金刚石刀具切削加工共29页
金刚石切削与精密磨削

2.0.1 金刚石超精密切削
1.金刚石超精密切削技术的进展
金刚石超精密切削是超精密加工技术的一个重要组成部分,早期主 要用来加工有色金属如无氧铀或铝合金等。 采用金刚石超精密切削技术可达到纳米级加工水平,不少国防尖端 产品零件(如陀螺仪、各种平面及曲面反射镜和透镜、精密仪器仪表和大 功率激光系统中的多种零件等)都需要利用金刚石超精密切削来加工。
最大进给速度mm/min 数控系统分辩率/mm
3000、5000或7000
5000 0.0001或0.00005
重复精度(±2σ)/mm
主轴径向圆跳动/mm 主轴轴向圆跳动/mm
≤0.0002/100
≤0.0001 ≤0.0001
滑台运动的直线度/mm
横滑台对主轴的垂直度/mm 主轴前静压轴承(φ100mm)的刚度/(N/μm) 主轴后静压轴承(φ80mm)的刚度/(N/μm) 纵横滑台的静压支承刚度/(N/μm) 径向
3. 误差补偿
2.0.4 精密与超精密加工机床
1.精密与超精密切削机床的性能要求
(1) 很高的精度(包括高的静精度和动精度) 主要指标有主轴的回转精度、导轨运动精度、定位精度、重复定 位精度,分辨率及分度精度。精密车床主轴回转精度一般在1μm之内 ,导轨直线度小于10μm /100mm,精密坐标磨床的定位精度在1~3μm ,分辨率一般为0.01μm ,具有能够进行微量切削并具有在线误差补偿 的微量进给系统。而超精密车床主轴的回转精度大多在0.03~0.05μm ,导轨直线度为0.1~0.2μm /250mm,定位精度为0.01μm ,重复定位 精度为0.006μm ,进给分辨率为0.003~0.008μm ,分度精度为0.5″。 (2) 具有较高的刚度(包括静刚度、动刚度和热刚度)
第二章 特种加工 金刚石切削原理
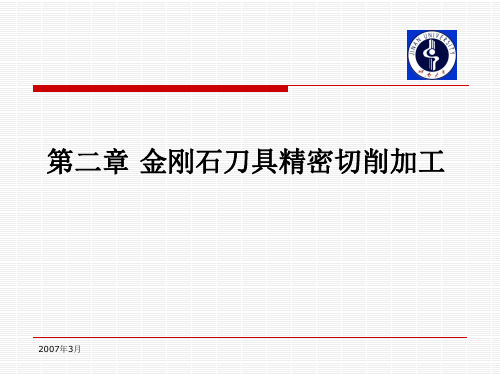
2007年3月
4、微量进给装置
设计要求: 1)精微进给和粗进给分开 2)运动部分必须是低摩擦和高稳定性 3)末端传动元件必须有很高的刚度 4)内部连接必须可靠 5)工艺性好 6)具有好的动特性 7)能实现微进给的自动控制
2007年3月
(1)压电和电致伸缩微进给装置:
2007年3月
(2)摩擦驱动装置:
2007年3月
基本要求: ★高精度 ★高刚度 ★高稳定性 ★高自动化
2007年3月
2、FG—001超精密机床
2007年3月
3、 Cranfield公司的OAGM2500大型超精密机床
◆ 研制时间:1991年 ◆ 工件: 2500X2500X610 mm大型曲面反射镜 ◆ 特点: 立式主轴结构; 龙门结构; 三轴数控联动; X、Y向采用液体 静压导轨,Z向采用空 气轴承 人造花岗岩填充床 身;附带坐标测量。
2007年3月
通用金刚石车刀--2
2007年3月
车刀的刀尖形状
2007年3月
三、金刚石刀具上金刚石的固定方法
