封装
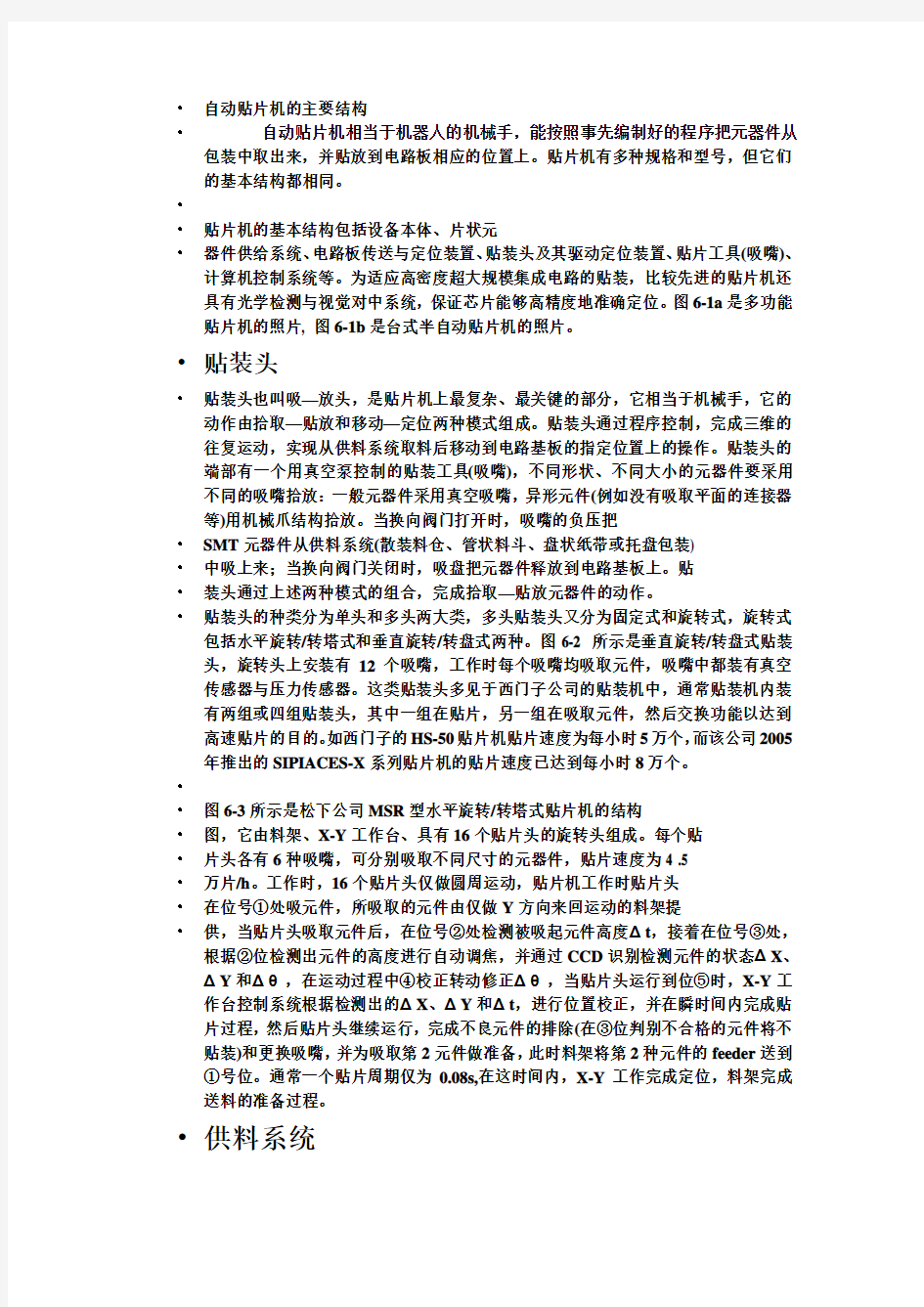
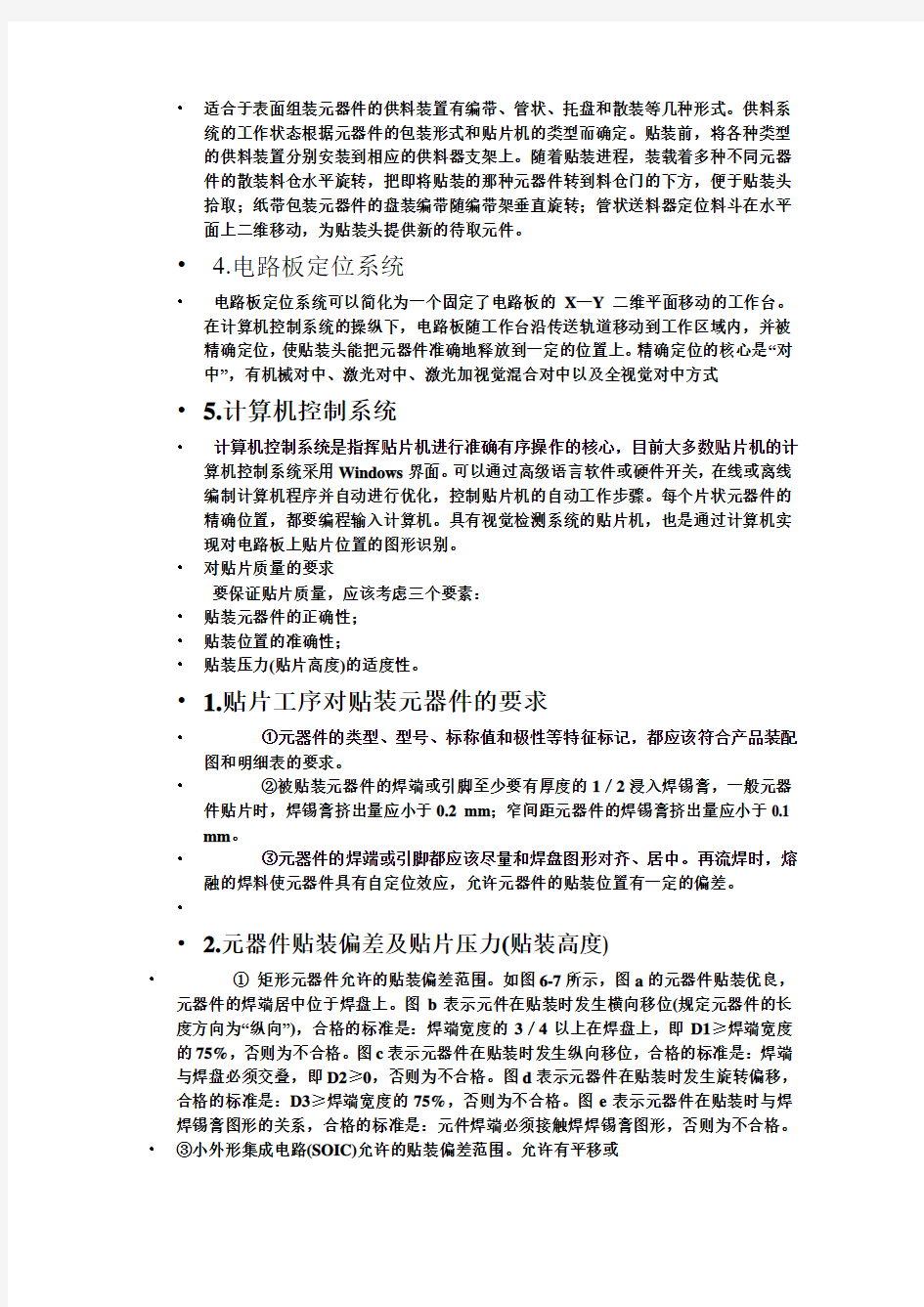
?自动贴片机的主要结构
?自动贴片机相当于机器人的机械手,能按照事先编制好的程序把元器件从包装中取出来,并贴放到电路板相应的位置上。贴片机有多种规格和型号,但它们的基本结构都相同。
?
