超硬磨料及其磨具的选择与应用
超硬磨料磨具 浓度 国标

超硬磨料磨具浓度国标摘要:1.超硬磨料磨具的概述2.浓度的定义及其在超硬磨料磨具中的重要性3.我国国家标准对超硬磨料磨具浓度的规定4.超硬磨料磨具浓度的合理选择与应用5.超硬磨料磨具浓度的检测方法正文:一、超硬磨料磨具的概述超硬磨料磨具是一种以超硬磨料为磨料,用于磨削硬质合金、陶瓷、硬质钢材等高硬度材料的磨具。
超硬磨料磨具具有高硬度、高耐磨性、高热稳定性等特点,广泛应用于各种高硬度材料的加工领域。
二、浓度的定义及其在超硬磨料磨具中的重要性浓度是指磨料在磨具中的分布密度,通常用百分比表示。
浓度是衡量磨具性能的重要参数,对磨具的磨削效率、耐用度等有着重要影响。
在超硬磨料磨具中,浓度的选择要根据被磨材料的硬度、磨削条件等因素综合考虑。
三、我国国家标准对超硬磨料磨具浓度的规定我国国家标准对超硬磨料磨具的浓度有严格的规定。
根据GB/T 23331-2009《超硬磨料磨具》的规定,超硬磨料磨具的浓度分为三个等级:高浓度、中浓度和低浓度。
不同浓度的磨具适用于不同的磨削场合。
四、超硬磨料磨具浓度的合理选择与应用在实际应用中,超硬磨料磨具浓度的选择要根据被磨材料的硬度、磨削效率、耐用度等因素综合考虑。
一般来说,浓度越高,磨削效率越高,但耐磨性会降低;浓度越低,耐磨性越好,但磨削效率会降低。
因此,要根据实际需求选择合适的浓度。
五、超硬磨料磨具浓度的检测方法超硬磨料磨具浓度的检测方法有多种,如重量法、容量法、X 射线荧光光谱法等。
这些方法各有优缺点,要根据实际情况选择合适的检测方法。
在生产和使用过程中,定期检测超硬磨料磨具的浓度,可以保证磨具的性能和使用寿命。
总之,超硬磨料磨具浓度是影响其性能的重要因素,要根据实际需求选择合适的浓度,并定期检测以保证磨具的使用效果。
超硬材料的研究和应用
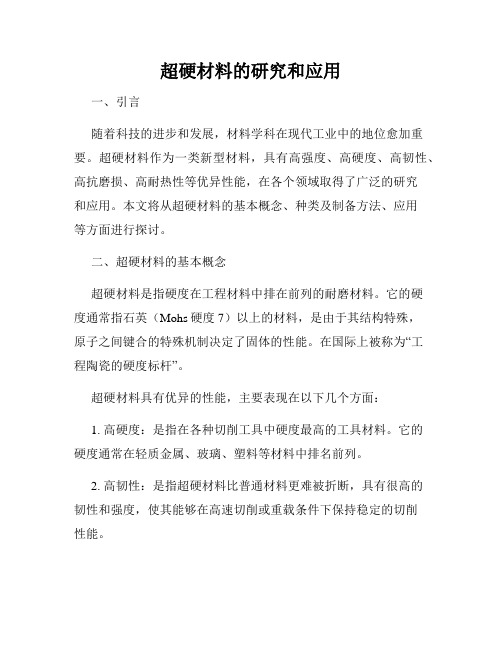
超硬材料的研究和应用一、引言随着科技的进步和发展,材料学科在现代工业中的地位愈加重要。
超硬材料作为一类新型材料,具有高强度、高硬度、高韧性、高抗磨损、高耐热性等优异性能,在各个领域取得了广泛的研究和应用。
本文将从超硬材料的基本概念、种类及制备方法、应用等方面进行探讨。
二、超硬材料的基本概念超硬材料是指硬度在工程材料中排在前列的耐磨材料。
它的硬度通常指石英(Mohs硬度7)以上的材料,是由于其结构特殊,原子之间键合的特殊机制决定了固体的性能。
在国际上被称为“工程陶瓷的硬度标杆”。
超硬材料具有优异的性能,主要表现在以下几个方面:1. 高硬度:是指在各种切削工具中硬度最高的工具材料。
它的硬度通常在轻质金属、玻璃、塑料等材料中排名前列。
2. 高韧性:是指超硬材料比普通材料更难被折断,具有很高的韧性和强度,使其能够在高速切削或重载条件下保持稳定的切削性能。
3. 高抗磨损性:超硬材料不易磨损,具有长寿命和更好的耐久性等特点,可用于高耐磨性材料制备和加工等领域。
4. 高耐腐蚀性:超硬材料可以耐受强酸、强碱、高温及腐蚀性物质,具有高耐腐蚀性和不受化学反应影响的特点。
