中国压铸行业发展历程及现状
中国压铸业发展历程与进步
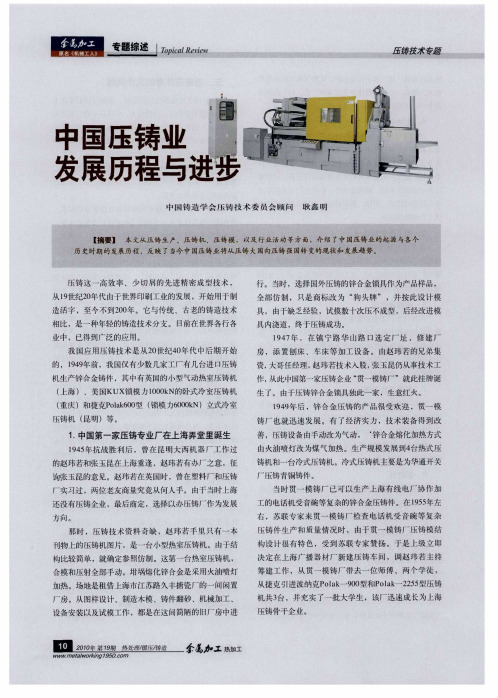
1 中国第一家压铸专业厂在上海弄堂里诞生 .
1 4 年抗 战胜 利后 ,曾在 昆 明大 西机 器 厂工 作过 95
的赵玮若和张玉 昆在上 海重逢 ,赵玮若有 办厂之意 ,征 询 张玉昆的意 见。赵玮 若在英国时 ,曾在 塑料 厂和压铸
机生 产锌合金铸件 ,其 中有 英国的小型 气动热 室压铸机 ( 上海 )、美 国KUX锁模 力10 k 0 0 N的卧式 冷室压 铸机 ( 重庆)和捷 ̄, l 6 0 ( P a 0 型 锁模 力6 0 k ok 0 0 N)立式冷室
l4 年 .在 镇 宁 路 华 山 路 口选 定 厂址 ,修 建 厂 7 9 房 ,添 置刨 床 、车 床等 加 工设 备 。 由赵玮 若 的兄弟集 资, 哥任经理 , 大 赵玮 若技术人股 , 玉昆仍从事技 术工 张发 国 展 压 历
;
I 摘要 l 本 文从压 铸 生 产 、压 铸 机 、压 铸模 , 以及行 业 活 动 等方 面,介 绍 了中 国压 铸 业 的起 源 与各 个 历 史时期 的发展 历程 ,反 映 了当今 中 国压铸 业将从 压 铸 大 国向压 铸 强 国转 变的现状 和 发展趋 势 。
构比较简单 ,就确 定参照仿制 。这第 一台热室压铸机 ,
合模和压射全部手 动。坩埚熔化锌合 金是采用火油喷灯 加热。场地是租借上海 市江苏路久丰搪 瓷厂的一 间闲置
从捷 克 引进 波纳克P lk o 型 ̄P l -2 5型压铸 oa 一90 N oa k 25
机 共3 ,并充实 了一批大 学生 ,该 厂迅速 成长 为上海 台
铸 程 业 与 进 醇 步
■ ■ ■一 ● ■ ■ ■ 一 ■■ ● I , ■ ■ 一一一, —
压铸行业情况分析 (一)

压铸行业情况分析 (一)压铸行业是一种以金属材料为主要原材料,将其加热到熔点后,通过高压力将其注入一定型腔内,冷却后获取所需要零部件的加工方法。
该行业在制造业中具有举足轻重的地位,是制造业的重要组成部分。
本文将就压铸行业的情况进行分析。
一、行业发展概述过去几年,随着我国汽车、5G、电子等领域的迅猛发展,压铸行业的应用范围也逐步扩大,对于形态干净的零部件需求日益增加。
2018年,我国铸造产业总产值达到2.78万亿元,其中压铸行业产值占据了20%的份额,是该行业中的龙头企业。
预计未来几年,随着一些新技术和新材料的推广,压铸行业将继续呈现出良好的增长态势。
二、市场现状分析1. 普通铸造行业的转型升级由于国内压铸行业技术含量较高,市场经营成本也居高不下,许多普通铸造企业已经开始向压铸模具方向进行转型,以求在激烈市场竞争中占据优势。
不仅如此,一些国外企业也纷纷进军国内市场,给国内企业带来了极大的压力。
2. 智能化程度的提升随着人工智能、大数据等技术的发展,压铸行业在智能化程度方面也在不断提升。
一方面,这些技术的应用能够将生产效率提高到更高的水平,另一方面也能够提高产品的可靠性和质量。
3. 生产工艺和生产设备的升级在压铸行业中,生产工艺和生产设备的升级也是非常重要的。
高端的压铸设备可提高产品的精度和表面质量,而最新的智能模具技术也能够降低生产成本。
因此,保持行业内核心技术的先进性也是企业在市场中获得成功的关键。
三、未来发展趋势1. 绿色生产将成为压铸行业的发展方向。
在恶劣的环境下,压铸行业长期以来存在诸多环境问题。
未来几年,绿色生产将成为压铸行业发展的一个重要方向,包括材料的绿色环保,节能减排等方面。
2. 智慧生产的应用将逐渐普及。
随着人工智能和大数据技术的快速发展,智能制造将逐渐普及到压铸行业中,这将使生产智能化、自动化程度提高,对于提高产品的质量和生产效率将有很大的帮助。
3. 拓展产业链以增加附加值。
