刀具参数和切削用量选择
第9章刀具合理几何参数的选择及切削用量优化

刀具合理几何参数和切削用量的选择是否合理对刀具使用寿命、加工质量、生产效率和加工成本等有着重要影响。
刀具的“合理”的几何参数是指在保证加工质量的前提下能够获得最高刀具耐用度达到提高切削效率或降低生产成本目的的几何参数。
第一节概述什么是刀具的合理或最佳几何参数呢在保证加工质量的前提下能够满足生产效率高、加工成本低的刀具几何参数称为刀具的合理几何参数。
一般地说刀具的合理几何参数包含以下四个方面基本内容1 刃形刃形是指切削刃的形状有直线刃、折线刃、圆弧刃、月牙弧刃、波形刃、阶梯刃及其他适宜的空间曲线刃等。
刃形直接影响切削层的形状影响切削图形的合理性刃形的变化将带来切削刃各点工作角度的变化。
因此选择合理的刃形对于提高刀具使用寿命、改善已加工表面质量、提高刀具的抗振性和改变切屑形态等都有直接的意义。
2 切削刃刃区的剖面型式及参数通常将切削刃的剖面型式简称为刃区型式。
针对不同的加工条件和技术要求选择合理的刃区型式如锋刃、后刀面消振棱刃、前刀面负倒棱刃、倒圆刃、零度后角的刃带及其合理的参数值是选择刀具合理几何参数的基本内容。
图所示为五种刃区型式。
图常见的五种刃区形式a锋刃b消振棱c-负倒棱d-倒圆刃e刃带3 刀面型式及参数前刀面上的卷屑槽、断屑槽后刀面的双重刃磨、铲背以及波形刀面等都是常见的刀面型式。
选择合理的刀面型式及其参数值对切屑的变形、卷曲和折断对切削力、切削热、刀具磨损及使用寿命有着直接的影响其中前刀面的影响和作用更大。
4 刀具角度刀具角度包括主切削刃的前角γ0、后角а0、主偏角κr、刃倾角λs和副切削刃的副后角а??0、副偏角κ??r等。
刀具合理几何参数的选择主要决定于工件材料、刀具材料、刀具类型及其他具体工艺条件如切削用量、工艺系统刚性及机床功率等。
当确定了刀具几何参数后还需选定合理的切削用量才能进行切削加工。
在机床、刀具和工件等条件一定的情况下切削用量的选择最富有灵活性和能动性。
对于充分发挥机床和刀具的功能以取得生产的最大效益来说切削用量的选择如果得当就可能最大限度地挖掘出生产潜力倘若选择不当会造成很大的浪费或导致生产事故。
刀具几何参数和切削用量的合理选择

加工条件:工艺系统刚性差时,易出现振
动,应选取较小的后角αo;加工表面质量要求 较高时,为减轻刀具与工件之间的摩擦,应选
取较大的后角αo;尺寸精度要求较高时,应选 取较小的后角αo,以减小刀具的径向磨损值NB 值,如下图所示。
硬质合金车刀合理后角的参考值如下表所示。
② 后角αo的选择
切削厚度hD:粗加工时,切削厚度hD较大,要 求切削刃坚固,应选取较小的后角αo。精加工时, 切削厚度hD较小,磨损主要发生在后刀面上,为降 低磨损,应选取较大的后角αo。
工件材料:工件材料强度和硬度较高时,为提
高切削刃强度,应选取较小的后角αo;工件材料软、 塑性大时,后刀面磨损严重,应选取较大的后角αo; 工件材料脆性较大时,载荷集中在切削刃处,为提
