变换催化剂性能和控制工艺指标
变换、、低温甲醇洗培训教材(新能)

新能凤凰(滕州)能源有限公司新能风凰(滕州)能源有限公司技术工人培训教材变换、低温甲醇洗培训教材编写:王磊李国方审核:吴萍批准:庄乾海新能风凰(滕州)能源有限公司合成车间第一章变换部分第一节变换工段的任务及意义本工段主要是将水煤浆气化来的煤气在变换工段把一氧化碳转化为用于生产甲醇的合成气,煤气中的一氧化碳与水蒸气在变换催化剂的作用下发生变换反应转化氢和二氧化碳,采用配气路线使出变换工段的合成气中CO含量约为20%(V干基),且H/CO≈2.15( V/V),同时将部分有机硫转化2成无机硫送至低温甲醇洗工段。
第二节 变换工段的生产原理原理:一氧化碳的变换反应是一个放热反应,其反应方程式为: CO+H 2O==CO 2+H 2+Q COS+H 2O==H 2S+CO 2+Q一氧化碳变换是一个放热、摩尔数不变的可逆反应。
从化学平衡来看,降低温度、增加蒸汽量和除去二氧化碳,可使平衡向右移动,从而提高一氧化碳变换率;从反应速度看,提高温度有利于反应速度的增加。
CO 在某种条件下,能发生下列副反应: CO+H 2=C+H 2O CO+3H 2=CH 4+ H 2O CO+4H 2= CH 4+2H 2O这几个副反应都是放热反应,副反应的发生对变换操作的正常进行是不利的。
由于这些副反应都是放热反应和体积减小的反应,所以低温高压有利于副反应的进行。
在变换的正常操作中,提高反应温度或是选用对变换反应具有良好选择性的催化剂就可以防止或减少副反应的发生。
下面就温度、压力、汽气比等对变换反应的影响作进一步说明。
1、温度温度对变换反应的速度影响较大,而且对正逆反应速度的影响不一样。
温度升高,放热反应即变换反应速度增加得慢,逆反应(吸热反应)速度增加得快。
同时,CO变换率随温度的升高而降低。
因此当变换反应开始时,反应物浓度大,提高温度可加快变换速度。
反应末期,须降低反应温度,使逆反应速度减慢,这样可得到较高的变换率。
同时,反应温度的确定还和汽气比、气体成份、触媒的活性温度范围等因素有关。
耐硫变换催化剂

耐硫变换催化剂一、概述耐硫变换催化剂是一种用于去除燃料中硫元素的催化剂。
由于燃料中含有硫元素,其在燃烧过程中会释放出二氧化硫等有害物质,对环境和人体健康造成危害。
因此,为了保护环境和人类健康,需要使用耐硫变换催化剂来净化燃料。
二、工作原理耐硫变换催化剂的工作原理是将燃料中的硫元素转化为无害物质。
在催化剂表面上,硫元素与氢气反应生成H2S,并被进一步氧化为SO2和水蒸气。
SO2会被吸附在催化剂表面上,并与NOx等其他有害物质反应生成无害的物质。
三、分类根据不同的应用场景和工艺要求,耐硫变换催化剂可以分为不同的类型。
其中常见的包括:1. 低温SCR(Selective Catalytic Reduction)催化剂:适用于低温条件下去除NOx和SOx等有害物质。
2. 高温SCR催化剂:适用于高温条件下去除NOx和SOx等有害物质。
3. 脱硝催化剂:适用于烟气中的NOx去除,可以分为V2O5-WO3/TiO2、V2O5-MoO3/TiO2等不同类型。
4. 脱硫催化剂:适用于燃料中的硫元素去除,可以分为Co-Mo/Al2O3、Ni-Mo/Al2O3等不同类型。
四、性能指标耐硫变换催化剂的性能指标包括以下几个方面:1. 活性:即在一定条件下,催化剂对目标物质的转化效率。
活性越高,转化效率越好。
2. 选择性:即在一定条件下,催化剂对目标物质与其他物质的选择反应。
选择性越好,对有害物质的去除效果越好。
3. 稳定性:即催化剂在长期使用过程中的稳定性能。
稳定性越好,使用寿命越长。
4. 耐腐蚀性:即催化剂在高温高压等恶劣环境下的耐受能力。
耐腐蚀性越好,使用寿命越长。
五、应用领域耐硫变换催化剂广泛应用于以下领域:1. 石油化工行业:用于石油加氢、裂化等过程中的脱硫、脱氮等处理。
