橡胶的成型加工原理
炼胶机原理

炼胶机原理炼胶机是橡胶工业中常用的一种设备,它主要用于将橡胶混炼成所需的品种和硬度。
炼胶机的原理是通过机械作用和热能作用,将橡胶与其他辅助原料混合均匀,达到一定的塑性和粘度,以便后续加工成型。
首先,炼胶机的工作原理是利用橡胶在受热和机械作用下发生塑性变形的特性。
在炼胶机内部,装有多个辊子,这些辊子通过不同的速度和方向进行旋转,使得橡胶在辊子之间受到挤压和牵拉,从而使其分子链发生断裂和重组,达到混炼的目的。
同时,炼胶机还可以通过加热系统对橡胶进行加热,使其软化和流动性增强,便于混合和塑形。
其次,炼胶机还配有一些辅助原料的加入装置,如填料、增塑剂、硫化剂等。
这些辅助原料在混炼过程中与橡胶一同被加入到炼胶机中,通过机械作用和热能作用,与橡胶充分混合和反应,从而使其性能得到改善和提高。
总的来说,炼胶机的原理是通过机械作用和热能作用,对橡胶和辅助原料进行混炼和加工,使其达到一定的塑性和粘度,并最终得到符合要求的橡胶混合物。
炼胶机在橡胶工业中具有非常重要的作用,它的工作原理和操作方法对于生产过程的稳定性和产品质量都有着至关重要的影响。
在实际操作中,需要根据不同的橡胶品种和加工要求,选择合适的炼胶机型号和工艺参数,以确保混炼效果和生产效率。
此外,对于炼胶机的维护和保养也是非常重要的,只有保持设备的良好状态,才能确保其正常运行和生产出优质的橡胶制品。
总之,炼胶机的原理是通过机械作用和热能作用,对橡胶和辅助原料进行混炼和加工,以达到一定的塑性和粘度。
它在橡胶工业中具有重要作用,对于生产过程的稳定性和产品质量都有着至关重要的影响。
因此,对于炼胶机的工作原理和操作方法,以及设备的维护和保养都需要引起重视。
橡胶 工艺 原理

橡胶工艺原理
橡胶是一种由橡胶树的乳液经过加工制成的具有弹性的材料。
橡胶的工艺原理主要包括以下几个方面。
1. 采集橡胶乳液:橡胶树的树干被割开后,乳液会自然流出。
采集工人使用刮刀将乳液慢慢刮下,收集到容器中。
2. 乳液稳定化:采集到的橡胶乳液中含有大量的水分和其他杂质,需要经过稳定化处理。
常用的稳定化剂包括氨水和醋酸,它们可以使乳液保持稳定状态,并防止乳液中的橡胶团聚。
3. 合成橡胶:乳液经过稳定化处理后,需要加入硫化剂、填充剂和加工助剂等多种化学物质进行合成橡胶的加工。
其中,硫化剂可以使橡胶分子之间的交联结构更加牢固,增加橡胶材料的强度和耐磨性;填充剂可以提高橡胶材料的硬度和耐磨性;加工助剂则可以调整橡胶材料的流动性和加工性能。
4. 橡胶成型:合成橡胶经过调配后,可以通过各种成型方法将其制成不同形状的橡胶制品。
常见的成型方法包括压延、压缩模压、浇注和挤出等。
5. 硫化和固化:成型后的橡胶制品需要进行硫化或固化处理,使其获得所需的弹性和耐磨性。
硫化是将成型的橡胶制品置于加热的硫化炉中,在一定温度下与硫化剂反应,形成较为稳定的交联结构;固化则是使用特定的固化剂或光线照射,使成型的橡胶制品的分子链交联,增加其硬度和强度。
通过以上的工艺原理,橡胶可以被制备成各种应用于工业、交通、建筑和日常生活中的橡胶制品,如轮胎、密封件、橡胶管、橡胶鞋等。
橡胶加工工艺