负前角双面型:该形式的刀具使刀具的重磨次数 增加,最大程度地减少了前刀面和后刀面的磨损。同 时负前角的倒棱应有足够的宽度,以确保切屑沿该棱 面流出。
(3)倒棱
倒棱是增强切削刃强度的一种措施。在用脆性大 的刀具材料粗加工或断续切削时,磨倒棱能够减小刀 具崩刃,显著提高刀具耐用度(可提高1~5倍)。
倒棱宽度br1不可太大,以便切屑能沿前刀面 流出。br1的取值与进给量f有关,常取br1≈ (0.3~0.8)f。其中,精加工时取小值,粗加工
② 前角γo的选择
工件材料:工件材料的强度、硬度较低,塑
性较好时,应选取较大的前角γo;工件材料脆性较 大时应选取较小的前角γo;工件材料强度、硬度较 高时,应选取较小的前角γo,甚至负前角。
刀具材料:刀具材料的强度和韧度高时,如高 速钢,可选取较大的前角γo;反之,刀具材料的强度 和韧度差时,如硬质合金,应选取较小的前角γo。
数控车削中切削用量的选择
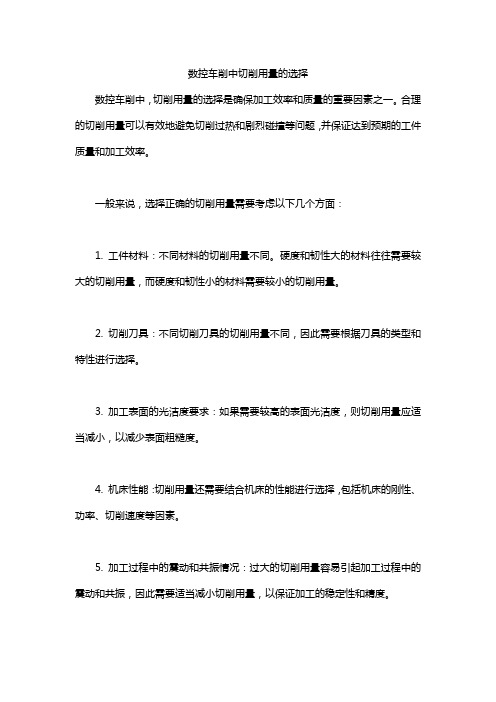
数控车削中切削用量的选择
数控车削中,切削用量的选择是确保加工效率和质量的重要因素之一。
合理的切削用量可以有效地避免切削过热和剧烈碰撞等问题,并保证达到预期的工件质量和加工效率。
一般来说,选择正确的切削用量需要考虑以下几个方面:
1. 工件材料:不同材料的切削用量不同。
硬度和韧性大的材料往往需要较大的切削用量,而硬度和韧性小的材料需要较小的切削用量。
2. 切削刀具:不同切削刀具的切削用量不同,因此需要根据刀具的类型和特性进行选择。
3. 加工表面的光洁度要求:如果需要较高的表面光洁度,则切削用量应适当减小,以减少表面粗糙度。
4. 机床性能:切削用量还需要结合机床的性能进行选择,包括机床的刚性、功率、切削速度等因素。
5. 加工过程中的震动和共振情况:过大的切削用量容易引起加工过程中的震动和共振,因此需要适当减小切削用量,以保证加工的稳定性和精度。
选择合适的切削用量可以帮助实现加工效率和质量的平衡,提高数控车削加工的效率和质量。
切削 用量的合理选择
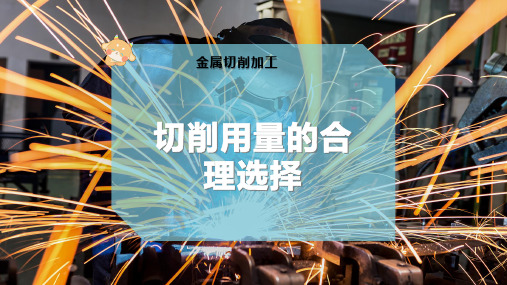
2)根据机床说明书,取机床实际进给量 =0.51mm/r。 3)检验机床进给机构允许的进给量。参考CA6140车床说 明书,查出机床进给机构允许的最大进给抗力为:FMfmax= 3528N。 计算切削时进给力为:
统、工件刚度以及精加工时表面粗糙度要求,确定进给量。
3)根据刀具寿命,确定切削速度。 4)所选定的切削用量应该是机床功率所允许的。
1.2切削用量的合理选择方法
1.背吃刀量的合理选择
背吃刀量一般是根据加工余量来确定。 粗加工(表面粗糙度Ra=50~12.5μm)时,尽可能一 次走刀即切除全部余量,在中等功率的机床上加工,取 ap=8~10mm;加工余量太大或余量不均匀、工艺系统刚性 不足或者断续切削时,可分几次走刀。 半精加工(Ra=6.3~3.2μm)时,取ap=0.5~2mm。 精加工(Ra=1.6~0.8μm)时,取ap=0.1~0.4mm。
