塑料挤出成型
挤出成型工艺—挤出成型原理(塑料成型加工课件)
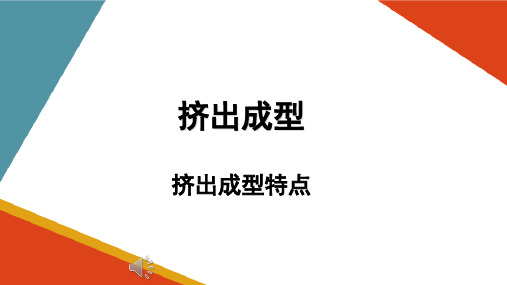
二、挤出成型过程
既有混合过 程,也有成 型过程
树脂原料 加热黏流 塑料熔体
助剂
混合过程
加压 挤出连续体
一定规格的 制品
切割 成型连续体
冷却定型
成型过程
以 管 材 挤 出 原料 成型为例
挤出连续体
熔体
定型连续体
制品
三、挤出成型特点
1. 可以连续化生产,生产效率高。 2. 设备自动化程度高,劳动强度低。 3. 生产操作简单,工艺控制容易。 4. 原料适应性强,适用大多数热塑性树脂和少数热固性 树脂。 5. 可生产的产品广泛,同一台挤出机,只要更换不同的 辅机,就可以生产不同的制品。
挤出成型
挤出成型特点
一、挤出成概述
挤出成型又叫挤出模塑,是利用加热使塑料熔融塑化成 为流动状态,然后在机械力(螺杆或柱塞的挤压)的作用下, 使熔融塑料通过一定形状的口模制成具有恒定截面连续的制 品,适用于绝大部分热塑性树脂和部分热固性树脂。
除了用于挤出造粒、染色、树脂掺和等共混改性,还可用于塑 料薄膜、网材、带包覆层的产品、截面一定、长度连续的管材、板 材、片材、棒材、打包带、单丝和异型材等塑料制品的生产。
料表面接近或达到黏流温度,表面发黏。
要求:输送能力要稍高于熔融段和均化段。
2. 压缩段 (熔融段)
位置:螺杆中部一段。 作用:输送物料,使物料受到热和剪切作用熔 融塑化,并进一步压实和排出气体。 特点:物料逐渐由玻璃态转变为粘流态,在熔 融段末端物料为粘流态。 要求:螺杆结构逐渐紧密,使物料进一步压实。
(3)横流(环流) 由垂直于螺棱方向的分速
度引起的使物料在螺槽内产生翻 转运动。对生产能力没有影响, 但能促进物料的混合和热交换。
(4)漏流 由机筒与螺棱间隙处形成的
挤出成型法名词解释

挤出成型法名词解释
挤出成型法是一种常见的塑料加工方法,也被称为挤塑或挤压成型。
它是利用
挤出机将熔化的塑料物料通过模具挤出,使其成型为所需的截面形状。
这种方法在塑料加工领域应用广泛,可以生产出各种形状复杂的塑料制品,如管材、板材、型材等。
挤出成型法的工作原理是通过将塑料颗粒或粉末加热熔化,然后将熔化的塑料
物料送入挤出机的螺杆筒内。
在螺杆的旋转作用下,熔化的塑料物料被压缩、混合、加热,最终在机筒出口处通过模具挤出,形成所需的截面形状。
挤出机通常由进料装置、加热装置、螺杆和机筒、模具、冷却装置等部件组成。
挤出成型法具有生产效率高、成型精度高、生产成本低等优点。
它适用于生产
