蜗轮蜗杆齿厚计算及检测方法
齿轮及蜗轮蜗杆的测绘方法

齿轮及蜗轮蜗杆的测绘齿轮和蜗轮蜗杆结构较为复杂,因而此类零件的测绘较一般常见零件更为繁琐,是一项细致的工作。
本章主要讨论我国最常用的标准直齿圆柱齿轮、标准斜齿圆柱齿轮和标准直齿圆锥齿轮以及蜗轮蜗杆的功用与结构、测绘步骤、几何参数的测量和基本参数的确定等内容。
1 齿轮测绘概述1.1 齿轮的功用与结构齿轮是组成机器的重要传动零件,其主要功用是通过平键或花键和轴类零件连接起来形成一体,再和另一个或多个齿轮相啮合,将动力和运动从一根轴上传递到另一根轴上。
齿轮是回转零件,其结构特点是直径一般大于长度,通常由外圆柱面(圆锥面)、内孔、键槽(花键槽)、轮齿、齿槽及阶梯端面等组成,根据结构形式的不同,齿轮上常常还有轮缘、轮毂、腹板、孔板、轮辐等结构。
按结构不同齿轮可分为实心式、腹板式、孔板式、轮辐式等多种型式,如果齿轮和轴做在一起,则形成齿轮轴。
按轮齿齿形和分布形式不同,齿轮又有多种型式,常用的标准齿轮可分为直齿圆柱齿轮、斜齿圆柱齿轮、圆锥齿轮等。
1.2 齿轮的测绘步骤齿轮测绘是机械零部件测绘的重要组成部分,测绘前,首先要了解被测齿轮的应用场合、负荷大小、速度高低、润滑方式、材料与热处理工艺和齿面强化工艺等。
因为齿轮是配对使用的,因而配对齿轮要同时测量。
特别是当测绘的齿轮严重损坏时,一些参数无法直接测量得到,需要根据其啮合中心距a和齿数z,重新设计齿形及相关参数,从这个意义上讲,齿轮测绘也是齿轮设计。
齿轮测绘主要是根据齿轮及齿轮副实物进行几何要素的测量,如齿数z,齿顶圆直径da,齿根圆直径df、齿全高h、公法线长度W k、中心距a、齿宽b、分度圆弦齿厚s及固定弦齿厚sc、齿轮副法向侧隙n及螺旋角β、分锥角δ、锥距R等,经过计算和分析,推测出原设计的基本参数,如模数m、齿形角α、齿顶高系数h a*、顶隙系数C*等,并据此计算出齿轮的几何尺寸,如齿顶圆直径d a、分度圆直径d及齿根圆直径d f等,齿轮的其它部分结构尺寸按一般测绘原则进行,以达到准确地恢复齿轮原设计的目的。
蜗杆的加工与检测
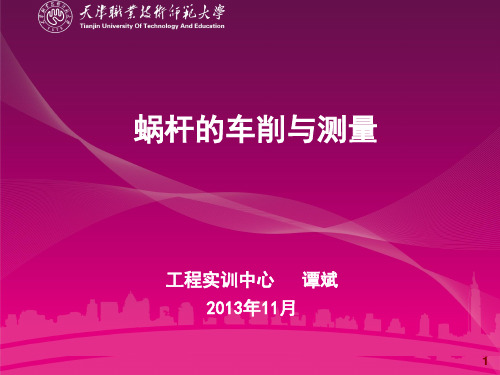
编写数控程序及精度控制
O0009;(第一次精加工) G40G97G99M03S180T11; G00 X50.0 Z5.0; G76 P020130 Q50 R0.03; G76 X39.2 Z-47 P4400 Q2000 F6.283; (G76C2A30X39.2Z-64K4.4U0.03V0.05Q2.0F6.283华中) G00 X150.0; Z200; M05; M30;
2.蜗杆车刀的装夹
(1)水平装刀法 车轴向直廓蜗杆时,用水平装刀法。在装夹车刀时一般用样板找正装夹。 装夹模数较大的蜗杆车刀,容易把车刀装歪。可采用万能量角器来找正车刀 刀尖角位置(见左图)。
(2)垂直装刀法 车削法向直廓蜗杆时,必须把车刀两侧切削刃组成的平面装得与蜗杆齿侧 垂直。 由于蜗杆的导程角比较大,为了改善切削条件和达到垂直装刀要求, 可采用可回转刀杆(见右图)。刀头可相对刀杆回转一个所需的导程角,然后用 螺钉紧固。这种刀杆开有弹性槽,车削时不易产生扎刀。 用水平装刀法车削蜗杆时,由于其中一侧切削刃的前角变得很小,切削不 顺利,所以在粗车轴向直廓蜗杆时,也常采用垂直装刀法。
六、蜗杆的测量方法
