脱模力计算
第10讲 脱模机构设计
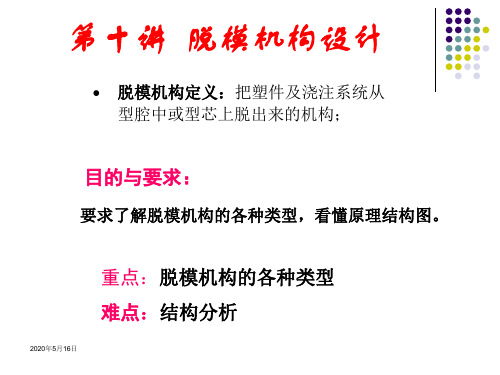
二级推出机构产生的原因
由于特殊形状或自动化生产的需要, 在一次脱模动作完成后,仍难于从 型腔中取出或不能自动脱落。
有时为避免一次脱模塑件受力过大,也采用二次脱模推出, 以保证塑件质量。
2013年7月14日
1.弹簧式二级推出机构
这种方法结构简单,装 配后所占面积小,缺点 是动作不可靠,弹簧容 易失效,需要及时更换。
2013年7月14日
2.斜楔滑块式二次推出机构
8-14斜楔滑块式二次推出机构 1- 动模座板 2-推板 3-弹簧 4-滑块 5-销钉 6-斜楔; 7-推件板 8-推杆 9-型芯 10-中心推杆 11-复位杆
2013年7月14日
3.三角滑块式二级推出机构
图8-15 三角滑块式二次推出机构 1- 一次推板 2- 三角滑块 3- 二次推板 4-推杆固定板 5-斜楔杆 6-推杆 7-动模型腔板 8-型芯 9-推杆
2013年7月14日
1.推杆推出机构
(1)推出机构组成: 推杆、拉料杆、复位杆、推杆固定板、推杆垫板、
推杆导柱、推杆导套、限位钉。
2013年7月14日
(2)推杆的设计
• • 适用范围:脱模阻力小的简单塑件 特点:简单、灵活,但与塑件接触面积小,易将 塑件顶变形或损坏。
推杆的形状及尺寸 推杆的固定及装配 推杆推出位置的选择
(四)螺纹塑件推出机构
手动脱螺纹机构
模内手动脱螺纹机构 齿轮齿条脱螺纹机构 直角式注射机脱螺纹机构 推杆轴承旋转式脱出机构
2013年7月14日
1.手动脱螺纹机构
2013年7月14日
手动脱螺纹机构
2013年7月14日
手动脱螺ቤተ መጻሕፍቲ ባይዱ机构
2013年7月14日
2.模内手动脱螺纹机构
第四章 推出机构的设计6

•
压缩空气配合推板脱模
• 设置引气装置以后:
4. 推块推出机构 平板状带凸缘的塑件,如 用推板件推出会黏附模具 时,则应使用推块推出机 构推出,如图所示。推块 是型腔的组成部分,因此 应有较高的硬度和较低的 表面粗糙度值,推块与型 腔及型芯应有良好的间隙 配合,既要求滑动灵活, 又不允许溢料。推块所使 用的推杆与模板不必要求 精度很高的配合。
难,同时因增加推件板而使模具质量增加。12
为减少脱模过程中推件板与 型芯之间的摩擦,两者之间 留有0.2~ 0.25mm的间隙, 并采用锥面配合,以防止推 件板 偏斜溢料,锥面的斜 度约取3~5˚左右,
4
推件板推出机构形式-4zzzzz 对于大型深腔的容器,尤其是采用软质塑料时, 如果用推件板脱模,应考虑附设引气装置,以防止在 脱模过程中内腔形成真空,造成脱模困难,甚至使塑 件变形损坏(见下图)。
(4)推管外径应比塑件外壁尺寸小0.5mm左右;推管内 径比塑件内径每边大0.2 ~0.5mm。 (5)推管与型芯的配合长度比推出行程S长3~5 mm,推 管与模板的配合长度一般为(1.5~2)D;其余部分扩 孔,推管扩孔d+l,模板扩孔D十1。推管的厚度一般取 1.5 ~5mm,以保证刚性。
• 3. 推件板推出机 构 • 深腔薄壁的容器、 壳体形塑件以及 不允许有推杆痕 迹的塑件都可采 用推件板推出机 构。推件板推出 机构的结构形式 与原理如图所示。
