铝合金表面微弧氧化技术的应用及发展
微弧氧化提高铝合金耐磨性能的研究

微弧氧化提高铝合金耐磨性能的研究摘要:铝合金因密度小、比强度高等特点而被广泛应用于航空、航天和其他民用工业中,但其硬度低、不耐磨损。
为了提高铝合金的硬度、耐磨性、耐蚀性以及涂装等性能,须对铝合金表面进行处理。
其中,阳极氧化处理或硬质阳极氧化处理是最常用的方法之一。
近年来,微弧氧化技术(Micro-arc oxidation,MAO)在国内外迅速发展,它是在普通阳极氧化的基础上,利用弧光放电增强并激活在阳极上发生的反应,从而在铝、钛、镁金属及其合金表面形成陶瓷氧化膜。
该技术工艺简单,生成的氧化膜均匀致密,与基体结合强度高,能够大幅度提高阀金属的力学性能,在航天、航空、汽车、电子和机械等行业中具有巨大的应用前景。
关键词:微弧氧化;铝合金;耐磨性;分析1导言微弧氧化技术是在传统的液相电化学氧化反应的基础上发展起来的。
它将工作区域引入到高压放电区域,使金属表面处在微弧形成的等离子体高温(约3000 K)、高压(20~50 MPa)作用下,在金属表面原位生成坚硬、致密的陶瓷氧化膜,如铝合金表面微弧氧化膜主要由α-Al2O3,γ-Al2O3相组成,所得的氧化膜硬度高、与基体结合牢固、结构致密,大大提高了有色金属的耐磨损、耐腐蚀、抗高温冲击及电特性等多种性能。
2微弧氧化技术的机理20世纪30年代初,研究人员等第一次报道了强电场下浸在液体里的金属表面会发生火花放电现象,而且火花对氧化膜具有破坏作用。
后来发现,利用该现象也可制成氧化膜涂层,最初应用于镁合金防腐。
从20世纪70年代开始,美国、德国和前苏联相继开展了这方面的研究。
Vigh等阐述了产生火花放电的原因,提出了“电子雪崩”模型,并利用该模型对放电过程中的析氧反应进行了解释。
Van等随后进一步研究了火花放电的整个过程,指出“电子雪崩”总是在氧化膜最薄弱、最容易被击穿的区域首先进行,而放电时的巨大热应力则是产生“电子雪崩”的主要动力,与此同时,Nikoiaev等提出了微桥放电模型。
铝合金表面微弧氧化处理
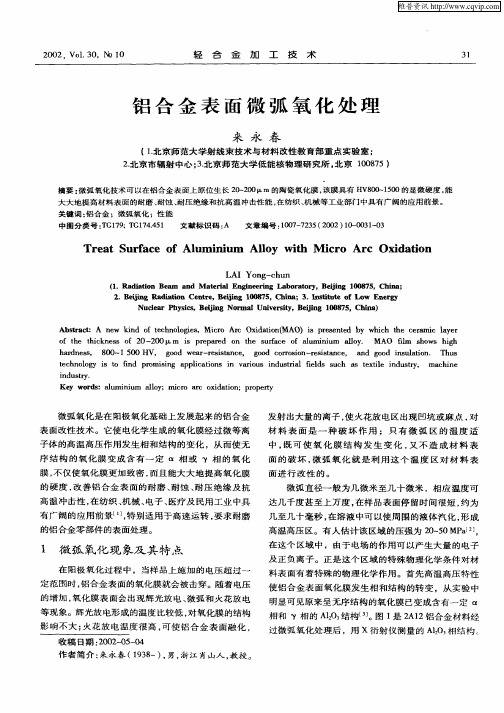
子体 的高 温 高 压作 用 发 生相 和结 构 的 变 化 ,从 而 使 无
序 结 构 的 氧 化 膜 变 成 含 有 一 定 O 或 L相 相 的 氧 化
膜 , 仅 使 氧化 膜 更 加 致密 , 不 而且 能 大 大 地提 高 氧化 膜 的 硬 度 , 善 铝合 金 表 面 的耐 磨 、 蚀 、 压 绝 缘 及 抗 改 耐 耐
维普资讯
2 002
,
V 13 ,N 0 o.0 o1
轻
合
金
加
工
技
术
3 1
铝 合 金 表 面 微 弧 氧 化 处 理
来 永 春