(1)机械夹固
2007年3月
(2)用粉末冶金法固定
(3)使用粘结或钎焊固定
2007年3月
金刚石刀具研磨机结构原理图
粗磨的目的:去除余量 (研磨方向、研磨速度、 压力、金刚石微粉粒度) 精研的目的:获得高质量 (金刚石微粉粒度、研磨 盘质量、研磨方向等)
2007年3月
-- 热稳定性: 在700℃以上温度,金刚石易与铁族 金属产生化学作用而形成碳化物,造成化学 磨损。
因此,金刚石单晶的热稳定性较低, 其刀具一般不适合切削钢铁材料。
2007年3月
四、金刚石晶体各晶面的刃磨方向
2007年3月
金刚石切削

金刚石刀具的寿命
1.金刚石刀具破损或磨损而不能 继续使用的标志为加工表面粗糙 度超过规定值 2.实际的金刚石刀具由于切削刃 产生的微小崩刃而不能继续使用 通常就是金刚石(111)面的解理
刀具刃磨
--金刚石刀具刃磨是超精密切削的重要内容
定向 检验 粗研 精研 检验
刀具刃磨主要包括两个方面的内容 1.晶面的选择 2.刀具刃口的刃磨方法 晶面的选择-刀具前刀面 ①主张用(110)面(国外) ②主张用(100)面(国内)
•单晶:晶胞在三维方向上是整齐重复排列
单晶、多晶 各向异性
•多晶:晶胞不是有规律的整齐排列 • 晶面和晶轴不同 • 面网密度和面网间距不同 •(111)面网之间间距大
解理现象 耐磨机理
•(111)相邻面网之间只有一个共价键
•(111)面硬度和耐磨性最高 • 硬度和耐磨性对应于面网密度
晶体受到定向的机械力作用,可以沿平行于某个平面平整的劈开的现象
刀具刃磨新方法
等离子化学抛光法 无损伤化学抛光法 热化学抛光法
极高的硬度、极高的耐磨性和 极高的弹性模量,保证刀具有 很长的寿命和很高的尺寸耐用 度 切削刃钝圆半径要极小才能实 现超薄切削厚度,切削刃无缺 陷 和工件材料的抗粘结性好、化 学亲和性小、摩擦因数低
总结:由于金刚石的这些特点,金刚石被公认 为理想的超精密切削刀具材料
金刚石刀具加工范围
金刚石刀具可以加工有色金属及其合金以及非金 属材料进行高速精细车削及镗孔。 但金刚石也有其本身的缺点 (1)耐热性低,当切削温度超过700-800℃时金 刚石就会石墨化失去硬度 (2)强度低脆性大,对振动敏感只适合于(超)精 密加工,切削厚度不能太大,对机床要求高 (3)与铁有很强的化学亲和力,一般不适于加工黑 色金属(因此利用与铁的亲和性进行金刚石刃磨 )
第二章 金刚石刀具精密切削加工

复习晶体结构
晶格模型
面心结构
晶体结构指晶体内部原子规则排列的方式.晶体结构不同, 其性能往往相差很大。为了便于分析研究各种晶体中原子 或分子的排列情况,通常把原子抽象为几何点,并用许多 假想的直线连接起来,这样得到的三维空间几何格架称为 晶格。
晶胞
Z
晶胞
c
b Y
a
X
晶格常数 a , b, c
人造单晶金刚石刀具 金刚石刀具 PCD刀具
多晶金刚石刀具
CVD金刚石薄膜涂层刀具
