42CrMo合金钢轧辊的堆焊
轧辊堆焊技术

轧辊堆焊技术轧辊堆焊技术是一种常用的金属表面修复技术,通过在轧辊表面堆积耐磨合金,提高轧辊的耐磨性和使用寿命。
轧辊作为轧制设备中的重要部件,承受着巨大的压力和摩擦,容易出现磨损和裂纹,影响轧制质量和效率,因此轧辊堆焊技术的应用具有重要意义。
轧辊堆焊技术的原理是在轧辊表面堆焊一层耐磨合金,通常采用电弧堆焊或激光堆焊的方法。
堆焊材料的选择非常关键,一般选择硬度高、耐磨性好的合金材料,如钨碳合金、铬铁合金等。
堆焊时需要控制好堆焊层的厚度和均匀性,确保轧辊表面能够达到所需的硬度和耐磨性。
轧辊堆焊技术的优点在于能够有效延长轧辊的使用寿命,降低了设备的维护成本和停机时间,提高了生产效率。
同时,堆焊后的轧辊表面光滑平整,有利于提高产品表面质量,减少生产中的废品率。
另外,堆焊后的轧辊还能够承受更大的工作压力,适应更高强度的轧制工艺,提高了设备的稳定性和可靠性。
然而,轧辊堆焊技术也存在一些挑战和难点。
首先,堆焊工艺需要在高温高压的环境下进行,操作要求高,工艺控制难度大。
其次,堆焊层与轧辊基体之间易产生热应力和变形,需要通过合理的焊接工艺和后续热处理来解决。
此外,堆焊后的轧辊需要经过精细的磨削和抛光处理,确保表面光洁度和精度,增加了生产成本和工艺复杂度。
为了克服这些困难,现代轧辊堆焊技术不断创新和发展。
通过优化堆焊材料、改进堆焊工艺、引入先进的焊接设备和自动化控制系统,提高了堆焊层的质量和一致性。
同时,结合无损检测技术和数值模拟分析,实现对轧辊堆焊过程的实时监测和控制,确保轧辊表面质量和性能达到设计要求。
总的来说,轧辊堆焊技术在金属加工行业中具有重要的应用前景和发展空间。
随着科学技术的不断进步和产业需求的不断提高,轧辊堆焊技术将更加普及和完善,为轧制设备的性能提升和生产效率的提高做出更大贡献。
希望未来能够有更多的创新和突破,推动轧辊堆焊技术向更高水平迈进,为金属加工行业的发展注入新的活力和动力。
热轧辊堆焊工艺技术

热轧辊堆焊工艺技术热轧辊是用于热轧钢板生产的重要设备之一,其工作环境极为恶劣,长期受到高温高压等多重因素的影响,容易出现磨损、疲劳、断裂等问题,因此,对热轧辊进行修复和保养是非常关键的。
热轧辊的堆焊工艺技术是目前较为常用的修复方法之一。
热轧辊堆焊的目的是在辊面上堆焊一层高硬度的抗磨料,以提高辊面耐磨性能,延长辊筒的使用寿命。
热轧辊堆焊工艺主要包括预处理、堆焊和后处理三个步骤。
首先是预处理。
在进行堆焊前,需要对热轧辊进行彻底的清洗,将辊面上的油脂、氧化物等杂质清除干净,以保证焊接的质量。
其次,对于一些严重磨损或断裂的地方,需要通过铣削或切割等方法将其修整平整,以便于后续的焊接。
然后是堆焊。
选择合适的堆焊材料是非常重要的,通常使用高硬度、高耐磨的合金钢作为抗磨层的材料,可根据实际需要选择不同成分的材料。