压铸行业是一个庞大的产业链,这个行业中的企业不仅可以承担生产和销售的角色,同时也可以拓展产业链,在行业内进行良好的补充和配合,来提高整个产业的附加值。
2023年压铸行业市场分析现状

2023年压铸行业市场分析现状压铸行业是一种通过将熔融金属注入模具中,并在冷却后形成所需形状的生产工艺。
压铸件在汽车、电子、军工、航空航天等众多领域都有广泛的应用。
本文将对压铸行业的市场现状进行分析。
一、市场规模和增长趋势压铸行业市场规模庞大且日益增长。
根据市场研究机构的数据,预计到2025年,全球压铸行业市场规模将超过3000亿美元。
这主要得益于汽车、航空航天等领域的发展,对复杂铸件的需求不断增长。
二、中国市场中国是全球最大的压铸市场之一。
近年来,随着汽车、电子等行业的快速发展,对高精度、高质量压铸件的需求呈现爆发式增长。
据统计,中国每年生产的压铸件数量超过2000万吨,约占全球总产量的40%以上。
三、市场竞争格局压铸行业的市场竞争格局较为复杂。
市场上存在着大量的中小型企业,规模较大的企业主要集中在中国、美国、德国等发达国家。
竞争主要体现在技术创新、产品质量和价格方面。
四、技术创新与产品升级随着市场需求的不断变化,技术创新和产品升级成为企业竞争的重要手段。
传统的压铸工艺已经不能满足市场的高要求,因此,企业需要加大研发投入,引进先进的生产设备和工艺,提高产品质量和生产效率。
五、环保与可持续发展在全球环保意识的提高下,压铸行业也面临着一系列的环保压力。
压铸工艺中使用的金属和化学品会对环境造成一定的污染。
因此,企业需要加强环保管理,推动减少能源消耗和废物排放的技术创新。
六、国际市场开拓随着全球一体化的推进,压铸行业国际市场的开拓日益重要。
中国的压铸企业在国内市场的竞争已经十分激烈,因此,更多的企业开始积极拓展国际市场。
通过参加国际展览会、建立海外销售网络等方式,企业可以增加海外订单和市场份额。
综上所述,压铸行业市场在中国和全球都呈现出良好的增长趋势。
随着技术的不断进步和市场需求的不断变化,压铸企业需要加大研发力度,提高产品质量和生产效率。
同时,环保和可持续发展也是企业发展的重要方向。
对于中国的压铸企业来说,拓展国际市场也是一项重要的战略,以增加市场份额和降低竞争压力。
2024年压铸件市场分析现状

2024年压铸件市场分析现状引言压铸件是一种常见的金属制品,广泛应用于汽车、电子、家电等行业。
本文将对当前压铸件市场的现状进行分析,并对未来的发展趋势进行展望。
市场概况压铸件市场是一个庞大的市场,涉及多个领域。
近年来,随着工业化的加速发展和全球经济的不断增长,压铸件市场也呈现出稳定增长的态势。
目前,中国是全球压铸件市场的主要生产和消费国家。
市场主要参与者压铸件市场的主要参与者包括压铸件制造商、供应商、经销商和最终用户。
压铸件制造商是市场的核心参与者,他们负责生产和提供各种类型的压铸件。
市场竞争格局目前,全球压铸件市场的竞争格局相对集中。
一些大型的压铸件制造商占据了市场的主导地位,他们通过技术创新和优质产品的提供来赢得市场份额。
此外,一些新兴的压铸件制造商也在市场中崭露头角,他们通过低成本和灵活性来吸引客户。
市场发展趋势未来,压铸件市场将面临以下几个发展趋势:1.技术创新:随着科技的不断发展,压铸件制造技术也在不断进步。
新的材料、新的工艺和新的设备将进一步改善压铸件的质量和性能。
2.环保要求:随着环保意识的增强,压铸件制造商将面临更严格的环保要求。
这将促使他们加大对环保技术和材料的研发投入。
3.智能制造:智能制造是当前制造业的发展趋势,压铸件制造也不例外。
通过引入自动化和物联网技术,压铸件制造商可以提高生产效率和产品质量。
4.新兴市场的崛起:一些新兴市场,如印度、巴西和东南亚国家,正在经历快速的工业化进程。
这将为压铸件市场带来新的增长机遇。
