检验和试验控制程序
检验与试验控制程序
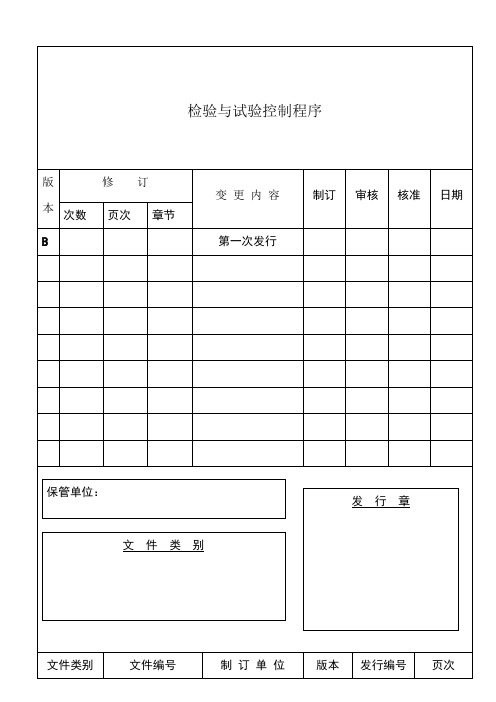
产品检验和测试完成后,品管人员依《抽样检验规范》中有关规定对该批货进行判定。
(1)对在制品,判定合格时由检查员在该批生产传单上签名确认,对检查中发现的不合格品按不良类别按区域放置隔离,并最终把不合格品统一送质量中心不合格品分析处处理,并做好不合格分析报告上,良品选出,可返修送相关部门处理,不良品依据数量经批准后报废,参见《不合格品分析作业指导书》。
品管部
(4)对其它物理特性之检验,按客户要求进行字体寿命测试或按打击次数,或送往外界公证机构执行检验后,将报告通知客户。
(5)每日QA人员将抽样检验结果汇总在QA品保记录表中。
检验与测试记录的管制:检验与测试记录应清晰、准确、由品管部门和检查部门保存,保存期限详见【质量记录控制程序】中规定期限。
7.附件:
文件类别
文件编号
制 订 单 位
版本
发行编号
页次
二阶
品管部
在制品和成品的检验和测试
生产部门在生产时,经IPQC确认和各检查员全数检查后,按工序流程把产品送至相应部门,待进步加工或送至QA由QA人员进行检验和测试。
IPQC和检查人员依各工序的检查标准卡对送检在制品和成品进行全数检查或抽验,对QS9000产品必须按客户要求对所有产品进行尺寸检验和功能验证,其结果供客户评审。
(2)对成品,判定合格时由QA在该批产品之每一包装袋中放置“合格标签”并在合格标签上盖“QA Acc”章,并按作业程序做好记录。
文件类别
文件编号
制 订 单 位
版本
发行编号
页次
二阶
品管部
(3)判定不合格时,由QA在该批产品生产传单上加盖“QA REJ”章,并发出QA通货传单随产品通给加工后检或IPQC重工,并将QS退货传单交QA主管确认,加工重工后须再经QA检验,合格后方可入库。
检验与试验控制程序
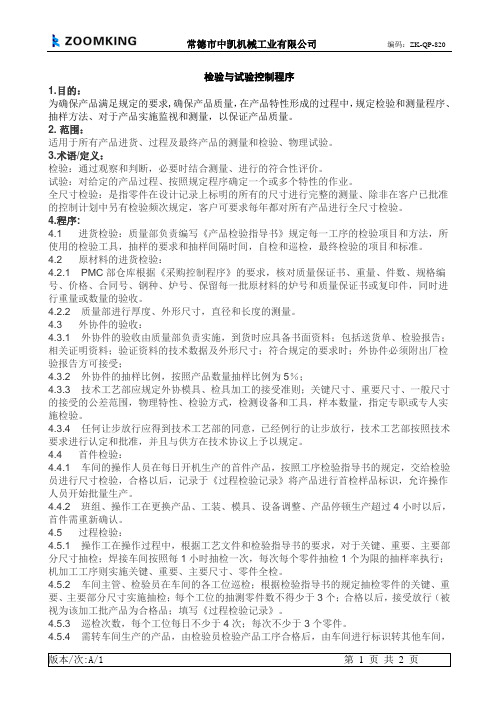
检验与试验控制程序1.目的:为确保产品满足规定的要求,确保产品质量,在产品特性形成的过程中,规定检验和测量程序、抽样方法、对于产品实施监视和测量,以保证产品质量。
2. 范围:适用于所有产品进货、过程及最终产品的测量和检验、物理试验。
3.术语/定义:检验:通过观察和判断,必要时结合测量、进行的符合性评价。
试验:对给定的产品过程、按照规定程序确定一个或多个特性的作业。
全尺寸检验:是指零件在设计记录上标明的所有的尺寸进行完整的测量、除非在客户已批准的控制计划中另有检验频次规定,客户可要求每年都对所有产品进行全尺寸检验。
4.程序:4.1 进货检验:质量部负责编写《产品检验指导书》规定每一工序的检验项目和方法,所使用的检验工具,抽样的要求和抽样间隔时间,自检和巡检,最终检验的项目和标准。
4.2 原材料的进货检验:4.2.1 PMC部仓库根据《采购控制程序》的要求,核对质量保证书、重量、件数、规格编号、价格、合同号、钢种、炉号、保留每一批原材料的炉号和质量保证书或复印件,同时进行重量或数量的验收。
4.2.2 质量部进行厚度、外形尺寸,直径和长度的测量。
