塑胶射出成型问题的分析(B)
射出成形不良原因及对策

1.流痕
在成品表面或透視成品時,可以看到流動的痕跡。
例如:冰線、橘皮及結合線。
註:其它成品表面的缺失請參考:銀線、凹陷、噴痕及光澤。
2.縮水造成的空洞
空洞的地方產生在壁厚最大的地方,如果將成品切開,就
可以看到許多空洞地方。
3.毛邊
在合模面形成薄的塑膠薄面。
4. 受應力而白化(頂白)
頂出造成成品變形而造成成品表面出現白色痕跡。
5. 表層剝落
鱗片狀的塑膠從表面剝落。
6. 成品脫模不良
成品黏在模具上。
7. 結合線
兩股塑料流動的前緣結合的地方清晰可見,這個地方會發生機械性能
降低。
8. 產品不完全
成型品不飽模。
表面不平坦。
重量太輕。
註:留意肋、流動末端和不良排氣造成的氣泡。
9.冷料痕
產品內有未熔的塑膠粒,特別是在澆口附近。
10.銀線
銀線出現在從澆口出來的成品表面。
11.凹陷(縮水)
成品的表面在肋或厚度改變的地方不平。
12. 噴痕
成品上可以看到從澆口開始呈鋸齒狀塑料流動的痕跡。
13.光澤
表面光澤度不對。
14. 斑點
成品表面及透視成品時,可以看到斑點。
15. 表面燒焦
成品表面在塑料流道的末端燒焦。
16. 翹曲
成品彎曲或扭曲。
17. 料頭脫模不良
料頭脫模不良。
射出成型不良原因分析报告

注:如果必要的,清潔并拋光2.減少使用或不使用潤滑劑,不管是內部(在塑是0.02mm,而高流動性的材料為0.01mm(壓力及速度) 注:如果必要,使用較多/或較大的頂針擇的塑料和成型條件(溫度)之間的相容性,使射出時不會混合不均F. 模面上有潤滑劑 1.減少使用潤滑劑,不管是混合在塑料中或是噴在模面上的離型劑G. 塑料未完全塑化 1.檢查螺桿的長度/直徑比注:必要的話,更換射出單元或使用混料裝5.使用空氣頂出針使頂出容易注:必要時,使用較多且較大的頂針6.檢查模具1)調整拔模角度2)調整倒角3)調整圓弧G. 機臺運轉不穩定 1.檢查模具:1>檢查液壓油壓力2>檢查液壓油溫度3>檢查液壓油油量4>檢查液壓油泄漏情況5>檢查濾網是否清潔2.檢查馬達及頂針控制系統塑料或外部潤滑(離型劑)C. 排氣不良 1.在融點線位置增加排氣孔2.檢查澆口尺寸注:如有必要,加大或重新安排澆口(平衡)D. 熔膠內含有熔合特性不良的色母 1.以不含色母的塑料射出來的檢驗色母和所使用的塑料在此加工條件下的相容性3.增加熱澆道溫度設定注:以空射料檢頭實際溫度和之間的差異2冷料痕產品內有未熔的塑膠粒,特別是在澆口附近原因解決方法/檢查要點A. 熔膠未完全熔融 1.增加料管溫度2.增加噴嘴溫度3.增加背壓4.增加螺杆轉速5.如果冷卻時間比塑化時間長,降低螺杆轉速6.如果塑化時間(當塑化時間比冷卻時間長時,周期時間會加長)7.檢查螺杆的長度/直徑比注:如有必要,更換射出單元或使用混料裝置B. 原料被污染 1.檢查原料是否摻有不同流動特性的異物原料內潤滑劑不夠9-4縮水原因對策模內進膠不足射出壓力太低保壓不夠射出時間太短射出速度太慢射料嘴阻塞冷卻間時間不夠機器或料管過大螺杆或逆止環磨損溢口不平衡模溫不當料溫過高成品本身或其肋(RIB)及柱(BOSS)過厚增加劑量提高射出壓力提高或增長保壓增長射出時間加快射出速度拆除檢查修理延長冷卻時間更換機器或料管拆除檢查修理調整模具溢口大小或位置調整適當之溫度及具部相對溫度降低料溫檢討成品降低射出壓力減少劑量減少射出時間降低射出速度變更溢口大小或位置修模具除去倒角打光模具開模或頂出減慢或模具加進氣設備檢修模具降低料溫對策降低射出壓力降低射出劑量時間及速度重新調整其配合修改模具延長冷卻時間或降低冷卻溫度修改模角具增加角度修改模具加設抓銷降低原料溫度對策降低射出壓力降低射出時間/速度及劑量增加開模壓力檢查清理檢查清理檢修模具降低原料溫度﹐降低模具溫度對策降低射出壓力/時間/速度及劑量升高模溫檢修模具檢修模具檢修模具檢修模具開模或頂出慢速加進氣設備檢修模具對策增快射出速度提高射出壓力提高模具溫度少用脫模劑油盡量不用調整模具增開排氣孔或檢查原有排氣孔是否堵塞變更溢口位置提高原料溫度提高背壓加快螺杆轉速檢查原料對策調整適當射出速度調整適當射出壓力提高模具溫度加大溢口變更成品設計或溢口位置提高原料溫度提高背壓加快螺杆轉速檢查原料成品頂出時尚未冷卻降低模具溫度延長冷卻時間降低原料溫度原料溫度太低提高原料溫度提高模具溫度9-11 成品內有氣孔原因對策射出壓力太低提高射出壓力射出時間及劑量不足增加射出時間及劑量射出速度太快調慢射出速度被壓不夠提高被壓料管溫度不當降低射嘴及前段溫度﹐提高后段溫度成品斷面肋或柱過厚變更成品設計或溢口位置澆道溢口太小加大澆道及溢口模具溫度不平均調整模具溫度冷卻時間太長減少模內冷卻時間使用水浴冷卻水浴冷卻過急減短水浴時間或提高水浴溫度原料含有水分原料徹底烘干原料溫度過高致分解降低原料溫度近澆口部分之原料太松或太緊減少或增大溢口大小成品頂出時尚未冷卻降低模具溫度延長冷卻時間降低原料溫度原料溫度太低提高原料溫度提高模具溫度9-11 