?贴片机的基本结构包括设备本体、片状元
?器件供给系统、电路板传送与定位装置、贴装头及其驱动定位装置、贴片工具(吸嘴)、计算机控制系统等。为适应高密度超大规模集成电路的贴装,比较先进的贴片机还具有光学检测与视觉对中系统,保证芯片能够高精度地准确定位。图6-1a是多功能贴片机的照片, 图6-1b是台式半自动贴片机的照片。
?贴装头
?贴装头也叫吸—放头,是贴片机上最复杂、最关键的部分,它相当于机械手,它的动作由拾取—贴放和移动—定位两种模式组成。贴装头通过程序控制,完成三维的往复运动,实现从供料系统取料后移动到电路基板的指定位置上的操作。贴装头的端部有一个用真空泵控制的贴装工具(吸嘴),不同形状、不同大小的元器件要采用不同的吸嘴拾放:一般元器件采用真空吸嘴,异形元件(例如没有吸取平面的连接器等)用机械爪结构拾放。当换向阀门打开时,吸嘴的负压把
?SMT元器件从供料系统(散装料仓、管状料斗、盘状纸带或托盘包装)
?中吸上来;当换向阀门关闭时,吸盘把元器件释放到电路基板上。贴
?装头通过上述两种模式的组合,完成拾取—贴放元器件的动作。
?贴装头的种类分为单头和多头两大类,多头贴装头又分为固定式和旋转式,旋转式包括水平旋转/转塔式和垂直旋转/转盘式两种。图6-2 所示是垂直旋转/转盘式贴装头,旋转头上安装有12个吸嘴,工作时每个吸嘴均吸取元件,吸嘴中都装有真空传感器与压力传感器。这类贴装头多见于西门子公司的贴装机中,通常贴装机内装有两组或四组贴装头,其中一组在贴片,另一组在吸取元件,然后交换功能以达到高速贴片的目的。如西门子的HS-50贴片机贴片速度为每小时5万个,而该公司2005年推出的SIPIACES-X系列贴片机的贴片速度已达到每小时8万个。
?
?图6-3所示是松下公司MSR型水平旋转/转塔式贴片机的结构
?图,它由料架、X-Y工作台、具有16个贴片头的旋转头组成。每个贴
?片头各有6种吸嘴,可分别吸取不同尺寸的元器件,贴片速度为4 .5
?万片/h。工作时,16个贴片头仅做圆周运动,贴片机工作时贴片头
?在位号①处吸元件,所吸取的元件由仅做Y方向来回运动的料架提
?供,当贴片头吸取元件后,在位号②处检测被吸起元件高度Δt,接着在位号③处,根据②位检测出元件的高度进行自动调焦,并通过CCD识别检测元件的状态ΔX、ΔY和Δθ,在运动过程中④校正转动修正Δθ,当贴片头运行到位⑤时,X-Y工作台控制系统根据检测出的ΔX、ΔY和Δt,进行位置校正,并在瞬时间内完成贴片过程,然后贴片头继续运行,完成不良元件的排除(在③位判别不合格的元件将不贴装)和更换吸嘴,并为吸取第2元件做准备,此时料架将第2种元件的feeder送到
①号位。通常一个贴片周期仅为0.08s,在这时间内,X-Y工作完成定位,料架完成
送料的准备过程。
?供料系统
?适合于表面组装元器件的供料装置有编带、管状、托盘和散装等几种形式。供料系统的工作状态根据元器件的包装形式和贴片机的类型而确定。贴装前,将各种类型的供料装置分别安装到相应的供料器支架上。随着贴装进程,装载着多种不同元器件的散装料仓水平旋转,把即将贴装的那种元器件转到料仓门的下方,便于贴装头拾取;纸带包装元器件的盘装编带随编带架垂直旋转;管状送料器定位料斗在水平面上二维移动,为贴装头提供新的待取元件。
? 4.电路板定位系统
?电路板定位系统可以简化为一个固定了电路板的X—Y二维平面移动的工作台。
在计算机控制系统的操纵下,电路板随工作台沿传送轨道移动到工作区域内,并被精确定位,使贴装头能把元器件准确地释放到一定的位置上。精确定位的核心是“对中”,有机械对中、激光对中、激光加视觉混合对中以及全视觉对中方式? 5.计算机控制系统
?计算机控制系统是指挥贴片机进行准确有序操作的核心,目前大多数贴片机的计算机控制系统采用Windows界面。可以通过高级语言软件或硬件开关,在线或离线编制计算机程序并自动进行优化,控制贴片机的自动工作步骤。每个片状元器件的精确位置,都要编程输入计算机。具有视觉检测系统的贴片机,也是通过计算机实现对电路板上贴片位置的图形识别。
?对贴片质量的要求
要保证贴片质量,应该考虑三个要素:
?贴装元器件的正确性;
?贴装位置的准确性;
?贴装压力(贴片高度)的适度性。
? 1.贴片工序对贴装元器件的要求
?①元器件的类型、型号、标称值和极性等特征标记,都应该符合产品装配图和明细表的要求。
?②被贴装元器件的焊端或引脚至少要有厚度的1/2浸入焊锡膏,一般元器件贴片时,焊锡膏挤出量应小于0.2 mm;窄间距元器件的焊锡膏挤出量应小于0.1 mm。
?③元器件的焊端或引脚都应该尽量和焊盘图形对齐、居中。再流焊时,熔融的焊料使元器件具有自定位效应,允许元器件的贴装位置有一定的偏差。
?
? 2.元器件贴装偏差及贴片压力(贴装高度)
?①矩形元器件允许的贴装偏差范围。如图6-7所示,图a的元器件贴装优良,元器件的焊端居中位于焊盘上。图b表示元件在贴装时发生横向移位(规定元器件的长度方向为“纵向”),合格的标准是:焊端宽度的3/4以上在焊盘上,即D1≥焊端宽度的75%,否则为不合格。图c表示元器件在贴装时发生纵向移位,合格的标准是:焊端与焊盘必须交叠,即D2≥0,否则为不合格。图d表示元器件在贴装时发生旋转偏移,合格的标准是:D3≥焊端宽度的75%,否则为不合格。图e表示元器件在贴装时与焊焊锡膏图形的关系,合格的标准是:元件焊端必须接触焊焊锡膏图形,否则为不合格。?③小外形集成电路(SOIC)允许的贴装偏差范围。允许有平移或
?旋转偏差,但必须保证引脚宽度的3/4在焊盘上。如图6-8所示、
?④四边扁平封装器件和超小型器件(QFP,包括PLCC器件)允许
?的贴装偏差范围要保证引脚宽度的3/4在焊盘上,允许有旋转偏差
?但必须保证引脚长度的3/4在焊盘上。
?⑤BGA器件允许的贴装偏差范围。焊球中心与焊盘中心的最大
?偏移量小于焊球半径,如图6-9所示。
?⑥元器件贴片压力(贴装高度)。元器件贴片压力要合适,如果压
?力过小,元器件焊端或引脚就会浮放在焊锡膏表面,焊锡膏就不能粘
?住元器件,在电路板传送和焊接过程中,未粘住的元器件可能移动位
?置。
?手工贴装SMT元器件
? 1.全手工贴装
?手工贴装SMT元器件,俗称手工贴片。除了因为条件限制需要手工贴片焊接以外,在具备自动生产设备的企业里,假如元器件是散装的或有引脚变形的情况,也可以进行手工贴片,作为机器贴装的补充手段。
?(1)手工贴片之前需要先在电路板的焊接部位涂抹助焊剂和焊锡膏。可以用刷子把助焊剂直接刷涂到焊盘上,也可以采用简易印刷工装手工印刷焊锡膏或手动滴涂焊锡膏。
?(2)采用手工贴片工具贴放SMT元器件。手工贴片的工具有:不锈钢镊子、吸笔、3~5倍台式放大镜或5~20倍立体显微镜、防静电工作台、防静电腕带。?(3)手工贴片的操作方法
?①贴装SMC片状元件:用镊子夹持元件,把元件焊端对齐两端焊盘,居中贴放在焊锡膏上,用镊子轻轻按压,使焊端浸入焊锡膏。
?②贴装SOT:用镊子夹持SOT元件体,对准方向,对齐焊盘,居中贴放在焊锡膏上,确认后用镊子轻轻按压元件体,使浸入焊锡膏中的引脚不小于引脚厚度的1/2。
?③贴装SOP、QFP:器件1脚或前端标志对准印制板上的定位标志,用镊子夹持或吸笔吸取器件,对齐两端或四边焊盘,居中贴放在焊锡膏上,用镊子轻轻按压器件封装的顶面,使浸入焊锡膏中的引脚不小于引脚厚度的1/2。贴装引脚间距在0.65 mm 以下的窄间距器件时,可在3~20倍的放大镜或显微镜下操作。
?④贴装SOJ、PLCC:与贴装SOP、QFP的方法相同,只是由于SOJ、PLCC 的引脚在器件四周的底部,需要把印制板倾斜450角来检查芯片是否对中、引脚是否与焊盘对齐。
(4)在手工贴片前必须保证焊盘清洁。新电路板上的焊盘都比较干净,但返修的电路板在拆掉旧元件以后,焊盘上就会有残留的焊料。贴换元器件到返修位置上之前,必须先用手工或半自动的方法清除残留在焊盘上的焊料,如使用电烙铁、吸锡线、手动吸锡器或用真空吸锡泵把焊料吸走。清理返修的电路板时要特别小心,在组装密度越来越大的情况下,操作比较困难并且容易损坏其他元器件及线路板
? 2.利用手动贴片机贴片
?手动贴片也可以利用手动贴片机进行,这类贴片机的机头有一套简易的手动支架,手动贴片头安装在Y轴头部,X/Y,θ定位可以靠人手的移动和旋转来校正位置,如图6-10所示。有时还可以采用配套光学系统来帮助定位,手动贴片机具有多功能,高精度的特点,主要用于新产品开发,适合中小企业与科研单位小批量生产使用。