各种截面形状的塑料制品,且可以通过更换模具实现生产不同形状和尺寸的产品。
此外,挤出成型法生产的制品表面光滑、一致性好,可以满足各种工业和民用领域的需求。
在挤出成型法中,塑料的选择、挤出机的参数调节、模具设计等因素都会影响
成型制品的质量和性能。
因此,在实际生产中,需要根据具体的产品要求和生产条件,合理选择塑料材料、挤出机型号和参数,设计合理的模具,确保生产出符合要求的塑料制品。
总的来说,挤出成型法是一种常用的塑料加工方法,具有广泛的应用前景。
通
过不断的技术改进和创新,挤出成型法将能够更好地满足不同行业的生产需求,为塑料制品的生产和应用提供更加便捷、高效的解决方案。
挤出成型和注塑成型的区别和联系
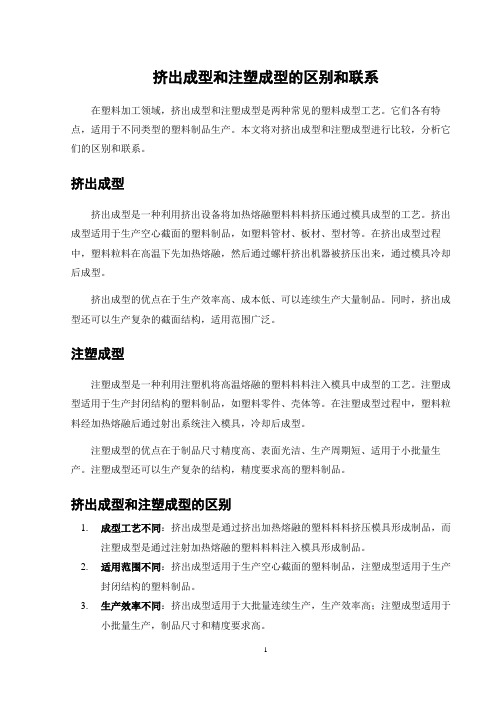
挤出成型和注塑成型的区别和联系在塑料加工领域,挤出成型和注塑成型是两种常见的塑料成型工艺。
它们各有特点,适用于不同类型的塑料制品生产。
本文将对挤出成型和注塑成型进行比较,分析它们的区别和联系。
挤出成型挤出成型是一种利用挤出设备将加热熔融塑料料料挤压通过模具成型的工艺。
挤出成型适用于生产空心截面的塑料制品,如塑料管材、板材、型材等。
在挤出成型过程中,塑料粒料在高温下先加热熔融,然后通过螺杆挤出机器被挤压出来,通过模具冷却后成型。
挤出成型的优点在于生产效率高、成本低、可以连续生产大量制品。
同时,挤出成型还可以生产复杂的截面结构,适用范围广泛。
注塑成型注塑成型是一种利用注塑机将高温熔融的塑料料料注入模具中成型的工艺。
注塑成型适用于生产封闭结构的塑料制品,如塑料零件、壳体等。
在注塑成型过程中,塑料粒料经加热熔融后通过射出系统注入模具,冷却后成型。
注塑成型的优点在于制品尺寸精度高、表面光洁、生产周期短、适用于小批量生产。
注塑成型还可以生产复杂的结构,精度要求高的塑料制品。
挤出成型和注塑成型的区别1.成型工艺不同:挤出成型是通过挤出加热熔融的塑料料料挤压模具形成制品,而注塑成型是通过注射加热熔融的塑料料料注入模具形成制品。
2.适用范围不同:挤出成型适用于生产空心截面的塑料制品,注塑成型适用于生产封闭结构的塑料制品。
3.生产效率不同:挤出成型适用于大批量连续生产,生产效率高;注塑成型适用于小批量生产,制品尺寸和精度要求高。
4.产品特点不同:挤出成型制品常为长条状或截面类,注塑成型制品常为封闭塑件或精密器件。
挤出成型和注塑成型的联系尽管挤出成型和注塑成型有着明显的区别,但它们也有一些联系点:1.塑料材料相同:挤出成型和注塑成型都是利用熔融后的塑料原料进行成型,所使用的塑料材料可能是相同的。
