自硬砂造型工艺研究.
树脂自硬砂烘干工艺

树脂自硬砂烘干工艺## 树脂自硬砂烘干工艺### 引言树脂自硬砂烘干工艺是一种常见于铸造工业中的重要工艺流程。
该工艺通过对含有树脂的砂型进行烘干,使其树脂固化并形成坚硬的砂型,以便于后续的铸造操作。
本文将对树脂自硬砂烘干工艺的原理、流程以及应用进行详细阐述。
### 原理树脂自硬砂烘干工艺的原理主要是通过热能将砂型中的树脂加热至一定温度,从而使树脂发生固化反应,形成硬度适宜的砂型。
通常,树脂自硬砂中的树脂成分具有一定的固化温度范围,通过控制烘干温度和时间,可以实现树脂的充分固化而不发生过度固化或不完全固化的情况。
### 流程树脂自硬砂烘干工艺的主要流程包括:1. **准备砂型**:首先,需要制备含有树脂的砂型,通常采用砂型制备设备将树脂与砂料混合,并在模具中成型。
2. **烘干预处理**:将制备好的砂型放置于烘干设备中,进行预处理。
预处理的目的是去除砂型中的水分和挥发性有机物,以避免在后续的加热过程中产生气泡或裂纹。
3. **加热固化**:将预处理后的砂型置于烘箱或烘干室中,通过加热使树脂固化。
在此过程中,需要控制好烘干温度和时间,以确保树脂能够充分固化而不出现质量缺陷。
4. **冷却处理**:待树脂固化完成后,将砂型从烘干设备中取出,进行冷却处理。
冷却处理有助于提高砂型的强度和稳定性,以便于后续的铸造操作。
### 应用树脂自硬砂烘干工艺广泛应用于各种铸造工艺中,特别适用于精密铸造和小批量生产。
其主要应用领域包括汽车制造、航空航天、机械制造等行业。
通过树脂自硬砂烘干工艺,可以制备出形状复杂、精度高的铸件,满足不同行业对铸造产品质量和性能的要求。
### 结论树脂自硬砂烘干工艺作为铸造工业中的重要工艺流程,在实际生产中发挥着重要作用。
通过本文的介绍,读者可以了解到该工艺的原理、流程及应用,为相关领域的工程技术人员提供了参考和借鉴,促进了铸造工艺的发展与应用。
新型水玻璃自硬砂工艺在铸钢生产中的应用

新型水玻璃自硬砂工艺在铸钢生产中的应用一.前言目前国内外冷凝自硬砂工艺主要分为二大类:无机类粘结剂以水玻璃砂工艺为主,有机类粘结剂以呋喃和碱性酚醛树脂砂工艺为主。
以上二大类自硬砂工艺在二十世纪下半期至今在全世界铸造业应用并不断成熟完善。
但此二种工艺在性能上各有特点,也存在问题。
特别在铸钢、合金钢件的铸造时有明显工艺上的不足。
CO2硬化水玻璃加入量高(一般为7%~8%),砂的残留强度高,溃散性差,旧砂再生回用困难。
有机粘结剂树脂砂工艺的出现,在一定程度上解决了CO2水玻璃砂的固有缺陷,但碱性酚醛树脂成本高,呋喃树脂砂易出现铸件裂纹、气孔等缺陷。
水玻璃“新三法”(VRH、微波烘硬、有机脂)的问世,使水玻璃的加入量降低了一半,溃散性大有改善,但新“三法”在工艺上存在着一定的缺陷,VRH 法因设备投资大及铸件尺寸受真空室限制;微波烘硬法因铸型吸湿性强及电微波转化率低;回用砂率综合性能差等缺点,严重制约了水玻璃砂的发展。
随着水玻璃基础理论研究的不断进展,水玻璃砂溃散性差和旧砂再生困难等缺点并非水玻璃的固有特性。
它来源于对水玻璃化学和胶体化学认识不足和使用不当(1)。
目前国内以沈阳汇亚通铸造材料有限责任公司等单位在这方面的研究取得了领先。
他对普通水玻璃进行一系列化学和物理改性及电离子架接,研制开发了新型水玻璃和专用酯类固化剂自硬砂工艺,为水玻璃砂的第三次中兴产生了质的飞跃。