表面组装涂敷工艺
1.焊膏的涂敷
2.贴片胶的涂敷
表面涂敷工艺介绍
涂敷工艺就是施加焊膏(或贴片胶),工艺的目的是把适量的焊膏(或贴片胶)均匀地施加在PCB的焊盘上,以保证贴片元器件与PCB相对应的焊盘达到良好的电气连接?表面组装涂敷工艺按照涂敷方式的不同可以分为整体印刷涂敷、个别点涂敷、整体点涂敷。锡膏涂敷经常采用印刷技术,贴装胶涂敷通常采用滴涂技术。
?Smt印刷工艺是电子产品smt制造工艺之一,在整个制造工艺过程中有举足轻重的作用,印刷涂敷工艺所造成的缺陷占整个工艺流程造成缺陷的60-70%。
焊膏涂敷方法与原理
?焊膏直接形成焊点,其涂敷工艺技术极为重要,它直接影响表面组装组件的性能和可靠性。为此,与粘接剂的涂敷工艺技术相比,对焊膏涂敷工艺技术有更高的要求。
?将焊膏涂敷到PCB焊盘图形上的方法,主要有注射滴涂和印刷涂敷二类,广泛采用的是印刷涂敷技术。使用注射式装置施加焊膏的工艺过程称为注射滴涂(亦称点膏或液料分配),该方法可采用人工手动滴涂,也可采用机器自动滴涂。主要用于小批量多品种生产或新产品的研制,以及生产中补修或更换元器该方法速度慢、精度低,但灵活性好。
常用的印刷涂敷方式有非接触印刷和直接印刷两种类型。非接触印刷即丝网印刷,直接接触印刷即模板漏印(亦称漏板印刷),目前多采用直接接触印刷技术。这两种印刷技术可以采用同样的印刷设备,即丝网印刷机
漏印模板
?模板(stencils),又称为漏板、钢板,它是焊锡膏印刷的关键工具之一,用来定量分配焊锡膏。由于焊锡膏的印刷来源于丝网印刷技术,因此早期的焊锡膏印刷多采用丝网印刷,丝网材料有尼龙丝、真丝、聚酯丝和不锈钢丝等,可用于SMT焊锡膏印刷的是聚酯丝和不锈钢丝。用乳剂涂敷到丝网上,只留出印刷图形的开口网目,就制成了非接触式印刷涂敷法所用的丝网。但由于丝网制作的漏板窗口开口面积始终被丝本身占用一部分,即开口率达不到100%,不适合于焊锡膏印刷工艺,故很快被镂空的金属板所取代。
金属模板的结构
金属模板的结构如图所示,常见模板的外框是铸铝框架(或铝方管焊接而成),中心是金属模板,框架与模板之间依靠张紧的丝网相连接,呈“钢一柔一钢”的结构。这种结构可以确保金属模板既平整又有弹性,使用时能紧贴PCB表面。铸铝框架上备有安装孔供印刷机上装夹之用,通常钢板上的图形离钢板的外边约50mm,以供印刷机刮刀头运行所需要的空间,周边丝网的宽度约30~40mm。
焊锡膏印刷机
?焊锡膏印刷机的种类
?当前,用于印刷焊锡膏的印刷机品种繁多,若以自动化程度来分类,可以分为:手工印刷机、半自动印刷机、全自动印刷机。PCB放进和取出的方式有两种,一种是将整个刮刀机连同模板抬起,将PCB放进和取出,PCB定位精度取决于转动轴的精度,一般不太高,多见于手动印刷机与半自动印刷机;另一种是刮刀机构与模板不动,PCB平进与平出,模板与PCB垂直分离,故定位精度高,多见于全自动印刷机。
? (1)手动印刷机。手动印刷机的各种参数与动作均需人工调节与控制,通常仅被小批量生产或难度不高的产品使用。图示是手动焊锡膏印刷机的照片?(2) 半自动印刷机。半自动印刷除了PCB装夹过程是人工放置以外,其余动作机器可连续完成,但第一块PCB与模板的窗口位置是通过人工来对中的。通常PCB通过印刷机台面下的定位销来实现定位对中,因此PCB板面上应设有高精度的工艺孔,以供装夹用。图示是半自动焊锡膏印刷机的照片。
?(3) 全自动印刷机。全自动印刷机通常装有光学对中
?系统,通过对PCB和模板上对中标志(Mark/FIDUCIAL)
?的识别,可以自动实现模板窗口与PCB焊盘的自动对中,印刷机重复精度达±
0.01mm(6a)。在配有PCB自动装载系统后,能实现全自动运行。但印刷机的多种
工艺参数,如刮刀速度、刮刀压力、漏板与PCB之间的间隙仍需人工设定。图4-6
是两种不同型号自动焊锡膏印刷机的照片。
?锡膏印刷的整体过程分析
?焊膏运行过程概括起来分为五个步骤:
?1)定位
?2)填充
?3)挂平
?4)释放:将印好的焊膏由钢网口中转移到印制电路板焊盘上的过程,良好的释放可以保证得到良好的焊膏外形。
?5)擦网:印刷中用来在线擦洗钢网底部的装置。
?漏印模板印刷法的基本原理
?漏印模板印刷法的基本原理如下图所示。
?将PCB板放在工作支架上,由真空泵或机械方式固定,将已加工有印刷图形的漏印模板在金属框架上绷紧,模板与PCB表面接触,镂空图形网孔与PCB上
的焊盘对准,把焊锡膏放在漏印模板上,刮刀(亦称刮板)从模板的一端向另一端推进,同时压刮锡膏通过模板上的镂空图形网孔印刷(沉淀)到PCB的焊盘上。假如刮刀单向刮焊锡膏,沉积在焊盘上的焊锡膏可能会不够饱满;而刮刀双向刮焊锡膏,焊锡膏图形就比较饱满。高档的SMT印刷机一般有A、B两个刮刀:当刮刀从右向左移动时,刮刀A上升,刮刀B下降,B压刮焊锡膏;当刮刀从左向右移动时,刮刀B上升,刮刀A下降,A压刮焊锡膏,如图4-7a所示。两次刮焊锡膏后,PCB 与模板脱离(PCB下降或模板上升),如图4-7b所示,完成焊锡膏印刷过程。下图描述了简易SMT印刷机的操作过程。
印刷机的工艺参数
?焊锡膏是触变流体,具有黏性。当刮刀以一定速度和角度向前移动时,对焊锡膏产生一定的压力,推动焊锡膏在刮板前滚动,产生将焊锡膏注入网孔或漏孔所需的压力。焊锡膏的黏性摩擦力使焊锡膏在刮板与网板交接处产生切变,切变力使焊锡膏的黏性下降,有利于焊锡膏顺利地注入网孔或漏孔。刮刀速度、刮刀压力、刮刀与网板的角度以及焊锡膏的黏度之间都存在一定的制约关系,因此,只有正确地控制这些参数,才能保证焊锡膏的印刷质量
工艺参数的调节
? 1.刮刀的夹角
?刮刀的夹角影响到刮刀对焊锡膏垂直方向力的大小,夹角越小,其垂直方向的分力Fy越大,通过改变刮刀角度可以改变所产生的压力。刮刀角度如果大于800,则焊锡膏只能保持原状前进而不滚动,此时垂直方向的分力Fy几乎没有,焊锡膏便不会压入印刷模板窗开口。刮刀角度的最佳设定应在45~600范围内进行,此时焊锡膏有良好的滚动性
2.刮刀的速度
?刮刀速度快,焊锡膏所受的力也大。但提高刮刀速度,焊锡膏压入的时间将变短,如果刮刀速度过快,焊锡膏不能滚动而仅在印刷模板上滑动。考虑到焊锡膏压入窗口的实际情况,最大的印刷速度应保证FQFP焊盘焊锡膏印刷纵横方向均匀、饱满,通常当刮刀速度控制在20~40mm/s时,印刷效果较好。因为锡膏流进窗口需要时间,这一点在印刷细间距QFP图形时尤为明显,当刮刀沿QFP焊盘一侧运行时,垂直于刮刀的焊盘上焊锡膏图形比另一侧要饱满,故有的印刷机具有刮刀旋转450
的功能,以保证细间距QFP印刷时四面焊锡膏量均匀。
1芯片封装行业资料
半导体封测市场格局及IC封装知识 封装测试,半导体产业链得重要一环,今天,小编就为大家整理了一些相关厂商、市场格局,以及封装知识。本文主要包括以下3方面内容:国内半导体封测市场格局;国际封测巨头介绍;芯片封装知识 (一)目前,国内半导体封测市场主要由3家企业把持,它们是:长电科技,华天科技,通富微电。 因为晶圆产能争夺和价格上涨,国内封装测试的三大巨头企业正在暗中较力。自2016年三季度以来,以DRAM和NAND Flash为代表的存储芯片价格上涨开启了芯片产品的涨价潮,作为芯片制造的原材料晶圆于今年2月份迎来其制造厂商的第一次提价。2017年2月11日,全球晶圆代工龙头企业台积电在其股东大会上确认半导体晶圆产能供应紧张,将开始涨价。2017年1季度全球半导体晶圆合约价平均涨幅约达10%,市场预计涨价行情将贯穿全年,晶圆产品价格可望逐季调涨5%至10%。7月,半导体行业将迎来传统旺季,多家上游芯片设计公司早在6月初就已提前下单预定晶圆产能,这直接导致诸多晶圆代工厂开始规划2017年第三季度的产能布局,产业链传出的信息显示,无论是8寸晶圆产能还是12寸晶圆产能均出现第三季度产能排程全满,生产周期由过去的8至10周直接延长至12周以上的情况,而且产业相关人士还预计两类晶圆的产能利用率均会一直排满到年底。实际上,早在2016年,晶圆下游的多家美股半导体设备公司业绩就创下多年新高,随之而来的是当年整个美股半导体板块涌现出多只涨幅惊人的股票,如英伟达、应用材料以及美光科技等。而且2016-2017年之间,全球确定新建的19座晶圆厂有10家落户中国大陆,叠加上本土IC 设计公司的高速增长,配套封测需求上升已经成为铁板钉钉的事情。