熔体纺丝成型
第六章-2-熔融纺丝

图
(3)影响取向的因素
①聚合物分子量:M ②卷绕速度 纺程上不结晶时:VL↑,使σxx Δn ↑ 纺程上结晶时:VL↑,使σxx ↑ 微晶取向↑ 进一步使VL↑↑,Δn 变化缓慢 ③熔体泵供量(细度不变):W ↑ Δn↓ ④ 纤维细度(泵供量不变) :d↓ Δn ↑ ⑤环境介质温度的影响:Ts ↑ Δn↓ ⑥熔体温度的影响:To ↑ Δn↓ ηe ↑ σxx ↑ Δn ↑
两个重要的结论: (1)在横吹风时(Vx =0, V y=a)的传热系数为纵向吹风(Vx=a, Vy=0)时的两倍
(2)在纺丝线上丝条冷却的控制因素是变化的
=0.428A-0.3332Vy0.334 =0.428A-0.333Vx0.334 在纺程上部, Vx<<8Vy(Vy/ Vx >>0.125)时 在纺程下部, Vx>>8Vy( Vy/ Vx << 0.125)时
卷曲,上油,切断和打包整个工序。
长丝的后加工-拉伸
拉伸加捻示意图 1—筒子架 2—卷绕丝筒 3,8—导 丝棒 4—喂入辊 5—上拉伸盘 6—加热器 7—下拉伸盘 9—钢领 10—筒管 11—废丝轴 12—钢丝圈
拉伸加捻流程
POY丝假捻变形的加工
POY丝假捻变形的加工原理
利用纤维的热塑性,经 过“变形”和热定型而制得 的高度卷曲蓬松的弹力丝。 加捻、热定型、解捻这 三个过程在同一台机器上完 成。
②表面张力Fs
纺丝液的拉伸流动使流体比表面积增大,但表面张力 要使液体表面趋于最小, Fs是一种抗拒拉伸的作用力 。 Fs=2π(R0-Rx) λ Fs仅在液态区域内起作用;熔纺中一般很小,除了纺 低分子量物料外可忽略。
③摩擦力Ff
熔体纺丝(meltspinning)工艺原理
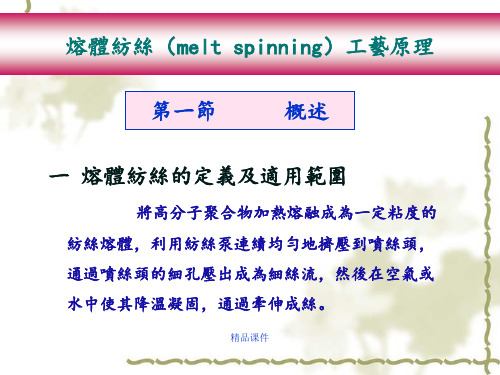
第三節 熔體紡絲過程中纖維結構的形成
❖ 初生纖維結構的形成和發展主要是指紡絲線上聚合物的取 向和結晶。
❖ 一 熔體紡絲過程中的取向作用
紡絲過程中發生取向是纖維製造中重要的結構
形成過程之一。對成品纖維的取向貢獻最大的不是 紡絲工序,而是拉伸工序。在紡絲過程中得到的取向 度,即預取向度,對拉伸工序和成品纖維的取向度有很
於絲條的方向上吹送調溫調濕氣流。
精品课件
初生纖維的後處理主要有拉伸、熱定型、捲曲 和假撚。
拉伸可改變初生纖維的內部結構,提高斷裂強度和
耐磨性,減少產品的伸長率。熱定型可調節紡絲過程帶
來的高聚物內部分子間作用力,提高纖維的穩定性和其
他物理-機械性能、染色性能。卷曲是改善合成纖維的
加工性(羊毛和棉花纖維都是捲曲的),克服合成纖維
❖ 二 熔體紡絲過程中的結晶
熔體紡絲線上的結晶是控制絲條固化的 一個極重要的動力學過程。紡絲線上的結晶對捲繞絲 的結構和性能起決定作用。 ❖ (一)熔體紡絲中纖維結晶的主要特徵
熔體紡絲中纖維結晶的特徵包括兩個方面 ,一是捲繞絲本身的晶態結構,二是熔體紡絲中聚合 物結晶過程的發展。