市场挑战尽管压铸件市场前景广阔,但也面临一些挑战:1.价格竞争:由于市场竞争激烈,压铸件制造商需要在保证产品质量的前提下降低成本,以提供竞争力的价格。
2.人才短缺:压铸件制造需要高技术工人的参与,但目前人才供给不足。
制造商需要加大对人才培养和引进的力度。
3.资源压力:压铸件制造需要大量的能源和原材料,随着资源的紧张和价格的不断上涨,制造商需要寻找替代资源或采取节约措施。
2024年压铸市场分析现状
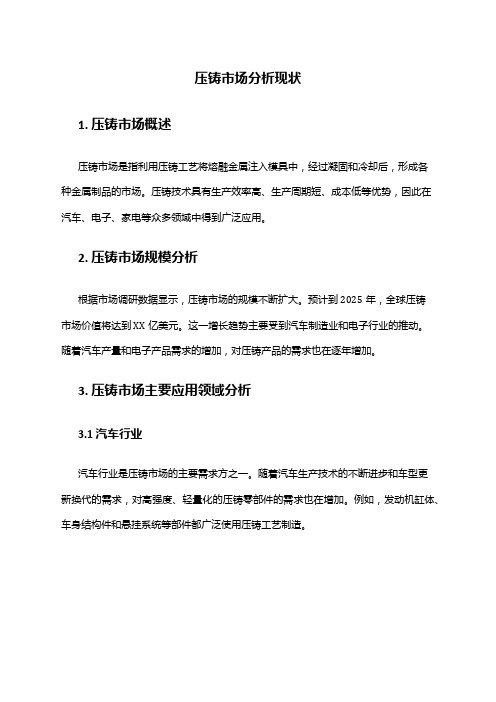
压铸市场分析现状1. 压铸市场概述压铸市场是指利用压铸工艺将熔融金属注入模具中,经过凝固和冷却后,形成各种金属制品的市场。
压铸技术具有生产效率高、生产周期短、成本低等优势,因此在汽车、电子、家电等众多领域中得到广泛应用。
2. 压铸市场规模分析根据市场调研数据显示,压铸市场的规模不断扩大。
预计到2025年,全球压铸市场价值将达到XX亿美元。
这一增长趋势主要受到汽车制造业和电子行业的推动。
随着汽车产量和电子产品需求的增加,对压铸产品的需求也在逐年增加。
3. 压铸市场主要应用领域分析3.1 汽车行业汽车行业是压铸市场的主要需求方之一。
随着汽车生产技术的不断进步和车型更新换代的需求,对高强度、轻量化的压铸零部件的需求也在增加。
例如,发动机缸体、车身结构件和悬挂系统等部件都广泛使用压铸工艺制造。
3.2 电子行业电子行业也是压铸市场的重要应用领域。
手机、电脑、摄像机等电子产品中的外壳、金属结构件等都需要通过压铸技术来实现生产。
随着电子产品的更新换代速度加快,对高精度、高速生产的压铸设备和技术的需求也在增加。
3.3 家电行业家电行业对压铸产品的需求主要集中在制造家电外壳和零部件方面。
随着家电产品多样化和个性化的需求增加,对高质量、高精度的压铸产品的需求也在不断增加。
4. 压铸市场竞争状况分析目前,全球压铸市场存在一定的竞争压力。
主要竞争者之一是中国,其在压铸设备和技术上具有一定的优势和竞争力。
然而,其他国家和地区也在不断提升竞争力,尤其是北美地区和欧洲地区。
这些地区拥有先进的制造技术和丰富的市场资源,对压铸市场的竞争力不容小觑。
5. 压铸市场发展趋势分析5.1 技术创新和设备升级随着科技的不断进步,压铸技术也在不断创新和改进。
新的材料和工艺的应用,使得压铸产品的质量和性能得到提升。
同时,压铸设备的自动化和智能化水平不断提高,提高了生产效率和稳定性。
5.2 轻量化和环保需求随着全球环保意识的提高,对于轻量化和环保的要求也越来越高。
压铸行业发展现状
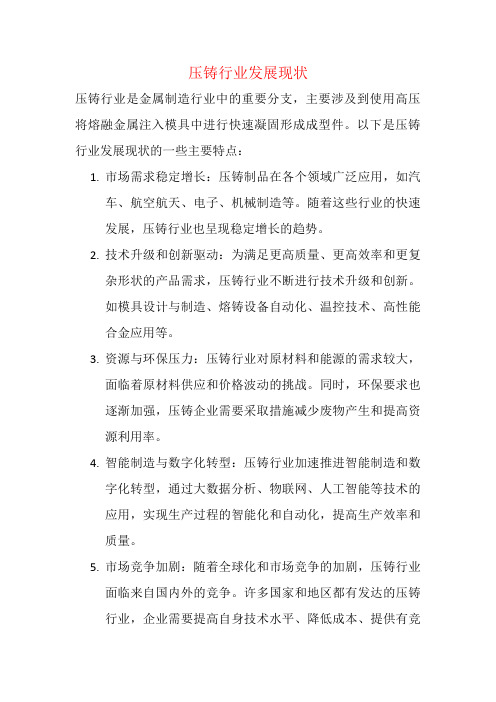
压铸行业发展现状
压铸行业是金属制造行业中的重要分支,主要涉及到使用高压将熔融金属注入模具中进行快速凝固形成成型件。
以下是压铸行业发展现状的一些主要特点:
1.市场需求稳定增长:压铸制品在各个领域广泛应用,如汽
车、航空航天、电子、机械制造等。
随着这些行业的快速发展,压铸行业也呈现稳定增长的趋势。
2.技术升级和创新驱动:为满足更高质量、更高效率和更复
杂形状的产品需求,压铸行业不断进行技术升级和创新。
如模具设计与制造、熔铸设备自动化、温控技术、高性能合金应用等。
3.资源与环保压力:压铸行业对原材料和能源的需求较大,
面临着原材料供应和价格波动的挑战。
同时,环保要求也逐渐加强,压铸企业需要采取措施减少废物产生和提高资源利用率。
4.智能制造与数字化转型:压铸行业加速推进智能制造和数
字化转型,通过大数据分析、物联网、人工智能等技术的应用,实现生产过程的智能化和自动化,提高生产效率和质量。
5.市场竞争加剧:随着全球化和市场竞争的加剧,压铸行业
面临来自国内外的竞争。
许多国家和地区都有发达的压铸行业,企业需要提高自身技术水平、降低成本、提供有竞