作为目前国内封装测试的三大巨头企业,长电科技、华天科技以及通富微电的业绩非常有希望因此轮晶圆产能争夺和价格上涨而迎来爆发,那么三家企业中究竟谁最受益? 华天科技领先:由于半导体封测行业属于劳动密集型产业,本身利润率水平就不高,因此在技术差别不大的情况下,生产规模及成本管控决定了行业内公司的竞争力(2016年长电科技和通富微电完成并购并且后续整合完成之前,三家公司的封测技术差别不大)。 从营收规模增速来看,过去五年长电科技的年均复合增长率最高,达到38.48%,华天科技以33.13%紧随其后,而相比于前两者,通富微电增速较低,为23.14%。不过,三家公司中,华天科技2012-2016五年间的同比增速最为稳定,除了2015年略低之外,其余年份均在24%以上,波动程度最小;而另外两家公司近两年通过外延并购,其营业收入增速较并购之前年份发生了较大的变化。而从反应公司盈利能力的销售净利率指标来看,华天科技遥遥领先另外两家公司:华天科技近5年销售净利率均保持在7.50%以上;通富微电仅有2015年的销售净利率在6%以上,而长电科技更为惨淡,仅有2014年的销售净利率在1%以上,2015年以及2016年更是为负。究其原因,主要还是成本管控的差距。营业收入规模排名第二的华天科技的成本管控能力非常出色,近5年营业成本(非营业总成本,营业总成本还包括营业税金及附加、销售费用、管理费用和财务费用等)占营业收入的比例仅有2015年未能实现最低,其余年份均为三家企业中最低。反观营收规模最大的长电科技,其成本管控水平较为糟糕,营业成本占营业收入比例基本位于80%以上,仅有2014年低于该水平,为78.87%;营收规模第三的通富微电与长电科技类似,只有2015年营业成本占营业收入比例低于80%,为78.20%。除了营业成本之外,相比于地处江苏的长电科技以及通富微电,华天科技主要生产基地位于甘肃天水和西安,人工成本成为公司相对于东部厂商的最大优势。这一点从公司近5年的职工薪酬(不包括销售费用中的职工薪酬)占整个营业收入的比例中也能看出来。另外,三家公司在管理水平上的差距也影响了各自的净利率水平。在这点上,
晶圆级封装产业
晶圆级封装产业(WLP) 晶圆级封装产业(WLP),晶圆级封装产业(WLP)是什么意思 一、晶圆级封装(Wafer Level Packaging)简介晶圆级封装(WLP,Wafer Level Package) 的一般定义为直接在晶圆上进行大多数或是全部的封装测试程序,之后再进行切割(singulation)制成单颗组件。而重新分配(redistribution)与凸块(bumping)技术为其I/O绕线的一般选择。WLP 一、晶圆级封装(Wafer Level Packaging)简介 晶圆级封装(WLP,Wafer Level Package) 的一般定义为直接在晶圆上进行大多数或是全部的封装测试程序,之后再进行切割(singulation)制成单颗组件。而重新分配(redistribution)与凸块(bumping)技术为其I/O绕线的一般选择。WLP封装具有较小封装尺寸(CSP)与较佳电性表现的优势,目前多用于低脚数消费性IC的封装应用(轻薄短小)。 晶圆级封装(WLP)简介 常见的WLP封装绕线方式如下:1. Redistribution (Thin film), 2. Encapsulated Glass substrate, 3. Gold stud/Copper post, 4. Flex Tape等。此外,传统的WLP封装多采用Fan-in 型态,但是伴随IC信号输出pin 数目增加,对ball pitch的要求趋于严格,加上部分组件对于封装后尺寸以及信号输出脚位位置的调整需求,因此变化衍生出Fan-out 与Fan-in + Fan-out 等各式新型WLP封装型态,其制程概念甚至跳脱传统WLP 封装,目前德商英飞凌与台商育霈均已经发展相关技术。 二、WLP的主要应用领域 整体而言,WLP的主要应用范围为Analog IC(累比IC)、PA/RF(手机放大器与前端模块)与CIS(CMOS Ima ge Sensor)等各式半导体产品,其需求主要来自于可携式产品(iPod, iPhone)对轻薄短小的特性需求,而部分NOR Flash/SRAM也采用WLP封装。此外,基于电气性能考虑,DDR III考虑采用WLP或FC封装,惟目前JEDEC仍未制定最终规格(注:至目前为止,Hynix, Samsung与Elpida已发表DDR III产品仍采F BGA封装),至于SiP应用则属于长期发展目标。此外,采用塑料封装型态(如PBGA)因其molding compo und 会对MEMS组件的可动部份与光学传感器(optical sensors)造成损害,因此MEMS组件也多采用WLP
matlab封装模块
在simulink中建立子模块的步骤如下: 1、建立系统框图。这步需要确定输入输出的个数,输入端为sources中的in,输出端为sinks中的out。将Simulink库下的Ports&Subsystems中的Subsystem拉至simulink框图中。 2、功能的搭建。点击建好的子模块,在其中进行功能模块的搭建。 3、子模块的封装。所谓封装(masking),即将其对应的子系统内部结构隐含以来,访问该模块的时候仅仅出现一个参数设置对话框。需要如下几步完成: 3.1、右击模块,选择Mask Subsystem选项,蹦出Mask Editor对话框。 3.2、Icon属性。如果要显示端口的名称,Transparency属性设置成Transparent。Drawing commands编辑框允许给该模块图标上绘制图像,可以选择的有plot()、disp()等等,比如disp('PID Controller')。在Drawing commands中输入语句,如何写函数的提示在封装编辑对话框的下方。 3.3、Parameters属性。这个东西是给模块中的变量赋值的,选择左方有朝左的小箭头的按钮是添加变量的,这时右方会有一横栏,Prompt是该变量的提示信息,Variable是相关联的变量名称,一定要与模块中的变量名称一样,Type是变量的类型,edit(可编辑)、popup(下拉框),选择后者的时候需要在左下方的popups中分行写上可以选择的数值。左方的叉按钮是删除变量的。 3.4、Initialization属性。对模块进行初始化操作。 3.5、Documentation属性。对模块进行说明。封装后双击模块就可以看见Mask Description中的内容。 关于模块封装的一些操作还有: (1)如果要观察模块的内部结构,右键模块,然后选择Look Under Mask即可。编辑模块封装选择Edit
IC封装ERP
用友软件股份有限公司
目录 一、半导体封装行业综述 (2) 1.1行业基本情况 (2) 1.2行业发展趋势 (2) 二、半导体封装行业业务特点 (4) 2.1行业主要特征 (4) 2.2行业管理特点 (6) 2.3行业业务流程 (8) 2.4行业管理困扰 (11) 三、半导体封装行业关键需求 (14) 3.1计划控制 (15) 3.2车间管理 (15) 3.3物料管理 (16) 3.4采购管理 (17) 3.5销售管理 (18) 3.6成本核算 (18) 3.7品质管理 (18) 四、半导体封装行业解决方案 (20) 4.1总体解决方案流程图 (20) 4.2基础数据管理 (21) 4.3销售及收款流程 (23) 4.4计划管理流程 (26) 4.5采购及付款流程 (30) 4.6生产任务作业流程 (33) 4.7委外加工作业流程 (36) 4.8车间作业流程 (40) 4.9仓储作业流程 (43) 五、解决方案价值 (47) 六、UFIDA半导体封装行业典型用户列表 (47)