2、影响塑件脱模力的因素: 1) 脱模力的大小主要与塑件包络型芯侧面积的大小有关 2)脱模力大小与型芯的脱模斜度有关 脱模斜度越大,脱模力越小。 3) 脱模力的大小与型芯的表面粗糙度有关 表面粗糙度值越低,型芯表面越光洁,所需的脱 模力 就越小。 4) 脱模力的大小与塑件的结构有关 塑件厚度越大、形状越复杂,冷却凝固时所引起的包 紧力和收缩应力越大,则所需的脱模力越大。 5)脱模力的大小还与塑件底部是否有孔有关。
粉末冶金原理及模具计算要求
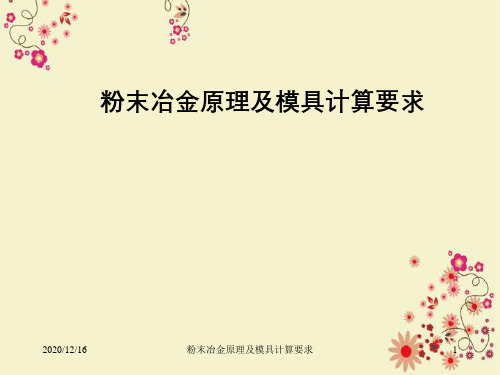
3.4 组合模具的设计原理
形状完整,具有一定强度
3.5 压制过程的图示
2020/12/16
粉末冶金原理及模具计算要求
2
•压制压力的计算
模压过程的总压制力等于净压力与外摩擦力 之和
单位压制压力与压坯密度定量关系的研究, 是近60年来粉末成形理论研究的主要内容
•脱模力的计算
压制压力去掉后,侧压力因为高度方向的弹 性后效,侧压力会下降35~77%
单向压制
S侧max/S=[1-(ρ下/ρ上)m]/μξ=K
当柱状压坯S侧/S<K或者圆柱体压坯高径比
H/D<K/4时,采用单向压制可以满足压坯密度
分布均匀性的要求
2020/12/16
粉末冶金原理及模
粉末冶金原理及模具计算要求
17
双向压制
S侧max/S=[1-(ρ中/ρ上)m]/μξ=2K
压力相等时双向压制与非同时双向压制的效 果相同
非同时双向压制中第二次压制的模冲移动距 离:
x=(d2-d1)h/d1
或者 y=x/l=100(d2-d1)/d1(k-1)
其中:d2为要求的压坯平均密度;d1为单向压 制的平均密度;h为压坯高度;k为压缩比;l 为装粉高度与压坯高度之差。
2020/12/16
•压制时粉体产生柱式流动,几乎不产生明显
的横向流动 2020/12/16
粉末冶金原理及模具计算要求
8
压坯中中立层的位置可以表示压坯密度分布
的均匀程度。通过压制方式和压模结构合理
选择使中立层2边受相同压缩,提高密度分布
均匀性 2020/12/16
粉末冶金原理及模具计算要求
9
2020/12/16
d粉—粉末松装密度; d1—第一次压制后压坯平均密度; 第一次压制后:d粉H粉=d1h1 x=h1-h d粉H粉=d1(h+x) ∴x=(d粉H粉-d1h)/d1 第二次压制后:d粉H粉=dh d粉=d ·h/H粉 x=(d-d1)h/d1; k=H粉/h=(l+h)/h 粉末冶金原理及∴模x具=计(算d要-d求1)l/d1(k-1); y=x/l ·11000%
注塑模具脱模 指标

注塑模具脱模指标注塑模具脱模是指在注塑过程中,将注塑成型的塑料制品从模具中取出的一项重要工序。
它是影响塑料制品质量的关键环节之一。
因此,注塑模具脱模的质量指标成为塑料制品加工过程中需要特别关注的问题。
注塑模具脱模的质量指标包括脱模力、脱模次数、脱模时间等多个方面。
首先,脱模力是指在脱模过程中所需要的力量。
脱模力的大小直接影响到模具的使用寿命。
如果脱模力过大,可能导致模具变形、损坏,甚至损坏塑料制品;如果脱模力过小,可能无法完全将塑料制品从模具中取出,造成生产工艺不稳定。
因此,在注塑模具设计和制造过程中,需要合理计算和控制脱模力的大小,以确保模具的正常运行和生产效率。
其次,脱模次数是指模具在使用过程中能够连续进行的脱模次数。