蜗杆的主要测量参数有齿距、齿顶圆直径、分度圆直径、法向齿厚。其中 齿顶圆直径可用千分尺测量,齿距由机床传动链保证。 1.分度圆直径的测量 分度圆直径的测量用三针或单针测量,方法与测量梯形螺纹相同(公式不同)。 M=d1+3.924dD-4.316mX d1-分度圆直径,dD=量针直径 dD=1.672 mx 2.法向齿厚的测量 法向齿厚使用齿轮游标卡尺测量(见下图)。适用于精度要求不高的蜗杆。 因图样上一般注明的是轴向齿厚,所以先要把轴向齿厚换算成法向齿厚。
五、蜗杆的车削方法 蜗杆的车削方法和车削梯形螺纹相似。有斜向进刀切削 法、左右切削法、车直槽法和车阶梯槽法。 由于蜗杆的齿距大,齿型深,切削面积大,车削时比梯 形螺纹困难些。一般粗车后留精车余量0.2~0.4mm,在精车 时,采用均匀的单面车削。切削深度不宜过深,否则会发生 “啃刀”现象。所以在车削过程中,必须注意观察切削情况, 控制切削用量,防止“扎刀”。最后再用刀尖角略小于齿型 角的车刀,精车蜗杆底径,把齿型修整清晰,以便保证蜗杆 齿面的表面粗糙度和精度要求。
蜗轮蜗杆计算公式(简洁版)

0
20 1.2004E-08 1.2E-08
中心距a(d1+d2+2*X2*m)/2 蜗杆分度圆导程角(γ)=atan(Z1/q) =atan(m*Z1/d1) 蜗杆齿顶高ha1(ha*=1)=m*ha*=(da1d1) 蜗轮齿顶高ha2=(ha*+X2)*m=(da2d2) 蜗杆齿根高hf1=(ha*+c*)m=(d1df1)/2 蜗轮齿根高hf2=(d2-df2)/2=m*(ha*X2+C*) 蜗杆分度圆直径d1=q*m 蜗轮分度圆直径d2=m*Z2=2a-d1-2*X2*m 蜗杆齿顶圆直径da1=(q+2) *m=d1+2*ha1=d1+2*m*h* 蜗轮喉圆直径da2= (Z2+2+2*X2)*m=d2+2*ha2 蜗杆齿根圆直径df1=d1-2*hf1
Z1大、 29.48
Z1小
Z1大、
33 29.48
普通圆柱螺杆L≥ X -1 -0.5 0 0.5 1
Z1=1~2 46
39.44 51.44 56.4 60.4
蜗杆螺纹部分长度L
圆弧圆柱蜗杆
Z1=3~4
X2
Z1
46
<1
1~2
49.16
1~1.5
1~2
61.16
<1
3~4
62.4
1~1.5
3~4
64.4
80
0
80
80
6.3434076 6.3434076 #DIV/0! 6.3434076
4
22
4
66
4
4.8
0
0
4.8
4.8
36 35.9999999
蜗轮蜗杆测绘、设计计算及图纸标注

m/mm 1 1.011 1.058 1.155 1.270 1.411 1.500 1.516 1.588 1.814 2 2.021 2.116 2.309 2.500 2.527 2.540 2.822 3 3.032 3.175 3.500
pz /mm 15.870 15.950 17.460 18.850 19.050 19.950 20.640 21.990 22.220 22.800 23.810 25.130 25.400 26.500 26.990 28.270 28.580 29.020 30.160 31.420 31.750 31.920
图 8-16 蜗轮喉圆直径 da2 的测量
图 8-17 蜗杆齿高 h l 的测量