成品內有氣孔原因對策射出壓力太低提高射出壓力射出時間及劑量不足增加射出時間及劑量射出速度太快調慢射出速度被壓不夠提高被壓料管溫度不當降低射嘴及前段溫度﹐提高后段溫度成品斷面肋或柱過厚變更成品設計或溢口位置澆道溢口太小加大澆道及溢口模具溫度不平均調整模具溫度冷卻時間太長減少模內冷卻時間使用水浴冷卻水浴冷卻過急減短水浴時間或提高水浴溫度原料含有水分原料徹底烘干原料溫度過高致分解降低原料溫度馬上做射出成行加工.2. 塑料預先干燥,尤其已拆封的塑料B.模面上有結露現象 1. 提高模具溫度注:提高模具開起關閉的速度可以避免模面結露現象凹陷成品的表面在肋及/或厚度改變的地方不平.原因解決方法/檢查要點A. 射膠量不足 1. 增加射膠量且經常秤成品的重量 (檢查重量)B. 射出速度/壓力不對 1. 調整射出速度2.射出速度曲線3.調整射出壓力4.射出壓力曲線C. 保壓壓力太低 1. 提高保壓壓力2.增加保壓時間3.檢查澆口是否阻塞(污染)注:如果必要的話,加大或重新安排嘵口位置(平衡)D. 由于塑料溫度太高,造成溫度收縮 1. 降低料管溫度E. 成品的壁厚差距太大 1. 使用泡劑(收縮不平均)F. 模溫太高 1. 降低模具溫度A. 塑料射入毫阻力的模穴內 1.降低射出速度(檢查重量) 2.調整射出速度曲線 注:尤其是剛開始射出的階段 3.降低射出壓力 4.調整射壓力曲線注:尤其是剛開始射出的階段 5.調整料管溫度曲線 6.檢查澆口的尺寸注:必要的話,加大或澆口尺寸7.檢查澆口是否阻塞(污染)且如果必 要的話,調整澆口的位置注:重新安排澆口的位置,使熔膠的流動提早分開8.在模穴內安置阻擋物 注:阻擋物可以使塑料通過澆口時,在模穴內形成阻力光 澤表面不夠光澤原因 解決方法/檢查要點A. 模具溫度太低或者不規劃 1.提高模具溫度(檢查重量)2.檢查模具冷卻均勻性及有無阻塞 B. 模具表面加工不正確 1.檢查模具表面是否受污染 注:必要的話,清潔拋光 C. 塑料溫度太低 1.調整料管溫度 2.提高噴嘴溫度3.提高熱澆道溫度設定 D. 射出速度不正確 1.調整射出速度A. 塑料受污染 1.檢查塑料有無受污染注:避免運送途中及混料系統中受污染 B. 不正確的色母1.用本色料射出,以便檢查在此加工條件時 母料與色母的相容性 C. 在料管內受污染1.檢查及清潔料管注:用料短清潔劑清洗料管,必要的話將料管分解2.用本色射出來檢查料管是否清潔 D. 流道及澆口系統受污染 1.檢查并清潔流道及澆口系統 2.檢查熱澆道系統的死角E. 在混料系統中受污染1.檢查混料系統中可能受污染的地方表面燒焦成品表面在塑料流道的未端燒焦原因 解決方法/檢查要點 A. 空氣在模具中無法排出1.降低射出速度2.調整射出速度曲線3.降低射出壓力4.調整射出壓力曲線注:尤其在射出的終了降壓及速度5.檢查成品未填飽的地方,是否排氣不良 注:必要的話,加入排氣口或排氣梢6.檢查模具排氣口是否污染7.檢查澆口是否阻塞(污染)8.檢查澆口尺寸注:必要的話,加大或重新安排澆口(平衡)成品彎曲或扭曲原因解決方法/檢查要點A. 模具冷卻系統操作不正常1.檢查模具冷卻的均勻度及冷卻道有無阻塞2.分別調整公模及母模的冷卻B.由于塑膠定向造成縱向與橫向 1.提高料管溫度的收縮率不同 2.調整射出速度3.調整射出壓力4.檢查澆口位置注:必要的話,增加或重新安排流道位置 C. 由于色母造成成品扭曲 1.以下不含色母的色料射出來檢查色母與塑料和成型條件溫度之間的相容性,使射出時不會有下料不均的情況D. 不正確的成型后收縮 1.調整冷卻時間注:如果無法排除這個問題的話,則使用冷卻定型劑料頭脫模不良Array料頭脫模不良原因解決方法/檢查要點A. 由于收縮不良使料頭無法脫離 1.降低保壓壓力2.降低背壓(如果沒以使用對閉式噴嘴的話)B. 料頭拔模不良 1.檢查料頭的拔模角度及受損情況2.檢查料頭與噴嘴銜接處的尺寸與R角.3.檢查是否料頭的拉拔倒勾不足注:必要的話,加大料拉拔倒勾C.因為料頭尚未完全凝固而折斷 1.降低料管溫度2.調整噴嘴溫度3.使用較小的料頭。
射出成型不良原因简介(doc 14页)
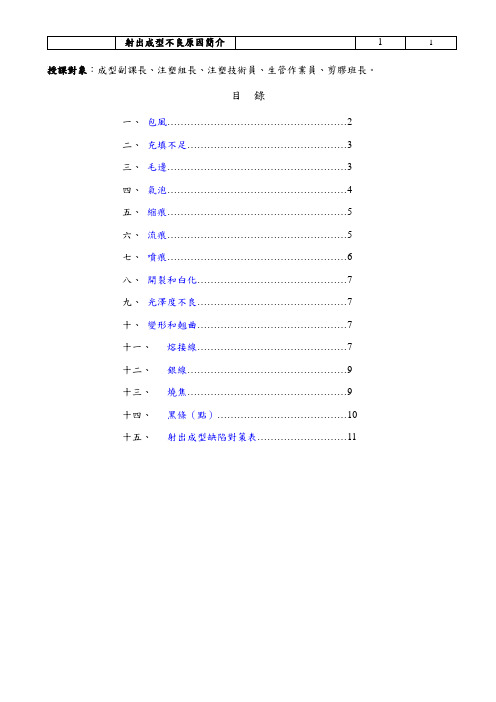
授課對象:成型副課長、注塑組長、注塑技術員、生管作業員、剪膠班長。