CVD金刚石刀具 金刚石厚度膜焊接刀具
金刚石刀具的性能特点
极高的硬度和耐磨性:硬度达HV10000,是自然界最硬的物质, 具有极高的耐磨性,天然金刚石耐磨性为硬质合金80-120倍,人 造金刚石耐磨性为硬质合金60-80倍。 各向异性能:单晶金刚石晶体不同晶面及晶向的硬度、耐磨性能 、微观强度、研磨加工的难易程度以及与工件材料之间的摩擦系 数等相差很大,因此,设计和制造单晶金刚石刀具时,必须进行 晶体定向。
二、典型机床简介
Pneumo 公司的MSG-325超精密车床
采用T形布局,机床空气主轴的径向圆跳动和轴向 跳动均小于等于0.05μm。床身溜板用花岗岩制造,导 轨为气浮导轨;机床用滚珠丝杠和分辨率为0.01μm的 双坐标精密数控系统驱动,用HP5501A双频激光干涉仪 精密检测位移。
DTM-3大型超精密车床
分为:液体静压和空气静压
供油压力恒定的液体静压轴承
主轴始终悬浮 在高压油膜上
液体静压轴承与气压轴承
1、液体静压轴承主轴
优点
回转稳定性好 刚度高 无振动
缺点
回转运动有温升 回油时有空气进入油源 注:空气静压轴承原理与静
#1_第二章 金刚石刀具精密切削加工
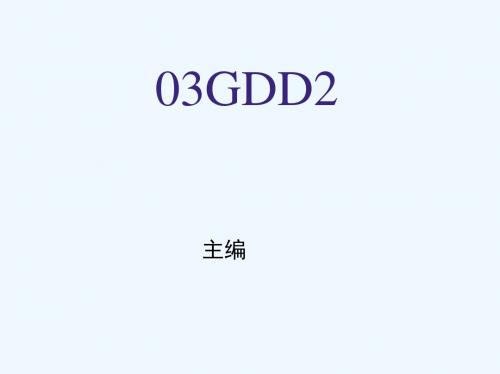
一、金刚石刀具切削部分的几何形状
(1)刀头形式 (2)前角和后角
(1)刀头形式
图2-34 金刚石刀具的刀头形式
(2)前角和后角
图2-35 圆弧修光刃金刚石车刀
(2)前角和后角
图2-36 通用金刚石车刀
二、选择合适的晶面作为金刚石刀具前、后面
单晶金刚石晶体各方向性能(如硬度和耐磨性、 微观强度和解理碎裂的概率、研磨加工的难易 程度等)相差极为悬殊。因此,前面和后面选择 是金刚石刀具设计的一个重要问题。目前国内 制造金刚石刀具,一般前面和后面都采用(110) 晶面或者和(110)晶面相近的面(±3°~5°)。 这主要是从金刚石的这两个晶面易于研磨加工 角度考虑的,而未考虑对金刚石刀具的使用性 能和刀具耐用度的影响。
3.金刚石晶体的解理现象
图2-29 (111)面网的碳原子分布示意图 和解理劈开面
三、金刚石晶体的性能
四、金刚石晶体各晶面的刃磨方向
图2-30 不同晶面研磨时研磨方向与磨削率关系 A—(100)晶面 B—(110)晶面 C—(111)晶面
四、金刚石晶体各晶面的刃磨方向
图2-31 金刚石各晶面的好磨难磨方向 好磨方向
(3)球形—径向空气轴承主轴
图2-11 前球形后圆柱径向轴承的空气轴承主轴 1—球轴承 2—主轴 3—径向轴承
4—电磁联轴器 5—径向及推力轴承 6—带轮
(4)立式空气轴承主轴
图2-12 立式空气轴承主轴 1—多孔石墨轴衬 2—主轴 3—空隙
3.主轴的驱动方式
(1)柔性联轴器驱动 (2)内装式同轴电动机驱动
(1)金刚石晶体各面网的原子排列形式——最小单元
图2-27 金刚石不同晶面的面网的 原子排列形式——最小单元
