数控系统补偿参数介绍
fanuc热位移补偿参数
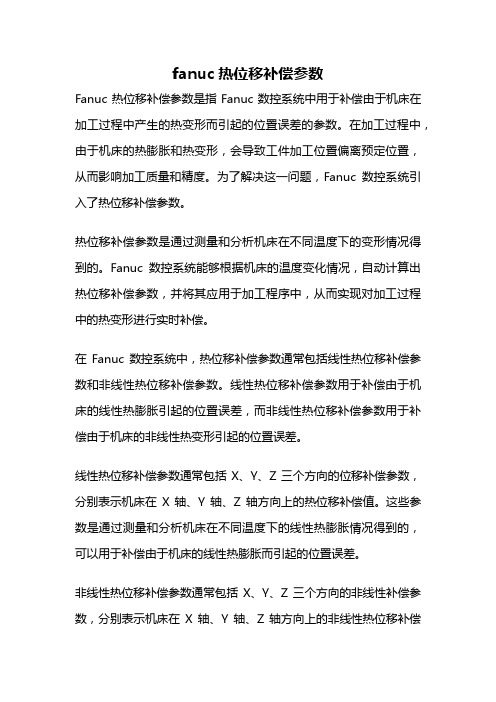
fanuc热位移补偿参数Fanuc热位移补偿参数是指Fanuc数控系统中用于补偿由于机床在加工过程中产生的热变形而引起的位置误差的参数。
在加工过程中,由于机床的热膨胀和热变形,会导致工件加工位置偏离预定位置,从而影响加工质量和精度。
为了解决这一问题,Fanuc数控系统引入了热位移补偿参数。
热位移补偿参数是通过测量和分析机床在不同温度下的变形情况得到的。
Fanuc数控系统能够根据机床的温度变化情况,自动计算出热位移补偿参数,并将其应用于加工程序中,从而实现对加工过程中的热变形进行实时补偿。
在Fanuc数控系统中,热位移补偿参数通常包括线性热位移补偿参数和非线性热位移补偿参数。
线性热位移补偿参数用于补偿由于机床的线性热膨胀引起的位置误差,而非线性热位移补偿参数用于补偿由于机床的非线性热变形引起的位置误差。
线性热位移补偿参数通常包括X、Y、Z三个方向的位移补偿参数,分别表示机床在X轴、Y轴、Z轴方向上的热位移补偿值。
这些参数是通过测量和分析机床在不同温度下的线性热膨胀情况得到的,可以用于补偿由于机床的线性热膨胀而引起的位置误差。
非线性热位移补偿参数通常包括X、Y、Z三个方向的非线性补偿参数,分别表示机床在X轴、Y轴、Z轴方向上的非线性热位移补偿值。
这些参数是通过测量和分析机床在不同温度下的非线性热变形情况得到的,可以用于补偿由于机床的非线性热变形而引起的位置误差。
热位移补偿参数的应用可以有效地提高机床的加工精度和稳定性。
通过对加工过程中的热变形进行实时补偿,可以使机床保持较高的加工精度,并且提高零件的尺寸稳定性。
同时,热位移补偿参数的应用还可以减少因机床热变形引起的零件废品率,提高生产效率和经济效益。
在使用Fanuc数控系统进行加工时,需要合理设置和调整热位移补偿参数,以适应不同的加工条件和要求。
一般来说,可以通过试切试验和实际加工验证来确定最佳的热位移补偿参数,并进行相应的调整和优化。
Fanuc热位移补偿参数是一种用于补偿机床在加工过程中由于热变形引起的位置误差的参数。
发那科加工中心四轴旋转误差补偿参数

发那科加工中心四轴旋转误差补偿参数一、发那科加工中心简介发那科(FANUC)是一家全球知名的数控系统制造商,其生产的加工中心广泛应用于各类加工制造领域。
加工中心是集铣削、镗削、钻孔、切削等多种功能于一体的数控机床。
在实际加工过程中,四轴旋转误差补偿技术对于提高加工精度和效率具有重要意义。
二、四轴旋转误差补偿原理四轴旋转误差补偿技术主要是针对加工中心在四轴旋转过程中出现的误差进行实时修正,从而提高加工精度。
该技术通过采集实时数据,对比理论模型与实际运动轨迹,计算出误差值,并实时调整电机驱动信号,使加工部件的运动轨迹尽量接近理论模型。
