拔模角度的深度分析
铸造拔模角度
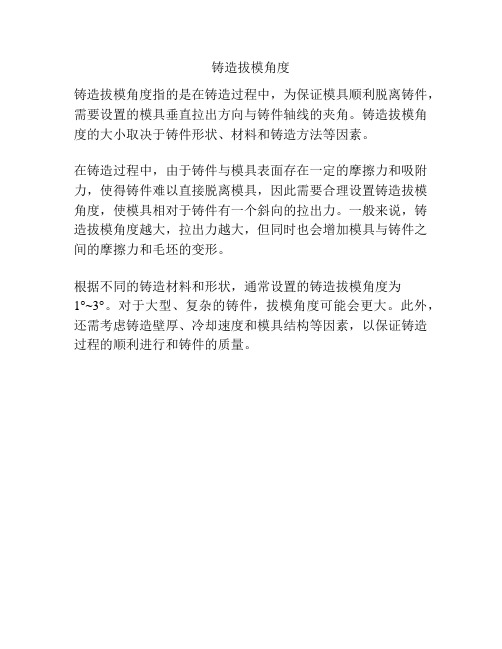
铸造拔模角度
铸造拔模角度指的是在铸造过程中,为保证模具顺利脱离铸件,需要设置的模具垂直拉出方向与铸件轴线的夹角。
铸造拔模角度的大小取决于铸件形状、材料和铸造方法等因素。
在铸造过程中,由于铸件与模具表面存在一定的摩擦力和吸附力,使得铸件难以直接脱离模具,因此需要合理设置铸造拔模角度,使模具相对于铸件有一个斜向的拉出力。
一般来说,铸造拔模角度越大,拉出力越大,但同时也会增加模具与铸件之间的摩擦力和毛坯的变形。
根据不同的铸造材料和形状,通常设置的铸造拔模角度为
1°~3°。
对于大型、复杂的铸件,拔模角度可能会更大。
此外,还需考虑铸造壁厚、冷却速度和模具结构等因素,以保证铸造过程的顺利进行和铸件的质量。
塑胶产品模具的拔模角度确定(一)
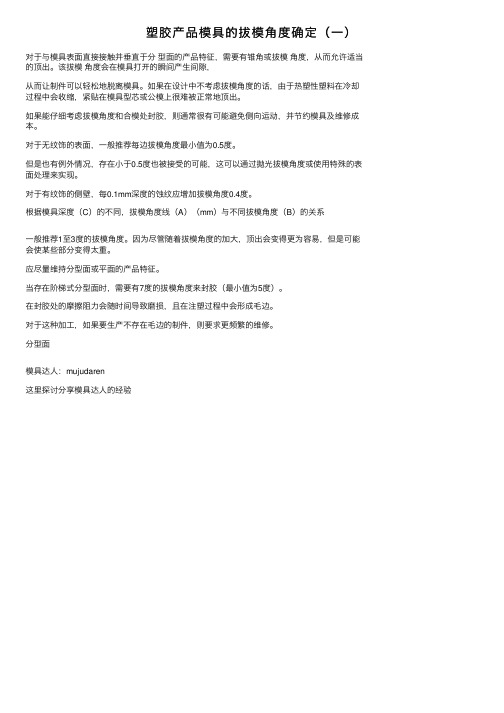
塑胶产品模具的拔模⾓度确定(⼀)
对于与模具表⾯直接接触并垂直于分型⾯的产品特征,需要有锥⾓或拔模⾓度,从⽽允许适当的顶出。
该拔模⾓度会在模具打开的瞬间产⽣间隙,
从⽽让制件可以轻松地脱离模具。
如果在设计中不考虑拔模⾓度的话,由于热塑性塑料在冷却过程中会收缩,紧贴在模具型芯或公模上很难被正常地顶出。
如果能仔细考虑拔模⾓度和合模处封胶,则通常很有可能避免侧向运动,并节约模具及维修成本。
对于⽆纹饰的表⾯,⼀般推荐每边拔模⾓度最⼩值为0.5度。
但是也有例外情况,存在⼩于0.5度也被接受的可能,这可以通过抛光拔模⾓度或使⽤特殊的表⾯处理来实现。
对于有纹饰的侧壁,每0.1mm深度的蚀纹应增加拔模⾓度0.4度。
根据模具深度(C)的不同,拔模⾓度线(A)(mm)与不同拔模⾓度(B)的关系
⼀般推荐1⾄3度的拔模⾓度。
因为尽管随着拔模⾓度的加⼤,顶出会变得更为容易,但是可能会使某些部分变得太重。
应尽量维持分型⾯或平⾯的产品特征。
当存在阶梯式分型⾯时,需要有7度的拔模⾓度来封胶(最⼩值为5度)。
在封胶处的摩擦阻⼒会随时间导致磨损,且在注塑过程中会形成⽑边。
对于这种加⼯,如果要⽣产不存在⽑边的制件,则要求更频繁的维修。
分型⾯
模具达⼈:mujudaren
这⾥探讨分享模具达⼈的经验。
冲压工艺中 拔模角定义

冲压工艺中拔模角定义拔模角是冲压工艺中的一个重要概念,它是指在冲压过程中,模具在脱模时与冲压件分离的角度。
