预裂爆破
预裂爆破技术
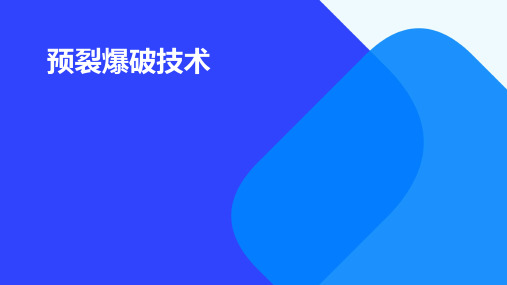
预裂爆破后的岩石破碎程度应满足工程要求, 以达到预期的工程效果。
预裂爆破效果的影响因素
炮眼布置
合理的炮眼布置可以提高预裂爆破效果,减 少对周围环境的影响。
装药结构
装药结构的合理性对预裂爆破效果有重要影 响,包括药包类型、药量等。
炸药性能
炸药的爆速、爆压等性能参数对预裂爆破效 果有直接影响。
特点
预裂爆破技术具有控制爆破规模、减轻爆破振动、减少爆破裂隙和保护岩体完 整性等特点,广泛应用于露天矿开采、路堑开挖、水下爆破等工程领域。
预裂爆破技术的应用范围
露天矿开采
在露天矿开采中,预裂爆破技术常用于控制采场边坡的破裂范围,保护边坡的完整性,提 高采矿作业的安全性和效率。
路堑开挖
在路堑开挖工程中,预裂爆破技术可以有效控制开挖断面的形状和尺寸,减少超挖和欠挖 现象,提高工程质量。
应力释放
当炸药在预裂孔中被引爆时,产生的应力波向四周传播,由于应力 波在预裂孔壁处受到阻碍,使得应力集中进一步增大。
裂缝形成
当应力波的强度超过岩石的抗拉强度时,预裂孔周围的岩石开始产 生拉伸裂缝,随着裂缝的扩展,最终形成预裂面。
预裂爆破的力学机制
应力波传播
炸药爆炸后产生的应力波在岩石中传播,使 岩石内部产生剪切、拉伸等应力状态。
动态挤压
炸药爆炸后产生的高温、高压气体迅速膨胀,对岩 石产生动态挤压作用,进一步促进岩石的破裂。
位移场形成
在预裂爆破过程中,由于应力波和动态挤压 的综合作用,使岩石内部形成位移场,导致 岩石破裂并形成预裂面。
03
预裂爆破的设计与实施
预裂爆破设计
01
确定爆破规模
02
设计炮眼布置
03
预裂爆破方案
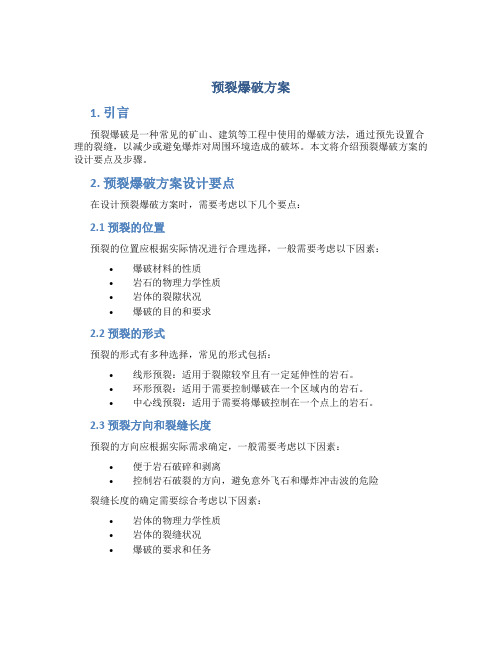
预裂爆破方案1. 引言预裂爆破是一种常见的矿山、建筑等工程中使用的爆破方法,通过预先设置合理的裂缝,以减少或避免爆炸对周围环境造成的破坏。
本文将介绍预裂爆破方案的设计要点及步骤。
2. 预裂爆破方案设计要点在设计预裂爆破方案时,需要考虑以下几个要点:2.1 预裂的位置预裂的位置应根据实际情况进行合理选择,一般需要考虑以下因素:•爆破材料的性质•岩石的物理力学性质•岩体的裂隙状况•爆破的目的和要求2.2 预裂的形式预裂的形式有多种选择,常见的形式包括:•线形预裂:适用于裂隙较窄且有一定延伸性的岩石。
•环形预裂:适用于需要控制爆破在一个区域内的岩石。
•中心线预裂:适用于需要将爆破控制在一个点上的岩石。