( . 京师 范大 学 射线 束 技术 与 材料 改性 教 育部 重 点实 验 室 ; 1 北 2 京市 辐 射 中心 :. . 北 3北京 师 范大 学 低能 核 物理 研 究所 , 京 1 0 7 北 0 8 5)
A s at e id o eh o g s b t c:A nw kn ft nl i ,Mi o Ac O ia o ( O speet y w i h ea i l e r c oe c r xdt nMA )i rsne b hc te crm c a r r i d h y
发 射 出大 量 的 离子 , 火 花放 电 区出现 凹坑 或麻 点 , 使 对
材料 表 面是 一 种破 坏 作 用 ;只 有微 弧 区 的 温度 适 中 , 可 使 氧 化 膜 结 构 发 生 变 化 , 不 造 成 材 料 表 既 又 面 的 破 坏 , 弧 氧 化 就 是 利 用 这 个 温 度 区 对 材 料 表 微
2-2014微弧氧化技术的研究与应用剖析
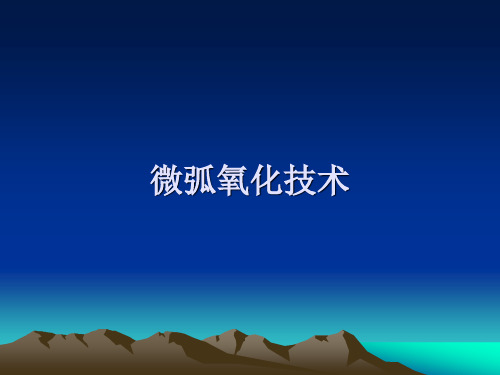
磁控溅射镀膜
• 真空溅射镀膜是指待镀材料源(称为靶)和基 体一起放入真空室中,然后利用正离子轰击作 为阴极的靶,使靶材中的原子、分子逸出并在 基体表面上凝聚成膜。
• 磁控溅射是70年代迅速发展起来的一种“高速低 温溅射技术”。
• 磁控溅射是在阴极靶表面上方形成一个正交电磁 场,当溅射产生的二次电子在阴极位降区内被加 速为高能电子后,并不直接飞向阴极而是在正交 电磁场作用下作来回振荡运动,在运动中高能电 子不断地与气体分子发生碰撞,并向后者转移能 量,使之电离而本身变为低能电子,消除了高能 电子对基体轰击,体现了“低能”特点.
3)整个膜层的厚度较小(﹤300μm),硬度高、耐蚀能力强的致 密层厚度通常只有总厚度的1/5左右。这使得膜层被作为耐磨耐 蚀涂层时的使用寿命受到影响。至今也没有进行过任何针对微 弧氧化膜层的长效可靠性研究。
4)高能耗。微弧氧化反应在高电压、大电流模式下进行,耗能较 大,单个工件的加工面积很难提高,降低了生产效率。
LY12铝合金表面的微弧氧化膜层
Al合金表面生成的微弧氧化膜层以α-Al2O3和γAl2O3为主组成相,另有少量其他反应沉积物如 Al-Si-O等。
AZ91D镁合金表面的微弧氧化膜层(400V) 镁合金表面的微弧氧化膜层以MgO和MgO2
为主组成相,另有少量其他反应沉积物如 Mg2SiO4等。
3、微弧氧化技术的特点
微弧氧化技术的优点主要有: 1)反应在溶液中进行,只要是溶液可及的地方都能够形成膜层,因
此对零件形状的适应性很强。 2)电解液中不含有害物质,反应过程也不会生成新的有毒物质,对
环境无污染。 3)硬度高(HV:500~2500)、耐磨性好,和其他工艺相比与基体