4.3 外协件的验收:4.3.1 外协件的验收由质量部负责实施,到货时应具备书面资料;包括送货单、检验报告;相关证明资料;验证资料的技术数据及外形尺寸;符合规定的要求时;外协件必须附出厂检验报告方可接受;4.3.2 外协件的抽样比例,按照产品数量抽样比例为5%;4.3.3 技术工艺部应规定外协模具、检具加工的接受准则;关键尺寸、重要尺寸、一般尺寸的接受的公差范围,物理特性、检验方式,检测设备和工具,样本数量,指定专职或专人实施检验。
4.3.4 任何让步放行应得到技术工艺部的同意,已经例行的让步放行,技术工艺部按照技术要求进行认定和批准,并且与供方在技术协议上予以规定。
4.4 首件检验:4.4.1 车间的操作人员在每日开机生产的首件产品,按照工序检验指导书的规定,交给检验员进行尺寸检验,合格以后,记录于《过程检验记录》将产品进行首检样品标识,允许操作人员开始批量生产。
检验与试验控制程序

1 目的对产品进行检验和试验以确保产品满足顾客的要求。
2 范围适用于本公司产品的全过程控制(包括来料检验、过程检验,工序检验和最终检验)。
3 职责3.1工程部负责制定各类检验标准。
3.2品管部负责按各类检验标准对来料、过程和成品实施检验,并对出现的不合格提出并跟踪验证。
3.3制造部负责对本工序生产的产品进行自检,并对出现的不合格采取纠正和预防措施。
4 程序4.1来料检验4.1.1工程部编制《检验标准》以作为物料检验的依据。
4.1.2进货物品(包括外发进厂)进入公司后,由仓管员对品名、规格/货号、颜色、数量核对无误后,在供方送货单签收后,通知检验员检验。
4.1.3 检验员接到通知后,依《检验标准》及相关图纸或样品进行检验,并填写“IQC检验及处理报告”。
检验合格进行合格标识后,方可入库,仓管员办理入库手续。
不合格产品依《不合格控制程序》处理。
4.1.4 因生产急需,须紧急放行的物品,依《不合格品控制程序》处理。
4.1.5当检验原材料判定不合格,其又不影响产品功能时,予以特采的,依《不合格品控制程序》执行。
4.2 过程检验4.2.1首件检验4.2.1.1有下列情形时必须做首件检验:a)首次量产时或每次订单、批次开始生产时;b)更换维修模具/夹具再生产时;c)每天重新开机生产时;d)更换材料时;e)巡检发现不合格为设备因素调整后;f)更换人员时。
4.2.1.2检验程序a)生产线员工开机量产前生产首件样品,经自检合格后,送IPQC检验员检验确认。
b)IPQC检验员依据《检验标准》及相关图纸或样品对首件样品进行检验并判定,并将检验项目及结果填写在“制程检验记录表”上。
c)如果首件样品检验合格,IPQC检验员通知生产班组负责人或操作员量产。
d)如果首件样品检验不合格,IPQC检验员立即通知生产班组负责人或操作员调整直到合格为止。
4.2.2自检生产过程中,操作员在作业时及作业完成后应依“生产流程卡”和《检验标准》对产品质量进行自检,并填写相关记录。
检验和试验控制程序
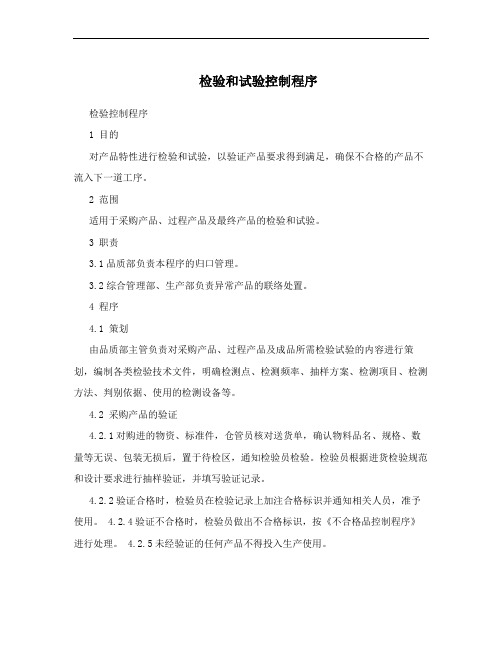
检验和试验控制程序检验控制程序1 目的对产品特性进行检验和试验,以验证产品要求得到满足,确保不合格的产品不流入下一道工序。
2 范围适用于采购产品、过程产品及最终产品的检验和试验。