精品课件
捲繞絲的結晶特性主要包括:晶格結構 、結晶度、結晶形態和結晶取向等,它們對纖
大的影響,對結晶動力學和晶體形態也有一定的影響。
精品课件
精品课件
❖ 兩種取向機理:
(1)處於熔體狀態下的流動取向機理:包括噴絲孔 中切變流場中的流動取向和出噴絲孔後熔體細流在 拉伸流場中的流動取向
T高,τ小,取向小,可忽略
控制取向的速度場:軸向
精品课件 速度梯度,主要
(2)纖維固化之後的形變機理
1)紡絲線上的任何一點上,高聚物的流動是“穩態”的和連 續的。
熔体纺丝工艺原理
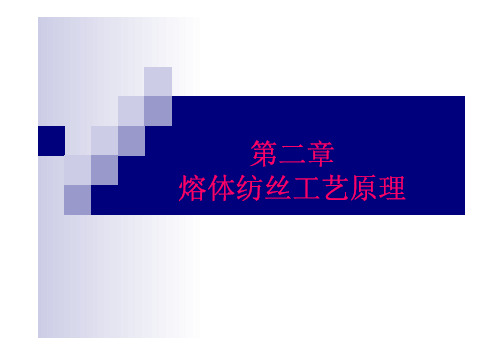
σ 12 ηγ̇ γ = = = τγ̇ = N Re,el G G
PP比PET纺丝流体的非牛顿性强,弹性 显著,τ值和ψ值越大,总法向应力差和 胀大比越大。因此流体的粘弹本质是决定 胀大比的内因。 � 适当提高纺丝温度,控制适宜的分子量, 适当增大喷丝孔径(0.4mm),以及增大 喷丝孔长径比(L/D值大于2)和降低剪切 速率。都是可以减小细流的胀大比,改善 PP的可纺性能。
�
1.简述影响纺丝流体弹性的因素及其对成形的影响。 2. 什么是孔口胀大?纺丝流体产生孔口胀大的原因是 什么?并说明欲提高纺丝产量会遇到哪些问题?怎样 克服? 3. 纺丝流体出现不稳定流动的原因是什么? 4. 什么是纺丝流体的可纺性?表征可纺性的方法有哪 些?纺丝中如何避免出现毛细断裂和内聚断裂? 5. 简述纺丝流体的挤出类型及其影响因素。
dmax时, d= d=d
dv x ̇x = ε =0 dx
X<10mm 弹性释放。
1.PA6,2.PET,3.PS
Ⅱ形变(细化)区: 丝条拉伸流动, 拉长变细。 Vx ↑, d ↓, 出现极大值, X=50-150cm 2 dv d vx a Ⅱ : x > 0, >0
dx dx 2
̇ ( X ) ↑ x ≈ 10cm T高, η 小,形变大。 ε V(x)增加快,大部分形变在此发生。
�
原则上,这两种断裂机理都能独立地对丝条的断裂 起作用。 两种断裂机理起控制作用的条件: η、 V0 较小时毛细破坏起控制作用 η、 V0 较大时内聚破坏起控制作用 在某一中间范围χ* 有极大值,可纺性最好
4. 纺丝中可能发生的断裂
表面张力(达因/cm2) PP.PE PA.PET 30-50 30-80
)=
熔体纺丝纤维成型原理
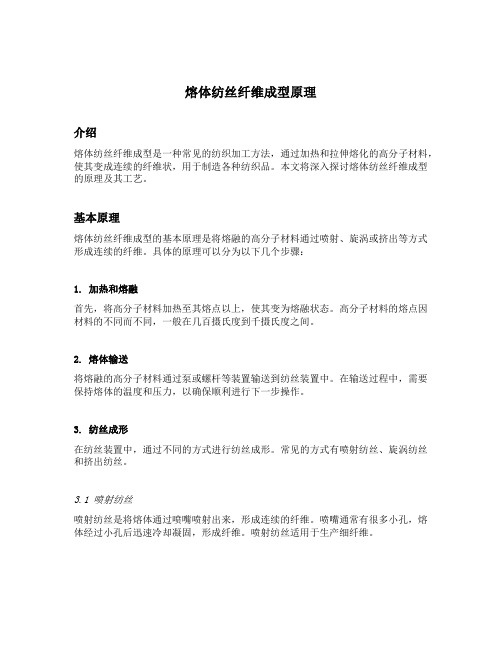
熔体纺丝纤维成型原理介绍熔体纺丝纤维成型是一种常见的纺织加工方法,通过加热和拉伸熔化的高分子材料,使其变成连续的纤维状,用于制造各种纺织品。
本文将深入探讨熔体纺丝纤维成型的原理及其工艺。
基本原理熔体纺丝纤维成型的基本原理是将熔融的高分子材料通过喷射、旋涡或挤出等方式形成连续的纤维。