目錄一、包風 (2)二、充填不足 (3)三、毛邊 (3)四、氣泡 (4)五、縮痕 (5)六、流痕 (5)七、噴痕 (6)八、開裂和白化 (7)九、光澤度不良 (7)十、變形和翹曲 (7)十一、熔接線 (7)十二、銀線 (9)十三、燒焦 (9)十四、黑條(點) (10)十五、射出成型缺陷對策表 (11)一、包風:(1)現象:空氣或氣體不及排出,被熔膠波前包夾在型腔內。
(2)可能原因:射出成型機1. 射速過高。
製品1.壁厚差異太大。
壁厚差異太大時,薄壁處塑流遲緩,熔膠循厚壁快速超前,有可能對模穴中空氣或氣體進行包抄,形成包風。
模具1. 澆口位置不當。
澆口位置不當時,塑流有可能包抄空氣或氣體,形成積風。
更改澆口位置,可以改變充填模式,包風有可能避免。
2. 流道(Runner)或澆口尺寸不當多澆口設計時,流道或/和澆口尺寸如果不當,塑流有可能包抄空氣或氣體,形成包風。
3. 排氣不良若是排氣不良,波前收口處會捲入空氣或氣體,形成包風。
(3)解決方法:1.降低射速。
2.檢討製品設計。
3.檢討模具設計。
(澆口、流澆道、排氣……)二、充填不足:(1)現象:樹脂沒有完全充填到模具型腔角落。
(2)可能原因:1.樹脂的流動性不足,內壓不足。
2.可塑性不足。
3.氣體、空氣造成注射不足(逃氣)。
(3)解決方法:1.提高最大射出壓力和射出速度,提高模具溫度和樹脂溫度。
2.提高背壓,提高料管溫度。
3.減慢射速、減小鎖模力。
三、毛邊:(1)現象:熔融樹脂流入模具的分割面和型芢的接合面等間隙成形後會發生毛邊。
(2)可能原因:射出成型機1. 鎖模力不足。
鎖模力不足時,模板有可能被模穴內的高壓撐開,熔膠溢出,產生毛邊。
2. 塑料計量過多。
塑料計量過多,過量的熔膠被擠入模穴,模板有可能被模穴內的高壓撐開,熔膠溢出,產生毛邊。
3. 料管溫度太高或太低。
料管溫度太高,熔膠太稀,容易滲入模穴各處的間隙,產生毛邊。
塑胶成型不良原因分析

塑胶成型不良原因分析塑胶成型不良原因分析注塑成型以前叫压铸成型,注塑成型的优点在于能生产出外形复杂,尺寸精确,色彩随意或带有金属嵌件镶块的制品。
注塑成型必须的二个条件是:1、塑料必须以熔融状态进入模具﹔2、塑料熔体必须具有足够的压力,流速保证及时充满模腔。
一、注塑机分为柱塞式注塑机和预塑化螺杆注塑机,预塑化螺杆注塑机主要有三部分组成:1、注塑装置:主要包括料筒及其加热装置,螺杆,喷嘴,料斗离合器及螺杆转动装置,注射油缸等﹔2、合模装置:主要包括固定模板,移动模板,连接模板的拉杆,开合模油缸,制品顶出装置﹔3、液压传动电气控制系统:主要包括电动机,油泵,液压管道各类配件及其它液压件,电气控制柜,仪表监控装置。
二、不良现象有:1、缺料、缺胶(制件不满)(1)进料调节不当:A:缺料,加料是不够﹔B:多料,加料量过多,因消耗额外的注射压力来压紧导致不满。
(2)射压力不妥,流动性差的用高压,形状复杂,厚薄变化大的宜用低压。
(3)料温过低,过早的在模内冷却,难以充满。
(4)模具温度低或温度分布不合理。
(5)塑料流动性差。
(6)喷嘴配合不良(大,小,堵塞,没配合好)。
(7)塑料溶块堵塞加料通道。
(8)喷嘴冷料入模。
(9)模具设计不合理。
2、飞边,飞边又称溢边,披锋,毛刺等,此种不良现象大多发生在模具的分合位置上,(动模和静模的分型面,滑块的滑配位置,镶件的缝隙顶杆孔隙等处)。
(1)原因一:模具分型面精度差A:塑料粘度太高或太低﹔B:分型面上沾有凸出之异和或撬印﹔C:注射速度,注射时间,制件壁薄的要快速充模,制件壁厚的要慢速充模。
3、银纹(包括表面气泡和内部气孔)这是一种常见的毛病,是塑料充模时受气体干扰而出现在制件表面熔料,流动方向上的缺陷。
气体成份包括:水气、分解气、溶解气以及空气。
(1)水气(不规则地分布在整个塑料件的表面,大致上就是水气所致)A:塑料从水气中吸潮﹔B:塑料从着色剂中吸潮﹔C:塑料干燥不良﹔D:型腔型芯壁面带水份(冷却水路漏水)。
射出成型常见不良现象级处理措施

射出成型中常見不良現象產生原因分析及對策以下所列舉的成型中產生的不良原因及對策是指在一般情況下可能出現的﹐也僅以本人在工作中的一些心得﹐體驗為例﹐如有不妥或不周之處﹐還請各位行家指正﹗(一)短射(不飽模)(1)短射(不飽模)﹕即是溶融塑膠未能完全填充填滿成型空間(模穴)各個角落的現象(2)原因及改善對策(見下表)原因 改善對策1, 料溫﹐模溫太低 提高料管溫度和模具溫度2﹐噴嘴﹐主流道及灌點尺寸太小 適當加大噴嘴,主流道及灌點尺寸3﹐模具排氣不良 模面保持潔淨﹐增開排氣孔4﹐噴嘴冷頭或堵塞 清除射嘴雜物﹐適當提高射嘴溫度5﹐料管﹑止逆閥磨損﹐內泄 更換止逆閥﹑料管6﹐射出速度﹐壓力不夠 提高射速﹐射壓7﹐塑料顆粒大小不一造成溶化不均 