3 职责3.1品质部负责本程序的归口管理。
3.2综合管理部、生产部负责异常产品的联络处置。
4 程序4.1 策划由品质部主管负责对采购产品、过程产品及成品所需检验试验的内容进行策划,编制各类检验技术文件,明确检测点、检测频率、抽样方案、检测项目、检测方法、判别依据、使用的检测设备等。
4.2 采购产品的验证4.2.1对购进的物资、标准件,仓管员核对送货单,确认物料品名、规格、数量等无误、包装无损后,置于待检区,通知检验员检验。
检验员根据进货检验规范和设计要求进行抽样验证,并填写验证记录。
4.2.2验证合格时,检验员在检验记录上加注合格标识并通知相关人员,准予使用。
4.2.4验证不合格时,检验员做出不合格标识,按《不合格品控制程序》进行处理。
4.2.5未经验证的任何产品不得投入生产使用。
4.2.6采购产品的验证方式,可包括:检验、测量、观察、工艺验证、查验合格证明文件等方式的一种或几种。
4.3过程检验4.3.1由检验员按《作业指导书》、《外观检查标准书》及相关技术要求对工序产品进行检验并填写相关工序质量检验记录,并根据检验结果作好检验状态标识。
4.3.2对检验出的不合格品,检验员开具《品质异常联络书》相关栏目后,按《不合格品的控制程序》执行。
4.3.3不合格品不允许流入下道工序。
4.4 最终检验和试验4.4.1产品组装完成后,品质部按照《完成品检验规范》《样品承认书》和相关技术要求对产品进行检验和试验;4.4.2检验或试验不合格时,检验员开具《品质异常联络书》相关栏目后,按《不合格品的控制程序》执行。
4.5 检验和试验记录4.5.1 在检验和试验记录中应清楚地表明产品是否已按规定要求经检验合格,记录应注明负责合格品放行的授权责任者。
检验和试验控制程序
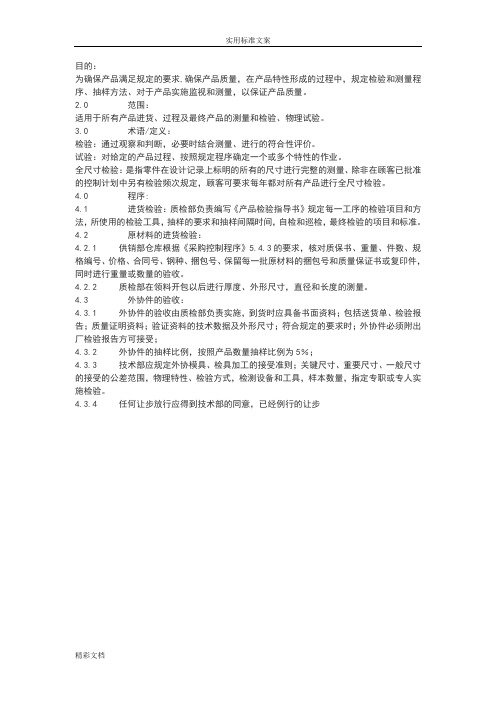
目的:为确保产品满足规定的要求,确保产品质量,在产品特性形成的过程中,规定检验和测量程序、抽样方法、对于产品实施监视和测量,以保证产品质量。
2.0 范围:适用于所有产品进货、过程及最终产品的测量和检验、物理试验。
3.0 术语/定义:检验:通过观察和判断,必要时结合测量、进行的符合性评价。
试验:对给定的产品过程、按照规定程序确定一个或多个特性的作业。
全尺寸检验:是指零件在设计记录上标明的所有的尺寸进行完整的测量、除非在顾客已批准的控制计划中另有检验频次规定,顾客可要求每年都对所有产品进行全尺寸检验。
4.0 程序:4.1 进货检验:质检部负责编写《产品检验指导书》规定每一工序的检验项目和方法,所使用的检验工具,抽样的要求和抽样间隔时间,自检和巡检,最终检验的项目和标准。
4.2 原材料的进货检验:4.2.1 供销部仓库根据《采购控制程序》5.4.3的要求,核对质保书、重量、件数、规格编号、价格、合同号、钢种、捆包号、保留每一批原材料的捆包号和质量保证书或复印件,同时进行重量或数量的验收。
4.2.2 质检部在领料开包以后进行厚度、外形尺寸,直径和长度的测量。