争力的产品和服务。
总体而言,压铸行业发展势头良好,但同时也面临一些挑战。
企业需要持续关注技术进步和市场需求变化,加强技术创新、环保和数字化转型,以保持竞争优势并实现可持续发展。
2024年压铸市场发展现状
2024年压铸市场发展现状一、引言压铸是一种高效、精确的金属成型工艺,广泛应用于汽车、电子、航空航天等工业领域。
本文将对当前压铸市场的发展现状进行分析和总结。
二、全球压铸市场概述1. 市场规模全球压铸市场在近年持续增长,市场规模不断扩大。
根据统计数据,2019年全球压铸产量达到XX万吨,产值超过XX亿美元。
2. 主要市场全球压铸市场主要集中在亚太地区、欧洲和北美地区。
中国、美国、德国、日本等国家在压铸产业方面占据较大的市场份额。
3. 市场竞争格局全球压铸市场竞争激烈,市场上存在着众多的压铸企业。
主要竞争策略包括技术创新、产品质量和价格竞争等。
优秀的企业通过提升工艺水平和研发能力获得竞争优势。
三、中国压铸市场现状1. 市场规模和发展趋势中国压铸市场近年来持续增长,市场规模不断扩大。
根据统计数据,2019年中国压铸产量达到XX万吨,产值超过XX亿元。
未来几年,中国压铸市场有望继续保持良好的增长态势。
2. 行业特点中国压铸行业具有市场规模大、企业数量众多的特点。
行业内企业规模参差不齐,大部分企业是小型和中型压铸公司,技术水平和生产设备相对较低。
一部分优秀企业通过技术升级和创新脱颖而出。
3. 发展趋势未来中国压铸市场的发展将呈现以下趋势:•技术升级和创新。
中国压铸企业将加大研发投入,提升产品质量和生产效率。
•自动化和智能化生产。
随着人工智能和机器人技术的不断发展,压铸行业也将向自动化和智能化方向发展。
•环保可持续发展。
目前,中国压铸行业面临着环保压力,未来将加强环境保护,推动可持续发展。
四、压铸行业面临的挑战虽然压铸市场发展迅速,但同时也面临一些挑战:1.价格竞争激烈。
市场上存在大量竞争对手,价格竞争压力较大。
2.需求变化不确定性。
随着市场需求的变化,压铸行业需不断调整产品结构和供应链。
3.环境压力增加。
环保法规越来越严格,对压铸行业的影响日益显著。
五、结论随着全球产业的发展和技术的进步,压铸市场持续扩大。
2024年压铸行业市场分析
2024年是中国压铸行业发展中的重要一年。
由于全球经济的不稳定和国内外市场竞争的加剧,中国压铸行业面临着许多挑战和机遇。
以下是2024年中国压铸行业的市场分析。
首先,2024年中国压铸行业市场需求疲软。
受国内外经济放缓的影响,许多行业的需求量下降,进而减少了对压铸产品的需求。
汽车行业是压铸行业的主要客户之一,然而汽车市场在2024年也面临着下滑的压力。
此外,其他行业如电子、机械和航空航天等也受到同样的影响。
这使得压铸企业面临市场需求疲软的问题,导致许多企业面临生存压力。
其次,2024年压铸行业面临着严峻的竞争形势。
中国压铸企业数量众多,竞争激烈。
其中一些大型企业具有规模效应和技术优势,能够承接大型订单并提供高质量的产品和服务。
小型企业则面临着价格竞争和技术瓶颈的挑战。
此外,国外压铸企业也进入中国市场,增加了竞争的压力。
这些竞争因素使得压铸企业必须不断提升技术水平、降低成本、提高产品质量和创新能力,以保持竞争优势。
第三,2024年中国压铸行业面临原材料成本上涨的挑战。
压铸生产过程中主要使用的原材料包括铝合金、锌合金、铸铁等。
然而,2024年全球原材料市场价格波动较大,铝和锌等主要原材料价格上涨。
这导致压铸企业的生产成本上升,进一步压缩了企业利润空间。
为了应对这一挑战,压铸企业需要积极寻找替代原材料或者与供应商进行资源整合,以降低成本并保证供应稳定。
第四,2024年中国压铸行业意识到了环境保护和可持续发展的重要性。
压铸生产过程中产生的废水和废气对环境造成了污染。