一、半导体封装行业综述 1.1 行业基本情况 自国务院2000年颁布《鼓励软件产业和集成电路产业发展的若干政策》文件以来,半导体产业即进入一个高速成长期,自2000年到2006年的6年间,国内集成电路产量和销售收入的年均增长速度超过27%,是同期全球最高的。中国集成电路产业的快速发展离不开封装行业的带动。2000年到2006年,国内半导体封装行业销售收入由134亿元扩大到496亿元。到2006年底,国内集成电路封装企业已经超过200家,年封装能力达到355.6亿块。2006年我国集成电路封装测试行业销售额同比增长44%,在产业链中的比重达到50.8%,是近几年增长最快的一年,赛迪顾问调查报告显示,2006年我国集成电路产业发展中最大的亮点当属封装测试行业的加速发展。封装测试行业在近几年一直呈现稳定增长的势头,进入2006年之后,出口需求大幅增长,现有企业大幅扩产,同时数个大型新建项目建成投产。在这些因素带动下,我国内地封装测试行业呈现加速发展的势头。其规模已接近500亿元。 从封装技术角度来看,半导体封装行业可划分为: 低端分立器件封装测试行业(TO/SO/DIP) 典型产品:二极管、三极管、单片开关电源、中小规模集成电路等中高端分立器件封装测试行业(QFP/ BGA/LCC/PGA) 典型产品:大规模集成电路 半导体封装行业已形成地区区域性集约化大生产。这主要体现在以上海为中心的长三角地区,以北京为中心的京津环渤海湾地区和以广州为中心的珠三角地区。其中尤以长三角地区为半导体封装行业的主要基地。在国内知名的有江苏省的长电科技、华润安盛科技、中电集团第58所、东芝公司、东光公司、富士通公司、三星、瑞萨科技、飞索、矽品等公司,上海市的金朋公司、安靠公司、纪元公司、新进公司、松下公司、宏茂、威宇、桐辰、捷敏、华旭、宏盛、双领和英特尔等公司。珠三角地区的知名公司有珠海南科、深圳深爱、深圳沛顿科技、深圳赛意法、佛山蓝箭、粤晶高科、东莞乐依文等公司。 1.2 行业发展趋势 虽然我国内地封装测试产业近年来取得了长足的发展,但整体来讲技术水平仍然相对落后。就封装形式来讲,我国内地市场目前的主要需求仍在DIP、SOP(SSOP、TSOP)、QFP(LQFP、TQFP)等中低端产品上。 由于低端分立器件市场的进入门槛并不高,所以将会有更多的我国内地企业加入该低端市场,竞争将日益激烈。在中高端分立功率器件的应用领域,能够满足高端客户需求,生产出高可靠性分立器件的厂商并不是很多,而这些核心技术大多为国际巨头所掌握,正是由于核心技术缺失制约,
芯片封装工艺及设备
《微电子封装技术》复习提纲 第一章绪论 ●微电子封装技术的发展特点是什么?发展趋势怎样?(P8、P9) 特点:微电子封装向高密度和高I/O引脚数发展,引脚由四边引出向面阵排列发展微电子封装向表面安装式封装(SMP)发展,以适合表面安装技术(SMT) 从陶瓷封装向塑料封装发展 从注重发展IC芯片向先发展后道封装再发展芯片转移 发展趋势:微电子封装具有的I/O引脚数更多 微电子封装应具有更高的电性能和热性能 微电子封装将更轻,更薄,更小 微电子封装将便于安装、使用和返修 微电子安装的可靠性会更高 微电子封装的性能价格比会更高,而成本却更低,达到物美价廉 ●微电子封装可以分为哪三个层次(级别)?并简单说明其内容。(P7) 用封装外壳将芯片封装成单芯片组件和多芯片组件的一级封装,将一级封装和其他元器件一同组装到印刷电路板上的二级封装以及再将二级封装插装到母版上的三级封装硅圆片和芯片虽然不作为一个封装层次,但却是微电子封装的出发点和核心。在IC芯片与各级封装之间,必须通过互连技术将IC芯片焊区与各级封装的焊区连接起来形成功能,也有的将这种芯片互连级称为芯片的零级封装 ●微电子封装有哪些功能?(P19) 电源分配、信号分配、散热通道、机械支撑、环境保护 ●芯片粘接方法分为哪几类?粘接的介质有何不同(成分)?(P12) Au-Si合金共熔法(共晶型) Pb-Sn合金片焊接法(点锡型) 导电胶粘接法(点浆型);环氧树脂 有机树脂基粘接法(点胶型);高分子化合物 ●简述共晶型芯片固晶机(粘片机)主要组成部分及其功能。 1 机械传动系统 2 运动控制系统 3 图像识别(PR)系统 4 气动/真空系统 5 温控系统 机械系统 ?目标:芯片+框架 ?组成部分: ? 1 框架供送部分进料(框架分离)、送料、出料 ? 2 芯片供送部分 ?目标:
我国封装业正从低端向中高端迈进
我国封装业正从低端向中高端迈进 我国IC 封装业一直是IC 产业链中的第一支柱产业。据赛迪顾问统计,2007 年国内集成电路封装测试业共实现销售收入627.7 亿元,同比增长 26.4%,继续保持了快速发展势头。目前国内封装企业如长电科技、南通富士通、天水华天、华润安盛公司近年来封测规模正在迎头赶上,产品档次也由低 端向中高端发展。长电科技的封装水平已与国际先进水平接轨。这些发展可以 说都离不开创新,贴近市场的创新技术直接带动了企业的快速健康发展。 随着IC 器件尺寸不断缩小和运算速度的不断提高,封装技术已成为极 为关键的技术。封装形式的优劣已影响到IC 器件的频率、功耗、复杂性、可 靠性和单位成本。据天水华天科技股份有限公司总工程师郭小伟介绍,目前封 装的热点技术为高功率发光器件封装技术、低成本高效率图像芯片封装技术、 芯片凸点和倒装技术、高可靠低成本封装技术、BGA 等基板封装技术、MCM 多芯片组件封装技术、四边无引脚封装技术、CSP 封装技术、SIP 封装技术等。郭小伟认为,未来集成电路技术,无论是其特征尺寸、芯片面积和芯片包含的晶体管数,还是其发展轨迹和IC 封装,发展主流都是:芯片规模越来越大,面 积迅速减小;封装体积越来越小,功能越来越强;厚度变薄,引线间距不断缩小,引线也越来越多,并从两侧引脚到四周引脚,再到底面引脚;封装成本越来越低,封装的性能和可靠性越来越高,单位封装体积、面积上的IC 密度越来高,线 宽越来越细,并由单芯片封装向多芯片封装方向发展。 集成电路封装的发展,一直是伴随着封装芯片的功能和元件数的增加而 呈递进式发展。封装技术已经经历了多次变迁,从DIP、SOP、QFP、MLF、MCM、BGA 到CSP、SIP,技术指标越来越先进。其中三维叠层封装(3D 封装)
windows10系统封装过程的详解
windows10系统封装过程的详解 首先说说windows10最新版的安装母盘过程,封装是为了更好的备份是恢复系统: 1、安装母盘。 安装系统前,删掉所有分区,以系统本身的光盘镜像启动,在安装过程中分区,分区多出来一个500M的小分区,有的是100M的分区,这个小分区一定要删掉,要不安装系统的时候,部分启动文件和引导文件会被安装到这个小分区里,会造成装系统后,不能引导启动的问题,不建议PE下安装母盘,要不容易出现分区排序错乱的情况。 安装系统过程中选测:【加入域】,其他方面没什么设置要求。 2、删除目前登录用户,设置管理员方式登录。 安装完母盘后,为访客登录方式,没有太多的权限,那就要登录管理员的登录,此时,右键开始菜--计算机管理--本地用户和组---双击:用户,再双击右面框里的【administrator】,将【账户已禁用】前面的勾去掉。点击确定退出对话框。再点击开始--注销--再用【administrator】用户登录。 进系统后,右键开始---打开【控制面板】--用户账户--删除用户账户--删除除管理员以外的用户账户--删除文件,确定退出。
3、激活系统。 激活系统后才能进行系统设置,否则某些设置项将无法设置。 4、启用管理员批准模式 开始--运行,输入:gpedit.msc回车,双击本地计算机策略的【windows 设置】--安全设置--本地策略--安全选项--双击【用户账户控制:用于内置管理员账户的管理员批准模式】,点击启用。 5、给系统瘦身一次。 这样可以在优化和设置的时候,时不时看看C盘实际占用的大小。 6、虚拟内存转移到D盘。关闭磁盘保护。 7、右键C盘,点击清理磁盘,删掉没有用的东西。顺便删除还原点。和没用的程序。 8、开启管理员权限。 先运行【获取管理员权限】和右键【以管理员权限运行】的注册表文件。 9、关闭电源休眠,节约体积。 右键开始菜单,右键打开管理员模式的命令提示符,运行:powercfg -h off
国内主要封装企业封装形式介绍