具体的原理可以分为以下几个步骤:1. 加热和熔融首先,将高分子材料加热至其熔点以上,使其变为熔融状态。
高分子材料的熔点因材料的不同而不同,一般在几百摄氏度到千摄氏度之间。
2. 熔体输送将熔融的高分子材料通过泵或螺杆等装置输送到纺丝装置中。
在输送过程中,需要保持熔体的温度和压力,以确保顺利进行下一步操作。
3. 纺丝成形在纺丝装置中,通过不同的方式进行纺丝成形。
常见的方式有喷射纺丝、旋涡纺丝和挤出纺丝。
3.1 喷射纺丝喷射纺丝是将熔体通过喷嘴喷射出来,形成连续的纤维。
喷嘴通常有很多小孔,熔体经过小孔后迅速冷却凝固,形成纤维。
喷射纺丝适用于生产细纤维。
3.2 旋涡纺丝旋涡纺丝是将熔体喷射到旋转的输送气流中,通过离心力的作用将其拉伸成纤维。
旋涡纺丝适用于生产中纤纤维。
3.3 挤出纺丝挤出纺丝是将熔体通过挤出机的挤出口挤出,形成连续的纤维。
挤出纺丝适用于生产粗纤维。
4. 冷却和拉伸成形的熔体纤维需要经过冷却和拉伸处理。
冷却可以固化纤维,拉伸可以提高纤维的强度和拉伸性能。
5. 收集和卷绕最后,完成的纤维被收集起来,并通过卷绕装置进行卷绕。
卷绕的方式通常根据需要选择,可以是平板卷绕、筒形卷绕或其他形式。
工艺参数熔体纺丝纤维成型的工艺参数对成品的质量有重要影响。
以下是一些常见的工艺参数:1.温度:熔体的温度对纤维的形成和性能有影响,需要根据具体材料选择合适的温度。
2.压力:熔体的压力决定了纤维的形状和尺寸,过高或过低的压力都会影响纤维的质量。
3.拉伸速度:纤维的拉伸速度会影响纤维的强度和拉伸性能,需要根据要求进行调节。
4.冷却方式:不同的冷却方式会导致纤维的结构和性能产生变化,可以选择气体冷却、水冷却等方式。
熔体纺丝(melt spinning)工艺原理

冷卻速率增加,結晶所需時間降低,結晶速率隨
紡速提高而增加。
取向使結晶速率大大增加的原因,可以概括為兩類: 一,從結晶理論的角度看,大分子取向區域越大, 生成晶核的臨界溫度也越高,因此,在熔體冷卻的 過程中,取向高的體系能夠在較高的溫度下形成晶
核,取向低的體系則相反,必須有較大的過冷度才
能形成晶核。
取向度的測定:一般用取向因數f 表徵。
該式用於表徵單軸取向中結構單元的取向,υ
表示單元晶胞某晶軸與纖維軸的平均夾角,當
結構單元完全平行于纖維軸時,υ=0,f=1;
垂直于纖維軸時,υ=90度,f=0.5 。
二 熔體紡絲過程中的結晶
熔體紡絲線上的結晶是控制絲條固化的一個極
重要的動力學過程。紡絲線上的結晶對捲繞絲的結構
流一經固化,就有巨大的抗張能力,所以熔紡的捲繞速
度比濕紡為高,一般在1000~1500米/分,噴絲頭拉伸 比(捲繞速度與熔體從噴絲孔噴出速度之比)也比濕紡 時高。
三、上油
熔紡纖維剛成形時幾乎是幹的,容易積聚靜電,纖
維間的抱合力差,與設備的摩擦力大,因此在捲繞前要 經過給油、給濕處理。
