最新AUTOFORM分析拉延成型资料
AUTOFORM单动拉延简易中文教程

AUTOFORM单动拉延简易中文教程第一步——新建目录:file—New File name(红色)输入自己文件名字第二步——导入IGSW文件:File-IMPORT导进之后点Apply(查看倒入的面是否有破面)第三步——选压边圈:右键选择压边圈(按住shift连选)选好之后点Binder再点apply(红色的)第四步——设置参数:Model-inpat generator定义料厚(sheet thickness)第五步——设置T ools第六步——(die-拉延凹模punch-凸模binder-压边圈。
)定义凹摸高度:Move(选负数)第七步——定义凸摸高度:Move(选零)第八步——定义压边圈高度:Move(选正数)红色的地方点tool center第九步——定义料片线和材料(die表示料片放在凹摸上点击die 可以定义料片放的位置)点Impot 导入料片线点Impot选材料第十步——设置凸凹模压边圈运动,点Downwnwards再点stationary(两个红色的地方)第十一步——再设置closing,点击show all按钮,再点stationary,设置凹模先向下运动到压边圈碰到(刚才设置傲模高度是300 压边圈高度是200 所以这里凹摸向下运动100就碰到压边圈)第十二步——再设置drawing,(force表示受力),凹摸继续往下运动200 ,此时压边圈binder 受到凹摸的力也随着往下200 (P=3表示受到凹摸的受力参数,其值一般为1.5—3)也可以设置力的大小,点P3出现再点const force 再红色的地方输入力的大小单位是牛顿50万牛顿=50钝。
接下来的就可以计算点job - start simulaion(save是默认保存;save as...... 是重新选择保存地方)第十三步——点kinematic check only 再点Start开始计算。
这样计算是看设置的高度有没错误拉下滚动条,拉到顶。
AUTOFORM-拉延教程制作

AUTOFORM简明操作过程启动AUTOFORM,如图1,选择incremental seat增量算法,点OK,出现启动后主界面,如图2;图1图2点击菜单栏的File-New,选择需要分析的IGS文件,并文件命名,建立新档;如图3点击Process generator图标,出现如图4界面图3图4输入文件名选择igs 文件输入板料厚度设置料片,可外界导入,也可直接绘制,如图6,图7.绘制料片线进入Process generator设置界面,未设置项为红色显示,如图5图5料片线输入坐标值图6图7开始设置工具Tools,如图8为为设置状态按范围选择图8依次选择die, punch, binder.各自参数设置如下:凹模位于板料上方凹模运动行程,该例设为200凸模位于板料下方压边圈位于板料下方压边圈拉延行程该例设为80 binder选择工具中心Process设置,设置参数如下图:重力加载项即模具装在压机上的初始状态闭合状态即凹模和压板圈的压料过程速度V=1时间Time=S/V=S/1=S故closing和drawingTime设置数值如下计算die:200binder:80closing=die-binder=120drawing=binder=80拉延过程即料片压紧后到拉延到底的板料成形过程恒定压边力,根据实际设定摩擦系数LubeAutoForm默认状态为0.15更改此系数对成形效果影响较大,有时更改一下拉延效果会很漂亮添加拉延筋,Add drawbead. AutoForm采用等效拉延筋添加拉延筋设置前后对比如下图结果控制:拉延筋宽度一般设12或15阻尼力根据需要可更改可外界导入或直接绘制重新计算/断点续算:标记设置为各工序的结尾。