脱模次数的多少直接关系到塑料制品的生产效率和模具的耐用程度。
通常情况下,脱模次数越多,模具的性能越好。
但是,在实际生产中,由于塑料材料的种类和模具结构的不同,脱模次数也会存在差异。
因此,在注塑模具的设计和选材中,需考虑模具的使用寿命和生产需求,选择合适的材料和工艺。
再次,脱模时间是指完成一次脱模过程所需要的时间。
脱模时间的长短与注塑模具的结构设计、模具表面涂层和塑料材料的性质等因素有关。
脱模时间过长可能导致生产效率低下,而脱模时间过短可能会造成塑料制品在脱模过程中受损。
因此,在注塑模具的制造和使用过程中,需要根据生产要求和具体情况,合理控制脱模时间,以提高注塑生产效率和塑料制品的质量。
在实际生产中,注塑模具脱模的质量指标对于塑料制品的质量、模具的寿命和生产效率起着非常重要的作用。
因此,制造商应该注重模具的设计和制造过程,严格遵守操作规范,保证模具的质量和性能。
同时,注塑加工企业也应加强对注塑过程中的脱模工序的控制和管理,采取适当的工艺措施,提高注塑生产效率,降低生产成本,提升产品质量。
总之,注塑模具脱模的质量指标是一个不可忽视的重要问题。
合理控制脱模力、脱模次数和脱模时间,对于提高塑料制品的质量、延长模具的使用寿命以及提高生产效率具有重要意义。
塑料模具设计第七周 第一讲(第四章)
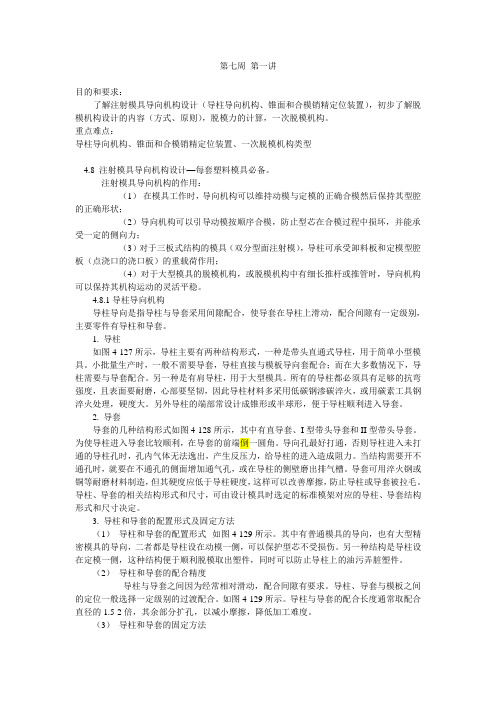
第七周第一讲目的和要求:了解注射模具导向机构设计(导柱导向机构、锥面和合模销精定位装置),初步了解脱模机构设计的内容(方式、原则),脱模力的计算,一次脱模机构。
重点难点:导柱导向机构、锥面和合模销精定位装置、一次脱模机构类型4.8 注射模具导向机构设计—每套塑料模具必备。
注射模具导向机构的作用:(1)在模具工作时,导向机构可以维持动模与定模的正确合模然后保持其型腔的正确形状;(2)导向机构可以引导动模按顺序合模,防止型芯在合模过程中损坏,并能承受一定的侧向力;(3)对于三板式结构的模具(双分型面注射模),导柱可承受卸料板和定模型腔板(点浇口的浇口板)的重载荷作用;(4)对于大型模具的脱模机构,或脱模机构中有细长推杆或推管时,导向机构可以保持其机构运动的灵活平稳。
4.8.1导柱导向机构导柱导向是指导柱与导套采用间隙配合,使导套在导柱上滑动,配合间隙有一定级别,主要零件有导柱和导套。
1. 导柱如图4-127所示,导柱主要有两种结构形式,一种是带头直通式导柱,用于简单小型模具。
小批量生产时,一般不需要导套,导柱直接与模板导向套配合;而在大多数情况下,导柱需要与导套配合。
另一种是有肩导柱,用于大型模具。
所有的导柱都必须具有足够的抗弯强度,且表面要耐磨,心部要坚韧,因此导柱材料多采用低碳钢渗碳淬火,或用碳素工具钢淬火处理,硬度大。
另外导柱的端部常设计成锥形或半球形,便于导柱顺利进入导套。
2. 导套导套的几种结构形式如图4-128所示,其中有直导套、I型带头导套和II型带头导套。
为使导柱进入导套比较顺利,在导套的前端倒一圆角。
导向孔最好打通,否则导柱进入未打通的导柱孔时,孔内气体无法逸出,产生反压力,给导柱的进入造成阻力。
当结构需要开不通孔时,就要在不通孔的侧面增加通气孔,或在导柱的侧壁磨出排气槽。
导套可用淬火钢或铜等耐磨材料制造,但其硬度应低于导柱硬度,这样可以改善摩擦,防止导柱或导套被拉毛。