1.5切削用量的优化概念
切削用量的优化是指在一定的预定目标及约束条件下, 选择最佳的切削用量。
在实际生产中,由于各种条件(加工零件、机床、刀 具、夹具等)都在变化,很难确定出一组最合理的切削用 量数值。
利用切削用量优化的方法,在确定加工条件下,综合 考虑各个因素,通过计算机辅助设计,能找出满足高效、 低成本、高利润和达到表面质量要求的一组最佳的切削用 量参数。实际切削用量的优化过程就是建立优化目标的数 学模型,用计算机求极值。主要目标函数有三个。
床功率是否允许。 在实际生产中,切削用量的合理选择,既可参照有关 手册的推荐数据,也可凭经验根据选择原则确定。
1.3车削用量的合理选择例题
刀具及切削参数选择
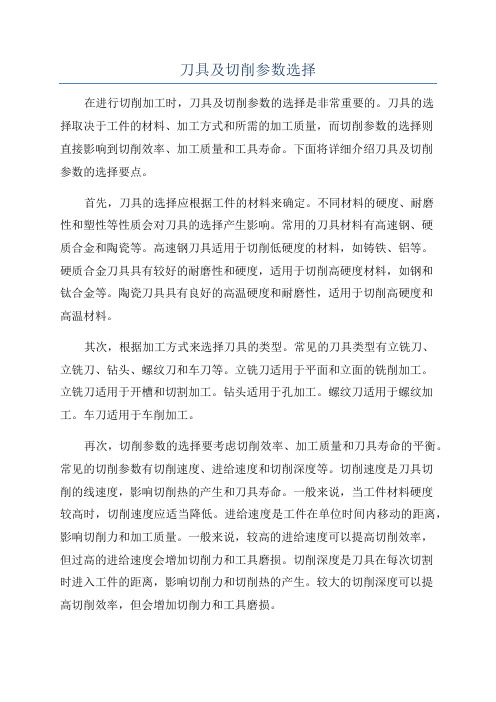
刀具及切削参数选择在进行切削加工时,刀具及切削参数的选择是非常重要的。
刀具的选择取决于工件的材料、加工方式和所需的加工质量,而切削参数的选择则直接影响到切削效率、加工质量和工具寿命。
下面将详细介绍刀具及切削参数的选择要点。
首先,刀具的选择应根据工件的材料来确定。
不同材料的硬度、耐磨性和塑性等性质会对刀具的选择产生影响。
常用的刀具材料有高速钢、硬质合金和陶瓷等。
高速钢刀具适用于切削低硬度的材料,如铸铁、铝等。
硬质合金刀具具有较好的耐磨性和硬度,适用于切削高硬度材料,如钢和钛合金等。
陶瓷刀具具有良好的高温硬度和耐磨性,适用于切削高硬度和高温材料。
其次,根据加工方式来选择刀具的类型。
常见的刀具类型有立铣刀、立铣刀、钻头、螺纹刀和车刀等。
立铣刀适用于平面和立面的铣削加工。
立铣刀适用于开槽和切割加工。
钻头适用于孔加工。
螺纹刀适用于螺纹加工。
车刀适用于车削加工。
再次,切削参数的选择要考虑切削效率、加工质量和刀具寿命的平衡。
常见的切削参数有切削速度、进给速度和切削深度等。
切削速度是刀具切削的线速度,影响切削热的产生和刀具寿命。
一般来说,当工件材料硬度较高时,切削速度应适当降低。
进给速度是工件在单位时间内移动的距离,影响切削力和加工质量。
一般来说,较高的进给速度可以提高切削效率,但过高的进给速度会增加切削力和工具磨损。
切削深度是刀具在每次切割时进入工件的距离,影响切削力和切削热的产生。
较大的切削深度可以提高切削效率,但会增加切削力和工具磨损。
此外,还应考虑冷却润滑剂的选择和使用。
合适的冷却润滑剂可以降低切削热的产生,减小工具磨损,提高加工质量。
综上所述,刀具及切削参数的选择需要考虑工件材料、加工方式和所需加工质量。
合理选择刀具类型和切削参数可以提高切削效率、加工质量和工具寿命。
在实际应用中,还需要根据具体情况进行调整和优化。
车削切削用量选取参考表讲解学习
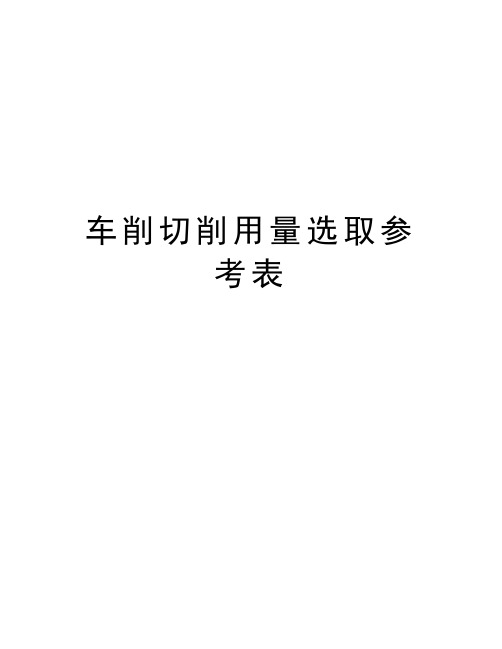
