要功能是吸收非金属杂质,提高钢的纯度。
钢渣是指钢水中含有的未完全还原的渣珠,它主要由氧化物、硅酸盐等组成。
四、冶炼渣冶炼渣是指在金属冶炼过程中产生的废渣,主要包括铝渣、铜渣、锌渣等。
铝渣是指在铝冶炼过程中形成的一种残留物,它由氧化物、硅酸盐等组成。
铜渣是指在铜冶炼过程中形成的一种残留物,它主要由氧化物、硅酸盐等组成。
锌渣是指在锌冶炼过程中形成的一种残留物,它由氧化物、硅酸盐等组成。
五、矿石渣矿石渣是指在矿石冶炼过程中产生的废渣,主要包括矿石渣、尾矿渣等。
矿石渣是指在矿石冶炼过程中形成的一种残留物,它由氧化物、硅酸盐等组成。
尾矿渣是指在选矿过程中产生的一种残留物,它主要由氧化物、硅酸盐等组成。
根据炉渣的来源和性质不同,可以将其分为高炉炉渣、转炉炉渣、电炉炉渣、冶炼渣和矿石渣等几种类型。
每种类型的炉渣都具有各自的特点和用途,在冶金行业中起着重要的作用。
高炉炼铁的反应原理
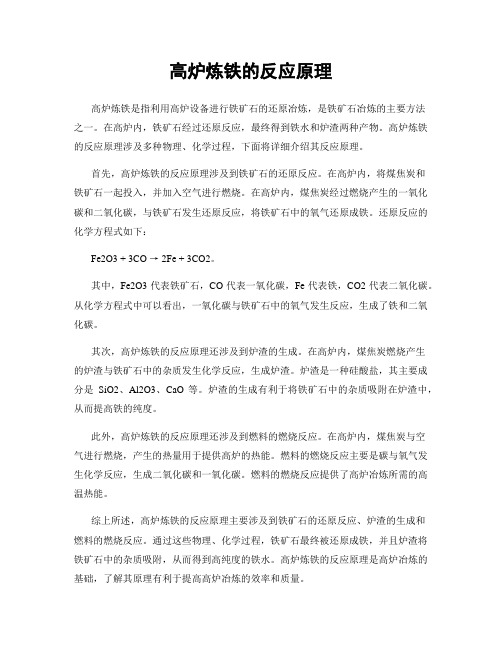
高炉炼铁的反应原理高炉炼铁是指利用高炉设备进行铁矿石的还原冶炼,是铁矿石冶炼的主要方法之一。
在高炉内,铁矿石经过还原反应,最终得到铁水和炉渣两种产物。
高炉炼铁的反应原理涉及多种物理、化学过程,下面将详细介绍其反应原理。
首先,高炉炼铁的反应原理涉及到铁矿石的还原反应。
在高炉内,将煤焦炭和铁矿石一起投入,并加入空气进行燃烧。
在高炉内,煤焦炭经过燃烧产生的一氧化碳和二氧化碳,与铁矿石发生还原反应,将铁矿石中的氧气还原成铁。
还原反应的化学方程式如下:Fe2O3 + 3CO → 2Fe + 3CO2。
其中,Fe2O3代表铁矿石,CO代表一氧化碳,Fe代表铁,CO2代表二氧化碳。
从化学方程式中可以看出,一氧化碳与铁矿石中的氧气发生反应,生成了铁和二氧化碳。
其次,高炉炼铁的反应原理还涉及到炉渣的生成。
在高炉内,煤焦炭燃烧产生的炉渣与铁矿石中的杂质发生化学反应,生成炉渣。
炉渣是一种硅酸盐,其主要成分是SiO2、Al2O3、CaO等。
炉渣的生成有利于将铁矿石中的杂质吸附在炉渣中,从而提高铁的纯度。
此外,高炉炼铁的反应原理还涉及到燃料的燃烧反应。
在高炉内,煤焦炭与空气进行燃烧,产生的热量用于提供高炉的热能。
燃料的燃烧反应主要是碳与氧气发生化学反应,生成二氧化碳和一氧化碳。
燃料的燃烧反应提供了高炉冶炼所需的高温热能。
综上所述,高炉炼铁的反应原理主要涉及到铁矿石的还原反应、炉渣的生成和燃料的燃烧反应。
通过这些物理、化学过程,铁矿石最终被还原成铁,并且炉渣将铁矿石中的杂质吸附,从而得到高纯度的铁水。
高炉炼铁的反应原理是高炉冶炼的基础,了解其原理有利于提高高炉冶炼的效率和质量。
炼铁原理解析高炉冶炼过程中的矿石还原与炉渣形成机制
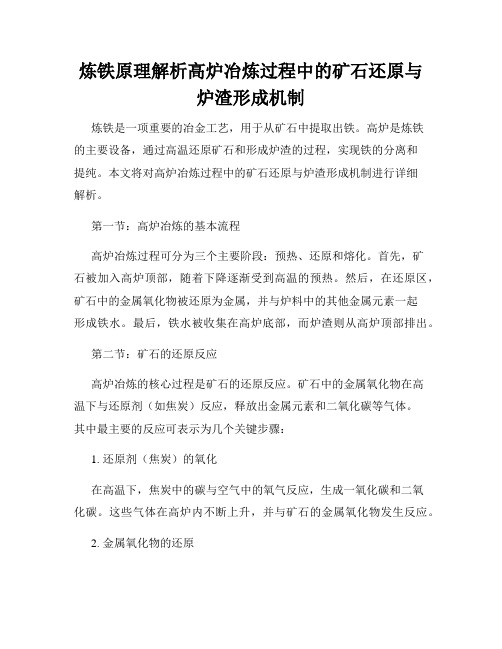
炼铁原理解析高炉冶炼过程中的矿石还原与炉渣形成机制炼铁是一项重要的冶金工艺,用于从矿石中提取出铁。
高炉是炼铁的主要设备,通过高温还原矿石和形成炉渣的过程,实现铁的分离和提纯。
本文将对高炉冶炼过程中的矿石还原与炉渣形成机制进行详细解析。
第一节:高炉冶炼的基本流程高炉冶炼过程可分为三个主要阶段:预热、还原和熔化。
首先,矿石被加入高炉顶部,随着下降逐渐受到高温的预热。