② 用游标卡尺测量蜗杆的齿顶圆直径 da1' ③ 和蜗杆齿根圆直径 df1' ,并按下式计算: d ' d f1 ' h1 a1 2 (4)蜗杆轴向齿距 pz ' 测量蜗杆轴向齿距 pz '可以用直尺或游标 卡尺在蜗杆的齿顶圆柱上沿轴向直接测量,如图 8-18 所示。为了精确起见,最好多跨几个轴向齿距, 然后将所测得的数除以跨齿数,就是蜗杆的轴向齿 距。 图 8-18 蜗杆轴向齿距的测量 (5)蜗杆齿形角α 蜗杆齿形角可用角度尺或齿形样板在蜗杆的轴向剖面和法向剖面内测量,将两个剖面的数值 都记录下来,作确定参数时的参考。也可以用不同齿形角的蜗轮滚刀插入齿部作比较来判断。
国家标准对普通圆柱蜗杆的压力角规定为: 阿基米德蜗杆轴向压力角取标准值a a =20°, 法向直廓蜗杆、渐开线蜗杆、锥面包络蜗杆的法向压力角取标准值α n =20。 (4)蜗杆分度圆直径d 1 为使蜗轮滚刀标准化,蜗杆直径d 1 值必须标准化,测绘时应该注意这一点。具体系列请 参看有关手册。 (5)齿顶高系数h a *、顶隙系数c* 在测得全齿高h 1 '和模数m a '后,—般可先试取齿顶高系数h a *=1,顶隙系数c* =0.2, 按公式h l =2 h a *m a +c*m a 核算所得数值。 如果h l ≠h 1 ' , 说明齿顶高系数h a *和顶隙系数c*取值 不正确,应当重新确定。 我国规定h a *=1,导程角γ>30°时,为满足高速重载传动的需要,可采用短齿制,取 h a1 *=0.8。对渐开线蜗杆、蜗轮可分别取为h a1 *=1,h a2 *=2cosγ-1。 为保证蜗轮滚刀的寿命,c* 值可能大于 0.2,某些特殊传动要求 c*值小于 0.2,因此国 家标准规定 c*=0.2,但还可在 0.15~0.35 之间取值。 重新选取h a *和c*后,再用h l 的计算公式核算,直到测得的值h 1 '与计算值h l 相符,即可 最后确定h a *和c*
蜗轮蜗杆的计算

蜗轮蜗杆的计算公司标准化编码 [QQX96QT-XQQB89Q8-NQQJ6Q8-MQM9N]蜗轮、蜗杆的计算公式:1,传动比=蜗轮齿数÷蜗杆头数2,中心距=(蜗轮节径+蜗杆节径)÷2 3,蜗轮吼径=(齿数+2)×模数 4,蜗轮节径=模数×齿数5,蜗杆节径=蜗杆外径-2×模数 6,蜗杆导程=π×模数×头数7,螺旋角(导程角)tg β=(模数×头数)÷蜗杆节径 一.基本参数:(1)模数m 和压力角α:在中间平面中,为保证蜗杆蜗轮传动的正确啮合,蜗杆的轴向模数m a1和压力角αa1应分别相等于蜗轮的法面模数m t2和压力角αt2,即 m a1=m t2=m αa1=αt2蜗杆轴向压力角与法向压力角的关系为: tgαa =tgαn /cosγ 式中:γ-导程角。
(2)蜗杆的分度圆直径d 1和直径系数q为了保证蜗杆与蜗轮的正确啮合,要用与蜗杆尺寸相同的蜗杆滚刀来加工蜗轮。
由于相同的模数,可以有许多不同的蜗杆直径,这样就造成要配备很多的蜗轮滚刀,以适应不同的蜗杆直径。
显然,这样很不经济。
为了减少蜗轮滚刀的个数和便于滚刀的标准化,就对每一标准的模数规定了一定数量的蜗杆分度圆直径d1,而把及分度圆直径和模数的比称为蜗杆直径系数q ,即: q=d1/m常用的标准模数m 和蜗杆分度圆直径d1及直径系数q ,见匹配表。
(3)蜗杆头数z 1和蜗轮齿数z 2蜗杆头数可根据要求的传动比和效率来选择,一般取z1=1-10,推荐 z1=1,2,4,6。
选择的原则是:当要求传动比较大,或要求传递大的转矩时,则z1取小值;要求传动自锁时取z1=1;要求具有高的传动效率,或高速传动时,则z1取较大值。