如果后续需要计算修边、翻边等,须选择此项输出选项ALL ON,以便显示所有的结果.设置完后,工具位置开始计算开始模拟计算检查:各行程是否正确开始计算单动拉延设置基本运用以上计算结果:。
AutoForm5 拉延 切边 翻边

定义steel
定义post
定义回弹
上面所 有的红 色都没 有,说 明设置 完毕
点此即 可计算
1.拉延数模
2.切边线
3.表示翻边下模形状的数模
4.表示翻边PAD形状的数模 5.表示翻边刀形状的数模
打开AUTOFORM^PLUS R5
点新建设计文件
点导放工具体,导入后如下图
点导入曲线,为切边工程用, 导入后如下图
1
3
4 2
点选你要分析的材质
输入料厚
点确认
1 2
拖动这三个工序到设定框中
拖动回弹工步到设定框中
1 2
4
3 5
完成状态
1、点工艺规划, 2、在D20下面点右建,选择Drawing 3、在Outer trim一排,对应的T-30下面点右建, 选自动分配 4、在增加特征的空白处追加一个折弯特征 5、在F-40下面点右建,选自动分配
在最上面处点板料
点红色标示,画一个 拉伸板料,如下图
点工具设定
点工具设定
选择一个产品基准 面
选DIE,来定 义拉伸凹模
点D-20,设 定拉伸工程 的工具
选定义
选DR面
选全部包含, 再确定
选DIE,来定 义拉伸凹模
选DR
Байду номын сангаас
选定义 选一个面
选转换,就能选 中我们要的面 同样的方法定义Binder
点下拉箭头,选第二个复制
定义PAD,
定义切边 工程的相 关工具, 参照视频
AUTOFORM5.0
使用AutoForm5.0作拉延+切边+翻边+反弹分析的设置步骤说明: 一、在作分析之前应准备的资料有: 1.拉延数模(DR data) 2.切边线(Trim line) 3. 表示翻边下模形状的数模 4.表示翻边PAD形状的数模 5.表示翻边刀形状的数模 以上数据都必须是单独的igs文件(如下图所示)。
AUTOFORM分析拉延成型
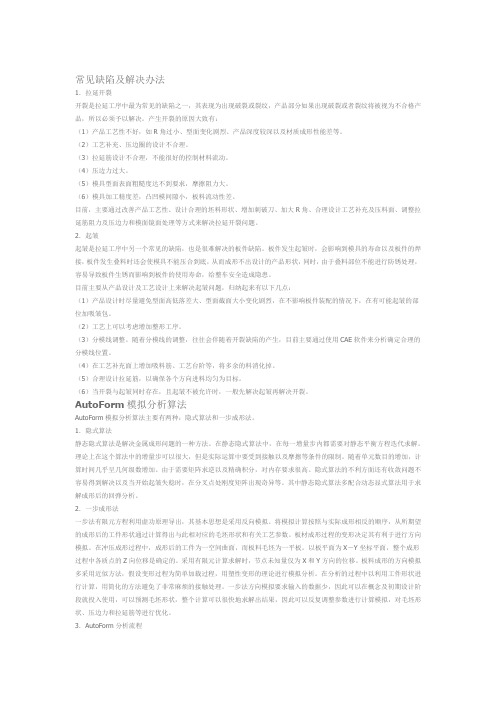
常见缺陷及解决办法1.拉延开裂开裂是拉延工序中最为常见的缺陷之一,其表现为出现破裂或裂纹,产品部分如果出现破裂或者裂纹将被视为不合格产品,所以必须予以解决。
产生开裂的原因大致有:(1)产品工艺性不好,如R角过小、型面变化剧烈、产品深度较深以及材质成形性能差等。
(2)工艺补充、压边圈的设计不合理。
(3)拉延筋设计不合理,不能很好的控制材料流动。
(4)压边力过大。
(5)模具型面表面粗糙度达不到要求,摩擦阻力大。
(6)模具加工精度差,凸凹模间隙小,板料流动性差。
目前,主要通过改善产品工艺性、设计合理的坯料形状、增加刺破刀、加大R角、合理设计工艺补充及压料面、调整拉延筋阻力及压边力和模面镜面处理等方式来解决拉延开裂问题。
2.起皱起皱是拉延工序中另一个常见的缺陷,也是很难解决的板件缺陷。
板件发生起皱时,会影响到模具的寿命以及板件的焊接,板件发生叠料时还会使模具不能压合到底,从而成形不出设计的产品形状,同时,由于叠料部位不能进行防锈处理,容易导致板件生锈而影响到板件的使用寿命,给整车安全造成隐患。
目前主要从产品设计及工艺设计上来解决起皱问题,归纳起来有以下几点:(1)产品设计时尽量避免型面高低落差大、型面截面大小变化剧烈,在不影响板件装配的情况下,在有可能起皱的部位加吸皱包。
(2)工艺上可以考虑增加整形工序。
(3)分模线调整。
随着分模线的调整,往往会伴随着开裂缺陷的产生,目前主要通过使用CAE软件来分析确定合理的分模线位置。
(4)在工艺补充面上增加吸料筋、工艺台阶等,将多余的料消化掉。
(5)合理设计拉延筋,以确保各个方向进料均匀为目标。
(6)当开裂与起皱同时存在,且起皱不被允许时,一般先解决起皱再解决开裂。
AutoForm模拟分析算法AutoForm模拟分析算法主要有两种:隐式算法和一步成形法。
1.隐式算法静态隐式算法是解决金属成形问题的一种方法。
