盘式制动器中英文对照外文翻译文献
汽车制动器论文中英文对照资料外文翻译文献

中英文对照资料外文翻译文献Automobile Brake SystemThe braking system is the most important system in cars. If the brakes fail, the result can be disastrous. Brakes are actually energy conversion devices, which convert the kinetic energy (momentum) of the vehicle into thermal energy (heat).When stepping on the brakes, the driver commands a stopping force ten times as powerful as the force that puts the car in motion. The braking system can exert thousands of pounds of pressure on each of the four brakes.Two complete independent braking systems are used on the car. They are the service brake and the parking brake.The service brake acts to slow, stop, or hold the vehicle during normal driving. They are foot-operated by the driver depressing and releasing the brake pedal. The primary purpose of the brake is to hold the vehicle stationary while it is unattended. The parking brake is mechanically operated by when a separate parking brake foot pedal or hand lever is set.The brake system is composed of the following basic components: the “master cylinder” which is located under the hood, and is directly connected tothe brake pedal, converts driver foot’s mechanical pressure into hydraulic pressure. Steel “brake lines” and flexible “brake hoses” connect the master cylin der to the “slave cylinders” located at each wheel. Brake fluid, specially designed to work in extreme conditions, fills the system. “Shoes” and “pads” are pushed by the slave cylinders to contact the “drums” and “rotors” thus causing drag, which (hopefully) slows the car.The typical brake system consists of disk brakes in front and either disk or drum brakes in the rear connected by a system of tubes and hoses that link the brake at each wheel to the master cylinder (Figure).Basically, all car brakes are friction brakes. When the driver applies the brake, the control device forces brake shoes, or pads, against the rotating brake drum or disks at wheel. Friction between the shoes or pads and the drums or disks then slows or stops the wheel so that the car is braked.In most modern brake systems (see Figure 15.1), there is a fluid-filled cylinder, called master cylinder, which contains two separate sections, there is a piston in each section and both pistons are connected to a brake pedal in the driver’s com partment. When the brake is pushed down, brake fluid is sent from the master cylinder to the wheels.At the wheels, the fluid pushes shoes, or pads, against revolving drums or disks. The friction between the stationary shoes, or pads, and the revolving drums or disks slows and stops them. This slows or stops the revolving wheels, which, in turn, slow or stop the car.The brake fluid reservoir is on top of the master cylinder. Most cars today have a transparent r reservoir so that you can see the level without opening the cover. The brake fluid level will drop slightly as the brake pads wear. This is a normal condition and no cause for concern. If the level drops noticeably over ashort period of time or goes down to about two thirds full, have your brakes checked as soon as possible. Keep the reservoir covered except for the amount of time you need to fill it and never leave a cam of brake fluid uncovered. Brake fluid must maintain a very high boiling point. Exposure to air will cause the fluid to absorb moisture which will lower that boiling point.The brake fluid travels from the master cylinder to the wheels through a series of steel tubes and reinforced rubber hoses. Rubber hoses are only used in places that require flexibility, such as at the front wheels, which move up and down as well as steer. The rest of the system uses non-corrosive seamless steel tubing with special fittings at all attachment points. If a steel line requires a repair, the best procedure is to replace the compete line. If this is not practical, a line can be repaired using special splice fittings that are made for brake system repair. Y ou must never use copper tubing to repair a brake system. They are dangerous and illegal.Drum brakes, it consists of the brake drum, an expander, pull back springs, a stationary back plate, two shoes with friction linings, and anchor pins. The stationary back plate is secured to the flange of the axle housing or to the steering knuckle. The brake drum is mounted on the wheel hub. There is aclearance between the inner surface of the drum and the shoe lining. To apply brakes, the driver pushes pedal, the expander expands the shoes and presses them to the drum. Friction between the brake drum and the friction linings brakes the wheels and the vehicle stops. To release brakes, the driver release the pedal, the pull back spring retracts the shoes thus permitting free rotation of the wheels.Disk brakes, it has a metal disk instead of a drum. A flat shoe, or disk-brake pad, is located on each side of the disk. The shoes squeeze the rotatin g disk to stop the car. Fluid from the master cylinder forces the pistons to move in, toward the disk. This action pushes the friction pads tightly against the disk. The friction between the shoes and disk slows and stops it. This provides the braking action. Pistons are made of either plastic or metal. There are three general types of disk brakes. They are the floating-caliper type, the fixed-caliper type, and the sliding-caliper type. Floating-caliper and sliding-caliper disk brakes use a single piston. Fixed-caliper disk brakes have either two or four pistons.The brake system assemblies are actuated by mechanical, hydraulic or pneumatic devices. The mechanical leverage is used in the parking brakes fitted in all automobile. When the brake pedal is depressed, the rod pushes the piston of brake master cylinder which presses the fluid. The fluid flows through the pipelines to the power brake unit and then to the wheel cylinder. The fluid pressure expands the cylinder pistons thus pressing the shoes to the drum or disk. If the pedal is released, the piston returns to the initialposition, the pull backsprings retract the shoes, the fluid is forced back to the master cylinder and braking ceases.The primary purpose of the parking brake is to hold the vehicle stationary while it is unattended. The parking brake is mechanically operated by the driver when a separate parking braking hand lever is set. The hand brake is normally used when the car has already stopped. A lever is pulled and the rear brakes are approached and locked in the “on” position. The car may now be left without fear of its rolling away. When the driver wants to move the car again, he must press a button before the lever can be released. The hand brake must also be able to stop the car in the event of the foot brake failing. For this reason, it is separate from the foot brake uses cable or rods instead of the hydraulic system.Anti-lock Brake SystemAnti-lock brake systems make braking safer and more convenient, Anti-lock brake systems modulate brake system hydraulic pressure to prevent the brakes from locking and the tires from skidding on slippery pavement or during a panic stop.Anti-lock brake systems have been used on aircraft for years, and some domestic car were offered with an early form of anti-lock braking in late 1990’s. Recently, several automakers have introduced more sophisticated anti-lock system. Investigations in Europe, where anti-lock brakin g systems have been available for a decade, have led one manufacture to state that the number of traffic accidents could be reduced by seven and a half percent if all cars hadanti-lock brakes. So some sources predict that all cars will offer anti-lock brakes to improve the safety of the car.Anti-lock systems modulate brake application force several times per second to hold the tires at a controlled amount of slip; all systems accomplish this in basically the same way. One or more speed sensors generate alternating current signal whose frequency increases with the wheel rotational speed. An electronic control unit continuously monitors these signals and if the frequency of a signal drops too rapidly indicating that a wheel is about to lock, the control unit instructs a modulating device to reduce hydraulic pressure to the brake at the affected wheel. When sensor signals indicate the wheel is again rotating normally, the control unit allows increased hydraulic pressure to the brake. This release-apply cycle occurs several time per second to “pump” the brakes like a driver might but at a much faster rate.In addition to their basic operation, anti-lock systems have two other things in common. First, they do not operate until the brakes are applied with enough force to lock or nearly lock a wheel. At all other times, the system stands ready to function but does not interfere with normal braking. Second, if the anti-lock system fail in any way, the brakes continue to operate without anti-lock capability. A warning light on the instrument panel alerts the driver when a problem exists in the anti-lock system.The current Bosch component Anti-lock Braking System (ABSⅡ), is a second generation design wildly used by European automakers such as BWM,Mercedes-Benz and Porsche. ABSⅡsystem consists of : four wheel speed sensor, electronic control unit and modulator assembly.A speed sensor is fitted at each wheel sends signals about wheel rotation to control unit. Each speed sensor consists of a sensor unit and a gear wheel. The front sensor mounts to the steering knuckle and its gear wheel is pressed onto the stub axle that rotates with the wheel. The rear sensor mounts the rear suspension member and its gear wheel is pressed onto the axle. The sensor itself is a winding with a magnetic core. The core creates a magnetic field around the winding, and as the teeth of the gear wheel move through this field, an alternating current is induced in the winding. The control unit monitors the rate o change in this frequency to determine impending brake lockup.The cont rol unit’s function can be divided into three parts: signal processing, logic and safety circuitry. The signal processing section is the converter that receives the alternating current signals form the speed sensors and converts them into digital form for the logic section. The logic section then analyzes the digitized signals to calculate any brake pressure changes needed. If impending lockup is sensed, the logic section sends commands to the modulator assembly. Modulator assemblyThe hydraulic modulator assembly regulates pressure to the wheel brakes when it receives commands from the control utuit. The modulator assembly can maintain or reduce pressure over the level it receives from the master cylinder, it also can never apply the brakes by itself. The modulator assembly consists ofthree high-speed electric solenoid valves, two fluid reservoirs and a turn delivery pump equipped with inlet and outlet check valves. The modulator electrical connector and controlling relays are concealed under a plastic cover of the assembly.Each front wheel is served by electric solenoid valve modulated independently by the control unit. The rear brakes are served by a single solenoid valve and modulated together using the select-low principle. During anti-braking system operation, the control unit cycles the solenoid valves to either hold or release pressure the brake lines. When pressure is released from the brake lines during anti-braking operation, it is routed to a fluid reservoir. There is one reservoir for the front brake circuit. The reservoirs are low-pressure accumulators that store fluid under slight spring pressure until the return delivery pump can return the fluid through the brake lines to the master cylinder.汽车制动系统制动系统是汽车中最重要的系统。
Wabco-Mannheim-Standardpr-sentation-盘式制动器翻译版

Clutch Servo Gear Shift Control Valve Check Valve Foot Brake Valves Relay Valve Trailer Control Valve Load Sensing Valve Quick Release Valve Operating Cylinders Hand Brake Valve Solenoid Valve
就在第一次世界大战爆发前不久的1913年,雷米纳沃克人开始制造汽车。 这些雷米纳汽车在1914年以前生产的大小8/25马力,10/30马力和16/45马力,此外还有一个较小的版本,6/18马力四缸 发动机可用。在1926年以前,这两种30马力和45马力的车型都是在改良和现代化的d型中制造的。 由于经济原因,雷米纳维克提高了汽车的产量。随后,佩罗特四轮制动器的生产许可证和公司成长为一个领先的公司在
Claye Souilly,法国
Servo Clutch Clutch Actuator Hand Brake Valve Pedal Box Car Compressors Leveling Valves
生产基地
Wroclaw, 波兰
Air Dryer
Air Processing Unit
ECAS Solenoid Valve
WABCO
1996 2000
首辆前后装有盘式制动器的货车(12t) 全球首创拖车用气动盘式制动器
2003 开创了22.5”空气盘式制动器的单推杆技术
FULMINA Limousine 16/45 HP 1914
制造商:
FULMINA的作品
技术数据: 四缸直列式发动机, 性能45马力,1800转/分,气缸内径100毫米,冲程130毫米,活塞排量4100 ccm, 热虹吸冷却,独立四速变速箱 ,universal-shaft驱动,底座3450毫米,轨道宽度1350毫米,最大速度90公里/小时
机械专业毕业论文中英文翻译--在全接触条件下,盘式制动器摩擦激发瞬态热弹性不稳定的研究
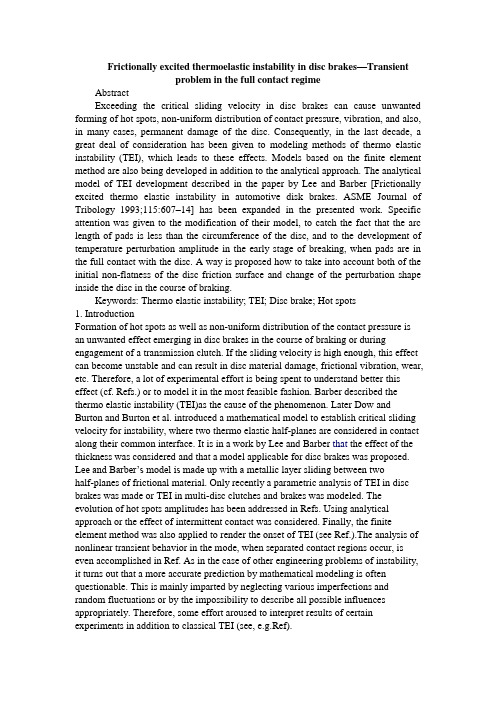
Frictionally excited thermoelastic instability in disc brakes—Transientproblem in the full contact regimeAbstractExceeding the critical sliding velocity in disc brakes can cause unwanted forming of hot spots, non-uniform distribution of contact pressure, vibration, and also, in many cases, permanent damage of the disc. Consequently, in the last decade, a great deal of consideration has been given to modeling methods of thermo elastic instability (TEI), which leads to these effects. Models based on the finite element method are also being developed in addition to the analytical approach. The analytical model of TEI development described in the paper by Lee and Barber [Frictionally excited thermo elastic instability in automotive disk brakes. ASME Journal of Tribology 1993;115:607–14] has been expanded in the presented work. Specific attention was given to the modification of their model, to catch the fact that the arc length of pads is less than the circumference of the disc, and to the development of temperature perturbation amplitude in the early stage of breaking, when pads are in the full contact with the disc. A way is proposed how to take into account both of the initial non-flatness of the disc friction surface and change of the perturbation shape inside the disc in the course of braking.Keywords: Thermo elastic instability; TEI; Disc brake; Hot spots1. IntroductionFormation of hot spots as well as non-uniform distribution of the contact pressure is an unwanted effect emerging in disc brakes in the course of braking or during engagement of a transmission clutch. If the sliding velocity is high enough, this effect can become unstable and can result in disc material damage, frictional vibration, wear, etc. Therefore, a lot of experimental effort is being spent to understand better this effect (cf. Refs.) or to model it in the most feasible fashion. Barber described the thermo elastic instability (TEI)as the cause of the phenomenon. Later Dow and Burton and Burton et al.introduced a mathematical model to establish critical sliding velocity for instability, where two thermo elastic half-planes are considered in contact along their common interface. It is in a work by Lee and Barber that the effect of the thickness was considered and that a model applicable for disc brakes was proposed. Lee and Barber’s model is made up with a metallic layer sliding between twohalf-planes of frictional material. Only recently a parametric analysis of TEI in disc brakes was made or TEI in multi-disc clutches and brakes was modeled. The evolution of hot spots amplitudes has been addressed in Refs. Using analytical approach or the effect of intermittent contact was considered. Finally, the finite element method was also applied to render the onset of TEI (see Ref.).The analysis of nonlinear transient behavior in the mode, when separated contact regions occur, is even accomplished in Ref. As in the case of other engineering problems of instability, it turns out that a more accurate prediction by mathematical modeling is often questionable. This is mainly imparted by neglecting various imperfections