2.后处理工艺相似:挤出成型和注塑成型在成型后都需要进行一定的后处理工艺,如切割、去毛刺、打磨等,以满足制品的质量要求。
3.在某些制品上可互相替代:在一些特定情况下,挤出成型和注塑成型也可以相互替代,根据制品的形状、尺寸和数量来选择合适的生产工艺。
塑料制品的挤出成型培训教程
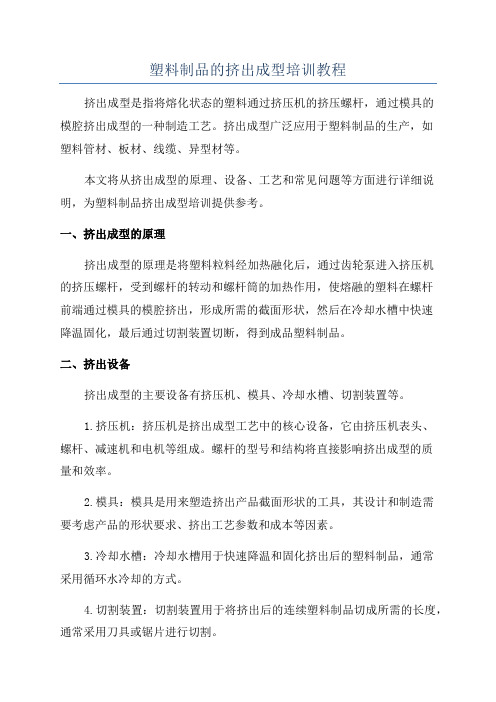
塑料制品的挤出成型培训教程挤出成型是指将熔化状态的塑料通过挤压机的挤压螺杆,通过模具的模腔挤出成型的一种制造工艺。
挤出成型广泛应用于塑料制品的生产,如塑料管材、板材、线缆、异型材等。
本文将从挤出成型的原理、设备、工艺和常见问题等方面进行详细说明,为塑料制品挤出成型培训提供参考。
一、挤出成型的原理挤出成型的原理是将塑料粒料经加热融化后,通过齿轮泵进入挤压机的挤压螺杆,受到螺杆的转动和螺杆筒的加热作用,使熔融的塑料在螺杆前端通过模具的模腔挤出,形成所需的截面形状,然后在冷却水槽中快速降温固化,最后通过切割装置切断,得到成品塑料制品。
二、挤出设备挤出成型的主要设备有挤压机、模具、冷却水槽、切割装置等。
1.挤压机:挤压机是挤出成型工艺中的核心设备,它由挤压机表头、螺杆、减速机和电机等组成。
螺杆的型号和结构将直接影响挤出成型的质量和效率。
2.模具:模具是用来塑造挤出产品截面形状的工具,其设计和制造需要考虑产品的形状要求、挤出工艺参数和成本等因素。
3.冷却水槽:冷却水槽用于快速降温和固化挤出后的塑料制品,通常采用循环水冷却的方式。
4.切割装置:切割装置用于将挤出后的连续塑料制品切成所需的长度,通常采用刀具或锯片进行切割。
三、挤出工艺流程挤出成型的工艺流程主要包括原料准备、挤出机操作、模具安装、温度调整、启动挤出机、过程监控和成品收集等步骤。
1.原料准备:根据产品要求,准备好所需的塑料粒料,并按照一定的比例混配拌和。
2.挤出机操作:将准备好的塑料粒料倒入挤压机的料斗中,启动挤压机,使螺杆开始转动,进料和挤压。
3.模具安装:将模具安装在挤压机的模具支架上,并根据产品要求调整模具的位置和间隙。
4.温度调整:根据塑料材料的熔点和工艺要求,调整挤压机的温度控制器,使熔融的塑料达到适宜的挤出温度。
5.启动挤出机:当挤压机和模具都调整好后,可以开始启动挤出机进行挤出成型。
6.过程监控:在挤出过程中,需要不断检查和调整挤压机的工作状态、模具的温度和位置等参数,确保挤出产品的质量。
塑料挤出成型技术
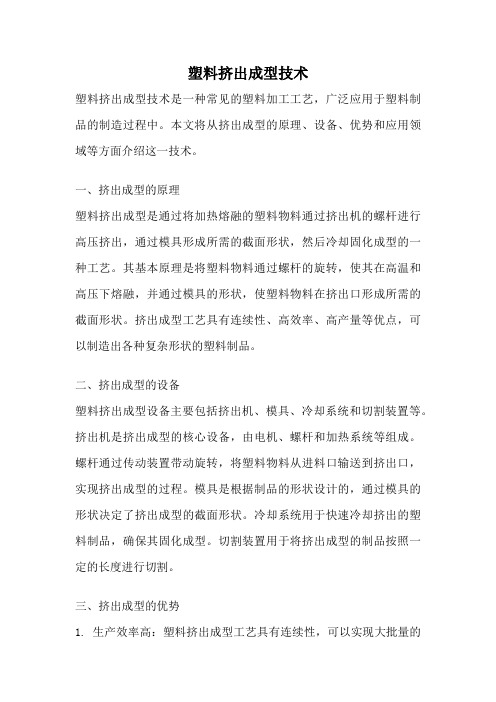