2.3 预裂方向和裂缝长度预裂的方向应根据实际需求确定,一般需要考虑以下因素:•便于岩石破碎和剥离•控制岩石破裂的方向,避免意外飞石和爆炸冲击波的危险裂缝长度的确定需要综合考虑以下因素:•岩体的物理力学性质•岩体的裂缝状况•爆破的要求和任务3. 预裂爆破方案设计步骤3.1 前期准备在设计预裂爆破方案之前,需要进行前期的准备工作,包括:•收集与岩石工程相关的资料和数据•进行现场勘察和实地调查,了解具体的地质情况和岩石特性•确定爆破的目的和要求•制定合理的工程计划和时间进度3.2 方案设计根据前期准备的结果,可以开始进行预裂爆破方案的设计:3.2.1 确定预裂的位置和形式根据岩体的特点和爆破的目标,选择适当的位置和形式进行预裂。
3.2.2 确定预裂方向和裂缝长度根据前期准备的数据和现场勘察结果,确定预裂的方向和裂缝长度。
3.2.3 选择合适的爆破材料根据岩体的物理力学性质和预裂的要求,选择适合的爆破材料。
3.2.4 设计合理的起爆序列根据岩体的裂隙状况和预裂的需要,设计合理的起爆序列,以达到预期的爆破效果。
3.3 方案评审和修改设计完预裂爆破方案后,需要进行方案评审和修改,主要包括:•经验技术人员对方案进行评审,提出修改意见和建议•根据评审结果,对方案进行修改和完善3.4 方案实施和监测在实施预裂爆破方案之前,需要进行必要的实施和监测工作,包括:•确保实施方案的安全性和可行性•监测预裂爆破的效果和影响•处理可能出现的意外情况和问题4. 结论预裂爆破方案是一种有效的控制爆破效果的方法,在岩石工程中得到广泛的应用。
预裂爆破施工方案
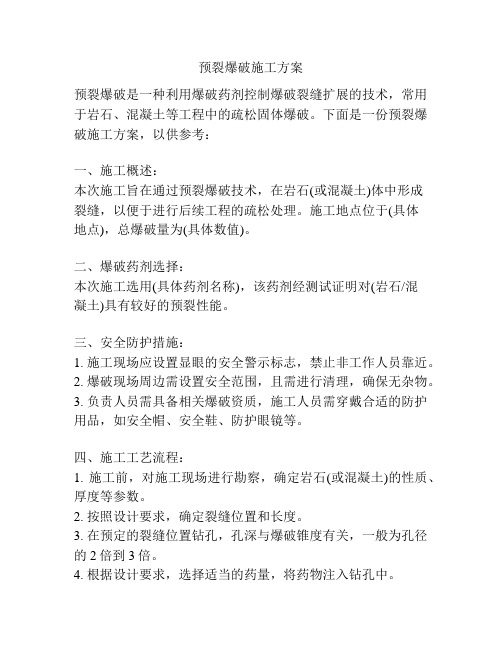
预裂爆破施工方案预裂爆破是一种利用爆破药剂控制爆破裂缝扩展的技术,常用于岩石、混凝土等工程中的疏松固体爆破。
下面是一份预裂爆破施工方案,以供参考:一、施工概述:本次施工旨在通过预裂爆破技术,在岩石(或混凝土)体中形成裂缝,以便于进行后续工程的疏松处理。
施工地点位于(具体地点),总爆破量为(具体数值)。
二、爆破药剂选择:本次施工选用(具体药剂名称),该药剂经测试证明对(岩石/混凝土)具有较好的预裂性能。
三、安全防护措施:1. 施工现场应设置显眼的安全警示标志,禁止非工作人员靠近。
2. 爆破现场周边需设置安全范围,且需进行清理,确保无杂物。
3. 负责人员需具备相关爆破资质,施工人员需穿戴合适的防护用品,如安全帽、安全鞋、防护眼镜等。
四、施工工艺流程:1. 施工前,对施工现场进行勘察,确定岩石(或混凝土)的性质、厚度等参数。
2. 按照设计要求,确定裂缝位置和长度。
3. 在预定的裂缝位置钻孔,孔深与爆破锥度有关,一般为孔径的2倍到3倍。
4. 根据设计要求,选择适当的药量,将药物注入钻孔中。
5. 确保药物注入后钻孔口无渗漏,如有渗漏,应迅速进行修补。
6. 检查作业现场,确保施工条件符合安全要求后,开始爆破作业。
7. 在爆破前,负责人员应清除现场人员。