調整背壓與螺杆轉速﹐使塑料混合均勻(二)毛邊(1)毛邊﹕即是在分模面﹑流道周圍及模仁鑲塊間隙內出現的膜狀或毛刺狀的多余膠料(2)原因及改善對策(見下表)原因 改善對策1, 模具鎖模力不足﹐射膠時模具被撐開 提高機台鎖模壓力或調較大型機台2﹐分模面不吻合或有雜物 清理模面﹐重新配模使公母模吻合3﹐模具鑲塊有間隙 鑲塊重配至無間隙4﹐模溫太高 調整模溫5﹐料溫太高 降低料管溫度6﹐射出壓力過大 降低射壓7﹐射出速度太快 減慢射速8﹐保壓時間﹐壓力設定不當 調整保壓壓力及時間9﹐背壓太大﹐螺杆轉速太快 降低背壓及螺杆轉速10﹐成品面積太大或灌點位置﹐數量設改用較大機台﹐改正灌點位置﹐數量 計不當*注﹕成型時間過長﹐模溫過低而采用高壓﹐高速射出也是產生毛邊的常見原因(三)銀 線(1)銀條(銀線)即是在成型產品表面或表面附近﹐沿塑料流動方向﹐呈放射狀的銀白色條紋。
(2)原因及改善對策(見下表)原因 改善對策1,塑料中含水份太多 成型前充分干燥成型材料2﹐材料中有易揮發性成份或雜質 原料盡量少用揮發性強的添加濟保証材料純度 3﹐模具溫度過低 適當提高模溫4﹐模具排氣不良 疏通排氣溝或增設排氣孔5﹐模穴內有油﹑水或脫模濟 清理模穴內水﹐油及脫模濟6﹐橫澆道﹑進澆口過小 加大橫澆道及進澆口7﹐射出壓力過大﹐射速太快 降低射壓及減緩射速8﹐料管中余料過火 減少料管余料及降低射嘴溫度縮短成型周期 9﹐材料在料管中分解過火 降低料管后段溫度﹐適當增加背壓﹐減慢螺杆轉速(四)成品光澤度低(1)成品光澤度低是指成品表面光澤達不到品質要求﹐表面無折光度。
塑胶产品的常见成型不良缺陷和原因分析

质量中心测试组2013
1
常见不良缺陷名称
1.缺胶 4.气纹 7.融接痕
2.披锋 5.银丝纹 8.气泡
3.缩水 6.拉伤 9.破裂
10. 翘曲变形
质量中心测试组2013
2
不良缺陷案例和原因分析
缺陷:缺胶
缺胶
质量中心测试组2013
3
不良缺陷案例和原因分析
缺胶
定义: 成品未充填完整,有一部分缺少的状态,称为缺胶。
质量中心测试组2013
4
不良缺陷案例和原因分析
缺陷:披峰 披峰
质量中心测试组2013
5
不良缺陷案例和原因分析
披峰
定义: 成品出现多余的塑胶现象,多在于模具的合模处,顶针处,滑 块处等活动处。
原因分析: 1、滑块与定位块如果磨损,则容易出现毛边; 2、模具表面附著异物时,也会出现毛边; 3、锁模力不足,射出时模具被打开,出现毛边; 4、原料温度以及模具温度过高,则粘度下降,所以在模具仅有间 隙上也容易产生毛边; 5、料量供给过多,原料多余射出产生毛边。
质量中心测试组2013
8
不良缺陷案例和原因分析
缺陷:气纹
毛纹
质量中心测试组2013
9
不良缺陷案例和原因分析
气纹
定义: 在胶口附近出现如蛇状的流线,只有在侧边进胶时出现
原因分析: 1、产品柱子、筋位等设计不合理; 2、注塑时料流动性差,润滑剂太少; ; 3、注射压力过低,速度太慢,注射时间和保压时间太短; 4、熔体温度和模具温度太高;
原因分析: 1、模具排气效果不佳,模穴内的空气如果没有在射出时排除, 则会由于残留空气的原因而使充填不完整; 2、模具温度低,原料流动距离长,或者有薄壁的部分,则在 原料充填结束前冷却固化; 3、熔融的原料温度低或射出速度慢,原料在未充满模穴之前 就固化而造成短射的现象; 4、灌嘴孔径小或灌嘴长,灌嘴温度低,灌嘴或射嘴孔变形, 则不仅使其流动的磨擦阻力加大,而且由于阻力的作用而使 速度减慢,结果原料提前固化; 5、射出压力低,造成充填不足。
塑胶射出常见不良分析及解决
光 寶 MCC 機 構 核 心 能 力 中 心
Lite-On (Guang-Zhou) Precision Tooling Ltd.
12
塑膠射出常見不良分析解決 三、银纹(料花、水花)
射速過快
原料混雜
料未烤幹
光 寶 MCC 機 構 核 心 能 力 中 心 Lite-On (Guang-Zhou) Precision Tooling Ltd.
改善方法 1.增加熔胶注射量 ① 增加熔胶计量行程 ② 提高注射压力 ③ 提高保压压力或保压时间 ④ 延长射出时间 ⑤ 加快注射速度或减慢注射速度 ⑥ 加大浇口尺寸或使模具入水平衡 ⑦ 拆除清理射嘴内异物,检查发热圈 ⑧ 重新对嘴或紧固射咀 2.调整料温 3.提高模温或适当降低模温 4.酌延冷却时间 5.改善成品设计,使胶厚均匀 7.更换机器或料管 8.加粗主/分流道尺寸,减短流道长度
下表即为缩水實例及原因分析
光 寶 MCC 機 構 核 心 能 力 中 心
Lite-On (Guang-Zhou) Precision Tooling Ltd.
