年产80万件日用瓷隧道窑设计
隧道窑的结构和工作原理
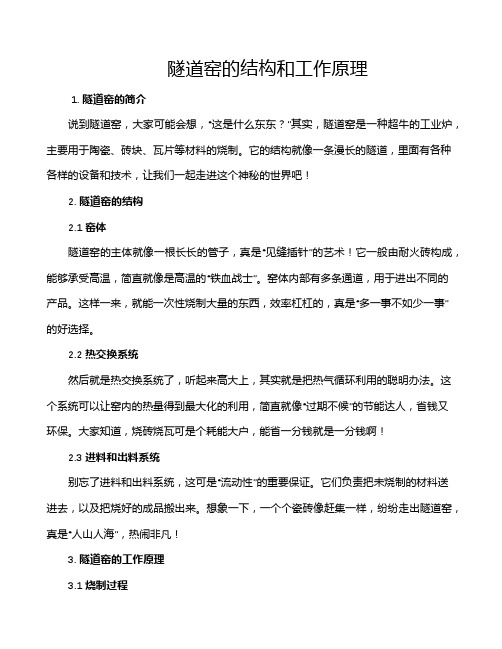
隧道窑的结构和工作原理1. 隧道窑的简介说到隧道窑,大家可能会想,“这是什么东东?”其实,隧道窑是一种超牛的工业炉,主要用于陶瓷、砖块、瓦片等材料的烧制。
它的结构就像一条漫长的隧道,里面有各种各样的设备和技术,让我们一起走进这个神秘的世界吧!2. 隧道窑的结构2.1 窑体隧道窑的主体就像一根长长的管子,真是“见缝插针”的艺术!它一般由耐火砖构成,能够承受高温,简直就像是高温的“铁血战士”。
窑体内部有多条通道,用于进出不同的产品。
这样一来,就能一次性烧制大量的东西,效率杠杠的,真是“多一事不如少一事”的好选择。
2.2 热交换系统然后就是热交换系统了,听起来高大上,其实就是把热气循环利用的聪明办法。
这个系统可以让窑内的热量得到最大化的利用,简直就像“过期不候”的节能达人,省钱又环保。
大家知道,烧砖烧瓦可是个耗能大户,能省一分钱就是一分钱啊!2.3 进料和出料系统别忘了进料和出料系统,这可是“流动性”的重要保证。
它们负责把未烧制的材料送进去,以及把烧好的成品搬出来。
想象一下,一个个瓷砖像赶集一样,纷纷走出隧道窑,真是“人山人海”,热闹非凡!3. 隧道窑的工作原理3.1 烧制过程说到工作原理,隧道窑的烧制过程简直像个大舞台,产品们在这里上演一场精彩的“火焰秀”。
首先,未烧制的材料被送入窑内,随着温度逐渐升高,它们就像变魔术一样,发生一系列化学变化。
刚开始的时候,温度可能在600℃左右,慢慢地,直到1300℃,那种高温简直是“热火朝天”!3.2 冷却过程烧制完后,接下来就是冷却过程了。
这时候,窑内的温度开始下降,就像“凉风习习”的秋天,产品们终于可以松一口气。
冷却的过程也很重要,太快可能会导致产品裂开,这可是“功亏一篑”的事情啊!所以,隧道窑一般采用渐进式冷却,让每一个产品都能安安全全地“顺风归家”。
4. 小结总的来说,隧道窑不仅仅是一座简单的窑炉,它就像是一台高效的生产机器,运转起来那叫一个顺畅。
它的设计和工作原理融合了许多现代科技,既节能又环保,真是“聪明绝顶”。
年产万件日用瓷隧道窑设计

摘要本设计是年产80 万件10 寸汤盘隧道窑。
窑炉总长,有效宽是米,烧成温度是1300C,烧成周期为24小时。
燃料采用发生炉煤气,燃烧器采用高速烧嘴。
设计的隧道窑,窑体趋向轻型化,烧成质量好,成品率高。
全窑的控制采用计算机自动控制来实现,这样既提高了产品的成品率又降低的工作人员的工作强度,降低了生产成本。
关键词:隧道窑汤盘发生炉煤刖言随着经济的不断发展,人民生活水平的不断提高,陶瓷工业在人民生产、生活中都占有重要的地位。
陶瓷的发展与窑炉的改革密切相关,一定结构特点的窑炉烧出一定品质的陶瓷。
因此正确选择烧成窑炉是获得性能良好制品的关键。
在日用瓷生产过程,烧成是非常重要的一道工序,烧成过程严重影响着产品的质量。
隧道窑是现代化的连续式烧成的热工设备,以窑车为运载工具,具有生产质量稳定、产量大、消耗低的特点,最适合于工艺成熟批量生产的日用瓷。