的结合牢固,能够有效弥补轻合金表面不耐磨的缺陷。 4)膜层能够经受高低温的变化,具有较好的热匹配性。 5)膜层的绝缘性能优良(击穿电压可达3000-5000V)。 6)膜层的表面质量较高,光洁度较好且易于着色,适合用作装饰涂
铝合金磷酸盐体系微弧氧化技术研究进展

铝合金磷酸盐体系微弧氧化技术研究进展王平;龚泽宇;胡杰;蒲俊;曹文洁;肖佑涛【摘要】铝合金具有密度低、强度高、塑性好等优点,在航空航天、机械电子、车辆船舶等领域有着广泛的应用前景,但铝合金表面硬度低、耐蚀性较差,这限制了其更广泛的应用.采用磷酸盐电解液体系对铝合金表面进行微弧氧化处理生成氧化膜层,能够有效提高铝合金表面硬度、耐蚀性等性能,是近年来热门的表面处理技术.本文概述铝合金微弧氧化研究历程以及微弧氧化的机制,总结六偏磷酸钠、磷酸二氢钠等单一磷酸盐及其复合体系下铝合金微弧氧化在表面形貌、相组成、硬度厚度、耐蚀性方面的特点,指出目前磷酸盐体系下铝合金微弧氧化中存在一些问题,如因各牌号铝合金中Si、Zn、Mn等元素含量不同而导致的电解液作用机理不同、大型铝合金件局部区域微弧氧化处理困难从而导致处理后得到的微弧氧化膜层不均匀、铝合金微弧氧化膜层在一定厚度范围内会降低基体膜层的抗疲劳性等.今后的研究还需要在磷酸盐电解液体系中各组分的作用、电解液与基体铝合金作用的机理、基体铝合金各元素对微弧氧化过程的影响等方面继续探索.【期刊名称】《西华大学学报(自然科学版)》【年(卷),期】2018(037)004【总页数】7页(P92-98)【关键词】铝合金;微弧氧化;磷酸盐;性能;研究进展【作者】王平;龚泽宇;胡杰;蒲俊;曹文洁;肖佑涛【作者单位】西南石油大学材料科学与工程学院,四川成都 610500;西南石油大学材料科学与工程学院,四川成都 610500;西南石油大学材料科学与工程学院,四川成都 610500;西南石油大学材料科学与工程学院,四川成都 610500;西南石油大学材料科学与工程学院,四川成都 610500;西南石油大学材料科学与工程学院,四川成都 610500【正文语种】中文【中图分类】TG174.4纯铝具有较高的塑性和良好的加工性能,但是强度很低,不宜作为结构材料使用;因此,出现了运用热处理技术和加入合金元素等方法制成的各个系列的铝合金[1]。
微弧氧化
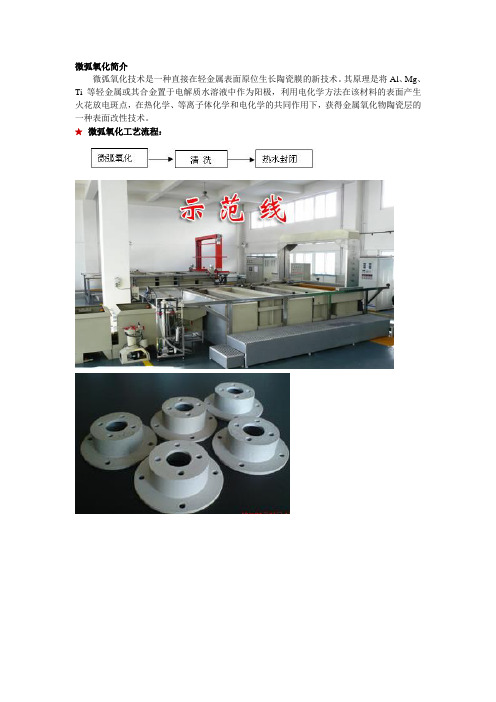
微弧氧化简介微弧氧化技术是一种直接在轻金属表面原位生长陶瓷膜的新技术。
其原理是将Al、Mg、Ti等轻金属或其合金置于电解质水溶液中作为阳极,利用电化学方法在该材料的表面产生火花放电斑点,在热化学、等离子体化学和电化学的共同作用下,获得金属氧化物陶瓷层的一种表面改性技术。