三、超硬材料的种类及制备方法一种超硬材料是金刚石(Diamond),它是所有材料中硬度最高的,因其在切削、研磨过程中不易磨损,因此常被用于石油探测、光学加工、切割和电子磊晶等领域。
其它超硬材料包括碳化硅、氮化硼、碳化硼、金刚石纳米线等,它们的硬度都很高,应用范围广泛。
超硬材料的制备方法主要分为以下几种:1. 高压高温法:在高温和高压(大约100千巴、1300℃)条件下,使用碳酸盐热合成金刚石材料。
2. 化学气相沉积法:通过在高温下,将含有金刚石原子的气体分解成金刚石薄膜,并在引入气体时控制温度、压力和流量,实现材料的稳定性。
3. 化学气相沉积-热解法:将金属附着在气体表面的薄膜上,施加微波、高频等电磁场,使其分解并在表面上热解成金刚石材料。
四、超硬材料的应用由于超硬材料具有优异的性能,已经广泛应用到各个领域,包括:1. 切削加工:超硬材料具有高强度、高硬度、高韧性等多种优秀性能,因此常被用作切削材料。
超硬材料的性能与应用

超硬材料的性能与应用摘要:本文在超硬材料的基础上讨论了其良好性能及在工业上的应用,同时提出超硬材料在其领域内所应该开发的新应用。
重点分析了超硬材料在应用过程中所表现出其他材料所不能替代的性能。
本文通过查阅相关文献阐述了超硬材料综述了超硬料的结构及其性能特点,为今后超硬材料在工业上的进一步发展有提供前景。
关键字:超硬材料、金刚石、立方碳化硼、性能、应用等一、超硬材料的简介所谓的超硬材料则是指硬度可与金刚石相比拟的材料。
目前使用的超硬材料主要是立方氮化硼与金刚石,但是还是许多超硬材料正在研发中,如碳化硼,富硼氧化物等。
金刚石包括天然金刚石和人造金刚石,天然金刚石是目前世界上最硬的工业材料,它具有硬度高、耐磨损、热稳定性能好等特性,而且抗压强度高、散热速率快、传声速率快、电流阻抗、防蚀能力、透光、低热胀率等物理性能,是工业材料中不可替代的材料;人造金刚石是加工业最硬的磨料,电子工业最有效的散热材料,半导体最好的晶片,通讯元器件最高频的滤波器,音响最传真的振动膜,机件最稳定的抗蚀层等等,已经被广泛应用于冶金、石油钻探、建筑工程、机械加工、仪器仪表、电子工业、航空航天以及现代尖端科学领域。
立方氮化硼CBN是硬度仅次于金刚石的材料,但是目前并未发现天然立方氮化硼的存在,工业和日常生活中使用的都是人造的。
它具有与金刚石的许多特性相比拟的特点,同时也具有更高的热稳定性和对铁族金属及其合金的化学惰性。
它作为工程材料,已经广泛应用于黑色金属及其合金材料加工工业。
同时,它又具有优异的热学、电学、光学和声学等性能,在一系列高科技领域得到应用,成为一种具有发展前景的功能材料。
二、超硬材料的性能A)结构组成:金刚石是碳原子按四面体成键方式互相连接,组成无限的三维骨架,是典型的原子晶体。
每个碳原子都以SP3杂化轨道与另外4个碳原子形成共价键,构成正四面体。
由于C-C键很强,所以所有的价电子都参与了共价键的形成,没有自由电子,所以钻石不仅硬度大,熔点极高,而且不导电。
超硬刀具材料的选用与使用(精)
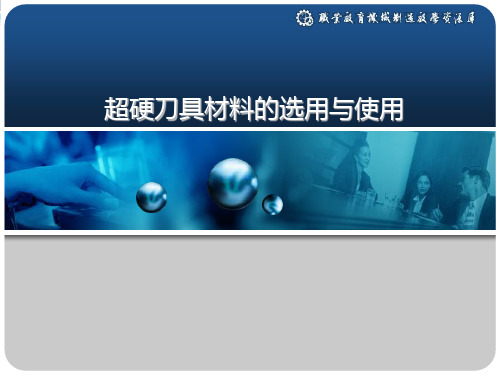
Produced by Мiss Хiè
涂层刀具材料