随着环保政策的不断加强,压铸企业受到了更严格的环保要求。
许多企业开始重视环境管理,加大了对环保设备和技术的投入。
同时,一些压铸企业也开始探索可持续发展的道路,通过研发和生产环保型产品来满足市场需求,并减少对环境的负面影响。
总体而言,2024年中国压铸行业面临着市场需求疲软、严峻的竞争形势、原材料成本上涨和环境保护的挑战。
面对这些挑战,压铸企业需要通过提升技术水平、降低成本、创新产品和环保管理来增强竞争力,并寻找新的市场机会。
分析国内外压铸模具发展历程及现状
分析国内外压铸模具发展历程及现状第一篇:分析国内外压铸模具发展历程及现状分析国内外压铸模具发展历程及现状中国压铸行业是一个新兴的行业,在上个世纪八十年代,中国只有几家单位有1000吨以下的压铸机,国内只能制造最大630吨压铸机,并且大部分压铸机合模机构还是全液压的,非常落后。
压铸领域仅限于个别军工或大型国营企业,压铸行业非常落后。
随着80年代末,中国摩托车行业的发展,中国陆续引进了国外的大批500至1000吨压铸机,国内首台1000吨压铸机也在90年开发成功,中国压铸行业因此得以快速发展,由此也拉动了中国压铸模具企业。
在上世纪九十年代,大部分压铸模具依赖进口,特别是台湾进口居多。
中国压铸模具企业特别是宁波北仑压铸模具企业快速发展真正开始起步应该是在九十年代末,基本上都是以摩托车配件压铸模具开始,应该说基本上都是小型压铸模具,基本上在280吨至800吨压铸机上使用的压铸模具为主,这时的压铸模具企业无论是从加工设备、检测设备等硬件,还是压铸人才都处于初始阶段,模具制造水平都相对较低。
自2000年开始,随着中国汽车行业开始发展,国内开始引进1000吨以上压铸机,国内外资企业如力劲公司等压铸机企业也开始生产1000吨以上压铸机。
这个期间企业引进的基本上在1000吨至1600吨压铸机,而模具基本上全部是随着设备一同引进,国内很少能够生产。
在经历了一轮引进后,因为国外压铸模具价格较高,个别企业为了降低成本开始寻求国内能够复制汽车配件的模具企业。
为此包括合力模具公司在内的部分较大一点的模具企业看准市场,积极应对挑战,加大了先进、大型装备的投入,购置了三坐标检测等先进检测设备,开始复制汽车配件压铸模具。
在这个过程中,企业加以吸收消化,逐步开始转型,以生产中型包括汽车手动变速箱壳体压铸模具为主,带动了模具企业快速发展,模具企业装备水平明显提高,模具制造水平以及制造能力大幅提高。
目前这类模具已基本上没有企业从国外引进。
压铸技术的发展现状与展望
压铸技术的发展现状与展望压铸技术是一种非常重要的金属加工技术,其应用范围广泛,可以制造汽车零配件、工业设备、电子设备等等。
随着人们对高品质、高精度、大型化、复杂化产品需求的不断提高,压铸技术也得到了不断的发展和改进。
下面就让我们来了解一下压铸技术的发展现状与展望。
一、发展现状1.自动化生产水平的不断提高随着现代自动化技术的不断发展和应用,压铸生产中的自动化程度也得到了大幅提升,使得压铸加工的生产效率大大提高,且质量得到了保证。
2.新材料的开发与应用压铸技术已经广泛应用于铝合金、锌合金等材料的生产中,但固态材料压铸技术等新材料的开发及应用仍在不断探索和实验中。
3.反应速度的提高压铸生产中的反应速度是影响生产效率的重要因素之一。
随着技术的不断发展和改进,反应速度也不断提高,使得生产效率更高。
二、发展趋势1.数字化设计优化数字化设计优化技术可以最大程度地减少生产成本,同时这种技术也能够提高产品的精度和质量,满足了人们对高品质和精度的需求。
2.创新的设计随着人们对产品需求的不断变化,创新的设计成为了压铸技术发展的一个重要趋势。
创新的设计除了提高产品质量,还可以在某些领域中赢得竞争优势。
3.环保型技术的应用环保型技术应用是当前的一个时代潮流,压铸技术也需要秉持环保理念,尤其是对于压铸生产中产生的废料等问题,需要在技术方面进行改进和优化。