三、误差补偿参数设置方法1.确定补偿类型:根据加工中心的结构和加工需求,选择合适的补偿类型,如线性补偿、角度补偿等。
2.采集数据:通过测量设备采集加工中心在四轴旋转过程中的实时数据,如位置、速度、加速度等。
3.建立数学模型:根据采集的数据,建立误差补偿的数学模型,以便后续计算和调整。
4.设置补偿参数:根据数学模型,合理设置补偿参数,如补偿值、补偿范围等。
5.调试与优化:在实际加工过程中,不断调试和优化补偿参数,使加工精度达到最佳状态。
四、实际应用中的注意事项1.确保测量数据的准确性:准确采集加工中心在四轴旋转过程中的数据,以便建立准确的数学模型。
2.合理选择补偿类型:根据加工中心和加工需求,选择合适的补偿类型,以提高加工精度。
3.定期检查与维护:定期检查加工中心四轴旋转系统的磨损情况,及时更换易损件,保证系统正常运行。
4.防止误操作:加强操作人员的培训,避免误操作导致的加工误差。
五、总结与建议发那科加工中心的四轴旋转误差补偿技术在实际应用中具有重要意义。
通过合理设置补偿参数,可以有效提高加工精度,提高生产效率。
为确保误差补偿效果,建议定期检查与维护加工中心,加强操作人员培训,确保加工过程的安全与稳定。
理解数控机床技术中的刀补偿和补偿参数设置

理解数控机床技术中的刀补偿和补偿参数设置数控机床技术是现代制造业中不可或缺的重要工具,它的使用使得加工工艺更加精确、高效。
在数控机床技术中,刀补偿和补偿参数设置是非常关键的环节。
本文将对数控机床技术中的刀补偿和补偿参数设置进行深入解析。
刀补偿是指在数控机床加工过程中,由于工具与工件之间的相对运动和机床的锥度、导轨的精度等原因,刀具的实际切削位置与编程指令的位置可能会有偏差。
为了保证加工结果的准确性,我们需要通过刀补偿来控制刀具的实际切削位置。
刀补偿通常分为几何补偿和半径补偿两种类型。
几何补偿是指根据刀具的几何形状,通过调整工件坐标系与机床坐标系之间的关系,使得刀具的实际切削位置与编程指令的位置相一致。
几何补偿可以分为长、宽、高三个方向的补偿。
通过适当地调整几何补偿的数值,可以实现刀具的侧向移动、刀具半径的变化以及刀具在加工过程中的顶部位置的调整等功能。
半径补偿是指在加工过程中,通过改变程序中圆弧指令的半径值,使得切削轮廓的半径与所需加工尺寸相吻合。
半径补偿一般用于加工圆弧和倾斜面等需求精度较高的部分。
它可以通过改变刀具半径值或者调整工件坐标系与机床坐标系之间的关系来进行补偿。
刀补偿参数设置是确定补偿效果的关键。
在数控机床中,刀补偿参数通常有偏心距、刀具半径、轨迹偏移等。
偏心距是指刀具切削点相对于轨迹的垂直距离,刀具半径是指实际使用中刀具的半径值,轨迹偏移是指在切削点相对于编程指令的距离。
通过合理设置这些参数的数值,可以实现刀具补偿。
在进行补偿参数设置时,首先要根据所加工零件的要求和加工特点来确定需要进行刀补偿的部分,然后根据实际情况来设置刀补偿参数的数值。
一般来说,刀补偿参数的数值越大,补偿效果越明显。