在静态隐式算法中,在每一增量步内都需要对静态平衡方程迭代求解。
AutoForm看图培训

一、材料利用率
是指零件重量与素材重量的比率 即零件重量/素材重量X100%=材料利用率 注:材料的利用率一般会在40~60%
二、下死点分析结果
起皱
起皱严重, 有叠料
四、材料流向变化
是指素材由平钣成形至零件所需的形状后 的材料流动方向;
一般看三个方向: 1、到下死点后材料的流动方向 2、零件局部的材料流动方向 3、外钣件的滑移线
如附图示:
1、到下死点后材料的流动方向;
2、零件局部的材料流动方向;
红色表示拉伸方向 蓝色表示收缩方向
3、外钣件的滑移线;
-30%
+10%
六、起皱分析
指零件拉延后的起皱分析,如以下图示:
七、问题与对策
指分析后的问题点及改修对策,如以下图示:
谢谢
是指分析到底下死点的结果,如以下图示:
三、拉延过程示意
一、指的是素材在自然状态到拉延到底成为需 求形状的过程状态,如附图示:
二、在拉延过程中,主要确认零件的成型〔走 料、起皱〕的趋势;
三、零件拉延过程使用成形性界面确认,成形 性界面各种颜色表示说明如下:
开裂
过渡的 开裂
危险的 开裂
拉延 充分
拉延不 充分
滑移线部位及滑移 线尺寸
五、变薄率
是指素材由平钣成形至零件所需的形状后 的变薄率;(如1.0mm的材料拉延后变薄率 为20%,即拉延后,材料厚度变为0.8mm)
A 一般分析后的材料变薄率不可大于30% B 外板件的变薄率最正确为3-5%
在CAE报告中会表达出每个局部的变薄率, 如附图示:
AutoForm二次拉延

104-110
105. 选 择 Add process step….弹出对话框1-46
106.选择Forming
1-45
107.选择Drawing
108.选择Insert after
109.选择positioning1
1-46
110.选择Add process step弹出对话框1-47
111.选择Drawing
1-51
1-52
136.指定需要保存的路径和名称
137.选择OK弹出对话框1-54
1-53
138. 选 择 Kinematic check only
138-140
139. 选 择 Start 开 始 检 查 运算弹出对话框1-55
1-54
表示检查运算结束
140.选择Dismiss切 换到主界面1-56
66-69
1-29
68.选择 binder
1-31 1-30
67.选择 “Add tool….” 弹出对话框1-31 69.选择 “Add tool”显示 对话框1-32
70.选择 “Above”
74. 选 择 Reference 弹出对话框1-33
70-78
71. 设 定 料 厚 偏 移 方向
72.设定为-1
动态观察3D数模的操作方式有: 1. Shift+左键——移动 2. Ctrl+左键 ——缩放 3. 左件 ——旋转 4. Ctrl+W ——显示所有 5. Ctrl+X ——X方向视图 6. Ctrl+Y ——Y方向视图 7. Ctrl+Z ——Z方向视图
1-5
11.选择成型方式
12.选择Binder图标
autoform详细设置

如图所示:
2.此产品由(1)拉延、(2)修边冲孔、(3)翻边整形、(4)冲孔侧冲孔切断四序完成(左右件共模)。仅介绍第三序翻边整形的设置过程。
3.设置过程
3.1过程准备
3.1.1按“Autoform操作规范”进行工艺补充(如图所示),并进行拉延序的计算,拉延序的计算结果达到最佳时,方可进行后序的计算。
整形是通过上或下模镶块与上压料芯或下托料芯的相对运动来完此产品需要向上翻边且拉延修边后的产品型和翻边前的产品型不一致因此在autoform中进行仿真参数设置时要相应的增加上压料芯上模镶块下托料芯和下模镶块这些工具
Autoform中整形的设置过程
以S21项目中的一个产品为例,介绍在Autoform中设置整形的过程。