由于现在能源价格不断上涨,为了节约成本,更好的赢取经济利益,就需要窑炉在烧成过程中严格的控制温度制度、气氛制度,压力制度,提高生产效率及质量,便于更好的节约燃料,降低能量消耗在烧成过程中,温度控制是最重要的关键。
没有合理的烧成控制,产品质量和产量都会很低。
要想得到稳定的产品质量和提高产量,首先要有符合产品的烧成制度。
然后必须维持一定的窑内压力。
最后,必须要维持适当的气氛。
这些要求都应该遵循。
本窑炉采用轻质耐火保温材料,高速调温烧嘴,对余热进行集中利用,产品能耗较低,实现了自动化控制,连续式生产,大大提高了生产效率。
符合大量生产的要求。
在设计过程中,使我对窑炉设计及施工过程有了更深的认识。
隧道窑是当前陶瓷工业中优质、高产、低消耗的先进窑炉,在我国已得到越来越广泛的应用。
1原始数据设计技术指标、参数:1.年产量:80万件(年工作日330天,合格率97%.2.产品规格:10英寸,件3.汤盘坯料组成(%4.入窑水分:<2%5.最高烧成温度:1300C6.燃料:发生炉煤气7.烧成周期:24h8.气氛制度:还原气氛9.隧道窑:窑车式拱顶隧道窑2烧成制度的确定根据制品的化学组成、形状、尺寸、线收缩率及其他一些性能要求,制订烧成制度如下:常温—200C小时预热阶段300C —500C小时预热氧化分解阶段500°C —750°C小时预热氧化分解阶段750C — 950C 小时 预热氧化分解阶段 950C —1300C 小时 烧成阶段 1300C —1300C 小时 保温阶段 1300C—800C小时 急冷阶段 800C — 400C 小时 缓冷阶段 400°C —60C 小时快冷阶段3窑体主要尺寸的确定棚板和立柱的选用查资料得10寸汤盘的详细参数如下:大小:255X 255X 30(单位 mm )单件制品质量:所以选用棚板的尺寸为:480X 480X 10 mm 支柱高度:50mm装车方法在窑车的长度方向上设置3块棚板,宽度方向上设置3块棚板,在窑车高度方向上 装10层。
自控日用瓷高温(还原焰)轻型隧道窑的设计及热工特征

成一个大的空间 , 窑道上部切面大 , 在烟气几何压 头的作用 , 上部流过的热烟气多而温度高,而坯垛 中下部温度低, 形成窑道切面上下部温度较大的差 异。 为了克服上述弊端, 轻体隧道窑采用悬挂式平
吊顶 ,烧成 带 向氧化带 、预 热带方 向分 倒梯 式降 低 窑顶 的高 度 。烧成 带高 温 区,上部 设烧 嘴 ,窑顶 与
( m W/ )
73 3
( ℃)
7 7
.
( ℃/ ) 量 ( / ) m W MJ m 16 .
16 .1
9
18 29
39 2
重质砖组合样体
轻质砖组合样体纤
轻型隧道 A 7 55
44 1
79 2
7 . 74
窑墙体
B 3o 0
5 7
76 5
7 3 9
连续式轻型隧道窑窑体在正常运行中处于稳态 传热过程 , 其窑体材料主要有足够大的热阻以减少
2 、轻型隧道窑主要 技术参数
窑 全长 :0 6 m
散热。 连续式窑有停窑、烘窑及窑温波动这些非稳 态传热问题 , 因此减少窑体蓄热以求快速烘窑、 停
窑, 并有利 自动控制。 以连续式窑窑体轻型化是 所
.