塑料挤出成型技术塑料挤出成型技术是一种常见的塑料加工工艺,广泛应用于塑料制品的制造过程中。
本文将从挤出成型的原理、设备、优势和应用领域等方面介绍这一技术。
一、挤出成型的原理塑料挤出成型是通过将加热熔融的塑料物料通过挤出机的螺杆进行高压挤出,通过模具形成所需的截面形状,然后冷却固化成型的一种工艺。
其基本原理是将塑料物料通过螺杆的旋转,使其在高温和高压下熔融,并通过模具的形状,使塑料物料在挤出口形成所需的截面形状。
挤出成型工艺具有连续性、高效率、高产量等优点,可以制造出各种复杂形状的塑料制品。
二、挤出成型的设备塑料挤出成型设备主要包括挤出机、模具、冷却系统和切割装置等。
挤出机是挤出成型的核心设备,由电机、螺杆和加热系统等组成。
螺杆通过传动装置带动旋转,将塑料物料从进料口输送到挤出口,实现挤出成型的过程。
模具是根据制品的形状设计的,通过模具的形状决定了挤出成型的截面形状。
冷却系统用于快速冷却挤出的塑料制品,确保其固化成型。
切割装置用于将挤出成型的制品按照一定的长度进行切割。
三、挤出成型的优势1. 生产效率高:塑料挤出成型工艺具有连续性,可以实现大批量的生产,提高生产效率。
2. 制品质量稳定:挤出成型的制品形状稳定,尺寸精确,质量可靠。
3. 适用范围广:挤出成型工艺适用于各种塑料,可以制造出各种形状的制品,如管材、板材、型材等。
4. 设备投资少:相对于其他塑料加工工艺,挤出成型设备投资较少,生产成本较低。
5. 可塑性强:挤出成型的塑料物料可根据需要选择,可以加入各种填充剂、增强剂等,增加塑料的性能。
四、挤出成型的应用领域塑料挤出成型技术广泛应用于建筑、包装、汽车、电子、家电等行业。
在建筑行业中,挤出成型制造的塑料管材、型材、板材等被广泛应用于室内装饰、给排水系统、电线电缆等方面。
在包装行业中,挤出成型用于制造各种塑料包装盒、瓶子、袋子等。
在汽车行业中,挤出成型的塑料制品用于汽车内饰、外饰等部件。
在电子和家电行业中,挤出成型的塑料制品用于电线电缆的保护管、电器外壳等。
挤出成型的原理和工艺流程
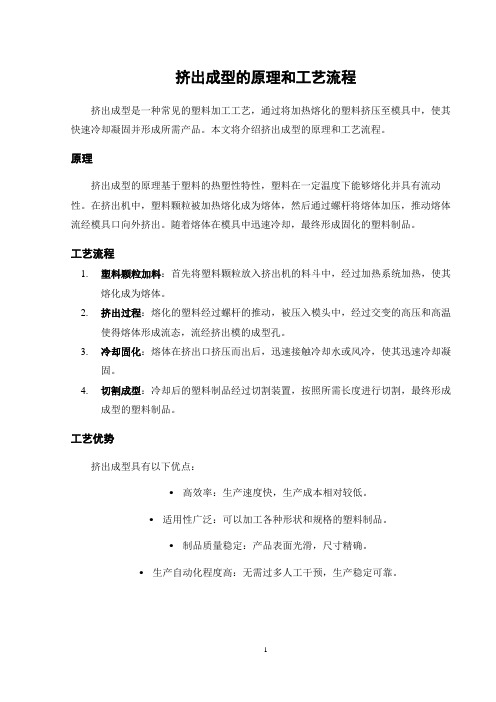
挤出成型的原理和工艺流程
挤出成型是一种常见的塑料加工工艺,通过将加热熔化的塑料挤压至模具中,使其快速冷却凝固并形成所需产品。
本文将介绍挤出成型的原理和工艺流程。
原理
挤出成型的原理基于塑料的热塑性特性,塑料在一定温度下能够熔化并具有流动性。
在挤出机中,塑料颗粒被加热熔化成为熔体,然后通过螺杆将熔体加压,推动熔体流经模具口向外挤出。
随着熔体在模具中迅速冷却,最终形成固化的塑料制品。
工艺流程
