检查、试验和检验的控制程序Examination, Test and Inspection Control
014检验、测量和试验设备控制程序
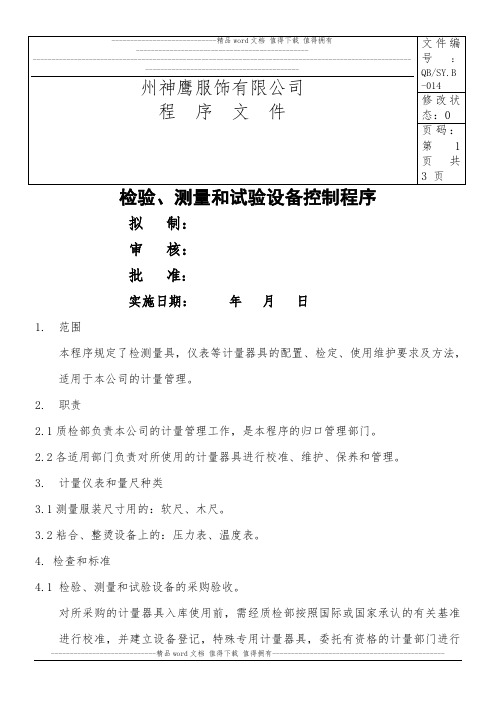
检验、测量和试验设备控制程序拟制:审核:批准:实施日期:年月日1. 范围本程序规定了检测量具,仪表等计量器具的配置、检定、使用维护要求及方法,适用于本公司的计量管理。
2. 职责2.1质检部负责本公司的计量管理工作,是本程序的归口管理部门。
2.2各适用部门负责对所使用的计量器具进行校准、维护、保养和管理。
3. 计量仪表和量尺种类3.1测量服装尺寸用的:软尺、木尺。
3.2粘合、整烫设备上的:压力表、温度表。
4. 检查和标准4.1 检验、测量和试验设备的采购验收。
对所采购的计量器具入库使用前,需经质检部按照国际或国家承认的有关基准进行校准,并建立设备登记,特殊专用计量器具,委托有资格的计量部门进行检验。
4.2 对于软尺、木尺,应用钢尺进行对比,对比校准合格的应由质检部编号登记,并标识其合格及校准时间,方可发放;对比相差1mm的为不合格,不准使用,对刻度模糊不清的、破损的应报废不得使用,对于长期使用因磨损不能使用的软尺、木尺应以旧换新,由质检部核实并发放合格的量尺。
质检部每月对软尺进行校准,木尺半年一次,并做好校准记录。
4.3 对于设备上的压力表、温度表,应委托有资格的计量部门进行检查鉴定,鉴定合格方可使用,并随机挂上鉴定合格证,每年进行一次校准,并作好校准记录。
对不能拆卸的仪表由质检部组织技术部、生产部在车间现场鉴定,按工艺规程加工产品合格,仪表在规定范围内,经分管领导审批准用证。
4.4 当校准发现偏差时,应从该计量器具所使用日期开始,对已测量的产品应从新进行测量和评定,确保产品符合规定要求。
5. 计量器具登记和管理5.1质检部应对量尺和压力表进行编号、登记、标识、校准、发放记录,明确使用人。
5.2 质检部应定期抽查各生产工位所使用的量尺进行校准,确定计量器具是否合格,对不合格的应及时收回,并补发合格的量尺,还应在台帐上作好更换补发记录。
5.3 对于失准的压力表或温度表,应及时送外检查鉴定或修理,保证其准确性。
检验和试验状态控制程序

检验和试验状态控制程序
(总3页)
本页仅作为文档封面,使用时可以删除
This document is for reference only-rar21year.March
1 目的
本程序规定了对公司的物料、过程产品及成品的检验和试验状态进行标识,以标明是否经检验和试验合格,确保只有经检验和试验合格的产品才能投入使用、转序和交付。
2范围
适用于本公司产品实现全过程的检验和试验状态的标识。
3 引用文件
下列文件所包含的条文,通过在本程序中引用而构成本程序的条文,在文件出版时,所示版本均为有效,所有文件都会被修订,应用本程序的各方应探讨使用下列文件最新版本的可能性。
QS/ 进货检验和试验程序
QS/ 过程检验和试验程序
QS/ 最终检验和试验程序
QS/ 产品标识和可追溯性控制程序
QS/ 不合格品控制程序
QS/ 顾客财产管理程序
4 定义
无
5 职责
质管部负责检验和试验状态标识方案的设计、生产过程执行情况的监督。
生产部负责外协、外购产品的检验和试验状态区域划分及标识实施。
生产车间负责产品在生产过程中的检验和试验状态区域划分及标识实施。
质控科负责成品检验及包装过程的检验和试验状态区域划分及标识实施。
6 工作描述
7 记录与表格无
8 附件
检验和试验状态控制流程图(附录A)
生产部
仓库保管员质控科
理化室
报验单
报验单
产品工序流转卡
不合格品通知
附录A:
检验和试验状态流程图责任部门主要流程相关资料/记录。
检验、测量和试验设备控制程序

1.目的对检验、测量和试验设备的配置、校准、周检、维修和使用进行有效的控制,以确保量值的准确可靠,并与要求的测量能力一致,满足预期的使用要求.2.适用范围本程序用于对影响产品质量的所有检验、测量和试验设备包括用作检验手段的各类器具、样板/样架、测量仪器、测量传感器、特殊的检测设备及其所属软件以及影响产品/过程质量工装、检测定位装置、比较基准和过程监控仪器.本程序也适用于顾客提供的测量和售后服务用以及员工自带的测量设备管理.3. 