4.3 外协件的验收:4.3.1 外协件的验收由质检部负责实施,到货时应具备书面资料;包括送货单、检验报告;质量证明资料;验证资料的技术数据及外形尺寸;符合规定的要求时;外协件必须附出厂检验报告方可接受;4.3.2 外协件的抽样比例,按照产品数量抽样比例为5%;4.3.3 技术部应规定外协模具、检具加工的接受准则;关键尺寸、重要尺寸、一般尺寸的接受的公差范围,物理特性、检验方式,检测设备和工具,样本数量,指定专职或专人实施检验。
4.3.4 任何让步放行应得到技术部的同意,已经例行的让步放行,技术部按照技术要求进行认定和批准,并且与供方在技术协议上予以规定。
4.4 首件检验:4.4.1 车间的操作人员在每日开机生产的首件产品,按照工序检验指导书的规定,交给检验员进行尺寸检验,合格以后,记录于《过程检验记录》将产品进行首检样品标识,允许操作人员开始批量生产。
检验和试验控制程序
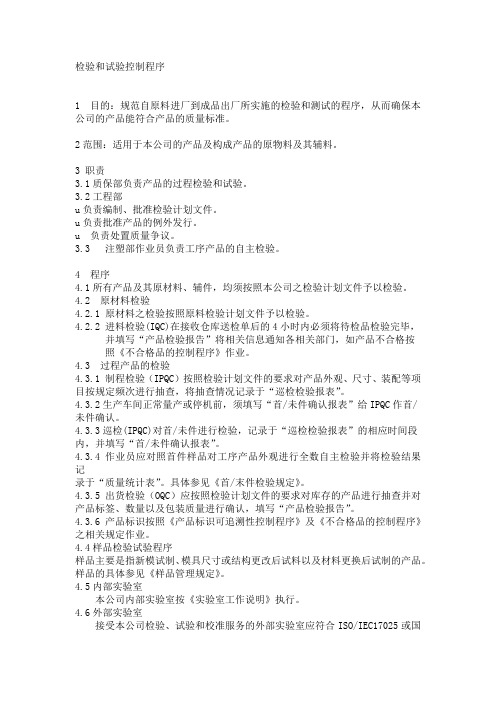
检验和试验控制程序1 目的:规范自原料进厂到成品出厂所实施的检验和测试的程序,从而确保本公司的产品能符合产品的质量标准。
2范围:适用于本公司的产品及构成产品的原物料及其辅料。
3 职责3.1质保部负责产品的过程检验和试验。
3.2工程部u负责编制、批准检验计划文件。
u负责批准产品的例外发行。
u 负责处置质量争议。
3.3 注塑部作业员负责工序产品的自主检验。
4 程序4.1所有产品及其原材料、辅件,均须按照本公司之检验计划文件予以检验。
4.2 原材料检验4.2.1 原材料之检验按照原料检验计划文件予以检验。
4.2.2 进料检验(IQC)在接收仓库送检单后的4小时内必须将待检品检验完毕,并填写“产品检验报告”将相关信息通知各相关部门,如产品不合格按照《不合格品的控制程序》作业。
4.3 过程产品的检验4.3.1 制程检验(IPQC)按照检验计划文件的要求对产品外观、尺寸、装配等项目按规定频次进行抽查,将抽查情况记录于“巡检检验报表”。
4.3.2生产车间正常量产或停机前,须填写“首/未件确认报表”给IPQC作首/ 未件确认。
4.3.3巡检(IPQC)对首/未件进行检验,记录于“巡检检验报表”的相应时间段内,并填写“首/未件确认报表”。
4.3.4作业员应对照首件样品对工序产品外观进行全数自主检验并将检验结果记录于“质量统计表”。
具体参见《首/末件检验规定》。
4.3.5出货检验(OQC)应按照检验计划文件的要求对库存的产品进行抽查并对产品标签、数量以及包装质量进行确认,填写“产品检验报告”。
4.3.6 产品标识按照《产品标识可追溯性控制程序》及《不合格品的控制程序》之相关规定作业。
4.4样品检验试验程序样品主要是指新模试制、模具尺寸或结构更改后试料以及材料更换后试制的产品。
样品的具体参见《样品管理规定》。
4.5内部实验室本公司内部实验室按《实验室工作说明》执行。
4.6外部实验室接受本公司检验、试验和校准服务的外部实验室应符合ISO/IEC17025或国家同等的认可的国家标准。
检验与试验控制程序
检验与试验控制程序1 目的检验是根据有关标准和合同要求,采用检查、测量或试验等方法,对电梯安装改造维修进行全过程检验和质量控制,以确保电梯安装改造维修工程质量符合法规、标准、图样和顾客的要求。
2 范围本章适用于电梯安装改造维修材料的开箱验收、安装过程检验及最终检验与试验的质量控制。