2、PVD高性能涂层 这类涂层适合于各种材料的刀具,主要用于立铣刀、钻头、阶 梯钻、油孔钻、铰刀、丝锥、可转位铣刀片、异形刀具、焊接 刀具等的涂层处理,适合半精加工、精加工等。 3、表面优化涂层 表面优化涂层适合高速精加工的技术要求。
Produced by Мiss Хiè
Produced by Мiss Хiè
超硬刀具材料的选用与使用
超硬刀具材料的选用与使用
2 1 3 2 2 2 2 5 3 3
陶瓷材料
涂层刀具材料
加工步骤 百分表 立方氮化硼
Produced by Мiss Хiè
涂层刀具材料
涂层刀具是在韧性较好的刀具上涂覆一层或多层耐磨性好 的TiN、TiCN、TiAlN和Al3O2等,涂层的厚度为2~18μm,能 有效地改善切削过程的摩擦和粘附作用,降低切削热的生成。 在机械制造方面主要使用以下 几种涂层材料: 1、MT-CVD涂层 主要用于硬质合金可转位车削 类刀片的涂层,涂层刀片适合 于高速、高温、大负荷、干式 切削条件下使用。
陶瓷材料
陶瓷刀具具有高硬度(HRA91~95)、高强度(抗 弯强度为750~1000MPa),耐磨性好,化学稳定性 好,抗粘结性能良好,摩擦系数低且价格低廉,具有 很高的高温硬度,1200°C时硬度达到HRA80等优点。
Produced by Мiss Хiè
立方氮化硼
立方氮化硼的硬度和耐磨性仅次于金刚石,有极好 的高温硬度,与陶瓷相比,其耐热性和化学稳定性稍差, 但冲击强度和抗破碎性能较好。它广泛适用于淬硬钢 (HRC≥50)、珠光体灰铸铁、冷硬铸铁和高温合金等的 切削加工,与硬质合金刀具相比,其切削速度可提高一 个数量级。
金刚石等超硬磨料知识

金刚石等超硬磨料知识1. 超硬磨料概述超硬磨料是指磨料颗粒硬度超过10000克法力的磨料,具有高硬度、高熔点、耐磨损等特点。
目前市场上比较常用的超硬磨料主要包括金刚石、CBN(立方氮化硼)等。
2. 金刚石磨料金刚石磨料,即人工合成金刚石微粉。
它具有高硬度、高热稳定性和化学稳定性,是目前公认的最优秀的超硬磨料之一。
2.1 金刚石磨料的制备方法金刚石磨料的制备方法主要包括高温高压法和高温热解法两种。
2.1.1 高温高压法高温高压法是指在高温高压下,使用金属催化剂和碳源催化石墨向金刚石转变而制备金刚石磨料的方法。
这种方法能够制备出质量优异、颗粒分布均匀、成本较低的金刚石磨料。
2.1.2 高温热解法高温热解法是指将经过粉碎和筛分的金刚砂或钻粉,置于高温下放置一定时间后热解成金刚石微粉的方法。
这种方法制备的金刚石微粉颗粒形态较好,但成本较高。
2.2 金刚石磨料的应用金刚石磨料主要应用于硬质合金、陶瓷、玻璃、石英等硬度较高的材料的加工中,特别是在轴承、气动元件等领域有广泛的应用。
3. CBN磨料CBN磨料(立方氮化硼)是一种以氮化硼为主要结构的超硬磨料,由于其与金刚石类似的物理特性和更优越的化学稳定性,被誉为“第二种金刚石”。
3.1 CBN磨料的制备方法CBN磨料的制备方法主要包括静压法和热解法两种。
3.1.1 静压法静压法是指将CBN微粉与金属粉末均匀混合,放入模具中,在1200℃左右温度下,通过机械、静压等方式,使之热成型成块状,再通过高温处理成为CBN磨料。