堆焊过程中需要注意熔融热的控制,保证焊接层与基体的粘附性和牢固性。
同时,还需注意控制焊接过程中的温度,避免辊面过热或过冷造成的焊接缺陷。
最后是后处理。
堆焊完成后,需要对焊接层进行热处理,以提高焊接层的抗磨性和强度。
热处理的温度和时间需要根据堆焊材料的不同进行合理选择。
热处理结束后,还需对热轧辊进行精细修磨和保养,以消除焊接层表面的不平整和残留应力,确保热轧辊的使用质量和寿命。
需要注意的是,热轧辊堆焊工艺技术虽然能够有效提高热轧辊的使用寿命,但并不能解决所有问题。
有些严重的裂纹或大面积磨损的辊筒可能需要更换,因此,及时的维护和保养仍然是预防和延长热轧辊使用寿命的关键。
总之,热轧辊堆焊工艺技术是一项重要的修复方法,通过选择合适的堆焊材料和控制适当的焊接参数,可以有效提高热轧辊的使用寿命,减少因磨损和断裂引起的生产故障,保证热轧生产线的稳定运行。
同时,定期的维护和保养也是非常重要的,可以进一步延长热轧辊的寿命,提高生产效率。
轧辊堆焊埋弧堆焊修复技术

轧辊堆焊埋弧堆焊修复技术随着工业化的发展,轧辊在各种机械设备中扮演着非常重要的角色,它主要用于金属材料的压轧加工,是许多工业生产中不可或缺的部件。
由于轧辊在工作过程中所受到的强大压力和摩擦,导致轧辊表面很容易出现磨损和裂纹等问题,从而影响了轧辊的使用寿命和生产效率。
为了解决这一问题,目前已经出现了多种轧辊修复技术,其中堆焊修复技术和埋弧堆焊修复技术是比较常用且效果较好的方法之一。
轧辊堆焊修复技术是指在轧辊磨损或裂纹部位进行表面堆焊后再经过热处理进行修复,其优点是修复后的轧辊表面硬度、耐磨性和抗裂性能都得到了很好的提高,可以有效延长轧辊的使用寿命。
而埋弧堆焊修复技术则是通过在轧辊磨损或裂纹部位进行埋弧堆焊,然后经过热处理进行修复,也可以达到类似的效果。
对于轧辊堆焊和埋弧堆焊修复技术来说,专业的技术和设备是非常重要的。
需要选择适合的焊接材料和焊接工艺,确保修复后的轧辊表面能够满足工作要求。
需要使用专业的堆焊设备和工具,确保修复过程中的焊接质量和稳定性。
还需要进行合理的热处理工艺,以确保修复后的轧辊表面能够达到理想的硬度和耐磨性能。
除了技术和设备,对于轧辊堆焊和埋弧堆焊修复技术来说,经验丰富的操作人员也是非常重要的。
因为修复过程中需要考虑到轧辊的材料、结构、工作环境等多种因素,需要有一定的经验和技巧才能确保修复效果和修复质量。
在实际应用中,轧辊堆焊和埋弧堆焊修复技术已经得到了广泛的应用,并取得了很好的效果。
通过修复后的轧辊,不仅可以延长轧辊的使用寿命,减少了更换轧辊的频率,也提高了生产效率和产品质量。
这些修复技术也在一定程度上减少了对资源的浪费,降低了生产成本,具有显著的经济和社会效益。
轧辊堆焊和埋弧堆焊修复技术是解决轧辊磨损和裂纹等问题的有效方法,通过选择合适的材料、严格的焊接工艺和合理的热处理工艺,加上经验丰富的操作人员的配合,可以达到较好的修复效果。