8
塑膠射出常見不良分析解決 二、缩水(凹痕)
肉位過厚
保壓過小
冷卻不夠
進膠點偏小
流道太長
光 寶 MCC 機 構 核 心 能 力 中 心
Lite-On (Guang-Zhou) Precision Tooling Ltd.
1.5~4.5 2~5 1~4.7
0.6~0.8 1.0
0.8~1.5 1.5~2.0 2~2.5 1.5~2.0 0.5~0.7 0.5~0.8 0.1~0.5
1~5 0.6~0.8
7
塑膠射出常見不良分析解決
塑料射出成型不良现象和改善对策ppt课件
8
44
3 3 3 1 15
2
7
888
6
11
5
33
2
87 7
8
6
45 5 5
3
11
12
66
11 2 2
44 433
5
5
7
66
28 8
Question
1.射出成型對成品物性的影響,可從哪四方面來考慮 2.毛邊的成因及對策 3.熔接線的成因及對策 4.縮水的成因及對策 5.翹曲/變形的成因及對策
此课件下载可自行编辑修改,供参考! 感谢您的支持,我们努力做得更好!
不良現象與對策處理 ---充填不足附表
不良現象與對策處理 ---充填不足附圖
不良現象與對策處理 ---毛邊
毛邊 可依序由机台鎖模力→原料→條件→模具來解決. 1.鎖模壓力不足 (可由油壓表看出 1.2*射出壓力=鎖喔模力). 2.模具與導銷磨損,模具配件產生間隔,或配件的密合度不良,而
產生毛邊. 3.异物附著合模面,應儘速清除. 4.料溫過高,原料黏度降低,材料滲入合模面(流動性太好)可降低
壓時度段段溫時 型
距段
道道 檢孔使各缸 時溫
力間 溫溫度間 銷
離距
大位 修 用部
間度
度度
溫
離
小置
度
塑膠自噴嘴滴流 充填不足 螺桿不退 收縮下陷 益料,毛邊 脫模時破裂 成型品黏著 流道黏著 表面光潔不良 黑條 燒焦 黑點或黑斑 流痕 熔合線 銀條 成品脆弱 成形品變形 成形品氣泡
3
21
2 33 1 4 42 3
原性 原 料
耐衝擊性
結晶化度
模腔形狀
模具設計 模具材質
強韌性
塑胶射出成型条件与调整之基本概念
塑料射出成型条件及调整之基本概念壹、成型条件决定之五大因素成型条件主要由压力、速度、位置、时间及温度等五种组成.并由此互五种因素相互调配而完成一个属于成品质量可接受的成型条件.其中即有压力必有速度、位置、时间的配合,若其中有一项设定为零时,则无法有其功能的产生.贰、成型条件的三大主要压功能之说明:(一)一次压力(即射出压力)射出压力可以说是射出成型中,最重要的参数之一.在射出成型阶段时,螺杆像柱塞般移动,使射出压力建立在螺杆前端熔体上.射出压力影响了螺杆前进速度及把塑料充填模穴内的过程,且在很短的时间内, 由零(或是系统最小之压力)升高到所要的压力,而这个压力由在射嘴、浇道、流道及模穴中之熔体的流动阻力来决定.在喷嘴及浇注系统中的阻力太高,会建立高的射出压力,使得模穴充满后的压缩阶段的起始点难以办识.相反地,如果流动阻小很小时,压缩阶段起始点就很容易区分.射出压其功能在填充模穴内各角落,使其呈现饱模状况,若压力速度配合得宜时,其完成时间约在1~2秒内完成.(二) 、二次(压即保持压)其功能在防止原料回流所继续提供的压力,其作用为使成品密度增加,不易缩水并防止变形的产生,但若保压过大,时间太长,则会产生内应力的现象,若内应力太高时,可利用保压段数实施退火处理解决.保持压力的大小及期间成形品尺寸精度及外观质量优劣有大的影响.同时也决定塑品及模穴表面的复制性.最佳的压力值可由塑品尺寸及缩水情况判熂决定,而保压时间长短通常是猜测的.模穴压力如果能量测到则其可提供可靠的信息,只要浇道、浇口或任何狭窄通道尚未凝固,改变保压之大小及时间对模穴压力将会有影响,在浇口封住(固化)之后,就没有任何的影响.(三) 、三次压(即背压)在塑化过程中,当螺杆头前端,塑料囤积至一定量时,便会顺应为了继续囤积的需求,产生一反作用力,将螺杆慢慢往后推.当此反作用力遇到阻力时,背压表指针便开始爬升,此阻力我们称之为背压,背压可在射出唧简后退行程中,以油压回油油路的流量调整阀加以控制,并可由背压表读取此值数,此控制用来减缓螺杆后退之速度,并可测计量区的反作用力,如果当背压太大将会造成螺杆不退原地空转,迫使塑料从喷嘴流出,因此一般背压使用很少超过35kg/cm2背压的主要作用为:●增加背压,可增加螺杆对熔融树脂所做的功.●增加背压,可提高熔融温度及其均匀程度.●增加背压,可消除未熔的塑料颗粒.●增加背压,可增加料管内原料密度及其均匀程度.由以上可知背压的优点.不过增加背压却会降低螺杆的出力,而且也会破坏玻璃纤维的长度并且改变下班的特性,不得不注意.若依螺杆而言,在没有加阻料环的情况下,通常螺沟愈深,则输出量对射出压力詷整会相当敏感,背压的作用亦非常明显,反之深浅则输出量对射压调整并不明显,机械背压的感应也就罗不敏感.背压常被运用来提高料管理温度,其效果最为显著.参、射出至保压力的切换:A: B: C: D:↑从射出阶段到保压阶段无切换点的射出成形↑切换廷迟切换提早正确的切换,从射出至保压是平顺的转换模具卸料(材料回料管)↑用保压力充满模穴↑时间→时间→时间→时间→模穴内压曲线及影响的因素(a)轴赂移动速度(v) (b)模具温度(t)(c)浇口几何形状 (d)压力传感器及浇口的距离(g)由于有关模穴的内压力数据一般都不可靠,而使压压力切换点的选择经常是不正确的.列出四种基本的可能性:(a)没切换的射出(b)切换较迟的射出(c)切换较早的射出(d)较佳切换的射出如果最后压力越近于填充压力时,不用保压压力切换点的操作是可行的,这操作大部分发生于有小的浇口及有大的流向长/厚度比的塑品.即使浇口很大,相对地要求达到高的射出速度,而发生延迟切换的机会很大,其经常伴随着高度挤压的危险.除了对尺寸及毛边的不良影响,延迟切换是造成模穴边缘变形及夹模单元超负载的危险的主因.继而造成对系杆(大柱)的永久性伤害,甚至于长期运转后会继裂而报废.当从高的射出压力切换到较低的保压压力时,会造成熔体的回流,而在塑品内部形成不好的应力排列,若保压压力于浇口塑料固化前被切掉,也会有同样的状况.