三现五原则教材
三现五原则培训讲义

五原则
1.
◎现状把握的目的 1.真对问题全面调查事实. 2.掌握变异. 3.归纳可疑方向
查明要因 真因追查
5W分析 特性要因图 再现试验 NG再现试验 OK再现实验
2.
问题 要因 真因 查明真因
不良原因 流出原因
≈
何谓三现五原则
≈
适当对策
*已留入市场处理
临时对策
*库存成品处理 *半成品处理 *在库物料处理
标准化
S.O.P修正
*试验规范 *限度样品
三现五原则对策注意事项 1.无科学根据DATA之解析对策
2.以偏盖全之解析对策
3.增加不必要成本之解析对策
4.以变更设计改善制程变异之改善对策 5.变化点分析不明确之解析对策 6.无回馈标准之解析对策 7.无再现之解析对策
8.无三现之解析对策
9.无制程面、流出面检讨之解析对策 10.五层分析内容不连续解析对策
一.没有科学根据DATA 问题点:常发生的直觉判断 焊接强度不足 对策:加锡 正确吗? 焊接器件不粘锡 对策:焊接温度提升10度 没问题吗?
思 考:加锡/提高烙铁温度10度如何得来的? 直觉+经验≠事实 100个直觉或经验不如1个数据
分析方法:科学的根据=实验数据 有实验的数据才能决定新的标准. 要去试验出加锡及温度提高10度是最好的作业条件.
三现五原则讲义
前
一.背景
言
1.品质是企业生存的基本条件. 2.品质经常发生异常.成本损失大. 3.品质不良,操作人员总是认为是品管部门的责任. 4.不良解析经常找不到真因.
二.基本想法
1.籍由提高三现五原则解析能力.真正改善重要的品质问题点. 2.解决问题 持续有效的解决问题 不再是问题
演示文稿三现五原则课件
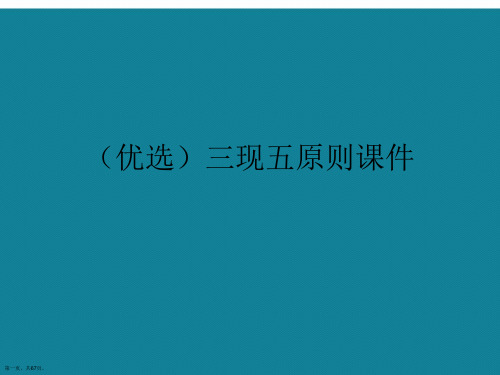
(WHAT)做什么:问题的症状,尽可能地使用图表等工具将问题表达清楚.
(WHEN)何时:记入问题发生的日期
(WHERE)何地:记入问题发生的场所
(WHY)为什么:具体的内容
.2H: (HOW)怎么做:(问题)是怎么样被发现的 (HOW MANY)什么程度:(问题)发生的量、程度
至少要问5个为什么 (WHY),具体参考
三现主义的定义
4
现场
不要只坐在办公室决策,而是要立即赶到现场,奔赴第一线。现场是生机勃勃的,每天都 在变化,不具备正确的观察方法,你就没法感觉它的变化,包括异常。 现物 管理的最重要的概念是“总是以事实为基础而行动”,解决问题要求你找到事实真相。因 为只有一个真理存在,最通用的方法是“到问题中去,并客观地观察其过程”。 观察你看不到的地方,这时,事实将出现。要发现其变化的原因,仔细观察事实。当你这 样做时,隐藏的原因将会出现,这样做,你可以提高发现真相的能力。 现实
解决问题需要你面对现实,把握事实真相。我们需要用事实解决问题,而事实总是变化无常的, 要抓住事实就要识别变化,理想与实际总是有很大的差距。
很多问题如果我们不亲临现场,不调查事实和背景原因,就不能正确认识问题。但为什么会发生那样 的问题呢?我们要多问几次“为什么”,对“现物”、“现实”进行确认。