这种方法可以制备出大块状和块状的CBN磨料。
3.1.2 热解法热解法是指将硝酸钨和氮化硼等材料充分混合后,在气氛下热解成立方氮化硼的方法。
这种方法可以制备出细粒、均匀分布的CBN磨料。
3.2 CBN磨料的应用CBN磨料主要针对加工难度较高的材料进行加工,如高速钢、冷却硬化工具钢、航空发动机的叶片等。
由于CBN磨料对钢铁材料的切削性能较好,因此在制造航空、航天、汽车、工具等领域都有着广泛的应用。
超硬材料磨具的选择与使用

超硬材料磨具的选择与使用一、超硬磨料磨具特性的选择1.、磨料的选择:RVD金刚石的树脂结合剂砂轮制品具有产品锋利、磨削速度快,金刚石不易脱落等特点,广泛应用于玻璃、硬质合金、宝石、陶瓷、木材加工以及大理石花岗岩的抛光磨削等行业。
RVD 特点:晶型不规则、自锐性好、表面粗糙与树脂结合剂粘结牢固。
MBD金刚石晶型较不规则,透明度较好,热稳定性较好,抗冲击性较好,适用于金属结合剂制品,具有耐磨性好、杂质含量低、强度高、使用寿命长等特点,适用于金刚石锯切片、金刚石地质钻头、金刚石电镀工具等。
MBD8:产品晶型规则,含有较多立方八面体结构晶体,产品的热稳定性和冲击韧性较高,适用于磨削硬度较高的材料。
MBD6:晶型比较完整,含有一定比例的立方八面体结构晶体适中,适用于磨削陶瓷、石材、玻璃等材料。
MBD4:一种中等强度产品,晶型较完整,适用于磨削中等强度的材料。
MBD2:产品的冲击韧性和热稳定性相对较低,适用于制造使用要求不高的金属结合剂工具,也用于制造陶瓷结合剂工具。
SMD 特点:晶型完整,表面光滑,抗压强度高。
用于制造切割工具、地质钻头、修整工具等。
CBN砂轮的优点:1、对于黑色金属,特别是硬度高、韧性大、高温强度高、热传导率低的材料,具有良好磨削性能。
2、磨削力小,耐用度高。
3、同一砂轮通常可磨削不同材料,不同规格的工件,尤其是适用于在多品种中,小批量生产和数控,柔性制造系统,微机集成制造时使用。
4、加工表面质量高、无裂纹、不易烧伤。
5、容易保持尺寸精度。
6、综合经济效益比不同砂轮明显提高,磨损小、寿命长、效率高。
CBN 特点:CBN是硬度仅次于金刚石的超硬磨料,与人造金刚石相比,它具有热稳定性好,与铁族金属化学惰性大等特点,适宜加工高矾钢、高速钢与合金钢等金属材料。
金刚石微粉是将人造金刚石单晶经过精加工后制成的一种极细的新型超硬材料。
它广泛应用于机械﹑电子﹑航天﹑航空﹑光学仪器﹑玻璃﹑陶瓷﹑石油﹑地质﹑军工等领域和部门﹐是研磨拋光硬质合金﹑陶瓷﹑宝石﹑光学玻璃等高硬度材料的理想材料。
浅谈模具材料的选择与应用

浅谈模具材料的选择与应用模具是工业生产中不可或缺的工具,它为压力成型或热成型等加工过程中的原料提供所需的形状,因此模具的质量和性能直接关系到产品质量和效率。
模具材料的选择和应用是模具设计和制造过程中的核心问题,本文将从材料类型、性能指标和应用案例等方面进行浅谈。
一、模具材料的类型常见的模具材料主要有金属和非金属两类。
金属材料包括钢、铝、铜、铸铁等,而非金属材料则包括陶瓷、塑料、橡胶等。
(一)金属材料1. 钢:钢是最常用的模具材料之一。
其主要优点是强度高、可塑性好、韧性好、切削性能佳等,适用于制作要求高强度和长寿命的模具,如汽车零部件模具、注塑模具等。