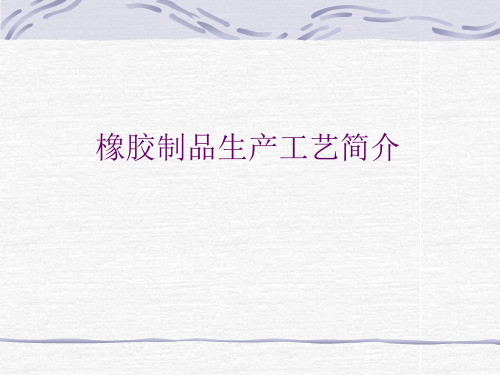
➢ 化学塑解剂:塑解剂的用量,在NR中一般为生胶重量的0.1~0.3%,合 成橡胶则应增大到2~3%。
橡胶制品生产工艺简介-塑炼工艺塑炼工艺
不同胶料开炼机混炼时辊筒温度
胶种
天然胶 丁苯胶 氯丁胶 丁基胶 丁腈胶 顺丁胶 三元乙丙胶 氯磺化聚乙烯 氟橡胶23—27 丙烯酸酯橡胶
橡胶制品生产工艺简介-塑炼工艺塑炼工艺
常用橡胶的塑炼特性
2. SBR ➢ 软SBR的初始门尼粘度一般在54~64之间,不需进行塑炼。 ➢ SBR采用机械塑炼效果不大,比较有效的方法时采用高温
塑炼法,以130~140℃温度最好,温度过高易生成凝胶。 3.BR ➢ BR一般不需要进行塑炼。 4.CR ➢ CR的初始门尼粘度都较低,一般不需要进行塑炼。但在储
➢ 物料在密炼室中主要受到几种作用: 转子间及转子与混炼室内壁间的作用;
转子棱间的搅拌作用;
转子轴向的往复切割作用。
➢ 优点:自动化程度高,生产效率高,节能,劳动强度低
➢ 缺点:温度高,冷却困难,易过炼,出料为无定形状
橡胶制品生产工艺简介-塑炼工艺塑炼工艺
密炼机
橡胶制品生产工艺简介-塑炼工艺塑炼工艺
存过程中其可塑性会下降,因此CR仍需经过塑炼加工,才 能获得所要求的可塑性。 ➢ CR宜采用开炼机进行塑炼,低温薄通塑炼效果最好。
橡胶制品生产工艺简介-塑炼工艺塑炼工艺
常用橡胶的塑炼特性
5.IIR ➢ 门尼粘度在38~75之间的品种一般不需要塑炼。 ➢ IIR采用机械塑炼效果不大,但用密炼机在120℃以上,并
且加入塑解剂进行高温塑炼则可取得较好的塑炼效果。 6.NBR ➢ NBR的塑炼应采用开炼机在低温(40℃以下)、小辊距
橡胶生产工艺简介

橡胶生产工艺简介橡胶生产工艺简介1 综述橡胶制品的主要原料是生胶、各种配合剂、以及作为骨架材料的纤维和金属材料,橡胶制品的基本生产工艺过程包括塑炼、混炼、压延、压出、成型、硫化6个基本工序。
橡胶的加工工艺过程主要是解决塑性和弹性矛盾的过程,通过各种加工手段,使得弹性的橡胶变成具有塑性的塑炼胶,在加入各种配合剂制成半成品,然后通过硫化是具有塑性的半成品又变成弹性高、物理机械性能好的橡胶制品。
2 橡胶加工工艺2.1塑炼工艺生胶塑炼是通过机械应力、热、氧或加入某些化学试剂等方法,使生胶由强韧的弹性状态转变为柔软、便于加工的塑性状态的过程。
生胶塑炼的目的是降低它的弹性,增加可塑性,并获得适当的流动性,以满足混炼、亚衍、压出、成型、硫化以及胶浆制造、海绵胶制造等各种加工工艺过程的要求。
掌握好适当的塑炼可塑度,对橡胶制品的加工和成品质量是至关重要的。
在满足加工工艺要求的前提下应尽可能降低可塑度。
随着恒粘度橡胶、低粘度橡胶的出现,有的橡胶已经不需要塑炼而直接进行混炼。
在橡胶工业中,最常用的塑炼方法有机械塑炼法和化学塑炼法。
机械塑炼法所用的主要设备是开放式炼胶机、密闭式炼胶机和螺杆塑炼机。
化学塑炼法是在机械塑炼过程中加入化学药品来提高塑炼效果的方法。
开炼机塑炼时温度一般在80℃以下,属于低温机械混炼方法。