and random fluctuations or by the impossibility to describe all possible influences appropriately. Therefore, some effort aroused to interpret results of certain experiments in addition to classical TEI (see, e.g.Ref).This paper is related to the work by Lee and Barber [7].Using an analytical approach, it treats the inception of TEI and the development of hot spots during the full contact regime in the disc brakes. The model proposed in Section 2 enables to cover finite thickness of both friction pads and the ribbed portion of the disc. Section 3 is devoted to the problems of modeling of partial disc surface contact with the pads. Section 4 introduces the term of ‘‘thermal capacity of perturbation’’ emphasizing its association with the value of growth rate, or the sliding velocity magnitude. An analysis of the disc friction surfaces non-flatness and its influence on initial amplitude of perturbations is put forward in the Section 5. Finally, the Section 6 offers a model of temperature perturbation development initiated by the mentioned initial discnon-flatness in the course of braking. The model being in use here comes from a differential equation that covers the variation of the‘‘thermal capacity’’ during the full contact regime of the braking.2. Elaboration of Lee and Barber modelThe brake disc is represented by three layers. The middle one of thickness 2a3 stands for the ribbed portion of the disc with full sidewalls of thickness a2 connected to it. The pads are represented by layers of thickness a1, which are immovable and pressed to each other by a uniform pressure p. The brake disc slips in between these pads at a constant velocity V.We will investigate the conditions under which a spatially sinusoidal perturbation in the temperature and stress fields can grow exponentially with respect to the time in a similar manner to that adopted by Lee and Barber. It is evidenced in their work [7] that it is sufficient to handle only the antisymmetric problem. The perturbations that are symmetric with respect to the midplane of the disc can grow at a velocity well above the sliding velocity V thus being made uninteresting.Let us introduce a coordinate system (x1; y1)fixed to one of the pads (see Fig. 1) thepoints of contact surface between the pad and disc having y1 = 0. Furthermore, let acoordinate system (x2; y2)be fixed to the disc with y2=0 for the points of the midplane. We suppose the perturbation to have a relative velocity ci with respect to the layer i, and the coordinate system (x; y)to move together with the perturbated field. Then we can writeV = c1 -c2; c2 = c3; x = x1 -c1t = x2 -c2t,x2 = x3; y = y2 =y3 =y1 + a2 + a3.We will search the perturbation of the uniform temperature field in the formand the perturbation of the contact pressure in the formwhere t is the time, b denotes a growth rate, subscript I refers to a layer in the model, and j =-1½is the imaginary unit. The parameter m=m(n)=2pin/cir =2pi/L, where n is the number of hot spots on the circumference of the disc cir and L is wavelength of perturbations. The symbols T0m and p0m in the above formulae denote the amplitudes of initial non-uniformities (e.g. fluctuations). Both perturbations (2) and (3) will be searched as complex functions their real part describing the actual perturbation of temperature or pressure field.Obviously, if the growth rate b<0, the initial fluctuations are damped. On the other hand, instability develops ifB〉0.2.1. Temperature field perturbationHeat flux in the direction of the x-axis is zero when the ribbed portion of the disc is considered. Next, let us denote ki = Ki/Qicpi coefficient of the layer i temperature diffusion. Parameters Ki, Qi, cpi are, respectively, the thermal conductivity, density and specific heat of the material for i =1,2. They have been re-calculated to the entire volume of the layer (i = 3) when the ribbed portion of the disc is considered. The perturbation of the temperature field is the solution of the equationsWith and it will meet the following conditions:1,The layers 1 and 2 will have the same temperature at the contact surface2,The layers 2 and 3 will reach the same temperature and the same heat flux in the direction y,3,Antisymmetric condition at the midplaneThe perturbations will be zero at the external surface of a friction pad(If, instead, zero heat flux through external surface has been specified, we obtain practically identical numerical solution for current pads).If we write the temperature development in individual layers in a suitable formwe obtainwhereand2.2. Thermo elastic stresses and displacementsFor the sake of simplicity, let us consider the ribbed portion of the disc to be isotropic environment with corrected modulus of elasticity though, actually, the stiffness of this layer in the direction x differs from that in the direction y. Such simplification is, however, admissible as the yielding central layer 3 practically does not take effect on the disc flexural rigidity unlike full sidewalls (layer 2). Given a thermal field perturbation, we can express the stress state and displacements caused by this perturbation for any layer. The thermo elastic problem can be solved by superimposing a particular solution on the general isothermal solution. We look for the particular solution of a layer in form of a strain potential. The general isothermal solution is given by means of the harmonic potentials after Green and Zerna (see Ref.[18]) and contains four coefficients A, B, C, D for every layer. The relateddisplacement and stress field components are written out in the Appendix A.在全接触条件下,盘式制动器摩擦激发瞬态热弹性不稳定的研究摘要超过临界滑动盘式制动器速度可能会导致形成局部过热,不统一的接触压力,振动分布,而且,在多数情况下,会造成盘式制动闸永久性损坏。
制动器的英文版及翻译

The BrakesThe brakes function by absorbing in friction the energy possessed by the moving car. In so doing they convert the energy into hear. There are tow types of brakes, the drum brake and the disc brake. Either or both types may be fitted. But where both types are used it is usual for the disc brakes to be fitted to the front wheels. In both drum and disc brakes, a hydraulic system applies the brakes. The hydraulic system connects the brake pedal to the brake parts at each wheel.1 、Drum BrakesThe drum brake consists of a pair of semicircular brake shoes mounted on a fixed back plate and situated inside a drum. This drum is fixed to the road wheel and rotates with it .One end of each shoe is on a pivot and a spring holds the other end in contact with the piston of a hydraulic cylinder.(In front brakes it is usual to use two hydraulic cylinders in order to equalize the pressures exerted by the shoes, as shown in Fig.7.1)Each shoe is faced with material ,known as brake lining ,which produces high frictio nal resistance.The hydraulic system comprises a master cylinder and the slave cylinders which are the cylinders on the road wheels. The slave cylinders are connected to the master cylinder by tubing and the whole system is filled with hydraulic fluid .A piston in the master cylinder is connected to the brake pedal, so that when the driver depresses the pedal the fluid is forced out to each slave cylinder and operates their pistons. The fluid pushes the pistons out of their cylinders. They ,in turn, push against the inner ends of the brake shoes and force them against the drums in each wheel. We say that the brakes are on. This friction of the shoes against the drums, which are fixed to the road wheels, slows down or stops the car.As the brake pedal is allowed to come up, the hydraulic fluid returns to its original position, the pistons retract, and a spring attached to each brake shoe returns it also to its original position. Free of the brake drum. Now we say that the brakes are off.(Fig.7.2)The brakes may also be operated by mechanical linkages from the foot pedal and hand brake lever. Common practice is to operate both front and rear brakes hydraulically with a secondary mechanical system operating the rear brakes only from the hand lever. One of the great advantages of hydraulic operation is that the system is self-balancing, which means that the same pressure is automatically produced at all four brakes, whereas mechanical linkages have to be very carefully adjusted for balance. Of course, if more pressure is put on one of the brakes than on the others there is a danger that the car will skid.The mechanical linkage on the rear brakes is a system of rods or cables connecting the handbrake lever to the brake-shoe mechanism, which work entirely independently of the hydraulic system. Drum brakes are prone to a reduction in the braking effort, known as “fade”, caused by the overheating of the brake linings and the drum. Fade can affect all or only some of the brakes at a time, but it is not permanent, and full efficiency returns as soon as the brakes have cooled down. However, fading is unlikely to occur except after the brakes have been used repeatedly in slowing the car from a high speed or after braking continuously down a steep hill. Descending such a hill, it would have been preferable to use engine braking by changing down into a lower gear. Drum brakes can be made less prone to fade by improving the cooling arrangements, by arranging formore air to be deflected over them, for example.2 Disc BrakesThe disc brake consists of a steel disc with friction pads operated by slave hydraulic cylinders. The steel disc is attached to the road wheel and rotates with it. Part of this steel disc is enclosed in a caliper. This caliper contains two friction pads,one on each side of the disc, and two hydraulic cylinders, one outside each pad. The pads are normally held apart by a spring, but when the driver depresses the brake pedal, pistons from the hydraulic cylinders force the pads against the sides of the disc. Because the disc is not enclosed all the way round, the heat generated when the brakes are applied is dissipated very much more quickly than it is from brake shoes which are entirely enclosed inside a drum. This means that disc brakes are less prone to fade than drum brakes.(Fig.7.3)3 、Anti-lock Brake System (ABS)The function of an anti-lock, or anti-skid, braking system is to prevent the wheels from locking under hard braking. Maximum braking force is obtained just before the wheels lock and skid. Such anti-skid system ate useful on slippery surfaces, such as ice and snow, where the wheels may lock easily. Locked wheels are dangerous because the car needs a much longer distance to stop. Locked wheels also can cause the driver to lose control.The system uses a sensor that knows when one wheel (or a pair of wheel) is skidding. (Fig.7.4) The sensor sends a signal to a computer, which signals a modulator valve. The modulator connects into the hydraulic system and can momentarily release the brake pressure and prevent the wheels from locking.(The pressure release is so fast that a driver is seldom aware of it.) pressure is then reapplied until the sensor again senses that the wheel is about to lock up. Thus, this system keeps the wheels as close to lock up as possible, without actually allowing the wheels to lock up and skid. This is called incipient lock up. Maximum braking occurs at that point. If any part of the system should fail to work, the system goes into a “fail-safe” mode. The brakes operate normally, as they would on a car that is not equipped with ABS. Today , ABS is an optional or standard feature that typically is found on expensive luxury cars and sports cars. In the future, ABS may be available for all cars.3.1、ABS overviewAnti-lock braking system is using the body of a rubber balloon, while hitting the brakes, will give brake oil pressure, feeding through to the ABS body, using of the air in the middle of the air layer to return the pressure, make wheels evade the locked points. When the wheel will arrive next locked point, brake oil pressure makes balloon in a repeat function, so can function eight to thirty times in one second equivalent constantly brake, relax, namely, similar to the "mechanical braking ". Therefore, ABS anti-lock braking system, can avoid the orientation losing control , the wheel’s lateral sliding coming up and the wheels rubbing on one point with the ground without being locked in the emergency brake,so it can make the brake friction efficiency achieves ninety percent. It also can reduce the braking consumption and prolong the brake wheel drum, disc and tire twice with the service life of the vehicle in the ABS. On the dry tarmac road or on snowy or on rainy days, the slippery performance reached 80% - 90%, 30% -10%, 15% - 20%. Ordinary braking system on a wet road surface brake, or in the emergency brake, it’s easy for wheels to be locked owing to the braking force exceeds the friction force of the tires and ground. In recent years, the consumers of the vehicle emphasis on the safety , so most of the cars have ABS listed as standard. Without ABS, emergency brake usually cause tire locked, then, the rolling friction becomes sliding friction, as a result, braking force dramatically decreased. And if front wheels are locked first, the vehicle will lose the steering ability; if the rear tires are first locked, the vehicle is easy to slide laterally , so the direction becomes impossible to control. Through electronic or mechanicalcontrol, the ABS system controls the braking fluid pressure at a fast speed to avoid the wheelslocked. Insure the tire have the biggest braking force and the turning ability when braking, and make the vehicle have the ability to evade the obstacles in emergency braking. With the rapid development of the automotive industry, safety increasingly become the important basis of that people choose and buy cars. At present the widespread adoption of holding brake system (ABS) that people can fully meet the safety of requirements. Automobile brake prevent embrace system, referred to as the ABS, is to improve the car an important device passive safety. Someone said brake prevent embrace system is auto safety measures relay belts after another major progress. Automobile braking system is the bus passengers safety is the most important relationship to one of the second systems. With the rapid development of the automotive industry, automobile safety for people appeals more and more attention. Automobile brake prevent embrace system, is another major progress to improve the safety.ABS braking system is controlled by automobile microcomputer, when braking, it can keep the wheel rotating to help driver control vehicle parking safely. The anti-locked braking system detects wheel speed by speed sensor, and then send the wheel speed signals to the microcomputer. The microcomputer controls wheel slipping rate by increasing or decreasing the brake pressure repeatedly according to the input wheel speed to keep wheel rotate. In braking process, keeping wheel rotate not only ensures the ability of controlling driving direction, but also provides higher brake force than the locked wheel in most circumstances, .3.2、The working principle of ABSIt includes control devices and ABS warning lights, in different ABS system, the structure of brake pressure adjusting device and working principle of electronic control devices are often different, the internal structure and control logic of ABS system usually includes the wheel speed sensors, brake pressure adjusting device, electronic identical and so on. In common ABS system, each wheel is installed a rotational speed sensor on the wheel speed, input the signal to electronic control device. The electronic control unit states monitoring and determination according to each wheel speed sensors’ sign al about each wheel movement, and has formed the corresponding control instruction. Brake pressure adjusting device is mainly