导柱、导套的相关结构形式和尺寸,可由设计模具时选定的标准模架对应的导柱、导套结构形式和尺寸决定。
第10讲 脱模机构设计 PPT

10.1 脱模机构概述 10.2 脱模力的计算 10.3 推出零件尺寸的确定 10.4 简单脱模机构 10.5 定模脱模机构 10.6 双脱模机构 10.7 顺序脱模机构 10.8 二次脱模机构 10.9 转动脱模机构 10.10 流道凝料的脱模机构
10.1 脱模机构概述
10.1.1 脱模机构的组成
10.2.1 影响脱模力的因素
F摩 ( F正F脱 si ) n
Fk 0 F摩 c o s F 脱 F正 s i n 0
F脱F正 1(ccooss ssii nn)
F 脱 F 正 ( c o s s i ) A n ( c p o s s i )
10.2.1 影响脱模力的因素
F 脱 F 正 ( c o s s i ) A n ( c p o s s i )
a. 推杆应设置在制品的内侧。 b. 如果必须设在其外表面时,可在推杆工作 端面加工一些装饰性标志。
大的地方。
推杆的位置 1-推杆(兼复位杆)2-塑件 3-推杆 4-型芯 5-盘形推杆
10.4.1 常见脱模机构的类型
1.推杆脱模机构
2)应设在塑件强度刚度 较大处。
推杆不宜设在塑件的薄壁
处,应尽可能设在塑件厚壁、
凸缘处及筋与筋或壁与筋的交点上,以免使塑件变形损坏。来自如必须设在薄壁处时,应
增大推杆截面积,以降低单位
10.1.3 推出机构的设计原则
2)塑件应滞留于动模。以便利用注射机推杆驱 动动模一侧的推出机构完成脱模动作。
3)保证良好的塑件外观。塑件的推出位置应尽 量设在塑件内部或对外观影响不大的部位。
4)脱模机构应动作灵活可靠、制造维修更换方 便。
对于生产批量不大的制品,应尽量选择简单的 脱模机构,以降低模具的制造成本。
脱模力计算
Thank You~ Thank You~
頂出力(脫模力)說明
(一)定義
在注射動作結束後,塑件在模內冷卻定型,由於體積收縮,對公模型腔產生包 緊力,當其從模具中推出時,就必須克服因包緊力而產生的摩擦力,對於底部 無孔的筒、殼類塑料製件,脫模推出時還要克服大氣壓力。 開始脫模時所需的脫模力最大,其後推出力的作用僅僅是為了克服推出機構移 動的摩擦力,所以計算脫模力的時候,總是計算剛開始脫模時的初始脫模力。 將塑件從型腔上頂出時所需克服的阻力,包括: 成形收縮的包緊力; 不帶通孔的殼體類塑件的大氣壓力; 機構運動的摩擦力; 塑件對模具的黏附力;
(二)影響脫模力的因素
公模型腔成形部份的表面積及其形狀; 收縮率及摩擦係數; 脫模斜度; 塑件壁厚和包緊公模型腔的數量; 公模型腔表面粗糙度; 成形條件(工藝):如成形壓力、冷卻時間
塑件脫模力的分析
力力)的大小隨著塑件包覆型腔的面積增加而增大, 隨著脫模斜度增大而減小,大氣壓力及推出機構本身在推出運動時的摩擦阻力之間的 摩擦係數有關,事實上,影響脫模力的因素很多,因此在計算公式中不可能一一反映, 所以只能做大概的分析和估算。 其影響脫模力因素整理如下: 主要與塑件包覆型腔側面積的大小有關。脫模斜度越大,所需的脫模力越小。 與型腔的脫模斜度有關。脫模斜度越大,所需的脫模力越小。 與型腔的表面粗糙度有關。表面粗糙度值越低,型腔表面越光潔,所需的脫模力越 小。 與塑件的結構有關。塑件厚度越大,形狀越複雜,冷卻凝固時所引起的包緊力和收 縮應力越大,則所需的脫模力越大。 與射出成形條件有關。 成形壓力越大,則包緊型腔的力越大,所需脫模力越大; 脫模時模具溫度越高,所需的脫模力越小; 塑件在模內停留時間越長,所需的脫模力越大。 與成形塑件的塑料種類有關。 不同的塑料種類,由於分子結構不一樣,因而它們的脫模力也不一樣。