二.新型水玻璃酯硬砂工艺的应用我公司年产阀门承压铸钢件2000余吨,产品以单价小批量为主,壳体主要壁厚10~60mm,且薄件居多。
材质牌号有普通碳素钢,耐热耐高温铬钼钢、铬钼钡钢及各种耐酸不锈钢。
其中有30%是电站阀门铸件,有20%左右是出口阀门配套铸件。
因此,对造型工艺及材料要求相当苛刻。
我们于2000年下半年开始对原粘土砂工艺进行技术改造,要求采用新工艺、新材料,以低成本高质量满足当前生产及市场竞争的需要,在选择工艺方案阶段,我们对普通水玻璃自硬砂,呋喃树脂自硬砂及新型水玻璃自硬砂三种砂型工艺,分别在不同材质、不同品种的阀门铸钢件上进行了工艺试验,试验用原砂为福建平潭优质擦洗硅砂,粒度为40/70目,SiO2含量≥96%,含泥量和含水量分别≤0.5%,角形系数≤1.25%,硬化性能冬季,硬透性较差硬化时间可调性差硬透性好,硬化时间可调硬透性好,硬化时间可调热裂倾向中易裂小操作环境无毒、无气味气味大无毒、无气味旧砂再生回用率≥60%≥90%≥85%工艺配比粘结剂4% 1.0%~1.2% 1.8%~2.5%固化剂占粘结剂量12%~15%占粘结剂量50%~60%占粘结剂量15%~20%材料成本(元/吨型砂)288245.04214.3材料单价(元/吨)水玻璃:800化剂:1700树脂:12600固化剂:3400水玻璃:2100固化剂:1700注:新砂成本210元/吨,再生砂成本为新砂成本的三分之一即70元/吨从表1可见,新型水玻璃自硬砂工艺具有成本低,操作方便,铸件表面质量好,无毒无污染,发气量低,热裂倾向小,旧砂回用率高,特别对单件小批量、薄壁易裂的合金钢件,更具有突出的经济和社会效益。
浅谈呋喃树脂自硬砂的生产及应用
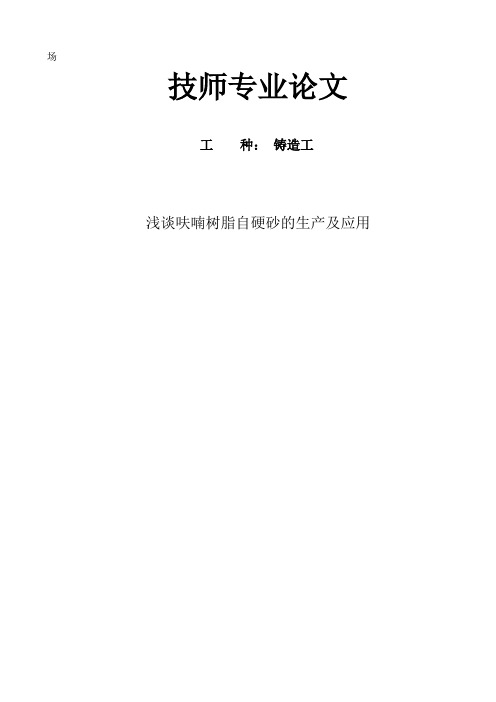
场技师专业论文工种:铸造工浅谈呋喃树脂自硬砂的生产及应用摘要 (2)引言 (2)1.呋喃树脂砂性能的优缺点 (2)2.呋喃树脂自硬砂的生产工艺技术 (3)3.工艺及现场控制 (6)4.呋喃自硬树脂砂铸件的缺陷分析及防止措施 (8)5.结论 (9)参考文献 (10)本论文针对呋喃树脂自硬砂的坭芯生产,阐述了呋喃树脂自硬砂的原材料配比、混制及硬化工艺。
结合作者多年在实际生产工作中的经验,就生产中出现的实际问题进行分析和讨论,通过采取文中提出的控制、解决措施,有效地解决了铸件出现的气孔、粘砂、热裂、冲/夹砂、脉纹等铸造缺陷。
关键词:呋喃树脂自硬砂、铸造缺陷、夹砂、热裂、脉纹引言呋喃树脂自硬砂工艺是指在呋喃树脂砂中加入一定量的酸性固化剂,使之在芯盒或砂箱内经历一定时间后,在常温条件下通过自行硬化成型(不需烘烤或吹入硬化气体)的一种造型制芯工艺。
呋喃树脂自硬砂硬化反应机理可简单描述为:涂敷在砂粒表面的树脂在酸性固化剂的催化作用下,呋喃树脂分子上的活性氢、羟甲基与羟甲基之间发生缩聚反应和呋喃环上的双键打开发生加成聚合反应,形成三维网状结构固体树脂,使型(芯)砂硬化成型。
1.呋喃树脂砂性能的优缺点1.1优点1)铸件的尺寸精度高、外部轮廓清晰、铸件表面光洁,外观质量好、组织致密、铸件综合品质高。
2)呋喃树脂自硬砂具有较好的流动性,容易紧实,脱模时间可调节,硬化后强度高,在其后的搬运及合箱过程中不变形,因树脂砂的强度高,在浇注和凝固过程中基本上不会出现位移现象,所以铸件的尺寸精度高。
3)不用烘干,缩短了生产周期、节省了能源、芯砂易紧实、溃散性好、容易清理、大幅度降低了劳动强度,为实现机械化生产创造了条件。