密炼机和螺杆混炼机的排胶温度在120℃以上,甚至高达160-180℃,属于高温机械混炼。
生胶在混炼之前需要预先经过烘胶、切胶、选胶和破胶等处理才能塑炼。
几种胶的塑炼特性:天然橡胶用开炼机塑炼时,辊筒温度为30-40℃,时间约为15-20min;采用密炼机塑炼当温度达到120℃以上时,时间约为3-5min。
丁苯橡胶的门尼粘度多在35-60之间,因此,丁苯橡胶也可不用塑炼,但是经过塑炼后可以提高配合机的分散性顺丁橡胶具有冷流性,缺乏塑炼效果。
顺丁胶的门尼粘度较低,可不用塑炼。
氯丁橡胶得塑性大,塑炼前可薄通3-5次,薄通温度在30-40℃。
橡胶生产工艺简介
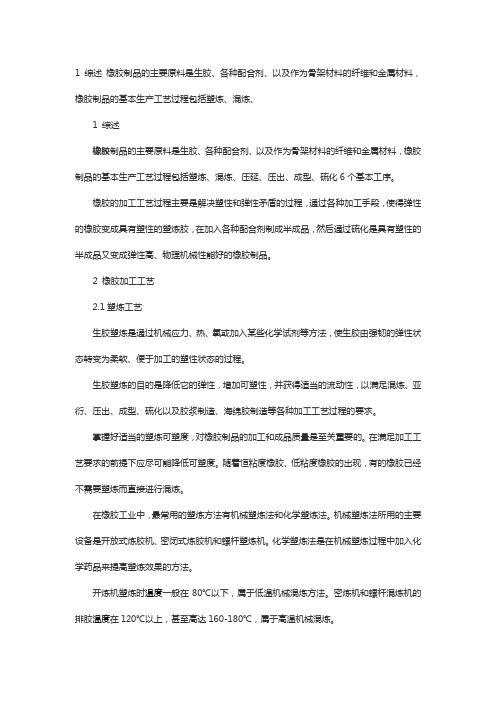
1 综述橡胶制品的主要原料是生胶、各种配合剂、以及作为骨架材料的纤维和金属材料,橡胶制品的基本生产工艺过程包括塑炼、混炼、1 综述橡胶制品的主要原料是生胶、各种配合剂、以及作为骨架材料的纤维和金属材料,橡胶制品的基本生产工艺过程包括塑炼、混炼、压延、压出、成型、硫化6个基本工序。
橡胶的加工工艺过程主要是解决塑性和弹性矛盾的过程,通过各种加工手段,使得弹性的橡胶变成具有塑性的塑炼胶,在加入各种配合剂制成半成品,然后通过硫化是具有塑性的半成品又变成弹性高、物理机械性能好的橡胶制品。
2 橡胶加工工艺2.1塑炼工艺生胶塑炼是通过机械应力、热、氧或加入某些化学试剂等方法,使生胶由强韧的弹性状态转变为柔软、便于加工的塑性状态的过程。
生胶塑炼的目的是降低它的弹性,增加可塑性,并获得适当的流动性,以满足混炼、亚衍、压出、成型、硫化以及胶浆制造、海绵胶制造等各种加工工艺过程的要求。
掌握好适当的塑炼可塑度,对橡胶制品的加工和成品质量是至关重要的。
在满足加工工艺要求的前提下应尽可能降低可塑度。
随着恒粘度橡胶、低粘度橡胶的出现,有的橡胶已经不需要塑炼而直接进行混炼。
在橡胶工业中,最常用的塑炼方法有机械塑炼法和化学塑炼法。
机械塑炼法所用的主要设备是开放式炼胶机、密闭式炼胶机和螺杆塑炼机。
化学塑炼法是在机械塑炼过程中加入化学药品来提高塑炼效果的方法。
开炼机塑炼时温度一般在80℃以下,属于低温机械混炼方法。
密炼机和螺杆混炼机的排胶温度在120℃以上,甚至高达160-180℃,属于高温机械混炼。
生胶在混炼之前需要预先经过烘胶、切胶、选胶和破胶等处理才能塑炼。
几种胶的塑炼特性:天然橡胶用开炼机塑炼时,辊筒温度为30-40℃,时间约为15-20min;采用密炼机塑炼当温度达到120℃以上时,时间约为3-5min。
丁苯橡胶的门尼粘度多在35-60之间,因此,丁苯橡胶也可不用塑炼,但是经过塑炼后可以提高配合机的分散性顺丁橡胶具有冷流性,缺乏塑炼效果。
橡胶加工工艺—橡胶压出工艺(高分子成型课件)
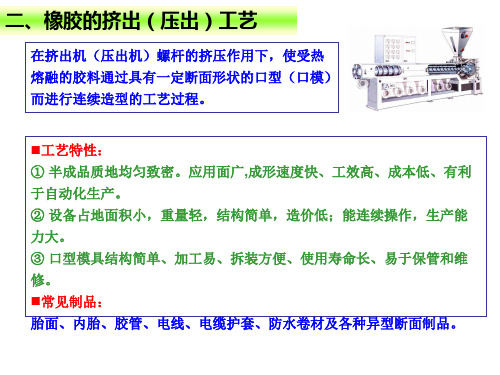
二、橡胶的挤出(压出)工艺