但是,过大的补偿参数可能会导致刀具过度磨损或加工精度不高。
因此,在确定刀补偿参数时,需要根据实际加工情况进行合理的调整。
此外,还需要根据刀具磨损程度和加工要求进行定期检查和调整刀补偿参数。
在实际加工过程中,由于刀具的磨损和变形,刀补偿参数的设置可能需要进行适当的修正。
数控系统位置误差的分析及参数补偿
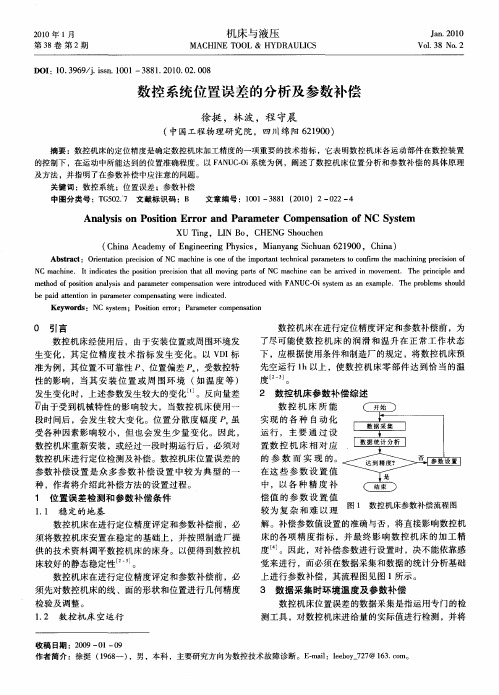
N c i e I i dc ts te p st n p e iin t a l mo i g p r fNC ma h n a e arv d i v me t T e p n i l d C ma h n . t n iae h o i o r cso t l vn a s o c ie c n b ri e n mo e n . h r c p e a i h a t i n meh d o o i o n y i a d p r mee o e s t n wee i t u e i ANUC Ois se a n e a l . T e p o lms s o l t o fp st n a a ss n aa t rc mp n a i r nr c d w t F i l o d o h - y tm s a x mp e h r be h u d b ad atn in i a a trc mp n ai g w r n iae . e p i t t n p r mee o e s t e e i dc td e o n
觉来进行 ,而必须在数据采集和
数 控 机 床 所 能 实现 的 各 种 自动 化
运 行 ,主 要 通 过 设
置数 控 机 床 相 对 应 的参 数 而 实 现 的。 在这 些 参 数 设 置 值
中,以各 种 精 度 补 偿值 的参 数 设 置 值 较 为复 杂 和 难 以理 图 1 数控机床参数补偿流程图 解 。补偿参数值设置 的准确与否 ,将直接 影响数控机 床 的各项 精度指 标 ,并 最终 影响 数控 机床 的加 工精
中 图分 类 号 :T 52 7 文 献 标 识 码 :B G 0. 文 章 编 号 :10 3 8 (0 0 0 1— 8 1 2 1 )2— 2 4 0 2—
浅析数控系统的刀具补偿

浅析数控系统的刀具补偿作者:陈永红来源:《现代企业文化·理论版》2010年第10期摘要:文章通过对不同数控机床的刀具补偿功能较全面的分析和计算。
掌握了其刀具补偿应用技能,为在理论教学和实践操作解决各种具体实际问题,提供了参考。
关键词:数控机床;刀具补偿;刀具轨迹;刀位点一、数控刀具补偿功能使用立铣刀在数控铣床或数控加工中心上加工工件时,可以清楚看出刀具中心的运动轨迹与工件已加工轮廓不重合,这是因为工件轮廓是立铣刀以运动包络的方式形成的。
立铣刀的中心称为刀具的刀位点,刀位点的运动轨迹即代表刀具的运动轨迹。