拔模角的大小直接影响着冲压件的成形质量和模具的寿命,因此合理定义和控制拔模角至关重要。
拔模角的定义可以从两个方面来考虑:一是从理论角度,二是从实际操作角度。
从理论角度来看,拔模角是指模具在脱模时与冲压件分离的角度。
在冲压过程中,当冲头下降压入工件后,随着冲头的上升,模具需要与冲压件分离,这个过程就是拔模。
拔模角的大小取决于模具设计和冲压件的形状。
一般来说,拔模角越大,冲压件的脱模越容易,但模具的寿命也会相应减少。
相反,拔模角越小,模具的寿命会增加,但脱模困难度也会增加。
从实际操作角度来看,拔模角是指在冲压过程中,模具设计师和操作工根据冲压件的材料、形状和尺寸等因素,在模具设计和调试过程中确定的一个角度值。
这个角度值一般通过试模和实际生产中的经验总结得出。
在模具设计中,拔模角需要考虑到冲压件的脱模要求、模具的结构和材料、冲压机的性能等因素,以确保冲压件能够顺利脱模,并且保证模具的寿命。
拔模角的大小对冲压件的成形质量和模具的寿命有着直接的影响。
如果拔模角过大,容易导致冲压件在脱模过程中变形或损坏,同时还会增加模具的磨损和疲劳,降低模具的使用寿命。
如果拔模角过小,可能导致冲压件无法完全脱模,从而影响冲压件的质量和尺寸精度。
因此,合理定义和控制拔模角对于冲压工艺的稳定性和高效性至关重要。
在实际操作中,设计师和操作工需要根据具体情况来确定拔模角的大小。
首先,需要考虑冲压件的材料和形状。
对于硬度较高或形状复杂的冲压件,一般需要较大的拔模角来保证脱模的顺利进行。
其次,需要考虑模具的结构和材料。
模具的设计和制造应考虑到拔模角的大小,以确保模具的寿命和稳定性。
最后,还需要考虑冲压机的性能和调试过程中的实际情况。
通过试模和不断调整拔模角的大小,可以找到最合适的拔模角值,以确保冲压件的成形质量和模具的寿命。
拔模角是冲压工艺中的一个重要概念,它的大小直接影响着冲压件的成形质量和模具的寿命。
拔模角度的深度分析
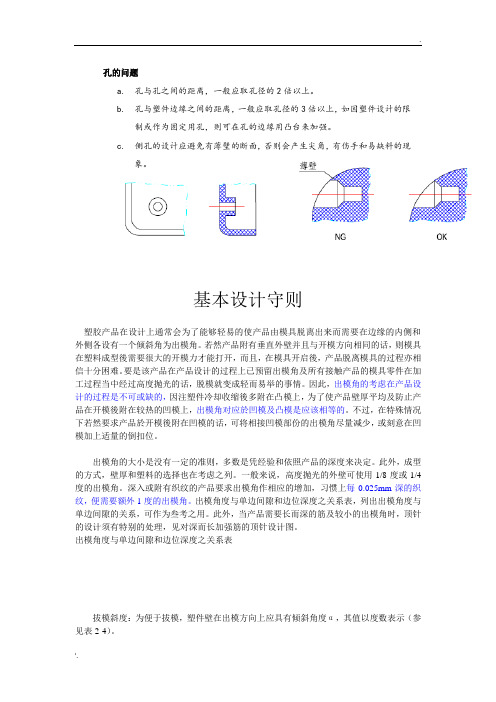
孔的问题a. 孔与孔之间的距离,一般应取孔径的2倍以上。
b. 孔与塑件边缘之间的距离,一般应取孔径的3倍以上,如因塑件设计的限制或作为固定用孔,则可在孔的边缘用凸台来加强。
c. 侧孔的设计应避免有薄壁的断面,否则会产生尖角,有伤手和易缺料的现象。
基本设计守则塑胶产品在设计上通常会为了能够轻易的使产品由模具脱离出来而需要在边缘的内侧和外侧各设有一个倾斜角为出模角。