15 .5
3. 85
维模块组合窑体
注 :蓄热量是指窑墙从常温到达稳态时的蓄热量。
拱顶 的 自重 由墙体 承受 。 型隧道 窑悬 挂式 平 吊顶 轻
热带 窑道上 下部 温差 。
其结构使窑顶和窑墙脱开, 窑顶的 自重力不再作用
于 窑体 , 而全 由钢 架立柱 承受 , 横推力 几乎 为零 。 弧 形拱的 最大缺 陷是 预热 带 , 坯垛 顶面 与拱 顶之 间形
陶瓷窑炉及设计 辊道窑1

SUST
18
陶瓷窑炉与设计----第二章 辊道窑 5.辊道窑的运载装置 包括辊子和辊子的传动装置,它的质量往往影响到窑炉的工作 性能和产量的高低等。应很重视辊道窑的运载装置。
(1)辊子 (a)辊子的材质要求: 一致和平直;很好的抗热震性 ;强的高温抗氧化性能 ;高的 荷重软化温度和小的蠕变性 ;好的耐久性;好的去污性能。
SUST
8
陶瓷窑炉与设计----第二章 辊道窑
辊道窑优点+低温快烧技术=理想烧成设备 陶瓷墙地砖和扁平产品的
SUST
9
陶瓷窑炉与设计----第二章 辊道窑
SUST
10
陶瓷窑炉与设计----第二章 辊道窑
SUST
11
陶瓷窑炉与设计----第二章 辊道窑
4.结构
现代辊道窑结构: 窑体、 燃烧系统、 运载装置、 入出窑机组、 钢结构 自动控制系统
SUST
12
陶瓷窑炉与设计----第二章 辊道窑
(1)窑体
➢窑体分节按模数设计,2.2m为一个模数段,模数段的长度 应为棍子间距的整数倍。
分节模数化实现了辊道窑设计制造的标准化,选用不同的 节数可以十分灵活地组成各种窑长、形成同一的型号,多种 生产能力的辊道窑系列,扩大了实用范围。节与节间用陶瓷 纤维毡子赌塞,起到膨胀缝的作用。
➢窑体采用金属框架承载结构,内衬耐火材料分段定制,现 场组装。
SUST
13
陶瓷窑炉与设计----第二章 辊道窑
➢窑顶采用悬挂式吊顶结构。 减少窑墙的承重,窑体轻型化,取代了老式窑顶采用大板
或拱形砖顶结构,可以延长窑顶的寿命,吊顶横向推力很小, 减少窑内气体分层现象。
➢窑选用轻质隔热耐火材料和陶瓷纤维毡、金属外壳。
窑炉设计

景德镇陶瓷学院《窑炉课程设计》说明书题目:年产860万件汤盘天然气隧道窑设计说明书目录前言一、设计任务书 (4)二、烧成制度的确定2.1 温度制度的确定 (5)三、窑体主要尺寸的计算..3.1棚板和立柱的选择 (5)3.2窑长及各带长的确定 (5)3.2.1 装车方法 (5)3.2.2 窑车尺寸确定 (6)3.2.3窑内宽、内高、全高、全宽的确定 (6)3.2.4 窑长的确定 (7)3.2.5 全窑各带长的确定 (7)四、工作系统的确定4.1 排烟系统 (7)4.2 燃烧系统 (8)4.3 冷却系统 (8)4.4 传动系统 (8)4.5 窑体的附属结构 (8)五、窑体材料及厚度的选择 (8)六、燃料燃烧计算 (12)七、物料平衡计算 (13)八、热平衡计算 (14)九.冷却带的热平衡计算 (18)十、烧嘴的选用 (21)十一、心得体会 (22)十二、参考文献 (23)前言隧道窑是耐火材料、陶瓷和建筑材料工业中最常见的连续式烧成设备。
是以一条类似铁路隧道的长通道为主体,通道两侧用耐火材料和保温材料砌成窑墙,上面为由耐火材料和保温材料砌成的窑顶,下部为由沿窑内轨道移动的窑车构成的窑底形成的一种烧成过程。
随着经济的不断发展,陶瓷工业在人民生产、生活中都占有重要的地位。
陶瓷的发展与窑炉的改革密切相关,某一种特定的窑炉可以烧制出其他窑炉所不能烧制的产品,而有时需要一种特定的产品,就需要对其窑炉的条件加以限制,因此,配方和烧成是陶瓷制品优化的两个重量级过程,每个过程都必须精益求精,才能得到良好,称心的陶瓷制品。
隧道窑是现代化的连续式烧成的热工设备,以窑车为运载工具,具有生产质量稳定、产量大、消耗低的特点,最适合于工艺成熟批量生产的日用瓷。
由于现在能源价格不断上涨,为了节约成本,更好的赢取经济利益,就需要窑炉在烧成过程中严格的控制温度制度、气氛制度,压力制度,提高生产效率及质量,更好的向环保节能型窑炉方向发展。
《QBT6017-2020日用陶瓷厂设计规范》条文说明
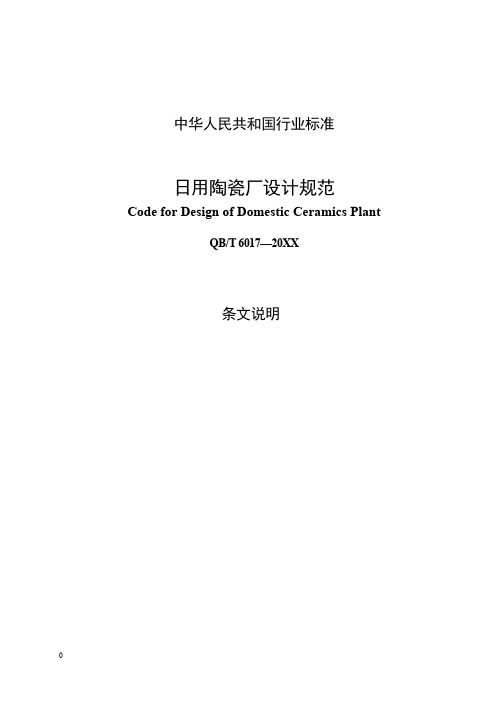