3 职责3.1 质量安全部是检验质量控制的归口管理部门,负责电梯安装改造维修过程检验和最终检验。
3.2 其他部门负责配合质量安全部做好检验工作。
4 控制要求4.1 检验准备4.1.1 检验文件的编制(1)应在工程的施工方案或单独的质量计划中对检验和试验做出安排,编制检验计划或检验工艺以及质量检测记录和报告等检验文件。
4.1.2 应配备必要的检验设备和计量器具,检验所用的计量器具应按规定进行检定并在有效期内使用。
4.2 开箱验收4.2.1 对到达施工现场的电梯零部件及包装箱进行外观检验。
4.2.2 清点箱数,检查箱体情况,按照生产厂家提供的货物清单会同顾客对包装箱进行确认,如有缺箱、坏箱由质量管理部代表记录,并由厂家、顾客及质量管理部代表三方签字确认。
4.2.3 建设方、检验员和施工队长共同对产品的外观、数量、规格型号进行清点,并在《开箱点验处理结果协议》中作好检验记录,记录内容填写齐全,属实,并由顾客、检验员和施工队长签字确认,开箱后《开箱点验结果处理协议》分别由三方人员持有,检验员认真审核产品合格证,合格证应齐全,需型式试验的零部件必须有型试验报告结论副本(其中限速器与渐进式安全钳还须有调试证书副本),检查装箱单与合同中技术条件是否一致。
4.2.4 检验中发现缺、错、损件要在《开箱点验结果处理协议》中根据装箱单与合同技术条件注明缺件、错件、损件的名称、规格、数量等,并及时将《开箱点验结果处理协议》报回质量管理部,按NTSY/QS804《不合格品的控制程序》执行。
4.2.5 对采购的零配件,由库房保管员根据采购文件,清点数量,在《入库登记单》上签字入库保管。
检验和试验状态控制程序
1.0目的:
对各阶段检验和试验的产品按规定的方法进行标识,确保只有合格
的产品才能转序及出厂。
2.0范围:
此文件适用于本公司所有产品的检验和试验状态控制。
3.0职责:
3.1工程部
-负责确定各检验和试验状态的标识形式,状态标识的日常管理工
作。
-负责产品质量的判断及货品放行。
算机及其他试验物品则应附检验报告。
4.3图纸质量状况按《图纸审核程序》处理。
4.4检验和试验状态的标识办法应由技术人员在制订有关文件时,在文
件中予以说明,操作者在工作中按文件要求,做好这些标记。
4.5仓库划分不合格品区,待检区及合格品区,或悬挂待检验、合格、
不合格标识牌。并按质量状况存放货品,对维修/退货产品,应予
贴纸表明。
4.6对标识不清或无法标识的产品不能使用转序或出厂,必须经过重新
检验并进行状态标识。
5.0附件
5.1合格证
5.2合格印章
5.3不合格印章
3.2仓库
-负责标识,分区存放不同检验和试验状态的产品。
3.3 MRB(物料评审委员会)
-负责不合格的处理
4.0程序:
4.1检验和试验状态有三种:(检验)合格、(检验)不合格、待检验。
4.2货品检验和试验状态标识
4.2.1所有验证类货品均由供应商提供客观证据,如合格证。
4.2.2检验类货品;DCS模件应在外包装上盖合格/不合格印章,计
检验和试验控制程序
检验和试验控制程序1. 0 目的通过检验和试验活动,验证产品形成的全过程是否满足规定要求,以保证不合格的产品不投入使用、不加工、不出厂。