★微弧氧化工艺流程:产品简介:金诺达微弧氧化研发中心是一家集科研、服务与一体的专业为铝、镁、钛轻金属合金零部件表面微弧氧化处理提供微弧氧化处理设备和工艺的高新技术研发中心!一、微弧氧化技术的原理及特点:微弧氧化陶瓷技术是一种在铝、镁、钛等轻金属合金表面原位生长陶瓷层的高新技术。
其原理是在工件表面生成阳极化膜的同时,通过微电弧瞬时7000K高温把极化膜转为陶瓷相。
该陶瓷层硬度高、高耐磨、韧性好、与基体结合力强、耐腐蚀、耐高温氧化、绝缘性好,特别适用于高速运动且需要高耐磨、耐腐蚀、抗高温冲击的轻金属合金零部件。
俄、美、德、日本等国在航空、航天、兵器、汽车、船舶、机械、石油、化工、医疗、电子等行业对该技术的应用已达到相当水平。
该技术的推广应用及产业化必将推进相关行业的发展,成为新的经济增长点。
微弧氧化技术的突出特点是:(1)大幅度地提高了材料的表面硬度,显微硬度在1000至2000HV,可与硬质合金相媲美,大大超过热处理后的高碳钢、高合金钢和高速工具钢的硬度;(2)良好的耐磨损性能;(3)良好的耐热性及抗腐蚀性。
这从根本上克服了铝、镁、钛合金材料在应用中的缺点,因此该技术有广阔的应用前景;(4)有良好的绝缘性能,绝缘电阻可达100MΩ以上。
(5)基体原位生长陶瓷膜,结合牢固,陶瓷膜致密均匀。
二、适用领域:微弧氧化技术广泛应用于航天、航空、兵器、机械、汽车、交通、石油化工、纺织、印刷,烟机,电子、轻工、医疗等行业。
如:铝合金加工成的子母导弹推进器、炮弹的弹底、铝合金阀门、内燃机中的活塞、气动元件中的气缸和阀芯、风动工具中气缸、纺织机械中导纱轮和纺杯、印刷机中搓纸辊和印刷辊等。
微弧氧化技术应用与发展前景分析
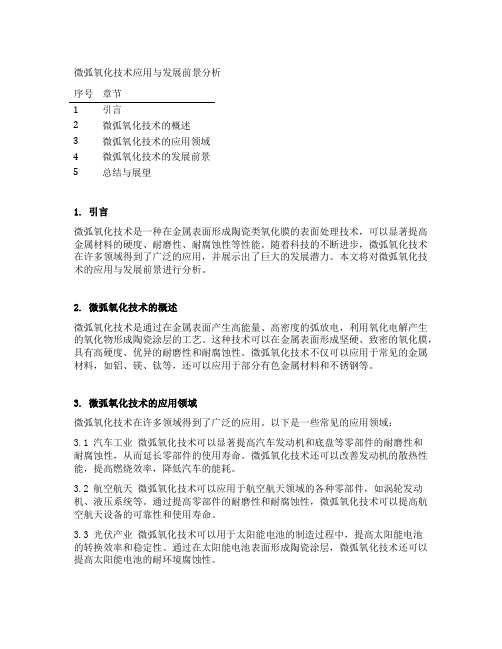
微弧氧化技术应用与发展前景分析序号章节1 引言2 微弧氧化技术的概述3 微弧氧化技术的应用领域4 微弧氧化技术的发展前景5 总结与展望1. 引言微弧氧化技术是一种在金属表面形成陶瓷类氧化膜的表面处理技术,可以显著提高金属材料的硬度、耐磨性、耐腐蚀性等性能。
随着科技的不断进步,微弧氧化技术在许多领域得到了广泛的应用,并展示出了巨大的发展潜力。
本文将对微弧氧化技术的应用与发展前景进行分析。
2. 微弧氧化技术的概述微弧氧化技术是通过在金属表面产生高能量、高密度的弧放电,利用氧化电解产生的氧化物形成陶瓷涂层的工艺。
这种技术可以在金属表面形成坚硬、致密的氧化膜,具有高硬度、优异的耐磨性和耐腐蚀性。
微弧氧化技术不仅可以应用于常见的金属材料,如铝、镁、钛等,还可以应用于部分有色金属材料和不锈钢等。
3. 微弧氧化技术的应用领域微弧氧化技术在许多领域得到了广泛的应用。
以下是一些常见的应用领域:3.1 汽车工业微弧氧化技术可以显著提高汽车发动机和底盘等零部件的耐磨性和耐腐蚀性,从而延长零部件的使用寿命。
微弧氧化技术还可以改善发动机的散热性能,提高燃烧效率,降低汽车的能耗。
