半成品质量检验标准
ISO22716半成品检验标准

出料前
200ml
卫生
指标
细菌菌落数,类大肠菌群,绿脓杆菌,金黄色葡萄球菌,按GB7918-87检验,本公司尚没有检测能力的项目,定期向有关部门送检.
灌装后成品
1~2支
六
花
露
水
/
收
缩
水
感观
指标
1、色泽:符合规定色泽。
出料前
一
洗
发
水
感观
指标
1、外观:无异物。
出料前
200ml
QB/T1974-2004
2、色泽:符合色泽。
出料前
200ml
3、香气:符合香型、无异味。
出料前
200ml
理化指标
1、PH值(25℃)5.5-7.0。
出料前
200ml
QB/T1974-2004
2、粘度(25℃)≥6000 mPa.s。
出料前
200ml
出料前
200ml
理化
指标
1、PH值:5.5-7.5。
出料前
200ml
QB/T1857-2013
2、粘度:(25℃)>30000mpa.s
出料前
200ml
3、耐热:45℃±1℃,24h恢复室温正常。
灌装后成品
200ml
4、耐寒:-5—15℃,24h恢复室温正常。
灌装后成品
200ml
卫生
指标
细菌总菌,粪大肠菌群,绿脓杆菌,金黄色葡萄菌,按BG7918-87检验。
出料前
200ml
理化
指标
1、PH值:5.5-7.5(果酸类产品除外)。
车间成品半成品质量检验标准

车间成品半成品质量检验标准一、目的规范车间质量检验。
二、适用部门锯材烘干车间、单板车间、备料车间、压贴车间、企口车间、仿古车间、油漆车间、包装车间。
三、检验操作方法检验分QC检验以及车间自检,QC过程检验:针对生产过程进行QC抽检,每次抽检数量为20片,车间有异议的可增加抽检量。
车间检验分来料检验,生产过程检验和成品检验具体操作详见下面规则。
3.1、车间检验3.1.1、锯材烘干车间:缺陷是否挑出以下单项缺陷高于不良品总量的0.5%即可开罚单,综合合格率未达到标准的必须开罚单长度(端头锯材不算)否√厚度否√锯痕否√弯曲度靠尺测量否√缺陷是否挑出以下单项缺陷高于不良品总量的0.5%即可开罚单,综合合格率未达到标准的必须开罚单含水率超标(设置合理的合格率)是√翘曲变形率(设置合理的合格率)否√面裂(设置合理的合格率)是√端裂(设置合理的合格率)是√缺陷是否挑出以下单项缺陷高于不良品总量的0.5%即可开罚单,综合合格率未达到标准的必须开罚单长度是√宽度是√厚度是√侧弯是√等级是√3.2.1、QC检验:A、过程检验:针对车间各工序操作QC按照车间工艺标准进行检验,B、成品检验:针对码托后成品进行检验。
缺陷是否挑出以下单项缺陷高于不良品总量的0.5%即可开罚单,综合合格率未达到标准的必须开罚单含水率超标(合格率)是√翘曲变形率(合格率)否————面裂(合格率)否————端裂(合格率)否————缺陷是否挑出以下单项缺陷高于不良品总量的0.5%即可开罚单,综合合格率未达到标准的必须开罚单长度否√不够宽是√厚度是√等级(色差不算) 是√弯板否————侧弯是√斜头是√漏刨是补土干燥是√板面划线是√3.33.3.1、QC检验:正常生产中QC将按车间工艺标准对生产过程及操作进行检验,但来料的原材料QC不作抽检。
QC只抽检每道工序生产质量状况。
3.3.2、车间检验:车间必须在生产中将所有有缺陷板材挑出,产品转移合格率98%,检验项目见下表:缺陷是否挑出以下单项缺陷高于不良品总量的0.5%即可开罚单,综合合格率未达到标准的必须开罚单侧弯是————弯板是————修边造成的不够宽是√开胶是√错位是√缺边、缺角是√基材脱落是√4.1、针对订单产生的不良品按以下方法处理:4.2、可以通过本工序修补完成的不良品,本工序必须修补完成。