压力逆传的现象表示提早切换至保压压力,充填过程中的平衡,发生在偏低的保压压力状况,且因而降低射出速度.在切换瞬间,会造成短暂的流动停而使产品的表面产生令人压烦贩痕迹.从射出压力切换至保压压力的决定有三个主要方法,而其及后列三项有关:(1)时间、(2)位置、(3)模穴压力.(一)、利用时间切换此方法是从射出起始点开始计时,经过预定设定的时间,即送出一信号.此法不考虑在螺杆前端熔体的压缩性及其粘滞性、进料的准确性、射出速度变化、其中油压压力会造成螺杆位置偏移(进料结束点保压起始点)及其它相关的行程(进料行程、射出行程).最成结果是大变化性的质量规范,尤其是有关成型品的重量尺寸.因此,利用时间切换,原则上是不适当的,不用怀疑,它是所有方法里最糟的选择.(二)利用位置这种方法由证实是有用的且广泛被应用,切换信号是经由保压压力换位置的极限开关所送出.如果射出行程大部分维持固定,则切换点可视同每次皆在相同充填容积下发生.这种方法在保太行程很短的情况下会出问题,危险的是小的变化阻止每次的切换动作,在此情况下,最好还是完全不要有切换过程.此外包括进料行程的变化,极限开关的不准确,止逆阀的失效、不同的熔体粘度都会造成此方法出现问题.(三) 、利用模穴压力切换最近几年,利用压力切换的方法已被成功地使用,即使是在最糟的实际生产条件下.模穴压力在达预设之压力时,去作动切换功能其优点是有稳定可靠的切换信号,而此信号是基于绝对量的压力值所产生,使得切换更有效率.采用压力监视,可使螺杆行程和止逆阀功能的影响被排除.此种方法和两种方法一样不能对液压油、熔融塑料、模具等作温度变化补偿,或是射出速度的变化被赏.在压缩阶段压力快速上升用此种方法更具效率,因为在此状况下特别精密及适时的切换可强制性地避免压力峰的出现.在多种成形种类之中,此法特别适合用于那些分模面宽广及不允许毛边出现的情形,例如设备的平面盖板,其只有一点深度.肆、一般工程塑料成型不良原因及解决方法一、聚碳酸酯(PC)二、聚氧化二甲苯(变性PPO树脂)(MPPO)三、苯对苯二甲酸丁酸(PBT)第 11 页。
射出成型之缺陷异常+原因分析与对策
射出成型之缺陷异常原因分析与对策【射出成型之缺陷異常原因分析与对策】概述成型品原则上都是依据规格/标准和客户的要求制造的,但在实际注塑秤过程中它的变化仍是相当广泛而复杂的;有时当生产进行得很顺利时,会突然产生缩水、变形、裂痕、银纹或其它不良缺陷等。
在注塑时我们需从胶件所产生的缺陷,来准确分析/判断问题点所在,找出解决问题的方法,这是一种专业性的技术及经验的累积。
有时只要变更注塑工艺条件、对模具/机器方面稍做调整与改善或更换所使用的原料,就可以解决问题。
注塑成型中对成型品物性的主要影响因素可从以下四个方面来考虑:A、原料B、注塑机C、注塑模具D、成型条件注塑过程中出现的异常问题很多,主要是“产品质量缺陷”和“注塑生产中特有的异常现象”两大类。
注塑产品常见的质量缺陷有:缺胶、缩水、银纹(料花)、披锋(飞边)、烧焦、气泡(缩孔)、水波纹、喷射纹(蛇纹)、流纹(流痕)、夹水纹、裂纹(龟裂)、顶白、表面无光泽、翘曲变形、黑条、混色、拖花、透明度不足、尺寸偏差、剥离(起皮)、冷料斑、黑点、气纹、色差、盲孔、断柱等……注塑生产中特有的异常现象有:喷嘴流涎(流涕)、漏胶、胶件粘模、水口拉丝、嵌件不良、多胶、断针、堵嘴、顶针位穿孔、模印、压模、塑化噪音、下料不畅、螺杆打滑、开模困难等等。
下面分析各种注塑缺陷及异常现象产生的原因并探讨其解决问题的方法。
A、注塑常见缺陷原因分析及改善方法目錄1、走胶不齐的原因分析及改善对策且 (2)2、缩水(缩痕)的原因分析及改善对策 (3)3、银纹(料花、水花)的原因分析对改善对策 (5)4、披锋(飞边)/烧焦(困气)原因分析及改善对策 (8)5、缩孔(真空泡)的原因分析及改善对策 (9)6、水波纹的原因分析及改善对策 (10)7、喷射纹(蛇纹)/流纹(流痕)的原因分析及改善对策 (11)8、夹水纹(熔接线)的原因分析及改善对策 (12)9、裂纹(龟裂)的原因分析及改善对策 (13)10、顶白或顶爆的原因分析及改善对策 (14)11、成品表面无光泽/胶件翘曲变形的原因分析及改善对策 (15)12、黑条(黑纹)的原因分析及改善对策 (17)13、混色的原因分析及改善对策 (18)14、拖花(拉伤)/透明度不足的原因分析及改善对策 (19)15、尺寸偏差/剥离(起皮)的原因分析及改善对策 (20)16、冷料斑/黑点的原因分析及改善对策 (21)17、气纹(阴影)的原因分析及改善对策 (22)18、色差的原因分析及改善对策 (23)19、强度不足的原因分析及改善对策 (24)20、气泡/金属嵌件不良的原因分析及改善对策 (25)21、盲孔的原因分析及改善对策 (26)22、内应力产生的原因及改善对策 (27)23、表面浮纤产生的原因对改善对策 (28)24、白点产生的原因及改善对策 (29)25、注塑生产特有的异常现象(11种现象) (30)26、其它注塑异常现象(10种情况) (36)一、走胶不齐(缺胶未射滿)provides venture platform, makes many youth round has venture dream, for national solution has important of employment problem. Relevant departments units carefully to discover, cultivate talent. From the perspective of Dongping, contradiction of rapid economic development and personnel shortages. Currently facing the industry transformation and upgrading, and transform and upgrade traditional industries, is the development of new industries such as tourism, logistics, e-commerce, we