3.2 航空航天微弧氧化技术可以应用于航空航天领域的各种零部件,如涡轮发动机、液压系统等。
通过提高零部件的耐磨性和耐腐蚀性,微弧氧化技术可以提高航空航天设备的可靠性和使用寿命。
3.3 光伏产业微弧氧化技术可以用于太阳能电池的制造过程中,提高太阳能电池的转换效率和稳定性。
通过在太阳能电池表面形成陶瓷涂层,微弧氧化技术还可以提高太阳能电池的耐环境腐蚀性。
3.4 建筑工程微弧氧化技术可以应用于建筑物的金属构件,如铝合金门窗、幕墙等。
通过形成坚硬的氧化膜,微弧氧化技术可以提高建筑物金属构件的耐候性和耐腐蚀性,延长其使用寿命。
4. 微弧氧化技术的发展前景微弧氧化技术作为一种表面处理技术,在未来具有广阔的发展前景。
以下是一些对其发展前景的分析:4.1 技术改进与创新目前,微弧氧化技术尚存在一些挑战,如工艺复杂、能耗较高等问题。
铝及铝合金的微弧氧化技术

铝及铝合金微弧氧化技术1.技术内容及技术关键(1)微弧氧化技术内容和工艺步骤铝及铝合金材料微弧氧化技术内容关键包含铝基材料前处理; 微弧氧化; 后处理三部分。
其工艺步骤以下: 铝基工件→化学除油→清洗→微弧氧化→清洗→后处理→成品检验。
(2)微弧氧化电解液组成及工艺条件例1.电解液组成: K2SiO3 5~10g/L, Na2O2 4~6g/L, NaF 0.5~1g/L, CH3COONa 2~3g/L, Na3VO3 1~3g/L; 溶液pH为11~13; 温度为20~50℃; 阴极材料为不锈钢板; 电解方法为先将电压快速上升至300V, 并保持5~10s, 然后将阳极氧化电压上升至450V, 电解5~10min。
例2两步电解法, 第一步: 将铝基工件在200g/LK2O·nSiO2(钾水玻璃)水溶液中以1A/dm2阳极电流氧化5min; 第二步: 将经第一步微弧氧化后铝基工件水洗后在70g/LNa3P2O7水溶液中以1A/dm2阳极电流氧化15min。
阴极材料为: 不锈钢板; 溶液温度为20~50℃。
(3)影响原因①合金材料及表面状态影响: 微弧氧化技术对铝基工件合金成份要求不高, 对部分一般阳极氧化难以处理铝合金材料, 如含铜、高硅铸铝合金均可进行微弧氧化处理。
对工件表面状态也要求不高, 通常不需进行表面抛光处理。
对于粗糙度较高工件, 经微弧氧化处理后表面得到修复变得更均匀平整; 而对于粗糙度较低工件, 经微弧氧化后, 表面粗糙度有所提升。
②电解质溶液及其组分影响: 微弧氧化电解液是获到合格膜层技术关键。
不一样电解液成份及氧化工艺参数, 所得膜层性质也不一样。
微弧氧化电解液多采取含有一定金属或非金属氧化物碱性盐溶液(如硅酸盐、磷酸盐、硼酸盐等), 其在溶液中存在形式最好是胶体状态。
溶液pH范围通常在9~13之间。
依据膜层性质需要, 可添加部分有机或无机盐类作为辅助添加剂。