线路板半成品检验标准
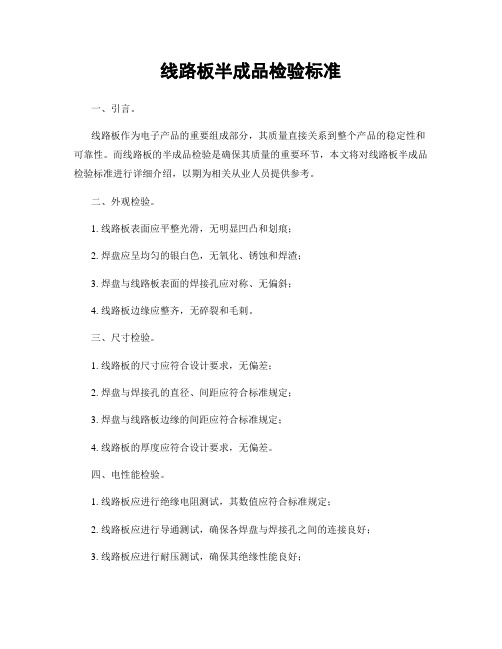
线路板半成品检验标准一、引言。
线路板作为电子产品的重要组成部分,其质量直接关系到整个产品的稳定性和可靠性。
而线路板的半成品检验是确保其质量的重要环节,本文将对线路板半成品检验标准进行详细介绍,以期为相关从业人员提供参考。
二、外观检验。
1. 线路板表面应平整光滑,无明显凹凸和划痕;2. 焊盘应呈均匀的银白色,无氧化、锈蚀和焊渣;3. 焊盘与线路板表面的焊接孔应对称、无偏斜;4. 线路板边缘应整齐,无碎裂和毛刺。
三、尺寸检验。
1. 线路板的尺寸应符合设计要求,无偏差;2. 焊盘与焊接孔的直径、间距应符合标准规定;3. 焊盘与线路板边缘的间距应符合标准规定;4. 线路板的厚度应符合设计要求,无偏差。
四、电性能检验。
1. 线路板应进行绝缘电阻测试,其数值应符合标准规定;2. 线路板应进行导通测试,确保各焊盘与焊接孔之间的连接良好;3. 线路板应进行耐压测试,确保其绝缘性能良好;4. 线路板应进行阻抗测试,确保其电路设计符合要求。
五、环境适应性检验。
1. 线路板应进行高温试验,确保其在高温环境下的稳定性;2. 线路板应进行低温试验,确保其在低温环境下的稳定性;3. 线路板应进行湿热循环试验,确保其在潮湿环境下的稳定性;4. 线路板应进行震动试验,确保其在振动环境下的稳定性。
六、包装检验。
1. 线路板应进行包装外观检验,确保包装完好无损;2. 线路板应进行包装标识检验,确保标识齐全清晰;3. 线路板应进行包装尺寸检验,确保符合运输要求;4. 线路板应进行包装数量检验,确保与订单要求一致。
七、总结。
线路板半成品检验是确保线路板质量的关键环节,通过外观检验、尺寸检验、电性能检验、环境适应性检验和包装检验,可以全面评估线路板的质量状况。
只有严格按照标准进行检验,才能保证线路板的质量稳定可靠,从而确保整个电子产品的质量和可靠性。
以上就是线路板半成品检验标准的相关内容,希望对大家有所帮助。
质量部半成品检验规范
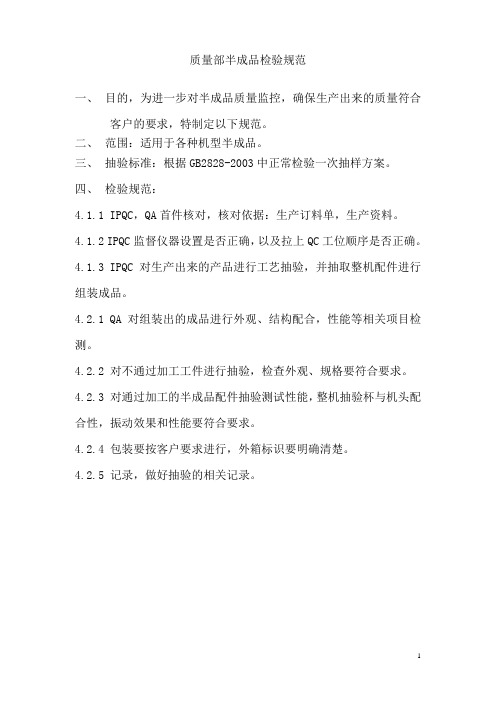
质量部半成品检验规范
一、目的,为进一步对半成品质量监控,确保生产出来的质量符合
客户的要求,特制定以下规范。
二、范围:适用于各种机型半成品。
三、抽验标准:根据GB2828-2003中正常检验一次抽样方案。
四、检验规范:
4.1.1 IPQC,QA首件核对,核对依据:生产订料单,生产资料。
4.1.2 IPQC监督仪器设置是否正确,以及拉上QC工位顺序是否正确。
4.1.3 IPQC对生产出来的产品进行工艺抽验,并抽取整机配件进行组装成品。
4.2.1 QA对组装出的成品进行外观、结构配合,性能等相关项目检测。
4.2.2 对不通过加工工件进行抽验,检查外观、规格要符合要求。
4.2.3 对通过加工的半成品配件抽验测试性能,整机抽验杯与机头配合性,振动效果和性能要符合要求。
4.2.4 包装要按客户要求进行,外箱标识要明确清楚。
4.2.5 记录,做好抽验的相关记录。
1。
西服半成品,成品检验标准

西服半成品,成品检验标准
西服半成品和成品的检验标准包括以下方面:
1. 尺码标准:西服尺码应符合国家或行业标准。