在数控加工中是按工件轮廓尺寸编制程序,还是按刀位点的运动轨迹编制程序,需要根据具体情况来处理。
二、数控系统中的刀具补偿(一)数控车床刀具补偿1刀具位置补偿。
对于刀具磨损或重新安装刀具引起的刀具位置变化,建立、执行刀具位置补偿后,其加工程序不需要重新编制。
办法是测出每把刀具的刀位点相对于某一理想位置的刀位偏差(X向与Z向)并输入到指定的存储器内,程序执行刀具补偿指令后,当前刀具的实际位置就到达理想位置。
2刀尖圆弧半径补偿。
编制数控车床加工程序时,车刀刀尖被看作是一个点(假想刀尖P 点),但实际上为了提高刀具的使用寿命和降低工件表面粗糙度,车刀刀尖被磨成半径不大的圆弧,这必将产生加工工件的形状误差。
由于刀尖圆弧所处的特殊位置。
车刀的形状对工件加工也将产生影响,而这些可采用刀尖圆弧半径补偿来解决。
3刀补参数。
每一个刀具补偿号对应刀具位置补偿(X和Z值)和刀尖圆弧半径补偿(R和T值)共4个参数,在加工之前输入到对应的存储器。
在自动执行过程中,数控系统按该存储器中的X、Z、R、T的数值,自动修正刀具的位置误差和自动进行刀尖圆弧半径补偿。
意义:在进行工件轮廓的加工时,由于刀具半径、刀尖半径的存在,刀具中心或假想刀尖和工件轮廓不重合。
当刀具磨损、重磨、换刀时,要重新计算刀心轨迹,修改程序。
然而当数控系统具备刀具半径自动补偿功能时,则只需按工件轮廓进行编程,数控系统会自动计算刀心轨迹,使刀具偏离工件轮廓一个半径值,不需要修改程序。
数控车床刀具参数补偿指令
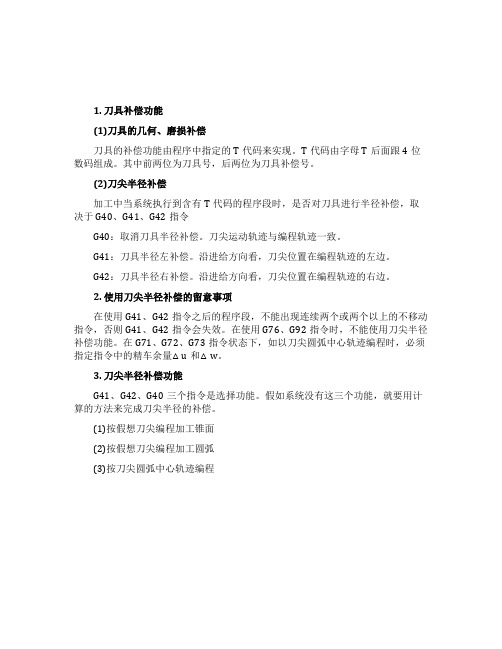
1. 刀具补偿功能
(1)刀具的几何、磨损补偿
刀具的补偿功能由程序中指定的T代码来实现。
T代码由字母T后面跟4位数码组成。
其中前两位为刀具号,后两位为刀具补偿号。
(2)刀尖半径补偿
加工中当系统执行到含有T代码的程序段时,是否对刀具进行半径补偿,取决于G40、G41、G42指令
G40:取消刀具半径补偿。
刀尖运动轨迹与编程轨迹一致。
G41:刀具半径左补偿。
沿进给方向看,刀尖位置在编程轨迹的左边。
G42:刀具半径右补偿。
沿进给方向看,刀尖位置在编程轨迹的右边。
2. 使用刀尖半径补偿的留意事项
在使用G41、G42指令之后的程序段,不能出现连续两个或两个以上的不移动指令,否则G41、G42指令会失效。
在使用G76、G92指令时,不能使用刀尖半径补偿功能。
在G71、G72、G73指令状态下,如以刀尖圆弧中心轨迹编程时,必须指定指令中的精车余量△u和△w。
3. 刀尖半径补偿功能
G41、G42、G40三个指令是选择功能。
假如系统没有这三个功能,就要用计算的方法来完成刀尖半径的补偿。
(1)按假想刀尖编程加工锥面
(2)按假想刀尖编程加工圆弧
(3)按刀尖圆弧中心轨迹编程。
数控设备刀具补偿技术讲解
刀具长度补偿:
补偿刀具长度方向尺寸的变化.