composed by pressure regulating solenoid valves, electric pump composition and liquid container components compose an independent whole, braking main cylinder and the cylinder brake wheel connected by the brake pipe. Brake pressure adjusting device is controlled by the electronic unit to control all brake wheel cylinders’ brake pressure. The working process of ABS can be divided into general braking, brake pressure kept brake pressure decrease and brake pressure increase stage. In general braking phase, ABS doesn't intervene brake pressure control, pressure regulating electromagnetic valve assembly in various into liquid solenoid valves are no electricity and is open, each produced liquid are no electricity and electromagnetic valve is in the closed position, electric pump also operates without electricity, and brake main cylinder to each brake wheel cylinder brake lines are in communication condition, and the brake wheel cylinder to liquid brake lines are in close condition, the brake wheel cylinder brake pressure change with the output pressure brake master cylinder, the brakingprocess at this time is completely the same with conventional braking system braking process.In braking process, when the electronic control detects that the wheels primarily tend to embrace dies according to the wheel speed sensors of the wheel speed signal input, ABS came into the braking anti-lock process. For example, when the electronic control unit judges the front-right wheel tends to embrace, the electronic control unit will make control scrape the dynamic pressure front-right wheel failure into liquid solenoid valves electricity, make the fluid electromagnetic valve closed, brake main cylinder output brake fluid no longer enter into brake wheel cylinder, right now, right at the end of a fluid electromagnetic valve still energized and closed, the right brake wheel cylinder brake fluid also won't outflow, the right brake wheel cylinder scraping dynamic pressure stays certain, and other arms tend to be dead wheel with still brake pressure braking main cylinder and the increase of output pressure increases; If the right brake wheel cylinder brake pressure keep certain, the electronic control unit front-right wheel failure still tend to judge lock, the electronic control unit and move out liquid solenoid valves also electrify into a state of opening, the part right brake wheel cylinder brake wave will pass is open from fluid electromagnetic valve flow back to liquid container, make right brake wheel cylinder brake pressure holding diminishes quickly front-right wheel failure will start to eliminate death trend, with the right brake wheel cylinder brake pressure decreases, the front-right wheel under the action of inertia force will speed up gradually; accelerate gradually When the electronic control device determines the lock front-right wheel failure to completely eliminate according to the wheel speed sensors input signal, the electronic control unit makes right into the fluid electromagnetic valve and a liquid solenoid valves are without electricity, make into fluid electromagnetic valve to open, use liquid into closed electromagnetic valve, also make electric pump operation, energized to brake wheel cylinder pump brake fluid, output by brake main cylinder brake fluid electromagnetic valve into the right brake wheel cylinders, make right brake wheel cylinder brake pressure increased rapidly, opening up a front-right wheel failure and slow rotation. ABS control the sliding rate of wheels which tend to be locked through holding the brake force of wheels that tends to be locked repeatedly ,adhesion coefficient is in peak within the scope of the sliding rate, until the bus speed reduced to very low or brake main cylinder pressure no longer tend to be locked. Brake pressure to adjust cycle of frequency can reach 3 ~ 20HZ. In the ABS each has on the fluid and the fluid electromagnetic valve in corresponding at each brake wheel cylinder, but by the electronic control device to control, therefore, respectively, the brake wheel cylinder brake pressure can be independently adjustment so that four wheels are not occur braking lock phenomenon. Although various ABS structure form and working process is not exactly the same, are based on the brake holding pressure adaptive cycle adjustment of wheel which tends to be locked, to prevent the controlled wheels holding in death occurred when brake.3.3、ABS functionThe braking performance is one of main auto performance, it is also related to the security of driving. Evaluate the braking performance of a car , the basic index is brake acceleration ,braking distance and direction of braking time and braking stability.Braking stability points to that the vehicle can still be specified in the direction of auto brake when driving in the direction of track. If cars proceed high-speed brake (especially when emergency brake) and make the wheel fully embrace die, it is very dangerous. If front wheel is locked, it will make cars lose steering ability. If the rear wheel is locked, it will appear to swing tail or switching (running deviation, sideslip) especially in the road is all wet slippery case, it will cause the traffic safety great harm. Automobile braking force depends on the brake friction, but the braking force which can make the car brake to slow, and also restricted by ground adhesion coefficient. When brake produces braking force increases to certain value, the tires will appear slipping on the ground. Its sliding rateδ = (Vt - Va) / Vt x 100%δ: delta - sliding rate;Vt - theoretical speed of the car;Va - the actual speed of the car.According to the experiments confirm, when wheel sliding rate delta range from 15% to 20% , the ground adhesion coefficient reach maximum, therefore, in order to get the best braking effect, we must control the slip rate in 15% ~ 20% range.ABS function will namely decrease the brake force when the wheels will embrace dies, , and when the wheel will not hold died and increase braking force, so repeated action, braking effect is the best.3.4、The problems needing attention when ABS is used(1) After replace brake or replace hydraulic brake system components, it should exhaust the air in the brake pipe, lest affect braking system work normally.(2)The car equipped with ABS should be replaced every year. Otherwise, brake fluid hygroscopic is very strong, water will not only reduce the boiling point to make it easy to produce corrosion, and still can cause braking performance recession.(3) To examine ABS braking system should pull power firstly.制动系简介制动器通过摩擦的形式吸收运动车辆所具有的能量而起作用。
机械 车辆工程 外文翻译 外文文献 英文文献 制动器

外文出处: The Brake Bible /brake_bible.html附件2:外文原文The Brake BibleThe simple answer: they slow you down.The complex answer: brakes are designed to slow down your vehicle but probably not by the means that you think. The common misconception is that brakes squeeze against a drum or disc, and the pressure of the squeezing action is what slows you down. This in fact is only part of the equation. Brakes are essentially a mechanism to change energy types. When you're travelling at speed, your vehicle has kinetic energy. When you apply the brakes, the pads or shoes that press against the brake drum or rotor convert that energy into thermal energy via friction. The cooling of the brakes dissipates the heat and the vehicle slows down. It's the First Law of Thermodynamics, sometimes known as the law of conservation of energy. This states that energy cannot be created nor destroyed, it can only be converted from one form to another. In the case of brakes, it is converted from kinetic energy to thermal energy. Angular force. Because of the configuration of the brake pads and rotor in a disc brake, the location of the point of contact where the friction is generated also provides a mechanic al moment to resist the turning motion of the rotor.If you ride a motorbike or drive a race car, you're probably familiar with the term brake fade, used to describe what happens to brakes when they get too hot. A good example is coming down a mountain pass using your brakes rather than your engine to slow you down. As you start to come down the pass, the brakes on your vehicle heat up, slowing you down. But if you keep using them, the rotors or drums stay hot and get no chance to cool off. At some point they can't absorb any more heat so the brake pads heat up instead. In every brake pad there is the friction material that is held together with some sort of resin and once this starts to get too hot, the resin starts to vapourise, forming a gas. Because the gas can't stay between the pad and the rotor, it forms a thin layer between the two whilst trying to escape. The pads lose contact with the rotor, reducing the amount of friction and voila. Complete brake fade.The typical remedy for this would be to get the vehicle to a stop and wait for a few minutes. As the brake components cool down, their ability to absorb heat returns and the next time you use the brakes, they seem to work just fine. This type of brake fade was more common in older vehicles. Newer vehicles tend to have less outgassing from the brake pad compounds but they still suffer brake fade. So why? It's still to do with the pads getting too hot. With newer brake pad compounds, the pads transfer heat into the calipers once the rotors are too hot, and the brake fluid starts to boil forming bubbles in it. Because air is compressible (brake fluid isn't) when you step on the brakes, the air bubbles compress instead of the fluid transferring the motion to the brake calipers. Voila. Modern brake fade.So how do the engineers design brakes to reduce or eliminate brake fade? For older vehicles, you give that vapourised gas somewhere to go. For newer vehicles, you find some way to cool the rotors off more effectively. Either way you end up with cross-drilled or grooved brake rotors. While grooving the surface may reduce the specific heat capacity of the rotor, its effect is negligible in the grand scheme of things. However, under heavy braking once everything is hot and the resin is vapourising, the grooves give the gas somewhere to go, so the pad can continue to contact the rotor, allowing you to stop.The whole understanding of the conversion of energy is critical in understanding how and why brakes do what they do, and why they are designed the way they are. If you've ever watched Formula 1 racing, you'll see the front wheels have huge scoops inside the wheel pointing to the front (see the picture above). This is to duct air to the brake components to help them cool off because in F1 racing, the brakes are used viciously every few seconds and spend a lot of their time trying to stay hot. Without some form of cooling assistance, the brakes would be fine for the first few corners but then would fade and become near useless by half way around the track.Rotor technology.If a brake rotor was a single cast chunk of steel, it would have terrible heat dissipation properties and leave nowhere for the vapourised gas to go. Because of this, brake rotors are typically modified with all manner of extra design features to help them cool down as quickly as possible as well as dissapate any gas from between the pads and rotors. The diagram here shows some examples of rotor types with the various modification that can be done to them to help them create more friction, disperse more heat more quickly, and ventilate gas. From left to right.1: Basic brake rotor. 2: Grooved rotor - the grooves give more bite and thus more friction as they pass between the brake pads They also allow gas to vent from between the pads and the rotor. 3: Grooved, drilled rotor - the drilled holes again give more bite, but also allow air currents (eddies) to blow through the brake disc to assist cooling and ventilating gas. 4: Dual ventilated rotors - same as before but now with two rotors instead of one, and with vanes in between them to generate a vortex which will cool the rotors even further whilst trying to actually 'suck' any gas away from the pads.An important note about drilled rotors: Drilled rotors are typically only found (and to be used on) race cars. The drilling weakens the rotors and typically results in microfractures to the rotor. On race cars this isn't a problem - the brakes are changed after each race or weekend. But on a road car, this can eventually lead to brake rotor failure - not what you want. I only mention this because of a lot of performance suppliers will supply you with drilled rotors for street cars without mentioning this little fact.Big rotors.How does all this apply to bigger brake rotors - a common sports car upgrade? Sports cars and race bikes typically have much bigger discs or rotors than your average family car. A bigger rotor has more material in it so it can absorb more heat. More material also means a larger surface area for the pads to generate friction with, and better heat dissipation. Larger rotors also put the point of contact with the pads further away from the axle of rotation. This provides a larger mechanical advantage to resist the turning of the rotor itself. To best illustrate how this works, imagine a spinning steel disc on an axle in front of you. If you clamped your thumbs either side of the disc close to the middle, your thumbs would heat up very quickly and you'd need to push pretty hard to generate the friction required to slow the disc down. Now imagine doing the same thing but clamping your thumbs together close to the outer rim of the disc. The disc will stop spinning much more quickly and your thumbs won't get as hot. That, in a nutshell explains the whole principle behind why bigger rotors = better stopping power.All brakes work by friction. Friction causes heat which is part of the kinetic energy conversion process. How they create friction is down to the various designs.Bicycle wheel brakesI thought I'd cover these because they're about the most basic type of functioning brake that you can see, watch working, and understand. The construction is very simple and out-in-the-open. A pair of rubber blocks are attached to a pair of calipers which are pivoted on the frame. When you pull the brake cable, the pads are pressed against the side or inner edge of the bicycle wheel rim. The rubber creates friction, which creates heat, which is the transfer of kinetic energy that slows you down. There's only really two types of bicycle brake - those on which each brake shoe shares the same pivot point, and those with two pivot points. If you can look at a bicycle brake and not understand what's going on, the rest of this page is going to cause you a bit of a headache.Drum brakes - single leading edgeThe next, more complicated type of brake is a drum brake. The concept here is simple. Two semicircular brake shoes sit inside a spinning drum which is attached to the wheel. When you apply the brakes, the shoes are expanded outwards to press against the inside of the drum. This creates friction, which creates heat, which transfers kinetic energy, which slows you down. The example below shows a simple model. The actuator in this case is the blue elliptical object. As that is twisted, it forces against the brake shoes and in turn forces them to expand outwards.The return spring is what pulls the shoes back away from the surface of the brake drum when the brakes are released. See the later section for more information on actuator types.The "single leading edge" refers to the number of parts of the brake shoe which actually contact the spinning drum. Because the brake shoe pivots at one end, simple geometry means that the entire brake pad cannot contact the brake drum. The leading edge is the term given to the part of the brake pad which does