a)(100)晶面 b)(111)晶面 c)(110)晶面
金刚石刀具超精密切削加工)
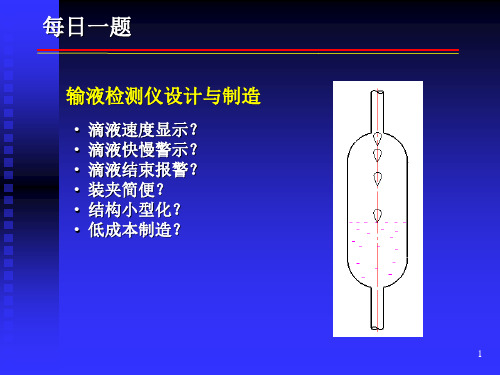
第2章 超精密切削与金刚石刀具
5) 刀具刃口锋锐度ρ ➢ 刃口圆弧半径ρ越小,切削厚度就越薄,越能够减小切
削表面弹性恢复和表面变质层。 ➢ ρ与切削刃的加工方位有关,普通刀具5~30μm,金刚石
刀具<10nm,最好能够< 5nm; ➢ 从物理学的观点,刃口半径ρ有一极限(后续介绍)。
37
ρ
第2章 超精密切削与金刚石刀具
(2)球面镜切削示例
球面镜加工原理
1-主轴;2-凹面镜;3-刀具轴
31
第2章 超精密切削与金刚石刀具
(3)大型金刚石刀具切削机床示例
LLNL的LODTM超精密车床
• Work table: 1.65 m dia
• Figure accuracy: 0.028 μm
• Surface finish :3.5-9.0 nm
35
第2章 超精密切削与金刚石刀具
2.2.2 超精密切削对刀具性能的要求
1) 极高的硬度、极高的耐磨性和极高的弹性模量,保证 长的刀具寿命。
2) 刀刃无缺陷,足够的强度,耐崩刃性能。 3) 切削时切削刃的粗糙度将决定加工表面的粗糙度, 普
通刀刃的粗糙度Ry0.3~5 μm,金刚石刀具刀刃的粗 糙度Ry0.1~0.2 μm,特殊情况Ry1nm,极难刃磨。 4) 化学亲和性小、与工件材料的抗粘结性好、摩擦系数 低,能得到极好的加工表面完整性。
(3) 变形加工 ——利用力、热、分子运动等手段使工件产生变形, 改变其尺寸、形状和性能。
主要包括: 锻造、热流动加工、铸造、液体流动加工等。
77
第1章 绪 论
1.3.2 根据加工过程中材料的流动形态来分类
——去除加工是使材料逐渐减少,一部分材料变为切屑,这 种流动称之为分散流;
超精密切削加工主要指金刚石刀具的超精密切削
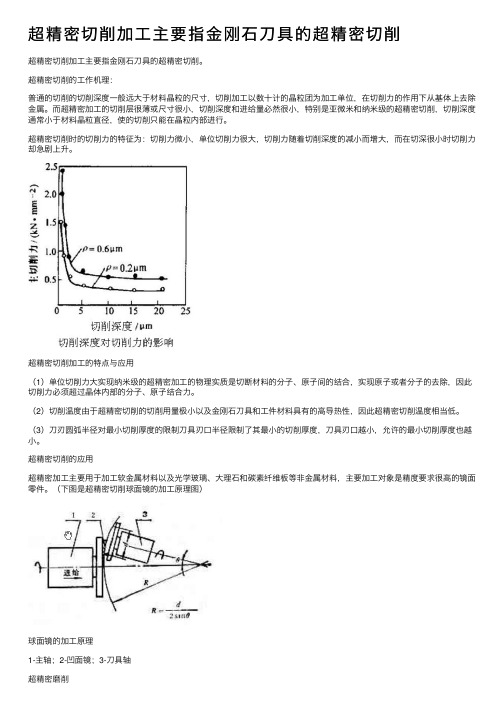
超精密切削加⼯主要指⾦刚⽯⼑具的超精密切削超精密切削加⼯主要指⾦刚⽯⼑具的超精密切削。
超精密切削的⼯作机理:普通的切削的切削深度⼀般远⼤于材料晶粒的尺⼨,切削加⼯以数⼗计的晶粒团为加⼯单位,在切削⼒的作⽤下从基体上去除⾦属。
⽽超精密加⼯的切削层很薄或尺⼨很⼩,切削深度和进给量必然很⼩,特别是亚微⽶和纳⽶级的超精密切削,切削深度通常⼩于材料晶粒直径,使的切削只能在晶粒内部进⾏。
超精密切削时的切削⼒的特征为:切削⼒微⼩,单位切削⼒很⼤,切削⼒随着切削深度的减⼩⽽增⼤,⽽在切深很⼩时切削⼒却急剧上升。
超精密切削加⼯的特点与应⽤(1)单位切削⼒⼤实现纳⽶级的超精密加⼯的物理实质是切断材料的分⼦、原⼦间的结合,实现原⼦或者分⼦的去除,因此切削⼒必须超过晶体内部的分⼦、原⼦结合⼒。
(2)切削温度由于超精密切削的切削⽤量极⼩以及⾦刚⽯⼑具和⼯件材料具有的⾼导热性,因此超精密切削温度相当低。