(一)压出机工作原理及胶料的运动状态 3 物料在口型中的流动状体和挤出变形 胶料经机头进入口型后,由于口型形状不同及内表 面对物料流动的阻碍,物料流动速度也存在有与机 头类似的速度分布。中间流速大,越接近口型壁流 速越小 。 一般粘弹性的物料,从口型挤出后就不可避免地存 在松弛现象,即:胶条的长度会沿挤出方向缩短, 厚度沿垂直挤出方向增加(离模膨胀现象或称作挤 出变形现象)。挤出后的变形(收缩和膨胀)可以控制 在一定范围,但不可能完全消除。要求收缩率为 2~5%。 物料可塑性小、含胶率大,填充剂用量小,物料挤 出快,机头和口型温度低,膨胀和收缩率就大。
二、橡胶的挤出(压出)工艺
在挤出机(压出机)螺杆的挤压作用下,使受热 熔融的胶料通过具有一定断面形状的口型(口模) 而进行连续造型的工艺过程。
工艺特性: ① 半成品质地均匀致密。应用面广,成形速度快、工效高、成本低、有利 于自动化生产。 ② 设备占地面积小,重量轻,结构简单,造价低;能连续操作,生产能 力大。 ③ 口型模具结构简单、加工易、拆装方便、使用寿命长、易于保管和维 修。 常见制品: 胎面、内胎、胶管、电线、电缆护套、防水卷材及各种异型断面制品。
二、橡胶的挤出(压出)工艺
(一)压出机工作原理及胶料的运动状态
1 胶料在挤出机中的运动状态
加料段:加入的条状胶料,受到旋转螺杆的推挤作用形成连续的胶 团,并沿着螺槽的空间一边旋转,一边不断前进。 压缩段:加料段输送过来的松散胶团在压缩段被逐渐压实、软化, 并把夹带的空气向加料段排出。同时胶团间间隙缩小,密度增高, 进而粘在一起,再加上受到剪切和搅拌作用,因而胶团逐渐被加热 塑化形成连续的粘流体。 挤出段:在挤出段,压缩段输送过来的物料进一步塑化均匀,并输 送到机头和口模处挤出成型。
橡胶生产六大工艺
橡胶生产六大工艺橡胶是一种广泛应用于工业和日常生活中的重要材料,其生产过程通常包括六大工艺。
本文将详细介绍这六大工艺,包括橡胶的采集、研磨、混炼、成型、硫化和加工。
第一大工艺是橡胶的采集。
橡胶主要来自于橡胶树的树液,树液在被采集后会流入集液器中。
采集橡胶树的树液需要注意采集时间和方式,以免对树液的质量和树木的健康造成不良影响。
第二大工艺是橡胶的研磨。
在研磨过程中,橡胶块被切碎成小颗粒,以便后续的混炼和成型工艺。
研磨的目的是使橡胶颗粒的尺寸和形状更加均匀,提高橡胶的可塑性和可加工性。
第三大工艺是橡胶的混炼。
混炼是将橡胶颗粒与其他添加剂(如增塑剂、硫化剂等)进行混合,以改善橡胶的性能。
混炼的过程中需要控制温度、时间和混炼机械的运行状态,确保橡胶与添加剂充分混合均匀。
第四大工艺是橡胶的成型。
成型是将混炼好的橡胶料通过挤出、压延、压制等方式制成所需的形状。
成型过程中需要根据产品的要求选择合适的成型设备和工艺参数,保证产品的尺寸和性能符合要求。
第五大工艺是橡胶的硫化。
硫化是橡胶加工中非常重要的一步,通过加热橡胶制品与硫化剂反应,使橡胶分子之间形成交联结构,提高橡胶的强度、耐磨性和耐老化性能。
硫化过程中需要控制硫化温度和时间,以及硫化剂的种类和用量,确保橡胶制品的质量。
最后一大工艺是橡胶的加工。
加工是指对硫化好的橡胶制品进行后续处理,包括修整边角、打磨表面、安装配件等。
加工的目的是使橡胶制品的外观更加美观,尺寸更加精确,以满足客户的需求。
通过以上六大工艺,橡胶从采集到最终成品的过程得以完整实现。
这些工艺相互衔接,每个环节都至关重要,对橡胶制品的质量和性能有着重要影响。