中华人民共和国行业标准日用陶瓷厂设计规范Code for Design of Domestic Ceramics PlantQB/T6017—20XX条文说明修订说明《日用陶瓷厂设计规范》QB/T6017-202X经工业和信息化部202X年X 月X日以第XX号公告批准发布。
本规范修订过程中,编制组进行了广泛征求意见及调查研究,认真总结了我国工程建设设计及咨询的实践经验,同时参考了国外先进技术法规,技术标准,参照原《日用陶瓷厂设计规范》QB/T6017-1997修订本规范。
与1997规范相比,《日用陶瓷厂设计规范》QB/T6017–20xx有以下修改和变动:1、增加第2章“术语和符号”、第14章“节能”、第16章“职业安全卫生”。
2、将原第2章由“总平面布置”修订为第3章“厂址选择和总平面布置”,并增加了有关厂址选择的条文内容。
3、中国作为世界制造业大国,具备十分完善的工业制造体系。
目前,社会分工越来越精细化,外部协作配套功能十分完备,新建工业项目的维修、保全等均实行社会化服务。
因此,本标准删除了原第3章第8节“维修车间”及条文。
4、将原第5章“燃料”的条文进行了大幅的删减,并增加了天然气等清洁燃料的条文。
5、将原“给水排水、消防章”章节拆分为两章,分别为第11章“给水排水”和第13章“消防”。
6、删除原来条文说明中的隧道窑长计算。
7、在第4章“工艺”中增加了第4.7节“包装仓储车间”及相关条文。
8、对原规范中不适应技术进步发展的内容进行了修改和调整。
I9、按照《工程建设规范编写规定》中的相关规定和要求,对原规范中部分条款进行了文字性修改和调整。
1997规范的主编单位:中国轻工总会长沙设计院(中国轻工业长沙工程有限公司的原名)1997规范的主要起草人:黄秉刚张福君翁新藩史维治吴鸣宁诚娃薛瑞元潘凯玲周尔惠李湘洲彭世辂杨泽洪潘瑞珍董光武本次修订过程中,1997规范的一些主要起草人如吴鸣、宁诚娃、彭世辂等,作为本次修订的顾问专家,对规范的修订原则、指导思想及具体条文的技术规定等,提出了中肯的意见和建议。
隧道窑
隧道窑
1.概述 2.隧道窑的结构 3.隧道窑的温度制度
概述
在耐火材料、陶瓷等制品的生产过程中, 烧成是一道重要工序,对产品的产量和质 量影响较大。 烧成设备主要有两大类,一类是连续式窑, 如隧道窑;另一种为间歇式窑,如倒焰窑 等。
高铝砖(3.5 万吨/年): 预热带/烧成带/冷却带 = 72/24/60.6(米)
镁质制品(4~4.5 万吨/年): 预热带/烧成带/冷却带 = 72/24/60(米)
日用瓷(7 x 106 吨/年): 预热带/烧成带/冷却带 = 29.86/26.47/35.67(米)
电瓷(还原焰)(562 万吨/年): 预热带/烧成带/冷却带 = 38.52/28.0/50.07(米)
概念: 一次空气:通过烧嘴直接进入燃烧室(或直接 进入窑内空间)与燃料混合燃烧的空气。它可 以是冷却带抽出的多余热风,可以是冷空气。 二次空气:在冷却带吹入的冷风的一部分,流 到烧成带,与燃料混合燃烧。
一次空气送风装置:风机、喷射器
★一次空气为冷空气时: 冷空气→通风机→空气管道→烧嘴。
★一次空气为热风时: 冷却带的多余热风→耐热风机→管道→烧嘴;
★窑的各带长度确定的一般原则:
1.预热带长度应根据排出废气温度来确 定,废气离开排烟机温 度应低于250℃;
2. 烧成带长度根据保温时间来确定 3.冷却带长度根据出窑制品的温度来确
定,一般应低于100℃
隧道窑长度及各带长度计算式:
V— 隧道窑的有效容积, m3;
隧道窑
1.曲封
曲封:由窑墙与窑车 车衬间凹凸曲折对应 面构成的一种密封结 构
曲封和砂封
曲封形式:窑墙凹进型 窑墙凸出型
图2-15 隧道窑窑体密封
曲封;2-砂封
窑车之间的曲封
2、砂封
由窑墙底部的砂槽和窑车两侧的钢制裙板组成的密封结构 包括裙板、砂封槽、漏砂管 砂子直径3-5mm, 裙板插入深度为50~100mm。
3、观察孔、测温孔、测压孔
热电偶测温
观火孔
2.4
预热带结构分析
隧道窑预热带存在的一个最主要问题:
窑内气体上下分层,热气体集中在上部,冷气体集中在下部。
预热带气体分层的原因(综合教材P17及参考教材P35): (1)处于负压下操作,易吸入外界冷风,冷风密度大,沉在 隧道窑下部,密度较小的热烟气向上流动。 (2)窑内热气体在几何压头作用下有自然向上流动的趋势, 加之料垛上部和窑顶之间空隙较大,阻力小,使大部分热气 体由上部流过。 (3)窑车砌体在下部的吸热,使下部气体温度降低。 上述多种原因,使气体分层十分严重,上下温差最大可达300~ 400℃,如不采取措施,将大大延长预热时间。 参考教材《陶瓷工业热工设备》(刘振群编,武汉理工大学 出版社)