2. 电力行业:用于火力发电厂烟气中的NOx和SOx去除。
3. 汽车尾气净化:用于汽车尾气中的有害物质去除,如NOx、CO等。
4. 钢铁冶金行业:用于高炉煤气、焦炉煤气等废气中的脱硫、脱硝。
一氧化碳变换工艺分析

万方数据
第 27卷 化 肥
中低低工艺是在吸收了中串低和全低变工艺 优点的基础上发展起来的,通常设2段Fe-Cr中 变催化剂后串2段Co-Mo耐硫低变催化剂,典 型的工艺流程如图4所示。中变两段之间通常采 用水冷激或原料气冷激降温,低变进口温度通常 仍采用调温水加热器调节。由于保留了一、二段 Fe-Cr中变催化剂,使得后串的Co-Mo耐硫低 变催化剂基本上不需要保护;由于第一、二段远离 平衡,反应推动力较大,在较高的温度下使用Fe -Cr中变催化剂效果也较理想;Co-Mo耐硫低 变催化剂的使用条件与中串低时相近,第一段热 点温度略高,因此对变换系统H2S浓度的要求亦 相对较低(100mg/m3已可满足工艺要求)。
26
段间、二三段间采用水冷激方法降温、增湿;变换 炉出口变换气经热交换器加热入口半水煤气、水 加热器加热热水而降温,再入热水塔回收热量后 离开变换工序。中温变换工艺是合成氨工业中历 史最悠久的,在长期的实践过程中,进行了不断的 改革和创新,主要有:采用活性温度低、催化活性 高 的 Fe-Cr中 变 催 化 剂 , 降 低 了 入 炉 温 度 和 水 汽 比;采用段间水冷激降温措施,减少了系统的热负 荷,降低了系统的阻力降,有利于节省蒸汽;强化 了热量回收系统,提高了系统的热利用率等。
变换工段操作规程

变换工段操作规程一、工艺概述经过脱硫、除尘后的水煤气中,除含有双氧水生产时所需要的氢气外,还含有26~30%的一氧化碳及其它气体。
直接分离一氧化碳是比较困难的,但在一定的温度条件下,借助低变催化剂的催化作用,可使水煤气中一氧化碳与水蒸汽发生反应,生成二氧化碳和氢气。
二、化学反应原理变换的主要反应是在一定的温度条件下,气体中的一氧化碳与水蒸汽反应生成氢气和二氧化碳,反应方程式如下:CO+H 2O (g 2+H 2+41KJ/mol这个反应的特点是:(1)反应前后体积没有变化;(2)反应前后是放热的;(3)是完全可逆的反应,当正反两个方面进行的速度相等时,反应达到平衡。
1、影响化学平衡的因素(1)温度的影响,变换反应是放热反应,温度降低、平衡向生成氢气和二氧化碳的方面移动。
(2)反应物浓度的影响,增加反应物浓度或减少生成物浓度,反应向有利于生成二氧化碳和氢气的方向进行,可采用增加蒸汽量来实现。
2、影响反应速度的因素,变换反应在有催化剂存在时,才能大大加快反应 速度,另外提高温度和增加蒸汽用量对加快变换反应的速度也有很大作用。
三、工艺流程1、水煤气气体流程:压缩机 → 冷却器 → 除油器 → 热交换器 → 电加热器 → 变换炉一 、二段 → 变换炉三段 → 热交换器 →冷却器 →气水分离器 → 精脱硫塔(A ) →精脱硫塔(B ) → PSA 提氢装置。
2、软化水流程:由电厂送的软化水 →加压水泵 →变换炉二、三段。
3、蒸汽流程:由电厂送的蒸汽 →汽水分离器 → 电加热器 →变换炉一段。
4、循环水流程:凉水泵→冷却器→热水池→热水泵→冷却塔→凉水池→凉水泵。
四、主要设备及性能1、水煤气压缩机:L—40/0.2—8型往复式压缩机,Q:40m3/min,N:280KW,压缩机的任务是把水煤气输送到后工段,并提供过程进行所必要的压力条件。
2、变换炉φ1600×7000,变换一段上层装填抗氧剂和抗毒剂,变换二、三段上层均装填耐火球,下部装填低变催化剂,是完成一氧化碳和水蒸汽反应生成二氧化碳和氢气的主要设备。
中温变换催化剂的升温还原原操作说明
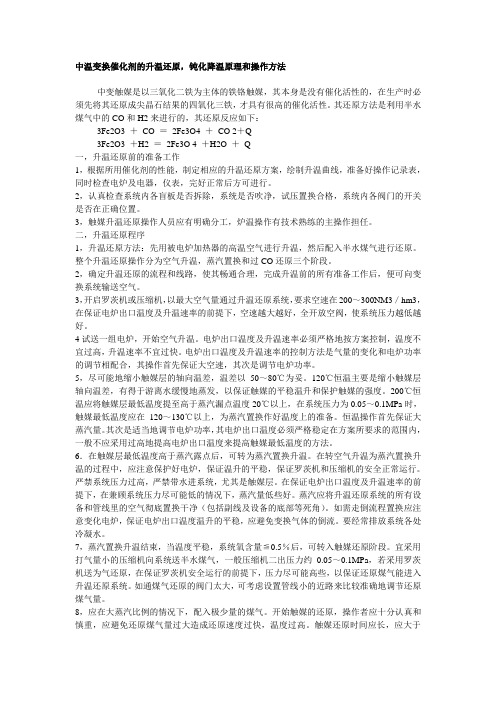