因此,在橡胶生产过程中,需要严格控制每个工艺的参数和操作方法,确保橡胶制品达到设计要求,并具有优良的性能和可靠的质量。
总结起来,橡胶生产的六大工艺包括采集、研磨、混炼、成型、硫化和加工。
这些工艺环环相扣,每个环节都不可或缺。
只有在每个工艺环节都严格把控,才能生产出优质的橡胶制品。
HCR工艺原理及特点
HCR工艺原理及特点HCR (High Consistency Rubber) 工艺是一种橡胶加工工艺,主要用于生产高浓度橡胶浆料,具有以下原理和特点:1.工艺原理:HCR工艺主要由橡胶破碎、粘度调节、混合和成套设备等组成。
首先,将橡胶颗粒破碎成为一定大小的颗粒;然后,通过添加粘度调节剂调节橡胶浆料的粘度,以满足不同需求;接下来,橡胶颗粒和粘度调节剂在混合机中充分混合,形成高浓度的橡胶浆料;最后,橡胶浆料可以通过输送设备直接投入到橡胶成型机中进行成型。
2.工艺特点:(1)适应性强:HCR工艺适用于各种类型的橡胶,包括天然橡胶、合成橡胶和再生橡胶等。
同时,可以根据需要调节粘度和浓度,以适应不同产品的要求。
(2)成本低:与传统的橡胶加工工艺相比,HCR工艺具有较低的生产成本。
这是因为HCR工艺不需要使用大量的溶剂和高温高压设备,节省了能源和原材料成本。
(3)生产效率高:HCR工艺具有较高的生产效率。
由于采用了高浓度橡胶浆料,可以减少麻胶的体积,提高输送效率。
此外,混合机搅拌速度快,可以快速将橡胶颗粒和粘度调节剂充分混合。
(4)产品质量好:HCR工艺可以获得优良的产品质量。
因为高浓度橡胶浆料可以提高橡胶的分散性和充填性,使得成型的橡胶制品具有良好的物理性能和外观质量。
(5)环保性好:HCR工艺对环境的影响较小。
与传统的橡胶加工工艺相比,HCR工艺不需要使用大量的溶剂和污水处理设备,减少了废物的排放和处理成本。
(6)工艺控制精度高:HCR工艺可以精确控制橡胶浆料的粘度、浓度和颗粒大小。
通过调节粘度调节剂的添加量和搅拌时间等参数,可以满足不同产品的要求。
总结起来,HCR工艺是一种适应性强、成本低、生产效率高、产品质量好、环保性好且工艺控制精度高的橡胶加工工艺。
该工艺在橡胶制品行业具有广泛应用前景。
实验14 -橡胶的成型加工
实验14橡胶制品的成型加工一、实验目的1.掌握橡胶制品配方设计基本知识。
熟悉橡胶加工全过程和橡胶制品模型硫化工艺;2.了解橡胶加工的主要机械设备如开炼机、平板硫化机等基本结构,掌握这些设备的操作方法;3.掌握橡胶物理机械性能测试试样制备工艺及性能测试方法。
二、实验原理橡胶制品的基本工艺过程包括配合,生胶塑炼,胶料混炼,成型,硫化五个基本过程,如图14-1所示。
图14-1橡胶制品生产工艺过程1.生胶的塑炼生胶是线型的高分子化合物,在常温下大多数处于高弹态。
然而生胶的高弹性却给成型加工带来极大的困难,一方面各种配合剂无法在生胶中分散均匀,另一方面,由于可塑性小,不能获得所需的各种形状。
为满足各种加工工艺的要求,使生胶由强韧的弹性状态变成柔软而具有可塑性的状态的工艺过程称作塑炼。
生胶经塑炼以增加其可塑性,其实质是橡胶分子链断裂,相对分子质量降低,从而橡胶的弹性下降。