1.2 呋喃树脂自硬砂的不足之处1)对原砂质量要求高2)在生产过程中有刺激性气味3)采用树脂砂生产,成本较高2.呋喃树脂自硬砂的生产工艺技术2.1 原材料的选用1)铸造用砂的要求:原砂对呋喃树脂砂的性能、粘结剂用量、以及对铸件表面质量的影响很大,要求原砂中的SiO2含量要高、含泥量和酸耗值要低。
自硬树脂砂造型工艺守则

自硬树脂砂造型工艺守则1准备1.1 熟悉工艺图纸,了解铸件形状、浇冒口和出气系统的位置。
1.2 准备好造型使用的工具、护具和辅助材料。
1.3 检查模型、浇注系统是否齐全完好。
有下列情况者应修复后再用。
1.3.1 模型破损、变形及尺寸不符合图纸规定及表面粗糙不平。
1.3.2 活块不全、位置不当、安装松紧不合适。
1.3.3 上、下模型定位销、孔配合松紧不合适。
1.3.4 模型的起模装置、吊运装置安装不合适。
1.4 模型必须均匀涂刷脱模剂,其干燥后方可使用。
1.5 清理造型底板,按工艺规定摆放砂箱。
砂箱有下列情况不能使用。
1.5.1 箱把脱落或有严重变形。
1.5.2 箱壁破裂未经修补,箱带严重损坏或影响浇冒口安放。
1.5.3 砂箱翘曲变形严重。
1.5.4 定位销、定位销套孔磨损超过极限偏差,见表1表1 ㎜1.5.5 销套孔内有严重锈皮或粘铁粘砂未清除。
1.6 检查造型设备,各电器开关、阀门应处于非工作状态,液压润滑应充分,树脂、固化剂的储量应充足。
1.7 检查树脂、固化剂加入量调节旋钮是否在规定刻度上,要定期测试砂子流量、树脂流量、固化剂流量的准确性,一般每月检查两次。
遇型砂强度或硬化不正常时要及时测试。
2 造型2.1 造型底板防平、垫实,木质底板要均匀支撑,不变形。
模型上的粘砂要擦净。
2.2 使用非加工砂箱将箱口垫平,加工砂箱的接触面不得有粘附物。
2.3 浇冒口、出气棒的放置应符合工艺要求,操作中用先填少量型砂适当捣实来定位。
2.4 局部使用冷铁时,应按工艺规定放置。
冷铁表面不得有锈蚀、油污、粘砂等。
2.5 放砂时,头砂(约5~10㎏)不能直接接触模型表面,可掺入砂型中间作填料用。
对于较大铸件,放砂采用推进式。
舂砂时使用橡胶舂头或木棒,应避免活块、浇冒口、出气棒的移位,注意模型周围、浇冒口根部以及流砂不易充填部位要舂实。
2.6 砂箱填满后刮平,扎Φ4~Φ8气眼,每100×100㎜范围内不少于1~2个,气眼距模型表面40~60㎜。
树脂自硬砂烘干工艺
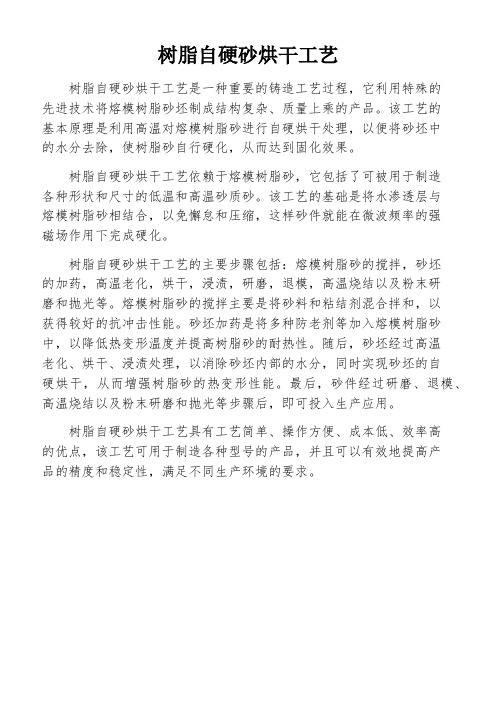
树脂自硬砂烘干工艺
树脂自硬砂烘干工艺是一种重要的铸造工艺过程,它利用特殊的
先进技术将熔模树脂砂坯制成结构复杂、质量上乘的产品。
该工艺的
基本原理是利用高温对熔模树脂砂进行自硬烘干处理,以便将砂坯中
的水分去除,使树脂砂自行硬化,从而达到固化效果。
树脂自硬砂烘干工艺依赖于熔模树脂砂,它包括了可被用于制造
各种形状和尺寸的低温和高温砂质砂。
该工艺的基础是将水渗透层与
熔模树脂砂相结合,以免懈怠和压缩,这样砂件就能在微波频率的强
磁场作用下完成硬化。
树脂自硬砂烘干工艺的主要步骤包括:熔模树脂砂的搅拌,砂坯
的加药,高温老化,烘干,浸渍,研磨,退模,高温烧结以及粉末研
磨和抛光等。
熔模树脂砂的搅拌主要是将砂料和粘结剂混合拌和,以
获得较好的抗冲击性能。
砂坯加药是将多种防老剂等加入熔模树脂砂中,以降低热变形温度并提高树脂砂的耐热性。
随后,砂坯经过高温
老化、烘干、浸渍处理,以消除砂坯内部的水分,同时实现砂坯的自