三、刀具补偿的方法
• •
人工预刀补:人工计算刀补量进行编程 机床自动刀补:数控系统具有刀具补偿功能。
四、刀具半径补偿功能
1、刀具半径补偿的作用
在数控铣床上进行轮廓铣削时,由于刀具半径的 存在,刀具中心轨迹与工件轮廓不重合。
从上述程序可以大致了解钻孔加工的走刀路线及钻孔的基本 编程方法,当所使用的数控铣床不具备更高级的钻孔专用指令 时,通常都需要这样一步步地编程,更方便的钻孔编程方法将 在后面的章节中逐步介绍。
返回上层
3、刀具长度补偿指令
刀具长度补偿G43,G44,G49 (1)格式
G43
G44 G49
G00
G01
Z— H—
G00
G01
Z—
G43 刀具长度正补偿
G49取消刀长补偿
G44 刀具长度负补偿
G43 G44 G49 均为模态指令
其中Z 为指令终点位置,H为刀补号地址,用H00~ H99来指定,它用来调用内存中刀具长度补偿的数值。
t01t02t031010刀补引入刀补取消采用刀座对刀后来安装刀具h0145d010004g92x1500y1600z1200g90g00x1000y600g43z20h01s100m03g42g01x750d01f100x350g02x150r100g01y700g03x150r150g01y600g02x350r100g01x750g09y0主程序号建立工件坐标系绝对值方式快进到x100y60指令高度z2实际到达高z43处刀径补偿引入插补至x75y60直线插补至x35y60顺圆插补至x15y60直线插补至x15y7015y70直线插补至x15y6035y60直线插补至x75y60直线插补至x75y0处程序单g01x450x750y200y650g40g00x1000y600g49z1200x1500y1600m05m30直线插补至x45y45直线插补至x75y20直线插补至x75y65轮廓切削完毕取消刀补快速退至10060的下刀处快速抬刀至z120的对刀点平面主轴停程序结束复位
掌握数控机床技术中的刀具选择和刀补偿参数设置技巧
掌握数控机床技术中的刀具选择和刀补偿参数设置技巧刀具选择和刀补偿参数设置是数控机床技术中至关重要的环节。
正确的刀具选择和刀补偿参数设置能够提高加工效率和加工质量,减少切削力和工件变形。
本文将介绍数控机床技术中的刀具选择和刀补偿参数设置的技巧。
首先,刀具选择是影响加工效果和工具寿命的关键因素之一。
在选择刀具时,需要考虑材料的切削性质、工件的几何形状和尺寸、加工方式等因素。
对于切削性能好的材料,如铸铁、钢等,可以选择高速钢刀具;而对于切削性能较差的材料,如高温合金、钻石等,应选择硬质合金或陶瓷刀具。
此外,刀具的刀尖半径、切削刃数和刀具类型也需要根据具体加工要求进行选择。
其次,刀补偿参数设置是确保数控加工精度的关键因素之一。
刀补偿参数用于修正刀具和工件之间的误差,使得加工结果与设计要求一致。
在刀补偿参数设置时,需要考虑切削力的方向和大小、材料的粘结性、工件形状的复杂性等因素。
正确设置刀补偿参数需要经验和技巧。
首先,需要根据工件的几何形状和尺寸,选择合适的刀具轨迹和切削路径。
其次,要根据加工材料的切削性质,选择合适的切削速度、切削深度和进给量。
此外,在设置刀补偿参数时,还应考虑刀具尺寸和摩擦系数对刀具半径和补偿值的影响。
在进行刀具选择和刀补偿参数设置时,还需注意以下几点技巧。