2.1
0.9
>360~500
1.4
0.7
1.5
0.7
1.5
0.8
1.7
0.8
1.9
0.9
2.2
1
1、粗加工,表面粗糙度为Ra50~12.5时,一次走刀应尽可能切除全部余量。
2、粗车背吃刀量的最大值是受车床功率的大小决定的。中等功率机床可以达到8~10mm。
二、高速钢及硬质合金车刀车削外圆及端面的粗车进给量
工件材料
车刀刀杆尺寸(mm)
工件 直径(mm)
切深
≤3
3~5
5~8
8~12
>12
进给量fmm/r
碳素结构钢、合金结构钢、耐热钢
16×25
20
0.3~0.4
—
—
—
—
40
0.4~0.5
0.3~0.4
—
—
—
60
0.5~0.7
0.4~0.6
0.3~0.5
—
—
100
0.6~0.9
0.5~0.7
0.5~0.6
0.4~0.5
275-335
0.25
8
17-21
0.5
66-72
82-90
0.75
YT5
105-120
0.5
215-245
0.4
高强度钢
225~350
1
20-26
0.18
90-105
115-135
0.18
YT15
150-185
0.18
380-440
0.13
>300HBS时宜用W12Cr4V5Co5及W2Mo9Cr4VCo8
简述切削用量的选用原则

简述切削用量的选用原则
切削用量是指切削刀具在切削工件时必须耗费的时间,物料和机械能力的集合。
一般
情况下,应尽可能少地消耗切削用量来降低成本和制造质量的波动。
本文介绍了选择切削
用量的原则。
一、选择切削用量时,首先应考虑机床的性能,特别是精密加工对机床的要求更高。
如果机床性能较低,那么选择合适的切削用量就尤为重要。
二、确定切削用量时,应考虑机器效率,机械效率越高,则需要的切削用量也会增加。
三、受到工件的影响,在评估适当的切削用量时,应考虑工件的复杂程度和几何形状。
如果工件复杂而且几何形状多变,那么将需要更多的切削用量。
四、在评估切削用量时,还应根据材料类型来处理,同一种材料可能会影响切削用量。
通常,脆性材料需要更多的切削用量,而韧性材料需要比较少的切削用量。
五、根据切削刀具的类型,选择合适的切削用量。
在一般情况下,切削刀具可分为几
何式、物理式和动力式,分别具有不同的切削效果。
选择不同类型的切削刀具后,切削用
量将会受到不同的影响。
六、受质量要求的影响,质量要求高的产品,外观、精度、尺寸等指标的误差小,则
需要更多的切削用量。
七、受加工精度要求的影响,切削用量越高,加工精度就越高,对于一些特殊的零件,如高精度的精密元件,需要增加切削用量来实现高精度的加工效果。
总之,在选择切削用量时,应考虑机床性能、机器效率、工件复杂性、材料影响、刀
具类型、质量要求、加工精度等因素,合理地选择切削用量,可以使加工效率及制造成
本达到最佳。
切削用量选择的基本原则
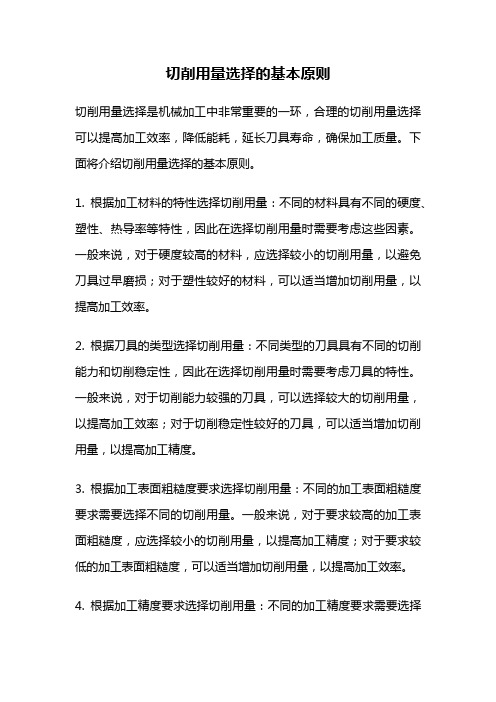