中温变换催化剂的升温还原,钝化降温原理和操作方法中变触媒是以三氧化二铁为主体的铁铬触媒,其本身是没有催化活性的,在生产时必须先将其还原成尖晶石结果的四氧化三铁,才具有很高的催化活性。
其还原方法是利用半水煤气中的CO和H2来进行的,其还原反应如下:3Fe2O3 +CO =2Fe3O4 +CO 2+Q3Fe2O3 +H2 =2Fe3O 4 +H2O +Q一,升温还原前的准备工作1,根据所用催化剂的性能,制定相应的升温还原方案,绘制升温曲线,准备好操作记录表,同时检查电炉及电器,仪表,完好正常后方可进行。
2,认真检查系统内各盲板是否拆除,系统是否吹净,试压置换合格,系统内各阀门的开关是否在正确位置。
3,触媒升温还原操作人员应有明确分工,炉温操作有技术熟练的主操作担任。
二,升温还原程序1,升温还原方法:先用被电炉加热器的高温空气进行升温,然后配入半水煤气进行还原。
整个升温还原操作分为空气升温,蒸汽置换和过CO还原三个阶段。
2,确定升温还原的流程和线路,使其畅通合理,完成升温前的所有准备工作后,便可向变换系统输送空气。
3,开启罗茨机或压缩机,以最大空气量通过升温还原系统,要求空速在200~300NM3/hm3,在保证电炉出口温度及升温速率的前提下,空速越大越好,全开放空阀,使系统压力越低越好。
4试送一组电炉,开始空气升温。
电炉出口温度及升温速率必须严格地按方案控制,温度不宜过高,升温速率不宜过快。
电炉出口温度及升温速率的控制方法是气量的变化和电炉功率的调节相配合,其操作首先保证大空速,其次是调节电炉功率。
5,尽可能地缩小触媒层的轴向温差,温差以50~80℃为妥。
120℃恒温主要是缩小触媒层轴向温差,有得于游离水缓慢地蒸发,以保证触媒的平稳温升和保护触媒的强度。
200℃恒温应将触媒层最低温度提至高于蒸汽漏点温度20℃以上,在系统压力为0.05~0.1MPa时,触媒最低温度应在120~130℃以上,为蒸汽置换作好温度上的准备。
浅谈变换催化剂和变换炉的选择

浅谈变换催化剂和变换炉的选择摘要:变换工艺根据所选用的催化剂是否耐硫,将变换工艺分为耐硫变换和非耐硫变换工艺。
变换反应的顺利进行主要取决于两方面的因素,催化剂和变换炉。
本文通过介绍不同类型变换催化剂和变换炉的发展、应用及优缺点,为广大化工同行在变换催化剂和变换炉的选择上提供帮助。
关键词:变换工艺;变换催化剂;变换炉1变换催化剂的选择通常使用的催化剂有高温变换催化剂、低温变换催化剂和宽温耐硫变换催化剂。
1.1高温变换催化剂高温变换催化剂其活性相是由Fe2O3部分还原得到的Fe3O4。
在实际应用过程中,高温烧结导致Fe3O4表面积下降,引起活性的急剧下降,造成纯Fe3O4的活性温区很窄,耐热性很差。
因此常加入结构助剂提高其耐热性,防止烧结引起的活性下降。
由于铁铬系高温变换催化剂中铬是剧毒物质,造成在生产、使用和处理过程中对人员和环境的污染及毒害,但工业化与应用业绩较少。
高温变换催化剂的粉化是它的一个主要问题。
催化剂的更换往往不是由于活性丧失,而是由于粉化造成过大的压差。
部分催化剂的粉化,引起气流不均匀,也将导致转化率下降。
蒸汽消耗较高,有最低水气比要求,要求变换入口水气比在1.4以上,变换后的水气比应大于0.8,导致过剩蒸汽冷凝量过多、能耗增加,不宜选用。
1.2低温变换催化剂低变催化剂的最大特点就是活性温度低,在200~260℃的范围内,变换反应就能迅速进行。
低变催化剂对硫化物极为敏感,由于生成铜盐而永久性中毒。
氯或氯离子也引起永久性中毒,这是由于催化剂发生结晶而引起的。
另外,原料气中的不饱和烃可能在催化剂表面析炭或结焦。
1.3宽温耐硫变换催化剂钴钼系耐硫宽温变换催化剂具有很高的低温活性,它比铁系高温变换催化剂起活温度低100~150℃,甚至在160℃就显示出优异的活性,与铜系低温变换催化剂相当,且其耐热性能与铁铬系高温变换催化剂相当,因此具有很宽的活性温区,几乎覆盖了铁系高温变换催化剂和铜系低温变换催化剂整个活性温区。
青岛联信催化材料有限公司QDB催化剂使用说明