国内主要封装企业封装形式介绍 国内主要独资封装企业概况 企业名称主要封装形式 飞思卡尔MAP BGA81 TAB SO1C28 PDIP 三星电子(苏州)QFP48-100S098-16 TO-220 1-PAK D-PAK 日立半导体(苏州)SOP SOT TSOP53 飞索半导体(AMD)PLCC44-64 苏州双胜DIP6-40 TO-220 TO-251/252 TO-925 SOT23 英特尔(上海)FCBGA TSOP WBGA SCSP VFBGA 金朋芯封(上海)PDIP PLCC SOIC SSOP TSSOP BGA/CSP 上海宏盛TSOP BGA CSP 安靠(上海)LQFP CABGA FLEXBGA SIP TSOP PLCC MLF CLBGA BGA 勤益(上海)SOT-23 25 26 89 223 25 252 220 263 SOP-8 桐辰(上海)TSOP PQFP PBGA MIC20 BGA sfackBGA PLCC 威宇(上海)PBGA TFBGA QFN SIP QFP 捷敏(上海)DPAK SOIC8 TSSOP8 GEM2021J TSOP6TSOP5 GEM2928J 国内主要合资封装企业概况 企业名称主要封装形式 南通富士通DIP SIP SOP QFP SSOP TSOP TQEP LCC MCM 首钢NEC SSIP SOP SSOP DIP SDIP SOT QFP TSOP 上海纪元微科PDIP PLCC TSSOP SOIC MSOP TSOP TO220 SOT23 无锡华芝SDIP24 54 56 QFP48 上海华旭DIP8 14 16 18 20 22 24 28 36 40PIN SOP8 14 16 20 28PIN QFP44 56PIN PLCC68PIN SIP9 10 DIP14 宁波明昕TO-92 TO-126 TO-220 TO-251 上海新康SOIC-8系列TSOP-6 PPAK SUPAK SOT 乐山-菲尼克斯SOIC TO-220 SC59 SOD3 SOT等 深爱半导体TO-92 TO-126 TO-220 TO-3P TO-3 三菱四通MCU MSIG SCR-LM 万立电子(无锡公司)TO-202 TO-220 TO-126A TO-126B TO-3PL TO-3 F2 上海松下NL-95 FS-16S QFS-80 TOP-3E TO-220E QFP-84 LQFP SDIL-42 USOF-26 E-3S LQFP-80 SDIL-64 深圳赛意法DIP8-16 SOP8 DQPAK TO-220 BGA 无锡开益禧TO-92 220 126 3PN 3PH 92M SOT-23 上海永华TO-92 TO-251 220 3P 国内部分封装厂家概况 企业名称主要封装型式 江苏长电HSOP SDIP HSIP SSOP FSIP FDIP DIP QFP PLCC LQFP PQF
先进微电子封装工艺技术
先进微电子封装工艺技术培训 培训目的: 1、详细分析集成电路封装产业发展趋势; 2、整合工程师把握最先进的IC封装工艺技术; 3、详细讲述微电子封装工艺流程及先进封装形式; 4、讲述微电子封装可靠性测试技术; 5、微电子封装与制造企业以及设计公司的关系; 6、实际案例分析。 参加对象: 1、大中专院校微电子专业教师、研究生;; 2、集成电路制造企业工程师,整机制造企业工程师; 3、微电子封装测试、失效分析、质量控制、相关软件研发、市场销售人员; 4、微电子封装工艺设计、制程和研发人员; 5、微电子封装材料和设备销售工程师及其应用的所有人员; 6、微电子封装科研机构和电子信息园区等从业人员 【主办单位】中国电子标准协会培训中心 【协办单位】深圳市威硕企业管理咨询有限公司 课程提纲(内容): Flip Chip Technology and Low Cost Bumping Method l What is Flip Chip l Why Use Flip Chip
l Flip Chip Trend l Flip Chip Boding Technology l Why Underfill l No Flow Underfill l Other Key Issues Wafer Level Packaging l What is IC packaging? l Trend of IC packaging l Definition and Classification of CSP l What is wafer level packaging? l Overview Technology Options —Wafer level High Density Interconnections —Wafer level Integration —Wafer Level towards 3D l WLP toward 3D l Wafer level Challenges l Conclusion 讲师简介: 罗乐(Le Luo)教授 罗教授1982年于南京大学获物理学学士学位,1988年于中科院上海微系统与信息技术研究所获工学博士学位。1990年在超导研究中取得重大突破被破格晋升为副研究员,1991—199
(最新整理)功率模块封装结构及其技术
(完整)功率模块封装结构及其技术 编辑整理: 尊敬的读者朋友们: 这里是精品文档编辑中心,本文档内容是由我和我的同事精心编辑整理后发布的,发布之前我们对文中内容进行仔细校对,但是难免会有疏漏的地方,但是任然希望((完整)功率模块封装结构及其技术)的内容能够给您的工作和学习带来便利。同时也真诚的希望收到您的建议和反馈,这将是我们进步的源泉,前进的动力。 本文可编辑可修改,如果觉得对您有帮助请收藏以便随时查阅,最后祝您生活愉快业绩进步,以下为(完整)功率模块封装结构及其技术的全部内容。
功率模块封装结构及其技术 摘要:本文从封装角度评估功率电子系统集成的重要性。文中概述了多种功率模块的封装结构形式及主要研发内容。另外还讨论了模块封装技术的一些新进展以及在功率电子系统集成中的地位和作用。 1 引言 功率(电源或电力)半导体器件现有两大集成系列,其一是单片功率或高压集成电路,英文缩略语为PIC或HIVC,电流、电压分别小于10A、700V的智能功率器件/电路采用单片集成的产品日益增多,但受功率高压大电流器件结构及制作工艺的特殊性,弹片集成的功率/高压电路产品能够处理的功率尚不足够大,一般适用于数十瓦的电子电路的集成;另一类是将功率器件、控制电路、驱动电路、接口电路、保护电路等芯片封装一体化,内部引线键合互连形成部分或完整功能的功率模块或系统功率集成,其结构包括多芯片混合IC封装以及智能功率模块IPM、功率电子模块PEBb、集成功率电子模块等。功率模块以为电子、功率电子、封装等技术为基础,按照最优化电路拓扑与系统结构原则,形成可以组合和更换的标准单元,解决模块的封装结构、模块内部芯片及其与基板的互连方式、各类封装(导热、填充、绝缘)的选择、植被的工艺流程的国内许多问题,使系统中各种元器件之间互连所产生的不利寄生参数少到最小,功率点楼的热量更易于向外散发,其间更能耐受环境应力的冲击,具有更大的电流承载能力,产品的整体性能、可能性、功率密度得到提高,满足功率管理、电源管理、功率控制系统应用的需求。 2 功率模块封装结构 功率模块的封装外形各式各样,新的封装形式日新月异,一般按管芯或芯片的组装工艺及安装固定方法的不同,主要分为压接结构、焊接结构、直接敷铜DBC基板结构,所采用的封装形式多为平面型以及,存在难以将功率芯片、控制芯片等多个不同工艺芯片平面型安装在同一基板上的问题。为开发高性能的产品,以混合IC封装技术为基础的多芯片模块MCM封装成为目前主流发展趋势,即重视工艺技术研究,更关注产品类型开发,不仅可将几个各类芯片安装在同一基板上,而且采用埋置、有源基板、叠层、嵌入式封装,在三维空间内将多个不同工艺的芯片互连,构成完整功能的模块. 压接式结构延用平板型或螺栓型封装的管芯压接互连技术,点接触靠内外部施加压力实现,解决热疲劳稳定性问题,可制作大电流、高集成度的功率模块,但对管芯、压块、底板等零部件平整度要求很高,否则不仅将增大模块的接触热阻,而且会损伤芯片,严重时芯片会撕裂,结构复杂、成本高、比较笨重,多用于晶闸管功率模块。焊接结构采用引线键合技术为主导的互连工艺,包括焊料凸点互连、金属柱互连平行板方式、凹陷阵列互连、沉积金属膜互连等技术,解决寄生参数、散热、可靠性问题,目前已提出多种实用技术方案。例如,合理结构和电路设计二次组装已封装元器件构成模块;或者功率电路采用芯片,控制、驱动电路采用已封装器件,构成高性能模块;多芯片组件构成功率智能模块。 DBC基板结构便于将微电子控制芯片与高压大电流执行芯片密封在同一模块之中,可缩短或减少内部引线,具备更好的热疲劳稳定性和很高的封装集成度,DBC通道、整体引脚技术的应用有助于MCM的封装,整体引脚无需额外进行引脚焊接,基板上有更大的有效面积、更高的载流能力,整体引脚可在基板的所有四边实现,成为MCM功率半导体器件封装的重要手段,并为模块智能化创造了工艺条件.