首先,刀具要保持锋利,及时更换磨损的刀具,以保证加工效率和加工质量。
其次,要根据工件的要求,设置合适的刀具切削参数,控制刀具切削力和温度,减少工件变形,提高加工精度。
此外,要合理设置刀具切削路径,避免过度切削或切削不足,保证加工过程的稳定性和工具寿命。
总而言之,刀具选择和刀补偿参数设置是数控机床技术中的重要环节。
正确的刀具选择和刀补偿参数设置能够提高加工效率和加工质量,降低切削力和工件变形。
在实际应用中,需要根据具体的加工要求和材料性质,灵活运用各种技巧和经验,确保刀具选择和刀补偿参数设置的准确性和有效性。
只有掌握了刀具选择和刀补偿参数设置的技巧,才能发挥数控机床的最大潜力,实现高效、精确的加工。
fanuc数控机床间隙补偿量控制功能参数的设定
Fanuc数控机床是一种广泛应用于制造业的高精度设备,其间隙补偿量控制功能参数的设定对于保证机床加工精度至关重要。
本文将对Fanuc数控机床间隙补偿量控制功能参数的设定进行详细讲解,帮助读者更好地掌握这一重要技术。
一、间隙补偿量的作用在机床加工过程中,由于各种因素的影响,机床零件的尺寸可能会出现偏差。
为了保证加工零件的精度,Fanuc数控机床引入了间隙补偿量控制功能。
通过设定间隙补偿量,可以在加工过程中自动进行补偿,从而实现加工精度的提高。
二、间隙补偿量的设定方法1. 进入参数设定界面操作人员需要进入Fanuc数控机床的参数设定界面,通常是通过按下特定的功能键或者输入指定的指令来实现。
进入参数设定界面后,可以看到间隙补偿量控制功能相关的参数选项。
2. 设定间隙补偿量参数在参数设定界面中,操作人员可以对间隙补偿量控制功能的各项参数进行设定。
这些参数包括间隙补偿量的大小、补偿方向、补偿速度等。
通过合理地设定这些参数,可以实现对加工过程中的尺寸偏差进行有效的补偿。
3. 保存设定参数设定完间隙补偿量控制功能的参数后,操作人员需要将其保存到机床的控制系统中。
通常可以通过按下确认键或者选择保存命令来完成这一步骤。
保存后,间隙补偿量控制功能的参数就会生效,可以在实际加工过程中发挥作用。
三、注意事项1. 熟悉机床型号不同型号的Fanuc数控机床可能具有不同的间隙补偿量控制功能参数设定方法和选项,因此操作人员在进行设定时需要事先熟悉机床的型号和相关技术文档,以便正确地进行操作和设定。
2. 调试参数设定在进行间隙补偿量控制功能参数设定后,操作人员需要对设定的参数进行调试和验证。
可以通过加工实际工件或者使用专门的验证工具来检验间隙补偿量控制功能的有效性,以确保设定的参数能够达到预期的效果。
3. 注意安全防护在进行间隙补偿量控制功能参数设定时,操作人员需要注意安全防护措施,避免发生意外伤害。
也需要确保设定的参数不会对机床和加工零件造成损坏,对设备和工件进行充分的保护。
数控机床刀补参数设置
数控机床刀补参数设置随着工业自动化的不断发展,数控机床在现代制造业中扮演着越来越重要的角色。
数控机床的刀具补偿参数设置是其正常运行的关键之一,合理设置刀具补偿参数能够保证加工精度和效率。
本文将介绍数控机床刀具补偿参数的设置方法及其影响因素。
1. 刀具补偿概述刀具补偿是数控机床加工中常用的一种技术手段,通过在程序中设置刀具补偿值,来补偿刀具的实际尺寸偏差,以保证加工零件的尺寸精度。
刀具补偿通常包括半径补偿、长度补偿和刀尖半径补偿等。