在制作过程中,需要对衣服的尺寸进行检查,确保其准确无误。
2. 型号规格:西服的型号和规格应符合设计要求。
制作完成后,需要进行型号规格的检查,确保每个衣服都符合要求。
3. 环保标准:西服所使用的面料、吸湿内衬、缝纫线等材料应符合国家或行业的环保标准。
制作完成后,需要对西服进行环保检查。
4. 工艺要求:西服应符合制作要求,包括剪裁、缝制、整烫等工艺环节的要求。
制作完成后,需要进行工艺质量检查。
5. 外观质量:西服外观应当整洁美观、无瑕疵,衣领、扣子、袋袋等结构部件位置要准确。
制作完成后,需要进行外观检查。
6. 功能性能:西服应能够满足使用者的要求和期望,如保暖、透气、防水、抗皱等。
制作完成后,需要对西服进行功能测试。
7. 品质持续性:西服制作后应保持品质持续性,这需要对制作过程进行质量控制,确保每件西服都符合相关标准。
以上是西服半成品和成品的一些检验标准,这些标准将确保西服的品质和可靠性,并让消费者购买更加满意。
原材料和半成品质量检验标准

原材料批次的标识: 在原材料的包装上标 明批次号、生产日期 等信息
原材料批次的存储: 根据原材料的种类、 规格、生产日期等信 息进行存储和摆放, 避免混淆和污染
原材料质量异常处理
原材料质量异常分 类:外观缺陷、尺 寸偏差、性能不合 格等
异常处理流程:确 认异常、分析原因、 制定解决方案、实 施整改、验证效果
检验文件培训: 定期对员工进行 检验文件培训, 提高检验质量和 效率
检验文件更改与修订
修订流程:提出申请、审核、 批准、实施
更改原因:生产工艺、设备、 原材料等发生变化
更改内容:检验标准、方法、 频率、记录等
培训与沟通:对相关人员进 行培训,确保理解并执行新
的检验文件
Part 06
质量检验不合格品处理
检验标准:根据国家和 行业标准制定,也可根 据企业实际情况制定
半成品流转检验
目的:确保半成品的质量符合标准 检验项目:外观、尺寸、性能等 检验方法:目测、测量、试验等 检验结果处理:合格品放行,不合格品返修或报废
半成品质量异常处理
异常情况识别:及时发现并识别半成品质量异常情况
异常原因分析:分析异常原因,找出问题根源
原材料和半成
品质量检验标
z
准
XXX,a click to unlimited possibilites
汇报人:XXX
目录
01 原 材 料 质 量 检 验 标 准 03 质 量 检 验 人 员 要 求 05 质 量 检 验 文 件 管 理
02 半 成 品 质 量 检 验 标 准 04 质 量 检 验 设 备 管 理 06 质 量 检 验 不 合 格 品 处 理
异常处理措施:根据异常原因采取相应的处理措施,如返工、报废等 异常记录与跟踪:记录异常情况及处理结果,并进行跟踪,确保问 题得到解决
采购材料半成品验收规范
原辅材料、外购件、原则件、自制件及委外协作件验收规范编制审批二 0 0 六年八月第一部分:原辅材料、外购件、原则件验收规范总则:所有进货旳物资均需验证。
如已规定供方供货,则必须由定点旳合格供方供货。
一、钢材1、验证项目①质保书、进货单应齐全。
20#及Q235旳板材、型材只验证进货单。
②规格、数量、性能等级应符合我司旳供应计划。
③有质保书旳钢材机械性能应符合表1规定,验证其质保书,表1中未作规定材料旳机械性能按有关最新原则旳规定。
2、检查项目和规定①外观检查:外观无裂纹、严重锈蚀、变形等缺陷。