QDB系列耐硫变换催化剂使用说明书青岛联信催化材料有限公司2006.12企业概况青岛联信催化材料有限公司(原青岛联信化学有限公司)位于青岛市胶州经济技术开发区,是一家集科研、生产、经营于一体的高新技术企业,是国内知名的耐硫变换催化剂专业生产厂家,与青岛科技大学联合建立了催化剂试验研究基地。
公司拥有多名业内知名专家、教授,以及一支科研力量雄厚的技术队伍,多年来与国内外知名大学和科研机构合作,开发出多项业内技术水平领先、具有自主知识产权的新产品和新工艺,并全面推向市场。
公司的各项产品和工艺先后获得国家发明专利和部级、省级科技进步奖二等奖、三等奖等十余项。
青岛联信催化材料有限公司(原青岛联信化学有限公司)占地33000平方米,具备年产3000吨的催化剂生产线,可以为用户提供催化剂、净化剂、脱硫剂和脱毒剂等30多种规格的系列产品。
其中,QDB系列耐硫变换催化剂的综合性能经业内知名专家评审后鉴定为已达到国际领先水平,该产品于2006年11月荣获中国石油和化学工业协会科学技术进步二等奖,已在国内多套煤气化制氨、制甲醇和城市煤气装置中得到成功的工业应用。
由公司开发的粉煤气化-低水/气耐硫变换新工艺于2010年10月15日荣获中国石油和化学工业联合会科技进步一等奖,该工艺操作灵活、运行安全平稳、节能效果显著,解决了高浓度CO原料气变换易发生甲烷化副反应和第一反应器深度难以控制的难题,实现了耐硫变换工艺的重大创新和突破,填补了国际空白,其综合技术处于国际领先水平。
青岛联信催化材料有限公司(原青岛联信化学有限公司)通过了ISO9001:2008质量管理体系认证,具有完善的质量控制体系;配有多种催化剂的分析、检测和评价方法,仪器设备和分析检测手段先进可靠;公司的技术服务队伍专业技术过硬、服务周到、信息反馈迅速,可以为用户做好使用前期、使用过程中等各个环节的各类技术服务。
面对竞争全球化的新形势,青岛联信催化材料有限公司(原青岛联信化学有限公司)始终以“联合创造财富,信誉成就伟业”为宗旨,坚持高科技、高质量和高水平技术服务的发展战略,不断挑战自我,为打造出业界名牌产品而持续创新。
甲醇装置操作规程 变换单元
变换单元操作规程第一章产品说明变换装置是煤气化的下游装置,其目的和作用是把粗煤气中过高的CO变换成CO2,同时副产H2,以调整粗煤气中CO和H2的含量,满足甲醇合成装置对氢碳比的要求。
来自煤气化装置的粗煤气经过三台变换炉变换后,变换气去低温甲醇洗装置。
装置运行期间,需要外界提供循环冷却水、锅炉给水、中压蒸汽、低压蒸汽、高压蒸汽、脱盐水、低压氮气、中压氮气、仪表空气、工厂空气。
生产过程中产生的变换冷凝液汇合冷却后送至污水处理系统。
1 生产能力变换装置对粗煤气的额定处理能力为241348.8Nm3/h,装置的操作弹性为50%至120%,粗煤气、变换气的组成和工艺参数情况如下表:表1 粗煤气的工艺参数表表2 变换气的工艺参数表2、物料消耗及能耗变换装置在生产过程中消耗变换催化剂QDB-04;催化剂在使用初期需要进行升温硫化还原,硫化剂采用纯品二硫化碳。
见下表:表3 化工原、辅材料消耗表表4 公用工程消耗表3、催化剂的特性表5:QDB-04催化剂物化性能表6:QXB-01吸附剂物化性能催化剂QDB-04有以下特点:(1)添加特殊助剂并使用活性载体,由于助剂、活性载体与活性组份三者的协同效应,提高了催化剂的变换活性,特别是提高了催化剂在高温低硫下的变换活性及活性稳定性。
(2)添加复合碱性物料,增强了催化剂的表面碱性,提高了催化剂的有机硫氢解和水解功能,特别是在反应温度较低的条件下,催化剂对有机硫的氢解和水解活性。
同时由于有机硫转化活性的提高,在原料气中H2S较低的情况下,能保持自身的硫化形态,从而可以提高催化剂的脱氧性能。
(3)添加抗水合助剂,减弱了Al2O3组份的水合反应能力,从而提高了催化剂的抗水合性能,使催化剂在压力较高的苛刻条件下使用时,不水合、不相变,具有较高的抗水合性和结构稳定性。