硬烘干,从而增强树脂砂的热变形性能。
最后,砂件经过研磨、退模、高温烧结以及粉末研磨和抛光等步骤后,即可投入生产应用。
树脂自硬砂烘干工艺具有工艺简单、操作方便、成本低、效率高
的优点,该工艺可用于制造各种型号的产品,并且可以有效地提高产
品的精度和稳定性,满足不同生产环境的要求。
自硬砂树脂砂工艺问答

自硬砂树脂砂工艺问答自硬砂树脂砂工艺问答■ 济南圣泉集团股份有限公司张本水李长元朱能山1.为什么磷酸多用作高氮呋喃自硬树脂的固化剂,而很少用作低氮呋喃自硬树脂的固化剂?这是因为低氮高糠醇树脂,采用酸做固化剂时,硬化速度慢,脱模时间长,且强度很低。
高氮低糠醇树脂使用磷酸做固化剂可获得必要的硬化速度。
而且,高氮低糠醇树脂采用磷酸作催化剂可获得很好的终强度。
造成这种结果的原因主要是由于磷酸与糠醇的互溶性差,而与水的亲和力大,使得树脂和催化剂中所含的水分以及树脂在缩聚反应中生成的水不易扩散排出而以磷酸为核心生成水滴残存于树脂膜中,破坏了树脂膜的致密性,故强度较低。
而高氮树脂与水的互溶性好,各种水分不易以磷酸为核心集中为水滴,树脂膜结构好,强度高。
2.为什么酚脲脘自硬树脂的硬透性比呋喃自硬树脂砂好?因为酚脲脘树脂的固化过程是聚合反应,固化过程中不产生小分子的水,不存在因型内外水分的挥发速度不同使其内外固化速度不一致的问题,而呋喃自硬树脂的固化过程是缩聚反应,反应过程中产生水分,因型芯内外的水分蒸发速度不同,导致了其内外固化速度不同,故其硬透性差些。
这也是呋喃自硬树脂砂的固化速度受空气相对湿度影响较大的原因。
3.为什么生产铸铝,铸铜件可以选用高氮呋喃树脂?由于铝、铜金属液对氮几乎不溶解,因此,即使使用高氮树脂在浇注过程中树脂分解产生的氮,也不会被铝、铜金属液吸收,也就不会在凝固过程中因析出氮而形成氮气孔。
因此,生产铸铝、铸铜件可以为潢足溃散性的需要而选用高氮树脂。
4.为什么自硬树脂砂生产重量大的铸件,浇注系统宜于用陶瓷管制作?采用自硬树脂砂造型,当生产重量较大的铸件时,由于浇注时间长,浇注系统在高温金属液的长时间热作用下,易使树脂砂过早溃散丧失强度,造成冲砂缺陷,因此,对重量较大的铸件,浇注系统宜用陶管制作,同时使浇注系统特别是直浇道不易上涂料的问题得到解决。
5.采用自硬树脂砂造型、制芯时,如何确定树脂砂的可使用时间是否满足要求?当采用间歇式混砂机时,树脂砂的可使用时间要大于树脂砂从混好卸砂到用完的这段时间;当采用连续式混砂机造型、制芯时,树脂砂的可使用时间要大于从混砂机的出砂口起始放砂位置到又回到该位置连续放砂的这段时间。
生产铸钢件用几种自硬砂工艺综述
( h n a gH iao gF u dn aei o , t ,S e yn 1 1 1 C ia S ey n uy tn o n igM tr l .L d h n a g1 0 4 ቤተ መጻሕፍቲ ባይዱ hn ) aC
Ab t a t Th d a a e n ia v n a e f s l h r e i g s n u h a u a e i sr c : e a v nt g s a d d s d a t g s o e f a d n n a d s c s f r n r sn, b sc r s n e t p — a i e i a d n w y e n
摘 要 : 绍 用 于 生 产 铸 钢 件 的 呋 喃 树 脂 自硬 砂 、 性 树 脂 自硬 砂 和 新 型 水 玻 璃 自硬 砂 , 述 各 型 砂 工 艺 的 优 缺 点 , 高 温 性 能 介 碱 叙 从