相信随着科技的不断发展和完善,轧辊修复技术在未来会有更广泛的应用和更好的发展。
轧辊堆焊是什么
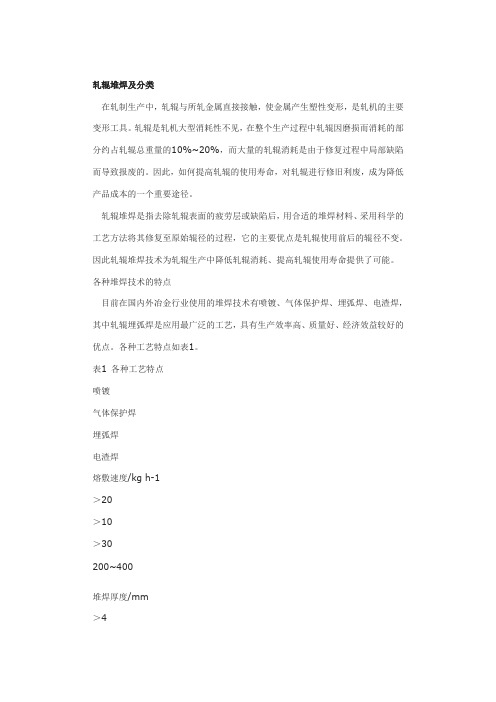
轧辊堆焊及分类在轧制生产中,轧辊与所轧金属直接接触,使金属产生塑性变形,是轧机的主要变形工具。
轧辊是轧机大型消耗性不见,在整个生产过程中轧辊因磨损而消耗的部分约占轧辊总重量的10%~20%,而大量的轧辊消耗是由于修复过程中局部缺陷而导致报废的。
因此,如何提高轧辊的使用寿命,对轧辊进行修旧利废,成为降低产品成本的一个重要途径。
轧辊堆焊是指去除轧辊表面的疲劳层或缺陷后,用合适的堆焊材料、采用科学的工艺方法将其修复至原始辊径的过程,它的主要优点是轧辊使用前后的辊径不变。
因此轧辊堆焊技术为轧辊生产中降低轧辊消耗、提高轧辊使用寿命提供了可能。
各种堆焊技术的特点目前在国内外冶金行业使用的堆焊技术有喷镀、气体保护焊、埋弧焊、电渣焊,其中轧辊埋弧焊是应用最广泛的工艺,具有生产效率高、质量好、经济效益较好的优点。
各种工艺特点如表1。
表1 各种工艺特点喷镀气体保护焊埋弧焊电渣焊熔敷速度/kg·h-1>20>10>30200~400堆焊厚度/mm>410~20>10015~100堆焊特点单层或多层多层多层多层第一层稀释率/%理论上为08~508~508~50结合形式机械冶金轧辊堆焊材料轧辊根据其使用要求的不同,对堆焊材料的选择也不同,按其合金类型可归纳为八类:1 低合金钢:此类合金价格便宜,堆焊金属组织以索氏体或屈氏体为主,冲击韧性好,抗裂性好,硬度HRC30~35,易于加工。
具有一定的耐磨性,但不能进一步提高轧辊使用寿命。
2 热作模具钢:该类材料具有良好的红硬性、高温耐磨性及较高的冲击韧性,焊后消除应力退火后,硬度一般在HRC45~50,使用寿命比原轧辊提高1~5倍。
3 马氏体钢:焊接性能好、耐磨、耐热性能也较好,但成本较贵。
4 弥散硬化钢:15Cr3Mo2MnV等,焊态硬度HRC35~38,易加工。
经560℃,保温15小时弥散硬化处理后,硬度可提高到HRC46~47。
5 奥氏体加工硬化钢:此类材料焊后硬度较低,但使用过程中由于冷加工硬化而大幅度提高。
轧辊表面耐磨堆焊工艺技术研究
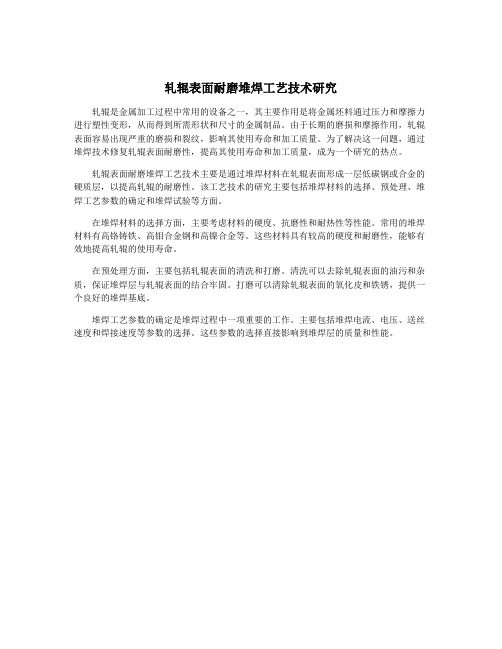
轧辊表面耐磨堆焊工艺技术研究
轧辊是金属加工过程中常用的设备之一,其主要作用是将金属坯料通过压力和摩擦力进行塑性变形,从而得到所需形状和尺寸的金属制品。
由于长期的磨损和摩擦作用,轧辊表面容易出现严重的磨损和裂纹,影响其使用寿命和加工质量。
为了解决这一问题,通过堆焊技术修复轧辊表面耐磨性,提高其使用寿命和加工质量,成为一个研究的热点。