新鲜催化剂中活性组份钴、钼以氧化钴、氧化钼的形式存在,使用时要先进行硫化,使活性金属组份由氧化物转变成硫化物。
通常的硫化方法对QDB-04催化剂都适用,即:可以用含硫工艺气体硫化,也可用硫化剂单独硫化。
变换催化剂性能和控制工艺指标
QCS―11催化剂的技术性能介绍QCS―11是钴钼系一氧化碳耐硫变换催化剂,是我公司专门为高CO、高水气比研究开发的催化剂。
已经在两个壳牌气化工艺一变使用。
和QCS-03/QCS-01催化剂相比,耐热温度高、活性稳定性好、孔结构更加合理,另外,颗粒度均匀、装填效果好,能够有效的保证装填均匀、阻力减小。
镁-铝-钛三元尖晶石载体及特殊的加工制作工艺是确保QCS-11催化剂具备上述特性的基础和必备条件。
目前高CO、高水气比工艺包括壳牌炉气化、航天炉气化、GSP气化等,其中神华宁煤使用GSP是目前CO和水气比最高的工艺,对催化剂的要求也最高。
我公司的QCS系列催化剂采用镁-铝-钛三元载体、稀土助剂,其活性稳定性、工况适应性是最好的,在与国外、国内催化剂对比使用过程中得到很多验证,获得中国、美国、德国、日本、印度、南非等国家的专利。
QCS―11钴钼系一氧化碳耐硫变换催化剂,适用于以重油、渣油部分氧化法或煤气化法造气的变换工艺,促进含硫气体的变换反应,是一种适应宽温(220℃~550℃)、宽硫(工艺气硫含量≥0.01% v/v)和高水气比(0.2~2.0)。
该催化剂具有机械强度高,结构稳定性好,脱氧能力强等特点,能有效地脱除与吸附原料气中的氧和焦油等杂质或毒物。
对高空速,高水气比的适应能力强,稳定性好,操作弹性较大。
具有稳定的变换活性,可延长一氧化碳耐硫变换催化剂的使用寿命。
新鲜催化剂活性组份钴、钼以氧化钴、氧化钼的形式存在,使用时应首先进行硫化,使金属氧化物转变为硫化物。
可以用含硫工艺气体硫化,也可用硫化剂单独硫化。
QCS―11耐硫变换催化剂不含对设备和人体有危害的物质,硫化时也只有少量的水生成并随工艺气排出,对设备无危害。
主要特点为:●耐热温度高、活性稳定性好、孔结构更加合理。
●颗粒度均匀、装填效果好,能够有效的保证装填均匀、阻力减小。
●镁-铝-钛三元尖晶石载体及特殊的加工制作工艺是确保QCS-11催化剂具备独特性能的基础和必备条件。
一氧化碳变换
一氧化碳变换概述一氧化碳的变换是指煤气借助于催化剂的作用,在一定温度下,与水蒸气反应,一氧化碳生成二氧化碳和氢气的过程。
通过变换反应既除去了煤气中的一氧化碳,又得到了制取甲醇的有效气体氢气。
因此,变化工段既是转化工序,又是净化工序。
前工段来的煤气中,一氧化碳含量高,通过变换反应以后,要求达到工艺气体中的CO/H2约为2.05~2.1的关系,以满足甲醇合成的要求。
一氧化碳变换反应是在催化剂存在的条件下进行的,是一个典型的气固相催化反应。
60年代以前,变换催化剂普遍采用Fe-Gr催化剂,使用温度范围为350~550℃,60年代以后,开发了钴钼加氢转化催化剂和氧化锌脱硫剂,这种催化剂的操作温度为200~280℃,为了区别这两种操作温度不同的变换过程,习惯上将前者称为“中温变换”,后者称为“低温变换”。
按照回收热量的方法不同,变换又可分为激冷流程和废锅流程,冷激流程中,冷激后的粗原料气已被水蒸气饱和,在未经冷却和脱硫情况下直接进行变换,因此,两种流程按照工艺条件的不同选用不同的催化剂,激冷流程采用Co-Mo耐硫变换催化剂,废锅流程采用Fe-Cr变换催化剂。
第一节变换反应原理变换过程为含有C、H、O三种元素的CO和H2O共存的系统,在CO变换的催化反应过程中,除了主要反应CO+H2O=CO2+H2以外,在某种条件下会发生CO分解等其他副反应,分别如下:2CO=C+CO22CO+2H2=CH4+CO2CO+3H2=CH4+H2OCO2+4H2=CH4+2H2O这些副反应都消耗了原料气中的有效气体,生成有害的游离碳及无用的甲烷,避免副反应的最好方法就是使用选择性好的变换催化剂。