中温阶段(300~950℃)
此阶段坯体内部发生了较复杂的物理化学变化。包括:(1)粘 土和其它含水矿物排除结构水;(2)碳酸盐(如MgCO3、 CaCO3)分解;(3)有机物、碳素和硫化物(如FeS)被氧化, (4)石英晶型转化(转化温度573 ℃)等。
1.3 陶瓷烧成制度之温度制度(据网上资料“ 烧成与烧结)
中间层 隔热 轻质砖 115—230 陶瓷纤维 50—150
2.3.2 窑墙
日用陶瓷火焰隧道窑热平衡、热效率测定与计算方法 计划编号
日用陶瓷火焰隧道窑热平衡、热效率测定与计算方法计划编号【实用版3篇】目录(篇1)- 引言- 火焰隧道窑热平衡测定方法- 火焰隧道窑热效率计算方法- 结论正文(篇1)一、引言随着人们生活水平的提高,日用陶瓷的需求量也在不断增加。
为了提高生产效率,降低能耗,火焰隧道窑被广泛应用于陶瓷生产中。
本文将介绍火焰隧道窑的热平衡和热效率测定方法,以及如何进行计算。
二、火焰隧道窑热平衡测定方法火焰隧道窑的热平衡是指窑炉在一定时间内所传递的热量与窑炉各部分散热量之间的平衡关系。
通过测量窑炉各部分的温度和热流量,可以计算出窑炉的热平衡。
通常,热平衡的测定需要采用热电偶、热辐射计等测量设备,以及数据采集和处理系统。
三、火焰隧道窑热效率计算方法火焰隧道窑的热效率是指窑炉在一定时间内所传递的热量与燃料燃烧所释放的总热量之间的比值。
通过热平衡测定可以得到窑炉的热平衡数据,进而计算出火焰隧道窑的热效率。
火焰隧道窑的热效率受到多种因素的影响,如燃料种类、燃烧温度、窑炉结构等。
因此,在实际应用中,需要根据具体情况进行调整和优化。
四、结论火焰隧道窑是陶瓷生产中常用的加热设备,其热平衡和热效率的测定和计算对于优化窑炉性能、降低能耗具有重要意义。
本文介绍了火焰隧道窑的热平衡和热效率测定方法,以及如何进行计算。
目录(篇2)- 引言- 火焰隧道窑热平衡测定方法- 火焰隧道窑热效率计算方法- 结论正文(篇2)一、引言随着人们对生活品质要求的提高,日用陶瓷的需求量也在逐渐增加。
为了提高生产效率,降低能耗,火焰隧道窑被广泛应用于陶瓷生产中。
本文将介绍火焰隧道窑的热平衡和热效率测定与计算方法。
二、火焰隧道窑热平衡测定方法1.测定原理:通过测量窑内的热量收支,计算出窑内的热平衡。
2.测定步骤:(1)在窑内安装热电偶、热辐射计等测量设备;(2)记录窑内温度变化;(3)根据温度变化计算出窑内的热量收支。
三、火焰隧道窑热效率计算方法1.计算原理:根据热平衡测定结果,计算出火焰隧道窑的热效率。
窑炉设计 隧道窑
洛阳理工学院《隧道窑课程设计》说明书题目:年产30万件蹲便器隧道窑设计学号:B07010221姓名:李志博院(系):材料科学与工程学院专业:无机非金属材料工程指导教师:钱跃进目录1 前言 (1)2 设计任务与原始资料 (4)3 窑体主要尺寸的确定 (5)3.1 装车方法…………………………………………………………………………3.2 窑车尺寸的确定…………………………………………………………………3.3 窑主要尺寸的确定…………………………………………………………………3.4 各带长度的确定3.5 推车时间4 烧成制度的确定…………………………………………………………………………5 工作系统的确定…………………………………………………………………………5.1燃烧系统…………………………………………………………………………5.2排烟系统…………………………………………………………………………5.3其他附属系统结构……………………………………………………………………5.3.1 事故处理孔…………………………………………………………………5.3.2 测温测压孔及观察孔………………………………………………………5.3.3 膨胀缝………………………………………………………………………5.3.4 挡墙…………………………………………………………………………5.3.5 窑体加固钢架结构形式……………………………………………………6 燃料及燃烧计算……………………………………………………………………………6.1 