定义3.1计量确认――为保证检测设备满足预定使用要求所需的一组操作程序.3.2计量标准――实现、保持或再现单位一个或多个已知值,并通过比较将它们传递到其它计量器具的实物量具,计量仪器等.3.3校准――在规定条件下,为确定计量器具或讲量系统的示值,或实物量具或物质所代表的值与相对应的由参考(计量)标准获得的量值之间关系的一组操作.3.4溯源性――通过连续的比较链,使用测量结果能够与有关的计量标准(通常是国际或国家计量标准)联系起来的特性.3.5测量不确定度――表征被测量的真值所处的量值范围的评定结果.3.6检具能力――由检测设备的测量不确定度与检验特性的公差的比例关系确定.4.职责4.1质保部负责检验、测量和试验设备(以下简称测量设备)的管理,包括设备的校准、维修及送检.4.2采购课负责测量设备的采购.4.3各部门、车间负责各自使用的测量设备的日常维护和保养工作.5.工作程序5.1测量设备的配置5.1.1新产品或顾客特殊要求的产品测量设备配置,应在投产前由技术课对产品质量要求提出的测量能力进行审核,并做好审核记录《检测设备选型记录》,以确保选配的测量设备所需准确度.5.1.2因生产需要确需更新或零星配置的测量器具,由质保部提出申请,经总经理批准,采购课根据批准的申请单实施采购.5.1.3测量设备到货后,采购课须将合格证和随箱附件、设备资料与设备一起报质保部,由计量管理员先核对合格证或制造商提供的验收/认可文件,再送外检定或自行校准,并列入《测量设备分类管理目录》.5.2测量设备的管理5.2.1质保部对全公司已入库的和在用的影响产品质量的测量设备进行登记编号,建立测量设备的分类台帐即《测量设备一览表》.5.2.2对本公司使用的最高计量标准、强制检定工作计量器具及需进行周期检定的测量设备,必须建立设备档案,其内容应包括:出厂合格单、使用说明书、首次检定证书/记录、历次的检定(校准)证书/记录维修记录、校准操作规程、失准时处理记录.工程理更改后按准则规程更改记录等,顾客要求时须提供查阅.5.2.3本公司所用测量设备必须采用彩色标记管理,标记的种类和用途如下:《计量标准》标记(紫红色):表示公司最高计量标准器,并处于合格状态.准予使用.《合格证》标记(绿色):表示按国家、部门和地方检定系统检定合格,准予使用.《禁用》标志(大红色):表示该设备国家已淘汰,经检定不合格,禁止使用.《限用证》标志(浅黄色):表示该设备在量程或功能的局部下限,禁止使用,也适用于降级设备.《报废》标志(红色):表示不能从现场立即撤走的报废设备.《封存》标志(蓝色):表示不投入使用的试验设备,视情况可以就地封存,也可以收回集中封存,在封存内不纳入周期检定,启封使用前检定即可.彩色标记由设备管理员负责粘贴,彩色标记须标明器具编号、有效期(检定期/失效期)和校准人员,与零件有关样板/样架须标明产品的编号及经实际更改状态.5.2.4测量设备的封存、降级与报废需填写《封存、降级、报废、测量设备一览表》经质保部审核,副总经理批准执行,并在《测试设备一览表》上做好相应记录.5.2.5测量设备在校准、使用时,应具备相应的规程或使用说明书,及所要求的环境条件.5.2.6测量使用人员要按操作规程操作使用,要做好日常维护、保养.按仪器设备搬运要求搬运,以防意外损坏.5.3测量设备的检定、校准5.3.1凡需进行周期检定(校准)的测量设备,由质保部根据器具磨损和使用频次编制《测量设备周期检验计划表》.5.3.2测量设备的检定、校准按以下原则进行:a.本公司需开展检定,应按规定检定,经最高计量标准器考核后才能开展.b.本公司不能检定的测量设备应送法定计量机构或经技术监督部门授权以及符合ISO/IEC导则25注册的机构检定,该机构校准范围须包括此种设备校准;c.无国家、部门或地方检定规程的测量设备,由本公司进行校准,但其校准标准应经法定计量单位检定合格.校准方法应进行不确定分析,并制订校准规程,或由原设备制造商负责校准.d.校准操作规程由技术课负责组织制订,管理者代表批准发布.内容须包括设备型号、校准地点、校准周期、校准方法、验收标准、标识要求以及发现问题时应采取措施等.5.3.3测量设备的检定、校准周期按以下原则确定:a.公司的最高标准的强制检定工作计量器具及送外单位检定的测量设备,按国家检定的周期检定;b.公司自行校准的测量设备,应根据设备性能、器具磨损情况使用频次及使用环境条件等因素综合考虑,一般为1-2年.5.3.4送外单位检定的测量设备应做好检定证书的存档工作.本公司自检自校的测量设备应按规定作好检定校准原始记录,出具检定合格证书或校准报告,并妥善保存.