在橡胶塑炼时,主要受到机械力、氧、热、电和某些化学增塑剂等因素的作用。
工艺上用以降低橡胶相对分子质量获得可塑性的塑炼方法可分为机械塑炼法和化学塑炼法两大类,其中机械塑炼法应用最为广泛。
橡胶机械塑炼的实质是力化学反应过程,即以机械力作用及在氧或其它自由基受体存在下进行的。
在机械塑炼过程中,机械力作用使大分子链断裂,氧对橡胶分子起化学降解作用,这两个作用同时存在。
本实验选用开炼机对天然橡胶进行机械法塑炼。
天然生胶置于开炼机的两个相向转动的辊筒间隙中,在常温(小于50℃)下反复受机械力作用,使分子链断裂,与此同时断裂后的大分子自由基在空气中的氧化作用下,发生了一系列力学与化学反应,最终达到降解,生胶从原先强韧高弹性变为柔软可塑性,满足混炼的要求。
塑炼的程度和塑炼的效率主要与辊筒的间隙和温度有关,若间隙愈小、温度愈低,力化学作用愈大,塑炼效率愈高。
此外,塑炼的时间,塑炼工艺操作方法及是否加入塑解剂也影响塑炼的效果。
2.橡胶的配合橡胶必须经过交联(硫化)才能改善其物理机械性能和化学性能,使橡胶制品具有实用价值。
橡胶加工工艺—橡胶注射工艺(高分子成型课件)
橡胶注射定义: 将胶料加热塑化成粘流态(熔融态),施以高压注射进入模具 热压硫化,然后开启模具取出成型制品的工艺过程。
三、橡胶的注射工艺
工艺特点
① 成型过程和硫化过程同时进行,工序简单,制品性能优异、质量稳 定; ② 胶料利用率高,可获得形状复杂的制品; ③ 自动化和半自动化程度高,劳动强度低,硫化速度快,生产效率高, 但需严格控制硫化工艺,否则胶料易过硫; ④属于周期性生产工艺,一次性投资大,模具结构复杂,加工成本高。 应用范围
6 成型周期—时间
高温快速硫化体系配方可大大缩短硫化时间。 厚制品硫化时由于制品内外层存在一定的温差,因此仍需适当延长硫化 时间保证制品质量。 一般情况下,充模时间与保压时间之和应小于焦烧时间,以防胶料在喷 嘴和模型流道处硫化,同时保证在硫化前完成压力均化过程,消除物料流 动中造成的内应力现象。
三、橡胶的注射工艺
适合于尺寸精度高、形状复杂、产量高的橡胶制品的生产,主要用于 密封圈、带金属骨架的模制品、减震垫及鞋类制品的生产。
三、橡胶的注射工艺
(一)注射过程及原理 1 注射成型过程
塑化
脱模
注射
热压 硫化
橡胶注射成型过程:塑化、注射、热压硫化,脱模。注射之前要求胶 料温度较低,防止发生焦烧,同时胶料应有较好的流动性,保证顺利注 模。注射保压后快速升温,且模具中内外层胶料温度均匀一致,提高 体系硫化效率。
三、橡胶的注射工艺
(二)注射工艺条件分析
5 喷嘴结构 喷嘴结构十分重要,喷嘴锥形部位斜度为30°-75°时,胶温上升最慢, 压力损失小。 减小喷嘴直径,注射时间延长,通过喷嘴摩擦生热高,易引起焦烧; 喷嘴直径增加,注射时间减小,焦烧危险性减小,但硫化时间增加。一 般情况下,喷嘴直径控制在2-6mm。
- 1、下载文档前请自行甄别文档内容的完整性,平台不提供额外的编辑、内容补充、找答案等附加服务。
- 2、"仅部分预览"的文档,不可在线预览部分如存在完整性等问题,可反馈申请退款(可完整预览的文档不适用该条件!)。