對於吸水性較大的聚醯胺纖維還可以防止繞在筒 管上的絲條再度吸水,以致發生縱向膨脹而出現松圈 和塌邊等現象。 化學纖維在紡絲和紡織加工過程中因不斷摩擦而 產生靜電,必須使用助劑以防止或消除靜電積累,,同 時賦於纖維以柔軟、平滑等特性,使其順利通過後道
熔體紡絲過程中的參數可以歸為三類
第二節 熔體紡絲過程的運動學和動力學
紡絲線上直徑的變化和速度的分佈
從速度分佈,可求出拉 伸應變速率(軸向速度 梯度)
根據拉伸應變速率的 不同,把整個紡絲線 分成三個區域
熔融纺丝法简介

熔体制备(螺杆挤压机) 含水率较高的成纤高聚物在熔融纺丝前要经过干燥处 理,以防止由于水分引起的高聚物熔体分子降解。高聚物 切片受热熔融过程中微细结构发生如下变化:非晶区从玻 璃态转变为高弹态,再变为粘流态;结晶区发生晶体的融 化,也成为粘流态,最后高聚物形成熔体。
纺丝工艺过程 熔融挤压→过滤→静态混和→计量→熔体分配→挤出 成形→冷却 过滤可去除聚合物熔体中一些凝胶和细小的固体粒子。 静态混和是指聚合物熔体输送管道中静态混和器对聚 合物熔体的均匀混和作用。 计量和熔体分配可精确控制产量和纤维细度的一致性。
一般,喷丝孔直径越大,所纺纤维直径越大,纤维 双折射越低。喷丝孔直径越大,可以减缓熔体在喷丝孔 中流动时的径向剪切速度梯度,降低毛细粘性流动的切 应变速率,减少出口时的熔体膨大现象。喷丝孔越长, 熔体弹性形变能松弛越多,将来出口处熔体膨大越小。 通常,喷丝孔直径和长度大一些,纺丝比较稳定,尤其 是对高粘度熔体的纺丝有利。一般长径比大些,有利于 熔体松弛,减小出口膨大;但当长径比大到某一数值时, 膨大系数不再随长径比变化。
• 液滴型不能成为连续细流,纤维无法成形;液滴型出现的 条件首先与纺丝流体的性质有关。流体表面张力α越大, 则细流缩小其表面积成为液滴的倾向也越大。此外,粘度 η的下降也促使液滴的生成。 • 漫流型虽已形成连续细流,但纺丝流体在流出喷丝孔后, 迅即沿喷丝板表面漫流。这种细流很不稳定,纺丝往往因 而中断;为避免漫流型细流的出现,应设法提高η和R0 或 降低界面张力
• 聚合物熔体从喷丝孔挤 出成形,经历入流、孔 流、出流、变形和稳定 的流变过程,其物理形 态和几何形态均发生变 化。 • 高聚物流体通过喷丝孔 的流动有明显的流场变 化,而包括毛细孔入口 区的收敛流场,毛细孔 区的管道流动,以及毛 细孔出口区向拉伸流动 的流场过渡
熔融纺丝工艺流程

熔融纺丝工艺流程熔融纺丝工艺是一种将高分子材料通过熔融加工成纤维的方法。
该工艺被广泛应用于纤维素、聚酯、聚酰胺等高分子材料的制备。
下面将详细介绍熔融纺丝工艺的流程。
一、准备工作1.1 原料准备首先需要准备好所需的高分子材料,如聚酯、聚酰胺等。
这些高分子材料通常以粉末或颗粒的形式存在。
1.2 设备准备熔融纺丝设备包括熔体供给系统、挤出机、旋转收卷器等部件。
在进行熔融纺丝之前,需要对这些设备进行检查和调整,确保其正常运行。