8. 在安全防护距离内按照预定的时间进行爆破操作。
9. 爆破后,对现场进行清理和检查,排除安全隐患。
五、设备和材料准备:1. 钻孔设备:包括钻孔机、钻头、扳手等。
2. 爆破药剂:按设计要求准备足够的爆破药剂。
3. 安全防护设备:包括安全帽、安全鞋、防护眼镜等。
六、质量控制:1. 采用药物验证测试,确保药剂性能符合要求。
2. 严格按照设计要求施工,确保裂缝位置和长度准确。
3. 在施工过程中进行实时监测,确保施工质量。
4. 对爆破后的效果进行评估,并进行记录和备份。
以上是一个基本的预裂爆破施工方案,具体实施时还需根据实际情况进行调整和完善。
在施工过程中,务必遵守相关法律法规,确保施工安全和质量,以保障人员和设备的安全。
《预裂爆破技术》课件

传播方向的控制主要是通过调整炮孔的布置方式和角度, 确保炸药爆炸能量沿预裂面方向传播,以提高预裂面的质 量和减少对周围岩体的破坏。
03
CATALOGUE
预裂爆破的改进方向
优化施工工艺
通过优化施工工艺,降低预裂爆破技术的施 工难度,提高施工效率。
研究新型炸药
研究新型炸药,减少炸药消耗量,降低对环 境的影响。
加强监测与控制
加强爆破过程中的监测与控制,提高预裂爆 破的效果和安全性。
拓展应用范围
研究预裂爆破技术在其他领域的应用,拓展 其应用范围。
06
CATALOGUE
01
研发更加高效、环保、安全的炸药和爆破器材,提高预裂爆破
技术的效果和安全性。
智能化控制系统的研究
02
深入研究智能化控制系统,实现更加精确、智能的预裂爆破。
爆破效果评估与优化研究
03
加强爆破效果评估与优化研究,提高预裂爆破技术的工程效益
。
THANKS
感谢观看
预裂爆破技术
contents
目录
• 预裂爆破技术概述 • 预裂爆破技术的原理 • 预裂爆破的设计与施工 • 预裂爆破的效果评价 • 预裂爆破的优缺点分析 • 预裂爆破的未来发展展望
01
CATALOGUE
预裂爆破技术概述
定义与特点
定义
预裂爆破技术是一种在露天矿开采中 常用的控制爆破技术,通过在主爆区 周围设置预裂孔,控制爆破能量释放 ,减少对周围岩体的破坏。
预裂爆破的缺点
施工难度大
预裂爆破技术需要精确的钻孔和装药技术, 施工难度较大。
10m以上深孔预裂爆破的安全技术要求
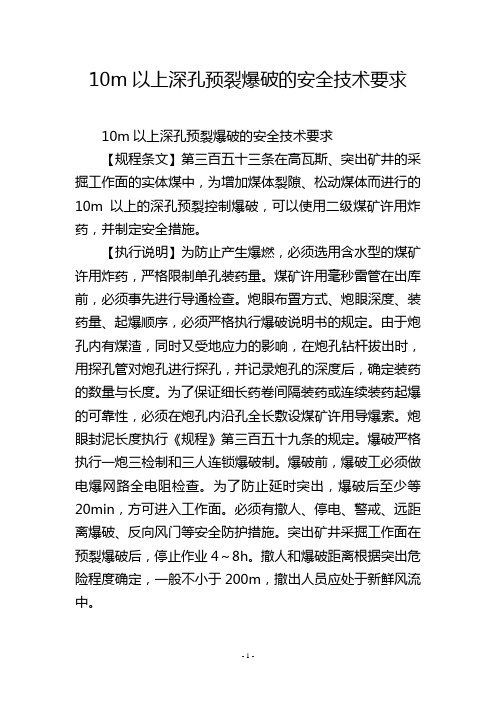
10m以上深孔预裂爆破的安全技术要求
10m以上深孔预裂爆破的安全技术要求
【规程条文】第三百五十三条在高瓦斯、突出矿井的采掘工作面的实体煤中,为增加煤体裂隙、松动煤体而进行的10m以上的深孔预裂控制爆破,可以使用二级煤矿许用炸药,并制定安全措施。
【执行说明】为防止产生爆燃,必须选用含水型的煤矿许用炸药,严格限制单孔装药量。