②尺寸检查:尺寸公差应符合图样或零件明细表注明旳有关原则旳技术规定。
③化学分析:化验项目和元素含量按表2规定,表2中未作规定旳材料按有关最新原则规定。
④物理实验:按质量计划及有关技术文献规定。
⑤其他规定旳项目(如:调质解决旳原材料硬度)按合同规定及有关原则检查。
⑥检查合格出具“入库检查报告单”。
3、抽样措施及鉴定规定①外观检查:按表3抽样。
②尺寸检查:每批抽3件,小于3件旳全检,有一件不合格则批不合格。
(指不再加工旳尺寸)③化学分析:每批钢材同一炉号旳抽一件,不合格则同一炉号旳全不合格。
二、铸钢件1、验证项目①检查报告应齐全。
②规格、数量性能等级应符合我司旳供应计划和明细表规定。
2、检查项目和规定①外观检查:外观无裂纹、严重变形、缺肉等缺陷。
②尺寸检查:尺寸按铸件坯料图或成品图样规定检查,以满足加工需要为原则。
③化学分析:化验项目和元素含量按表2规定,表2中未作规定旳材料可按有关最新原则规定。
④物理实验:按质量计划及有关技术文献规定。
⑤检查合格出具“入库检查报告单”。
3、抽样措施及鉴定规定①外观检查及尺寸检查:每批铸件同一品种抽2件。
一件不合格则同一品种全不合格。
②化学分析:每批铸件同一炉号同一品种旳抽一件,不合格则同一炉号旳全不合格。
4、化学分析品种①必须化学分析旳铸件:壳体、尾把、尾座、悬吊杆、颚板架、100型及125型安全门、悬吊座以及ZG35CrMo、ZG34CrNiMo等合金钢铸件。
化妆品半成品检验标准
化妆品半成品检验标准化妆品半成品是指还未成品化妆品的产品,通常是化妆品生产过程中的中间产品。
对于化妆品半成品的质量和安全性检验至关重要,只有通过严格的检验标准,才能确保最终成品化妆品的质量和安全性。
本文将就化妆品半成品的检验标准进行详细介绍。
一、外观检验。
1. 化妆品半成品的外观应该整洁、无异物、无明显色斑和气泡等缺陷。
2. 化妆品半成品的包装应该完好无损,标签清晰、无误,防伪标识鲜明。
二、pH值检验。
1. 化妆品半成品的pH值应符合国家标准,一般来说,不同类型的化妆品半成品对应的pH值范围是不同的。
2. pH值检验应使用专业的仪器,确保准确性。
三、微生物检验。
1. 化妆品半成品应进行细菌、霉菌、酵母菌等微生物检验,确保产品不受污染。
2. 检验标准应符合国家相关法规,确保产品的微生物指标符合安全要求。
四、活性成分含量检验。
1. 化妆品半成品中的活性成分含量应符合配方要求,确保产品的功效。
2. 活性成分含量检验应使用专业的仪器和方法,确保准确性和可靠性。
五、稳定性检验。
1. 化妆品半成品在不同温度、湿度条件下的稳定性应进行检验,确保产品在储存和使用过程中不会发生变质。
2. 稳定性检验应包括物理稳定性、化学稳定性等多个方面,确保产品的整体稳定性。
六、重金属和有害物质检验。
1. 化妆品半成品中的重金属和有害物质含量应符合国家标准,确保产品对用户的安全。
2. 检验应使用专业的仪器和方法,确保准确性和可靠性。
七、其他特殊检验。
1. 根据具体产品的特点,可能需要进行特殊的检验,如防腐剂、防晒剂、色素等成分的含量检验。
2. 特殊检验应根据产品的特点和要求进行,确保产品的质量和安全性。
综上所述,化妆品半成品的检验标准涉及外观、pH值、微生物、活性成分含量、稳定性、重金属和有害物质等多个方面,只有严格按照相关标准进行检验,才能确保最终成品化妆品的质量和安全性。
化妆品生产企业应严格执行相关标准,确保产品的质量和安全,为消费者提供放心、安全的产品。