然后,在还原区,矿石中的金属氧化物被还原为金属,并与炉料中的其他金属元素一起形成铁水。
最后,铁水被收集在高炉底部,而炉渣则从高炉顶部排出。
第二节:矿石的还原反应高炉冶炼的核心过程是矿石的还原反应。
矿石中的金属氧化物在高温下与还原剂(如焦炭)反应,释放出金属元素和二氧化碳等气体。
其中最主要的反应可表示为几个关键步骤:1. 还原剂(焦炭)的氧化在高温下,焦炭中的碳与空气中的氧气反应,生成一氧化碳和二氧化碳。
这些气体在高炉内不断上升,并与矿石的金属氧化物发生反应。
2. 金属氧化物的还原金属氧化物与一氧化碳发生反应,还原成金属元素和二氧化碳。
这个还原反应是炉内主要的化学反应之一。
不同金属氧化物的还原程度和速率有所不同,这取决于各自的化学性质及温度条件。
3. 金属元素的迁移还原后的金属元素在高温下与其他金属元素结合,形成熔化的铁水。
这些金属元素在高炉内上升,直至达到悬浮于铁水上方的炉渣层。
第三节:炉渣的形成机制炉渣是高炉冶炼过程中的重要产物,它具有多种功能,如吸附杂质、稀释硫和磷等。
在高炉冶炼过程中,炉渣的形成主要经历以下几个步骤:1. 矿石中杂质的熔化矿石中的杂质(如硅、铝、钙等)在高温下被熔化,并分散于铁水和炉渣中。
这种熔化是高炉冶炼过程中的一个重要步骤,它有助于将杂质从铁水中分离出来。
2. 杂质的反应和吸附杂质在铁水和炉渣中发生各种化学反应,如与炉渣中的主要成分形成化合物或吸附于炉渣颗粒表面。
通过这些反应和吸附作用,炉渣能够有效地吸附和脱除铁水中的杂质。
高炉,炉渣、煤气,炉尘的用途
高炉煤气的用途
高炉煤气一般含有20%以上的一氧化碳、少量的氢和甲烧,发热值一般为2900-3800KJ/M3,是一种很好的低发热值气体燃料,除用来烧热风炉以外,还可供炼焦、加热炉和烧锅炉用。
高炉炉尘的用途
炉尘是随高速上升的煤气带离高炉的细颗粒炉料。
一般含铁30%—50%,含碳10%—20%。
经煤气除尘器回收后,可用作烧结矿原料。
高炉渣的用途
1。
液态炉渣用水急冷成水渣,可做水泥原料;
2。
液态炉渣用高压蒸汽或高压空气吹成渣棉,可做绝热保温材料;
3。
液态炉渣用少量高压水冲到一个旋转的滚筒上急冷而成膨珠,是良好的保温材料。
也用做轻质混凝土骨料;
4。
用炉渣制成的矿渣砖、干渣块可做铺路材料。
西安聚能仪器有限公司是专业从事气体成份分析技术以及仪器研发、生产、销售和服务为一体的高新技术企业,经过多年的研制开发和实践应用,在检测技术方面,成功的研制出拥有自主知识产权的在线分析检测系统和新型氧分析仪系列:微水量
(露点)分析仪系列,红外线分析仪系列,热导分析仪系列等;气相色谱仪等。
高炉炼铁中出铁口低于出渣口的原因
高炉炼铁中出铁口低于出渣口的原因
在高炉炼铁过程中,出铁口低于出渣口的设计是基于多方面的考虑的。
首先,生铁的密度大于炉渣的密度。
由于铁水相对较重,会自然下沉到炉缸底部,而炉渣则相对较轻,会浮在铁水上方。
因此,将出铁口设置在较低的位置,可以更容易地让铁水流出,而炉渣则通过出渣口排出。
其次,炉渣在炼铁过程中起到了过滤的作用。
炉渣可以吸收和去除铁水中的杂质和有害元素,使铁水更加纯净。
将出渣口设置在较高的位置,可以让炉渣在排出时经过更长的路程,从而提高过滤效果。
此外,出铁口低于出渣口的设计还可以减少铁水和炉渣的混合。