still lack a large number of capital operation and management of talents, the lack of technological innovation, technology transfer, product research and development, tourism services and other high-level professional and technical personnel. Especially with theIndustry further develops, the demand is growing. We must stand in the global and strategic height, with a high degree of political responsibility and historical mission, counties implement talent strategies as a major and pressing task to seize good, practical human resource development as industrial counties of the country. Departments at all levels must firmly establish the "talent is wealth, talent is competitive, talent is creativity" concept, fully aware of the extreme importance of talent, the real talent working on the agenda, the primary task of the primary resources to support the development of talent. 2 the construction of enterprisers ' as the starting point, and promote the transformation and充填不足是溶融的塑料未完全注满模具成型空间的各个角落之现象。
- 1、下载文档前请自行甄别文档内容的完整性,平台不提供额外的编辑、内容补充、找答案等附加服务。
- 2、"仅部分预览"的文档,不可在线预览部分如存在完整性等问题,可反馈申请退款(可完整预览的文档不适用该条件!)。
- 3、如文档侵犯您的权益,请联系客服反馈,我们会尽快为您处理(人工客服工作时间:9:00-18:30)。
20
FIRST ENGINEERING
FIRST ENGINEERING (GUANGZHOU) CO., LTD ●射出成形上的调整:
1、于工程塑胶须充分除湿且乾燥
2、二次料的使用比例须严格控管或不用 3、依成品的大小选用适当的料管(炮筒直径)
4、调整射出温度
5、提高模具温度
4、降低頂出速度
SANXING/QA
14
FIRST ENGINEERING
FIRST ENGINEERING (GUANGZHOU) CO., LTD
七、充填不足(Short Shot)
●形成原因:塑料于模具內充填时,因墙厚太薄、进胶口的位置不 當...等因素造成,塑料无法有效的完全充填于模具內, 形成缺料,称充填不足。 ●成品的影响:形狀尺寸均不完整
SANXING/QA
9
FIRST ENGINEERING
FIRST ENGINEERING (GUANGZHOU) CO., LTD ●结构设计上的预防: 1、加补强肋防止 2、增加墙厚 3、拔模角的增加 4、选用钢性较高的塑料(如PBT或PBT加GF)
●模具设计上的调整: 1、进胶口 的位置、大小、数量的选择 2、頂出的平衡 3、冷却系統的不平衡
●射出成形上的调整: 1、提高成形温度 2、提高射出速度 3、提高射出压力 4、增加背压 5、减少脱模剂使用
SANXING/QA
4
FIRST ENGINEERING
FIRST ENGINEERING (GUANGZHOU) CO., LTD
二、缩水、凹痕(Sink Mark)
●形成原因:塑胶料在热胀冷缩时,因墙厚不均,而使墙厚较厚部 份冷却较慢,墙厚较薄部份,冷却较快,而在其厚 薄交接处,会产生一個痕跡,称缩水痕。 ●成品的影响: 1、视觉外观上的不良 2、尺寸上会有差异 ●外观造型上的预防: 1、外观造型上勿太复杂且多孔,易造成射出压力损失 2、外观造型尽量以大弧面或R圆角修饰 3、外观表面是纹理面更不易看出缩水痕
FIRST ENGINEERING
FIRST ENGINEERING (GUANGZHOU) CO., LTD
塑胶射出成型问题的分析、 预防及解决对策探讨
主讲人: 杨穗章
日期:2005.04.30
SANXING/QA
版数:B 1
FIRST ENGINEERING
FIRST ENGINEERING (GUANGZHOU) CO., LTD 塑胶射出成型品所产生的问题,其实包括从外观设计、 结构设计 、 模具设计 、射出成型条件上的设定 、生产制造、包装运送…… 等,均是息息相关, 而且环环相扣。所以针对问题分析其根源, 才能 对症下药, 防患问题于未然。 以下就针对塑胶射出成型品常见问题的分析及探讨:
2、降低射出压力 3、降低保压时间
4、提高锁模力
5、更换较合适机台或料管(炮筒直径)
SANXING/QA
12
FIRST ENGINEERING
FIRST ENGINEERING (GUANGZHOU) CO., LTD
六、頂白(Whitening)
●形成原因:塑胶件于公模頂出时,因粘公模、頂出不平衡、墙厚太 薄…等因素,造成頂出困难,形成于頂針处有白痕称为 頂白。 ●成品的影响:外观上有白痕且严重时有凸出的现象
19
FIRST ENGINEERING
FIRST ENGINEERING (GUANGZHOU) CO., LTD