若然产品附有垂直外壁并且与开模方向相同的话,则模具在塑料成型後需要很大的开模力才能打开,而且,在模具开启後,产品脱离模具的过程亦相信十分困难。
要是该产品在产品设计的过程上已预留出模角及所有接触产品的模具零件在加工过程当中经过高度抛光的话,脱模就变成轻而易举的事情。
因此,出模角的考虑在产品设计的过程是不可或缺的,因注塑件冷却收缩後多附在凸模上,为了使产品壁厚平均及防止产品在开模後附在较热的凹模上,出模角对应於凹模及凸模是应该相等的。
不过,在特殊情况下若然要求产品於开模後附在凹模的话,可将相接凹模部份的出模角尽量减少,或刻意在凹模加上适量的倒扣位。
出模角的大小是没有一定的准则,多数是凭经验和依照产品的深度来决定。
此外,成型的方式,壁厚和塑料的选择也在考虑之列。
一般来说,高度抛光的外壁可使用1/8度或1/4度的出模角。
深入或附有织纹的产品要求出模角作相应的增加,习惯上每0.025mm深的织纹,便需要额外1度的出模角。
出模角度与单边间隙和边位深度之关系表,列出出模角度与单边间隙的关系,可作为叁考之用。
此外,当产品需要长而深的筋及较小的出模角时,顶针的设计须有特别的处理,见对深而长加强筋的顶针设计图。
出模角度与单边间隙和边位深度之关系表拔模斜度:为便于拔模,塑件壁在出模方向上应具有倾斜角度α,其值以度数表示(参见表2-4)。
3.1拔模斜度确定要点(1) 制品精度要求越高,拔模斜度应越小。
(2) 尺寸大的制品,应采用较小的拔模斜度。
(3) 制品形状复杂不易拔模的,应选用较大的斜度。
拔模斜度 斜率
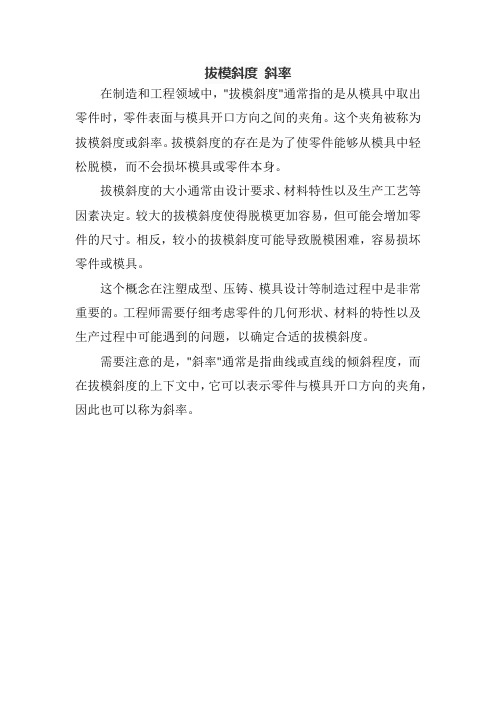
拔模斜度斜率
在制造和工程领域中,"拔模斜度"通常指的是从模具中取出零件时,零件表面与模具开口方向之间的夹角。
这个夹角被称为拔模斜度或斜率。
拔模斜度的存在是为了使零件能够从模具中轻松脱模,而不会损坏模具或零件本身。
拔模斜度的大小通常由设计要求、材料特性以及生产工艺等因素决定。
较大的拔模斜度使得脱模更加容易,但可能会增加零件的尺寸。
相反,较小的拔模斜度可能导致脱模困难,容易损坏零件或模具。
这个概念在注塑成型、压铸、模具设计等制造过程中是非常重要的。
工程师需要仔细考虑零件的几何形状、材料的特性以及生产过程中可能遇到的问题,以确定合适的拔模斜度。
需要注意的是,"斜率"通常是指曲线或直线的倾斜程度,而在拔模斜度的上下文中,它可以表示零件与模具开口方向的夹角,因此也可以称为斜率。
拔模斜度标准