二、挤出加工2.1 熔体供给系统首先将高分子材料放入熔体供给系统中,通过加热和搅拌使其变成流动状态。
这个过程中需要控制温度和压力,以确保高分子材料能够顺利地进入挤出机。
2.2 挤出机接下来,在挤出机的作用下,将熔体推出并拉伸成细丝。
挤出机的主要部件包括螺杆、筛网和模头。
螺杆通过旋转将熔体向前推进,筛网则用于过滤杂质,模头则用于控制纤维的形状和尺寸。
2.3 拉伸在挤出机的作用下,高分子材料被拉伸成细丝。
这个过程中需要控制温度和速度,以确保纤维的质量和性能。
三、收卷3.1 冷却在拉伸完成后,纤维需要进行冷却处理。
这个过程中需要控制温度和速度,以确保纤维能够顺利地进行收卷。
3.2 收卷最后,将冷却后的纤维送入旋转收卷器中进行收卷。
这个过程中需要控制张力和速度,以确保纤维能够均匀地分布在收卷器上。
四、检验与包装4.1 检验在完成收卷之后,需要对纤维进行检验。
这个过程中需要检查纤维的外观、尺寸、强度等指标,并对不合格品进行处理。
4.2 包装最后,将合格的纤维进行包装。
通常将纤维卷成一定长度和重量的卷筒,并进行标记和记录。
总结:熔融纺丝工艺是一种将高分子材料通过熔融加工成纤维的方法。
该工艺包括准备工作、挤出加工、收卷和检验与包装等步骤。
在进行熔融纺丝之前,需要对设备进行检查和调整,确保其正常运行。
在挤出机的作用下,高分子材料被拉伸成细丝,并经过冷却和收卷处理后进行检验和包装。
熔体纺丝定义

熔体纺丝定义熔体纺丝定义熔体纺丝是一种制备纤维的方法,它利用高分子材料的熔融状态将其挤出成细丝,并在空气中冷却和固化。
该方法广泛应用于纤维、薄膜、管材等领域,并有着广泛的应用前景。
一、熔体纺丝的基本原理熔体纺丝是利用高分子材料在加热条件下从固态转变为液态,经过特定的挤出系统将其挤出成细丝,然后通过空气或其他方式进行冷却和固化。
这个过程主要包括以下几个步骤:1.高分子材料加热:将高分子材料放入挤出机中,在一定的温度和压力下加热。
2.挤出成形:在加热条件下,高分子材料从机头中挤出成细丝。
3.冷却固化:将挤出来的细丝通过空气或其他方式进行冷却和固化,使其变得坚硬并具有所需的物理性能。
二、熔体纺丝的分类根据不同的加工方式和设备类型,熔体纺丝可以分为以下几种:1.单丝熔体纺丝:将高分子材料从单一的机头中挤出成细丝。
2.多丝熔体纺丝:将高分子材料从多个机头中挤出成多根细丝,然后通过特定的方式进行合并。
3.微纳米级熔体纺丝:利用电场、气流等特定条件对高分子材料进行加工,制备出微小尺寸的纤维或薄膜。
三、熔体纺丝的应用由于熔体纺丝具有制备成本低、生产效率高、产品性能优良等优点,因此在许多领域都有广泛的应用。
以下是几个典型的应用领域:1. 纤维制备:利用熔体纺丝技术可以制备各种类型的合成和天然纤维,如聚酯、聚酰胺、聚乙烯等。
2. 薄膜制备:通过控制挤出速度和冷却方式,可以制备各种类型的薄膜,如聚乙烯薄膜、聚氨酯薄膜等。
3. 医疗器械:熔体纺丝技术可以制备出具有良好生物相容性的材料,用于制备医用敷料、人工血管等医疗器械。