切削用量选择的基本原则切削用量选择是机械加工中非常重要的一环,合理的切削用量选择可以提高加工效率,降低能耗,延长刀具寿命,确保加工质量。
下面将介绍切削用量选择的基本原则。
1. 根据加工材料的特性选择切削用量:不同的材料具有不同的硬度、塑性、热导率等特性,因此在选择切削用量时需要考虑这些因素。
一般来说,对于硬度较高的材料,应选择较小的切削用量,以避免刀具过早磨损;对于塑性较好的材料,可以适当增加切削用量,以提高加工效率。
2. 根据刀具的类型选择切削用量:不同类型的刀具具有不同的切削能力和切削稳定性,因此在选择切削用量时需要考虑刀具的特性。
一般来说,对于切削能力较强的刀具,可以选择较大的切削用量,以提高加工效率;对于切削稳定性较好的刀具,可以适当增加切削用量,以提高加工精度。
3. 根据加工表面粗糙度要求选择切削用量:不同的加工表面粗糙度要求需要选择不同的切削用量。
一般来说,对于要求较高的加工表面粗糙度,应选择较小的切削用量,以提高加工精度;对于要求较低的加工表面粗糙度,可以适当增加切削用量,以提高加工效率。
4. 根据加工精度要求选择切削用量:不同的加工精度要求需要选择不同的切削用量。
一般来说,对于要求较高的加工精度,应选择较小的切削用量,以提高加工精度;对于要求较低的加工精度,可以适当增加切削用量,以提高加工效率。
5. 根据切削热量选择切削用量:切削过程中会产生大量的热量,如果切削用量选择不当,会导致切削热量过大,影响加工质量。
因此,在选择切削用量时需要注意控制切削热量,避免过热引起刀具磨损和工件变形。
6. 根据加工环境选择切削用量:加工环境对切削用量也有一定的影响。
例如,如果加工环境温度较高,应适当减小切削用量,以避免切削热量过大;如果加工环境湿度较大,应选择较大的切削用量,以提高切削稳定性。
切削用量选择的基本原则是根据加工材料特性、刀具类型、加工表面粗糙度要求、加工精度要求、切削热量和加工环境等因素综合考虑,选择合适的切削用量,以达到提高加工效率、降低能耗、延长刀具寿命和确保加工质量的目的。
- 1、下载文档前请自行甄别文档内容的完整性,平台不提供额外的编辑、内容补充、找答案等附加服务。
- 2、"仅部分预览"的文档,不可在线预览部分如存在完整性等问题,可反馈申请退款(可完整预览的文档不适用该条件!)。
- 3、如文档侵犯您的权益,请联系客服反馈,我们会尽快为您处理(人工客服工作时间:9:00-18:30)。
取较大值,如Κr´=30°~45°。
1.5 刃倾角的选择
刃倾角对切削加工的影响:刃倾角λs的正负和大小,影响刀尖部分的
强度、切屑流出的方向和切削分力之间的比值。
2.2 进给量f的确定
粗加工时,进给量的确定主要受切削力的限制, 在刀杆和工件刚度以及机床进给机构强度允许的情况 下,同时考虑工件材料和断屑等问题,应尽量选择较 大值。
精加工时,一般切削力不大,进给量主要受表面 粗糙粗限制,一般根据表面粗糙度的要求来选取,具 体数值参见切削用量手册。