2. 0 适用范围适用于本公司产品形成全过程的检验和试验的控制。
3. 0 职责3. 1 质管部——是检验和试验的归口管理部门,负责产品检验和试验的组织与实施,对产品的质量进行最终判定。
3. 2 技术部——检验和试验的协助部门,协助质管部制定相关的产品检验技术标准。
3. 3 制造部、采购部、财物部——为本程序文件的执行部门。
4. 0 定义4. 1首件——班次或工作条件(工装、模具、设备人员更换)或产品变更后经自检、互检、专检合格的第一件(试模件除外)。
4. 2外购物资—指构成产品所需外购的原材料、坯件、成品制件等。
5. 0 工作程序5. 1检验和试验人员的要求5.1.1检验和试验人员人数的配备应与公司生产规模和方式相适应。
5.1.2 检验和试验人员的素质应能满足岗位专业要求;质管部应定期或不定期对检验和试验人员按《培训管理程序》组织有关的培训及考核。
5.2检验和试验的分类5.2.1进货检验和试验——外购物资质量的验证确认。
5.2.2过程检验和试验——制造过程中工序质量的验证确认。
5.2.3最终检验和试验——提供成品符合规定要求的证据,其作业方式有:a、总成的最终检验和试验——验证产品成品的性能及尺寸在装配过程中是否能得到保证,由装配专检人员负责。
b、最终产品审核——以适当频次抽取已包装的产品进行审核,对其符合性所规定的要求进行验证,由质管部试验室负责。
c、全尺寸检验和功能试验——按顾客提出的频次及有关产品进行尺寸检验和功能试验,由质管部试验室负责,并将试验结果提交给顾客评审。
5.3检验和试验的依据为《进货检验作业指导书》、《过程检验作业指导书》、《最终检验作业指导书》及《试验规程》等。
5.4检验和试验的实施5.4.1 进货检验和试验5.4.1.1 进货的供方应是经评价的合格分承包方,所供物资应是通过初物验证合格后的供货,所供初物物资执行《初物管理办法》。
IATF16949-2016-SP-08-01检验和试验控制程序
原: 现: 原: 现: 原: 现:
过程文件名称 过程管理编号 编制日期 编 1.目的和适用范围 制
检验和试验控制程序 SP-08
编制部 版本号 [变更码] 页 码
品质管理部 B[00版] 第 1 页试验,以验证产品是否满足规定要求(包括确认检验),特制定本程序。 1.2 适用范围:本程序适用于新产品和量产品的外部购买原材料、零部件、产品包装,以及自制件的检验和试验。 2.职责 品质管理部负责检验计划的编制,检验和测量设备及检验文件的提供,新产品和量产品的部品检验。 试验室负责各部依赖的检验/试验。 制造部负责工序内产品的自检。 内检负责工序内的首件检查、过程巡检、尾件检查。(必要时实施100%全检) 物流部负责发货前的包装确认。 3.术语和定义 无。 4.内容 详见内容附页 5.相关程序/指导书 COP-06-D01 COP-06-S04 COP-06-D06 SP-08-D02 SP-09 SP-08-D01 6.质量记录 编号 COP-06-R21 SP-08-R03 SP-08-R02 SP-08-R05 SP-08-R04 SP-08-R06 SP-08-R01 SP-08-R07 SP-08-R03 SP-08-R13 SP-08-R08 7.