模具理论计算
理论计算1.1脱模力与锁模力包紧力P可采用式(1)计算:P=Q(Rkl一Rk2)/Rk2=EεT/Rk2(1)式中:Q—拉应力,Pa;RK1 、Rk2注塑件和型芯的径向尺寸,m;E ——弹性模量,Pa;ε——收缩率,%;T——注塑件壁厚,m。
Q=KhPA(μcosa-sina)=31.7MN (3)式中:地F1、F2——注塑件和型芯的当量截面积,m2Q——脱模力,N;K——可靠性系数,一般取2~3;h ——型芯埋入注塑件深度,m;A——型芯断面周长,m;μ——摩擦系数,取0.1~0.2;a-脱模斜度,为23°。
锁模力F=P′×s,最大注塑压力P取100MPa,注塑件和浇注系统在轴向的投影面积之和S约为1.44 m2,实际生产中F为:F ≥P' x S=100 x 1. 44=144 MN (4)1.2开模行程与侧抽芯尺寸开模行程H可用式(5)计算:H≥Hl+H2+a十10 mm=2 650 mm(5)式中H1——注塑件脱模距离,为1200 mm;H2——注塑件高度,为1200 mm;a—脱出浇口所需次分型面打开距离,为240 mm。
骨架尾部有对称的单向侧抽芯孔,抽芯距离S′=156 mm,斜导柱与水平线夹角a=23°,因此得到斜导柱有效长度L为:L=S'/sina=400 mm(6)最小开模行程Hc=L x cosa=445 mm,因此保证了Hc<Hl+H2。
1.3冷却水道尺寸研究表明,湍流状态下的对流传热效果比层流状态下好。
判断流动状态的准则是雷诺数(Re)。
Re ≥4000时即为湍流状态,由此可以计算出当量直径大于等于4 mm时为湍流。
本模具初定水孔直径为50.5 mm。
假设制品冷却时所有热量全由冷却系统带走,则模具冷却水道最大长度式中:μ——冷却水流速,实际生产中为1~1.5 m/s;dw冷却水道断面为非圆形时的当量直径,为0.0505 m;p—水的密度,为998.2 kg/m3;μ—水的粘度,为1.005 x 10 -3 Pa·S ;Cw—水的比热容,为4. 183 kJ/ ( kg·K);λ—热导率,为0. 599 W/(m·K)(以上均为20 ℃下的数据);θm-模具平均温度,为60℃;θw—冷却水平均温度,为25 ℃;C-熔体比热容,为2. 2 kJ/(kg·K);Pi—熔体密度,为778 .3 kg/m3;V—一次注射量,m3。
3-推出机构-脱模力计算
Ft = Fb ( µ cos α − sin α ) = Ap ( µ cos α − sin α )
由上面的式子可以看影响因素脱模力的大小主要有以下几点: 由上面的式子可以看影响因素脱模力的大小主要有以下几点: 影响因素脱模力的大小主要有以下几点