四、总结从发展现状到发展趋势,可以看出压铸技术在不断的改进和创新中,并且逐渐朝着更精准,更智能,更环保等方向进行发展。
同时,压铸技术与许多高精尖技术紧密结合,通过数字化和智能化加工生产,将会有更广泛的应用前景。
- 1、下载文档前请自行甄别文档内容的完整性,平台不提供额外的编辑、内容补充、找答案等附加服务。
- 2、"仅部分预览"的文档,不可在线预览部分如存在完整性等问题,可反馈申请退款(可完整预览的文档不适用该条件!)。
- 3、如文档侵犯您的权益,请联系客服反馈,我们会尽快为您处理(人工客服工作时间:9:00-18:30)。
中国压铸行业发展历程及现状孙猛力劲力劲科技科技科技集团集团集团有限公司有限公司杨达康 李培杰清华大学机械工程系摘要摘要::本文从压铸机的生产、压铸产品、压铸模、压铸单元等方面介绍了我国压铸业的发展历程与现状,反映了我国正逐步从压铸大国迈向压铸强国的现状及趋势。
同时梳理了压铸机关键技术的发展脉络及里程碑事件,并对压铸机行业的发展进行了展望。
关键词关键词::压铸 压铸机 中国压铸行业前言压力铸造技术是金属加工工艺中发展较快的一种铸造方法,液态金属在高速高压作用下射入紧锁的模具型腔内,并在保压条件下结晶凝固,形成半成品或成品。
压铸作为一种高效率、少切屑的先进精密成型技术,随着19世纪20年代世界印刷工业的发展,起源于活字制造,至今不到200年。
它与传统铸造技术相比,是一种年轻的铸造技术分支,目前已应用到各行各业中。
一、我国我国压铸机生产厂家的变迁压铸机生产厂家的变迁我国的应用压铸技术以20世纪40年代中后期作为起点。
1949年前,我国仅少数几家工厂有少量进口压铸机并生产锌合金铸件。
机型主要为小型压铸机,冷压室热压室均有。
1947年,中国第一家压铸专业厂在上海弄堂里诞生。
20世纪50年代,航空、仪器仪表、汽车等工业发展迅速,促进了中国压铸业的兴起。
50到60年代,以南京为中心,许多科研工作者在压铸行业的发展中作出了卓有成效的工作。
20世纪60年代中期,上海及南京一带的压铸生产厂家在技术上有了较快发展,可生产精密、薄壁、小孔、螺丝、齿轮、花纹及镶件组合结构等复杂的压铸件。
真空压铸除南京外,在上海也开始用于生产。
此时压铸技术的水平有了提高,上海、南京、沈阳等一些地方已开始研究充氧压铸。
60年代,为适应国内压铸件生产,上海压铸机厂成为国内第一家压铸机专业生产厂,不久,压铸机的生产厂家不断涌现,相继有隆华、灌南、阜新等一批专业生产压铸机的骨干企业。
多年来,这些压铸机厂生产了大量的国产压铸机。
在大型压铸机方面,阜新压铸机厂曾生产了锁模力为28000kN 的大型压铸机,当时填补了国内的空白,但因为技术及配套设施所限,没有进行批量生产。
进入70年代,摩托车行业的发展充分带动了我国压铸业,这时,国内压铸件生产厂如雨后春笋般的涌现,发展最快的是江苏、浙江、重庆等地。
80年代,中国实行改革开放模式下的市场经济模式。
以深圳为试点的改革开放诸多举措的实施,以及港、台、日、韩等四小龙来华投资,促进了我国五金、摩托车、手表等产业的快速发展,给压铸生产企业带来了十分广阔的发展空间。
此阶段我国压铸机生产企业猛增至50余家,是计划经济时代的八倍。
其共有的特征是:以自行设计为主,仿型为辅;其已实现了批量生产,专业配套门类较全,具有独立的研发机构,开始注重自主知识产权。
其中,力劲公司是典型的代表,该公司开发了多项国内领先的压铸机机型。
近几年,国内压铸机制造厂家数量激增,约有100家,其中具有一定规模的约为有20家,多分布在沿海地区,如表一。
2001~ 2010年的压铸机年产量见表二。
图一为中国压铸机装备产业成长轨迹。
可见我国近年来压铸产业发展迅猛。