蜗轮齿数的多少,影响运转的平稳性,并受到两个限制:最少齿数应避免发生根切与干涉,理论上应使z2min≥17,但z2<26时,啮合区显着减小,影响平稳性,而在z2≥30时,则可始终保持有两对齿以上啮合,因之通常规定z2>28。
(完整版)蜗轮蜗杆-齿轮-齿条的计算及参数汇总

蜗轮蜗杆-齿轮-齿条的计算及参数汇总渐开线齿轮有五个基本参数,它们分别是:名称符号意义标准化数值齿数(teeth number)Z 在齿轮整个圆周上轮齿的总数称为齿数模数(module)m齿距分度圆齿距p与π的比值模数决定了齿轮的大小及齿轮的承载能力。
我国规定标准化模数压力角(特指分度圆压力角)(pressure angle)决定渐开线齿形和齿轮啮合性能的重要参数我国规定标准化压力角为20度齿顶高系数齿顶高计算系数:我国规定标准化齿顶高系数为1顶隙系数顶隙(clearance)计算系数我国规定标准化顶隙系数为0.25标准齿轮:模数、压力角、齿顶高系数、顶隙系数为标准值,且分度圆上的齿厚等于齿槽宽的渐开线齿轮。
我国规定的标准模数系列表第一系列0.10.120.150.20.250.30.40.50.60.81 1.25 1.52 2.534568 10121620253240 50第二系列0.350.70.9 1.75 2.25 2.75(3.25) 3.5(3.75) 4.5 5.5 (6.5)78(11)14182228(30)3645注:选用模数时,应优先采用第一系列,其次是第二系列,括号内的模数尽可能不用.系列(1)渐开线圆柱齿轮模数(GB/T 1357-1987)第一系列0.1 0.12 0.15 0.2 0.25 0.3 0.4 0.5 0.6 0.8 11.25 1.5 22.5 3 4 5 6 8 10 12 16 20 25 32 40 50第二系列0.35 0.7 0.9 0.75 2.25 2.75 (3.25)3.5 (3.75) 4.55.5 (6.5)7 9 (11)14 18 22 28 (30)36 45(2)锥齿轮模数(GB/T 12368-1990)0.4 0.5 0.6 0.7 0.8 0.9 1 1.125 1.25 1.375 1.5 1.75 2 2.25 2.5 2.75 3 3.25 3.5 3.75 4 4.5 5 5.5 6 6.5 7 8 910 11 12 14 16 18 20 22 25 28 30 32 36 40 45 50注: 1.对于渐开线圆柱斜齿轮是指法向模数。
蜗轮蜗杆的计算
蜗轮、蜗杆的计算公式: 1,传动比=蜗轮齿数÷蜗杆头数 2,中心距=(蜗轮节径+蜗杆节径)÷2 3,蜗轮吼径=(齿数+2)×模数 4,蜗轮节径=模数×齿数 5,蜗杆节径=蜗杆外径-2×模数 6,蜗杆导程=π×模数×头数7,螺旋角(导程角)tg β=(模数×头数)÷蜗杆节径 一.基本参数:(1)模数m 和压力角α:在中间平面中,为保证蜗杆蜗轮传动的正确啮合,蜗杆的轴向模数m a1和压力角αa1应分别相等于蜗轮的法面模数m t2和压力角αt2,即 m a1=m t2=m αa1=αt2蜗杆轴向压力角与法向压力角的关系为: tgαa =tgαn /cosγ 式中:γ-导程角。
(2)蜗杆的分度圆直径d 1和直径系数q为了保证蜗杆与蜗轮的正确啮合,要用与蜗杆尺寸相同的蜗杆滚刀来加工蜗轮。
由于相同的模数,可以有许多不同的蜗杆直径,这样就造成要配备很多的蜗轮滚刀,以适应不同的蜗杆直径。