轧辊表面耐磨堆焊工艺技术主要是通过堆焊材料在轧辊表面形成一层低碳钢或合金的硬质层,以提高轧辊的耐磨性。
该工艺技术的研究主要包括堆焊材料的选择、预处理、堆焊工艺参数的确定和堆焊试验等方面。
在堆焊材料的选择方面,主要考虑材料的硬度、抗磨性和耐热性等性能。
常用的堆焊材料有高铬铸铁、高钼合金钢和高镍合金等。
这些材料具有较高的硬度和耐磨性,能够有效地提高轧辊的使用寿命。
在预处理方面,主要包括轧辊表面的清洗和打磨。
清洗可以去除轧辊表面的油污和杂质,保证堆焊层与轧辊表面的结合牢固。
打磨可以清除轧辊表面的氧化皮和铁锈,提供一个良好的堆焊基底。
堆焊工艺参数的确定是堆焊过程中一项重要的工作。
主要包括堆焊电流、电压、送丝速度和焊接速度等参数的选择。
这些参数的选择直接影响到堆焊层的质量和性能。
轧辊堆焊埋弧堆焊修复技术
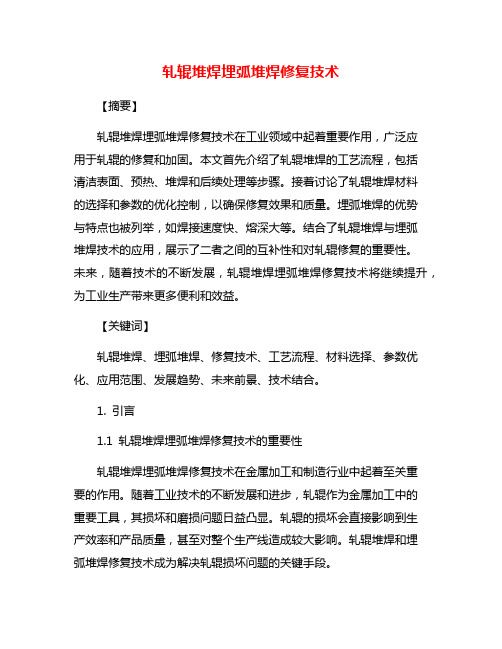
轧辊堆焊埋弧堆焊修复技术【摘要】轧辊堆焊埋弧堆焊修复技术在工业领域中起着重要作用,广泛应用于轧辊的修复和加固。
本文首先介绍了轧辊堆焊的工艺流程,包括清洁表面、预热、堆焊和后续处理等步骤。
接着讨论了轧辊堆焊材料的选择和参数的优化控制,以确保修复效果和质量。
埋弧堆焊的优势与特点也被列举,如焊接速度快、熔深大等。
结合了轧辊堆焊与埋弧堆焊技术的应用,展示了二者之间的互补性和对轧辊修复的重要性。
未来,随着技术的不断发展,轧辊堆焊埋弧堆焊修复技术将继续提升,为工业生产带来更多便利和效益。
【关键词】轧辊堆焊、埋弧堆焊、修复技术、工艺流程、材料选择、参数优化、应用范围、发展趋势、未来前景、技术结合。
1. 引言1.1 轧辊堆焊埋弧堆焊修复技术的重要性轧辊堆焊埋弧堆焊修复技术在金属加工和制造行业中起着至关重要的作用。
随着工业技术的不断发展和进步,轧辊作为金属加工中的重要工具,其损坏和磨损问题日益凸显。
轧辊的损坏会直接影响到生产效率和产品质量,甚至对整个生产线造成较大影响。
轧辊堆焊和埋弧堆焊修复技术成为解决轧辊损坏问题的关键手段。
轧辊堆焊埋弧堆焊修复技术能够有效地修复轧辊表面的裂纹、磨损和变形等问题,延长轧辊的使用寿命,提高生产效率和产品质量。
通过采用合适的堆焊材料和优化的堆焊参数,可以实现轧辊表面的修复和涂覆,使轧辊重新获得理想的工作表面,减少能源消耗和生产成本,提高轧辊的耐磨性和耐腐蚀性。
1.2 轧辊堆焊埋弧堆焊修复技术的应用范围1. 钢铁行业:轧辊是钢铁行业中不可或缺的重要设备,其表面易受磨损和腐蚀的影响。
而轧辊堆焊埋弧堆焊修复技术可以有效地修复和加固轧辊的表面,延长其使用寿命,提高生产效率。
2. 能源行业:在煤矿、电力等领域,轧辊在煤矿输送和发电过程中起着关键作用。
经常受到磨损和冲击的影响,需要进行修复和强化。
轧辊堆焊埋弧堆焊技术可以为其提供良好的修复修理方案。