电子封装专用设备
电子封装专用设备 第一部分 1.半导体制造主要工艺流程与设备概述。 图1 半导体制造、封装、测试工艺流程 图2 芯片制造基本工艺流程图
半导体制造工艺是由多种单项工艺组合而成的,主要包括以下四类:薄膜形成工艺;图形转移工艺;掺杂工艺;热处理工艺。 ⑴薄膜形成工艺与设备 薄膜工艺包括氧化工艺和薄膜淀积工艺。通过生长或淀积的方法,生成集成电路制造过程中所需的各种材料的薄膜,如金属层、绝缘层等。 氧化(Oxidation)工艺的主要目的是在硅衬底表面形成氧化膜SiO2。 在硅衬底表面形成SiO2氧化膜的方法:化学气相淀积(CVD)和氧化。其中氧化又分为自然氧化(在常温下,硅表面可生长出SiO2氧化层,厚约2nm)和热氧化(Thermal Oxidation)(在高温炉中反应,形成较厚的SiO2氧化层,也称为热生长法) 热氧化法的3种环境:①干氧氧化(O2) ②水蒸气氧化(H2O) ③湿氧氧化(H2O+O2) 图3 热氧化生成二氧化硅设备原理示意图氧化炉主要有高温干式氧化炉和高温湿式氧化炉两种,基本原理
如上图所示。 化学气相淀积(CVD, Chemical Vapor Deposition)是利用气态的先驱反应物,以某种方式激活后,通过原子或分子间化学反应的途径在衬底上淀积生成固态薄膜的技术。利用CVD可获得高纯的晶态或非晶态的金属、半导体、化合物薄膜,能有效控制薄膜化学成分,且设备运转成本低,与其他相关工艺有较好的相容性。CVD技术已有100多年历史,应用领域很广,如轴承的耐磨涂层、核反应堆里的耐高温涂层。 CVD工艺采用的设备为CVD反应炉,有卧式反应炉立式反应炉。 (PECVD)其中PECVD是通过高能射频源获得的等离子体提供能量,
封装材料行业基本概况
封装材料行业研究报告 研究员:高鸿飞一、行业定义 根据国民经济行业分类《国民经济行业分类GB/T 4754-2011》),引线框架和LED支架制造业属于为计算机、通信和其他电子设备制造业(行业代码:C39);根据中国证监会行业分类(《上市公司行业分类指引》),引线框架和LED支架制造业属于计算机、通信和其他电子设备制造业C396。 二、行业的监管体制 引线框架和LED支架制造业所属的行业主管部门是国家发展改革委员会、中国环境保护部及中国工业和信息化部。国家发改委主要负责本行业发展政策的制定;中国环境保护部负责环境污染防治的监督管理,制定环境污染防治管理制度、标准和技术规范并组织实施;中国工业和信息化部负责制定我国电子元器件行业的产业规划和产业政策,对行业的发展方向进行宏观调控。 引线框架和LED支架制造业的行业自律性组织是中国电子材料行业协会(以下简称“行业协会”),该协会是由从事电子材料生产、研制、开发、经营、应用、教学的单位及其他相关企、事业单位自愿结合组成的全国性的行业社会团体,为政府对电子材料行业实施行业管理提供帮助,同时也是政府部门和企业单位之间的桥梁纽带。行业协会主要在电子材料行业自律、技术培训、信息交流、国内外交流与合作等方面广泛开展工作,为行业的进步和发展起到了促进作用。行业协会下设集成电路分会、半导体分立器件分会、半导体封装分会、集成电路设计分会和半导体支撑业分会等5个分会。 三、封装材料行业基本概况 (1)引线框架概念及应用领域 引线框架是一种用来作为芯片载体的专用材料,借助于键合丝使芯片内部电
路引出端(键合点)通过内引线实现与外引线的电气连接,形成电气回路的关键结构件。在半导体中,引线框架主要起稳固芯片、传导信号、传输热量的作用,需要在强度、弯曲、导电性、导热性、耐热性、热匹配、耐腐蚀、步进性、共面形、应力释放等方面达到较高的标准。 (2)LED支架概念及应用领域 LED是“Light Emitting Diode”的缩写,中文译为“发光二极管”,是一种可以将电能转化为光能的半导体器件,不同材料的芯片可以发出红、橙、黄、绿、蓝、紫色等不同颜色的光。LED的核心是由p型半导体和n型半导体组成的芯片,而LED支架就是芯片的承载物,担负着机械保护,提高可靠性;加强散热,降低芯片结温、提高LED性能;光学控制,提高出光效率,优化光束分布;供电管理,包括交流/直流转变、电源控制等作用。 (3)半导体封装材料产业链结构 ①引线框架产业链结构 引线框架的上游行业主要是铜合金带加工企业和生产氰化银钾的化工企业,由于铜基材料具有导电、导热性能好,价格低以及和环氧模塑料密着性能好等优势,当前已成为主要的引线框架材料,其用量占引线框架材料的80%以上。 公司引线框架产业的下游行业是集成电路和分立器件封装测试行业。一般的封装工艺流程为:划片→装片→键合→塑封→去飞边→电镀→打印→切筋和成型→外观检查→成品测试→包装出货。引线框架主要是在装片步骤中,作为切割好晶片的基板,是封装过程中所需的重要基础材料。 公司引线框架产业处于产业链中游,随着电子信息技术的高速发展,对集成电路的性能要求越来越多样化,对集成电路封装测试行业的要求也越来越高。公司将会充分发挥创新优势,致力于研发多样化和高性能的引线框架。 ②LED支架产业链结构 LED支架的主要原材料为铜合金带、氰化银钾和PPA,铜合金带属于金属加工产品,氰化银钾属于化工产品,而PPA则是塑料制品,因此,公司的上游产业主要是金属加工企业、化工企业和塑料制品企业。 LED支架主要应用在电子和照明领域,主要产品有汽车信号灯、照明灯、家用电器、户外大型显示屏、仪器仪表等光电产品。LED支架主要是作为LED
matlab如何封装模块
Simulink模块制作过程大体可以分为两步:s函数的编写和模块封装。 S函数(system function)是模块的核心,是完成功能实现的关键。S函数的编写可以使用多种程序语言,其中M语言是最常用的,同时也是最简单的。在运用M语言进行s函数编写的时候,可以调用MATLAB提供的函数,简化了开发过程。但是如果要与其他进程通讯或驱动外部硬件接口,则要调用API函数,这样就需要用C语言来开发S函数。较M语言的开发,C语言开发S函数更具有灵活性,但是相对复杂一些。 下面讲解C语言S函数的开发方法: C语言写S函数,顾名思义,运用C语言语法,依照S函数格式要求,最后在MATLAB中MEX命令编译,编译成功既得函数。 S函数格式可简单看成:初始化、采样时间设定、系统输出、结束四个部分。对应的函数分别为mdlInitializeSizes()、mdlInitializeSampleTimes()、mdlOutputs()、mdlTerminate()。这四个函数是一个S函数必不可少的,缺少任何一个在编译的时候都无法通过,输出信息会提示哪个函数没有写。 一个最基本的C语言S函数模版如下: #define S_FUNCTION_NAME name #define S_FUNCTION_LEVEL 2 #include “simstruc.h” Static void mdlInitializeSizes(SimStruct *S){} Static void mdlInitializeSampleTimes(SimStruct *S){} Static void mdlOutputs(SimStruct *S,int_T tid){} Static void mdlTerminate(SimStruct *S){} #ifdef MATLAB_MEX_FILE #include “Simulink.c” #else #include “cg_sfun.h” #endif S函数的运行依托于Simulink,Simulink的运行是采用循环方式,计算各采样时间点的系统状态得到的,由此可理解S函数,在初始化之后,S函数也通过循环完成输出状态计算。 结合上述格式,首先自定义S函数名称,然后定义S函数级别,这里写2,1级是老版本Simulink使用的,现已经不是用,之所以保留1级是为了兼容原有的老程序,现在写的S函数都是2级的。接下来将需要的头文件包含进来,这里必须包含simstruc.h文件,这里的SimStruc是Simulink提供的数据结构,S函数中的输入输出等信息都包含在这个结构体中,同时,在编写S函数的时候也要把使用到的C语言库中的头文件包含进来,所有的C语言库文件在这里都可以使用。接下来即可按照格式顺序编写代码。最后要注意,如果用于仿真则添加Simulink.c 文件,如果用于RTW代码生成,则添加cg_sfun.h头文件。这里的RTW代码生成是指非内嵌的S函数,如果要做一个内嵌的S函数则需要在S函数中添加mdlRTW()函数,并额外编写TLC文件。其中,TLC文件用于优化的C代码生成,mdlRTW()函数则把模块参数传递到生成的代码当中。具体TLC文件的编写方法这里不再赘述。 除了上述必需的函数外,系统提供了其他可选用的函数,功能各异,例如mdlStart()等。