对经检定或校准为不合格的测量设备应及时贴上《禁用》标志停止使用,等候处理.5.3.5检定/校准进的环境必须符合校准规程规定,并在校准/检定报告中记录,校准控制须《实验室质量控制手册》执行.5.4自制检测设备的管理自制检测设备由技术课根据工艺卡要求设计专用检测设备图纸,交制造部制作,经质保部检定合格后进行标识,填写检测设备台帐《测量设备一览表》和《检测设备历史记录卡片》,编制检定周期,并发放至生产部门,由专人保管.检定由质保部根据《自制检测设备校验方法》检定.5.5不合格测量设备的处理5.5.1不合格测量设备是指:经检定、校准不合格的,超过规定的检定、校准周期而未被检定、工作不正常或已损坏的.5.5.2当判定为不合格测量设备时,应立即停止使用,贴上“禁用”标记.5.5.3对不合格测量设备应及时地送维修部门检查修理,在排除不合格原因后,在经重新检定(校准),合格后方可使用.对不能修复的设备按规定手续作降级或报废处理,由计量室填写《封存、降级、报废计量器具清单》上登记.5.5.4对由偏离校准状态测量设备出具的检测数据的可靠性,应进行重新评定,必须进行复测.应做好评定和复测的记录,填写《偏离校准状态产品复测记录》并通知相关部门.如不合格则按《不合格品控制程序》执行,如可疑产品已发运则须迅速通知顾客.5.6人员资格5.6.1对从事计量工作的人员,必须参加项目的技术培训,经技术监督部门考核合格,取得《计量检定员》资格证书后方可开展检定工作,否则检定无效.5.6.2校准人员须经本公司组织的专业培训、考核合格后,由本公司颁发上岗证.5.6.3检定校准人员的培训、考核、发证由公司办组织进行.5.7测量系统分析对于在控制计划中提及的所有可重复性测量器具和系统均须按测量系统分析参考手册每年进行一次测量系统分析,对于样本小于300件时,计量型测量设备应采用极差法;计数型测量设备采用小样法.对于样本大于300件时,计量型测量设备采用均值和极差法;计数型测量设备采用大样法.通过测量系统分析进行系统的偏倚性、稳定性、重复性和再现性研究,如顾客批准,可采用其他分析方法及接收准则.5.8测量设备在搬运、防护和贮存时须确保测量设备准确度和适用性完好,测量设备使用者须严格按操作规范执行,防止因使用不当例其失效.6.使用记录略。
检测、校准和检定结果的质量保证控制程序

-检测、校准/检定结果的质量保证控制程序1 目的对检测/校准/检定的有效性进行监控,确保检测/校准/检定结果的质量。
2 适用范围适用于采用统计等技术对检测/校准/检定结果进行监控,保证检测/校准/检定结果质量的各项活动。
3 职责3.1 监督员负责监控方法的确定、监控计划的制定及组织实施。
3.2 专业室负责人负责监控计划的审核,质量部批准。
3.3 专业室负责人对监控方法有效性的评审,并将结果上报质量部审核。
3.4 检测/校准/检定人员参与质量保证方案的实施。
4 程序4.1 参加CNAS组织实施或承认的能力验证活动及参加实验室间比对4.1.1 能力验证是利用实验室间比对确定实验室的校准/检定/校准能力,是一种有效的外部质量保证活动,也是实验室内部质量控制技术的补充。
本院各专业室应积极参加CNAS组织实施或承认的能力验证计划、实验室间比对和测量审核。
4.1.2 各专业室监督员定期登录CNAS网站,及时记录并向专业室负责人汇报CNAS组织实施的能力验证计划、实验室间比对和测量审核。
4.1.3 质量负责人定期登录CNAS承认的组织的网站,及时记录并向各专业室负责人通报这些组织的能力验证计划、实验室间比对和测量审核。
4.1.4 各专业室必须参加与本院检定/校准项目有关的CNAS组织的能力验证计划、实验室间比对和测量审核;只要条件允许,应尽可能参加与本院各专业室检定/校准项目有关的CNAS 承认的能力验证计划、实验室间比对和测量审核。
各专业室应根据CNAS的要求制定相应计划,报技术负责人批准实施。
如果不能参加上述能力验证活动,必须书面说明原因,并经技术负责人批准。
CNAS组织实施的同一项目的能力验证,不允许连续两次不参加。
4.1.5 如果CNAS组织的能力验证计划、实验室间比对和测量审核没有包括各专业室的认可项目,各专业室可以根据需要参加CNAS认可的能力验证计划提供者提供的能力验证计划,或者创造条件自行组织或参加已经通过CNAS认可的实验室的比对或能力验证试验。
1-1-检验-测量和实验设备控制程序

1.目的1.1本程序规定了对检验、测量和试验设备的控制方法和内容,确保本公司的检验、测量和试验设备运行处于受控状态,以满足产品质量检测、环境检测的使用要求。
2.范围2.1本程序规定了公司用以确定产品、环境/安全符合规定要求的检验、测量和试验设备的控制,包括试验软件和比较标准以及定制特殊检具。