煤矿许用毫秒雷管在出库前,必须事先进行导通检查。
炮眼布置方式、炮眼深度、装药量、起爆顺序,必须严格执行爆破说明书的规定。
由于炮孔内有煤渣,同时又受地应力的影响,在炮孔钻杆拔出时,用探孔管对炮孔进行探孔,并记录炮孔的深度后,确定装药的数量与长度。
为了保证细长药卷间隔装药或连续装药起爆的可靠性,必须在炮孔内沿孔全长敷设煤矿许用导爆索。
炮眼封泥长度执行《规程》第三百五十九条的规定。
爆破严格执行一炮三检制和三人连锁爆破制。
爆破前,爆破工必须做电爆网路全电阻检查。
为了防止延时突出,爆破后至少等20min,方可进入工作面。
必须有撤人、停电、警戒、远距离爆破、反向风门等安全防护措施。
突出矿井采掘工作面在预裂爆破后,停止作业4~8h。
撤人和爆破距离根据突出危险程度确定,一般不小于200m,撤出人员应处于新鲜风流中。
- 1 -。
预裂爆破的原理

预裂爆破的原理预裂爆破技术是在岩石破碎领域中广泛应用的一种技术。
其原理是通过在岩石中预先制造一定的裂缝或已存在的微小裂缝,并将炸药放置在这些裂缝中,来达到最佳的岩石破碎效果。
本文将详细介绍预裂爆破技术的原理、方法以及适用情况。
一、预裂爆破的原理预裂爆破技术是将炸药安置在预制或已存在的微小裂缝中,通过炸药所产生的巨大压力,使得裂缝得以扩张,形成一定的破碎面和破碎面倾向,最终达到最佳的破碎效果。
预裂爆破的原理是利用了岩石在受力下的不同性质。
当岩石受到引力或弯曲作用时,其表面形成一定的应力,这时如果应力达到岩石的破坏强度,则岩石就会产生裂纹。
如果应力仍在增加,并且达到一定程度时,裂纹将继续扩张,直至岩石破碎。
在常规爆破中,炸药直接放置在岩石中心或顶部,产生的爆炸波直接产生压力,向四周膨胀,并最终达到破碎的目的。
与此不同的是,预裂爆破技术将炸药置于预制的或已存在的微小缝隙中,使炸药能够直接作用于裂缝中,产生更大的爆炸力和压力,并引起热量和气体的急剧释放,从而使缝隙得到更充分的扩张和扩展,进一步促进岩石的破碎。
二、预裂爆破的方法预裂爆破技术的主要方法包括:孔隙注浆法、无缝注浆法、爆破剂固化预制法、激光预制缝隙法等。
孔隙注浆法是通过向已有微小缝隙注入浆料,使得缝隙得到更深入的扩张和扩展,并且增加其稳定性。
注浆材料通常是聚丙烯酰胺树脂和岩石砂浆等,注入方法可以是振动注浆、离心注浆和压力注浆等。
无缝注浆法是将炸药固化在已有缝隙内,通常通过硅胶和硅酸盐水泥等材料进行注浆,来保证炸药的安全性和可靠性。
爆破剂固化预制法是将爆破剂与快固化粘合剂混合后直接固定在岩石上,以制造出一定的预制缝隙。
这种方法适用于岩石比较硬的情况下,能够有效地提高爆破效果。
激光预制缝隙法是将激光束直接照射到岩石表面,制造出一定的缝隙。