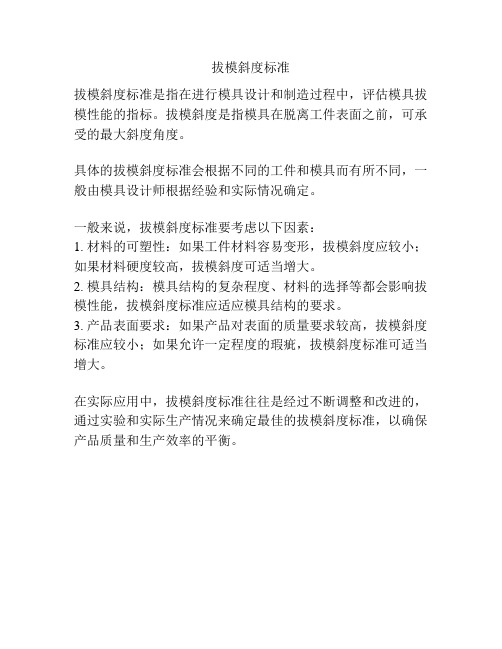
拔模斜度标准
拔模斜度标准是指在进行模具设计和制造过程中,评估模具拔模性能的指标。
拔模斜度是指模具在脱离工件表面之前,可承受的最大斜度角度。
具体的拔模斜度标准会根据不同的工件和模具而有所不同,一般由模具设计师根据经验和实际情况确定。
一般来说,拔模斜度标准要考虑以下因素:
1. 材料的可塑性:如果工件材料容易变形,拔模斜度应较小;如果材料硬度较高,拔模斜度可适当增大。
2. 模具结构:模具结构的复杂程度、材料的选择等都会影响拔模性能,拔模斜度标准应适应模具结构的要求。
3. 产品表面要求:如果产品对表面的质量要求较高,拔模斜度标准应较小;如果允许一定程度的瑕疵,拔模斜度标准可适当增大。
在实际应用中,拔模斜度标准往往是经过不断调整和改进的,通过实验和实际生产情况来确定最佳的拔模斜度标准,以确保产品质量和生产效率的平衡。
铸件拔模斜度介绍
根据生产环境和设备条件选择合适的拔模斜度
手工脱模
对于手工脱模的生产环境,由于工人操作时力度不易控制,需要较大的拔模斜度以减小 脱模阻力。一般拔模斜度在3°-5°之间。
机械脱模
对于机械脱模的生产环境,由于机械设备的力度和精度易于控制,可以减小拔模斜度。 一般拔模斜度在2°-4°之间。
05
铸件拔模斜度的测量与控制
采用目视检查、测量检查等多种方 法,确保铸件拔模斜度符合要求。
检查结果处理
对于不符合要求的铸件,及时采取 措施进行修正或报废处理,防止不 合格品流入下一道工序。
06
铸件拔模斜度对铸件质量的影响
拔模斜度对铸件尺寸精度的影响
拔模斜度是铸造过程中为了便于从模具中取出 铸件而设计的斜度,它对铸件的尺寸精度有直 接影响。
03
铸件拔模斜度的应用场景
金属铸造
金属铸造是使用金属材料通过熔炼和模具成型的过程,制造出各种形状和尺寸的 铸件。在金属铸造过程中,拔模斜度通常用于防止铸件粘附在模具上,以确保顺 利脱模。
拔模斜度的角度取决于铸件的材料、模具表面处理和铸造工艺等因素。一般来说 ,金属铸造的拔模斜度角度较大,以增加脱模的可靠性。
适当的拔模斜度有助于减少铸
砂型铸造
砂型铸造是一种使用砂型模具的铸造方法,适用于生产各种 复杂形状的铸件。在砂型铸造中,拔模斜度主要用于防止铸 件与砂型表面粘结,以确保铸件能够顺利从砂型中取出。
砂型铸造的拔模斜度角度通常较小,因为砂型表面的粗糙度 较高,需要较小的角度才能有效防止粘结。
玻璃铸造