2.3 切削速度v的确定
粗加工时,切削速度v主要受刀具耐用度的限制,由于ap、f的 值比较大,需核算机床电机的功率是否足够。
当切削速度由刀具耐用度确定时,可按下式计算:
C T mapxv
f
yv
kv
当切削速度受机床功率限制或校验机床功率时,可按下式计算:
6104 PEη Fz
m/min
精加工时,ap、f的值都比较小,切削力较小,一般机床电机 功率足够,所以切削速度主要由刀具耐用度决定。
1.4 副偏角的选择
副偏角Κr´的作用: 减小副切削刃、副后刀面和已加工表面之间的摩擦,其大
小会影响已加工表面粗糙度和刀尖部分的强度。 副偏角对切削加工的影响:
减小副偏角Κr´,使刀尖部分体积增大,刀尖强度提高,
残留面积高度降低,但刀具与工件之间的摩擦增加。 副偏角的选择:
副偏角变化幅度不大。一般外圆车刀取Κr´=6°~15°,
2.4 切削用量确定的具体方法和实例
例 在车床CA6140上按下图所示方式加工外圆,毛坯直径为φ57, 材料为调质45钢,外圆车削后的尺寸φ50×200mm,表面粗糙度Ra
为3μm,试确定的选择
刀具材料对前角选择的影响: 高速钢的抗弯强度和冲击韧性好于硬质合金,故相同加工条
件下,高速钢刀具可选较大前角,硬质合金应选较小前角,以保 证刃口强度和抗冲击能力。但前角不宜过小,否则会使刀具锋利 度过度削弱,使切削力增加。 工件材料对前角选择的影响: 切削脆性材料,切屑呈崩碎状,切削力带有冲击性,并集中 在刃口附近,为增加刃口强度,防止崩刃,一般选用较小前角; 切削塑性材料,切屑沿前刀面流动,切削力作用中心远离刀 刃,为使刀具锋利,减小切削力,一般选较大前角。 工件材料的强度、硬度越高,切削时产生的切削力越大,刀 头应有足够的强度,前角应越小,反之应越高。
车削断续表面或具有 冲击载荷时,一般采 用较大负刃倾角 λs=-5°~-15°, 同时选用正前角,平 衡“锋利与强固”之 间的矛盾,以免背向 力过大。
表1-10给出了刃倾角λs选用值
1.6 前刀面形状的选择
正前角平面形:形状简单、制造方便、 刀刃锋利,但强度较低,常用于单刃、 多刃精加工车刀和形状复杂刀具,如 螺纹车刀、切齿刀具等。
精加工应选用 正的刃倾角, 粗加工可以选 负的刃倾角。
λs=0°,切屑沿 前刀面卷曲
λs <0°,切屑流向已 加工表面,有可能划伤 已加工表面
λs>0°,切屑
流向待加工表面
1.5 刃倾角的选择
刃倾角正负对刀尖强度的影响:
λs为负值时,刀刃首 先接触工件,保护了 刀尖,不容易打刀
λs为正值时,刀尖首 先接触工件,受到冲 击,容易打刀
1.2 后角的选择 例如:加工低碳钢时,粗车时取α0 =8°~10°,精车时 取α0 =10°~12°。加工高强度、高硬度的材料如淬火钢 时,常采用负前角以增加刃口强度,此时,应采用较大的 后角α0 =12°~15°,使刀具刃口保持必要的锋利。