显然,这样很不经济。
为了减少蜗轮滚刀的个数和便于滚刀的标准化,就对每一标准的模数规定了一定数量的蜗杆分度圆直径d1,而把及分度圆直径和模数的比称为蜗杆直径系数q,即:q=d1/m常用的标准模数m和蜗杆分度圆直径d1及直径系数q,见匹配表。
(3)蜗杆头数z1和蜗轮齿数z2蜗杆头数可根据要求的传动比和效率来选择,一般取z1=1-10,推荐 z1=1,2,4,6。
选择的原则是:当要求传动比较大,或要求传递大的转矩时,则z1取小值;要求传动自锁时取z1=1;要求具有高的传动效率,或高速传动时,则z1取较大值。
蜗轮齿数的多少,影响运转的平稳性,并受到两个限制:最少齿数应避免发生根切与干涉,理论上应使z2min≥17,但z2<26时,啮合区显着减小,影响平稳性,而在z2≥30时,则可始终保持有两对齿以上啮合,因之通常规定z2>28。
另一方面z2也不能过多,当z2>80时(对于动力传动),蜗轮直径将增大过多,在结构上相应就须增大蜗杆两支承点间的跨距,影响蜗杆轴的刚度和啮合精度;对一定直径的蜗轮,如z2取得过多,模数m 就减小甚多,将影响轮齿的弯曲强度;故对于动力传动,常用的范围为z2≈28-70。
蜗杆的检测与质量分析.
Produced by Мiss Хiè
1.在工件上先车出一条很浅 的螺旋线,测量轴向齿距是 否正确 2.调整轴向齿距 (1)调整好主轴和丝杠的 轴向窜动量 (2)将溜板箱手轮拉出, 使之与传动轴脱开或加装平 衡块使之平衡 (3)调整好开合螺母间隙 3.用重物挂在开合螺母手柄 上防止中途抬起
Produced by Мiss Хiè
二、蜗杆的质量分析
法向齿厚的测量
3.注意事项
1.测量时卡脚的测量面必须与齿侧平行,也就是把刻度所在的卡尺平 面与蜗杆轴线相交一个蜗杆螺旋升角。
2.测量时应把齿高卡尺读数调整到齿顶高ha的尺寸(必须注意齿顶圆 直径尺寸的误差对齿顶高的影响),齿厚卡尺所测得的读数就是法向 齿厚的实际尺寸。
Produced by Мiss Хiè
废品种类 齿形不正确
产生原因
1.车刀刃磨不正确 2.车刀装夹不正确 3.车刀磨损
表面粗糙度大
1.产生积屑瘤 2.刀柄刚度不够,切削时产生振 动
3.车刀背前角太大,中滑板丝杠 螺母间隙过大产生扎刀
4.工件刚度低,而切削用量选用 过大
预防方法
1.正确刃磨合测量车刀角度 2.装刀时使用对刀样板 3.合理选用切削用量并及时 修磨车刀
提示
ProduceMd=bdy1+М3i.s9s2Х4idèD-4. 316mx
法向齿厚的测量
1.使用量具
蜗杆的法向齿厚可以用 齿厚游标卡尺进行测量, 齿厚游标卡尺由互相垂 直的齿高卡尺和齿厚卡 尺组成。
Produced by Мiss Хiè
蜗轮蜗杆的计算
蜗轮蜗杆的计算(总4页) -CAL-FENGHAI.-(YICAI)-Company One1-CAL-本页仅作为文档封面,使用请直接删除蜗轮、蜗杆的计算公式:1,传动比=蜗轮齿数÷蜗杆头数2,中心距=(蜗轮节径+蜗杆节径)÷2 3,蜗轮吼径=(齿数+2)×模数 4,蜗轮节径=模数×齿数5,蜗杆节径=蜗杆外径-2×模数 6,蜗杆导程=π×模数×头数7,螺旋角(导程角)tg β=(模数×头数)÷蜗杆节径 一.基本参数:(1)模数m 和压力角α:在中间平面中,为保证蜗杆蜗轮传动的正确啮合,蜗杆的轴向模数m a1和压力角αa1应分别相等于蜗轮的法面模数m t2和压力角αt2,即 m a1=m t2=m αa1=αt2蜗杆轴向压力角与法向压力角的关系为: tgαa =tgαn /cosγ 式中:γ-导程角。