3.定义无4.职责4.1质量部4.1.1质量部是计量工作的主管部门,负责公司检验、测量和试验设备(以下简称:测量仪器)的标识、校正、检定和管理工作,负责建立测量仪器档案,开展测量系统分析工作,实施测量仪器的入库验收、周期检定、维修、办理转移、封存手续;4.1.2本公司无条件进行的检定项目,由质量部委托国家认可的计量检定机构进行检定。
本公司不能维修的测量仪器,由质量部申请委外修理;4.1.3当不存在国际和国家认可的检定/校准规程时,负责编制公司内部检定规程;4.1.4质量部负责测量仪器的选型和验收。
4.2使用部门4.2.1负责在用的测量仪器的日常维护工作,确保状态完好;4.2.2在使用前必须检查其校准合格标签是否完好,且应在有效期内;4.2.3参与测量系统分析工作;4.2.4当接到不合格测量仪器通知单时,负责对放行产品作出重新评定。
4.3采购部负责操作测量仪器的采购和入库事宜。
5.内容5.1测量仪器的选型、采购。
5.1.1测量仪器(包括检具)的选型、采购应根据《非生产性材料采购指导书》进行。
5.1.2测量仪器验收合格后,由质量部进行统一编号并登录到“测量仪器管理软件(instrument-management)”。
测试工程师负责维护“测量仪器管理软件”。
5.2搬运和贮存5.2.1测量仪器在搬运、贮存时,依据设备说明书要求,采取适当的防范措施,如防霉、防潮、防冲击等。
贮存环境条件的选择依设备说明书规定的范围执行。
5.3使用和维护5.3.1质量工程师根据测试仪器使用的复杂程度,决定是否需要编制操作指导书,如需要,应及时编制“设备操作指导书”,交质量部助理归档、发放。
检验和试验控制程序
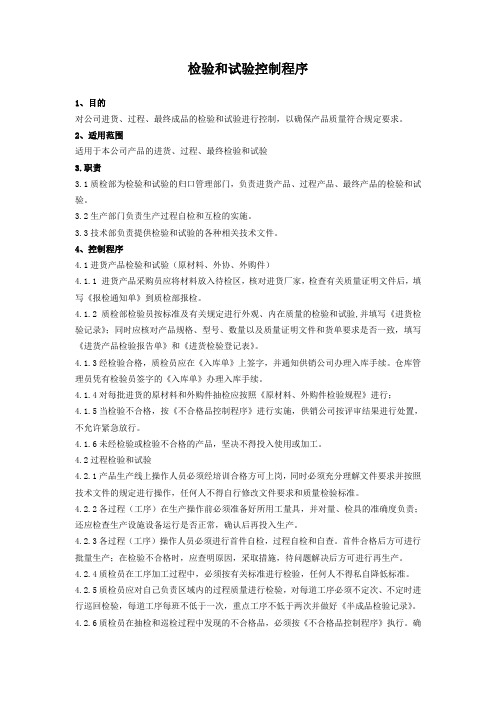
检验和试验控制程序1、目的对公司进货、过程、最终成品的检验和试验进行控制,以确保产品质量符合规定要求。
2、适用范围适用于本公司产品的进货、过程、最终检验和试验3.职责3.1质检部为检验和试验的归口管理部门,负责进货产品、过程产品、最终产品的检验和试验。
3.2生产部门负责生产过程自检和互检的实施。
3.3技术部负责提供检验和试验的各种相关技术文件。
4、控制程序4.1进货产品检验和试验(原材料、外协、外购件)4.1.1 进货产品采购员应将材料放入待检区,核对进货厂家,检查有关质量证明文件后,填写《报检通知单》到质检部报检。
4.1.2质检部检验员按标准及有关规定进行外观、内在质量的检验和试验,并填写《进货检验记录》;同时应核对产品规格、型号、数量以及质量证明文件和货单要求是否一致,填写《进货产品检验报告单》和《进货检验登记表》。
4.1.3经检验合格,质检员应在《入库单》上签字,并通知供销公司办理入库手续。
仓库管理员凭有检验员签字的《入库单》办理入库手续。
4.1.4对每批进货的原材料和外购件抽检应按照《原材料、外购件检验规程》进行;4.1.5当检验不合格,按《不合格品控制程序》进行实施,供销公司按评审结果进行处置,不允许紧急放行。
4.1.6未经检验或检验不合格的产品,坚决不得投入使用或加工。
4.2过程检验和试验4.2.1产品生产线上操作人员必须经培训合格方可上岗,同时必须充分理解文件要求并按照技术文件的规定进行操作,任何人不得自行修改文件要求和质量检验标准。
4.2.2各过程(工序)在生产操作前必须准备好所用工量具,并对量、检具的准确度负责;还应检查生产设施设备运行是否正常,确认后再投入生产。
4.2.3各过程(工序)操作人员必须进行首件自检,过程自检和自查。
首件合格后方可进行批量生产;在检验不合格时,应查明原因,采取措施,待问题解决后方可进行再生产。
4.2.4质检员在工序加工过程中,必须按有关标准进行检验,任何人不得私自降低标准。
检验和试验控制程序

检验和试验控制程序1. 目的按控制计划和程序规定要求对产品生产各阶段进行检验或试验,并向客户提供相应的合格证据;本程序规定了验证产品是否满足规定要求。
2. 适用范围本程序适用于进货、过程、半成品及成品最终检验和试验。
适用于产品的质量形成全过程的检验和试验。
3. 职责3.1 质量部制定检验指导书。
3.2 质量部负责按控制计划对原材料、外协件的进货检验和试验、首件检验、过程巡检、以及成品半成品的入库检。
4工作程序针对具体的产品,由质量部制定检验指导书,详细规定各项检验的方法/技术及接收标准。
质检员按检验作业指导书,对产品的特性进行监控和测量,并保留相关的记录。
如发现作业指导书有不合理或不具可操作性等,向质量部长提出更改申请。