玻璃铸造是一种使用热熔玻璃成型的方法,用于制造各种 玻璃制品。在玻璃铸造过程中,拔模斜度主要用于防止玻 璃制品与模具表面粘结。
适当的拔模斜度可以保证铸件尺寸的稳定性, 减小铸件与模具之间的摩擦,提高模具的使用 寿命。
讨论拔模角度
讨论拔模角度讨论一下拔摸斜度,请发表高见,多大的产品需要多大的拔摸斜度。
请大家举例说明。
拔摸斜度和产品的深度有关系.看你要达到什么目的了.而且对于产品外观的拔摸斜度和产品的表面处理有关系.相同的深度,表面咬花需要的拔摸斜度比光面要大. 而BOSS柱和加强肋就不是要求很严,以容易脱模和不缩水为原则.我们外形一般用1~2度左右以下是我的经验值:电视产品缺省的斜度是1:40,前壳为1.5度(我刚做了一个2度的)。
后盖因为牵扯到皮纹,如果深度不大(小于30毫米),一般不等小于3度。
深度较大,一般不小于6~8度。
至于有什么理论公式,还请版主赐教这个话题刚好我在别的论坛上发表过先转贴过来了:「拔模角」这个问题对机构人员来说,是个非常重要的课题 .什么情况要画拔模斜度?什么情况不需要斜度?外观斜度要多少?补强肋,螺丝驻斜度要多少?真的都需要经验,及和模具设计人员讨论对机构人员来说,不要画拔模角是最好的因为在画所有的结构时,标尺寸的参考只有「一条线」加了斜度后,正式图看起来就有「二条线」万一选错条,以后就麻烦了(有经验的人应该听的懂吧!)提供一下个人的经验:拔模斜度可以在所有的结构都完成后,再来一次画出来一方面可以避免出错一方面可以加快软件运算的速度.其实一个负责任的机构人员 .应该是要把「该有」的「所有拔模斜度」都画出来 .如果你把这项工作交给模具设计人员来画的时候 .他怎么知道你哪些地方是做「紧配合」,哪些有「间隙」?而且拔模基准面应该是以「底部」,还是「顶部」为准呢?一旦「猜错」了,有可能成品就会有干涉了 .还有有些比较高,比较深的结构是做「入子」的以及有些螺丝孔是做「套筒」的那时需不需要做斜度,那里不需要做斜度就要跟模具人员好好讨论了「拔模斜度」这个话题还有很多可以讨论的常常为了这个问题会让模具设计人员对机构设计人员有很大的抱怨这个可以多听听版上那些模具设计人员的心声一般我的经验是:能不作斜度的尽量不作!原则是:1、作模具的时候容易加的!2、作大作小关系不大的!外观的如果是出模方向的,斜度一定要作!如果是行位上出的,可以作直的!一些柱子、筋等,如果不是很深也不作!需要配合的,斜度一定要作!斜度的大小一般根据蚀纹的型号,有具体的数值,可以查的!基本全是经验值,要考虑模具的制作方法!。
讨论拔模角度.