- 3、如文档侵犯您的权益,请联系客服反馈,我们会尽快为您处理(人工客服工作时间:9:00-18:30)。
作用 机理
作用 机理 种类
作用 机理
种类 作用 机理
硫化剂
防老剂
种类
软化剂/ 增塑剂
橡 胶 配 合 剂
补强剂/ 填充剂
种类
7.3 橡胶的加工
塑炼
混炼
Mixing
Plastication
Calendering Extrusion
一、生胶的塑炼
1、塑炼的目的与要求
(1)塑炼
定义:橡胶加工过程中,把高弹性生胶转变为可 塑性胶料的工艺过程,叫塑炼
(2)丁苯橡胶
软丁苯胶,不塑炼或轻微塑炼
(3)顺丁橡胶
顺丁橡胶,一般不需塑炼
(4)丁腈橡胶
软丁腈胶一般不需要塑炼
硬丁腈胶需充分塑炼,开炼,低温(< 40
℃)、薄通、低容量
(5)氯丁橡胶
通用型的氯丁橡胶,一般不需进行塑炼 若塑炼,温度要控制 < 70℃
氯丁胶 小知识
Tr ~ 70℃时为弹性体,易包辊,不粘辊
加料顺序:塑炼胶→ 小料(促进剂、活性剂、 防老剂等)→ 补强填充剂 → 液体增塑剂
密炼机优点:机械化程度高,劳动强度小,混炼 时间短,效率高,减少粉剂的飞扬
4、混炼的影响因素
(1)配合剂的种类
疏水性配合剂,表面特性与橡胶同,易被橡胶润湿,好 混炼,如各种炭黑
亲水性配合剂,表面特性与橡胶不同,不易被橡胶润湿, 如碳酸钙、陶土、氧化锌、锌钡白等
(2)丁苯橡胶 混炼生热大、升温快,温度应比天然橡胶低;对 粉剂的润湿能力差,粉剂难分散,混炼时间长 开炼机混炼,需增加薄通次数 密炼机混炼,二段混炼,混炼要注意温度控制
(3)氯丁橡胶
开炼机混炼,辊温在40~50℃,温度高易粘辊
加料时先加MgO,后加ZnO,可避免焦烧;或掺入10 %的天然橡胶或顺丁橡胶,能改善工艺性能
快速确定生胶的塑炼程度及评价加工性能的好坏
威氏可塑度P:指试样在一定外力作用下产生压
缩形变的大小和除去外力后保持形变的能力 可塑度越高,胶料的流动性越好
3、塑炼的方法
开放 开炼
密闭 密炼
(1)开炼机塑炼
低温塑炼
(2)密炼机塑炼
高温塑炼
4、塑炼的影响因素
(1)分子量的影响
天然胶70万 分子量大的易切断 分子量小的难切断 顺丁胶40万 丁苯胶30万
生胶 塑炼胶
塑炼
(2)塑炼的目的
使生胶具有一定的可塑性, 使其适合于后续工艺操作
(3)塑炼的要求
满足其它工艺要求为前 提,避免过度的塑炼
2、塑炼的原理
橡胶分子量大,分子链相对 位移难,粘度高,难加工
降低分子量,力-化学反应
机械剪切力、氧分子链断裂, 可塑性↑↑ 低温塑炼 高温塑炼
可塑性用可塑度表征
(2)炭黑颗粒的分散
结合橡胶 充分分散
生胶混炼性能好坏,用炭黑混入时间BIT表示 BIT(Black Incorporation Time炭黑在生胶中被 混炼到均匀分散程度所需要的时间 炭黑混入时间BIT值↓,生胶越容易混炼
3、混炼的方法
开炼机混炼、密炼机混炼
(1)开炼机混炼
加料顺序:塑炼胶→ 小料(促进剂、活性剂、防老
在70~94℃,严重粘辊,不能塑炼、混炼、 压延
塑炼
混炼
Mixing
Plastication