(4)Input Generator中的Tools对话框
3.2.3.2根据需要添加工具,在Input Generator中的Tools对话框[如图(4)所示]中选择Add tool,弹出如图(5)所示对话框。
(5)
确认后弹出如图(6)所示对话框:
(6)
选择工具的范围,点击Reference,弹出如图(7)所示对话框:
右键在数型上选择工具范围,按照图(7)旁的注释根据需要单击1或2或3确定所选工具的范围,最后单击OK确认增加工具。
(7)
如果需要继续增.3根据需要添加运动过程,在Input Generator中的Process对话框[如图(8)所示]中选择Add process step,弹出如图(9)所示对话框。
选中Kinematic check only,进行运动关系检查,运动关系正确,方可以进行仿真计算。
AutoForm分析报告

二次拉延制件料厚变化显示云图
板料变薄量云图 板料变厚量云图
板材成形过程图(Draw)
Gravity
BLANK HOLD
80mm from bottom
70mm froΒιβλιοθήκη bottom50mm from bottom
30mm from bottom
10mm from bottom
5mm from bottom
工艺补充介绍(Draw) 拉延筋设计
产品工艺补充形状及拉延筋设计
工艺补充介绍(ReDraw) 拉延筋设计
无拉延筋
拉延/成形板料成形性评估分析结果
产品成形性评估分析结果(Draw)
E B C
成形极限图
D Detail of A A
Detail of B
Detail of C
Detail of D
Detail of E
目录?产品及基本参数介绍?毛坯形状尺寸及材料性能?产品工艺补充形状及拉延筋设计?拉延成形板料成形性评估分析结果?拉延成形板料料厚变化显示云图?二次拉延制件成形性评估分析结果?二次拉延制件料厚变化显示云图?板材成形过程图?总结产品及基本参数介绍产品名称左右前车门内板产品形状产品号6200032930分析软件autoform42分析材质st14zf宝钢实际材质st14zf浦项料厚08mm成形类型拉延毛坯尺寸2040895数据格式igs毛坯形状尺寸及材料性能毛坯形状尺寸非最终材料性能materialname
总结
本零件拉延分析基本成功,可以进行下一步设 计工作.
产品及基本参数介绍
产品名称 产品号 分析软件 分析材质 实际材质 料 厚 成形类型 毛坯尺寸 数据格式 左/右前车门内板 62000329/30 Autoform4.2
- 1、下载文档前请自行甄别文档内容的完整性,平台不提供额外的编辑、内容补充、找答案等附加服务。
- 2、"仅部分预览"的文档,不可在线预览部分如存在完整性等问题,可反馈申请退款(可完整预览的文档不适用该条件!)。
- 3、如文档侵犯您的权益,请联系客服反馈,我们会尽快为您处理(人工客服工作时间:9:00-18:30)。
常见缺陷及解决办法
1.拉延开裂
开裂是拉延工序中最为常见的缺陷之一,其表现为出现破裂或裂纹,产品部分如果出现破裂或者裂纹将被视为不合格产品,所以必须予以解决。
产生开裂的原因大致有:
(1)产品工艺性不好,如R 角过小、型面变化剧烈、产品深度较深以及材质成形性能差等。
(2)工艺补充、压边圈的设计不合理。
(3)拉延筋设计不合理,不能很好的控制材料流动。
(4)压边力过大。
(5)模具型面表面粗糙度达不到要求,摩擦阻力大。
(6)模具加工精度差,凸凹模间隙小,板料流动性差。
目前,主要通过改善产品工艺性、设计合理的坯料形状、增加刺破刀、加大R 角、合理设计工艺补充及压
料面、调整拉延筋阻力及压边力和模面镜面处理等方式来解决拉延开裂问题。
2.起皱
起皱是拉延工序中另一个常见的缺陷,也是很难解决的板件缺陷。