討論拔模角度不同材料的设计要点: ABS 一般应用边0.5°至1°就足够。
有时因为抛光纹路与出模方向相同,出模角可接近至零。
有纹路的侧面需每深0.025mm(0.001 in)增加1°出模角。
正确的出模角可向蚀纹供应商取得。
LCP 因为液晶共聚物有高的模数和低的延展性,倒扣的设计应要避免。
在所有的肋骨、壁边、支柱等凸出膠位以上的地方均要有最小0.2-0.5°的出模角。
若壁边比较深或没有磨光表面和有蚀纹等则有需要加额外的0.5-1.5°以上。
PBT 若部件表面光洁度好,需要1/2°最小的脱模角。
经蚀纹处理过的表面,每增加0.03mm(0.001 in)深度就需要加大1°脱模角。
PC 脱模角是在部件的任何一边或凸起的地方要有的,包括上模和下模的地方。
一般光华的表面1.5°至2°已很足够,然而有蚀纹的表面是要求额外的脱模角,以每深0.25mm(0.001 in)增加1°脱模角。
PET 塑胶成品的肋骨,支柱边壁、流道壁等,如其脱模角能够达到0.5°就已经足够。
PS 0.5°的脱模角是极细的,1°的脱模角是标准方法,太小的脱模角会使部件难于脱离模腔。
无论如何,任何的脱模角总比无角度为佳。
若部件有蚀纹的话,如皮革纹的深度,每深0.025mm就多加1°脱模角。
讨论一下拔摸斜度,请发表高见,多大的产品需要多大的拔摸斜度。
请大家举例说明。
拔摸斜度和产品的深度有关系.看你要达到什么目的了.而且对于产品外观的拔摸斜度和产品的表面处理有关系.相同的深度,表面咬花需要的拔摸斜度比光面要大. 而BOSS柱和加强肋就不是要求很严,以容易脱模和不缩水为原则. 我们外形一般用1~2度左右以下是我的经验值:电视产品缺省的斜度是1:40,前壳为1.5度(我刚做了一个2度的)。
后盖因为牵扯到皮纹,如果深度不大(小于30毫米),一般不等小于3度。
产品的拔模角度
產品的拔模角度
∙產品的拔模角度(Drafts)主要幫助從模具中取出成品。
拔模角度的多寡必須考量產品深度與產品的功能。
∙拔模角主要是平行於模具的開關動作方向。
若是可能拔模角應該要儘可能大。
正常的拔模角度為1~2度,而
肋則可選擇0.5度的拔模角,若深度不超過12.5mm(0.5inch),且
將需要拔模角的地方拋光,則可以使用很小的拔模角。
若有咬花時
每千分之一深的咬花加上1~1.5度的拔模角。
咬花時所需的最小拔
模角度與成品的材料收縮率,壁厚與咬花種類有關。
∙若是需要完全沒有拔模角則要考慮使用側向移動開模,如滑塊。
- 1、下载文档前请自行甄别文档内容的完整性,平台不提供额外的编辑、内容补充、找答案等附加服务。
- 2、"仅部分预览"的文档,不可在线预览部分如存在完整性等问题,可反馈申请退款(可完整预览的文档不适用该条件!)。
- 3、如文档侵犯您的权益,请联系客服反馈,我们会尽快为您处理(人工客服工作时间:9:00-18:30)。
孔的问题
a. 孔与孔之间的距离,一般应取孔径的2倍以上。
b. 孔与塑件边缘之间的距离,一般应取孔径的3倍以上,如因塑件设计的限
制或作为固定用孔,则可在孔的边缘用凸台来加强。
c. 侧孔的设计应避免有薄壁的断面,否则会产生尖角,有伤手和易缺料的现
象。
基本设计守则
塑胶产品在设计上通常会为了能够轻易的使产品由模具脱离出来而需要在边缘的内侧和外侧各设有一个倾斜角为出模角。
若然产品附有垂直外壁并且与开模方向相同的话,则模具在塑料成型後需要很大的开模力才能打开,而且,在模具开启後,产品脱离模具的过程亦相信十分困难。
要是该产品在产品设计的过程上已预留出模角及所有接触产品的模具零件在加工过程当中经过高度抛光的话,脱模就变成轻而易举的事情。
因此,出模角的考虑在产品设计的过程是不可或缺的,因注塑件冷却收缩後多附在凸模上,为了使产品壁厚平均及防止产品在开模後附在较热的凹模上,出模角对应於凹模及凸模是应该相等的。
不过,在特殊情况下若然要求产品於开模後附在凹模的话,可将相接凹模部份的出模角尽量减少,或刻意在凹模加上适量的倒扣位。
出模角的大小是没有一定的准则,多数是凭经验和依照产品的深度来决定。
此外,成型的方式,壁厚和塑料的选择也在考虑之列。
一般来说,高度抛光的外壁可使用1/8度或1/4度的出模角。