十、脆弱(Brittleness)
●形成原因:塑胶件成型时,因塑料发生劣化或热裂解产生脆化,降低 塑胶件原有的强度称脆弱。
●成品的影响:无法通过信赖性测试 ●外观造型的预防:无 ●结构设计上的预防: 1、增加塑件墙厚 2、防止结合线位置于受应力处 3、加肋补强 4、选用冲击强度较高的塑料 ●模具设计上的调整:改变浇口位置及尺寸
SANXING/QA
21
FIRST ENGINEERING
FIRST ENGINEERING (GUANGZHOU) CO., LTD
十一、银纹(Silver Streak)
●形成原因:塑胶料于成型中,因胶粒大小不一或含水份偏高,造成如 银色流纹称银纹。 ●成品的影响:外观不良
●外观造型上的预防:无
●射出成型上的调整: 1、降低射出压力 2、减少保压时间 3、增加冷却时间
SANXING/QA
10
FIRST ENGINEERING
FIRST ENGINEERING (GUANGZHOU) CO., LTD
五、毛边(Flash)
●形成原因:于公、母模的合模面上,有间隙或是射出压力过大、流料 不均……..等因素造成塑胶溢料,形成毛边现象。 ●成品的影响: 1、毛边过大会有刮手的感觉 2、毛边有时会影响和另一配件的组配间隙 ●外观造型上的预防:外观造型设计时,尽量勿造成脱模方向干涉
●外观造型上的预防: 1、外观拔模角度的正确选定 2、外观亮面较纹理面不易产生粘母模 ●结构设计上的预防: 1、公、母模面的投影面绩比 2、公、母模面的表面粗糙度比较 ●模具设计上的调整: 1、外观拔模角适度加大或降低外观粗糙度 2、公模面适度加倒勾
SANXING/QA
17
FIRST ENGINEERING
四、翹曲、变形(Warpage)
● 形成原因:成品因形狀太长或复杂、厚度太薄,而造成冷却不均 、射出压力不平衡………等因素造成。
●成品的影响:
1、外观变形 2、尺寸变形而影响组配的方便性
●外观造型上的预防: 1、外观造型上勿太复杂,且为大弧面 2、成品形狀力求左、右对称 3、尽量勿设计长且薄或深且薄的成品形狀
●外观造型上的预防:无
●结构设计上的预防: 1、防止塑件墙厚不均或太薄 2、太长的肋须有适当拔模角 3、选用流动性较好的塑料 ●模具设计上的调整: 1、进胶口的位置、大小、数量配置调整 2、模具排气孔的调整 3、设置冷却井
SANXING/QA
15
FIRST ENGINEERING
FIRST ENGINEERING (GUANGZHOU) CO., LTD ●射出成形上的调整: 1、成形机台的适当选用 2、提高射出温度 3、提高射出压力
●成品的影响: 1、强度降低 2、视觉外观上不良 ●外观造型上的预防: 1、外观造型力求顺畅,避免有太深的凹或凸槽产生 2、外观表面是纹理面更不易看出结合线 3、减少孔的产生
SANXING/QA
3
FIRST ENGINEERING
FIRST ENGINEERING (GUANGZHOU) CO., LTD ●结构设计上的预防: 1、成品墙厚力求平均,如须设计成墙厚不均,也以墙厚70﹪ 为下限,且厚、薄交接处须作R圆角 2、为使流料平衡,可局部增加或减少墙厚(范例:听筒) ●模具设计上的调整: 1、提高整体模温或接合线处的模温 2、进胶口位置、大小、数量的选择。(靠近孔) 3、接合处的排气
●外观造型上的预防:无
●结构设计上的预防: 1、拔模角的选定 2、墙厚较薄处,勿有頂針或是局部加墙厚 3、內部设计勿太复杂造成脱模困难 ●模具设计上的调整: 1、頂出结构的平衡及顺畅 2、公模面再推亮 3、检修排气孔 SANXING/QA
13
FIRST ENGINEERING
FIRST ENGINEERING (GUANGZHOU) CO., LTD ●射出成形上的调整: 1、增加冷却时间 2、降低射出压力 3、适度使用脱模剂
1、咬花及放电花的选定 2、推亮面的模材选择。STAVAX,MAK80,电镀
●模具设计上的调整:
1、增加拔模角 2、检查拔模面是否平整 3、检查頂出系統是否平衡
●射出成型上的调整: 1、降低射出压力(会导致缩水现象) 2、增加冷却时间
SANXING/QA
8
FIRST ENGINEERING
FIRST ENGINEERING (GUANGZHOU) CO., LTD
●结构设计上的预防:无 ●模具设计的调整: 1、增加排气孔 2、扩大浇口或浇道 ●射出成形上的调整: 1、胶料大小要平均,且勿中空,勿混合过小胶粒 2、胶粒须充分乾燥 4、降低射出温度 3、提高背压 5、降低射出速
一、 结合线 ( Weld - Line ). 二、 缩水 凹陷 ( Sink Mark ). 三、 脱模拉伤. 四、 翹曲变形 ( Warpage ). 五、 毛边 ( Flash ). 六、 顶白 ( Whitening ) . 七、 充填不足 ( Short Shot ). 八、 粘母模 (Adhere-Female die) . 九、 流纹、流痕 ( Flow Mark ). 十、 脆裂 ( Brittleness ). 十一、银纹 ( Silver Streak ). 十二、烧焦 (Scorch). 十三、玻纤浮面 (FG-Surface). SANXING/QA
4、提高模温
5、提高射出速度
SANXING/QA
16
FIRST ENGINEERING
FIRST ENGINEERING (GUANGZHOU) CO., LTD
八、粘模(脱模不良)
●形成原因:塑件于母模開模时,因外观拔模角太小、射出压力品的影响:无法成形
拉伤
●外观造型上的预防:
1、外观造型须考虑适当的拔模角度。(为纹路最小拔模角 再加 1~2°) 2、外观亮面较纹理面不易产生脱模拉伤 3、修饰外观防止脱模拉伤,側边作一圈亮面
SANXING/QA
7
FIRST ENGINEERING
FIRST ENGINEERING (GUANGZHOU) CO., LTD ●结构设计上的预防:
●结构设计上的预防:分模面的正确选定
●模具设计上的调整: 1、排气孔的调整 2、进胶口的位置(流料平衡) 3、公、母模合模面是否有间隙