变更内容一览表 变更活动名称 变更标记 变更人 变更开始 实施日期 原: 现: 变更内容简述 名称 《产品检验计划》 《检验指导书》 《量产品检验报告》 《过程抽检成绩书》 《检查成绩书》 《成品抽检成绩书》 《新产品检验报告》 《(出厂)产品检验报告》 《委托检测申请单》 《试验报告书》 《入库单》 保存期 10年 10年 10年 10年 10年 10年 10年 10年 10年 20年 10年 存档部 品质管理部 品质管理部 外检 内检 内检 内检 品质管理部 品质管理部 品质管理部 试验室 外检/内检 《检具设计、制作、购置指导书》 《制品检验规范编制指导书》 《部品检验规范编制指导书》 《试验管理指导书》 《不合格品控制程序》 《进货检验管理指导书》
- 1、下载文档前请自行甄别文档内容的完整性,平台不提供额外的编辑、内容补充、找答案等附加服务。
- 2、"仅部分预览"的文档,不可在线预览部分如存在完整性等问题,可反馈申请退款(可完整预览的文档不适用该条件!)。
- 3、如文档侵犯您的权益,请联系客服反馈,我们会尽快为您处理(人工客服工作时间:9:00-18:30)。
1.0 目的
对原辅材料、半成品及成品进行规定的检验或试验,确保未经检验和不合格的材料、产品不投入使用、加工和出厂。
2.0 范围
适用于原辅材料、半成品及成品的检验和试验。
3.0 职责
3.1质检部负责原辅材料、半成品、成品检验标准的制订和检验。
3.2生产部各小组负责自检及互检。
4.0 方法
4.1进料检验控制(IQC)
4.1.1 仓管员在收到到货的原辅材料后,依照《物料申购单》上品名、规格、应到数量,
负责核对实际到货数量、重量,合格后通知IQC进行来料检验。
4.1.2 质检部IQC接到通知后,按照《进料检验规范》要求进行抽检或全检,将检验结果
记录在《进料检验记录表》上,合格后办理入库手续,如不合格按照《不合格品控制程序》进行处理。
4.2过程检验和试验控制
4.2.1自检、互检
各班组工人工作时应按照《工艺卡》和技术图纸、过程检验规范进行自检和互检。
4.2.2巡检
检验员按照《过程检验规范》、工艺卡质量要求、技术图纸对现场每道工序进行巡检。
每天上午、下午各巡检一次,每道工序至少抽检一件产品,并将检验结果记录于《巡检日报表》上。
出现不合格时应及时反馈给操作工人,进行返工。
具体参考《不合格品控制程序》。
4.3 最终、出货检验和试验控制
4.3.1最终成品检验和试验依据:《成品检验规范》和工艺卡、技术图纸要求执行,并将
检验结果记录于《成品检验报告》上。
4.5 对所有检验不合格品都依据:《不合格品控制程序》要求执行,并标识清楚。
4.6 所有要求的检验项目,在相应的记录中都要填写具体的检验数值或内容及日期并有
经授权的检验人员的签字或盖章,经检验主管审批。
4.7 检验和试验记录由质检部负责保存,当合同中有规定时,检验和试验的相关记录
可提供给客户查阅。
5.0 记录
进料检验记录
巡检记录
成品检验记录
6.0 参考文件
《进料检验规范》
《不合格品控制程序》
《过程检验规范》
《成品检验规范》
进料检验记录表
成品检验单
检验日期:
QP8.2-3-3/A0
过程巡检记录
部长:组长:检验员:。