表一全国压铸机主要生产企业企业名称所在地卧式冷室压铸机锁模力/kN 热室压铸机锁模力/kN力劲集团香港、深圳、上海、宁波1300~45000 80~4000 锌合金160~4000 镁合金上海压铸机厂(上海强晟压铸机有限公司)上海1250~13500 250~1000 锌合金灌南压铸机有限公司江苏灌南630~16000 300~1000 锌合金苏州三基铸造装备股份有限公司江苏苏州1600~25000伊之密精密压铸科技有限公司广东佛山1800~30000无锡新佳盛压铸机制造有限公司江苏无锡1500~32000 380-40000锌合金宁波东方压铸机床有限公司浙江宁波250~3000 160~1800 锌合金常州华晨机械制造有限公司江苏常州1400~20000许昌意斯特精机有限公司河南许昌1600~16000 500~4000 锌合金东莞宝弘机械有限公司广东东莞1600~14000 PWHM 镁合金表二2001年~2010年我国压铸机产量年份2001200220032004200520062007200820092010数量(台)1960224025103030339039404530422046305580图一中国压铸机装备产业成长轨迹近20年中,压铸产业多元化带动了中国由压铸大国向压铸强国转变。
除江苏、浙江、上海之外,广东、重庆发展最快。
压铸厂遍及全国各地,压铸件产量从2006年起就超过100万t。
涌现出重庆渝江、重庆捷力轮毂、重庆志成、哈尔滨东安、广东鸿图、广东文灿、江苏江旭、徐州徐航等一大批压铸产值达数亿至数十亿的压铸企业。
压铸件除能满足国内需求外,还出口到国外。
2004~ 2009年各类有色合金压铸件产量见表三。
表三2004~ 2009 年各类有色合金压铸件产量类别2004年2005年2006年产量/万吨比例/% 产量/万吨比例/% 产量/万吨比例/% 铝合金56.28 72.3 63.07 73.0 80.21 78.3 锌合金20.24 26.0 21.85 25.3 20.24 19.8 镁合金0.78 1.0 0.896 1.0 1.362 1.33 铜合金0.56 0.7 0.605 0.7 0.584 0.57 合计77.86 100 86.421 100 102.396 1002007年2008年 2009年 类别 产量/万吨比例/% 产量/万吨 比例/% 产量/万吨 比例/% 铝合金96.32 81.0 105.9 81.3 126.8 85.16 锌合金20.12 16.9 21.6 16.6 18.0 12.2 镁合金1.826 1.552.064 1.6 2.4 1.6 铜合金0.624 0.55 0.646 0.5 0.8 0.5 合计 118.89 100 130.21 100 148 99.46二、我国我国压铸机吨位压铸机吨位压铸机吨位及相应技术及相应技术及相应技术现况与发展现况与发展2.1压铸机吨位发展20世纪40年代我国压铸机处于刚刚起步的时期。
1949年前,我国仅有少数几家工厂有几台进口压铸机生产锌合金铸件,其中有英国的小型气动热室压铸机(上海)、美国KUX 锁模力1000kN 的卧式冷室压铸机(重庆)和捷克Polak600型(锁模力6000kN )立式冷室压铸机(昆明)等。
20世纪50年代末期,随着压铸业的发展,我国开始自行设计与制造卧式冷室压铸机,同时也仿制了立式冷室压铸机(如国营金城机械厂设计制造了1150kN 卧式冷室压铸机、长春机电研究所成功研制500kN 、1500kN 两种型号压铸机等)。
同时,我国成批进口了捷克的Polak 立式冷室压铸机,最大的锁模力为2200kN ;前苏联卧式冷室压铸机,合模为曲肘式,共3种规格,最大的锁模力为5300kN 。
到了20世纪60年代初,我国开始自行制造立式冷室压铸机及卧式冷室压铸机,即900型(锁模力为l150kN )和J1113型(锁模力1250kN )。