2. 铝:铝是轻质金属,具有密度低、导热性好、强度高等特点。
由于铝的热膨胀系数低,因此适用于制作热变形模具,如铸造模具、低压铸造模具等。
3. 铜:铜是一种优良的导电和导热材料,具有良好的塑性和韧性。
因此适用于制作冷挤压模具、拉盘模具等。
1. 陶瓷:陶瓷具有优良的高温稳定性和抗化学腐蚀性,因此适用于制作热处理模具、玻璃熔制模具等。
二、模具材料的性能指标模具材料的性能指标包括机械性能、物理性能、化学性能等,不同的模具材料对这些指标的要求不尽相同。
(一)机械性能1. 强度:模具材料需要具有足够的强度才能承受来自生产过程中的高压力和高温度。
2. 韧性:模具材料需要具有足够的韧性才能防止开裂并保持稳定的形状。
3. 硬度:模具材料需要具有一定的硬度才能耐受重复的冲压、绞线等操作过程。
(二)物理性能1. 导热性:模具材料需要具有较好的导热性,以快速将温度分布均匀。
2. 膨胀系数:模具材料需要具有较低的膨胀系数以防止塑料、金属等材料在加工过程中产生变形、扭曲等不良现象。
(三)化学性能1. 耐磨性:模具材料需要具有很好的耐磨性,以满足长时间、高强度的使用要求。
2. 抗腐蚀性:模具材料需要具有很好的抗腐蚀性,以适应不同的生产环境和工艺要求。
1. P20钢:P20钢是最常用的注塑模具钢之一,主要用于制作中小型注塑模具,如家电、汽车零部件等。
如何选择塑胶模具材料及硬度

如何选择塑胶模具材料及硬度如何选择塑胶模具材料及硬度1.受热处理影响小为了提髙硬度和耐磨性,一般对模具要进行热处理,但这种处理应使其尺寸变化很小。
因此,最好采用能切削加工的预硬化钢。
2.高耐蚀性很多树脂和添加剂对型腔表面都有腐蚀作用,这种腐蚀使型腔表面金属溶蚀、剥落,表面状况变坏、塑件质量变差。
所以,最好使用耐蚀钢,或对型腔表面进行镀铬、钹镍处理。
3.易于加工双色塑胶模具零件多为金属材料制成,有的结构形状还很复杂,为了缩短生产周期、提高效率,要求模具材料易于加工成图纸所要求的形状和精度。
4.抛光性能好塑件通常要求具有良好的光泽和表面状态,因此要求型腔表面的粗糙度非常小,这样,对型腔表面必须进行表面加工,如抛光、研磨等。
所以,选用的钢材不应含有粗糙的杂质和气孔等。
5.耐磨性好塑件表面的光泽度和精度都和模具型腔表面的耐磨性有直接关系,特别是有些塑料中加人了玻纤、无机填料及某些颜料时,它们和塑料熔体一起在流道、模腔中髙速流动,对型腔表面的摩擦很大,若材料不耐磨,很快就会磨损,使塑件质量受到损伤。
6.良好的尺寸稳定性在注塑成型时,模具型腔的温度要达到300℃以上。
为此,最好选用经适当回火处理的工具钢(热处理钢)。
否则会引起材料微观结构的改变,从而造成双色塑胶模具尺寸的变化。
如何选择塑胶模具材料及硬度 [篇2]目前,塑料制品广泛用于日常生活的各个方面,包括注塑工艺的80%左右。
由于成型注塑模具、精密、插入、生产率、易于实现现代化和少等特点,广泛用于制造后,汽车、建筑、家用电器、食品、医药、日化等。
塑胶模具塑胶工业生产,可以获得良好的经济效益十分要害,因此,模具设计的基本要求,了解材料选择适当的`材料是必要的。