(l)主要与塑件包络型芯侧面积的大小有关。型芯的侧面积越大,所需的脱 主要与塑件包络型芯侧面积的大小有关。型芯的侧面积越大, 模力也越大。 模力也越大。 与型芯的脱模斜度有关。脱模斜度越大,所需的脱模力越小。 (2)与型芯的脱模斜度有关。脱模斜度越大,所需的脱模力越小。 (3)与型芯的表面粗糙度有关。表面粗糙度值越低,型芯表面越光洁,所需 与型芯的表面粗糙度有关。表面粗糙度值越低,型芯表面越光洁, 的脱模力就越小。 的脱模力就越小。 与塑件的结构有关。塑件厚度越大、形状越复杂, (4)与塑件的结构有关。塑件厚度越大、形状越复杂,冷却凝固时所引起的 包紧力和收缩应力越大,则所需的脱模力越大。 包紧力和收缩应力越大,则所需的脱模力越大。 与注射工艺有关。 (5)与注射工艺有关。 注射压力越大,则包紧型芯的力越大,所需脱模力越大; 注射压力越大,则包紧型芯的力越大,所需脱模力越大; 脱模时模具温度越高,所需的脱模力越小; 脱模时模具温度越高,所需的脱模力越小; 塑件在模内停留时间越长,所需的脱模力越大。 塑件在模内停留时间越长,所需的脱模力越大。 与成型塑件的塑料品种有关。不同的塑料品种,由于分子的结构不一样, (6)与成型塑件的塑料品种有关。不同的塑料品种,由于分子的结构不一样, 因而它们的脱模力也不一样。 因而它们的脱模力也不一样。
Fm cos α − Ft − Fb sin α = 0
Fm = ( Fb − Ft sin α ) µ
浅谈注塑模具的计算
浅谈注塑模具的计算浅谈注塑模具的计算引导语:下面是店铺为大家精心准备的关于浅谈注塑模具的计算的相关资料,希望可以帮助到大家哦!1.引言工业设计的目的,就是通过对产品的合理规划,而使人们能更方便地使用它们,使其更好地发挥效力。
在研究产品性能的基础上,工业设计还通过合理的造型手段,使产品能够具备富有时代精神,符合产品性能、与环境协调的产品形态,使人们得到美的享受。
工业设计强调技术与艺术相结合,所以它是现代科学技术与现代文化艺术融合的产物。
它不仅研究产品的形态美学问题,而且研究产品的实用性能和产品所引起的环境效应,使它们得到协调和统一,更好地发挥其效用。
丛林法则(the law of the jungle)是自然界里生物学方面的物竞天择、适者生存、优胜劣汰、弱肉强食的规律法则。
激烈的市场竞争让塑料制品在利用工业设计的同时,不得不引入丛林法则,正是工业设计和丛林法则促使塑料制品的外观造型越来越复杂,而电脑技术的发展,特别是计算机辅助设计和制造使这一切复杂的设计造型都有了实现的可能性。
塑料制品的成型,绝大多数都离不开模具。
近年来,计算机辅助设计和制造的发展,对塑料制品的设计和模具制造带来了翻天覆地的变化。
模具制造的技术已经由过去的以钳工手工为主发展到以数控机床加工为主,塑料产品的设计也从手工制图发展到完全利用电脑绘图,产品制图的表现手法也由过去2D图纸转向3D数据为主,产品的造型也从过去的方形、三角形和圆形等规则形状变化为复杂的空间曲面造型,这些变化都使得产品的外观形状越来越复杂,也给模具设计和制造带来了极大的挑战。
因此要求我们的模具设计必须适应这种挑战,与时俱进。
对于注塑模具的计算,模具专业教科书、技术资料、论文和设计手册已经有很多公式和资料,在过去几十年的岁月里,这些公式在模具行业得到广泛的应用,现在利用计算机辅助设计与制造的情况下,这些公式的局限性也凸显出来,因而有些传统的模具设计计算公式在实际中已经失去使用价值,继续使用某些公式可能会给模具设计专业的新生带来困扰,本文旨在探讨在模具设计的实践中哪些内容需要计算,哪些内容不需要计算,如何选择计算公式等问题。