经相关部门审核后,对检验指导书进行修订或更改。
并做好更改记录。
本公司产品实现过程中的产品监控和测量的阶段,一般分进货、首件检验、过程巡检、半成品、成品、发货审核等阶段。
4.1 进货检验对于进货检验与试验,公司为确保未经检验或未经检验合格的原材料/外协件不投入使用或加工,在原材料/外协件入库前,质量部负责原材料/外协件的入厂检验,并做好检验记录。
我司无条件检测的,质量部长委外安排检测。
检验合格后,通知库管员入库。
如检验不合格,填写《质量异常报告单》,交于质量部长。
质量部长根据多方意见,做出评审结果,让步接收的,通知库管员入库。
评审为不合格的,由采购员通知供应商退货。
进货检验流程图序号流程支持性文件责任部门输出文件/记录1/ 原材料仓管员 待检标识卡2检验指导书 质量部 检验记录单3/ / 委外检测申请单4检验指导书 质量部检验记录单 委外检测报告5/相关部门质量异常报告单6/ 原材料庫管员采购员入库单4.1.1 末经检验或末验证材料或产品,库管员不得对原材料/外协件办理入库,生产部不得将检验通知入厂检验入库 委外检测判定不合格评审认步接收退货末经检验或末验证的材料或产品投入生产。
检验和试验控制程序

检验和试验控制程序
在计算机科学和通信领域中,检验和试验是一种常见的错误检测技术。
在数据通信和存储过程中,数据传输时往往会出现数据损坏或丢失的可能,这种情况下使用检验和技术可以有效地检测到误差并进行纠正。
本文将介绍检验和试验的原理、实现和应用,并提供示例。
原理
检验和是指一种计算方法,用于验证数据传输或存储过程中是否存在错误。
它通过对数据进行求和并通过特定的算法生成一个校验和(checksum)值的方式来实现这一目的。
接收方收到数据后同样对数据进行计算,并将计算后的校验和值与发送方传送的校验和值进行比较,如果两个校验和值相同,则数据被视为正确的。
如果不相同,则接收方需要请求重新传输数据。
常用的计算方法包括:
1.模2和校验和(MOD-2 checksum):将数据作为二进制进
行计算,仅对加法和取余运算使用模2算法。
2.CRC(循环冗余校验):使用多项式算法进行计算,常用
于数据总线系统中。
3.Fletcher校验和:对数据进行分块,使用两个独立的16位
和校验和对块内数据进行校验,通过累加校验和的值来计算校验和。
实现
下面给出一个简单的MOD-2校验和实现:```python def generate_checksum(data):。
- 1、下载文档前请自行甄别文档内容的完整性,平台不提供额外的编辑、内容补充、找答案等附加服务。
- 2、"仅部分预览"的文档,不可在线预览部分如存在完整性等问题,可反馈申请退款(可完整预览的文档不适用该条件!)。
- 3、如文档侵犯您的权益,请联系客服反馈,我们会尽快为您处理(人工客服工作时间:9:00-18:30)。
1 PLANNING1.1The Technology Engineer shall prepare Check List (Form No. 5-1-1,5-1-2,5-1-3) based onthe drawings and the general examination specification. This Check List lists all examinations and tests, applicable procedure No. & revision No., and provides space for signature of the Examiner and AI to indicate activities accepted. Meanwhile, all Check Lists for the Code Items shall be collected on a Checklist Package (Form No.5-1-1). When entry to the vessel is not provided, an inspection stage shall be included on the Check List prior to setting up of the closure weld for inspection by the Examiner and AI.1.2Prior to start of manufacturing operations, the Technology QC Engineer shall approve theCheck