在相同微弧电解电压下, 电解质浓度越大, 成膜速度就越快, 溶液温度上升越慢, 反之, 成膜速度较慢, 溶液温度上升较快。
铝合金微弧氧化(MAO)
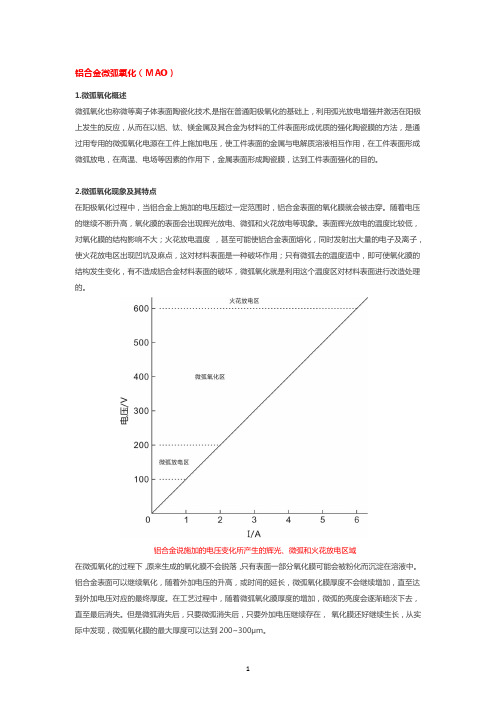
铝合金微弧氧化(MAO)1.微弧氧化概述微弧氧化也称微等离子体表面陶瓷化技术,是指在普通阳极氧化的基础上,利用弧光放电增强并激活在阳极上发生的反应,从而在以铝、钛、镁金属及其合金为材料的工件表面形成优质的强化陶瓷膜的方法,是通过用专用的微弧氧化电源在工件上施加电压,使工件表面的金属与电解质溶液相互作用,在工件表面形成微弧放电,在高温、电场等因素的作用下,金属表面形成陶瓷膜,达到工件表面强化的目的。
2.微弧氧化现象及其特点在阳极氧化过程中,当铝合金上施加的电压超过一定范围时,铝合金表面的氧化膜就会被击穿。
随着电压的继续不断升高,氧化膜的表面会出现辉光放电、微弧和火花放电等现象。
表面辉光放电的温度比较低,对氧化膜的结构影响不大;火花放电温度,甚至可能使铝合金表面熔化,同时发射出大量的电子及离子,使火花放电区出现凹坑及麻点,这对材料表面是一种破坏作用;只有微弧去的温度适中,即可使氧化膜的结构发生变化,有不造成铝合金材料表面的破坏,微弧氧化就是利用这个温度区对材料表面进行改造处理的。
铝合金说施加的电压变化所产生的辉光、微弧和火花放电区域在微弧氧化的过程下,原来生成的氧化膜不会脱落,只有表面一部分氧化膜可能会被粉化而沉淀在溶液中。
铝合金表面可以继续氧化,随着外加电压的升高,或时间的延长,微弧氧化膜厚度不会继续增加,直至达到外加电压对应的最终厚度。
在工艺过程中,随着微弧氧化膜厚度的增加,微弧的亮度会逐渐暗淡下去,直至最后消失。
但是微弧消失后,只要微弧消失后,只要外加电压继续存在,氧化膜还好继续生长,从实际中发现,微弧氧化膜的最大厚度可以达到200~300μm。
微弧氧化与普通阳极氧化一样,也存在着表面氧化和氧离子渗透到基体内与铝离子氧化结合,俗称渗透氧化的过程。
实际发现有大约70%的氧化层存在于铝合金的基体中,因此样品表面的几何尺寸变动不大。
由于渗透氧化,氧化层与基体之间存在着相当厚的过渡层,使氧化膜和基体呈闹牢固的冶金结合,不易脱落,这也是微弧氧化优于电镀和喷涂的地方。
- 1、下载文档前请自行甄别文档内容的完整性,平台不提供额外的编辑、内容补充、找答案等附加服务。
- 2、"仅部分预览"的文档,不可在线预览部分如存在完整性等问题,可反馈申请退款(可完整预览的文档不适用该条件!)。
- 3、如文档侵犯您的权益,请联系客服反馈,我们会尽快为您处理(人工客服工作时间:9:00-18:30)。
铝合金表面微弧氧化技术的应用及发展
作者:张彦涛
来源:《环球市场信息导报》2013年第06期