和发 气性检 测 看 , 序 结果 当属 水 玻璃 自硬 砂 最佳 。由 于在 铸 件 品质 、 排 生产 成 本 以及 环 保 等诸 方 面具 有优 势 , 用势 头 强劲 应
s du ic t o d d s n r n r d c d o imsl ae b n e a d a e ito u e .Ba e n t er s l fhg e p r t r r p rya d g se ou in ts . i sd o h e u t o ih t m e au e p o e t n a v lt e t s o
生 产 铸 钢 件 可 供 选 择 的 型 砂 工 艺 有 : 喃树 脂 自 呋 硬 砂 、 性 树 脂 自硬 砂 和 新 型 水 玻 璃 自硬砂 。 碱
新型改性铸造用磷酸盐无机树脂自硬砂性能的研究
Fig. 1 Sto ring time measur atio n of pho sphate self - har dening
2. 2
常温抗压强度与粘结剂加入量的关系 表 3 为试样制样后 24 h 的强度。可见随粘结剂
加入量的增加, 试样强度也不断地提高。由于粘结剂 在砂粒之间起着联结/ 桥0 的作用, 粘结剂必须完全包 覆在每个砂粒表面, 太少的粘结剂会使砂粒得不到完 全包覆, 从而削弱 / 桥0 的作用, 使砂型 或砂芯强度不 高。但太多的粘结剂使混砂变得困难, 成本也随之增 高。粘结剂的加入量主要应根据砂的质量、 粒度粗细 和砂型或砂芯所需要的强度确定。
摘要 : 研究了一种适用于铸造的粘结剂 ) 磷酸盐无机树脂 。 通过对传统的磷酸 盐进行改 性 , 解决 了磷酸盐 抗吸湿性差 及存放 稳定性差的问题 , 并保持了其良好的溃散性及无害性 , 属绿色环保型铸造材料 。 关键词 : 磷酸盐无机树脂 ; 抗吸湿性 ; 稳定性 ; 溃散性
中图分类号 : TG 22 文献标识码 : A 文章编号: 1000 -8365( 2005) 04 -0268 -02
表 4 试样的强度与试样在高湿度环境 中存放时间的关系 T ab. 4 T he relation betw een the specimens. st reng th and the sto ring time in hig h humidity env iro nment 吸湿时间 / h 抗压强度 / M Pa 0 8 16 32 40 80 200
表3 T ab. 3 无机树脂试样的抗压强度 T he strength r esisting compressio n o f the specimens 2 1. 22 3 1. 45 4 1. 70 5 2. 6
潮模砂与自硬砂造型工艺方案选用
潮模砂与自硬砂造型工艺方案选用姜仁华;吴殿杰【摘要】目前砂型铸造车间最主要的铸造方法为潮模砂(湿型黏土砂)造型工艺和自硬砂造型工艺两大类.本文简单介绍两种造型工艺及装备的应用现状并提出针对不同材质和用途及批量铸件生产纲领的特点,如何选择潮模砂工艺和自硬砂工艺.【期刊名称】《铸造设备与工艺》【年(卷),期】2016(000)002【总页数】9页(P56-63,68)【关键词】潮模砂;自硬砂;性价比【作者】姜仁华;吴殿杰【作者单位】无锡锡南铸造机械股份有限公司,江苏无锡414142;机械工业第九设计研究院有限公司,吉林长春130011【正文语种】中文【中图分类】TG24主题词:潮模砂;自硬砂;性价比砂型造型工艺在铸件生产过程中是关键工序,它直接影响铸件的质量水平、生产成本、生产效率及环境污染程度。