塑胶模具的工作条件和不同,一般冷死在150°c -200℃时,除按一定的工作压力、温度在外面。
根据塑胶模具使用条件、不同的处理方法对塑胶模具钢将全面概括如下基本性能要求。
塑胶模具硬度通常是在50-60hrc下面的模具热处理后,应足以保证其表面硬度,模具有足够的刚性。
- 1、下载文档前请自行甄别文档内容的完整性,平台不提供额外的编辑、内容补充、找答案等附加服务。
- 2、"仅部分预览"的文档,不可在线预览部分如存在完整性等问题,可反馈申请退款(可完整预览的文档不适用该条件!)。
- 3、如文档侵犯您的权益,请联系客服反馈,我们会尽快为您处理(人工客服工作时间:9:00-18:30)。
超硬磨料及其磨具的选择与应用
磨削过程就是磨具中的磨粒对工件的切削过程。
选择磨具就是要充分利用磨粒的切削能力去克服工件材料的物理力学性能产生的抗力。
由于磨具的品种规格繁多,而每一种磨具都不是万能的切削工具,只有一定的适用范围。
因此对每一种磨削工作,都必须适当选择磨具的特性参数,才能达到良好的磨削效果。
磨具特性主要包括磨粒、粒度、硬度、结合剂、组织、形状和尺寸。
这里从磨具特性方面叙述选择磨具的一般原则。
一.超硬磨料及其磨具
(一)超硬磨料磨具的加工特点
超硬磨料系指金刚石和立方氮化硼均属立方晶系。
与刚玉和碳化硅相比,具有硬度高、强度好、颗粒形状好、良好的导热性和低的热膨胀系数等特点。
磨削能力强及良好的磨削性能。
是非常优异的磨削材料。
由超硬磨料制成的磨具,其磨削性能突出,主要加工特点有:
1.极高的磨料硬度
2.耐磨损性能好
3.形状和尺寸保持性能好
4.能长时间保持磨粒微刃的锋锐性
5.磨削温度低
(二)超硬磨料磨具的特性
1.超硬磨料磨具结构
超硬磨料磨具的结构与普通
磨具不同,其结构形式由工作
层、过渡层和基体三部分组成。
如图一所示。
工作层即磨料层,
由金刚石或立方氮化硼磨料、结
合剂及填料组成。
是磨具
进行磨削加工的部分。
过渡层是
由结合剂和其它材料组成,以保图一超硬磨料金刚石、立方氮化硼磨具结构
证工作层的充分使用,不含超硬磨料,将工作层牢固把持在基体上。
近年来,有些厂家取消了过渡层,直接将过渡层把持在基体上。
基体是磨具的基本形体,起支承工作层的作用。
2.超硬磨料磨具的特性及标志
⑴磨料超硬磨料的品种有天然金刚、人造金刚石及立方氮化硼(CBN)。
人造金刚石又有多种牌号。
人造金刚石、立方氮化硼的品种、代号及适用范围列于表一表一人造金刚石和立方氮化硼品种、代号及适用范围(摘自GB/T6405-1994)
⑵粒度粒度系标志超硬磨料金刚石、立方氮化硼颗粒尺寸的大小。
粒度的标记按国家标准的规定,超硬磨料的各粒度颗粒尺寸范围及粒度组成按表二规定。
⑶结合剂结合剂起着把持超硬磨料和使磨具具有正确的几何形状的作用。
超硬磨料磨具的结合剂分四大类,即树脂结合剂(B)、金属(青铜)结合剂(M),陶瓷结合剂(V),电镀金属结合剂(M)
⑷浓度浓度是超硬磨料磨具所特有的概念。
它表示磨具工作层单位体积中超硬磨料的含量。
一般规定为每立方厘米体积中含4.4克拉(1克拉=0.2g,0.88g/cm3)的超硬磨料磨具的浓度为100%;每增加或减少1.1克拉磨料,则浓度增加或减少25%。