微弧氧化是一种在金属表面原位生长陶瓷膜的表面处理技术,可大幅提高铝合金表面耐磨性及耐蚀性。
本文阐述了铝合金微弧氧化技术的特点及应用概况,以及微弧氧化技术的发展趋势。
微弧氧化技术又称微等离子体氧化、火花放电阳极氧化。
它是将铝,镁,钛等有色金属及其合金,在适当的电参数条件下使其与电解液中的溶质发生反应,最终在金属表面生成了具有一定厚度的陶瓷膜。
利用该技术在铝及其合金上生长一层Al2O3陶瓷膜,该陶瓷膜具有良好的耐磨、耐蚀性,而且可通过改变电参数和电解液等得到不同性能、不同颜色的陶瓷膜。
铝合金微弧氧化过程
微弧氧化过程中具有等离子体放电通道的高温高压及电解液温度低的特点,在此极限条件下的反应过程可赋予陶瓷膜层其它技术难以获得的优异的耐磨、耐腐蚀等性能,同时使铝合金基体的保持原有性能。
液相中参与反应并形成陶瓷膜的粒子在电场力的作用下传输到基体附近的空间参与成膜,陶瓷膜层的厚度、组成、结构可以通过电源电参数和改变电解液组成进行控制,从而实现陶瓷膜层的设计与构造。
微弧氧化过程一般可以分为以下四个阶段:
普通阳极氧化阶段:在氧化初期,样品表面颜色变暗,形成一层较在电流密度恒定的条件下,电压迅速升高。
该阶段形成的阻挡层是后续阶段产生火花放电的必要条件。
微弧氧化阶段:随着电压的不断升高,在氧化膜层的相对薄弱的地方将会被击穿,在样品表面能够观察到火花放电现象。
这些火花较小,但密度很大(约为105个/cm2),它在样品表面形成了大量的等离子微区。
这些熔融物与电解液发生反应,并被溶液冷却形成Al2O3,从而使这一区域的膜相应地增厚。
微弧氧化和弧放电共存阶段:该阶段样品表面开始出现较大的红色放电弧斑,它是由某些部位经过多次放电后,使得原来较小的放电通道彼此相连而形成较大的放电气孔。
在这一阶段可以观察到电压缓慢下降。
弧放电阶段至反应结束随着薄膜的增厚,红色放电弧斑逐渐减少,电压迅速上升。
最终在样品表面形成具有内部致密层和外部疏松层的双层结构。
铝合金微弧氧化技术特点
微弧氧化是在传统阳极氧化基础上发展而来的,但与阳极氧化相比较,具有其优越的特点:
微弧氧化电解溶液以碱性电解液为主,环境污染小,而阳极氧化为酸性电解液,环境污染大;在基体表面原位生长陶瓷膜,陶瓷膜致密均匀,膜层与基体结合强度高,而阳极氧化膜层比较脆,柔韧性差;良好的耐磨损性,耐热性及抗腐蚀性,一般不需要后处理化学封孔,而阳极氧化膜层耐磨性、耐蚀性较差。
良好的绝缘性能,电阻可达100M ;能大幅度提高铝合金材料的表面硬度,显微硬度一般在100~2000HV的范围内,最高可达3000HV,阳极氧化的最大硬度仅为500HV;通过改变工艺条件和电解液组分或添加胶体微粒等可实现陶瓷膜层的功能化,调整膜层的微观结构及膜层厚度。