一、变换反应的热效应一氧化碳变换反应是一个放热反应,CO+H2O=CO2+H2+41kJ/gmol反应的热效应视H2O的状态而定,若为液态水,则是微吸热反应,若是水蒸气,则为放热反应。
变换反应的反应热随温度的升高而降低,具体反应热列表如下:表1 CO+H2O=CO2+H2的反应热温度℃25 200 250 300 350 400 450 500 550 △HkJ/gmol 41 39.8 39.5 39 38.5 38 37.6 37 36.6压力对变换反应的反应热影响较小,一般不做考虑。
- 1、下载文档前请自行甄别文档内容的完整性,平台不提供额外的编辑、内容补充、找答案等附加服务。
- 2、"仅部分预览"的文档,不可在线预览部分如存在完整性等问题,可反馈申请退款(可完整预览的文档不适用该条件!)。
- 3、如文档侵犯您的权益,请联系客服反馈,我们会尽快为您处理(人工客服工作时间:9:00-18:30)。
QCS― 11 催化剂的技术性能介绍QCS― 11 是钴钼系一氧化碳耐硫变换催化剂,是我公司专门为高CO、高水气比研究开发的催化剂。
已经在两个壳牌气化工艺一变使用。
和QCS-03/QCS-01催化剂相比,耐热温度高、活性稳定性好、孔结构更加合理,另外,颗粒度均匀、装填效果好,能够有效的保证装填均匀、阻力减小。
镁-铝-钛三元尖晶石载体及特殊的加工制作工艺是确保QCS-11 催化剂具备上述特性的基础和必备条件。
目前高CO、高水气比工艺包括壳牌炉气化、航天炉气化、GSP 气化等,其中神华宁煤使用GSP是目前CO 和水气比最高的工艺,对催化剂的要求也最高。
我公司的QCS 系列催化剂采用镁- 铝-钛三元载体、稀土助剂,其活性稳定性、工况适应性是最好的,在与国外、国内催化剂对比使用过程中得到很多验证,获得中国、美国、德国、日本、印度、南非等国家的专利。
QCS― 11 钴钼系一氧化碳耐硫变换催化剂,适用于以重油、渣油部分氧化法或煤气化法造气的变换工艺,促进含硫气体的变换反应,是一种适应宽温(220℃~550℃)、宽硫(工艺气硫含量≥0.01% v/v )和高水气比(0.2~2.0)。
该催化剂具有机械强度高,结构稳定性好,脱氧能力强等特点,能有效地脱除与吸附原料气中的氧和焦油等杂质或毒物。
对高空速,高水气比的适应能力强,稳定性好,操作弹性较大。
具有稳定的变换活性,可延长一氧化碳耐硫变换催化剂的使用寿命。
新鲜催化剂活性组份钴、钼以氧化钴、氧化钼的形式存在,使用时应首先进行硫化,使金属氧化物转变为硫化物。
可以用含硫工艺气体硫化,也可用硫化剂单独硫化。
QCS― 11 耐硫变换催化剂不含对设备和人体有危害的物质,硫化时也只有少量的水生成并随工艺气排出,对设备无危害。
主要特点为:耐热温度高、活性稳定性好、孔结构更加合理。
颗粒度均匀、装填效果好,能够有效的保证装填均匀、阻力减小。
镁-铝-钛三元尖晶石载体及特殊的加工制作工艺是确保QCS-11 催化剂具备独特性能的基础和必备条件。
抗水合性能好,适用高水气比:0.2-2.0,可耐5.0MPa 水蒸气分压。
耐热稳定性好,适合宽温变换:200-550℃。
适应高 CO 变换条件: CO 入口干基组成可达 75%。
容易硫化。
变换活性高,特别是低温、低硫变换活性。
机械强度高、选择性好、稳定性好。
对高空速和宽水气比适应能力强。
具有较强的吸灰和抗毒能力。
对 COS 和 HCN 有很强的加氢功能。