1.塑料颗粒加料:首先将塑料颗粒放入挤出机的料斗中,经过加热系统加热,使其
熔化成为熔体。
2.挤出过程:熔化的塑料经过螺杆的推动,被压入模头中,经过交变的高压和高温
使得熔体形成流态,流经挤出模的成型孔。
3.冷却固化:熔体在挤出口挤压而出后,迅速接触冷却水或风冷,使其迅速冷却凝
固。
4.切割成型:冷却后的塑料制品经过切割装置,按照所需长度进行切割,最终形成
成型的塑料制品。
工艺优势
挤出成型具有以下优点:
•高效率:生产速度快,生产成本相对较低。
•适用性广泛:可以加工各种形状和规格的塑料制品。
•制品质量稳定:产品表面光滑,尺寸精确。
•生产自动化程度高:无需过多人工干预,生产稳定可靠。
应用领域
挤出成型广泛应用于塑料制品生产行业,如管道、板材、型材、薄膜、包装材料等领域。
其高效率、高质量的特点使其成为塑料制品生产中不可或缺的一环。
总的来说,挤出成型作为一种常见的塑料加工工艺,通过简单高效的操作流程,可以生产出质量稳定的塑料制品,在工业生产中发挥着重要作用。
塑料挤出成型技术
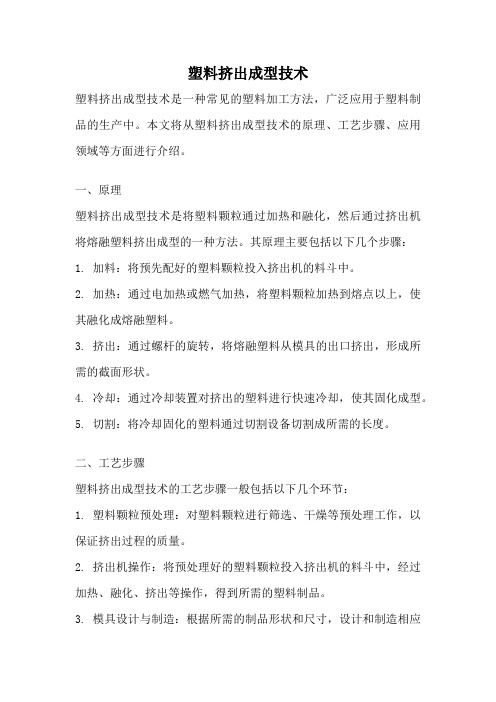
塑料挤出成型技术塑料挤出成型技术是一种常见的塑料加工方法,广泛应用于塑料制品的生产中。
本文将从塑料挤出成型技术的原理、工艺步骤、应用领域等方面进行介绍。
一、原理塑料挤出成型技术是将塑料颗粒通过加热和融化,然后通过挤出机将熔融塑料挤出成型的一种方法。
其原理主要包括以下几个步骤:1. 加料:将预先配好的塑料颗粒投入挤出机的料斗中。
2. 加热:通过电加热或燃气加热,将塑料颗粒加热到熔点以上,使其融化成熔融塑料。
3. 挤出:通过螺杆的旋转,将熔融塑料从模具的出口挤出,形成所需的截面形状。
4. 冷却:通过冷却装置对挤出的塑料进行快速冷却,使其固化成型。
5. 切割:将冷却固化的塑料通过切割设备切割成所需的长度。
二、工艺步骤塑料挤出成型技术的工艺步骤一般包括以下几个环节:1. 塑料颗粒预处理:对塑料颗粒进行筛选、干燥等预处理工作,以保证挤出过程的质量。
2. 挤出机操作:将预处理好的塑料颗粒投入挤出机的料斗中,经过加热、融化、挤出等操作,得到所需的塑料制品。
3. 模具设计与制造:根据所需的制品形状和尺寸,设计和制造相应的模具。
4. 挤出成型:将熔融塑料从模具的出口挤出,形成所需的截面形状。
5. 冷却与固化:通过冷却装置对挤出的塑料进行快速冷却,使其固化成型。
6. 切割与包装:将冷却固化的塑料通过切割设备切割成所需的长度,并进行包装。
三、应用领域塑料挤出成型技术广泛应用于各个领域的塑料制品生产中,例如:1. 建筑行业:生产塑料管道、塑料板材、塑料薄膜等建筑材料。