List then present it with all related documents to the AI for his review and for designation of inspection point. The AI inspection points are classified into three categories: H-Hold Point, W-Witness Point, R-Review Point.1.3When design document(s) or general examination specification be revised, the Check Listshall be reviewed by Technology Engineer to check if it could be applicable to those revised documents or not. When necessary, a Check List or a supplementary Check List shall be prepared by Technology Engineer, and be approved and accepted as specified by Paragraph 1.2 above.2CONTROL OF PROCESS2.1The manufacturing operations shall be performed by Shop Workers under supervision ofthe Foremen in accordance with drawings and procedures.2.2The Foremen shall inform status of process to the Examination QC Engineer to requestexaminations, tests and inspections.2.3The Examination QC Engineer shall notify AI in advance of approaching AI Hold pointsand Witness points.2.4Work shall not proceed beyond AI Hold points (required by Check List) without presenceof the AI and his signature. The AI Witness point may proceed with prior consent of the AI, then AI will review and sign on record sheet to confirm to his consent afterwards. The Examination QC Engineer shall document AI’s permission of consent on the Check List at the sequence bypassed.2.5Examiner shall perform examinations in accordance with procedures referenced on CheckList. When required by the procedure, records for examination shall be prepared.2.6Examiner shall evaluate the results of examination and test, if acceptable, he shall sign anddate on the Check List and release to proceed work.2.7For part of Code Items done by the subcontractors, such as forming operation, heattreatment, mechanical performance test, impact test and NDE, etc, entrustment contract shall be prepared. During manufacturing by the subcontractors, the Material