板件发生起皱时,会影响到模具的寿命以及板件的焊接,板件发生叠料时还会使模具不能压合到底,从而成形不出设计的产品形状,同时,由于叠料部位不能进行防锈处理,容易导致板件生锈而影响到板件的使用寿命,给整车安全造成隐患。
目前主要从产品设计及工艺设计上来解决起皱问题,归纳起来有以下几点:
(1)产品设计时尽量避免型面高低落差大、型面截面大小变化剧烈,在不影响板件装配的情况下,在有可能起皱的部位加吸皱包。
(2)工艺上可以考虑增加整形工序。
(3)分模线调整。
随着分模线的调整,往往会伴随着开裂缺陷的产生,目前主要通过使用CAE 软件来分
析确定合理的分模线位置。
(4)在工艺补充面上增加吸料筋、工艺台阶等,将多余的料消化掉。
(5)合理设计拉延筋,以确保各个方向进料均匀为目标。
(6)当开裂与起皱同时存在,且起皱不被允许时,一般先解决起皱再解决开裂。
AutoForm 模拟分析算法
AutoForm 模拟分析算法主要有两种:隐式算法和一步成形法。
1.隐式算法
静态隐式算法是解决金属成形问题的一种方法。
在静态隐式算法中,在每一增量步内都需要对静态平衡方程迭代求解。
理论上在这个算法中的增量步可以很大,但是实际运算中要受到接触以及摩擦等条件的限制。
随着单元数目的增加,计算时间几乎呈几何级数增加。
由于需要矩阵求逆以及精确积分,对内存要求很高。
隐式算法的不利方面还有收敛问题不容易得到解决以及当开始起皱失稳时,在分叉点处刚度矩阵出现奇异等。
其中静态隐式算法多配合动态显式算法用于求解成形后的回弹分析。
2.一步成形法
一步法有限元方程利用虚功原理导出,其基本思想是采用反向模拟。
将模拟计算按照与实际成形相反的顺序,从所期望的成形后的工件形状通过计算得出与此相对应的毛坯形状和有关工艺参数。
板材成形过程的变形决定其有利于进行方向模拟。
在冲压成形过程中,成形后的工件为一空间曲面,而板料毛坯为一平板。
以板平面为X-Y坐标平面,整个成形过程中各质点的Z向位移是确定的。
采用有限元计算求解时,节点未知量仅为X和Y方向的位移。
板料成形的方向模拟多采用近似方法,假设变形过程为简单加载过程,用塑性变形的理论进行模拟分析。
在分析的过程中以利用工件形状进行计算,用简化的方法避免了非常麻烦的接触处理。
一步法方向模拟要求输入的数据少,因此可以在概念及初期设计阶段就投入使用,可以预测毛坯形状,整个计算可以很快地求解出结果,因此可以反复调整参数进行计算模拟,对毛坯形状、压边力和拉延筋等进行优化。
3.AutoForm 分析流程
分析一个CAD 模型的一般步骤是:导入CAD 模型(软件自动进行网格划分)、网格检查及空洞填充、确定基准模具、料厚及冲压方式、工具设定、坯料尺寸确定及网格自动划分、材料选择、拉延筋布置、工艺参数设置和分析计算等。
轿车翼子板模拟流程分析
1.导入CAD 模型
由于AutoForm曲面处理功能的局限性,对一些曲面问题很难解决,所以有必要在三维CAD软件NX里对
工艺数模进行检查,避免出现面交叉、面重叠等曲面问题,同时须提取 B 曲面,保证工艺数模在导入AutoForm 时不出现面丢失、面交叉等缺陷(见图1)。
图1导入CAD模型
2 •网格检查及空洞填充
工艺数模导入之后,AutoForm会自动进行网格划分,可以通过显示网格边界的方式检查网格质量,对于平坦的空洞可以通过自动填充来解决,如果对填充的效果不满意,可以通过改变参数max size值来解决问题,对于边界复杂的空洞,AutoForm填充不能得到理想结果时,需要在NX软件中对数模空洞进行填充。
3•确定分析类型、模具基准、料厚及冲压方式
(1)AutoForm提供了增量法与一步法两种求解方式,对于成形性分析选用incremental增量法能得到更加精确的结果。
(2)根据客户要求,该件生产时所在冲压线首台设备为双动机床,所以本文选择双动拉延方式。
(3)根据客户要求,设定料厚为0.8mm。
(4 )根据产品数模给定的料厚基准,选择凹模为几何偏置基准。