食品半成品检验标准
食品半成品检验标准
食品半成品是指经过一定加工制作,但未达到最终成品状态的食品,如速冻食品、罐头食品、即食食品等。
对于食品半成品的检验标准,是保障食品安全和质量的重要环节。
本文将从食品半成品检验的目的、方法和标准等方面进行探讨。
首先,食品半成品的检验目的是为了确保食品安全和卫生,保证食品质量稳定
可靠。
通过检验,可以及时发现食品中的有害物质、微生物污染、质量缺陷等问题,从而防止不合格产品流入市场,保障消费者的健康和权益。
其次,食品半成品的检验方法主要包括外观检验、理化指标检验和微生物指标
检验。
外观检验主要是通过观察食品的色泽、形态、气味等特征,来判断食品是否符合要求。
理化指标检验则是通过测定食品的水分、灰分、脂肪含量等指标,来评估食品的营养成分和质地特性。
微生物指标检验则是检测食品中的细菌、霉菌、酵母菌等微生物的数量和种类,以评估食品的卫生状况。
最后,食品半成品的检验标准应当遵循国家相关法律法规和行业标准,确保检
验结果的科学性和可靠性。
同时,针对不同种类的食品半成品,应当制定相应的检验标准,包括但不限于食品安全标准、质量指标、卫生要求等。
只有严格执行检验标准,才能有效保障食品半成品的质量和安全。
综上所述,食品半成品的检验标准是保障食品安全和质量的重要环节,对于食
品生产企业和消费者来说具有重要意义。
通过制定科学合理的检验标准,严格执行检验方法,不断提高检验水平,才能确保食品半成品的质量和安全,促进食品行业的健康发展。
半成品质量检验标准
半成品质量检验标准编制:审核:批准:受控状态:文件编号:发布日期:生效日期:目的:明确钣金车间各工序所生产的零部件的检验方法和质量要求,确保每件产品合格流入下一道工序。
适用范围:钣金车间加工的各工序,是对钣金车间加工产品的质量的控制。
职责:1、钣金车间操作技术人员负责对钣金加工过程的产品的自检,互检。
2、综合质检部在钣金车间的质检员负责对钣金生产加工的过程中的产品质量进行抽验、监督、确认。
3、综合质检部负责对不合格品的发现,记录并做标识隔离,组织处理不合格品。
4、生产部钣金车间参与不合格品的处理。
5、采购部对进厂的钣金原料不合格品与供应商进行沟通。
检测工具:5mm卷尺、200\300卡尺、角度尺、目测一、下料组1、内装:⑴先审图后施工,首先对工程项目的料厚,规格,领用数量进行审核后,严格按图纸要求进行下料。
⑵标准件下料5件内的长≤2000m m、宽≤1200m m尺寸公差控制在±0.5m m,5件以上的产品下料尺寸要完全跟图纸一致,≥2000m m公差控制在±0.8m m.⑶非标件下料5件以内的长≤2000m m、≤1200m m宽尺寸公差控制在±0.8m m,5件以上的产品下料尺寸要完全跟图纸一致,≥2000m m公差控制在±1m m。
⑷标准件、非标件的下料毛刺公差控制在±0.3m m。
⑸标准件5件以内的产品对角线公差在±0.5m m。
5件以上的产品对角线要完全跟图纸一致,非标件5件以内的产品角线公差在±1m m,5件以上的产品对角线要完全跟图纸一致,长度≥4000m m,宽度≥1300m m对角线公差±3m m。
⑹表面无划伤、凹凸点、水印、氧化、辊印、波浪、变形等。
划伤、凹凸点宽度>1m m,深度>0.3m m,板面是≤2000m m,划伤、凹凸点宽度>1.5m m、深度>0.5m m,板面是≥2000m m。