由于该方法需要使用高功率激光,所以必须注意安全问题,并且其适用范围较为有限。
三、预裂爆破的适用情况预裂爆破技术适用于以下情况:1.岩石质量较硬、坚固并且密度较大的情况下,传统的爆破方法效果较差。
光面爆破与预裂爆破比较分析
光面爆破与预裂爆破比较分析
一、光面爆破与预裂爆破比较
1、光面爆破与预裂爆破的材料
光面爆破是指对爆破石墨板上的龙门、冰裂缝等表面形成一道裂缝,
而预裂爆破则是利用梁状结构(如混凝土砌体、钢筋混凝土结构等),将
爆破材料(如煤屑、沙子、砂粒等)填充在梁状的缝隙,然后点燃爆破剂,以达到爆破的目的。
2、光面爆破与预裂爆破的特点
(1)光面爆破产生的爆破效果比较剧烈,能够产生较强的冲击波,
但是其爆轰片最多只能达到一定的范围,不能达到比较大的空间效果。
(2)预裂爆破产生的爆破效果稳定,能够产生比较大的散落物,可
以有效地增加爆破的空间效果,但是其产生的冲击波相对较小,爆轰片范
围也较小。
3、光面爆破与预裂爆破的应用
光面爆破主要用于采矿、建筑施工、核电站建设、管道建设等场合,
而预裂爆破则主要应用于采掘工程、深孔爆破等行业,以及需要有较大空
间效果的场合。
综上所述,光面爆破与预裂爆破各有其优势和不足,在实际应用中应
当根据不同的情况来选择不同的爆破方法,以达到最佳的爆破效果。
预裂爆破
预裂爆破进行石方开挖时,在主爆区爆破之前沿设计轮廓线先爆出一条具有一定宽度的贯穿裂缝,以缓冲、反射开挖爆破的振动波,控制其对保留岩体的破坏影响,使之获得较平整的开挖轮廓,此种爆破技术为预裂爆破。
预裂爆破不仅在垂直、倾斜开挖壁面上得到广泛应用;在规则的曲面、扭曲面、以及水平建基面等也采用预裂爆破。
预裂爆破要求:(1)预裂缝要贯通且在地表有一定开裂宽度。
对于中等坚硬岩石,缝宽不宜小于1. 0cm;坚硬岩石缝宽应达到0.5cm左右;但在松软岩石上缝宽达到1.0cm以上时,减振作用并未显著提高,应多做些现场试验,以利总结经验。
(2)预裂面开挖后的不平整度不宜大于15cm。
预裂面不平整度通常是指预裂孔所形成之预裂面的凹凸程度,它是衡量钻孔和爆破参数合理性的重要指标,可依此验证、调整设计数据。
(3)预裂面上的炮孔痕迹保留率应不低于80%,且炮孔附近岩石不出现严重的爆破裂隙。
预裂爆破主要技术措施如下:(1) 炮孔直径一般为50~200mm,对深孔宜采围较大的孔径。
(2)炮孔间距宜为孔径的8~12倍,坚硬岩石取小值。
(3)不耦合系数(炮孔直径d与药卷直径d0的比值)建议取2~4,坚硬岩石取小值。
(4)线装药密度一般取250~400g/m。
(5)药包结构形式,目前较多的是将药卷分散绑扎在传爆线上(图1-21)。
分散药卷的相邻间距不宜大于50cm和不大于药卷的殉爆距离。
考虑到孔底的夹制作用较大,底部药包应加强,约为线装药密度的2~5倍。