3. 冶金行业:冶金行业中的轧辊在轧制过程中承受着巨大的压力和摩擦,容易受到磨损和变形。
连铸辊的埋弧自动焊堆焊修复工艺

连铸辊的埋弧自动焊堆焊修复工艺本文分析了连铸辊损坏的原因,阐述了采用埋弧自动堆焊工艺方法使用药芯焊丝堆焊连铸辊的工艺措施,修复后的连铸辊能够满足现场工况条件的使用要求,达到了新连铸辊的质量和使用寿命,资源得到了有效的再生利用,从而降低了生产成本,具有很好的经济效益和社会效益。
我公司修复了一批连铸辊,其直径为φ160~340mm不等,辊身长度L= 373~626mm 不等,母材材质为42CrMo,堆焊后辊子表面硬度为HRc43~47,其结构见图1。
连铸辊是连铸设备的关键备件之一,在热疲劳、氧化、腐蚀、磨损的工况条件下服役,经过使用一段时间后,会出现表面龟裂、裂纹、磨损、弯曲、剥离掉肉、氧化与腐蚀鳞皱等缺陷,而这些缺陷直接影响到板坯质量而不能使用需要修复,因些有必要分析连铸辊使用过程中的损坏原因,并制订适宜的连铸辊的修复工艺。
1 连铸辊产生损坏的原因分析连铸辊在生产过程中产生损坏的原因主要有以下四个方面:1)连铸辊在与高温铸坯接触的同时,受到高压冷却水的快速冷却,承受着反复高温急冷、急热,这样的冷热循环造成严重的冷热疲劳作用;同时连铸辊还受到板坯鼓肚力和静压力的交变机械应力作用;当连铸过程中出现滞坯和漏钢时,连铸辊还受到非平衡热和非平衡应力的作用;这些因素的共同作用下,连铸辊辊面出现不同程度的网状热裂纹和弯曲变形。
2)辊面与高温铸坯接触,受到高温氧化、冷却水和连铸生产用的保护渣中的氟离子的腐蚀作用,引起连铸辊辊面氧化、腐蚀鳞皱脱落,使辊子外径减薄, 导致辊面磨损,甚至导致辊子报废。
3)原材料质量的好坏是造成连铸辊损坏的原因之一,原材料中非金属夹杂物含量较多,锻造不当,保留了铸态形貌、枝晶间的低熔点夹杂物、化学成分偏析铸态缺陷,调质处理温度过高或保温时间较长,形成魏氏组织,降低低了连铸辊的力学性能。
4)堆焊材料的质量直接影响着连铸辊的工作质量,连铸辊若采用以碳作为固溶强化元素来提高堆焊层的硬度,由于碳在高温下(400~900℃)极易与Cr形成Cr23C6金属间化合物,造成堆焊层尤其是搭接过渡区出现贫铬现象,而连铸辊长期处在高温潮湿的环境下工作, 易造成堆焊层晶间贫铬开裂损坏。
轧辊堆焊埋弧堆焊修复技术
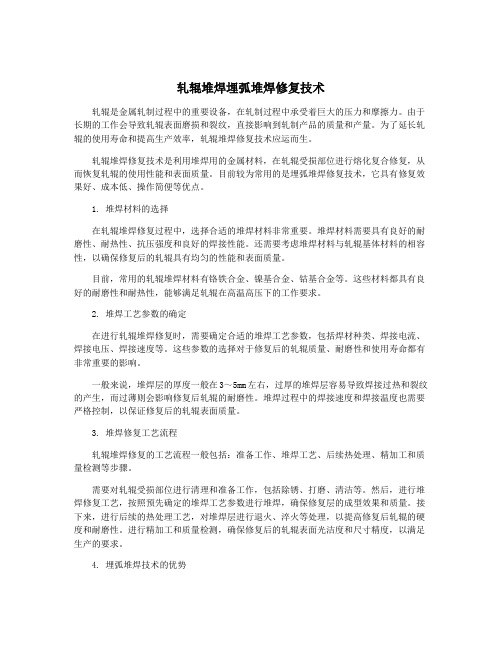
轧辊堆焊埋弧堆焊修复技术轧辊是金属轧制过程中的重要设备,在轧制过程中承受着巨大的压力和摩擦力。
由于长期的工作会导致轧辊表面磨损和裂纹,直接影响到轧制产品的质量和产量。
为了延长轧辊的使用寿命和提高生产效率,轧辊堆焊修复技术应运而生。
轧辊堆焊修复技术是利用堆焊用的金属材料,在轧辊受损部位进行熔化复合修复,从而恢复轧辊的使用性能和表面质量。
目前较为常用的是埋弧堆焊修复技术,它具有修复效果好、成本低、操作简便等优点。