(3)⼑刃圆弧半径对最⼩切削厚度的限制⼑具刃⼝半径限制了其最⼩的切削厚度,⼑具刃⼝越⼩,允许的最⼩切削厚度也越⼩。
超精密切削的应⽤超精密加⼯主要⽤于加⼯软⾦属材料以及光学玻璃、⼤理⽯和碳素纤维板等⾮⾦属材料,主要加⼯对象是精度要求很⾼的镜⾯零件。
(下图是超精密切削球⾯镜的加⼯原理图)球⾯镜的加⼯原理1-主轴;2-凹⾯镜;3-⼑具轴超精密磨削超精密磨削是当代能达到最低磨削表⾯粗糙度值和最⾼加⼯精度的磨削⽅法。
超精密磨削去除量最薄,采⽤较⼩修整导程和吃⼑量来修整砂轮,是靠超微细磨粒等⾼微刃磨削作⽤,并采⽤较⼩的磨削⽤量磨削。
超精密磨削要求严格消除振动,并保证恒温及超净的⼯作环境。
超精密磨削的光磨微细摩擦作⽤带有⼀定的研抛作⽤性质。
1.超精密砂轮磨削的磨削超精密砂轮磨削机理:( 1 ) 超微量切除超精密磨削是⼀种极薄切削,切屑厚度极⼩,磨削深度可能⼩于晶粒的⼤⼩,磨削就在晶粒内进⾏,因此磨削⼒⼀定要超过晶体内部⾮常⼤的原⼦、分⼦结合⼒,从⽽磨粒上所承受的切应⼒就急速地增加并变得⾮常⼤,可能接近被磨削材料的剪切强度的极限。
金刚石刀具切削加工课件
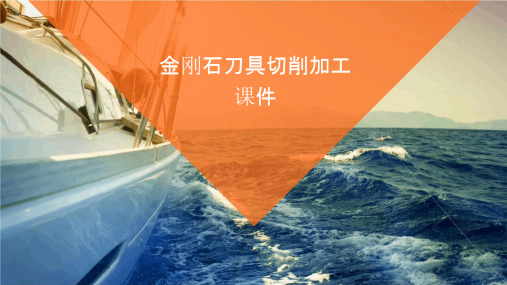
1.谢谢聆 听
03
降低成本和提高经济效益
随着金刚石刀具材料的发展和新型切削工艺的应用,金刚 石刀具在难加工材料切削加工中的应用将会降低成本和提 高经济效益。
金刚石刀具切削加工案例分析
06
案例一
要点一
总结词
高效、高精度、高可靠性
要点二
详细描述
金刚石刀具在汽车零件切削加工中表现出高效、高精度和 高可靠性的优势。通过优化切削参数和刀具设计,能够实 现高效加工,提高生产效率。同时,金刚石刀具具有高硬 度和高耐磨性,可保证加工精度和延长刀具使用寿命。此 外,金刚石刀具切削过程中产生的热量较少,可减少工件 热变形和加工误差。
素有关。
通过合理的选择刀具材料和几何 参数,可以降低切削力,提高加
工效率。
金刚石刀具的切削热
金刚石刀具的切削热主要来自于切削刃与工件之间的摩擦和冲击。
切削热会导致刀具温度升高,从而影响刀具的硬度和耐磨性,甚至引起工件变形和 产生表面缺陷。
通过使用冷却润滑剂和选择合适的刀具材料和几何参数,可以降低切削热的影响。
特点
硬度高、耐磨性好、热稳定性优 异、抗粘结性好、导热性好、化 学稳定性好。
金刚石刀具切削加工的应用范围
01
难加工材料
如硬质合金、陶瓷、玻璃等硬脆材料。
02
高精度加工
如超精密切削、微细加工等。
03
高效率加工
如粗加工、重型切削等。
金刚石刀具切削加工的历史与发展
历史
金刚石刀具的发展可以追溯到20世纪初,当时人们开始利用天然金刚石进行手 工切削。随着科技的发展,人造金刚石的出现进一步推动了金刚石刀具的发展。
智能化控制
随着人工智能技术的发展,智能化控制技术在金刚石刀具切削加工中得到了广泛应用,通 过智能化控制技术,能够对切削过程进行实时监控和调整,从而提高加工精度和效率。