注:当刀具磨钝标准均为VB时,后角 大的刀具由于径向磨损量NB大,刀具 每次重磨后,径向尺寸明显减小,使 加工尺寸变化量大,影响加工精度。 所以铰刀、内孔拉刀等定尺寸精加工 刀具,特别不适宜采用大的后角。
➢ 尽可能一次走刀切除全部加工余量,使走刀次数最少。 ➢ 当加工余量太大或工艺系统刚性不足或余量很不均匀时, 分两次或多次走刀。
第一次走刀,ap1 =(2/3~3/4)Z 第二次走刀,ap2 =(1/3~1/4)Z
Z为加工余量,加工回转体时应为单边余量。
精加工时ap确定原则:
一般采用逐渐减小ap的方法来保证加工精度,终加工则 根据加工表面的技术要求和加工方法确定。
1.6 前刀面形状的选择
负前角形:前刀面可做成单面形和双面形两种。 单面形适用于后刀面上磨损的车刀;双面形适用于前、后
刀面同时磨损的车刀,可以减少刀具前刀面重磨面积,增加刀 片的重磨次数。
负前角形的刀具切削刃强度高,散热好,加工高强度、高 硬度材料的硬质合金刀片多采用这种形式。
1.7 刀尖与过渡刃
正前角曲面带倒棱形:前 刀面在刃口处作出负倒棱, 以增加刃口的强度,改善 散热条件。倒棱宽度br= (0.5~0.8)f,γ01= 5°~-25°,保证切屑沿 前刀面流出,不沿负倒棱 流出。有时为了断屑,在 前刀面上磨出或压出曲线 形的卷屑槽。这种前刀面 既能保证刃口的强度,又 能保证刀具的正前角,广 泛用于车刀、钻头、拉刀、 铣刀等刀具。
(2)强化刀尖。由于主偏角较大,刀尖强度受到影响,采取的补偿 措施包括:磨出直线过渡刃(长2~4mm,偏角45°);采用较大的刃口圆
弧半径,rε=1.5~2mm。
3)断屑措施 为了使切削过程顺利,切屑清理运送方便,前刀面上磨出前宽后窄的
圆弧形卷屑槽(与主切削刃夹角为10°),以保证可靠断屑。
2 合理确定切削用量
模块二:切削过程及控制
第三单元 金属切削过程 及控制
五、刀具参数和切削用量选择
注:课件内部分图片、动画、视频为引用,来源不详。
1 合理选择刀具材料和刀具几何参数
1.1 前角的选择 前角对切削加工的影响: 优点:增大前角,刃口变锋利,前刀面对切屑金属的挤压和 摩擦减少,切削变形和切削力减小,可抑制或消除积屑瘤,有 利于消除振动,提高加工表面质量。 缺点:增大前角对断屑不利,且刀刃和刀头的强度被削弱, 散热条件差,影响刀具耐用度。 选择前角的原则:保证刃口的锋利,并兼顾刃口的强度。 具体选择时要考虑刀具材料、工件材料和具体加工情况等。
1.7 刀尖与过渡刃
过渡刃的形式 :
圆弧形过渡刃(修圆刀尖):参 数为刀尖圆弧半径rε。圆弧形过 渡刃刃磨复杂,一般用于半精加 工或精加工,在难加工材料切削 时也常采用圆弧刀尖,以保证刀 尖有足够的强度。
1.8 车刀几何参数选择的综合分析实例 例:图1-40所示是一把用于粗车大、中型铸钢件或锻件用的大切深
合理确定切削用量是为了提高切削效率、保证加工质 量和刀具耐用度。切削用量三要素中切削速度对刀具耐用 度影响最大,背吃刀量影响最小。综合考虑切削用量对刀 具耐用度、生产率和加工质量的影响,选择时一般遵循以 下原则:
➢ 首先选择背吃刀量ap, ➢ 其次确定进给量f, ➢ 最后确定切削速度v。
2.1 背吃刀量ap的确定 粗加工时ap确定原则:
强力车刀,这种车刀采用P30硬质合金刀片,试分析这把车刀几何参 数的选用特点。
分析:粗加工时重点考虑的问题是提高效率,在机床功率允许的范围内, 尽量加大ap和f,这就要求车刀刃口尽可能锋利;同时考虑毛坯形状不规 则,余量大且不均,切削时会有冲击,要求车刀刃口要有足够的强度。针 对这把车刀既要锋利,又要强固的要求,其几何参数作了如下选择: 1)保证锋利
1.1 前角的选择
加工要求对前角选择的影响: 粗加工时选择较小前角; 精加工时选择较大前角; 加工成形表面时,刀具前角应小些,以减小
刃形误差。
1.2 后角的选择
后角的主要作用:减小后刀面与加工表面之间的摩擦,并配合 前角调整刀具的锋利程度和刃口的强度。 后角对切削加工的影响:增大后角,可减少后刀面与加工表面 之间的摩擦,使刃口锋利。但后角过大,刃口强度和散热条件 会变差,影响刀具耐用度。 后角的选择:后角一般在一个较小范围内优选。 粗加工时,刀具承受的切削力较大,并伴有冲击性负荷,为 保证刃口强度,后角应小一些; 精加工时,切削力较小,切削过程平稳,为减小摩擦,保证 已加工表面质量,后角应大些。 加工弹性材料时,工件表面弹性恢复程度大,应取较大后 角以减小后刀面与加工表面之间的摩擦。
过渡刃:刀具主、副切削刃之间磨出一段过渡直线或圆弧刃,统称为 过渡刃。
过渡刃的作用:增加刀尖强度,改善散热条件,降低表面粗糙度。但 过渡刃增大了背向力Fy,容易引起系统振动,所以不宜过大。
过渡刃的两种形式 :
直线形过渡刃(倒角刀尖):特征参数为过渡 刃长度bε和偏角Κrε,通常取bε=0.5~2mm, Κrε≈Κr/2。过渡刃偏角Κrε=0°,称为 修光刃,在大进给量条件下切削时,采用这种 刀刃切削可得到较小的表面粗糙度,但背向力 很大,要求工艺系统刚性好。直线形过渡刃结 构简单,容易刃磨,一般粗加工或强力切削用 的车刀、切断刀、可转位面铣刀都采用直线形 过渡刃。
取大前角γ0=18°~20°,刀具锋利,减小了切削力。同时为了减小 背向力,防止系统发生振动,采用了大主偏角Κr=75°。 2)兼顾强固
(1)强化刃口。由于前角较大,粗加工负荷大,必须采取措施对刃 口强度进行补偿。措施有三:一是磨出“负倒棱”,宽0.8~1,前角
γ01=-10°;二是减小后角,刀片后角α0=4°,刀杆后角6°;三是采用 负刃倾角λs= -4°~-6°
1.3 主偏角的选择
例如:车削细长轴时,取Κr =75°~90°;车削高强度、 高硬度的冷硬轧辊,取Κr≤15°,以提高刀尖强度,减 小单位刀刃长度上的切削力;车削阶梯轴时,为同时车出 台肩端面,取Κr =90°~93°;有时用一把车刀依次车 削外圆、端面、内孔、倒角,此时取Κr =45°;镗盲孔 时使Κr >90°。
1.3 主偏角的选择