如果出铁口和出渣口高度相同或接近,可能会导致铁水和炉渣在流出时相互混合,影响铁水的质量和纯度。
通过降低出铁口的位置,可以减少这种混合的可能性。
另外,这种设计也有利于高炉的操作和维护。
较低的出铁口位置使得铁水的流动更加稳定,便于控制出铁速度和流量。
同时,出渣口的较高位置可以减少炉渣对出铁口的侵蚀和堵塞,延长高炉的使用寿命。
综上所述,出铁口低于出渣口的设计是为了优化炼铁过程中的铁水和炉渣分离、过滤效果,提高铁水质量,以及便于高炉的操作和维护。
这样的设计经过长期的实践和验证,被认为是一种较为合理和有效的高炉结构布置。
大型高炉提高利用系数的措施
大型高炉提高利用系数的措施随着钢铁工业的快速发展,大型高炉已成为钢铁生产的主要设备之一。
高炉的利用系数是衡量高炉生产效率的重要指标之一,提高高炉的利用系数对于提高钢铁生产效率和降低生产成本具有重要意义。
本文将探讨几种提高大型高炉利用系数的措施。
一、提高炉渣质量炉渣是高炉生产中不可避免的产物,其质量对高炉生产效率有着重要的影响。
炉渣的质量与高炉炉料的质量和配比、高炉操作、炉渣处理等因素有关。
提高炉渣质量的措施主要包括:1.严格控制炉料质量和配比,保证炉渣成分合理。
2.优化高炉操作,控制炉渣的基本性质,如炉渣的碱度、粘度、流动性等。
3.对炉渣进行有效处理,如采用高温煅烧、深度冷却等方式,提高炉渣的熔化度和流动性。
二、优化高炉操作高炉操作是影响高炉利用系数的重要因素之一。
优化高炉操作可以提高高炉的生产效率和稳定性,降低生产成本。
具体措施如下:1.优化炉料配比和质量,合理控制炉渣成分和性质。
2.控制高炉风量和压力,保证氧气供应充足,提高燃烧效率。
3.控制高炉温度和热负荷,避免高炉过热或过冷,保证高炉正常运行。
4.优化高炉煤气利用,提高回收率和利用效率。
三、提高炉料利用率提高炉料利用率是提高高炉利用系数的重要措施之一。
炉料利用率包括燃料利用率和铁料利用率。
提高炉料利用率的具体措施如下:1.优化炉料配比和质量,降低炉料消耗。
2.采用先进的炉料预处理技术,如煤气热解、炉料预热等,提高炉料利用率。
3.采用高效的炉内还原技术,如高温还原、低温还原等,提高铁料利用率。
四、加强高炉维护和管理高炉维护和管理是保证高炉正常运行和提高高炉利用系数的重要保障。
加强高炉维护和管理的具体措施如下:1.定期检查和维护高炉设备,保证高炉的正常运行。
2.建立完善的高炉管理制度,加强高炉生产数据的收集和分析,及时发现和解决问题。
3.加强高炉安全管理,保障生产人员的安全和健康。
综上所述,提高大型高炉利用系数的措施是多方面的,需要从炉渣质量、高炉操作、炉料利用率和高炉维护和管理等方面入手。
炼铁原理与工艺3(炉渣与脱硫)
13
3.2高炉炉渣的性质及其影响因素
2. 炉渣的黏度 • 炉渣黏度是炉渣流动性的倒数,黏度低流动性 好,反之亦然。 • F=η·S·dv/dx • F——流体流动时所克服的液体层间的内摩擦力; • S——两液体层间的接触面积; • dv——两液体间的速度差; • dx——两液体间的垂直距离; • η——内摩擦比例系数,称为黏度。
14
3.2高炉炉渣的性质及其影响因素