(6)装药时距孔口1m左右的深度内不要装药,可用粗砂填塞,不必捣实。
填塞段过短,容易形成漏斗,过长则不能出现裂缝。
预裂爆破和光面爆破为保证保留岩体按设计轮廓面成型并防止围岩破坏,须采用轮廓控制爆破技术。
常用的轮廓控制爆破技术包括预裂爆破和光面爆破。
所谓预裂爆破,就是首先起爆布置在设计轮廓线上的预裂爆破孔药包,形成一条沿设计轮廓线贯穿的裂缝,再在该人工裂缝的屏蔽下进行主体开挖部位的爆破,保证保留岩体免遭破坏;光面爆破是先爆除主体开挖部位的岩体,然后再起爆布置在设计轮廓线上的周边孔药包,将光爆层炸除,形成一个平整的开挖面。
5.2预裂爆破
5.2 预裂爆破定义:沿开挖边界布置密集炮孔,采取不耦合装药或装填低威力炸药,在主爆区之前起爆,在爆破与保留区之间形成一道有一定宽度的贯穿裂缝,以减弱主爆区爆破时对保留岩体的破坏,并形成平整轮廓面的爆破作业,称为预裂爆破。
预裂爆破是露天深孔周边控制爆破的一种主要爆破技术,由于具有明显的降震作用,已被广泛采用。
国内露天预裂爆破一次预裂的深度达25m。
5.2.1 露天预裂爆破参数设计5.2.1.1 孔网参数包括:预裂孔直径、孔间距、孔深、预裂孔的排列方式及预裂孔与主爆孔的相互排列方式。
(1)炮孔直径d一般孔径越小,孔痕率就越高。
一般采用50~120mm的孔径;国内一些矿山,采用Φ150mm~250mm 也能获得满意的效果。
(2)孔间距a孔间距是直接影响预裂带壁面光滑程度的重要参数,孔间距小则预裂带壁面光滑平整。
①永久边坡宜取:a =(7~10)d ;②3~5年的临时边坡宜取:a =(10~15)d 倍;③其他临时边坡取:a =(15~20)d 。
原则是硬岩取大值,软岩、破碎岩石取小值。
(3)炮孔深度与超深孔深必须考虑减少对台阶底部的破坏。
因此,超深值必须尽量减少。
预裂孔原则不得超深,最多不超过0.5m。
(4)与邻近孔的排距一般为正常炮孔的一半,主要是控制孔底距离不得大于1.5—2.5m。
如果最后一排主爆孔的孔径和装药量都比较大,其值可适当放宽到6~7 m。
其评价标准是,预裂缝与最后一排炮孔之间的岩体能够得到应有的破碎,且不能破坏已形成的预裂面。
5.2.1.2 装药参数(1)不耦合系数k在实际使用中,其控制在2~5,以2~4为多。
硬岩取小值,软岩、破碎岩石取大值。
(2)线装药密度Q线线装药密度指炮孔装药量对不包括堵塞部分的炮孔长度之比。
其一般为0.1~1.5kg/m。
由于孔底岩石夹制作用大,为确保预裂缝贯通到孔底,在孔底:l~2m长度上,应适当增加装药量:当孔深小于5m时,每延米装药量增加1~2倍;孔深为5~10m时,增加2~3倍,孔深大于10m 时,增加3~5倍。
什么叫预裂爆破?预裂爆破和缓冲爆破有何区别?