企业常见的缺乏“三现主义”的现象
◆等待生产现场的联系或生产现场对于技术、品质、资材等部门服务、指导、指示、供应的等待。等待下级的汇报,任务虽已布
置,但是没有检查,没有监督。不主动去深入实际调查研究,掌握第一手资料,只是被动地听下级的汇报,没有核实,然后作决定或向上 级汇报,瞒天过海没有可信度,出了问题,责任往下级身上一推。“三现主义”的缺乏是等待中的最致命原因之一,严重影响生产现场工 作的及时解决。
三现五原则-最终版

要点二
详细描述
为了确保三现五原则的有效实施,企业应重视员工的培训 与参与。这可以通过开展定期培训、提供学习资源、鼓励 员工参与决策等方式实现。此外,企业应建立良好的激励 机制,表彰在原则实施过程中表现优秀的员工,以提高员 工的积极性和参与度。通过提高员工素质和参与度,企业 可以进一步推动三现五原则的落实,实现更好的发展成果 。
持续改进与优化的实施与效果
总结词
持续改进与优化是五原则的核心目标之一,它有助于组 织不断适应变化、提高竞争力和可持续发展。
详细描述
组织需要鼓励员工不断寻求改进和优化的机会,并为其 提供必要的资源和支持。这包括制定改进计划、设立改 进团队、引入创新技术和方法等。同时,组织还需要建 立有效的绩效评估体系,以衡量改进与优化的成果并持 续改进。持续改进与优化能够提高生产效率、降低成本 、增强创新能力、提升客户满意度和增强组织竞争力。
现状反思
定期对当前的工作情况进行反思和总结,找出可以改 进的地方。
现行措施调整
根据实际情况和反馈,及时调整现行措施,以实现持 续改进的目标。
04
五原则的实施与效果
管理层的决心和承诺的实施与效果
总结词
管理层对实施五原则的决心和承诺是至关重 要的,它决定了整个组织对五原则的重视程 度和执行力。
详细描述
VS
详细描述
随着企业内外部环境的变化,三现五原则 的实施方案也应不断调整和完善。企业应 定期评估原则的执行情况,总结经验教训 ,并根据实际情况调整实施方案。此外, 企业应关注行业动态和最佳实践,不断引 入新的理念和方法,以保持原则的先进性 和有效性。
原则五:员工培训与参与
要点一
总结词
员工培训与参与是三现五原则的重要支撑,需要提高员工 素质和参与度。
三现主义培训教材
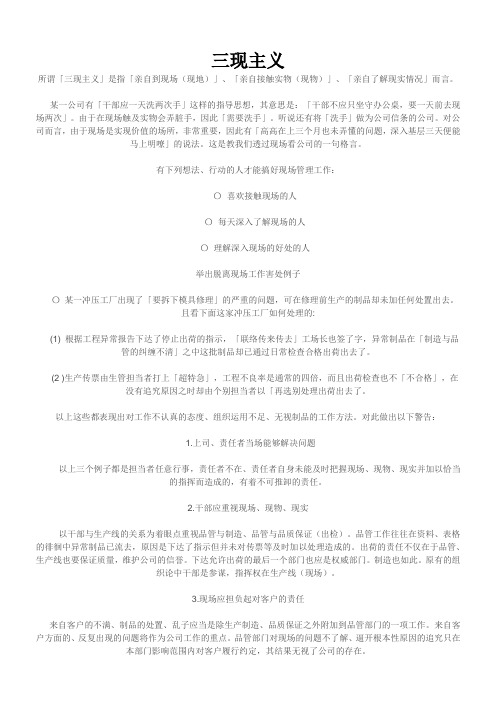
三现主义所谓「三现主义」是指「亲自到现场(现地)」、「亲自接触实物(现物)」、「亲自了解现实情况」而言。
某一公司有「干部应一天洗两次手」这样的指导思想,其意思是:「干部不应只坐守办公桌,要一天前去现场两次」。
由于在现场触及实物会弄脏手,因此「需要洗手」。
听说还有将「洗手」做为公司信条的公司。
对公司而言,由于现场是实现价值的场所,非常重要,因此有「高高在上三个月也未弄懂的问题,深入基层三天便能马上明嘹」的说法。
这是教我们透过现场看公司的一句格言。