Calendering Extrusion
二、胶料的混炼
1、混炼的定义及目的
定义:通过机械剪切力和挤压作用,使塑炼胶与各 种配合剂均匀混合而分散的过程 目的:提高橡胶产品的使用性能、改善橡胶工艺性 能、降低生产成本
剂等)→ 液体软化剂 → 补强剂、填充剂 → 硫磺 优点:胶料品种多,可以制造特殊胶料
缺点:粉剂飞扬,劳动强度大,效率低,规模小 生产中,各种配合剂与橡胶混炼成母炼胶,提高 混炼均匀性,减少粉剂飞扬,提高生产效率
(2)密炼机混炼
生胶和配合剂在混炼室中混合,在压延机上压制成 片;然后加入硫化剂和需低温加入的配合剂,压炼 2种混炼工艺 一段混炼:通过密炼机和压延机的一次混炼就得 到均匀混炼胶 两段混炼:通过密炼机和压延机的两次混炼而得 到均匀混炼胶
2、压延的影响因素
1、压延的方法
(A)胶片压延
积胶
天然橡胶不积胶,丁苯橡胶要积胶
(B)压型
使胶料压制成具有一定断面形状或表面有某种花纹
(1)压型的原理பைடு நூலகம்
据胶料流动性的变化,急速冷却,使花纹定型
(2)压型的要求
压型要求规格准确、花纹清晰、胶料致密性好
(C)织物挂胶
在骨架织物上覆上一层薄胶(贴胶、擦胶)
(1)挂胶目的
密炼机混炼,二段混炼,ZnO第二段混炼加
塑炼
混炼
Mixing
Plastication
Calendering Extrusion
三、橡胶的压延
橡胶压延过程
胶料热炼、 供胶
压延
半成品
冷却、卷取、 截断、放臵
橡胶压延的用途 将胶料制成一定厚度和宽度的胶片 在胶片上压出某种花纹 在骨架织物上覆上一层薄胶(贴胶、擦胶)
2、混炼的机理
塑炼胶与配合剂的混合、分散和产生结合等过程, 同时也包含橡胶发生的各种流动过程 橡胶是粘度很大的 热塑性的粘流体, 处于流动状态
炭黑的均匀分散过程 (1)炭黑颗粒的润湿
炭黑颗粒被生胶润湿→包容橡胶,炭黑空隙体积
减小直至零,体系比体积减到最小,润湿过程结束
V比 = V生胶 + V炭黑 + V空隙
(2)温度的影响
开炼,T↓,粘度↑,分子链伸直,剪切力↑,效率↑ 密炼,T ↑ ,氧活性 ↑ ,塑炼效率 ↑
(3)氧的影响
氧↑ ,塑炼效率 ↑
(4)化学塑解剂的影响
化学塑解剂会加速橡胶塑炼过程
5、常用橡胶的塑炼特性
(1)天然橡胶
开炼,低温(40~50℃)薄通(辊距0.5~1mm)
密炼,温度~155℃
加入表面活性剂,改善无机填料与橡胶之间界面
(2)配合剂的尺寸与结构
粒子越小,越难分散 结构性强(二次结构),空隙大,易分散
5、常用橡胶的混炼特性
(1)天然橡胶
天然橡胶塑性增加快,发热量少,配合剂易分散
混炼时间长,对胶料性能影响比合成橡胶大 开炼机混炼,辊温50~60℃,前辊比后辊高~5℃ 密炼机混炼,多一段混炼
使织物的线与线、层与层之间互相紧密的贴合成整体, 共同承受外力的作用;
提高织物弹性、防水性,保证制品有良好的使用性能
(2)贴胶
用压延机上两个辊筒的压力,将一定厚度的胶片贴在 织物上的过程
(3)压力贴胶
用积胶的压力,将胶料挤压到布缝中,与贴胶共用
(4)擦胶
用压延机辊筒转速不同产生的剪切力和辊筒的压力, 将胶料擦入到布缝中的过程。一般只适于帆布