4•工具设定
对于拉延分析而言,需设定凹模、凸模和压边圈三个工具,其中凹模处于坯料的下面,凸模、压边圈处于
坯料的上部,各工具的工作方向均为工具指向坯料的方向,软件默认Z轴的负方向为冲压方向,工具的工
作方向与冲压方向相同时为正值,相反时为负值,如凹模工作方向为凹模指向坯料的方向,即为Z轴负方向,因此凹模工作方向为正值。
凸模与压边圈由凹模网格偏置得到,工作方向为负值。
5.坯料尺寸、材质确定及网格自动划分
AutoForm提供了5种不同的方式来设定坯料的大小:通过画线的方式来得到坯料线轮廓;输入IGS格式的坯料文件;通过中心坐标、长和宽的方式输入坯料尺寸;通过复制现有模型中的线来作为坯料线;通过
对模型中的线进行拓展而得到的线作为坯料线(见图 2 )。
图2坯料尺寸确定
本次分析所采用的坯料线是由NX软件设计的,通过IGS的方式导入到模型中,材料为特深冲用热镀锌钢
板DC54D+Z,该材料耐腐蚀能力强、有良好的力学性能、加工性和焊接性,屈服强度为140〜220MPa , 抗拉强度为270〜350MPa,n值不小于0.18,r值不小于1.6,断后延长率不小于36%。
AutoForm提供了较为完善的材料库,包括中国、日本、欧洲以及美国等常用钢板材料,用户可以新建或者修改现有材料库参数,并且可以通过设置roll angle参数来设置板料的轧制方向。
6.拉延筋布置
在冲压成形中,为了限制板料的流动,需要设置各种形状的拉延筋。
AutoForm中不需要建立实际的拉延筋有限元模型,而是采用一些曲线来模拟拉延筋行为,当板料流过时,施加拉延筋阻力(见图3)。
采用这种等效拉延筋后,在分析时可以很方便的调整拉延筋阻力,节省分析时间,分析成功之后再根据相应的拉延筋阻力系数来设计真实拉延筋几何形状。
7•工艺参数设置
这一步主要是对摩擦系数、压边力以及冲压速度等工艺参数进行设置,因为拉延分析为典型的工艺分析,AutoForm有专门针对拉延分析的模版,所以只需要修改一些工艺参数即可,在输出结果的界面选择默认输
出结果即可,由于采用虚拟拉延筋分析,默认的板料网格大小以及时间步长大小都可以满足正常分析的需要。
8•分析计算
以上步骤完成以后,可以用动画的形式检查一下工具的运动情况,如果没有问题就可以提交计算,计算的结果文件都保存在*.sim文件中,在计算的过程中随时可以查看计算结果。
9• CAE结果判断
计算完成之后,就可以用后处理打开结果文件,对计算结果进行分析、判定。
(1)料厚减薄评价。
判断准则:单向拉伸区域,减薄超过极限料厚一律视为破裂;单向拉伸区域和双向拉伸区域,减薄超过30 律视为破裂;双向拉伸区域,减薄在极限料厚和30%之间,查看FLD指示。
对于外覆盖件,需同时评价最大变薄及最小变薄,将料厚减薄云图的刻度设置为-0.3〜0.02,用不同颜色
来显示,最大减薄为-0.283,产品部分的最小变薄率大于0.02。
本文所例产品料厚减薄情况如图4所示。
图4料厚减薄
(2)成形极限图。
成形极限图刻度如图5所示,可以看岀双向拉伸区域有黄色,说明有开裂的趋势,但离极限曲线还有一定安全量。
-0J6 -C* -CJ -CO fl? 0* Minor strain
Forming Limit Diagram
图5成形极限
(3)主应变和副应变评价。
通过主应变和副应变来评价拉延质量,在产品内基本都属于双向拉伸状态,拉延质量良好,副应变和主应变变化情况如图6、7所示。
图6副应变变化
图7主应变变化
(4)滑移线评价。
外板件要求在可见区域内无滑移线,本分析显示滑移量很小,能满足要求(见图
图8滑移线显示
10 .实际板件拉延情况
随着CAE技术以及计算机技术的发展,CAE的计算精度也越来越能反映出真实情况,本文利用AutoForm 对汽车翼子板进行拉延分析,分析结果显示拉延有开裂的趋势,无起皱、滑移线等缺陷,实际情况为拉延一次成功,无缺陷,CAE与实际情况符合较好。