1. 堆焊材料的选择在轧辊堆焊修复过程中,选择合适的堆焊材料非常重要。
堆焊材料需要具有良好的耐磨性、耐热性、抗压强度和良好的焊接性能。
还需要考虑堆焊材料与轧辊基体材料的相容性,以确保修复后的轧辊具有均匀的性能和表面质量。
目前,常用的轧辊堆焊材料有铬铁合金、镍基合金、钴基合金等。
这些材料都具有良好的耐磨性和耐热性,能够满足轧辊在高温高压下的工作要求。
2. 堆焊工艺参数的确定在进行轧辊堆焊修复时,需要确定合适的堆焊工艺参数,包括焊材种类、焊接电流、焊接电压、焊接速度等。
这些参数的选择对于修复后的轧辊质量、耐磨性和使用寿命都有非常重要的影响。
一般来说,堆焊层的厚度一般在3~5mm左右,过厚的堆焊层容易导致焊接过热和裂纹的产生,而过薄则会影响修复后轧辊的耐磨性。
堆焊过程中的焊接速度和焊接温度也需要严格控制,以保证修复后的轧辊表面质量。
3. 堆焊修复工艺流程轧辊堆焊修复的工艺流程一般包括:准备工作、堆焊工艺、后续热处理、精加工和质量检测等步骤。
需要对轧辊受损部位进行清理和准备工作,包括除锈、打磨、清洁等。
然后,进行堆焊修复工艺,按照预先确定的堆焊工艺参数进行堆焊,确保修复层的成型效果和质量。
接下来,进行后续的热处理工艺,对堆焊层进行退火、淬火等处理,以提高修复后轧辊的硬度和耐磨性。
进行精加工和质量检测,确保修复后的轧辊表面光洁度和尺寸精度,以满足生产的要求。
4. 埋弧堆焊技术的优势埋弧堆焊技术是目前轧辊堆焊修复中比较常用的一种技术,它具有以下几个优势:(1)成本低:埋弧堆焊技术所需的设备和材料成本相对较低,能够有效降低修复成本。
- 1、下载文档前请自行甄别文档内容的完整性,平台不提供额外的编辑、内容补充、找答案等附加服务。
- 2、"仅部分预览"的文档,不可在线预览部分如存在完整性等问题,可反馈申请退款(可完整预览的文档不适用该条件!)。
- 3、如文档侵犯您的权益,请联系客服反馈,我们会尽快为您处理(人工客服工作时间:9:00-18:30)。
二冷辊的堆焊修复工艺
摘要:通过对转炉二冷辊的焊接性分析,提出了对磨损的二冷辊表面进行合金堆焊修复工艺,使修复辊表面具有更耐磨、耐高温、耐疲劳性能。
关键词:二冷辊堆焊合金工艺刖言
转炉二冷辊是板坯连铸机的夹送辊,母材质是42CrMo合金钢,一组辊由三节组成,直径在?100〜?300之间,表面堆焊合金层后要求在过红钢和受水冷的工况条件下具有较强的抗热、耐磨和抗裂性能,辊面硬度要求为HRC42〜45。
图(1)为一节水平段?250自由辊。
图(1) ?285自由辊
1、焊接性分析
1.1二冷辊母材及化学成份。
二冷辊母材为42CrMo,为中碳合金钢,其化学成份见下表
1.2合金钢42CrMo的综合碳当量为0.76% ,碳当量较高,淬硬倾向较强,属于较难焊材料,其成分中的Mn、Mo等元素增加了白点的敏感性,容易产生裂纹。