4. 环保材料:利用可降解高分子材料进行熔体纺丝制备,可以制备出可降解的环保材料,如可降解塑料袋、餐具等。
四、熔体纺丝的优缺点1. 优点:(1)生产效率高,可以大批量生产;(2)生产成本低,适合大规模生产;(3)产品性能优良,具有较高的强度和耐磨性;(4)可以制备出各种类型的高分子材料。
2. 缺点:(1)对原始材料要求较高;(2)设备成本较高;(3)对操作人员技术要求较高。
- 1、下载文档前请自行甄别文档内容的完整性,平台不提供额外的编辑、内容补充、找答案等附加服务。
- 2、"仅部分预览"的文档,不可在线预览部分如存在完整性等问题,可反馈申请退款(可完整预览的文档不适用该条件!)。
- 3、如文档侵犯您的权益,请联系客服反馈,我们会尽快为您处理(人工客服工作时间:9:00-18:30)。
熔体纺丝成型
一、实验目的
了解熔体纺丝机的各部分组成,掌握螺杆挤压机、计量泵的工作原理,了解纺丝工艺条件和工艺流程,设计出合理的纺丝工艺,纺制出合格的纤维
二、实验原理
一)螺杆挤压机的工作原理和结构
1、工作原理
物料从加料口进到螺杆的螺槽中,由于螺杆的转动,把切片向前推进。
切片不断吸收加热装置供给的热能;另一方面因切片和切片、切片与螺杆及套筒的摩擦及液层之间的剪切作用,而由一部分机械能转化成热能,切片在前进过程中温度不但升高而逐渐熔化成熔体。
熔化过程聚合物在温度、压力、粘度和形态等方面发生变化,由固态(玻璃态)转变为高弹态,随温度的进一步提高,出现塑性流动,成为粘流体(粘流态)。
粘流态的聚合物经螺杆的推进和螺杆出口的阻力作用,以一定的压力向熔体管道输送
2、挤压机的结构
螺杆挤压机主要由四部分组成(见图1)
高聚物熔融装置:主要由螺杆和套筒组成,其作用是将固体的物料挤压,外加热,使其熔融成均匀的熔体,并以一定的温度、压力和排出量从螺杆头部挤出,经过熔体管道送至纺丝装置进行纺丝。
按物料在螺杆中的输送、压缩和熔融等过程,一般将螺杆的的工作长度分为进料段、压缩段和计量段;根据物料在螺杆中的物理状态,将螺杆分为固体区、熔融区和熔体区。
加热和冷却系统:主要是由铝套加热器和水冷却夹套组成,其作用是通过对套筒的加热和冷却保证高聚物在工艺要求的温度范围内挤出。
传动系统:主要由变速电动机和齿轮箱组成,其作用是保证螺杆以需要的扭矩和转速稳定而均匀的工作。
电器控制系统:由温度、压力和转速控制系统构成,一方面通过熔体压力传感器控制电动机按所需要的转速运转,另一方面通过测温单元控制加热、冷却系统按设定温度工作。
二)计量泵的工作原理和结构
计量泵的作用是精确计量、连续输送成纤高聚物熔体或溶液,并于喷丝头组件结合产生预定的压力,保证纺丝流体通过滤层到达喷丝板,以精确的流量从喷丝孔喷出。
1、计量泵的结构
计量泵为外啮合齿轮泵,它由一对相等齿数的齿轮、三块泵板、两根轴和一副联轴器以及若干螺栓组成(见图2).