contact the drum, and in the case of a single leading edge system, it's the part of the pad closest to the actuator. This diagram (right) shows what happens as the brakes are applied. The shoes are pressed outwards and the part of the brake pad which first contacts the drum is the leading edge. The action of the drum spinning actually helps to draw the brake pad outwards because of friction, which causes the brakes to "bite". The trailing edge of the brake shoe makes virtually no contact with the drum at all. This simple geometry explains why it's really difficult to stop a vehicle rolling backwards if it's equipped only with single leading edge drum brakes. As the drum spins backwards, the leading edge of the shoe becomes the trailing edge and thus doesn't bite.Drum brakes - double leading edgeThe drawbacks of the single leading edge style of drum brake can be eliminated by adding a second return spring and turning the pivot point into a second actuator. Now when the brakes are applied, the shoes are pressed outwards at two points. So each brake pad now has one leading and one trailing edge. Because there are two brake shoes, there are two brake pads, which means there are two leading edges. Hence the name double leading edge.Disc brakesSome background. Disc brakes were invented in 1902 and patented by Birmingham car maker Frederick William Lanchester. His original design had two discs which pressed against each other to generate friction and slow his car down. It wasn't until 1949 that disc brakes appeared on a production car though. The obscure American car builder Crosley made a vehicle called the Hotshot which used the more familiar brake rotor and calipers that we all know and love today. His original design was a bit crap though - the brakes lasted less than a year each. Finally in 1954 Citroën launched the way-ahead-of-its-time DS which had the first modern incarnation of disc brakes along with other nifty stuff like self-levelling suspension, semi-automatic gearbox, active headlights and composite body panels. (all things which were re-introduced as "new" by car makers in the 90's).Disc brakes are an order of magnitude better at stopping vehicles than drum brakes, which is why you'll find disc brakes on the front of almost every car and motorbike built today. Sportier vehicles with higher speeds need better brakes to slow them down, so you'll likely see disc brakes on the rear of those too.附件1:外文资料翻译译文制动器制动器:它们的作用?简单的说:它会使你的汽车慢下来。
盘式制动器制动系统原理外文文献翻译、中英文翻译、外文翻译

盘式制动器制动系统原理外文文献翻译、中英文翻译、外文翻译制动系统原理摩擦力是指抵抗两个物体之间相对运动的力。
在制动系统中,通过产生摩擦力来使汽车停止运动或减速行驶。
摩擦力的大小取决于物体表面粗糙度和接触面所受压力的大小。
当发生摩擦运动时,动能就会转化为热能。
因此在刹车时,必须尽量减少热量的产生,以避免制动系统故障。
摩擦力和制动系统在制动系统中,摩擦力的大小是由控制器控制的。
通过改变摩擦力,可以使汽车停止运动或以不同的速度行驶。
控制器通过制动蹄或制动板传递给旋转的制动鼓或制动盘。
当驾驶员踩在制动脚踏板上的力增大时,摩擦力也会随之增加。
车轮在制动摩擦力的作用下逐渐停止转动,但轮胎和地面之间也会产生摩擦力。
制动器上产生的摩擦力必须与轮胎与地面之间产生的摩擦力大小相匹配,避免车轮锁死或打滑的现象。
为了控制车轮在减速时出现打滑的现象,现在广泛使用电脑控制的制动器。
鼓式制动器的基本操作原理鼓式制动器由一个铸造鼓和连接在制动板上的制动蹄构成。
铸造鼓固定在车轮上,随车轮一起转动。
制动器内还有液压缸、弹簧和连接杆等部件。
制动蹄和摩擦材料连接在一起,制动器工作时,摩擦材料贴附在制动鼓的内表面,制动蹄在力的作用下紧贴在制动鼓的内表面,产生摩擦力。
制动器的工作原理是通过液压缸控制制动蹄的运动,使其紧贴在制动鼓上,从而实现制动效果。
在刹车系统开始工作时,盘式制动器的制动片会被推向制动盘。
制动片与制动盘之间的摩擦力会使得车轮减速或停止旋转。
制动盘通常是由铁制成的,而制动片则通常是由摩擦材料制成的。
制动片与制动盘之间的摩擦力是由制动液压缸内部的液压力驱动的。
这种液压力是由操纵者的脚踏板产生的。
盘式制动器的优点是可以承受更高的温度和更大的力量,因为它们的制动面积更大。
此外,盘式制动器的制动片更容易被更换和维护。
缺点是盘式制动器比鼓式制动器更昂贵,并且更容易受到灰尘和水的影响。
总的来说,盘式制动器是一种高效、可靠的刹车系统,适用于高速行驶和紧急制动。
汽车制动系统外文文献翻译、中英文翻译、外文翻译
Automobile Brake SystemThe braking system is the most important system in cars. If the brakes fail, the result can be disastrous. Brakes are actually energy conversion devices, which convert the kinetic energy (momentum) of the vehicle into thermal energy (heat).When stepping on the brakes, the driver commands a stopping force ten times as powerful as the force that puts the car in motion. The braking system can exert thousands of pounds of pressure on each of the four brakes.Two complete independent braking systems are used on the car. They are the service brake and the parking brake.The service brake acts to slow, stop, or hold the vehicle during normal driving. They are foot-operated by the driver depressing and releasing the brake pedal. The primary purpose of the brake is to hold the vehicle stationary while it is unattended. The parking brake is mechanically operated by when a separate parking brake foot pedal or hand lever is set.The brake system is composed of the following basic components: the “master cylinder” which is located under the hood, and is directly connected to the brake pedal, converts driver foot’s mechanical pressure into hydraulic pressure. Steel “brake lines” and flexible “brake hoses” connect the master cylinder to the “slave cylinders” located at each wheel. Brake fluid, specially designed to work in extreme conditions, fills the system. “Shoes” and “pads” are pushed by the slave cylinders to contact the “drums” and “rotors” thus causing drag, which (hopefully) slows the car.The typical brake system consists of disk brakes in front and either disk or drum brakes in the rear connected by a system of tubes and hoses that link the brake at each wheel to the master cylinder .Basically, all car brakes are friction brakes. When the driver applies the brake, the control device forces brake shoes, or pads, against the rotating brake drum or disks at wheel. Friction between the shoes or pads and the drums or disks then slows or stops the wheel so that the car is braked.In most modern brake systems, there is a fluid-filled cylinder, called master cylinder, which contains two separate sections, there is a piston in each section and both pistons are connected to a brake pedal in the driver’s compartment. When the brake is pushed down, brake fluid is sent from the master cylinder to the wheels. At the wheels, the fluid pushes shoes, or pads, against revolving drums or disks. The friction between the stationary shoes, or pads, and the revolving drums or disks slows and stops them. This slows or stops the revolving wheels, which, in turn, slow or stop the car.The brake fluid reservoir is on top of the master cylinder. Most cars today have a transparent r reservoir so that you can see the level without opening the cover. The brake fluid level will drop slightly as the brake pads wear. This is a normal condition and no cause for concern. If the level drops noticeably over ashort period of time or goes down to about two thirds full, have your brakes checked as soon as possible. Keep the reservoir covered except for the amount of time you need to fill it and never leave a cam of brake fluid uncovered. Brake fluid must maintain a very high boiling point. Exposure to air will cause the fluid to absorb moisture which will lower that boiling point.The brake fluid travels from the master cylinder to the wheels through a series of steel tubes and reinforced rubber hoses. Rubber hoses are only used in places that require flexibility, such as at the front wheels, which move up and down as well as steer. The rest of the system uses non-corrosive seamless steel tubing with special fittings at all attachment points. If a steel line requires a repair, the best procedure is to replace the compete line. If this is not practical, a line can be repaired using special splice fittings that are made for brake system repair. You must never use copper tubing to repair a brake system. They are dangerous and illegal.Drum brakes, it consists of the brake drum, an expander, pull back springs, a stationary back plate, two shoes with friction linings, and anchor pins. The stationary back plate is secured to the flange of the axle housing or to the steering knuckle. The brake drum is mounted on the wheel hub. There is a clearance between the innersurface of the drum and the shoe lining. To apply brakes, the driver pushes pedal, the expander expands the shoes and presses them to the drum. Friction between the brake drum and the friction linings brakes the wheels and the vehicle stops. To release brakes, the driver release the pedal, the pull back spring retracts the shoes thus permitting free rotation of the wheels.Disk brakes, it has a metal disk instead of a drum. A flat shoe, or disk-brake pad, is located on each side of the disk. The shoes squeeze the rotatin g disk to stop the car. Fluid from the master cylinder forces the pistons to move in, toward the disk. This action pushes the friction pads tightly against the disk. The friction between the shoes and disk slows and stops it. This provides the braking action. Pistons are made of either plastic or metal. There are three general types of disk brakes. They are the floating-caliper type, the fixed-caliper type, and the sliding-caliper type.Floating-caliper and sliding-caliper disk brakes use a single piston. Fixed-caliper disk brakes have either two or four pistons.Brakes - what do they do?Brakes are designed to slow down your vehicle but probably not by the means that you think. The common misconception is that brakes squeeze against a drum or disc, and the pressure of the squeezing action is what slows you down. This in fact is only part of the equation. Brakes are essentially a mechanism to change energy types. When you're travelling at speed, your vehicle has kinetic energy. When you apply the brakes, the pads or shoes that press against the brake drum or rotor convert that energy into thermal energy via friction. The cooling of the brakes dissipates the heat and the vehicle slows down. It's the First Law of Thermodynamics, sometimes known as the law of conservation of energy. This states that energy cannot be created nor destroyed, it can only be converted from one form to another. In the case of brakes, it is converted from kinetic energy to thermal energy.Angular force. Because of the configuration of the brake pads and rotor in a disc brake, the location of the point of contact where the friction is generated also provides a mechanical moment to resist the turning motion of the rotor.Thermodynamics, brake fade and drilled rotors.If you ride a motorbike or drive a race car, you're probably familiar with the term brake fade, used to describe what happens to brakes when they get too hot. A good example is coming down a mountain pass using your brakes rather than your engine to slow you down. As you start to come down the pass, the brakes on your vehicle heat up, slowing you down. But if you keep using them, the rotors or drums stay hot and get no chance to cool off. At some point they can't absorb any more heat so the brake pads heat up instead. In every brake pad there is the friction material that is held together with some sort of resin and once this starts to get too hot, the resin starts to vapourise, forming a gas. Because the gas can't stay between the pad and the rotor, it forms a thin layer between the two whilst trying to escape. The pads lose contact with the rotor, reducing the amount of friction and voila. Complete brake fade.The typical remedy for this would be to get the vehicle to a stop and wait for a few minutes. As the brake components cool down, their ability to absorb heat returns and the next time you use the brakes, they seem to work just fine. This type of brake fade was more common in older vehicles. Newer vehicles tend to have less outgassing from the brake pad compounds but they still suffer brake fade. So why? It's still to do with the pads getting too hot. With newer brake pad compounds, the pads transfer heat into the calipers once the rotors are too hot, and the brake fluid starts to boil forming bubbles in it. Because air is compressible (brake fluid isn't) when you step on the brakes, the air bubbles compress instead of the fluid transferring the motion to the brake calipers. V oila. Modern brake fade.So how do the engineers design brakes to reduce or eliminate brake fade? For older vehicles, you give that vapourised gas somewhere to go. For newer vehicles, you find some way to cool the rotors off more effectively. Either way you end up with cross-drilled or grooved brake rotors. While grooving the surface may reduce the specific heat capacity of the rotor, its effect is negligible in the grand scheme of things. However, under heavy braking once everything is hot and the resin is vapourising, thegrooves give the gas somewhere to go, so the pad can continue to contact the rotor, allowing you to stop.The whole understanding of the conversion of energy is critical in understanding how and why brakes do what they do, and why they are designed the way they are. If you've ever watched Formula 1 racing, you'll see the front wheels have huge scoops inside the wheel pointing to the front (see the picture above). This is to duct air to the brake components to help them cool off because in F1 racing, the brakes are used viciously every few seconds and spend a lot of their time trying to stay hot. Without some form of cooling assistance, the brakes would be fine for the first few corners but then would fade and become near useless by half way around the track.Rotor technology.If a brake rotor was a single cast chunk of steel, it would have terrible heat dissipation properties and leave nowhere for the vapourised gas to go. Because of this, brake rotors are typically modified with all manner of extra design features to help them cool down as quickly as possible as well as dissapate any gas from between the pads and rotors. The diagram here shows some examples of rotor types with the various modification that can be done to them to help them create more friction, disperse more heat more quickly, and ventilate gas. From left to right.1: Basic brake rotor. 2: Grooved rotor - the grooves give more bite and thus more friction as they pass between the brake pads They also allow gas to vent from between the pads and the rotor. 