使用范围广:适用于各种气化流程,尤其是高 CO 高水气比的变换3.产品的使用3.1适用条件操作温度(℃) :200~ 550 操作压力( MPa ): 2.0~10.01、催化剂的物理化学性质1.1 物理性质 外观 外形尺寸( mm ): 堆密度( kg/l ): 径向抗压碎力( N/cm ): 比表面( m2/g )1.2 化学组成CoO (%): MoO 3(%): 助剂( %):载体:CO 变换活性( 350℃)2、产品质量指标 项目 抗压碎力( N/ 颗): CoO(%): MoO 3(%):兰绿色球形 直径 3.5~ 4.2 0.82~0.88 ≥ 200 ≥ 120 ≥ 3.5 ≥ 8.0 ≥5.0 TiO 2-MgO-Al 2O 3 三元尖晶石 ≥ 93% 指标 ≥ 200 ≥ 3.5运行空速(h-1): 1000~4000蒸汽/干气: 0.2~2.0预计使用寿命(a):2~6为了防止水汽冷凝,入口温度通常选择在高于水蒸汽露点温度25℃以上,随着使用时间的延长(当出口CO含量超标时),可逐渐提高入口温度,使出口CO 含量控制在要求范围内。
催化剂床层的热点温度不宜长时间超过500℃,否则将会缩短催化剂的使用寿命。
3.2催化剂的装填催化剂的装填质量直接关系到床层的气流分布,床层的阻力降及催化剂的使用性能,因此应十分重视装填工作。
1)为了保证装填质量,要选择晴朗天气,并避开油污、灰尘及化学物质污染。
2)装填催化剂前,应该认真检查反应器,确保清洁干净,支撑栅格牢固。
在炉内壁标出耐火球、钢丝网、篦子板和催化剂的装填线。
3)在装填之前,通常没有必要对催化剂进行筛选,但是在运输及装卸过程中,由于不正确作业可能使催化剂损坏,若发现磨损或破碎则应过筛。
4)首先向炉底装Ф 50mm的耐火球,装至预定高度。
其上再装Ф 25mm耐火球100~200mm 的高度,铺二层钢丝网,然后装催化剂。
5)将催化剂慢慢吊至炉顶,缓慢侄入接有帆布口袋的漏斗或溜槽中,催化剂从帆布袋口流入炉内。
炉内有人手握帆布袋口,不断移动下料口位置,使催化剂按水平面上升。
催化剂自由下落高度不得超过1米。
如炉内无人,则要分层装填,每层约0. 5m高催化剂,要整平之后再装下一层,防止疏密不均,在装填期间,如果需要在催化剂上走动,应垫上木板,使身体重量分散在木板上。
6)催化剂装好后,将表面耙平,覆盖两层钢丝网,再装入100~200mm 厚的拉西环或耐火球以及篦子板。
当确认催化剂装填质量合格,炉内无异物后封炉。
用空气或惰性气体吹扫至炉出口无粉尘为止。
7)为保证人身安全,在装填过程中的入炉人员需要配戴长管或过滤罐式防尘面具。
3.3 升温硫化首次开车升温时 ,为防止水蒸汽在催化剂上冷凝,应使用惰性气体(如空气或天然气, 最好是氮气)做为升温介质,当催化剂床层温度升至水蒸汽的露点温度以上时,可以改用 工艺气升温。
催化剂床层的升温速度可控制在 ≤ 50℃/h ,并根据可获得的最大的介质流量来设定压 力,以确保气体在催化剂床层上能有很好的流态分布。
在通常情况下, 气体的有效线速 应控制在设计值的 50~ 100%。
载气流量应保持在一次通过或循环操作时空速至少为 300h -1。
载气中氧含量应小于 0.05%。
当催化剂床层温度达到 200~ 220℃时,可转入硫化程序。
如选用空气做升温介质,在导入硫化气之前必须用氮气或水蒸汽吹扫系统,以置换残余氧气。
常用的硫化剂有 H 2S 、CS 2 和 COS ,硫化反应可用下式表式:ΔH 0298= ― 13.4KJ/mol可以看出,反应( 3)发生时,要产生大量的热。
因此,如果用 CS 2 来硫化催化剂, 应控制加料速度,以防止催化剂床层超温。
温度达 200℃时, CS 2 的氢解才具有较大的转 化率。
硫化时,硫的加入量一般根据催化剂中的活性组份完全硫化来计算, QCS-01 催化剂 每 1000kg 约需 55kg 硫,加硫速度依催化剂床层温升情况而定。
由反应器出口 H 2S 含量大 大增加并与入口含量平衡来确定硫化结束。
温度大于 200℃时,硫化反应就以足够快的速度进行,选用天然气或氮气加热催化剂 时应加入 5~10%氢气,以利于 CS 2 氢解。
硫化时,催化剂床层 ΔT 不超过 30℃。