2. 包装行业:生产塑料袋、塑料瓶、塑料容器等包装制品。
3. 汽车行业:生产汽车零部件,如塑料车门、塑料仪表盘等。
4. 家电行业:生产电视机外壳、冰箱内胆等家电配件。
5. 日用品行业:生产塑料梳子、塑料杯子、塑料衣架等日用品。
总结:塑料挤出成型技术是一种常见的塑料加工方法,通过加热和融化塑料颗粒,然后通过挤出机将熔融塑料挤出成型。
该技术具有工艺简单、生产效率高、适用范围广等优点,被广泛应用于各个领域的塑料制品生产中。
塑料挤出成型工艺及模具设计教学

其他质量问题的原因与解决方案
06
塑料挤出成型工艺实例分析
管材挤出成型工艺主要包括原料准备、模具设计、挤出成型、冷却定型和牵引切割等步骤。
工艺流程
关键技术
应用领域
管材挤出成型的关键技术包括温度控制、压力调节、模具设计和材料选择等。
管材挤出成型广泛应用于建筑、给排水、农业灌溉等领域。
塑料挤出成型工艺及模具设计教学
目录
contents
挤出成型工艺简介 塑料挤出成型设备 塑料挤出成型模具设计 塑料挤出成型工艺参数控制 塑料挤出成型质量问题及解决方案 塑料挤出成型工艺实例分析
01
挤出成型工艺简介
挤出成型工艺是一种塑料加工技术,通过螺杆旋转加压,使塑料从挤出机机筒中连续挤出,经过模具定型后形成所需的制品形状和尺寸。
详细描述
04
塑料挤出成型工艺参数控制
温度参数控制是塑料挤出成型工艺中的重要环节,它直接影响着产品的质量和生产效率。
温度参数控制包括机筒温度、模具温度和塑料温度的控制。机筒温度的设置要根据塑料的特性和工艺要求来确定,以保证塑料在机筒内能够充分塑化。模具温度则影响着塑料的流动和成型,其设定要根据产品的大小、形状和材料特性来决定。塑料温度的控制也十分重要,合适的塑料温度可以保证塑料在挤出过程中保持稳定的流动状态。
常见的冷却定型设备包括冷却水槽、冷却隧道等。
这些设备通常配有强力的风扇,以加速冷却过程。
其他辅助设备
除了上述主要设备外,挤出成型工艺还需要其他辅助设备,如切粒机、振动筛、上料机等。
这些设备在生产过程中起到各自的作用,如切粒机用于将挤出的塑料切成一定长度的小颗粒,振动筛则用于筛选出不合格的塑料颗粒。
- 1、下载文档前请自行甄别文档内容的完整性,平台不提供额外的编辑、内容补充、找答案等附加服务。
- 2、"仅部分预览"的文档,不可在线预览部分如存在完整性等问题,可反馈申请退款(可完整预览的文档不适用该条件!)。
- 3、如文档侵犯您的权益,请联系客服反馈,我们会尽快为您处理(人工客服工作时间:9:00-18:30)。