深入或附有织纹的产品要求出模角作相应的增加,习惯上每0.025mm深的织纹,便需要额外1度的出模角。
出模角度与单边间隙和边位深度之关系表,列出出模角度与单边间隙的关系,可作为叁考之用。
此外,当产品需要长而深的筋及较小的出模角时,顶针的设计须有特别的处理,见对深而长加强筋的顶针设计图。
出模角度与单边间隙和边位深度之关系表
拔模斜度:为便于拔模,塑件壁在出模方向上应具有倾斜角度α,其值以度数表示(参见表2-4)。
3.1拔模斜度确定要点
(1) 制品精度要求越高,拔模斜度应越小。
(2) 尺寸大的制品,应采用较小的拔模斜度。
(3) 制品形状复杂不易拔模的,应选用较大的斜度。
(4) 制品收缩率大,斜度也应加大。
(5) 增强塑料宜选大斜度,含有自润滑剂的塑料可用小斜度。
(6) 制品壁厚大,斜度也应大。
(7) 斜度的方向。
内孔以小端为准,满足图样尺寸要求,斜度向扩大方向取得;外形则以大端为准,满足图样要求,斜度向偏小方向取得。
一般情况下拔模斜度。
可不受制品公差带的限制,高精度塑件的拔模斜度则应当在公差带内。
拔模斜度α值可按表2-4选取。
由表中可以看出,塑料硬脆、刚性大的,拔模斜度要求大。
具备以下条件的型芯,可采用较小的拔模斜度:
(1) 顶出时制品刚度足够。
(2) 制品与模具钢材表面的摩擦系数较低。
(3) 型芯表面的粗糙度值小,抛光方向又与制品的拔模方向—致。
(4) 制品收缩量小,滑动摩擦力小。
不同材料的设计要点
ABS
一般应用边0.5°至1°就足够。
有时因为抛光纹路与出模方向相同,出模角可接近至零。
有纹路的侧面需每深0.025mm(0.001 in)增加1°出模角。
正确的出模角可向蚀纹供应商取得。
LCP
因为液晶共聚物有高的模数和低的延展性,倒扣的设计应要避免。
在所有的筋、壁边、支柱等凸出膠位以上的地方均要有最小0.2-0.5°的出模角。
若壁边比较深或没有磨光表面和有蚀纹等则有需要加额外的0.5-1.5°以上。
PBT
若部件表面光洁度好,需要1/2°最小的脱模角。
经蚀纹处理过的表面,每增加0.03mm (0.001 in)深度就需要加大1°脱模角。
PC
脱模角是在部件的任何一边或凸起的地方要有的,包括上模和下模的地方。
一般光滑的表面1.5°至2°已很足够,然而有蚀纹的表面是要求额外的脱模角,以每深0.25mm(0.001 in)增加1°脱模角。
PET
塑胶成品的筋,支柱边壁、流道壁等,如其脱模角能够达到0.5°就已经足够。
PS
0.5°的脱模角是极细的,1°的脱模角是标准方法,太小的脱模角会使部件难于脱离模腔。
无论如何,任何的脱模角总比无角度为佳。
若部件有蚀纹的话,如皮革纹的深度,每深0.025mm 就多加1°脱模角。
3.2 制品拔模斜度设计
1.箱体与盖类制品(图2-1)
当H ≤50mm 时,S/H=1/30~1/50
当50<H ≤100mm 时,S/H ≤1/60
2.格子板形制品(图2-2)
当格子的间距P ≤4mm 时,拔模斜度α=1/10P 。
格子C 尺寸越大,拔模斜度越大。
当格子高度H 超过8mm ,拔模斜度不能取太大值时,可采用图(b)的形式,使一部分进入动模一侧,从而使拔模斜度满足要求。
3.带加强筋类制品(图2-3)
)200/1~500/1(2arctg H
B A arctg =-=α A=(1.0~1.8)T mm ;B=(0.5~0.7)T mm
4.底筋类制品(图2-4)
)100/1~150/1(2arctg H B A arctg =-=α A=(1.0~1.8)T mm ;B=(0.5~0.7)T mm
5.凸台类制品(图2-5、表2-5)
)20/1~30/1(2'arctg H
D D arctg =-=α 高凸台制品(H >30mm )的拔模斜度:
型芯:)30/1~50/1(2'arctg H
d d arctg
=-=α 型腔:)50/1~100/1(2'arctg H D D arctg =-=α 型芯的拔模斜度应大于型腔。
6.最小拔模斜度(表2-6)
拔模斜度影响制品的脱出情况。
如果拔模斜度很小,拔模阻力增大,顶出机构就会失去作用。
在一般情况下,不能小于最小拔模斜度,以防止制品留模。