空气量的计算……………………………………………………………………6.2 烟气量的计算……………………………………………………………………6.3 理论燃烧温度的计算………………………………………………………………7 窑体材料及厚度的确定……………………………………………………………………8热平衡计算…………………………………………………………………………………8.1 预热带及烧成带热平衡计算…………………………………………………8.1.1 热平衡计算基准及范围………………………………………………………8.1.2 热平衡框图……………………………………………………………………8.1.3 热收入项目……………………………………………………………………8.1.4 热支出项目……………………………………………………………………8.1.5 列出热平衡方程式……………………………………………………………8.1.6 列出预热带烧成带热平衡表…………………………………………………9 冷却带热平衡………………………………………………………………………………9.2.1 热平衡计算基准及范围………………………………………………………9.2.2 热平衡框图……………………………………………………………………9.2.3 热收入项目……………………………………………………………………9.2.4 热支出项目……………………………………………………………………9.2.5 列出热平衡方程式……………………………………………………………9.2.6 列出冷却带热平衡表…………………………………………………………10 烧嘴的选用…………………………………………………………………………………11总结…………………………………………………………………………………………12参考文献……………………………………………………………………………………二设计任务与原始资料2.1 课程设计的目的与任务本课程的目的是对学生学习《陶瓷工业热工设备》课程的最后总结,学生通过课程设计将能综合运用和巩固所学知识,并学会如何将理论知识和生产实践相结合,去研究解决实际中的工程技术问题,本设计的任务主要是培养学生设计与绘图的基本技能,初步掌握窑炉设计的程序、过程与内容。
- 1、下载文档前请自行甄别文档内容的完整性,平台不提供额外的编辑、内容补充、找答案等附加服务。
- 2、"仅部分预览"的文档,不可在线预览部分如存在完整性等问题,可反馈申请退款(可完整预览的文档不适用该条件!)。
- 3、如文档侵犯您的权益,请联系客服反馈,我们会尽快为您处理(人工客服工作时间:9:00-18:30)。
本设计是年产80万件10寸汤盘隧道窑。
窑炉总长43.5m,有效宽是1.7米,烧成温度是1300℃,烧成周期为24小时。
燃料采用发生炉煤气,燃烧器采用高速烧嘴。
设计的隧道窑,窑体趋向轻型化,烧成质量好,成品率高。
全窑的控制采用计算机自动控制来实现,这样既提高了产品的成品率又降低的工作人员的工作强度,降低了生产成本。
关键词:隧道窑汤盘发生炉煤摘要 (I)前言 (1)1 原始数据 (2)2 烧成制度的确定 (2)3 窑体主要尺寸的确定 (2)3.1 棚板和立柱的选用 (2)3.2 装车方法 (3)3.3 隧道窑有效高度 (3)3.4隧道窑宽度 (3)3.5 窑总长及各带长的确定 (3)3.5.1 窑总长的确定 (3)3.5.2 各带长度的确定 (4)3.6 窑车数量及推车间隔时间 (4)3.7 核算隧道窑的实际生产能力 (4)4 隧道窑工作系统的确定 (4)4.1 燃烧系统的确定 (4)4.2 通风系统的确定 (5)4.2.1 烧成带一次空气送风系统 (5)4.2.2 冷却带抽风系统 (5)4.3 排烟系统 (5)4.4 冷却系统 (5)4.4.1 急冷段 (5)4.4.2 缓冷段 (5)4.4.3 快冷段 (5)4.4.4 窑尾段 (5)5 窑顶结构的确定 (6)6 窑体材料和厚度的确定 (6)6.1 窑体材料确定原则 (6)6.2 整个窑炉的材料名称和厚度 (6)6.2.1窑炉窑墙部分的材料名称和厚度 (6)6.2.2窑炉窑顶部分的材料名称和厚度 (7)7 燃料燃烧计算 (7)7.1 所需空气量 (7)7.2 燃烧产生烟气量 (7)7.3 燃烧温度 (8)8 隧道窑热平衡计算 (9)8.1 预热带、烧成带热平衡 (9)8.1.1 燃料化学热 (9)8.1.2 燃料的显热 (10)8.1.3 助燃空气的显热 (10)8.1.4 入窑坯体带入显热 (10)8.1.5 坯体物化反应过程所需的热量 (10)8.1.6 制品出烧成带带出的显热 (11)8.1.7 其它热量 (11)8.2 冷却带的热平衡计算 (11)8.2.1 烧成带制品带入显热 (11)8.2.2 窑车衬砖及金属件带入显热 (12)8.2.3 冷却制品用空气带入显热 (12)8.2.4 出窑制品带走显热 (12)8.2.5 热空气从冷却带带走热量 (12)9 全窑热平衡及热效率 (12)9.1 全窑热平衡 (12)9.2 隧道窑热效率 (13)10 烧嘴选用及燃烧室计算 (13)10.1烧嘴选用 (13)10.2 燃烧室的计算 (13)11 总结 (14)参考文献 (14)前言随着经济的不断发展,人民生活水平的不断提高,陶瓷工业在人民生产、生活中都占有重要的地位。
陶瓷的发展与窑炉的改革密切相关,一定结构特点的窑炉烧出一定品质的陶瓷。
因此正确选择烧成窑炉是获得性能良好制品的关键。
在日用瓷生产过程,烧成是非常重要的一道工序,烧成过程严重影响着产品的质量。
隧道窑是现代化的连续式烧成的热工设备,以窑车为运载工具,具有生产质量稳定、产量大、消耗低的特点,最适合于工艺成熟批量生产的日用瓷。
由于现在能源价格不断上涨,为了节约成本,更好的赢取经济利益,就需要窑炉在烧成过程中严格的控制温度制度、气氛制度,压力制度,提高生产效率及质量,便于更好的节约燃料,降低能量消耗。
在烧成过程中,温度控制是最重要的关键。
没有合理的烧成控制,产品质量和产量都会很低。
要想得到稳定的产品质量和提高产量,首先要有符合产品的烧成制度。
然后必须维持一定的窑内压力。
最后,必须要维持适当的气氛。
这些要求都应该遵循。
本窑炉采用轻质耐火保温材料,高速调温烧嘴,对余热进行集中利用,产品能耗较低,实现了自动化控制,连续式生产,大大提高了生产效率。
符合大量生产的要求。
在设计过程中,使我对窑炉设计及施工过程有了更深的认识。
隧道窑是当前陶瓷工业中优质、高产、低消耗的先进窑炉,在我国已得到越来越广泛的应用。
1 原始数据设计技术指标、参数:1.年产量:80万件(年工作日330天,合格率97%.2.产品规格:10英寸,0.375kg/件3.汤盘坯料组成(%)4.入窑水分:≤2%5.最高烧成温度:1300℃6.燃料:发生炉煤气7.烧成周期:24h8.气氛制度:还原气氛9.隧道窑:窑车式拱顶隧道窑2 烧成制度的确定根据制品的化学组成、形状、尺寸、线收缩率及其他一些性能要求,制订烧成制度如下:常温-200℃ 3.5小时预热阶段300℃-500℃ 1.0小时预热氧化分解阶段500℃-750℃ 2.0小时预热氧化分解阶段750℃-950℃ 1.0小时预热氧化分解阶段950℃-1300℃ 5.5小时烧成阶段1300℃-1300℃ 2.0小时保温阶段1300℃-800℃ 2.5小时急冷阶段800℃-400℃ 5.0小时缓冷阶段400℃-60℃ 1.5小时快冷阶段3 窑体主要尺寸的确定3.1 棚板和立柱的选用查资料得10寸汤盘的详细参数如下:大小:255×255×30(单位mm) 单件制品质量:0.375kg所以选用棚板的尺寸为:480×480×10 mm 支柱高度:50mm3.2 装车方法在窑车的长度方向上设置3块棚板,宽度方向上设置3块棚板,在窑车高度方向上装10层。
棚板间的间隙在长度方向上为10mm ,棚板与车边间距为20 mm 。
棚板间的间隙在宽度方向上为10mm ,棚板与车边间距为20 mm 。
由此确定窑车车面尺寸为:长:480×3+10×2+20×2=1500mm宽:480×3+10×2+20×2=1500mm窑车架高225mm ,窑车衬面边缘用4层的轻质砖共260mm ,在窑车的中部铺4层硅酸铝纤维棉和1层含锆纤维毯。
窑车总高为:225+260=485mm在车面与棚板间留火道,其高度为200mm 。
3.3 隧道窑有效高度制品距窑顶的距离为200mm ,窑车上装制品的高度为(50+10)×10=600mm ,所以隧道窑有效高度:预热带、冷却带为:200+600+200=1000mm ;为了加强传热,烧成带加高100mm,故烧成带有效窑高为:200+600+200+100=1100mm 。