目前铸造车间最主要的砂型铸造方法为潮模砂(湿型黏土砂)造型工艺和自硬砂造型工艺两大类[1]。
用黏土作为黏结剂潮模砂造型方法生产铸件,是历史悠久的工艺方法,也是应用范围最广的铸造工艺。
尤其大批量的汽车发动机铸件、农用拖拉机铸件多采用潮模砂造型工艺;球铁件主要产品是汽车底盘类铸件(主减速器壳体、差速器壳体、制动器钳体和支架)、发动机曲轴和凸轮轴等。
缸体造型线主要以水平分型气流预紧实加压实的静压线。
尤其是青岛昆格瓦格纳(青岛)的KW静压线、德国HWS公司静压线等发展成熟的静压造型。
汽车、拖拉机底盘保安件等大批量生产的中小铸件一般采用垂直或水平分型造型,如DISA、华佩、新东、亨特和东久造型线等。
上述是目前潮模砂铸造造型工艺的最新代表,都是追求提高砂型紧实的均匀性,从而保证砂型的表面光洁,尺寸精确,内部致密性。
2.1 水平分型静压造型工艺大多数静压线都是用来生产汽车零部件的,少数是用来生产拖拉机或者其他行业铸件的。
据不完全统计,在国内静压线应有300条左右,这个数据包括KW、HWS、BMD以及济南铸锻所、苏铸成套、保定维尔等静压线,并且主要应用在汽车铸件领域。
铸钢常用自硬砂工艺的选用-无锡铸钢型砂专题会议论文董鄂 (1)
铸钢常用自硬砂工艺的选用董鄂李伟(无锡锡南铸造机械有限公司,江苏无锡,214142)摘要:本文从工艺特性、旧砂再生、环保和经济成本等四个方面对五种常用的铸钢自硬砂,即呋喃树脂砂、碱酚醛树脂砂、酯硬化水玻璃砂、Pep-Set树脂砂和邦尼树脂砂进行了分析和比较,提出了选用的参考性建议。
关键词:铸钢型砂工艺选用一、前言近半个多世纪来,在我国铁路、重机、工程机械、船舶、阀门、冶金机械等行业的铸钢件生产中,酯硬化水玻璃砂工艺、呋喃树脂砂工艺、Pep-Set树脂砂工艺、碱酚醛树脂砂工艺、邦尼树脂砂工艺等自硬砂工艺得到广泛应用,生产出了许多我国铸造史上重量创记录的特大型铸钢件和其他一些有代表性的铸钢件;诞生了各种铸钢自硬砂自动化生产线,及配套的旧砂再生线,标志着我国铸钢型砂工艺和铸造装备很大的技术进步。
对广大铸钢自硬砂用户来说,如何选用最适合本企业产品生产的型砂工艺是一个重要的问题,它涉及到产品的质量、生产效率、经济成本、旧砂的再生利用、环境保护等诸多方面,在建厂、改造之前必须加以科学地、综合地比较和论证才能达到预期的效果。
以下就目前铸钢生产中常用的五种型砂工艺作一粗略的分析、比较,供铸造业同行作为设计选型时参考。
二、几种常用铸钢自硬砂型砂的工艺、再生及环保特性2.1呋喃树脂自硬砂这是应用于铸造业最多、最广、工艺及配套设备最成熟的一种自硬砂工艺,相对其他树脂砂工艺铸件成本较低、旧砂利用率高、旧砂再生简单,是常用的自硬砂工艺。
呋喃树脂砂在灰铁、球铁、铸钢、有色等铸造中都得到广泛地应用。
但由于呋喃树脂砂高温退让性差,树脂中含有较高的N,固化剂中含有S,因此一些壁厚不匀的铸钢件容易造成热裂,厚大铸钢件易造成N气孔,一些低碳铸钢件还易造成增碳,所以在铸钢件生产中选用应慎重考虑。
其主要技术参数及特点如下:○1树脂加入量:0.8~1.1%○2可使用时间为:1~20min○3起模时间为:15~60min○4常温及高温强度是所有铸钢自硬砂中最高的;24小时抗拉强度:0.8~1.2Mpa。