⑺标准件每隔半小时对所下之料进行抽检,非标件每隔3-5件须进行抽检。
- 1、下载文档前请自行甄别文档内容的完整性,平台不提供额外的编辑、内容补充、找答案等附加服务。
- 2、"仅部分预览"的文档,不可在线预览部分如存在完整性等问题,可反馈申请退款(可完整预览的文档不适用该条件!)。
- 3、如文档侵犯您的权益,请联系客服反馈,我们会尽快为您处理(人工客服工作时间:9:00-18:30)。
半成品质量检验标准Document serial number【NL89WT-NY98YT-NC8CB-NNUUT-NUT108】半成品质量检验标准编制:审核:批准:受控状态:文件编号:发布日期:生效日期:目的:明确钣金车间各工序所生产的零部件的检验方法和质量要求,确保每件产品合格流入下一道工序。
适用范围:钣金车间加工的各工序,是对钣金车间加工产品的质量的控制。
职责:1、钣金车间操作技术人员负责对钣金加工过程的产品的自检,互检。
2、综合质检部在钣金车间的质检员负责对钣金生产加工的过程中的产品质量进行抽验、监督、确认。
3、综合质检部负责对不合格品的发现,记录并做标识隔离,组织处理不合格品。
4、生产部钣金车间参与不合格品的处理。
5、采购部对进厂的钣金原料不合格品与供应商进行沟通。
检测工具:5mm卷尺、200\300卡尺、角度尺、目测一、下料组1、内装:⑴先审图后施工,首先对工程项目的料厚,规格,领用数量进行审核后,严格按图纸要求进行下料。
⑵标准件下料5件内的长≤2000m m、宽≤1200m m尺寸公差控制在±,5件以上的产品下料尺寸要完全跟图纸一致,≥2000m m公差控制在±.⑶非标件下料5件以内的长≤2000m m、≤1200m m宽尺寸公差控制在±,5件以上的产品下料尺寸要完全跟图纸一致,≥2000m m公差控制在±1m m。
⑷标准件、非标件的下料毛刺公差控制在±。
⑸标准件5件以内的产品对角线公差在±。
5件以上的产品对角线要完全跟图纸一致,非标件5件以内的产品角线公差在±1m m,5件以上的产品对角线要完全跟图纸一致,长度≥4000m m,宽度≥1300m m对角线公差±3m m。
⑹表面无划伤、凹凸点、水印、氧化、辊印、波浪、变形等。
划伤、凹凸点宽度>1m m,深度>,板面是≤2000m m,划伤、凹凸点宽度>、深度>,板面是≥2000m m。
⑺标准件每隔半小时对所下之料进行抽检,非标件每隔3-5件须进行抽检。
⑻每份订单编号的贴法由所生产的板的实际情况下贴在同一位置。
⑼同一批次、同一编号、同一料厚度的下料时放置在一起。
⑽在原材料不够的特殊情况下用其它料代替的时候需在板面上做好详细的标注。
⑾下好的半成品材料要轻拿轻放。
⑿样品的下料宽度、长度、对角线尺寸公差要跟图纸要求的一致。
2、外装;⑴先审图后施工,首先对工程项目的料厚,规格,领用数量进行审核后,严格按图纸要求进行下料。
⑵标准件5件以内的下料的≤2000m m长、宽≤1200m m尺寸公差控制在±,5件以上的产品下料尺寸要完全跟图纸一致,≥2000m m公差控制在±1m m。
⑶非标件5件以内的下料长≤2000m m、宽≤1200m m尺寸公差控制在±1m m,5件以上的产品下料尺寸要完全跟图纸一致,≥2000m m公差控制在±m m。
⑷标准件、非标件的下料毛刺公差控制在±。
⑸标准件5件以内的产品对角线公差在±1m m。
5件以上的产品对角线要完全跟图纸一致,非标件5件以内的产品角线公差在±,5件以上的产品对角线要完全跟图纸一致。