- 1、下载文档前请自行甄别文档内容的完整性,平台不提供额外的编辑、内容补充、找答案等附加服务。
- 2、"仅部分预览"的文档,不可在线预览部分如存在完整性等问题,可反馈申请退款(可完整预览的文档不适用该条件!)。
- 3、如文档侵犯您的权益,请联系客服反馈,我们会尽快为您处理(人工客服工作时间:9:00-18:30)。
脱模力的大小需根据具体情况具体计算,对于小型制品脱模力很小,可能只有几十牛顿,甚至仅仅几牛顿;而对于较大型制品会大的多,达到几十千牛,甚至更大。
如福建华橡自控技术股份有限公司的45 寸轮胎定型硫化机中,脱模力F=27.43KN 。
因此对于不同的制品脱模力的计算需根据具体的公式进行计算,计算公式如下:
计算简单形状制(如圆筒)的脱模力计算方法是:Ac Pc f Fe ⨯⨯=
Pc 为型芯的接触压力;
Ac 为型芯与塑件的接触而积;
f 为制品顶出时塑料与型芯之间的摩擦系数。
针对圆筒其中m r s d T E Pc ⨯∆⨯=)(,)(T E 为塑料在顶出温度下的弹性模量,r d ∆为制品脱模后的直径相对变化量,m s 为制品厚度。
L Ac π2=,其中L 为制品与型芯接触部分的长度。
一个使用较为普遍的脱模力计算模型:
公式中定义接触压力为:
()t
t E T T Pc e m 421μ
α-⨯-= m T 为材料软化温度,t 为制品厚度,μ为泊松比。
以此为依据,脱模力计算式为: ()t
t f L E T T Fe e m 421μ
πα-⨯⨯⨯-= 针对空心薄壁锥体,并考虑了拔模角及真空力对脱模力的影响,其公式为:
()B f f L S E Fe m 10cos sin 1tan cos 12++-⨯-=θ
θθθμεπ ε为塑料的拉伸应变,B 为垂直于脱模方向型芯的投影而积。
该公式中,第一部分代表总包紧力,通过对于薄壁中空锥形体的力和应力分析获得;第二部分代表摩擦因数;第三部分代表真空力。
圆形制品和矩形制品的脱模力计算模型分别为:
()θθθθμεπcos sin 1tan cos 12f f tL E Fc +-⨯-= θθθμεcos sin 1tan 18f f tL E Fr +-⨯-=
其中ε为材料收缩率,E 为弹性模量,μ为泊松比,t 为材料厚度,L 为制品与型芯接触部分的长度,θ为脱模斜度。
《塑料成型模具》一书,在推导脱模力计算公式时, 受力分析如图1 所示, 其推导过程是: ∑=0Fx
ααsin cos 1P Q F += (1)
上式中摩擦阻力F 为:
()αsin 1Q P f F -= (2)
将(2)式带入(1)式得:
()α
αααcos sin 1tan cos 1f f P Q +-= 其中1Q ——脱模力(1Q 未考虑不带通孔塑件脱出时需克服的大气压力所造成的阻力) P ——正压力(即型芯上沿锥面全面积上的总压力)
f ——摩擦因数
α——脱模斜度(型芯锥角的一半)
杠杆式脱模机构(轮胎硫化机)受力分析:
杠杆式脱模机构在推动中心机构时,为滚子传递推力。
由于滚子与中心机构下部为滚动接触,中心机构受力为滚子法线作用力F (即脱模力)和滚动摩擦阻力f ,见图2所示。
p b
a D p
b a T F ⨯⨯⨯⨯=⨯⨯=42π p ——动力水压力。