- 1、下载文档前请自行甄别文档内容的完整性,平台不提供额外的编辑、内容补充、找答案等附加服务。
- 2、"仅部分预览"的文档,不可在线预览部分如存在完整性等问题,可反馈申请退款(可完整预览的文档不适用该条件!)。
- 3、如文档侵犯您的权益,请联系客服反馈,我们会尽快为您处理(人工客服工作时间:9:00-18:30)。
自硬砂造型工艺研究
随着机械行业的发展,对外经济贸易的扩大,以及环境污染、能源紧张、材料涨价等问题的日益严重,对铸造生产和铸件质量提出了更高的要求,要能满足这些要求,特别是造型制芯工艺的选择上更应满足这些要求,先进造型制芯工艺应具备以下基本条件:
①生产的铸件质量好、尺寸精度高、铸造缺陷少;
②劳动条件好、环境污染少;
③生产成本低、生产效率高;
④最大限度地利用自然资源、节省能源。
传统的型砂工艺已经不能满足以上的条件,这就要求选用适合自己的先进型砂工艺。
近几年来,主要使用的先进型砂工艺有:新型水玻璃自硬砂工艺、碱性酚醛树脂自硬砂工艺和呋喃树脂自硬砂工艺等自硬砂型砂工艺。
下面以我们公司为例对型砂工艺进行简单阐述:
一.型砂工艺的选用
1.现用型砂工艺性能分析
1.1现用造型材料及造型方式
(1)面砂、芯砂——CO
硬化水玻璃砂、“70”砂、铬铁矿砂
2
(2)背砂——粘土砂
(3)手工造型
(4)烘干窑烘干小型砂型及坭芯,移动烘干大型砂型
(5)表面刷醇基涂料
1.2现造型材料的生产特点
(1)人工加砂,劳动强度大,生产效率低,砂型、坭芯的紧实度主要靠人工打风锤,硬化主;
要吹CO
2
(2)水玻璃加入量高(≥9%),造成成本高,型(芯)砂溃散性差,铸件清理难度大,效率低;
(3)旧砂直接破碎再生,再生后只能作背砂,不能作面砂,回用率低,新砂耗量高,型砂成本高,废砂大量排放,严重污染环境;
(4)铸件尺寸精度低,表面粗糙度差,铸件综合质量不高,后道工序工作量增大,工作效率就低;
(5)型(芯)砂冬季硬透性差,CO
耗量大。
2
1.3铸件质量情况
铸件尺寸精度低,表面粗糙,多气孔、砂眼,产生裂纹多,导致后道工序修理大,成本高,效率低。
2、新型水玻璃自硬砂工艺性能分析
2.1原辅材料
(1)原砂:新工艺对原砂要求较高,尽可能选取泥份、微粉含量少,颗粒形貌好的原砂(2)改性水玻璃
(3)有机酯固化剂
2.2工艺优势及特点:
(1)水玻璃加入量大大降低(2.5--3.5%);
(2)型砂溃散性大大改善,铸件清砂容易;
(3)旧砂可干法再生回用,回用率≥80%;
(4)系列化水玻璃与固化剂配套使用,型砂综合工艺性能优良,冬季硬透性好,硬化速度可调(10-90 min),可实现大批量机械化生产;
(5)有效防止铸件裂纹、气孔等缺陷,铸钢件综合质量优于呋喃树脂砂工艺的铸件;
(6)生产成本低,劳动环境好,环境污染少。
2.3工艺存在的问题:
|(1)型芯砂溃散性得到大幅度改善,但仍不及树脂砂工艺;
(2)型芯在湿度较大时有吸湿现象,需在设备、工艺上采取适宜的措施,加强生产管理和型砂工艺控制。
3、呋喃树脂自硬砂工艺:
3.1工艺优势及特点:
(1)铸件表面质量好、尺寸精度高;
(2)型芯溃散性好,铸件落砂清理容易;
(3)旧砂干法再生回用容易,回用率高(≥90%);
(4)提高工艺装备水平和生产效率,降低工人劳动强度。
3.2工艺及设备现状:
(1)机器化的生产线造型制芯,人工辅助;
(2)采用型内硬化,硬化后起模,辅助型外表干;
(3)采用机器化的旧砂再生回用生产线,干法再生回用容易,回用率约90% 。