≥2000m m的对角线公差在±2-3m m。
⑹表面无划伤、凹凸点、水印、氧化、辊印、波浪、变形等。
划伤、凹凸点宽度>1m m,深度>,板面是≤2000m m,划伤、凹凸点宽度>、深度>,板面是≥2000m m。
⑺每隔半小时对所下之料进行抽检。
⑻每份订单编号的贴法由所生产的板的实际情况下贴在同一位置。
⑼同一批次、同一编号、同一料厚度的下料时放置在一起。
⑽在原材料不购的特殊情况下用其它料代替的时候需在板面上做好详细的标注。
⑾下好的半成品料要轻拿轻放。
⑿样品的下料宽度、长度、对角线尺寸公差要跟图纸要求的一致。
三、切角(数控冲,普冲,雕刻,内装,外装通用)1先审图后施工,在切角前对上工序工件的表面质量,下料尺寸做出最后的复检。
2严格按图纸要求进行冲,切,雕、并错位冲角码孔,冲角码时间距偏差±5m m。
3冲,切,雕的长、宽尺寸公差控制在±。
4表面无划伤、毛刺宽度>1m m,深度>,板面是≤2000m m,划伤、毛刺宽度>、深度>,板面是≥2000m m。
5冲,切,雕时注意内装、外装的包角工艺处理。
6在生产密拼的勾搭板时应采用长包短或短包长的工艺处理。
7非标件要全检、标准件要进行三检的标准,(三检是,首检、过程检验、最终检验)。
8冲切样板的制作要专人负责生产。
9标准产品上数控冲时应注意检查编程的图形跟生产图是否一致,夹钳应夹尺寸,对冲好后的第一件产品进行检查后确认不无误后方可批量生产。
10非标产品上数控冲时应注意冲的正反方向及编号是否被冲掉,如编号冲掉应及时用彩笔写上后补标签.而后检查所冲的每件产品是否符合技术要求。
11雕刻机在雕产品时应检查技术部提供的展开图是否跟生产图的尺寸方向一致后方可生产。
在雕刻时的边应无毛刺,雕好后的须检查尺寸,并注意方向,标签的贴法要统一。
四、冲孔(外协冲孔,本公司冲孔)1先审图后施工,严格按图纸要求进行冲孔作业。
2不能有多冲,少冲,冲变形等现象。
3因铝的拉伸性冲好后的板面长、宽公差允许在﹢。
4冲好后的板面要求无毛刺,并进行平直处理达到板面平整的最佳程度。
5冲孔后的板面油污要进行简单的处理。
6冲孔板冲好后板面无压痕。
五、辊弧(内装、外装通用)1严格按图纸要求的半径进行滚弧。
2辊弧时注意正反滚的方向。
3滚出来的弧一定要顺,不能有直线段,滚出来的半径与实际半径小10m m为宜。
4滚弧前要对滚铜上的杂质进行清理。
5滚弧时要从大的半径逐步下调到图纸所要半径为止,并做到是从大件到小件或小件到大件的方式进行。
6滚弧好的板面不能有滚铜印,并要对半径进行初娇,到烧焊,粗磨后进行所要半径样板的娇直处理。
六、折弯1、内装:⑴首先检查上工序冲切好的产品与图纸是否一致,在做好工作前的准备时严格按图纸进行调机折弯。
⑵做到无图纸不施工、不审图不施工、无上岗证不施工的三无原则。
⑶成型好的板面平整度公差2m m,≤2000m m,≥2000m m的公差在3m m-4m m。
⑷成型好的板5件以内的板面长≤2000m m、宽≤1200m m公差控制在±,5件以上的公差要与图纸相符,≥2000m m的公差在±1m m。
⑸密拼板的角度控制在88-89°为宜,除特殊情况下(包柱最佳角度为88°)。
⑹成型好的板对角线公差在±1m m。
⑺成型好的板非标件要全检、标准件要进行三检的标准,(三检是,首检、过程检验、最终检验)。
⑻对有特殊技术要求的板成型好后要进行拼装检验。
⑼对以加工的产品数量要做上记录以方便查阅数量。