总之,微弧氧化技术属于环境友好型技术,工艺简便,受工件形状影响比较小,与电镀、阳极氧化等表面改性技术相比,具有工序简单、效率高、生成的膜层性能良好等优点。
铝合金微弧氧化技术应用现状
20世纪70年代,俄、美、日等世界发达国家在微弧氧化成膜性能、产业化应用等方面投入了大量的研究工作。
我国研究微弧氧化技术开始从于20世纪90年代,研究起步较晚,同时微弧氧化主要集中在实验过程上,理论研究相对滞后。
近年来相关科研院所通过深入研究微弧氧化技术,进一步扩大其应用领域。
主要研究机构为北京师范大学低能核物理研究所,对铝合金微弧氧化陶瓷层的制备过程、能量交换、膜的形貌结构以及应用等都进行了有益的探索,哈尔滨工业大学材料科学与工程学院采用等离子增强电化学表面处理技术(PECC)对铝合金表面陶瓷化处理,研究陶瓷膜层成膜过程和成膜机制,哈尔滨三利亚有限公司由试验阶段开始转向小批量生产,还有北京航空材料研究院、西安理工大学、湖南大学、北京矿冶研究总院等单位参与此技术的研究。
近年来在铝、钛及镁合金微弧氧化的应用开发方面有很大的进步,如蒋百灵等对铝、镁合金微弧氧化设备及工艺技术的研究开发,并在许多领域有所应用。
例如一汽红旗世纪星轿车发动机壳体、镁合金高压热水交换管、镁合金轮毂、铝合金微型冲锋枪托架、铝合金发动机缸体、柴油发动机活塞的表面处理均采用微弧氧化技术进行生产,其成本只有硬质阳极氧化和电镀硬铬的1/3~1/4。
深圳法兰士公司的超硬铝构件、深圳佳驰油泵盖以及某显微镜公司的载物小平台也在使用国产设备进行微弧氧化,产品的耐磨性能较硬质阳极氧化膜提高了35%,并已经开始批量化生产。
相关企业都在积极地推广或应用微弧氧化技术。
微弧氧化技术的发展趋势
将微弧氧化技术应用在铝合金表面改性中,可制备出高硬度、高结合强度的陶瓷膜层,能使铝合金原有的耐磨性差的问题得到大幅度提高,可解决铝合金耐磨性差的问题,并且改善与提高铝合金的耐腐蚀性。
随着人们对微弧氧化技术的不断探索以及该技术日益表现出的独特的
优点,微弧氧化技术在金属表面改性技术领域展示了更为广泛的应用前景,预计其发展趋势有以下几个方面:
微弧氧化电源的优化设计:微弧氧化的合适放电区间较窄,要求对放电后的电参数控制比较精确,大电流、高电压对供电电源提出了高要求,由于对微弧氧化本质认识限制,使得电源的设计及制造仍停留在经验摸索层面上,带有很大的盲目性。
电解液的合理开发及选择:缺乏对单组分电解液及反应机理的深入研究,电解液的选择停留在经验摸索上,难以与微弧氧化电源的合理衔接,进行陶瓷膜层的构造设计。
提高微弧氧化效率:电源消耗的能耗中用到膜层生长的大约为10~30%之间,提高微弧氧化效率也是微弧氧化技术得已推广应用的关键因素之一,还存在电解液冷却困难,消除噪声等问题。
微弧氧化陶瓷膜着色工艺:目前对制备颜色均匀的微弧氧化陶瓷膜的研究重视不够,一步方法完成特定颜色性能良好的陶瓷膜较为困难。