① 黏度的物理意义: • 液体的黏度是一个常数。其物理意义是:在单 位面积上,相距单位距离的两液体层之间,为 维持单位速度差所必须克服的内摩擦力。 • 黏度单位用Pa· s(帕· 秒)表示,1 Pa· s=1 N· s/m2,即F=1N,S=1 m2,dv=1 m/s,dx=1 m。过去使用泊(P)为单位,1 Pa· s=10 P ② 通常高炉炉渣黏度范围为0.5~2Pa· s之间,最 好在0.4~0.6Pa· s。
29
3.4高炉内的脱硫
4. 硫在煤气,渣,铁中的分配 S料=S挥+S铁+S渣 S料=S挥+ [S] + n(S) LS=(S)/[S] [S]=(S料-S挥)/1+nLS
30
3.4高炉内的脱硫
5.降低生铁含硫的途径 ① 降低炉料带入的总硫量 ② 改善炉渣脱硫能力 ③ 提高煤气带走的硫量
31
3.4高炉内的脱硫
3.3炉渣结构及矿物组成
③ 应用离子结构理论解释一些重要现象 A. 酸性渣在熔化后黏度仍较大,而碱性渣熔化后 黏度很低。 B. 向酸性渣中加入碱性氧化物MeO能降低黏度。 O/Si比增大。 C. 在一定温度下,炉渣的碱度升高超过一定值后, 炉渣黏度反而增加。使熔化温度升高则液相中 出现固体结晶颗粒,破坏了熔渣的均一性。 D. 炉渣中加入CaF2会大大降低炉渣的黏度。F-的 作用相似于O2-作用,它可使硅氧复合离子团分 解,变为简单的四面体,结构变小,黏度降低。
- 1、下载文档前请自行甄别文档内容的完整性,平台不提供额外的编辑、内容补充、找答案等附加服务。
- 2、"仅部分预览"的文档,不可在线预览部分如存在完整性等问题,可反馈申请退款(可完整预览的文档不适用该条件!)。
- 3、如文档侵犯您的权益,请联系客服反馈,我们会尽快为您处理(人工客服工作时间:9:00-18:30)。
---李利平
炉渣的成分
• • • • • • 炉渣的成分主要来源: 1.矿石中的脉石 2.焦炭灰分 3.溶剂氧化物 4.被侵的炉衬 5.初渣中大量的氧化物
炉渣的成分
• 对炉渣起决定性作用主要是前三项。脉石 好灰分主要成分是SiO2和Al2O3,称酸性氧 化物,溶剂氧化物主要是CaO和 MgO,称碱 性氧化物。它们之间相互作用形成低熔点 化合物,才能溶化成具有良好流动性的炉 渣。炉渣的主 1、分离渣铁。由于炉渣具有熔点低、密度小和不溶于生铁的特 点,所以高炉在冶炼过程中渣、铁才能得以分离,获得纯净的 和一铁,这是高炉造渣过程的基本作用。 • 2、调整生铁成分。渣铁之间进行合金元素的还原及脱硫反应, 起着控制生铁成分的作用。例如:高碱度渣铁能促进脱硫反应, 有利于锰的还的,从而提高生铁质量;SiO2含量高的护渣促进Si 的还原,从而控制生铁含Si量等。 • 3、对炉料下降和煤气分布的影响。炉渣的形成造成了高炉内的 软熔带及滴落带,对炉内煤气流分布及炉料的下降都有很大的 影响,因此,炉渣的性质和数量对高炉操作直接产生作用。 • 4、保护炉衬。炉渣附着在炉墙上形成渣皮,起扣护和护衬的作 用。但另一种情况下又可分能侵蚀炉衬,起破坏性作用。因此, 炉渣成分和性质直接影响高炉寿命。 • 在控制和调整炉渣成分和性质量,必须兼顾上述几方面的作用。
造渣制度
• 造渣制度的选择,取决于原料条件和冶炼 生铁的品种。确定适宜的造渣制度,使炉 渣物理热充足,流动性良好,脱硫能力强, 能保证高炉冶炼正常进行,获得优质产品。 • 1.高炉操作碱度由工长讨论,炉长决定,在 保证生铁质量的情况下,尽量维持较低碱 度。 • 2.维持渣中MgO含量在8-10%,以改善炉渣 性能