什么叫预裂爆破?预裂爆破和缓冲爆破有何区别?预裂爆破?预裂爆破和缓冲爆破有何区别?露天矿预裂爆破是边坡境界上钻一排密集的预裂孔,在主炮孔爆破之前爆破。
预裂孔爆破时沿孔连线发展成为预裂缝。
预裂爆破可以显著地减少爆破对边坡的破坏和清帮工作量。
预裂爆破施工如图1所示。
图1 预裂爆破示意图1-辅助孔;2-预裂孔;3-预裂线;4-缓冲孔;S1-2.5~3m;S2-1~2m预裂爆破施工时要注意以下要点:一、严格按设计孔位施工,露天开挖工程中,炮孔前后移位偏差不应大于20~30cm。
二、采用不耦合装药结构时,药包应尽可能放置在炮孔中心,炮孔底部药量应增加1~3倍。
三、炮孔一般不超深,孔口未装药部分是孔深的15%~30%。
四、预裂孔应预先起爆或超前邻近主炮孔50~100ms 起爆。
五、预裂孔一般应同时起爆,但为了降低预裂孔爆破的地震波效应,亦可分段起爆。
缓冲爆破是选择前排孔到后排孔递减的药量比例,使爆区后方震动强度取决于最后一排孔的爆炸。
缓冲爆破的特点是:以前排孔到未排孔的排距、超深逐步减小,在边坡境界线的未排孔较密。
使装药量逐步递减,且分布更加均匀,使爆破震动降低。
缓冲爆破和预裂爆破都叫减震爆破。
二者的不同是:预裂爆破于主爆炮孔之前起爆,在主爆与被保护岩体之间预先炸出一条裂隙,缓冲爆破则是与主爆炮孔同时起爆,由于装药量的减少,减轻了爆破震动破坏。
预裂爆破?预裂爆破和缓冲爆破有何区别?露天矿预裂爆破是边坡境界上钻一排密集的预裂孔,在主炮孔爆破之前爆破。
预裂孔爆破时沿孔连线发展成为预裂缝。
预裂爆破可以显著地减少爆破对边坡的破坏和清帮工作量。
预裂爆破施工如图1所示。
图1 预裂爆破示意图1-辅助孔;2-预裂孔;3-预裂线;4-缓冲孔;S1-2.5~3m;S2-1~2m预裂爆破施工时要注意以下要点:一、严格按设计孔位施工,露天开挖工程中,炮孔前后移位偏差不应大于20~30cm。
二、采用不耦合装药结构时,药包应尽可能放置在炮孔中心,炮孔底部药量应增加1~3倍。
- 1、下载文档前请自行甄别文档内容的完整性,平台不提供额外的编辑、内容补充、找答案等附加服务。
- 2、"仅部分预览"的文档,不可在线预览部分如存在完整性等问题,可反馈申请退款(可完整预览的文档不适用该条件!)。
- 3、如文档侵犯您的权益,请联系客服反馈,我们会尽快为您处理(人工客服工作时间:9:00-18:30)。
预裂爆破和光面爆破
为保证保留岩体按设计轮廓面成型并防止围岩破坏,须采用轮廓控制爆破技术。
常用的轮廓控制爆破技术包括预裂爆破和光面爆破。
所谓预裂爆破,就是首先起爆布置在设计轮廓线上的预裂爆破孔药包,形成一条沿设计轮廓线贯穿的裂缝,再在该人工裂缝的屏蔽下进行主体开挖部位的爆破,保证保留岩体免遭破坏;光面爆破是先爆除主体开挖部位的岩体,然后再起爆布置在设计轮廓线上的周边孔药包,将光爆层炸除,形成一个平整的开挖面。
预裂爆破和光面爆破在坝基、边坡和地下洞室岩体开挖中获得了广泛应用。
(一)成缝机理
预裂爆破和光面爆破都要求沿设计轮廓产生规整的爆生裂缝面,两者成缝机理基本一致。
现以预裂缝为例论述它们的成缝机理。
预裂爆破采用不耦合装药结构,其特征是药包和孔壁间有环状空气间隔层,该空气间隔层的存在削减了作用在孔壁上的爆炸压力峰值。
因为岩石动抗压强度远大于抗拉强度,因此可以控制削减后的爆压不致使孔壁产生明显的压缩破坏,但切向拉应力能使炮孔四周产生径向裂纹。
加之孔与孔间彼此的聚能作用,使孔间连线产生应力集中,孔壁连线上的初始裂纹进一步发展,而滞后的高压气体的准静态作用,使沿缝产生气刃劈裂作用,使周边孔间连线上的裂纹全部贯通成缝。