3: Grooved, drilled rotor - the drilled holes again give more bite, but also allow air currents (eddies) to blow through the brake disc to assist cooling and ventilating gas. 4: Dual ventilated rotors - same as before but now with two rotors instead of one, and with vanes in between them to generate a vortex which will cool the rotors even further whilst trying to actually 'suck' any gas away from the pads.An important note about drilled rotors: Drilled rotors are typically only found (and to be used on) race cars. The drilling weakens the rotors and typically results in microfractures to the rotor. On race cars this isn't a problem - the brakes are changedafter each race or weekend. But on a road car, this can eventually lead to brake rotor failure - not what you want. I only mention this because of a lot of performance suppliers will supply you with drilled rotors for street cars without mentioning this little fact.Big rotors.How does all this apply to bigger brake rotors - a common sports car upgrade? Sports cars and race bikes typically have much bigger discs or rotors than your average family car. A bigger rotor has more material in it so it can absorb more heat.More material also means a larger surface area for the pads to generate friction with,and better heat dissipation. Larger rotors also put the point of contact with the pads further away from the axle of rotation. This provides a larger mechanical advantage to resist the turning of the rotor itself. To best illustrate how this works, imagine a spinning steel disc on an axle in front of you. If you clamped your thumbs either side of the disc close to the middle, your thumbs would heat up very quickly and you'd need to push pretty hard to generate the friction required to slow the disc down. Now imagine doing the same thing but clamping your thumbs together close to the outer rim of the disc. The disc will stop spinning much more quickly and your thumbs won't get as hot. That, in a nutshell explains the whole principle behind why bigger rotors = better stopping power.The different types of brake.All brakes work by friction. Friction causes heat which is part of the kinetic energy conversion process. How they create friction is down to the various designs. Bicycle wheel brakesI thought I'd cover these because they're about the most basic type of functioning brake that you can see, watch working, and understand. The construction is very simple and out-in-the-open. A pair of rubber blocks are attached to a pair of calipers which are pivoted on the frame. When you pull the brake cable, the pads are pressed against the side or inner edge of the bicycle wheel rim. The rubber creates friction, which creates heat, which is the transfer of kinetic energy that slows you down.There's only really two types of bicycle brake - those on which each brake shoe shares the same pivot point, and those with two pivot points. If you can look at a bicycle brake and not understand what's going on, the rest of this page is going to cause you a bit of a headache.Drum brakes - single leading edgeThe next, more complicated type of brake is a drum brake. The concept here is simple. Two semicircular brake shoes sit inside a spinning drum which is attached to the wheel. When you apply the brakes, the shoes are expanded outwards to press against the inside of the drum. This creates friction, which creates heat, which transfers kinetic energy, which slows you down. The example below shows a simple model. The actuator in this case is the blue elliptical object. As that is twisted, it forces against the brake shoes and in turn forces them to expand outwards. The return spring is what pulls the shoes back away from the surface of the brake drum when the brakes are released. See the later section for more information on actuator types.The "single leading edge" refers to the number of parts of the brake shoe which actually contact the spinning drum. Because the brake shoe pivots at one end, simple geometry means that the entire brake pad cannot contact the brake drum. The leading edge is the term given to the part of the brake pad which does contact the drum, and in the case of a single leading edge system, it's the part of the pad closest to the actuator. This diagram (right) shows what happens as the brakes are applied. The shoes are pressed outwards and the part of the brake pad which first contacts the drum is the leading edge. The action of the drum spinning actually helps to draw the brake pad outwards because of friction, which causes the brakes to "bite". The trailing edge of the brake shoe makes virtually no contact with the drum at all. This simple geometry explains why it's really difficult to stop a vehicle rolling backwards if it's equipped only with single leading edge drum brakes. As the drum spins backwards, the leading edge of the shoe becomes the trailing edge and thus doesn't bite.Drum brakes - double leading edgeThe drawbacks of the single leading edge style of drum brake can be eliminated by adding a second return spring and turning the pivot point into a second actuator. Now when the brakes are applied, the shoes are pressed outwards at two points. So each brake pad now has one leading and one trailing edge. Because there are two brake shoes, there are two brake pads, which means there are two leading edges. Hence the name double leading edge.Disc brakesSome background. Disc brakes were invented in 1902 and patented by Birmingham car maker Frederick William Lanchester. His original design had two discs which pressed against each other to generate friction and slow his car down. It wasn't until 1949 that disc brakes appeared on a production car though. The obscure American car builder Crosley made a vehicle called the Hotshot which used the more familiar brake rotor and calipers that we all know and love today. His original design was a bit crap though - the brakes lasted less than a year each. Finally in 1954 Citro毛n launched the way-ahead-of-its-time DS which had the first modern incarnation of disc brakes along with other nifty stuff like self-levelling suspension, semi-automatic gearbox, active headlights and composite body panels. (all things which were re-introduced as "new" by car makers in the 90’s).Disc brakes are an order of magnitude better at stopping vehicles than drum brakes, which is why you'll find disc brakes on the front of almost every car and motorbike built today. Sportier vehicles with higher speeds need better brakes to slow them down, so you'll likely see disc brakes on the rear of those too.The brake system assemblies are actuated by mechanical, hydraulic or pneumatic devices. The mechanical leverage is used in the parking brakes fitted in all automobile. When the brake pedal is depressed, the rod pushes the piston of brake master cylinder which presses the fluid. The fluid flows through the pipelines to the power brake unit and then to the wheel cylinder. The fluid pressure expands the cylinder pistons thus pressing the shoes to the drum or disk. If the pedal is released, the piston returns to theinitialposition, the pull back springs retract the shoes, the fluid is forced back to the master cylinder and braking ceases.The primary purpose of the parking brake is to hold the vehicle stationary while it is unattended. The parking brake is mechanically operated by the driver when a separate parking braking hand lever is set. The hand brake is normally used when the car has already stopped. A lever is pulled and the rear brakes are approached and locked in the “on” position. The car may now be left without fear of its rolling away. When the driver wants to move the car again, he must press a button before the lever can be released. The hand brake must also be able to stop the car in the event of the foot brake failing. For this reason, it is separate from the foot brake uses cable or rods instead of the hydraulic system.Anti-lock Brake SystemAnti-lock brake systems make braking safer and more convenient, Anti-lock brake systems modulate brake system hydraulic pressure to prevent the brakes from locking and the tires from skidding on slippery pavement or during a panic stop.Anti-lock brake systems have been used on aircraft for years, and some domestic car were offered with an early form of anti-lock braking in late 1990’s. Recently, several automakers have introduced more sophisticated anti-lock system.Investigations in Europe, where anti-lock brakin g systems have been available for a decade, have led one manufacture to state that the number of traffic accidents could be reduced by seven and a half percent if all cars had anti-lock brakes. So some sources predict that all cars will offer anti-lock brakes to improve the safety of the car. Anti-lock systems modulate brake application force several times per second to hold the tires at a controlled amount of slip; all systems accomplish this in basically the same way. One or more speed sensors generate alternating current signal whose frequency increases with the wheel rotational speed. An electronic control unit continuously monitors these signals and if the frequency of a signal drops too rapidly indicating that a wheel is about to lock, the control unit instructs a modulating device to reduce hydraulic pressure to the brake at the affected wheel. When sensor signalsindicate the wheel is again rotating normally, the control unit allows increased hydraulic pressure to the brake. This release-apply cycle occurs several time per second to “pump” t he brakes like a driver might but at a much faster rate.In addition to their basic operation, anti-lock systems have two other things in common. First, they do not operate until the brakes are applied with enough force to lock or nearly lock a wheel. At all other times, the system stands ready to function but does not interfere with normal braking. Second, if the anti-lock system fail in any way。
外文翻译---制动系统
外文翻译---制动系统附录1Hydraulic Brake SystemsThe braking system is the most important system in cars. If the brake system fail, the result can be disastrous.When you step on the brake pedal, you expect the vehicle to stop. The brake pedal operates a hydraulic system that is used for two reasons. First, fluid under pressure can be carried to all parts of the vehicle by small hoses or metal lines with out taking up a lot of room or causing routing problems. Second, the hydraulic fluid offers a great mechanical advantage-little foot pressure is required on the pedal, but a great deal of pressure is generated at the wheels. The brake pedal is linked to a piston in the brake master cylinder, which is filled with hydraulic brake fluid. The master cylinder consists of a cylinder containing a small piston and a fluid reservoir.Modern master cylinders are actually two separate cylinders. Such a system is called a dual circuit, because the front cylinder is connected to the front brakes and the rear cylinder to the rear brakes. (Some vehicles are connected diagonally.) The two cylinders are actually separated, allowing for emergency stopping power should one part of the system fail.The entire hydraulic system from the master cylinder to the wheels is full of hydraulic brake fluid. When the brake pedal is depressed, the pistons in the master cylinder are forced to move, exerting tremendous force on the fluid in the lines. The fluid has nowhere to go, and forces the wheel cylinder pistons (drum brakes) or caliper pistons (disc brakes) to exert pressure on the brake shoes or pads. The friction between the brake shoe and wheel drum or the brake pad and rotor (disc) slows the vehicle and eventually stops it.Also attached to the brake pedal is a switch that lights the brake lights as the pedal is depressed. The lights stay on until the brake pedal is released and returns to its normal position.Each wheel cylinder in a drum brake system contains two pistons, one at either end, which push outward in opposite directions. In disc brake systems, the wheel cylinders are part of the caliper (there can be as many as four or as few asone). Whether disc or drum type, all pistons use some type of rubber seal to prevent leakage around the piston, and a rubber dust boot seals the outer ends of the wheel cylinders against dirt and moisture.When the brake pedal is released, a spring pushes the master cylinder pistons back to their normal positions. Check valves in the master cylinder piston allow fluid to flow toward the wheel cylinders or calipers as the piston returns. Then as the brake shoe return springs pull the brake shoes back to the released position, excess fluid returns to the master cylinder through compensating ports, which have been uncovered as the pistons move back. Any fluid that has leaked from the system will also be replaced through the compensating ports.All dual circuit brake systems use a switch to activate a light, warning of brake failure. The switch is located in a valve mounted near the master cylinder.A piston in the valve receives pressure on each end from the front and rear brake circuits. When the pressures are balanced, the piston remains stationary, but when one circuit has a leak, greater pressure during the application of the brakes will force the piston to one side or the other, closing the switch and activating the warning light. The light can also be activated by the ignition switch during engine starting or by the parking brake.Front disc, rear drum brake systems also have a metering valve to prevent the front disc brakes from engaging before the rear brakes have contacted the drums. This ensures that the front brakes will not normally be used alone to stop the vehicle. A proportioning valve is also used to limit pressure to the rear brakes to prevent rear wheel lock-up during hard braking.1. Friction materialsBrake shoes and pads are constructed in a similar manner. The pad or shoe is composed of a metal backing plate and a friction lining. The lining is either bonded (glued) to the metal, or riveted. Generally, riveted linings provide superior performance, but good quality bonded linings are perfectly adequate.Friction materials will vary between manufacturers and type of pad and the material compound may be referred to as: asbestos, organic, semi-metallic, metallic. The difference between these compounds lies in the types and percentages of friction materials used, material binders and performance modifiers.Generally speaking, organic and non-metallic asbestos compound brakesare quiet, easy on rotors and provide good feel. But this comes at the expense of high temperature operation, so they may not be your best choice for heavy duty use or mountain driving. In most cases, these linings will wear somewhat faster than metallic compound pads, so you will usually replace them more often. But, when using these pads, rotors tend to last longer.Semi-metallic or metallic compound brake linings will vary in performance based on the metallic contents of the compound. Again, generally speaking, the higher the metallic content, the better the friction material will resist heat. This makes them more appropriate for heavy duty applications, but at the expense of braking performance before the pad reaches operating temperature. The first few applications on a cold morning may not give strong braking. Also, metallic and semi-metallic are more likely to squeal. In most cases, metallic compounds last longer than non-metallic pads, but they tend to cause more wear on the rotors. If you use metallic pads, expect to replace the rotors more often.When deciding what type of brake lining is right for you, keep in mind that today's modern cars have brake materials which are matched to the expected vehicle's performance capabilities. Changing the material from OEM specification could adversely affect brake feel or responsiveness. Before changing the brake materials, talk to your dealer or parts supplier to help decide what is most appropriate for your application. Remember that heavy use applications such as towing, stop and go driving, driving down mountain roads, and racing may require a change to a higher performance material.Some more exotic materials are also used in brake linings, among which are Kevlar and carbon compounds. These materials have the capability of extremely good performance for towing, mountain driving or racing. Wear characteristics can be similar to either the metallic or the non-metallic linings, depending on the product you buy. Most race applications tend to wear like metallic linings, while many of the street applications are more like the non-metallic.2. Brake fluidOn a disk brake, the fluid from the master cylinder is forced into a caliper where it presses against a piston. The piston, in-turn, squeezes two brake pads against the disk(rotor)which is attached to the wheel, forcing it to slow down or stop. This process is similar to a bicycle brake where two rubber pads rub against the wheel rim creating friction.With drum brakes, fluid is forced into the wheel cylinder which pushes the brake shoes out so that the friction linings are pressed against the drum which is attached to the wheel, causing the wheel to stop.In either case, the friction surfaces of the pads on a disk brake system, or the shoes on a drum brake convert the forward motion of the vehicle into heat. Heat is what causes the friction surfaces (linings) of the pads and shoes to eventually wear out and require replacement.Brake fluid is a special oil that has specific properties. It is designed to withstand cold temperatures without thickening as well as very high temperatures without boiling.(If the brake fluid should boil, it will cause you to have a spongy pedal and the car will be hard to stop). Figure shows a brake hydraulic system.The brake fluid reservoir is on top of the master cylinder. Most cars today have a transparent r reservoir so that you can see the level without opening the cover. The brake fluid level will drop slightly as the brake pads wear. This is a normal condition and no cause for concern. If the level drops noticeably over a short period of time or goes down to about two thirds full, have your brakes checked as soon as possible. Keep the reservoir covered except for the amount of time you need to fill it and never leave a cam of brake fluid uncovered. Brake fluid must maintain a very high boiling point. Exposure to air will cause the fluid to absorb moisture which will lower that boiling point.The brake fluid travels from the master cylinder to the wheels through a series of steel tubes and reinforced rubber hoses. Rubber hoses are only used in places that require flexibility, such as at the front wheels, which move up and down as well as steer. The rest of the system uses non-corrosive seamless steel tubing with special fittings at all attachment points. If a steel line requires a repair, the best procedure is to replace the compete line. If this is not practical, a line can be repaired using special splice fittings that are made for brake system repair. You must never use copper tubing to repair a brake system. They are dangerous and illegal.制动系统制动系统是汽车中最重要的系统。