IC封装设备切片机电控系统设计
IC封装设备切片机电控系统设计 宋佳丽 (长春税务学院计算机系 吉林 长春 130117) 摘要:为了高速、高精度切割半导体晶片,切片机的电控系统要求具备高精度及高稳定度。根据系统设计指标和可编程控制器(PLC)的特点,选用日本OMRON公司的CS1G型PLC构成主控系统,FC10/400型高速电机及其配套变频器构成高速主轴系统,Y、Z轴则用PD-0535M型步进电机驱动器驱动步进电机构成开环控制系统,X轴采用交流伺服电机及增量式编码器构成半闭环系统,θ轴选用美国Parker公司DM1004B 型转台交流伺服电机及DrvMⅡ型电机驱动器,供电系统采用隔离变压器等方法来屏蔽电磁干扰。通过多模块运动控制软件协调控制,该系统完全达到了设计要求。 关键词:运动控制;可编程序控制器;集成电路封装;切片机 中图分类号:TP273+.5 文献标识码:B Control system design of wafer incision device for IC encapsulation SONG Jia-li (Changchun College of Taxation, Changchun 130117, P. R. China) Abstract: To incise apace and precisely semiconductor wafer, control system of wafer incision machine must be also high-accuracy and high-stability. Based on design demand and characteristic of programmable logic controller (PLC), a CS1G PLC of OMRON Corporation is selected for main system. A FC10/400 high speed motor and its frequency-converter is selected for high speed rotation system, a PD-0535M stepper motor driver is selected for Y and Z axis, and a AC servo motor is half closed looped by an incremental encoder for X axis. For θaxis, a DM1004B AC servo motor and a DrvMⅡ driver of American Parker Corporation are selected, and the electromagnetic interference of current supply system is shielded by a separate voltage changer. The system’ kinetic control software is design by means of multiple modular programming. So the system attained design demand quite. Key words: Kinetic control; PLC; IC encapsulation; wafer incision device 1引 言 IC封装是半导体三大产业之一,其后封装工序主要包括:切片、粘片、金丝球焊、塑封、检测及包装[1]。切片IC后封装中的第一道工序,其加工质量将直接影响整个生产线的产品质量。作为半导体后封装线上的第一道关键设备,切片机的作用是把制作好的晶片(矩形或棱形)切割成独立单元器件,为下一步单元晶片粘接作好准备[2][3]。 为了完成对3—6英寸的晶片的切割,切片机要高速、高精度完成一系列运动步骤,将整个晶片切割成许多的矩形或多边形单元晶片。因此,切片机的电控系统必须是一套高精度、高稳定度电控系统。 2电控系统设计 2.1总体结构及功能要求 切片机总体结构如图1所示,工件台采用真空吸附方式固定晶片,与θ轴一体安放在X轴运动导轨台上,X轴导轨带动工件台做往复运动。带动划片刀高速旋转的气浮主轴安放在Y导轨上,依单元晶片的尺寸大小随同Y导轨做进给切割运动。Z轴座在Y轴导轨上,随同Y轴运动,Z轴以杠杆结构方式带动高速主轴上下运动实现划片过程中的抬刀落刀功能,杠杆的一端为高速主轴,另一端为Z轴系统。 根据晶片加工质量要求,切片机必须实现下列主要指标及功能:
功率模块封装工艺
功率模块封装工艺 摘要:本文从封装角度评估功率电子系统集成的重要性。文中概述了多种功率模块的封装结构形式及主要研发内容。另外还讨论了模块封装技术的一些新进展以及在功率电子系统集成中的地位和作用。 1 引言 功率(电源或电力)半导体器件现有两大集成系列,其一是单片功率或高压集成电路,英文缩略语为PIC或HI VC,电流、电压分别小于10A、700V的智能功率器件/电路采用单片集成的产品日益增多,但受功率高压大电流器件结构及制作工艺的特殊性,弹片集成的功率/高压电路产品能够处理的功率尚不足够大,一般适用于数十瓦的电子电路的集成;另一类是将功率器件、控制电路、驱动电路、接口电路、保护电路等芯片封装一体化,内部引线键合互连形成部分或完整功能的功率模块或系统功率集成,其结构包括多芯片混合IC封装以及智能功率模块IPM、功率电子模块PEBb、集成功率电子模块等。功率模块以为电子、功率电子、封装等技术为基础,按照最优化电路拓扑与系统结构原则,形成可以组合和更换的标准单元,解决模块的封装结构、模块内部芯片及其与基板的互连方式、各类封装(导热、填充、绝缘)的选择、植被的工艺流程的国内许多问题,使系统中各种元器件之间互连所产生的不利寄生参数少到最小,功率点楼的热量更易于向外散发,其间更能耐受环境应力的冲击,具有更大的电流承载能力,产品的整体性能、可能性、功率密度得到提高,满足功率管理、电源管理、功率控制系统应用的需求。 2 功率模块封装结构 功率模块的封装外形各式各样,新的封装形式日新月异,一般按管芯或芯片的组装工艺及安装固定方法的不同,主要分为压接结构、焊接结构、直接敷铜DBC基板结构,所采用的封装形式多为平面型以及,存在难以将功率芯片、控制芯片等多个不同工艺芯片平面型安装在同一基板上的问题。为开发高性能的产品,以混合IC封装技术为基础的多芯片模块MCM封装成为目前主流发展趋势,即重视工艺技术研究,更关注产品类型开发,不仅可将几个各类芯片安装在同一基板上,而且采用埋置、有源基板、叠层、嵌入式封装,在三维空间内将多个不同工艺的芯片互连,构成完整功能的模块。 压接式结构延用平板型或螺栓型封装的管芯压接互连技术,点接触靠内外部施加压力实现,解决热疲劳稳定性问题,可制作大电流、高集成度的功率模块,但对管芯、压块、底板等零部件平整度要求很高,否则不仅将增大模块的接触热阻,而且会损伤芯片,严重时芯片会撕裂,结构复杂、成本高、比较笨重,多用于晶闸管功率模块。焊接结构采用引线键合技术为主导的互连工艺,包括焊料凸点互连、金属柱互连平行板方式、凹陷阵列互连、沉积金属膜互连等技术,解决寄生参数、散热、可靠性问题,目前已提出多种实用技术方案。例如,合理结构和电路设计二次组装已封装元器件构成模块;或者功率电路采用芯片,控制、驱动电路采用已封装器件,构成高性能模块;多芯片组件构成功率智能模块。DBC基板结构便于将微电子控制芯片与高压大电流执行芯片密封在同一模块之中,可缩短或减少内部引线,具备更好的热疲劳稳定性和很高的封装集成度,DBC通道、整体引脚技术的应用有助于MCM的封装,整体引脚无需额外进行引脚焊接,基板上有更大的有效面积、更高的载流能力,整体引脚可在基板的所有四边实现,成为MCM功率半导体器件封装的重要手段,并为模块智能化创造了工艺条件。