3.3工艺存在的问题:
(1)型芯砂高温退让性差,铸件裂纹倾向大,尤其是薄壁、壁厚差大、结构复杂的铸件更易产生;
(2)固化剂含S,易导致铸件表层增硫,造成表面微裂纹;
(3)型砂发气量大、且迅速,铸件易产生气孔缺陷;
(4)铸件焊补回火率高,清整成本高,铸件综合成本较高;
(5)混砂、造型、浇注、保温、落砂过程中产生SO
2、H
2
S、CO等有害气体,作业环境差,污染
环境;
(6)废弃物中的呋喃是持久性污染物,已列入《斯德哥尔摩公约》十二种物质黑名单,全球即将禁止使用。
根据我们公司产品生产特点来说,新型水玻璃自硬砂工艺是最适合我们的型砂型砂工艺,所以我们选用新型水玻璃自硬砂工艺作为我们的新的型砂工艺。
二、新型水玻璃自硬砂工艺
1、新工艺用原砂
新工艺对原砂的要求与树脂砂类似,但比树脂对原砂的敏感性小,并且原砂适用范围广,可以用硅砂,铬铁矿砂,镁橄榄石砂等多种砂,其指标要求如下:
粒度 30--100
角形系数 <1.45
含水量 <0.5%
2、混砂工艺
原砂+酯固化剂――混砂―― +粘结剂――混砂―― 出砂
3、新工艺的型砂配制
型砂的硬化性能受原砂质量,粘结剂和固化剂的种类及加入量、外界环境条件、混砂工艺设备等因素影响,使用厂可根据现场原砂的种类、状态,型(芯)砂的生产工艺要求,外界条件(温度、湿度)选择相应的粘结剂、固化剂的种类及加入量来调整型砂的硬化性能,满足铸件生产的要求。
下表为推荐的型砂配比:
表1 推荐配比
1.型砂实验室的建立
1.1型砂试验室检测仪器
(1)SHY树脂砂混砂机一台
(2)SWY液压强度试验机或XQY-Ⅱ型智能强度机一台
(3)SSZ震摆式筛砂机一台
(4)∞字试样芯盒两个,非金属的,每个芯盒可制12个∞字试样
1.2化学分析试验仪器
(1)红外线电烘箱一台(300℃)
(2)万分之一g分析天平一台
0~1000g托盘天平一台
0~500g托盘天平一台
(3)0~200g电子天平一台(分度值0.01g)
(4)磁力加热搅拌器一台(78-Ⅰ型)
(5)玻璃器皿:
烧杯:200ml, 100ml, 50ml 若干
量筒:200ml, 100ml, 50ml,10 ml若干
移液管:10 ml 两支
酸、碱式滴定管:25ml 各一支
锥型烧瓶:25ml 若干
温度计:100℃若干
(6)湿温度计
(7)秒表一块
在公司原来实验室的基础上,我们替换掉了陈旧老损的实验器材。
2.原砂的选用
原砂的一些指标对强度影响较大,我们按以下要求选用原砂:SiO
≥97%,角形因数<1.20,
2
微粉≤0.8%,含泥量≤0.3%,含水量≤0.5%,砂温≤35℃,粒度40-100目,用福建平潭标准砂和漳浦标准砂来进行工艺验证
3.水玻璃和固化剂的选用
对于自硬砂,关键的就是改性水玻璃和固化剂,所以,选用合适的水玻璃和固化剂尤其重要。
经过多方考察及同行的建议,我们选用重庆和深圳两厂家提供的水玻璃和固化剂来进行实验。
4.型砂工艺
原砂+酯固化剂――混砂(30秒)―― +水玻璃――混砂(30秒)―― 出砂
5.实验结果
我们根据不同的配比、不同的原砂和不同单位提供的水玻璃、固化剂进行了多组实验,下面
四、结论
新型水玻璃自硬砂工艺不管在铸件质量,还是在减少工人劳动强度,尤其是在节能减排上都是比较理想的型砂工艺。
对于企业,不仅要考虑可观的经济效益,更要考虑怎么样去节约能源、减少环境的污染。
所以,就要根据自己的实际情况去选择适合自己的型砂工艺。