不同浓度超硬磨料磨具中磨料含量及代号列于表三。
表二金刚石、立方氮化硼粒度标记、各粒度颗粒尺寸范围及粒度组成(摘自GB/T6406-1996)
注:隔离粗线以上者用金属编织筛,其余用电成型筛筛分。
表三金刚石、立方氮化硼的浓度代号(摘自GB/T64091-1994)
3. 超硬磨料磨具形状尺寸
超硬磨料磨具形状及代号:砂轮类,油石磨头类,锯类。
参见GB/T6409.1-1994
超硬磨料磨具的形状标记系统包括二或三种代号,仅用于金刚石与立方氮化硼砂轮、油石、磨头和锯形状。
超硬磨料磨具的基本形状代号分为:1、2、3、4、6、9、11、12、14、15。
共10个代号。
参见GB/T6409.1-1994标准中表4的规定,基本形状可根据需要进行改型,其代号按GB/T6409.1-1994表7的规定。
超硬磨料磨具的磨料层在基体上位置代号按GB/T6409.1-1994中的表6规定。
磨料层断面形状代号按GB/T6409.1-1994标准的表5规定。
二.超硬磨料磨具特性的选择
(一)超硬磨料的选择
鉴于金刚石和立方氮化硼磨料性能上有差异,其使用范围也不同。
金刚石的硬度、强度、研磨能力、导热系数和热膨胀系数均优于立方氮化硼,因此适于加工硬而脆的材料,如硬质合金、陶瓷、玛瑙、光学玻璃、石材、混凝土、半导体材料等,但由于金刚石是碳的同素异体,在较高温度下易与钢中的铁族金属产生化学反应,形成碳化物,造成严重的化学磨损,影响磨具的磨削性能,且加工效果也不好,所以,金刚石不适宜用来加工铁族金属材料。
与金刚石比,立方氮化硼磨料的热稳定性,化学惰性均较优,不易和铁族金属及其它元素发生化学反应,因此,尽管其硬度等物理性能比金刚石稍差一些,但用它来加工硬而脆的金属材料,如磨削工具钢、磨具钢、不锈钢、耐热合金,高钒高速钢等黑色金属,具有独特的优点,是理想的磨料。
天然金刚石以NC为代号,人造金刚石分为RVD、MBD、SCD、SMD、DMD、M-SD六个牌号;立方氮化硼有CBN,M-CBN两个牌号,其相应地适应范围参见表3.8.3.2。
(二)超硬磨料的粒度选择
超硬磨料的粒度选择,一般是根据被加工工件的表面粗糙度和加工效率的要求而决定的。
金刚石磨具与立方氮化硼磨具选择原则基本相同,与普通磨具比较,如要达到相同的表面粗糙度要求,选用磨料粒度应细1~2个粒度号;同时,在满足粗糙度要求的前提下,还是应考虑能达到较高的加工效率,取得满意的加工效果,应尽量选取尽可能粗的粒度,磨料粒度与加工表面粗糙度的关系如表四
虑。
磨削加工各工序推荐选择的粒度号如下:
粗磨选用80#~100#;半精磨120#~180#;精磨细磨选用180#~W40;研磨抛光选用W40~W1。
(三)超硬磨料磨具结合剂的选择
金刚石磨具与立方氮化硼磨具常用的结合剂有树脂结合剂、陶瓷结合剂、金属结合剂和电镀金属结合剂四类。
金属结合剂有青铜结合剂、铸铁结合剂及铸铁短纤维结合剂。
按结合能力及耐磨性排序如下:
树脂 陶瓷 金属 电镀金属 结合能力及耐磨性 (四) 浓度的选择
浓度是超硬磨料磨具的重要特性之一,它对磨削效率和加工成本有很大的影响。
浓度低,磨削效率不高,满足不了生产的要求;浓度过高,很多磨粒过早脱落、造成浪费。