1.3二冷辊母材属于低合金结构钢,焊接时容易产生延迟性冷裂纹,堆焊修复是在其表面堆焊5〜6mm的高强度耐磨材料,焊接过程中由于
工件局部受热不均匀,如果冷却速度过快,焊缝会产生巨大的内应
力而产生冷裂纹。
1.4合金42CrMo属中碳材料,当P、S含量也较高时容易形成热裂
纹。
为了防止热裂纹的产生,在选用焊丝时,C、P、S含量要低点,
Mn含量高点以加强脱S。
2、焊接材料的选择
2.1焊丝的选择
对于二冷辊的特性要求,选用耐磨耐热性好的Cr-Mo-Ni马氏体不
锈钢堆焊材料,由于母材的含碳量或合金含量相对较高,为确保母材和堆焊金属之间的良好冶金结合,在工作层材料堆焊前,先使用低碳抗压强度较高的焊丝材料进行过渡层堆焊。
我们选用H0Cr17药芯焊丝?2.4为过度层焊丝,H2Cr13药芯焊丝?2.4作为堆焊工作层焊丝。
2.2焊剂的选择
选用熔炼型焊剂HJ260,是低锰刘硅中氟焊剂,焊缝成形美观,
且成本较低,产生的烟尘少,不容易受潮的优点。
但用于二冷辊堆
焊,高温脱渣性比烧结型焊剂差。
通过与生产厂家合作,降低它的化学活性,并加强脱氧,生产出一种改进型HJ260,较好地改善了高温脱
渣性能, 同时控制好层间温度, 就能达到使用要求。
3、堆焊工艺
3.1 焊前准备
3.11车去轧辊表面疲劳层5〜6mm并保持辊面清洁。
3.12焊丝焊前300C烘焙1小时,焊剂250C下烘焙2小时以去除水分。
3.13 焊前预热
焊前对工件整体预热,升温速度为30〜50 C /h,预热至250〜
350 C,保温1〜2h。
预热目的是降低熔池冷却速度,减少淬硬倾向,防止马氏体形成过快而产生热裂纹。
3.2 堆焊参数
焊丝直径?2.4,
堆焊电流300〜350A
电压28〜32V
焊接线速度650〜750 mm /min
焊丝伸出长度25〜30 mm
堆焊层厚度2〜 2.5 m。
3.3 保温堆焊
在堆焊过程中,必须严格保持层间温度在200〜250C。
层间温
度的均匀将直接影响到堆焊轧辊表面的组织性能及硬度的均匀性。
层间温度太高会使焊道成形不良,脱渣性能差,层间温度太低焊道
熔透性差,堆焊层易产生裂纹。
3.4焊后热处理
焊后立即进行回火热处理,温度曲线如图所示。
回火热处理的目
的是消除焊接内应力,同时使堆焊层弥散强化,提高轧辊的耐高温
4. 成品的检验
4.1对精加工后的轧辊堆焊表面进行DT (渗透剂检验),未发现夹
渣、气孔、裂纹等焊接缺陷。
4.2对轧辊堆焊部位高温急冷试验后进行VT (超声波探伤),未
发现裂纹和其它缺陷。
4.3沿轧辊轴线方向各取若干点,进行硬度测定,所有硬度值均达到
HRC4各48的要求。
5. 结语
5.1工艺过程的重点在于焊接和温度控制,才能达到预期的硬度,耐磨性、抗疲劳性能,为此我们积累了很好的经验。
5.2经使用证明,该工艺修复后的二冷辊完全达到工况使用要求。