2. 刀具补偿参数设置方法2.1 刀具半径补偿设置刀具半径补偿是在数控机床中常见的一种补偿方式。
具体设置方法如下:- 定义刀具半径补偿的序号;- 设置补偿数值,根据实际情况调整;- 选择切削方向,确定补偿方向。
2.2 刀具长度补偿设置刀具长度补偿主要用于控制刀具与工件接触的位置,避免刀具碰撞。
设置方法如下:- 定义刀具长度补偿的序号;- 设置补偿数值,根据实际情况调整;- 确定刀具路径,避免与工件干涉。
2.3 刀尖半径补偿设置刀尖半径补偿常用于弥补刀具的圆弧轮廓误差。
设置方法如下:- 定义刀尖半径补偿的序号;- 设置补偿数值,根据实际情况调整;- 确定刀具轮廓路径,保证加工精度。
3. 刀具补偿参数影响因素刀具补偿参数的设置需考虑以下因素:•刀具材质和尺寸;•工件材料和形状;•加工精度要求;•切削速度和进给速度。
综上所述,数控机床刀具补偿参数设置是保证加工精度和效率的重要步骤,正确设置补偿参数可以提高机床加工的稳定性和质量。
在实际操作中,操作人员需要根据具体情况灵活调整参数,不断优化加工过程,以获得更好的加工效果。
希望本文对数控机床刀具补偿参数的设置有所帮助,并能引发更多关于数控机床加工技术的讨论与思考。
- 1、下载文档前请自行甄别文档内容的完整性,平台不提供额外的编辑、内容补充、找答案等附加服务。
- 2、"仅部分预览"的文档,不可在线预览部分如存在完整性等问题,可反馈申请退款(可完整预览的文档不适用该条件!)。
- 3、如文档侵犯您的权益,请联系客服反馈,我们会尽快为您处理(人工客服工作时间:9:00-18:30)。
三菱数控系统MITSUBISHI
(一)FANUC-0M系列螺距误差补偿参数(表1-1)
软限位参数(表1-2)
反向间隙补偿参数(表1-3)
(二)FANUC-i系列螺距误差补偿参数(表2-1)
软限位参数(表2-2)
反向间隙补偿参数(表2-3)
(三)FANUC-0T系列螺距误差补偿参数(表3-1)
软限位参数(表3-2)
反向间隙补偿参数(表3-3)
门子数控系统SIEMENS
SINUMERIC 840D/840Di/810D螺距误差补偿参数
1. 坐标轴反向间隙补偿参数:MD32450:BACKLASH
2. 坐标轴反向间隙补偿倍率:MD32452:BACKLASH-FACTOR
补偿值范围:0.01-100.00 (In SW5 and later)
3. 螺距误差补偿值输入有效:MD32700:ENC-COMP-ENABLE
“0”有效,先置成“0”,输入完成后,再改为“1”。
螺距误差补偿有两种方法:
1. 传输法:数控系统自动生成补偿文件,将补偿文件传入计算机,在计算机上编辑并输入补偿值,再将补偿文件传回数控系统。
2. 运行法:数控系统自动生成补偿文件,将补偿文件格式改为零件程序格式,通过操作单元将补偿值输入到零件程序中,运行该零件程序,即可将补偿值写入系统。
海德汉数控系统HEIDENHAIN
(一)i530螺距误差补差参数
反向间隙补偿参数1.旋转编码器
2.直线编码器
线性坐标误差补偿参数
坐标误差补偿方式选择参数
坐标行程软限位参数
进入坐标误差补偿文件密码:807667
(二)370螺距误差补差参数
反向间隙补偿参数
线性坐标误差补偿参数
坐标误差补偿方式选择参数
坐标行程软限位参数
进入坐标误差补偿文件密码:105296。