制动器零件中英文对照
CE-1FRT BRAKE[breik]ASS'Y — LH/RH 前左/右转向节带盘式制动器轮毂总成KNUCKLE[’nʌkl]ASS'Y WITH HUB[hʌb]BEARING[’bεəriŋ]— LH/RH左/右转向节带轮毂总成KNUCKLE M/C — LH/RH左/右转向节KNUCKLE CASTING[’kɑ:stiŋ]- LH/RH左/右转向节毛坯BEARING — 1ST GEN双列球轴承CIRCLIP ['sə:klip]孔用弹性挡圈HUB FLANGE[flændʒ]前轮毂WHEEL[hwi:l]MT'G BOLT[bəult]前轮毂螺栓SPLASH[splæʃ]SHIELD[ʃi:ld]前防溅罩BOLT - D/COVER 六角梅花头组合螺栓M6×14DISC[disk]M/C 前制动盘FLANGE BOLT 支架安装螺栓M12×1。
25×28FRT. CALIPER ['kælipə(r)] ASS'Y-LH/RH 前左/右制动钳总成CYLINDER['silində] M/C [PLATING['pleitiŋ]] -LH/RH 前左/右制动钳体CYLINDER CAST’G [PLATING]- LH/RH 前左/右制动钳体毛坯BOOT[bu:t]PISTON['pistən] ASS’Y前钳体活塞防尘罩RIM[rim] - BOOT PISTON 骨架BOOT PISTON前活塞防尘罩SEAL[si:l]PISTON 前活塞密封圈PISTON M/C 前钳体活塞CARRIER['kæriə]M/C [PLATING]制动钳支架CARRIER CASTING 制动钳支架毛坯GUIDE[ɡaid] PILLAR['pilə]SHIELD[ʃi:ld] 导柱防尘盖GUIDE PILLAR CUSHION[’kuʃən] COLLAR['kɔlə] 导柱缓冲套GUIDE ROD[rɔd]导柱ASS’Y PAD[pæd] - LH/RH 左/右内/外制动衬块总成BERAKE LINING[’lainiŋ] WEAR[’wεə]SENSOR[’sensə,-sɔ:]- LH/RH左/右报警弹簧片SNAP[snæp] RING[riŋ]卡簧VIBRATION[vai'breiʃən] DAMPING[’dæmpiŋ]PIECE[pi:s] 内/外减振片PAD KIT[kit] 内/外制动衬块LINING 摩擦材料INTERNAL[in’tə:nəl]BRAKE PAD BASEPLATE[beis—pleit]内制动衬块底板EXTERNA L[ik'stə:nəl] BRAKE PAD BASEPLATE 外制动衬块底板PLACING[’pleisiŋ] STEEL[sti:l]WIRE ['waiə] 限位钢丝BLEED [bli:d] SCREW [skru:]放气螺钉CAP[kæp] BLEED SCREW 放气螺钉防尘罩PLUG [plʌɡ]堵头REAR [riə]CORNER[’kɔ:nə]ASS’Y — LH/RH 左/右后鼓式制动器带轮毂总成DRUM [drʌm] M/C 后制动鼓DRUM CASTING 后制动鼓毛坯WHEEL BEARING ASS’Y - 3RD GEN 左/右后轮毂轴承单元DRUM BRAKE ASS'Y-LH/RH左/右后制动器总成BACK [bæk]PLATE ASS'Y-LH/RH 左/右后制动底板总成BACK PLATE PIERCING[’piəsiŋ]-LH/RH 左/右后制动底板CABLE ['keibl]GUIDE—LH/RH 左/右拉线导向块RIVET['rivit] 铆钉LOCATING[ləu’keitiŋ] PLATE 支承块BEARING SLICE[slais] 支承片SHOE[ʃu:]HOLD[həuld]DOWN[daun]PIN[pin]制动蹄压下销HEXAGON[’heksəɡən]HEAD[hed] ASSEMBLING[ə’sembliŋ]BOLT六角头组合螺栓LINED SHOE ASS'Y -LH/RH左/右从蹄带摩擦片拉杆总成WAVE[weiv]—PATTERN[’pætən]GASKET[’ɡæskit]波形垫圈OPERATING[’ɔpəreitiŋ]LEVER['li:və,’le-]—LH/RH 左/右拉杆PULLING['puliŋ]ROD RIVET 拉杆铆钉WEB[web] 制动蹄筋BRAKE SHOE STRETCHED[stretʃd] SPRING[spriŋ]制动蹄拉紧弹簧BRAKE SHOE DEPRESSING[di’presiŋ]SPRING PIECE 制动蹄压下弹簧片LINED SHOE ASS'Y 制动领蹄带摩擦片总成ADJUSTER[ə’dʒʌstə] ASS'Y-LH/RH 左/右调整器总成ADJUSTING ROD ASSEMBLY 调整杆总成GUIDE BAR[bɑ:]导向杆SUPPORTING[sə'pɔ:tiŋ]BLOCK[blɔk] 支撑块SUPPORT II 支架ⅡPULLING PIECE 拔片STOP PLATE 限位板ROUND[raund]WIRE SNAP RINGS FOR SHAFT轴用钢丝挡圈ADJUSTING COVER-LH/RH左/右调整套STETCHING SCREW—LH/RH 左/右调整螺杆SHOE RETURN[ri'tə:n]SPRING—UPPER(A)制动蹄回位弹簧DUST[dʌst] COVER 分泵活塞防尘罩BLEED[bli:d] SCREW[skru:] 放气螺钉CAP BLEED SCREW 放气螺钉防尘罩PARKING['pɑ:kiŋ]CABLE ASS'Y — LH/RH 左/右手制动拉索总成SPRING 弹簧FIXED[fikst] MOUNT[maunt]II -LH/RH 左/右固定架ⅡSTEEL WIRE INTERLAYER PROTECTION PIPE[paip] 钢丝夹层保护管FASTENER[’fɑ:sənə]卡扣PIPE CLAMP[klæmp]III — LH/RH 左/右管夹ⅢPROTECTIVE SLEEVE III 保护套ⅢSTEEL WIRE ROPE[rəup]ASSEMBLY- LH/RH 左/右钢丝索总成(鼓式)RR。
刹车制动系统中英文对照外文翻译文献
中英文对照外文翻译THE BRAKESDon't expect miracles from tuning on the brakes-improvement, yes-but no miracles. There are two reasons for this. First, the racing disc brake system has been developed to a very high state indeed so that there just isn't a lot left in the line of practical improvement and, second, we just don't spend very much time under the brakes. On the average road racing circuit, something less than ten percent of the time required to complete a lap is spent braking. Therefore, a five percent improvement in braking performance (not brake efficiency) would net a theoretical improvement in lap time of one half of one percent or about one half second in a 90 second lap. In actuality, the improvement would be somewhat less because human and practical limitations always prevent us from realizing the full potential benefit from any performance improvement.The big payoff of a well sorted out braking system comes, not from any increase in braking power itself, but in the confidence, consistency and controlability that it provides to the driver. This is particularly true when it comes to corner entry-entry speed, placement, precision and repeatability are all directly dependent upon braking performance and consistency.I would be astonished to learn of a modern road racing car which was delivered with inadequate brakes. Badly arranged or badly set up I'm willing to believe, but inadequate-NO. This statement is valid only so long as we do not change tire size, power output and/or gross weight all out of proportion to the original design. It is definitely not true in those classes of production based touring car and G.T. Car racing where the sanctioning body, through sheer ignorance and/or bloody mindedness prohibits changes to the braking system.BRAKING POWER: WHERE DOES IT COME FROM?It takes an astonishing amount of energy to decelerate a moving vehicle-in fact it takes the same amount of energy to decelerate from one speed to another as it would to accelerate between the two speeds-except that we can decelerate faster because most of the inertial forces are working for us rather than against us. The actual energy required to decelerate our racer is given by the equation:Energy (Ib/ft) = .0335 x [(mph max)2 (mph min)2] x gross weight (lb).For a 1760 Ib car braking from 150 mph to 60 mph we are talking about .0335 x [( 150)2_(60)2] x 1760 = I, I 14,344 Ib/ft.No matter what terminology we use, this is a hell of a lot of energy absorbed in a very short period of time. Somebody once converted the braking energy put out by a GT 40 over the twelve hours of Sebring and came to the conclusion that the same amount of energy could supply the electrical requirements of a fair sized city for a goodly period of time. So where does the energy come from-what actually stops the car?Some comes from the rolling resistance of the tires-not much, but some. A notable amount, at least at high road speeds, comes from the vehicle's aerodynamic drag. A little bit comes from the friction generated between the moving parts of the entire mechanism. Most of it, however, must come from the vehicle's braking system which converts the kinetic energy of vehicle inertia into thermal energy which must then be dissipated into the airstream-because we have yet to figure out a practical method to collect it, store it, and use it for propulsive thrust. We really aren't very efficient. This chapter is devoted to investigating the braking system itself. We shall conveniently ignore the other factors which slow the car because what we really want to do with them is minimize them to increase the acceleration of the vehicle.WHAT WE CAN EXPECT FROM THE BRAKESWhat exactly are we looking for in braking system performance? First of all we need a braking system which is capable of developing enough braking force to exceed the deceleration capacity of the tires-at any speed that the vehicle can reach-time after time, for the duration of the race. All racing cars, and many modified production cars, have such a system-provided that it is properly installed, adjusted and maintained. The braking effortproduced must be directly and linearly proportional to the pedal pressure exerted by the driver. Further, the driver effort required must be reasonable, pedal pressures must be neither so great that Godzilla is required to stop the car nor so light that it will be easy to lock the tires. The pedal position must be correctly matched to the geometry of the driver's foot and ankle, must remain at a constant height and should be really firm and have minimum travel. The system must deliver optimum balance of braking force between the front and rear tires so that the driver can maintain steering control under very heavy braking and yet use all of the decelerative capacity of all four tires. Lastly, the system must offer complete reliability. If the driver is braking as deep and as hard as he should be, any brake system failure will inevitably result in the car leaving the circuit. What happens after that is up to the man upstairs. Brake failure in a racing car at the limit has to be experienced to be understood. This is why even the most heroic drivers are liable to give the brake pedal a reassuring tap before they arrive at their braking marker.We need a vehicle suspension system capable of dealing with the loads and forces generated by heavy braking without wheel hop, suspension bottoming, compliance, adverse camber effects, pull or darting. Most of all we need a driver sensitive and skillful enough to balance the car on the edge of the traction circle under braking and under the combination of braking and cornering. If we do not provide the driver with all of the system parameters listed above, he can not provide us with the skill and daring necessary to ride the edge of the traction circle.EV ALUATION AND DRIVER TECHNIQUEWe'll start out with what is probably the most difficult part of the whole braking scene-evaluation of what you have. Measuring the braking performance of your particular projectile against that of the competition is no easier than comparing any other aspect of vehicle performance-and for the same reasons-too many variables and too much ego involved. This is where instrumentation is invaluable. The biggest variable is, of course, the driver. The very last thing that a really good racing driver learns to do truly well is to use the brakes. Most people take too long to get them on hard, leave them hard on too long and brake too heavily too deep into the corner. Almost invariably the lap times generated by the King of The LateBrakers are slow. His adrenalin level is liable to be abnormally high and he has a tendency to fall off the road. There are several reasons for these characteristics. When you leave your braking too late you are very liable to arrive at the point on the race track where you really want to start your turn only to find that the car will not turn. It will not do so because, in your efforts to save your life, you have the binders on so hard that all of the front tires' available traction is being used in deceleration and there is none left to allow the generation of the side force necessary to turn the car-or, should you somehow succeed in initiating a turn, to keep it in a balanced cornering state. In addition, the front tires are liable to be very nearly on fire and dangerously close to the compound temperature limit. Thirdly, if you are still hard on the brakes when the turn is initiated, forward load transfer has unbalanced the car, the front suspension travel is about used up, the front tires are steeply cambered and, if the thing turns at all, things are going to happen a bit quickly.If you persist in braking too late, the spectators will "ooh" and "ahh" and be impressed no end and the announcer will mention your name frequently-noting that you are really trying out there. You will complain pitifully about corner entry understeer followed by an incredibly rapid transition to power on oversteer. The other drivers will pour by you-either while you are exploring the grey areas of the track in your frantic scrabble for traction or on the way out of the corner when they have both higher exit speed and a better bite. You will do a lot of exploring as your self induced understeer forces you into unintentional late corner entries. Your team manager will eventually catch on, wander out on the course and observe your antics. If the ensuing frank discussion of technique does not inspire you to mend your ways, he will seriously consider either another driver (if you don't own the car) or another job (if you do).So any time that you are going in noticeably deeper than the competent opposition (assuming similar cars) but your lap times are not reflecting the degree of heroism that you feel they should-and the car is entering corners badly-have a good think about the wisdom of your braking points. Slow in and fast out will beat fast in and slow out every time. Of course fast in and fast out beats either of the above-and that's what we are trying to achieve-but you won't come out fast if you go in with the car unbalanced and the front tires on fire. This is notto say that a super late brake application followed by a deliberate early corner entry and a bit of slithering around which uses up a portion of the track that might otherwise be useful to someone else is not a valid desperation maneuver. It is, and it will continue to be-but it isn't very often fast and it is even less often repeatedly fast.THE BRAKE PEDALHaving disposed of the system actuator, it is time to discuss hardware. We will begin with the brake pedal since it is the closest part to the driver. The brake pedal should be very strong-and so should its attachment to the chassis. This may sound very basic and a bit ridiculous-and so it should. Any fool should be able to figure out that if the brake pedal, or any of the associated bits, fractures, bends or tears out of its mountings, big trouble is about to happen. And yet it happens-not very frequently-but it does happen. It has even happened to very good operations. Don't let it happen to you. Take a long hard look at the pedal/master cylinder setup and, if anything even looks like being questionable, redesign and/or reinforce as seems necessary. Remember that the typical brake pedal has a mechanical advantage of at least 3: I and it may be as much as 8: I. The pedal arm must be plenty stout and it must be generously gusseted at the intersection of the bias bearing tube. If the pedal bracket is a chunk of 20 gauge aluminum pop riveted to the floor, it won't be good enough. If it doesn't eventually tear out, it will distort and it is difficult enough to modulate brake pressure without the pedal waving about. The pedal pivot support should be at least 18 gauge steel, it should be either boxed or flanged and it should tie into a corner of major structure. You are going to lean on the pedal very frequently and plenty hard. If the master cylinders are mounted to either sheet metal or to slightly stiffened sheet metal, you will end up with a soft or vague pedal. This particulardesign sin is nowhere near so rare as it should be-especially in those vehicles which do not employ a front bulkhead (a major Sin In Itself). I'll be damned if I know why this is ever allowed, but it is easily detected and remedied. Also look at the master cylinder push rods. It is very desirable that they should not bend. In normal lengths the stock Girting bits will do just fine. Trouble starts at about six inches. We can also get into trouble with really thin wall tubular extensions and with butt welds.PEDAL GEOMETRY AND ADJUSTMENTTake some time and adjust the fore and aft position of the brake (and