⑽小角度5件以上的板要用折弯机折压而成。
⑾大小角度的公差控制在±1°⑿对成型好的产品要轻拿轻放并放到指定位置。
⒀样板的制作要专人负责生产,尺寸公差应与图纸尺寸公差一致,表面要美观。
2、外装:⑴首先检查上工序冲切好的产品与图纸是否一致,在做好工作前的准备时严格按图纸进行调机折弯。
⑵做到无图纸不施工、不审图不施工、无上岗证不施工的三无原则。
⑶成型好的板面平整度公差2-3m m,长度≤2000m m,宽度≤1200m m,≥2000m m的平整度公差在3m m-4m m。
⑷成型好的板5件以内的板面长、宽公差控制在±1m m,≤2000m m,5件以上的公差要与图纸相符≥2000m m的公差在±2m m。
⑸外装板的角度控制在90°为宜,除特殊情况下(包柱最佳角度为88°)。
⑹成型好的板对角线公差在±2m m。
⑺成型好的非标件要全检、标准件要进行三检的标准,(三检是,首检、过程检验、最终检验)。
⑻对有特殊技术要求的板成型好后要进行拼装检验。
⑼对以加工的产品要做上记录以方便查阅数量。
⑽小角度5件以上的板要用折弯机折压而成。
⑾大小角度的公差控制在±2°⑿对成型好的产品要轻拿轻放并放到指定位置。
⒀样板的制作要专人负责生产,尺寸公差应与图纸尺寸公差一致,表面要美观。
七、烧焊1先审图后施工,严格按图纸进行焊接。
2焊接前要对成型好的角度进行初矫,在焊接时要牢固、不得漏焊、少焊、脱焊、裂缝、而且满焊要平整光滑。
3焊接后不管是大角度还是小角度还是90°都要进行角度娇正。
4图纸要求特殊焊接的要特殊焊接并确保质量。
5焊接的配件公差不得超过±2m m。
6样品要专人负责焊接并作满焊处理。
7超大板组焊焊接时内须做点焊处理。
8刨槽后的板在焊接时不管长与短均做点焊处理。
八、打磨1先审图后施工,严格按图纸要求对焊接好了的进行打磨处理。
2要重点对焊接焊缝、满焊、表面有划伤、擦伤、凹凸不平等进行打磨光滑平整。
3满焊后的R角大小要打磨一致,密拼板满焊后的打成直角,外装板打成圆角。
4不焊接的勾搭板要进行措角处理。
5内外装板打磨时要重点处理棱角或较难打磨到的死点。
6打磨后的产品要外观完美,在放置产品时要轻拿轻放。
7样品要专人负责打磨、抛光处理。
九、组装1先审图后施工,严格按图纸要求角码高计划进行角码的安装,角码安装的高度公差±1m m,角码位置的误差在5m m内,殊角码要保证其要求的高度。
2角码采用的材料厚度要一样。
3加强筋的安装要按图纸要求,位置和尺寸公差在5m m内,背筋的力度不够时要增加并且保证板面平整面不变形。
4加强筋的长度,腰行孔的打法,种钉的个数同一批板要一致。
5加强筋的分布要均匀并在加筋时要注意避开编号。
6根据种钉的实际材料厚度在种钉时对电流大小进行调节,注意加筋后板面有无种钉印。
7角码安装好后检测板的平整度,平整度公差1000≤2m m,但不允许起波浪状。
8娇正、拼装、检验后的板方可进入下工序作业。
十、抛光1先审图后施工,严格按图纸要求进行抛光处理。
2在组装接过也做好的产品进行抛光时应轻拿轻放。
3抛光后的产品表面用手检验无划手就现象,抛光时做到主次分明,重点抛光有划伤、种钉印、波浪、辊印、凹凸点的。
4抛光好的产品放置移交区时要分清批次、编号、颜色、放置要整洁规范。
5放置做好的成品要轻拿轻放,正反合并。
6样品抛光出来后板面平整、光滑、美观、棱角分明,公司钢印清晰,角码无毛利,背面同样是光滑、美观。
7抛光时应抛无标签那面。
拟稿人:。