(二)质量控制标准
1)开挖壁面岩石的完整性用岩壁上炮孔痕迹率来衡量,炮孔痕迹率也称半孔率,为开挖壁面上的炮孔痕迹总长与炮孔总长的百分比率。
在水电部门,对节理裂隙极发育的岩体,一般应使炮孔痕迹率达到10%~50%;节理裂隙中等发育者应达50%~80%;节理裂隙不发育者应达80%以上。
围岩壁面不应有明显的爆生
裂隙。
2)围岩壁面不平整度(又称起伏差)的允许值为±15cm。
3)在临空面上,预裂缝宽度一般不宜小于1cm。
实践表明,对软岩(如葛洲坝工程的粉砂岩),预裂缝宽度可达2cm以上,而且只有达到2cm以上时,才能起到有效的隔震作用;但对坚硬岩石,预裂缝宽度难以达到1cm。
东江工程的花岗岩预裂缝宽仅6 m m,仍可起到有效隔震作用。
地下工程预裂缝宽度比露天工程小得多,一般仅达0.3~0.5cm。
因此,预裂缝的宽度标准与岩性及工程部位有
关,应通过现场试验最终确定。
影响轮廓爆破质量的因素,除爆破参数外,主要依赖于地质条件和钻孔精度。
这是因为爆生裂缝极易沿岩体原生裂隙、节理发展,而钻孔精度则是保证周边控爆
质量的先决条件。
(三)参数设计
预裂爆破和光面爆破的参数设计一般采用工程类比法,并通过现场试验最终确
定。
(1)预裂爆破参数
1)孔径
明挖工程为7 0~165mm;隧洞开挖为40~90mm;大型地下厂房为50~110mm。
2)孔距
与岩石特性、炸药性质、装药情况、开挖壁面平整度要求和孔径大小有关。
孔距一般为孔径的7~12倍。
爆破质量要求高、岩质软弱、裂隙发育者取小值。
3)装药不偶合系数
不偶合系数指炮孔半径与药卷半径的比值,为防止炮孔壁的破坏,该值一般取
2~5。
4)线装药密度
线装药密度是单位长度炮孔的平均装药量。
影响预裂爆破参数的因素复杂,很难从理论上推导出严格的计算公式,以经验公式为主,目前国内较常用公式的基本
形式为
式中,QX—预裂爆破的线装药密度,kg/m;
σC—岩石的极限抗压强度,MPa;
a—炮孔间距,m;
d—钻孔直径,mm;
K、α、β和γ—经验系数。
随岩性不同,预裂爆破的线装药密度一般为200~500g/m。
为克服岩石对孔底的夹制作用,孔底段应加大线装药密度到2~5倍。
(2)光面爆破参数
1)光面爆破层厚度即最小抵抗线的大小,一般为炮孔直径的10~20倍,岩质
软弱、裂隙发育者取小值。
2)孔距一般为光面爆破层厚度的0.75~0.90倍,岩质软弱、裂隙发育者取小
值。
3)钻孔直径及装药不偶合系数
参照预裂爆破选用。
4)线装药密度Qx
一般按照松动爆破药量计算公式确定
式中q—松动爆破单耗,kg/m3;
a—光面爆破孔间距,m;
W—光面爆破层厚度,m。
(四)装药结构与起爆
(1)装药结构
1)堵塞段
堵塞段的作用是延长爆生气体的作用时间,且保证孔口段只产生裂缝而不出现爆破漏斗,对深孔爆破该段长一般取0.5~1.5m。
2)孔底加强段
段长大体等于堵塞段。
由于孔底受岩石夹持作用,故需用较大的线装药密度。
3)均匀装药段该段一般为轴向间隔不偶合装药,并要求沿孔轴线方向均匀分布。
轴向间隔装药须用导爆索串联各药卷起爆。
为保证孔壁不被粉碎,药卷应尽量置于孔的中心。
国外一般用炮孔中心定位器定位,国内一般是将药卷及导爆索绑于
竹片进行药卷定位。
(2)起爆
为保证同时起爆,预裂爆破和光面爆破一般都用导爆索起爆,并通常采用分段并
联法。
由于光面爆破孔是最后起爆,导爆索有可能遭受超前破坏。
为保证周边孔准爆,对光面爆破孔可采用高段延期雷管与导爆索的双重起爆法。
预裂孔若与主爆区炮孔组成同一网路起爆,则预裂孔应超前第一排主爆孔75~100ms起爆。