clutch) pedal to suit the driver's geometry and preference. To do this right may not be as simple as it sounds. The easiest method is that practiced by Lolas, who screw the foot pad into the pedal shaft with a long bolt which is welded to the pad. This gives lots of adjustment without deranging the pedal geometry and offers the added advantage of allowing you to install the pad at an angle should your driver prefer.It is vital that the swing of the pedal be properly positioned on its arc. If the pedal is allowed to go over center as it is pushed, we will have an unfortunate situation where, the harder we push on the pedal, the less braking effort we get-and confusion is a certain result. Once the (minimal) free play has been taken up, we are not going to push the pedal very far, just hard, so that it is a relatively simple matter to adjust the actuating rod length and the position of the pedal pivot so that increased pressure results in increased, or at least linear mechanical advantage. Do so. All of this may involve new brackets, actuating rods, or even a new pedal. It really is important, so do it.We no longer row our way down through the gears to decelerate the car-pity, one more glorious sound gone away. The present racing disc brake system is plenty powerful enough to exceed the tire capacity without help from engine friction. Downshifting while braking merely upsets the balance of the car, involves unnecessary foot movements and makes it more difficult to precisely modulate braking effort. However, we still do downshift. So long as racing drivers must downshift, the traditional heel and toe exercise with the brake and the throttle is a necessity. Otherwise, we will snatch the rear wheels when the clutch engages and instantaneous oversteer will be achieved. As the downshift always occurs either during corner entry or immediately prior to it, oversteer-even transient oversteer-is not to be desired. Whilst downshifting, we are, by definition, braking and, more than likely, braking hard. It would be best if the driver could still modulate the brakes while jabbing at the accelerator. The common deficiency in this department is for the driver to unintentionally decrease brake pedal pressure while stabbing the throttle. Watch the braking area before a slow corner at any race-you can actually see the noses of the slow cars come up during downshifts. Next watch the aces andnote the difference. You will also notice that the nose of the ace's car comes up before the car is locked over into the corner. At any rate, if the driver is not going to upset the pedal pressure while downshifting, the relative positions of the brake and throttle pedals must be perfect-for the individual driver.There are two workable methods of "heel and toeing"-that I know of. The first involves rocking the right foot sideways and catching the throttle with the side of the foot. This is probably the more popular method, but it is difficult to control brake pressure while rocking the foot. The second way is to so arrange things that the heel of the right foot is carried further outboard than the ball and to jab the throttle by extending the heel. It is very much a case of personal preference and ankle geometry. In either case, the throttle pedal, or some part thereof had better be ready to foot when the time comes-we do not want to either hunt for it or stretch for it. Contrariwise, it must be impossible for the driver to inadvertently hit the throttle when he goes for the brakes or to get his foot tangled between the pedals-don't laugh. The necessary fiddling about and moving of things can be greatly facilitated by a bit of forethought. The pedal system most compatible with human geometry and lie down cars is to pivot the brake (and clutch) pedals on the floor and hang the accelerator from the ceiling. It helps a lot if the throttle setup incorporates a left and right hand threaded connector at the pedal end. It is unlikely that your first efforts at getting it right will be successful-drivers have trouble making up their minds and what feels right sitting on the jack stands may not be worth a damn on the race track-especially if the driver was wearing street shoes when you set it up. You may get to do a lot of this sort of thing for a while (sometimes I regret telling drivers that the pedals can be adjusted) so you may as well make it easy on yourself. This may well include making a larger access hole in the top of the tub for your hands. Remember that after each adjustment to the throttle pedal you get to reset the full throttle stop and that, if you change master cylinder sizes, you get to do it all over again.Playing with the shape of the throttle pedal and its arch often pays unexpected dividends.Most drivers insist on some sort of heel locating plate or brace running transversely across the cockpit floor. If the driver does not insist on one, you should-he needs It.The last pedal is the left footrest. There should be one. It provides a place for the driverto brace himself and does away with the worrisome possibility that he might unintentionally rest his left foot on the clutch to the detriment of the clutch plates. Its height should be the same as the clutch pedal and it should be located slightly behind the clutch so that the left foot can simply be slid sideways when required. It should be as wide as practical-making sure that the clutch can be depressed without getting the foot trapped between the two. There usually isn't a lot of excess room in the foot well so the clutch pedal may have to be made more narrow in order to create room for the dead pedal. The footrest should be well attached to the chassis because it will take a lot of pressure, and it is bad if it comes undone.BIG FEET IN SMALL COCKPITSAll English racing drivers must have size six feet! If your hero features size twelve, his fancy footwork in the average kit car is going to suffer some impairment due to interference between his toes and the bodywork, the tub, the anti-roll bar or the steering rack. This is one of the major reasons why the cockpit extends so far forward on the present Formula One Cars. Extensions and/or blisters are sometimes a necessity. Occasionally you will run into foot interference of a more serious nature-worst possible case being the steering rack-the anti-roll bar is a less serious case because it is easier to move. A situation of this nature calls for moving either the offending member or the driver-or maybe finding a driver with smaller feet. Minor interference can be cured by shoe surgery. If you move the driver you will also have to move the pedals. If you move the rack, you will have to re-do the geometry. It is easier not to buy a car with this type of built-in problem. Finding out about this sort of thing on your first test can ruin your whole day-so find out early-particularly if your driver, or his feet, are oversized.DISC BELLS OR TOP HATSWe have now arrived at a point where the pedals fit the driver and nothing is going to bend or fall off-so what can we do to help the actual retarding mechanism? Prepare to Win covered the plumbing, installation and maintenance ends of things and all of this has to be done-step by step. It did not, however, cover the now popular method of attaching the brake discs to the top hats or bells by six bolts in single shear. It did not cover it for the excellentreason that I had not dreamed that anyone would do such a thing. Wrong again! I had reckoned without Lola and March. Not only do these otherwise fine firms cheerfully commit this crime against nature, but they do not allow sufficient bolt hole edge distance or flange thickness to stabilize the bolts and they have been known to use less than optimum grades of aluminum for the bells. They also use fully threaded Allen bolts. Talk about looking for trouble! Chevron also use the same basic system, but their flange thickness is sufficient to get away with it.The layout is a lot less bad and critical on Formula Atlantic cars simply because both vehicle speed and vehicle mass are considerably less than, say Can Am Cars, and so the brake torque is less. Still I have seen the rear bells shear on an Atlantic car. Nothing good has ever been reported about this sort of thing. If you happen to have lots of money, the obvious solution is to get rid of the whole mess and install dog drive discs and bells. This is probably not practical as the dog drive top hats are very expensive to make. So let's explore the alternatives.Step one is to scrap the stock bolts. They are not the prime offenders, but getting rid of them is both cheap and easy. You will have to use either a twelve point or an internal wrenching NAS bolt. If you cannot obtain them, use an "Unbrako" Allen bolt with the correct grip length and cut off the unneeded thread. If you can get the NAS bolts, you may have to turn down the heads to make them fit. In some installations, it is just not possible to use a washer under the bolt head-even a turned down washer. In this case, the bolt hole must be countersunk to clear the radius under the head of the NAS bolts. Do not use stainless or titanium bolts in this application, and use all metal lock nuts.Unfortunately, the prime offender is the top hat itself. It may have several shortcomings. Normally there is both insufficient flange thickness to stabilize the bolt and insufficient edge distance to prevent the bolt from tearing out. The material may also be soft, allowing the bolt head to work into the aluminum which results in a loose assembly and eventual self destruction. The alloy may also be unstable under the heat involved which will cause disc runout. If you check the stupid things as frequently as you should, you will detect the symptoms before a disaster occurs-unless, of course, you are running on a really severe coursewhere you get airborne under the brakes-like Long Beach or Elkhart Lake. In this case the disaster may happen before you notice the symptoms and your driver will go through the experience of shearing the discs off the bells. He will not enjoy the experience, and you will not enjoy rebuilding the resultant wreck.For about 50% of the cost of a stock disc bell, any decent machine shop can make units from high quality forged alloy stock. Probably the best alloy to use is 2024-T4 with 7075T651 and 2017-T451 being acceptable. 6061 is not a good alloy for this application. If space permits, increase both the edge distance and the flange thickness. Save yourself some money by drilling twelve bolt holes instead of the required six and indexing the disc when the holes show elongation or cracking. In addition to lasting a lot longer, the bells will remain more true-especially if you set them up in a lathe and take a truing cut off them every so often. Tilton Engineering makes good top hats and a very clever steel plate to convert bolt on discs to dog drive.制动系统不要指望从调整刹车改进,奇迹,但没有奇迹。
- 1、下载文档前请自行甄别文档内容的完整性,平台不提供额外的编辑、内容补充、找答案等附加服务。
- 2、"仅部分预览"的文档,不可在线预览部分如存在完整性等问题,可反馈申请退款(可完整预览的文档不适用该条件!)。
- 3、如文档侵犯您的权益,请联系客服反馈,我们会尽快为您处理(人工客服工作时间:9:00-18:30)。
中英文对照外文翻译文献(文档含英文原文和中文翻译)外文:An Experimental Analysis of Brake Efficiency Using fourFluids in a Disc Brake SystemABSTRACTThe paper studies disc brake failure in Mini-buses using an experimental analysis to test the maximum braking force when different brake fluids such as clean, less dirty, dirty and soapy water solution were used in the braking system. The experimental results clearly showed that the soap solution appears to be the best fluid as far as low viscosity and stability of viscosity with increase in temperature are concerned. However, the soap solution is not compatible with other fluid which makes it difficult to be substitute as a clean brake fluid. The result of the Thepra Universal Brake Testing Equipment used for the braking efficiency test indicated that a pedal brake of 117 kN produce a brake force of 0.96 kN for clean brake fluid, 0.91 kN for the less dirty, 0.85 kN for dirty and 1.44 kN forsoap solution. The value of 1.44 kN which was achieved when the soap solution was used indicated a positive braking force and the indicating that soap solution could be used to produce a high pedal force within a very short time (about 10-30 min) and can therefore be used only in case of emergency. The brake efficiency test indicated that under hot conditions the braking efficiency is reduced and the presence of air in the system renders the braking ineffective because higher pedal force was needed to be able to produce a significant braking force which is noted for causing brake failure.Keywords: Brake fade, brake failure, disc brake, efficiency, pedal force INTRODUCTIONWhen a vehicle is accelerated, energy supplied by the engine causes the vehicle’s speed to increase. Part of this energy is instantly used up in overcoming frictional and tractive resistance but a large amount of it remains stored in the vehicle. According to Heinz (1999) this energy of motion is called the kinetic energy and the existence of kinetic energy is observed when a vehicle is moving and neutral gear is selected. The vehicle does not immediately come to rest; instead it travels for a considerable distance before it becomes stationary. In this case the stored energy is used to drive the vehicle against the resistances that oppose the vehicle’s motion. Relying on these r esistances to slow down a vehicle could cause many problems, so an additional resistance called a brake is needed to convert the kinetic energy to heat energy at a faster rate in order to reduce the speed of the vehicle Mcphee and Johnson (2007). This reduces the speed of the vehicle at a faster rate and brings the vehicle to rest within the shortest possibletime when the brakes are applied.From the point of view of Johnson et al. (2003) most automotive systems in use today utilize front disc brakes, but four-wheel disc systems are also common In disc brakes, the rotor rotates with the wheel and the pads move out to rub the rotor when the brakes are applied. Most disc brakes use floating calipers. The caliper slides in and out as the brakes are applied and released. The piston moves the inside pad out and pushes the outside pad into the rotor by sliding the caliper back toward the rotor.The use of disc brakes to reduce speed or bring the vehicle to rest when in motion cannot be over emphasized if the safety of the occupant is to be guaranteed Heinz (1999). To bring a vehicle to a stop, the disc brakes have to absorb all the energy given to thevehicle by the engine and that due to the momentum of the vehicle. This energy must then be dissipated. In most vehicle disc brakes, the energy is absorbed by friction, converted into heat and the heat dissipated to the surrounding air (Thoms, 1988). As the energy is absorbed, the vehicle is slowed down; in other words, its motion is retarded. The brakes must also pull up the vehicle smoothly and in a straight line to bring the vehicle to a stop position.It is therefore very important that the disc brakes of vehicles operate with the highest efficiency. This couldreduce the rate of accidents due to brake failure so that life and property could be preserved and also to ensure that occupants of these commercial vehicles go about their normal lives without any fear of being involved in an accident. Available crash data in Ghana suggests that about 1,900 persons are killed annually in road traffic crashes (Afukaar et al., 2008) and that more than 40% of the road traffic fatalities are occupants of cars, buses and trucks. Most often than not, some of the road accidents involving commercial vehicles, such as the mini-buses have been attributed to the failure of the disc brakes. The reason for testing the viscosity of these brake fluids, especially that of the soap solution was as a result of the practice of most Ghanaian drivers sometimes using the soapy solution as a substitute to the original brake fluid in the braking system and also using dirty brake fluid which has been used for bleeding purposes. The main objective of this study which is part of a larger work seeks to investigate and establish the reasons for the disc brake failure due to brake fluid also check the efficiency of the four different types of fluids used in the transmission of braking forces. The study looked at the maximum braking force when using clean, less dirty, dirty and soapy water solution in the braking system. It also looked at the braking force when the braking system is with or without servo unit and operating under cold or hot condition with air or without air in the braking systemDISC BRAKESThe disc brake consists of an exposed disc which is attached to the hub flange; the two friction pads arepressed on to this disc to give a braking action. Figure 1a, shows the disk brake system of a car and pad that is separated from wheel assembly to better shows the disk and the pad in sliding contact. As it can be seen, typical disk brake system and caliper assembly of a solid disk brake rotor is completely noticeable. Figure 1b shows schematic form of the disk and the pad in sliding contact assembly.