1960年,国营金城机械厂设计了6300kN 卧式冷室压铸机,并制作了机体等木模,后转给上海制造。
60年代,中国压铸件生产主要用2500kN 以下的压铸机。
70年代,为适应压铸件生产的发展,在压铸机方面,国家组织了以济南铸锻机械研究所为主,上海工艺研究所和上海压铸机厂参加,联合进行了相关技术工作:编制压铸机型谱草案,规范了我国压铸机系列的主要技术参数;设计和试制了J1125、J1140和J1163型全液压卧式冷室压铸机;设计制造了1台锁模力40000kN 全液压卧式冷室压铸机(上海锻压机床厂制造);生产了第一台热室压铸机和第一台自动浇料装置;完成了锁模力16000kN 以下的卧式冷室压铸机系列产品的开发;立式冷室压铸机也形成了锁模力2500kN 以下的系列产品;1986年试制出国内第一台J1163A 型自动压铸机组。
80年代,我国设计制造压铸机的压射性能已接近国际水平,合模机构采用液压驱动、曲肘扩力结构取代了全液压式。
而热室压铸机在当时也形成了锁模力1500kN以下的系列化产品,全立式压铸机也有了锁模力3150kN以下的系列化产品。
90年代以来,为适应压铸件生产的要求,我国的压铸机发展更为迅速,压铸机的设计水平、技术参数、性能指标、机械结构、制造质量等都有不同程度的提高,某些指标已经达到或接近国际水平,正在向大型化、自动化和单元化进军。
目前,中国压铸机年产量约5600台,其中冷室机3300台左右,热室机2300台左右,制造能力居世界第一。
其中,力劲公司是典型的代表。
该公司开发了多项国内领先的压铸机机型,例如:卧式冷室压铸机最大空压射速6m/s(1997年)和8m/s(2000年初)、镁合金热室压铸机(2000年初)、匀加速压射系统(2002年)、最大空压射速10m/s及多段压射系统(2004年6月)、实时控制压射系统(2004年8月)、锁模力30000kN的大型压铸机(2004年7月)、锁模力40000kN 的卧式冷室大型压铸机(2010年)等。
力劲公司还开发研制了国内第一台镁合金热室及冷室压铸机,填补了国内的空白。
近年来,苏州三基、广东伊之密、无锡新佳盛、灌南压铸机等压铸企业也生产了26000kN以上的大型压铸机。
由此可见,我国正在形成一个有实力、具有自主知识产权的压铸机制造业。
表四为我国卧式压铸机研制生产能力变化。
表五为国外卧式压铸机发展情况。
表四我国卧式压铸机研制生产能力变化表时间1958 1963 1978 1993 1996 1999 2002 2006 2008 2010 吨位30 80 160 280 400 800 1600 2000 3000 4000 等级普通普通普通普通高精度高精度高精度高精度高精度高精度表五国外卧式压铸机发展情况时间1950~19591960~19691970至今吨位800~1400 2000~3000 5000程度普通高精度精密级我国现有压铸机中,从数量上,10000kN及以上压铸机占2%,8000~9000kN 压铸机占5%,5000~7000kN压铸机占13%,3500~4000kN压铸机占20%,3000kN及以下压铸机占60%。
在3000kN以下的压铸机中,热室压铸机约占30%。
中小型压铸机仍以国产设各为主,大型、超大型、精密型压铸机和镁合金压铸机国外品牌占有较大比重,如图二所示。
值数亿元,用于生产汽车发动机缸体;2005~2008年间,日本汽车制造商丰田公司、本田公司均采用中国压铸装备生产其汽车关键零部件,同时,出口到多个国家;2007~2010年富士康、比亚迪大批量购进国内超大型压铸生产单元;2008年,DCC2500、DCC3000卧式冷室压铸机和DCC3000卧式冷室镁合金压铸机获得“深圳市自主创新产品”奖;2009年,3500吨压铸成套装备列入国家重大科技攻关项目。