3.4隧道窑宽度根据窑车和制品的尺寸,窑车车边距窑内墙取100mm ,所以窑内宽B 为1700mm3.5 窑总长及各带长的确定3.5.1 窑总长的确定窑车装载量为1×9×10=90件每车,每件制品的质量为:0.375kg 。
则每车的质量为:33.75kg ,故装窑密度为:3/25)01.005.0(105.15.175.33m Kg kgg =+⨯⨯=日产量为:24.2424330800000=,取2500件/天。
则 h kg G h /3924375.02500=⨯=隧道窑的有效容积3m gt G V h η=36.382597.02439m V =⨯⨯=窑长 3m gAt G L h η= t=24h η=97%g=25kg/3mA=0.6×1.5=0.92mL= (39×24)/(25×0.97×1.35)=42.89m窑车数量n=42.89/1.5=28.6,取29辆,则 隧道窑实际窑长L=29×1.5=43.5m3.5.2 各带长度的确定预热带带长:L t t L 11=m L 6.135.43245.71=⨯= 因窑炉每节长度为1.5米,故预热带取9节。
烧成带带长:L t t L 22=m L 6.135.43245.72=⨯=因窑炉每节长度为1.5米,故预热带取9节。
冷却带带长:L tt L 33=3.165.432493=⨯=L 因窑炉每节长度为1.5米,故预热带取11节。
3.6 窑车数量及推车间隔时间窑车数量n=42.89/1.5=28.6,取29辆 推车时间间隔辆min/50296024,=÷⨯=∆t3.7 核算隧道窑的实际生产能力窑车每车转载质量g=1×9×10×0.375=33.75kgL tJg G p ,6024∆⨯=ηkg kg G p 55100.31016.35097.075.333306024⨯>⨯=⨯⨯⨯⨯=故满足需求。
4 隧道窑工作系统的确定4.1 燃烧系统的确定此窑采用小功率多分布高速调温烧嘴的布置方式。
两侧垂直和水平交错排列,这样有利于均匀窑温和调节烧成曲线。
下部烧嘴喷火口对准装载制品的下部火道,上部烧嘴喷火口对准装载制品上方的部分。
烧嘴砖直接砌筑在窑墙上,采用刚玉莫来石材质。
烧嘴的具体布置情况为:10~18节只设置下部烧嘴8对,共16只。
并在每个烧嘴的对侧窑墙上设置一个观火孔。
烧嘴总数为:16只,助燃风全部为外界空气。
4.2 通风系统的确定4.2.1 烧成带一次空气送风系统燃料燃烧所需的一次空气,一般由风机单独供给,也可用高温风机从冷却带抽出部分热空气送至各烧嘴,但抽出空气温度不能超过风机所能允许的使用温度。
当要求采用高温助燃空气时,可采用喷射器最为一次空气输送装置。
4.2.2 冷却带抽风系统为使制品有效的冷却,从冷却带鼓入的冷风量一般都比燃料燃烧所需的空气量要大,因此,热空气在进入燃烧带之前要从窑内抽出一部分。
为避免烧成带烟气向冷却带倒流,抽热风口位置不宜太靠近烧成带。
4.3 排烟系统为了更好的利用烟气的余热,采用分散排烟的方式。
在预热带第4节箱体位近窑车台面的窑墙上设1对排烟口,使烟气自上而下流动,使得制品受热均匀,最终由排烟机排出,一部分送干燥房,其余的从烟囱排入大气。
4.4 冷却系统制品在冷却带有晶体成长、转化的过程,并且冷却出窑,是整个烧成过程最后的一个环节。
从热交换的角度来看,冷却带实质上是一个余热回收设备,它利用制品在冷却过程中所放出的热量来加热空气,余热风可供干燥用,从而达到节能目的。
4.4.1 急冷段采用直接向窑内吹入冷风的方式,在19节中间位置设置了一道急冷阻挡气幕,19-21节分上下两排设置了12对急冷风管,直接向窑内喷入冷风,并在22节设置了2对侧部抽热风口。
4.4.2 缓冷段制品冷却到800~400℃范围时,是产生冷裂的危险区,应严格控制该段冷却降温速率。
为了达到缓冷的目的,本设计采用间壁冷却的形式,在23至26节设置2组中空墙来进行间壁冷却。
4.4.3 快冷段在27-28节分上下两排设置12对快冷风管,气源为外界空气。
并在顶部设置抽热口,由抽热风机送至干燥室。
4.4.4 窑尾段29节设置3对轴流风机,直接对窑内的制品进行冷却,以保证制品的出窑温度低于60℃。
5 窑顶结构的确定考虑到烧成温度,窑顶重量,保温性能,窑内气流等因素,本隧道窑选取拱顶窑顶。