(a) (b)Fig. 1: Disc brakeThe pads are moved by hydraulic pistons working in cylinders formed in a caliper that is secured to a fixed part of the axle. When the hydraulic pressure is applied to the two cylinders held in the fixed caliper, the pistons move; this action forces the friction pads into contact with the rotating cast iron disc. The sandwiching action of the pads on the disc gives a retarding action and heat generated from the energy of motion is conducted to the disc.Greater part of the disc is exposed to the air; therefore heat is easily radiated, with the result that the brake can be used continuously for long periods before serious fade occurs. Since the friction pads move at a right angle to the disc, any drop in the friction value does not affect the force applied to the pad. As a result this type of brake is not less sensitive to heat (Mudd, 1972). The disc brake was developed to minimize the fade problems. When fading occurs, the driver has to apply a much larger effort and in extreme cases it becomes impossible to bring the vehicle to rest. No assistance is obtained from the rotating disc to aid the driver in the application of a disc brake to achieve a given retardation. A disc brake requires a greater pedal pressure and toachieve this pressure required the hydraulic braking system using a good quality brake fluid in its operation.The fluid used in the hydraulic braking systems is a vegetable oil with certain additives. According to Nunney et al. (1998) a good brake fluid should have the following requirements, low viscosity, high boiling point, compatibility with rubber components, lubricating properties, resistance to chemical ageing and compatibility with other fluids. However, mostGhanaian drivers sometimes used other fluid such as dirty brake fluid, less dirty fluid and even soapy water sometimes as a substituted to the original brake fluid. This study among other things will also investigate which of these brake fluid, clean, dirty, less dirty and soapy water will have the best viscosity, high boiling point and less braking force.MATERIALS AND METHODSThe design used for this study was experiment which employed the used of viscometer and Thepra Universal Automotive Brake Testing machine to check the efficiency of the four fluids in the transmission of braking forces.Laboratory analysis: The viscosity tests on the four different liquids were carried out at the Kwame Nkrumah University of Science and Technology (KNUST) Thermodynamics laboratory. The liquids were clean brake fluid, less dirty brake fluid, dirty brake fluid and soap solution. It was necessary to find out how the viscosity of different qualities of brake fluid affected braking efficiency and to find out whether there was any correlation between these and the occurrence of brake failure.Viscosity test on the various fluids used: The viscosity test was carried out on a Redwood Viscometer in Fig. 2 on the four different kinds of fluids to determine their viscosities. The apparatus consists of a vertical cylinder containing the fluid under test which was allowed to flow through a calibrated orifice situated at the centre of the cylinder base. The orifice is closed by a ball valve when it is not being used.Fig. 2: Redwood viscometer used to determine the viscosity of the fluidsThe oil cylinder is surrounded by a water jacket which maintains the lubricant under test at a required temperature by means of a Bunsen burner flame applied to the heating tube. The thermometer for the water in the jacket is mounted in a paddle-type stirrer which can be rotated by hand, using the handle (Zammit, 1987).Procedure for testing various viscosities of the fluids: To test the viscosity of a fluid, the water jacket was filled with water with the orifice ball valve in position. Fluid was poured into the cylinder to the level of the pointer. A 50 mL measuring flask was placed centrally under the orifice. The water was stirred gently until the water and fluid thermometers were the same (room temperature, 30ºC). Thetemperature was recorded. The ball valve was then raised and a stopwatch used to record the time (in seconds) for a 50 mL of fluid to flow into the measuring flask. The test was repeated with the fluid temperatures increasing by 10ºC each time up to 90ºC. All the data for the four differentfluids were recorded as shown in Table 1Thepra universal stand automotive brake testing equipment:The ThepraUniversal Stand Automotive brake testing equipment is structured in such a way that the driven part, such as brake disc, was plugged on to the motor shaft. The brake anchor plate and the caliper are fastened to a flange via a linkage of bar which is connected to the flange. The brake force is measured and displayed on a digital indicator. The individualunits are plugged into the two span-frames which are fastened to both sides. All the brake components used in the testing equipment are original vehicle components. The pedalforce is measured at the actuating linkage of the brake master cylinder and displayed on a digital indicator (Technolab, 2009)RESULTS AND DISCUSSIONExperimental results of viscosity test: Table 1 present the results of viscosity test inan experiment for the four fluids, using the Redwood Viscometer.From the test results obtained using Redwood viscometer, Viscosity-Temperature graphs for the fluids were plotted. Figure 3 shows the plot of viscosity againsttemperature of the four fluids.Table 1: Viscosity testValues of the various viscosities werecalculated using the formula:V = hfρgD232hfvwhere,V : The Viscosityhf : The capillary heightρ : The density of the fluidg : Acceleration due to gravityD : The diameter of the orificev : The velocity (Bird et al., 1960) Fig. 3: Viscosity-temperature relationship of the fluidsFrom Fig. 3 the dirty fluid has the highest viscosity followed by the less dirty fluid, clean fluid and soap solution in that order. From the results shown in Fig. 2 and theviscosity test shown in Table 1, the soap solution appear to be the best fluid as far as lowviscosity and stability of viscosity with increase in temperature are concerned. However, it is less compatible with other fluids, difficult to mix easily with other brake fluids and has a low boiling point which will not make it suitable to be substitute as clean brake fluid (Nunney et al., 1998).The clean brake fluid is next as far as viscosity and stability of viscosity with increase in temperature are concerned. On the other hand, it satisfies all the other requirements of a good fluid for the braking system given in Table 1. According to Mudd (1972) and Nunney et al. (1998), a good brake fluid should have properties such as high boiling point, compatibility with rubber components, good lubrication properties, resistance to chemical ageing (long shelf life) and compatibility with other fluids. The less dirty fluid is very unstable as far as viscosity change with temperature increase is concerned. It is therefore not very reliable in a braking system since its behavior changes as the braking system heats up. The viscosity of the dirty fluid is stable with increase in temperature, however, it is very viscous (235-178 kgs/m3 in the temperature range 30 to 90ºC). It will therefore not be good and effective in brake force transmission. From these results and literature, it is obvious that the clean brake fluid is more suitable for the transmission of braking force as it’s possess all the good brake fluid qualities.Experimental results of the disc brake system:These sections present the results and discussion of the experiments using the four fluids in a Disc brake system under different conditions. Test results for hot and cold conditions of the Disc brake system using a servo system and without using a servo system were considered.Disc brake in cold condition with and without servo unit: The result in Table 2 clearly shows the pedal force and the brake force for clean, less dirty, dirty and soap solution when using disc brake in cold condition with servo unit with the Thepra Universal Brake Testing Equipment. A pedal brake of 117 kN produce a brake force of 0.96 kN for a clean brake fluid,Table 2: Results of disc brake in cold condition with servoTable 3: Results of disc brake in hot condition with servo0.91 kN for the less dirty, 0.85 kN for dirty and 1.44 kN for soap solution. Comparatively, a maximum brake force is achieved when the fluid is clean. When there is the presence of dirt,the brake force decreases and therefore more pedal force is needed to take up thewithout servoloss created by the dirt.Hence the greater the dirt, the greater thepedal force required.The value of 1.44kN which wasachieved when the soap solution wasused indicated a positive braking force compared with all the three fluids at the same pedal force. Subsequent pedal forces applied as shown in Table 2 gave a reduction in the brake force when soap solution was used. The implication was that soap solution could be used to produce a high pedal force within a very short time (about 10-30 min) and can therefore be used in case of emergency.From Table 2, it can be observed that for the same pedal force of 117 KN the soap solution transmitted the highest amount of brake force followed by the clean fluid, less dirty fluid and dirty fluid in that order. This implies that in cold condition using servo, the soap solution performs best followed by the clean, less dirty and dirty respectively.Disc brake in hot condition with servo unit: When the experiment was carried out using a disc brake under the hot conditions with the introduction of a servo, a pedal force of 120 kN gave a brake force of 0.95 kN for clean fluid, 0.90 kN for less dirty, 0.85 kN for a dirty fluid and 0.19 KN for soap solution. The result could be explain that, the clean brake fluid gave the highest brake force follow by less dirty, dirty and soap solution. It was observed that the soap solution perform poorly at this time recording a brake force of 0.19 KN as shown in Table 3.Disc brake in hot condition without servo: Figure 4 shows a plot of disc brake inhot condition without servo unit. It can be observed that, under hot conditions for the disc brake without servo, the trend is generally the same. The soap solution performed very badly compare with the other fluids, unlike its performance under cold conditions. This may be due to evaporation of the fluid making the fluid compressible; as if air was in the braking system. Generally, the clean fluid performed best in terms of transmission of brake force followed by the less dirty, dirty and soap solution in that order.Disc brake with air in system under cold condition: Braking force for this experiment was generally low as compared with the case when air was not trapped in the system as shown in Table 4. When the experiment was conducted with a pedal force of 165 kN, braking force ofTable 4: Results of disc brake with air in system under cold condition with servoFig. 5: Results of disc brake with air in system under hot condition with servo0.32 kN soap solution was obtained, for 0.37 KN for dirty, 0.28 KN for less dirty and 0.30 kN for clean fluid. This is in line with literature because according to Mudd (1972) the presence of air in the braking system makes the system ineffective since much of the drivers effort will be used to compress the air leaving very little for the brake application.Again, the soap solution did not give the least braking force because when the system is cold, soap solution is effective and its density is higher since there is nooccurrence of evaporation of the solution.Disc brake with air in system under hot condition: The Fig. 5 shows the plot of a graph indicating disc brake with air in the system under hot condition clearly shows that, when a pedal force of 152 kN was applied, a brake force of 1.11 kN was obtained for clean, 0.37 kN for less dirty, 0.28 kN for dirty and 0.26 kN for soap solution. It was observed that the maximum brake force was attained when the fluid was clean and on the introduction of dirty fluid, the brake force reduced drastically, though the pedal force was very high at 152 kN in the hot condition.Soap solution provides the least brake force because the air content in the system increases due to evaporation and hence the pedal force compresses air rather than transmitting power. As the system heats up, the air in the system expands thereby reducing the braking efficiency which results in brake failure.CONCLUSIONThe study was conducted using an experiment performed on a Thepra Brake Testing Equipment to check the efficiency of the four fluids in the transmission of braking forces. According tothe viscometer test shown that the soap solution appears to be the best fluid as far as low viscosity and stability of viscosity with increase in temperature is concerned. However, it is less compatible with other fluids, difficult to mix easily with other brake fluids and has a low boiling point which will not make it suitable to be substituted as a clean brake fluid.Again, when air is trapped in the braking system, which results in the brake fluid being compressible, higher pedal force was needed to be able to produce a significant braking force.Also, when brakes are operated under hot conditions its efficiency is reduced, a fault known as brake fade occurs as a result of the heating up of the brakes which creates less frictional resistance between rotating disc and the frictional pads.Finally, Soap solution when used at cold condition produces high braking force but becomes less effective after prolong use due to the presence of heat which evaporates the soap solution.REFERENCESAfukaar, F., K. Agyemang, W. Ackaah and I. Mosi, 2008. Road traffic crashes inGhana, statistics 2007. Consultancy Service Report for National Road SafetyCommission of Ghana.Bird, R., S. Wright and E.N. Light, 1960. Transport Phenomena, Gibrine Publishing Company,Heinz, H., 1999. Vehicle and Engine Technology. 2nd Edn.,Butterworth-Heinemann Publications, Nurumberg, pp: 235-291Johnson, D., B. Sperandei and R. Gilbert, 2003. Analysis of the flow through a vented automotive brake rotor. J. Fluids Eng., 125: 979-986.Mcphee, A.D. and D.A. Johnson, 2007. Experimental heat transfer and flow analysis of a vented brake rotor. Int. J. Thermal Sci., 47(4): 458-467.译文:一个使用四个液体系统分析盘式制动器的制动效率的实验摘要当车辆加速时能量由发动机提供使汽车的速度增加。