2、工作原理
计量泵工作时,传动轴插在联轴器的槽中,带动主动轴转动,从而使一对齿轮在中泵板的“8”字形孔中啮合运转。
当齿轮啮合运转时,在吸入孔造成负压,流体被吸入泵内并填满两个齿轮的齿谷,齿谷间的熔体在齿轮的带动下紧贴着“8”字孔的内壁回转近一周后送至出口,由于出口容积的不断变化,而将流体排出。
图1 螺杆挤压机
图2 计量泵结构及工作图
三)纺丝组件与喷丝板
纺丝组件的主要作用是将计量泵送来的熔体进行最终过滤,混合均匀后分配到每个喷丝孔中,形成均匀的细流。
喷丝板的主要作用是将高聚物熔体通过微孔转变成具有特定截面的细流,经过冷却固化而形成丝条。
喷丝板的主要参数包括喷丝孔的直径和长径比、孔的排列和喷丝孔的加工精度。
四)热拉伸辊
热拉伸辊是用于纺牵一步法联合机上的主要部件,装在纺丝机和卷绕机之间,经过热拉伸辊后再卷绕,称为全拉伸丝(注:一般需要是高速纺或超高速纺才能够达到全拉伸)。
五)卷绕机构
卷绕机构的作用是把丝条按一定规律卷绕收集,形成一定形状和容量的卷装。
任何一种卷装形式都应当满足一定的要求,主要有:
1、形状稳定:不论卷装采取何种形状,丝层怎样分布,卷装应十分稳定,经久不变。
2、容量大:卷装的容量增大,意味着降低丝条街头,减少机器停台时间和提高效率。
3、丝条分布均匀:卷装上的丝条应分布均匀,密度一致,软硬适中。
不能有重叠,有重叠后将出现密集丝带;也不能有凸边,否则会擦伤丝条,损坏成形,增加退绕时的阻力。
4、张力均匀:卷绕过程一定要保持一定的张力,才能使丝条卷绕成结实的卷装。
张力过大,卷装端面会出现起皱和胀边现象,张力过小,则卷装松软,退绕时容易产生塌边和脱圈。
5、退绕容易:卷装上的丝层必须层次分明,在卷装端不能有蛛网丝。
卷绕机构由导丝机构和卷取机构两部分组成。
卷绕机构工作时,只能完成卷绕作用的称为单纯卷绕机构。
三、仪器和药品
纺丝牵伸一体小型熔体纺丝机(非标,临淄方辰母料厂),干燥好的成纤树脂切片
四、实验步骤
1、打开冷却水,打开机器电源,打开各控制柜,将螺杆各部分加热到设定温度
2、温度升到后,打开热拉伸辊,并将热拉伸辊的转速(低速档)和温度设定到指定参数。
计量泵及各辊频率设定原则:
1)计量泵频率的的设定(以PA6为例):
0()t dtex 10000()t 10000V Q V Q ⨯⨯=
⨯=一辊速度(线密度,)R (拉伸倍数)
(对应线密度的单位)卷绕(线密度)或 注:泵供量单位为:g/min ;线密度单位为分特时,分母为10000;为特时,分母为1000;为旦时,分母为9000。
本设备的计量泵电机50HZ 对应1400r/min ,减速机速比为40:1,则计量泵1HZ 对应1400/50/40=0.7r
假设V0=600r/min ,t=100dtex ,r=4,则
6001004=24g /min 10000
Q ⨯⨯= 而本设备计量泵的规格为2.4cm3/r ,PA6的密度为1.14g/cm3,用泵供量除以物料密度,可以得到泵供体积,以泵供体积除以计量泵规格,可以得到计量泵转速,进而得到频率。
24g /min f 12.51.14g/3 2.43/0.7/HZ cm cm r r HZ
=≈⨯⨯ 2) 热辊频率设定
热辊的电机频率为50HZ 对应1500r/mim ,辊子直径为0.24m ,则
1HZ 对应30r/min,热辊转一周的长度为πD=0.75m
热辊1HZ 对应的线速度为22.608m/min
卷绕棍1HZ 对应的线速度为14.13m/mim
3、当各工艺参数均达到指定参数时,开启空压机,开启螺杆主机,并将主机调到高速档,从螺杆进料口加入物料切片;打开油盘;开启卷绕装置;待纺丝细流稳定后,将主机调回低俗档,开始纺丝。
4、当开始纺丝后,用吸枪吸丝后,依次经过油盘,导丝钩,三道热辊,最后进入卷绕装置前。
5、当吸丝稳定后,将热拉伸辊调节到高速挡,转速达到后开始卷绕。
6、纺丝结束后,将剩余的物料挤空。
关闭温控单元及各传动单元,待温度降下后关掉冷却水,并将实验室打扫干净,关闭所有电源方可离开实验室。
五、思考题
1、何为环结阻料?采用哪些措施避免?
2、何谓螺杆的压缩比?为何不能过大或过小?
3、挤压机进料段为何加冷却装置?
4、上油装置可以起到哪些作用?
5、为了获得性能均匀的纤维,需要加强哪些工艺环节的控制?如何控制?
6、何谓卷绕比?纺丝过程如何控制卷绕比?。