总结
低密度聚乙烯吹膜过程中应注意的地方
总结
高密度聚乙烯膜成型工艺特点
与低密度聚乙烯和线性低密度聚乙烯吹塑薄膜相同,高密度聚乙烯薄膜 采取平挤上吹法成型,但膜泡的形状与低密度聚乙烯、线性低密度聚乙烯的 形状截然不同。图4-31表现了高密度聚乙烯的膜泡形状和冷却定型装置。由 此,我们可以看出,薄膜的吹胀发生在离开口模一段距离之后,膜泡的下部 是一段细长的管状,其长度约为口模直径的5~8倍。这是由高密度聚乙烯 的熔体特性和拉伸比决定的。实际上,这种泡形产生的结果相当于在工艺上 是先成型出一段管,再在一定的温度下对其进行双向拉伸的过程,因此,取 向效果显著,薄膜获得高强度。薄膜的吹胀比是4~6,拉伸比是3~7。
塑料挤出成型
2020年5月27日星期三
认识
认识
这三种吹塑方法应该用那种呢?
认识
认识
这些机头有什么特点呢?
项目8:匹配挤出机及模具,生产薄膜 ——主要训练过程
• 任务8-1: • 制定成型工艺 • • 任务8-2:
匹配挤出机及模具,启动生产线生产薄膜
今天的任务: 任务8-2
1.任务告知:
• 拟实现的能力目标:
总结
低密度聚乙烯和线性低密度聚乙烯吹塑薄膜工艺及设备 折径为300mm以上的普通低密度聚乙烯膜采用平挤上吹法成型。螺杆直径为
40~200mm;螺杆长径比为20~30。螺杆挤出速度不超过最大线速度0.8~ 1.2m/s。表4-6列出吹膜挤出机规格与产量、功率的关系。
机头多采用螺旋式机头或支架式机头,口模直径100~1000mm。风环采用 堤坝式铸铝风环,鼓风机压力为4000~8000Pa,流量为15~75m3/min。
薄膜从机头挤出吹胀后,立即进行冷却,若冷却效果不好,则薄膜发粘而无法 引膜。为提高产量,有采用双风环冷却的办法,而较为先进的冷却方法是内冷法。 通过改变内部气流进行内部冷却对薄膜质量有着重要的改善。
总结
• 高密度聚乙烯膜
由于高密度聚乙烯分子链较为规整,结晶度高,造成了高密度 聚乙烯生产的吹塑薄膜在力学性能、耐热性和阻隔性方面与低 密度聚乙烯薄膜的不同,见表4-7。 高密度聚乙烯可以生产包装薄膜、包装袋和购物提袋,其透明 性较低密度聚乙烯低,比低密度聚乙烯硬、挺。
9.你们知道流延膜吗?流延和吹膜法有哪些不同 ?
3.任务的实施
• 教学工厂-》图书馆:
选择匹配的挤出机和 模具
3.任务的实施
• 图书馆->上网查看挤出机操作 注意事项;
• 教学工厂->分组操作,启动挤 出机生产薄膜
ቤተ መጻሕፍቲ ባይዱ
3.任务的实施
挤出机的匹配和模具的选择是否合理呢? 你在生产中遇到了什么问题?如何解决的?