硫化结 束时,将温度慢慢提升到规定的变换入口温度,一般不必要超过 300℃。
下面列出了循环氮气、工艺气一次通过的升温硫化程序供选择 1) CoO+H 2S CoS+H 2O MoO 3+2H 2S+H 2MoS 2+3H 2O ΔH 0298= ― 48.1KJ/mol 2) CS 2+ 4H 2 2H 2S+CH 4 ΔH 0298= ― 240.6KJ/mol 3)COS+H 2O CO 2+H 2SΔH 0298= ― 35.2KJ/mol 4)3.3.1 用循环氮气硫化1)用氮气彻底置换循环回路,并检查回路中无其它工艺气体漏入的可能。
2)通过变换炉的循环氮气应保持稳定的压力(一般0.5~1.5 MPa),以提供合适的空速,此值最好能高于300 h-1。
3)催化剂从室温开始升温,适宜的升温速度是每小时25℃,当入口温度升到120℃时恒温4~6 小时,以脱除催化剂中吸附的物理水,同时分离器注意排水,然后再继续升温至200~220℃,恒温3~4 小时拉平床层温度。
4)当床层的温度都稳定在200~220℃以后,把氢气加到氮气中,控制反应器入口温度在200℃~220℃,分析变换炉入口氢气含量10~20%左右(进出口气体分析1 次/小时)。
5)二硫化碳贮槽加装二硫化碳后,打开二硫化碳贮槽的氮气(钢瓶氮)入口给二硫化碳贮槽充压,用背压阀控制压力大于系统压力0.2MPa~0.3MPa 时,稍开二硫化碳贮槽出口阀门,将少量二硫化碳压入系统,系统控制床层温升△T<30℃/hr,如床层温度上升过快,可减少或停止加入二硫化碳,同时加大N2 量,至床层温度冷却到250℃后再加入二硫化碳。
6)根据催化剂床层温度控制二硫化碳的加入量,一般控制二硫化碳的含量在0.2%~1.0%左右,在变换炉的进出口分析H2S 含量来确定。
7)硫化过程中入口温度维持在200℃~220℃,床层热点温度<350℃。
由于二硫化碳氢解产生一定的甲烷,循环系统要保持一定量的弛放气。
8)当出口有硫穿透催化剂床层时,逐步提高硫化压力至1.0MPa,提高入口温度继续硫化,当入口温度230℃~260℃时,热点温度300~320℃,变换炉出口有硫穿透,并且硫含量与进口硫含量基本持平,保持3 小时以上不再变化时,可认为硫化结束。
9)若串联几个反应器,当第一反应器的催化剂床层有硫穿透时,要注意调整第二反应器的入口温度200-220℃继续硫化。
整个硫化期间,应保持温度稳定,并且温升ΔT不应超过30℃。
10)硫化结束后,关闭二硫化碳入系统的阀门,二硫化碳贮槽泄压,回收剩余的二硫化碳;关闭补氮气阀、补氢气阀,停开工加热器高压蒸汽,停压缩机,开放空阀泄压。
11)变换系统用氮气置换合格,以10~15℃/h 的速度把入口温度提高到规定的反应温度。
然后将原料气送入催化剂床层,慢慢地把压力和温度调整到设计值。
在这个阶段,应该一直小心保持流速,并且根据压力调节气体流量。
注意催化剂上的气体有效线速度不超过设计值。
每个反应器的催化剂床层温度都必须保持在高于水蒸汽露点温度25℃以上。
3.3.2 用工艺气硫化采用工艺气一次通过法硫化催化剂,尤其是在较高压力下,应该注意存在甲烷化反应的可能。
为了防止此反应发生,或者已经发生了此反应,应通过控制温度来限制(一般当温度高于400℃时,甲烷化反应才会明显发生)。
1)硫化前,应该用氮气吹净反应器。
2)按4.4.1 所述升温程序用氮气升温到200~220℃,然后,把湿工艺气加到氮气中(比例:湿工艺气:氮气=1:3)一起进入反应器,并保持温度和压力。
采用工艺气作原料,由于气体混合物中,氢气分压、CO 分压低,甲烷化反应的可能性很小,万一发生此反应导致超温时,可通过减少或切断工艺气,用氮气将催化剂床层冷却到250℃左右,再慢慢地加入湿工艺气继续硫化。
3)当催化剂床层温度稳定时,将湿工艺气流量增加一倍。
同时相应减少氮气,目的是使气体的线速度不超过允许值,此时气体的比率为:工艺气:氮气=1.0~1.5。