不同种类的结合剂对磨粒的结合力不同,因此对每一种结合剂都有它的最佳浓度范围。
树脂结合剂超硬磨具的浓度范围为50~75;陶瓷结合剂磨具的浓度为75~100;金属结合剂磨具的浓度为100~150。
结合剂对磨粒的结合强度越高,最佳浓度范围越高。
(五) 超硬磨料磨具形状和尺寸的选择
超硬磨料磨具形状的选择,主要根据磨床和工件加工表面形状对磨具的要求来决定。
如平行砂轮(1A1)主要用于外圆、平面、工具刃磨及砂轮机上的磨削;平行小砂轮(1A8)主要用于内圆磨削;单面凹砂轮(6A2)主要用于工具刃磨和平面磨削等;碗形砂轮(11A2)主要用于刀具刃磨和平面磨削。
超硬材料磨具的尺寸选择是根据磨床的规格、型号及加工工件形状大小来决定。
可参考磨床说明书上对磨具尺寸的要求予以选择
超硬磨料磨具即金刚石或立方氮化硼磨具的形状和尺寸按GB/T6409.2-1996选取。
三、超硬磨料磨具的使用 渐强
2、磨削深度的选择
一般地,磨料粒度越粗,选用的磨削深度越大,平面磨削方式的磨削深度大于外圆磨削;结合剂强度越高时,选择的磨削深度可大些。
3、工件速度的选择
一般来说,工件速度增高,磨具渐耗增大,加工表面粗糙度略有上升。
在一般磨削加工中,建议工件速度在10~20m/min范围选择,内圆磨削或细砂轮粒度精磨时,可适当提高工件速度。
对于深切缓进给磨削,工件速度十分缓慢,一般为每分钟几十至几百毫米。
4、轴向进给速度和轴向进给量
经验证明,超硬磨料磨具磨削时,随着轴向进给速度的增大,磨削效率提高,粗糙度值上升。
一般情况磨削下,内、外圆磨削的轴向进给速度建议取0.5~1m/min,平面磨取0.5~2mm/行程。
刃磨时工作台多为操作者手动控制,常在1~2m/min范围内选择。
5、使用超硬磨料磨具对磨削液的选择
超硬磨料磨具工作表面组织疏松,气孔很少,有的甚至没有气孔,在磨削过程中极易堵塞。
所以,要求对磨削液具有很好的浸润性和清洗性,能及时冲洗粘结在磨具表面的磨屑,保证磨粒的切削能力。
金刚石磨具在磨削硬质合金,钢结硬质合金时,采用的磨削液有轻质矿物油(如煤油、低号机油和汽油等)、苏打水(不适用树脂结合剂)及各种水溶性磨削液;磨削非金属材料时,常采用水作磨削液。
但立方氮化硼磨具在高温度下易于水发生化学反应。
所以,使用立方氮化棚磨削时,采用轻质矿物油(如煤油,清柴油)磨削液能获得良好的磨削效果。
当必须采用水溶液时,则应加入极压添加剂以减弱水解作用。
6、使用超硬磨料磨具时对机床的要求
1. 砂轮主轴精度须高于使用普通磨料磨具的机床。
一般要求轴向窜动量控制在0.005mm以内,径向振摆控制在0.01mm以内。
2.机床必须有足够的刚性,一般要比普通机床的高50%。
3.机床的密封性能必须良好,尤其是头架主轴和轴承部分,必须有十分可靠的密封。
4.机床的进给机构的精度要高,应保证准确均匀的送进,操作方便,每行程应有0.005mm 以下的进给系统。
参考文献:
1、李伯民,赵波.实用磨削技术.北京:机械出版社,1996
2、李伯民,赵波.现代磨削技术.北京:机械出版社,2003
3、陆剑中,孙家宁.金属切削原理与刀具.北京.机械出版社,1984。