低密度聚乙烯吹膜挤出机和机头的温度控制是薄膜生产中的关键,它直接影响 产品质量,应使物料熔融充分,熔体粘度均匀一致,且粘度适当。可控制为机身从 料斗向机头方向的第一段为140~150℃,第二段为170~180℃,第三段为180~ 190℃,机头温度180℃左右。
低密度聚乙烯和线性低密度聚乙烯吹膜工艺中,熔融物料从机头口模被挤出后 形成管坯,立即吹胀而被横向拉伸,同时在牵引辊的作用下被纵向拉伸,因此分子 链在纵横向发生取向,取向程度对薄膜强度有显著影响,取向度大,强度高。为了 使薄膜纵横向强度均等,应使吹胀比与拉伸比相同,但实际生产中为扩大机头的适 用范围,通过调节吹胀比与牵伸比使同一规格的机头在一定范围内吹制不同折径、 不同厚度的薄膜。吹胀比通常控制在1.5~3,拉伸比控制在3~7。
3.任务的实施
制造出来的薄膜是否符合要求呢?如何判 别呢?
4.任务深化
• 怎样确定拉伸比和吹胀比? ?
5.归纳总结
• 生产线认识辨别能力; • 生产线配置选型能力; • 生产线开车、维护、调节能力; • 生产线故障排除能力; • 方法能力; • 社会能力;
6.拓展
• 改善薄膜厚度的方式有哪些? • 旋转模头与旋转牵引的区别? • 怎样提高薄膜的透明性 ?
生产线认识辨别能力; 生产线配置选型能力; 生产线开车、维护、调节能力; 生产线故障排除能力; 方法能力; 社会能力;
2.任务的引入
引导课文:
1.挤出吹塑薄膜加工工艺参数设定的依据是什么?如何进行 设定 ?
2.挤出吹塑薄膜生产线的开机操作步骤是什么 ? 3.挤出吹塑薄膜生产线开机前有哪些准备工作 ? 4.挤出吹塑薄膜生产线的开机过程中,在设备运转中要注意
7.作业布置
• 查阅资料:吹膜工艺中设备要求和挤出机 操作技巧。
布置学生整理粘贴板,写总结报 告
end
总结
低密度聚乙烯膜
用于吹塑薄膜生产的乙烯类聚合物和共聚物有很多种,低密度聚乙烯膜和 线性低密度聚乙烯均为其中重要的树脂品种。低密度聚乙烯有较好的力学 性能、光学性能、热封合性能等,选择适当牌号的低密度聚乙烯对吹膜加 工有很好的适应性,操作容易。线性低密度聚乙烯的分子量分布窄,平均 分子量较大,加工流动性不如低密度聚乙烯,但拉伸强度、伸长率、耐穿 刺性、耐撕裂性等都优于低密度聚乙烯。线性低密度聚乙烯可以单独吹膜 ,但需对有关设备进行改进,才能满足吹塑成型要求。因此,线性低密度 聚乙烯常以共混组分的形式在吹膜工艺中出现,线性低密度聚乙烯的加入 ,可以有效地提高低密度聚乙烯薄膜的强度和韧性。 LDPE主要用于制造农用膜、地膜,另外少部分用于各种轻、重包装膜, 如食品袋、货物袋、工业重包装袋、复合薄膜或编织内衬、涂层、各种管 材、电线绝缘层等。
哪些问题 ?
2.任务的引入
• 引导课文:
5.挤出吹塑薄膜过程中,如发现薄膜制品卷取不平 ,请分析产生原因及解决办法 ?
6.挤出吹塑薄膜过程中,薄膜制品有“鱼眼”现象指的 是什么?如何造成的 ?
7.挤出吹塑薄膜过程中,如发现薄膜厚度不均,请 分析产生原因并给出相应解决办法?什么是延伸 率、收缩率?
8.挤出吹塑薄膜成型中最容易出现的质量问题有哪 些?如何解决?比如横向厚度不均匀、薄膜皱折 、表面发花白点等?横向、纵向条纹?