(2)蜗杆的分度圆直径d 1和直径系数q为了保证蜗杆与蜗轮的正确啮合,要用与蜗杆尺寸相同的蜗杆滚刀来加工蜗轮。
由于相同的模数,可以有许多不同的蜗杆直径,这样就造成要配备很多的蜗轮滚刀,以适应不同的蜗杆直径。
显然,这样很不经济。
为了减少蜗轮滚刀的个数和便于滚刀的标准化,就对每一标准的模数规定了一定数量的蜗杆分度圆直径d1,而把及分度圆直径和模数的比称为蜗杆直径系数q ,即: q=d1/m常用的标准模数m 和蜗杆分度圆直径d1及直径系数q ,见匹配表。
(3)蜗杆头数z 1和蜗轮齿数z 2蜗杆头数可根据要求的传动比和效率来选择,一般取z1=1-10,推荐 z1=1,2,4,6。
选择的原则是:当要求传动比较大,或要求传递大的转矩时,则z1取小值;要求传动自锁时取z1=1;要求具有高的传动效率,或高速传动时,则z1取较大值。
蜗轮齿数的多少,影响运转的平稳性,并受到两个限制:最少齿数应避免发生根切与干涉,理论上应使z2min≥17,但z2<26时,啮合区显着减小,影响平稳性,而在z2≥30时,则可始终保持有两对齿以上啮合,因之通常规定z2>28。
蜗轮蜗杆的计算
蜗轮、蜗杆的计算公式:1,传动比=蜗轮齿数÷蜗杆头数 2,中心距=(蜗轮节径+蜗杆节径)÷2 3,蜗轮吼径=(齿数+2)×模数 4,蜗轮节径=模数×齿数 5,蜗杆节径=蜗杆外径-2×模数 6,蜗杆导程=π×模数×头数7,螺旋角(导程角)tg β=(模数×头数)÷蜗杆节径 一.基本参数:(1)模数m 和压力角α:在中间平面中,为保证蜗杆蜗轮传动的正确啮合,蜗杆的轴向模数m a1和压力角αa1应分别相等于蜗轮的法面模数m t2和压力角αt2,即 m a1=m t2=m αa1=αt2蜗杆轴向压力角与法向压力角的关系为: tgαa =tgαn /cosγ 式中:γ-导程角。
(2)蜗杆的分度圆直径d 1和直径系数q为了保证蜗杆与蜗轮的正确啮合,要用与蜗杆尺寸相同的蜗杆滚刀来加工蜗轮。
由于相同的模数,可以有许多不同的蜗杆直径,这样就造成要配备很多的蜗轮滚刀,以适应不同的蜗杆直径。
显然,这样很不经济。
为了减少蜗轮滚刀的个数和便于滚刀的标准化,就对每一标准的模数规定了一定数量的蜗杆分度圆直径d1,而把及分度圆直径和模数的比称为蜗杆直径系数q ,即: q=d1/m常用的标准模数m 和蜗杆分度圆直径d1及直径系数q ,见匹配表。
(3)蜗杆头数z 1和蜗轮齿数z 2蜗杆头数可根据要求的传动比和效率来选择,一般取z1=1-10,推荐 z1=1,2,4,6。
选择的原则是:当要求传动比较大,或要求传递大的转矩时,则z1取小值;要求传动自锁时取z1=1;要求具有高的传动效率,或高速传动时,则z1取较大值。
蜗轮齿数的多少,影响运转的平稳性,并受到两个限制:最少齿数应避免发生根切与干涉,理论上应使z2min≥17,但z2<26时,啮合区显著减小,影响平稳性,而在z2≥30时,则可始终保持有两对齿以上啮合,因之通常规定z2>28。
另一方面z2也不能过多,当z2>80时(对于动力传动),蜗轮直径将增大过多,在结构上相应就须增大蜗杆两支承点间的跨距,影响蜗杆轴的刚度和啮合精度;对一定直径的蜗轮,如z2取得过多,模数m就减小甚多,将影响轮齿的弯曲强度;故对于动力传动,常用的范围为z2≈28-70。