QC Engineer or Examination QC Engineer of SURF and the AI has the rights to review the subcontractor’s qualification and to perform the on site inspection. All parts of Code Items on which the work is performed by the subcontractors shall be accepted by receiving examination done by Material Examiner or Examiner of SURF. The associated documents shall be submitted to the appropriate QC Engineers for their review with signatures on the documents. No further processing can be performed until acceptance of receiving inspection.2.8When nonconformity is found, the disposition shall be controlled in accordance withSection 6 of this Manual.3FINAL TESTS3.1Prior to the final Code pressure test, the Examination QC Engineer shall verify that allrequired operations, examinations, tests and internal inspections have been completed and all nonconformities have been disposed.3.2Preparation for the final Code tests shall be performed by the Shop Workers.The finalpressure test is carried out using proc edure QCP18“PRESSURE TEST PROCE D URE”.3.3The test gauge used for the final Code test shall be calibrated in accordance with Section10 of this QC Manual. Dial indicating pressure gages used in testing shall be graduatedover a range of about double the intended maximum test pressure, but in no case shall be less than 1.5 and nor more than 4 times that pressure. Digital reading pressure gages having a wider range of pressure maybe used provided the readings give the same or greater degree of accuracy as obtained with dial pressure gages.3.4The Examiner shall check for any leakage or deformation, evaluate the result of tests andprepare the record. The Pressure Test Report (Form No. 5-2) shall be signed by the Examiner.3.5The final pressure test shall be performed in the presence of the AI.4EXAMINATION PROCEDURES AND RECORDS4.1 The Examiner shall prepare the Examination Procedure which shall be reviewed by the。