有下列想法、行动的人才能搞好现场管理工作:〇喜欢接触现场的人〇每天深入了解现场的人〇理解深入现场的好处的人举出脱离现场工作害处例子〇某一冲压工厂出现了「要拆下模具修理」的严重的问题,可在修理前生产的制品却未加任何处置出去。
且看下面这家冲压工厂如何处理的:(1) 根据工程异常报告下达了停止出荷的指示,「联络传来传去」工场长也签了字,异常制品在「制造与品管的纠缠不清」之中这批制品却已通过日常检查合格出荷出去了。
(2 )生产传票由生管担当者打上「超特急」,工程不良率是通常的四倍,而且出荷检查也不「不合格」,在没有追究原因之时却由个别担当者以「再选别处理出荷出去了。
以上这些都表现出对工作不认真的态度、组织运用不足、无视制品的工作方法。
对此做出以下警告:1.上司、责任者当场能够解决问题以上三个例子都是担当者任意行事,责任者不在、责任者自身未能及时把握现场、现物、现实并加以恰当的指挥而造成的,有着不可推卸的责任。
2.干部应重视现场、现物、现实以干部与生产线的关系为着眼点重视品管与制造、品管与品质保证(出检)。
品管工作往往在资料、表格的徘徊中异常制品已流去,原因是下达了指示但并未对传票等及时加以处理造成的。
出荷的责任不仅在于品管、生产线也要保证质量,维护公司的信誉。
下达允许出荷的最后一个部门也应是权威部门。
制造也如此。
原有的组织论中干部是参谋,指挥权在生产线(现场)。
3.现场应担负起对客户的责任来自客户的不满、制品的处置、乱子应当是除生产制造、品质保证之外附加到品管部门的一项工作。
品质管理三现五原则

品质管理三现五原则嘿,朋友们!今天咱们来聊聊品质管理的三现五原则,这可不像听起来那么枯燥哦。
先说说三现吧,所谓三现就是现场、现物、现实。
这就好比是破案,现场就是犯罪现场,那是所有线索的源头。
要是品质出了问题,你不到现场去,就像侦探光靠想象猜犯人一样不靠谱。
现场就像是一个充满秘密的魔法阵,每个角落都可能藏着解开品质谜题的关键。
现物呢,就是这个魔法阵里的魔法道具啦,那些产品、零部件就像是有话要说的小物件,你得仔细端详它们,就像端详宝藏一样。
而现实呢,就是要面对真实发生的情况,不要自欺欺人,别以为在办公室里瞎琢磨就能搞定品质问题,那是不可能的,这就像你想知道鱼的滋味,却只看画一样荒谬。
再来说说五原则,那可是品质管理的五大神器。
第一个原则就像是给品质问题照X光,要查明原因。
这原因啊,就像调皮的小怪兽躲在暗处,你得拿着放大镜,把它揪出来。
有时候原因可能超级复杂,就像一团乱麻,你得耐心地一点点解开。
第二个原则是要采取措施,这措施就像是超级英雄的技能。
针对那些品质小怪兽,得使出对应的绝招。
要是问题是个大恶魔,你还慢悠悠地出招,那就等着品质灾难降临吧,就像面对洪水只拿个小勺子舀水一样可笑。
第三个原则是要确认效果。
这就像是考完试看成绩一样,你得看看你那些超级英雄的招数有没有打败小怪兽。
如果没效果,那就像放了个哑炮,白忙活一场。
第四个原则是要标准化,这就像把成功的魔法咒语记录下来,让所有人都能照着做。
要是不标准化,就像每个人都按照自己的想法做菜,那做出来的味道肯定千奇百怪,品质也就乱套了。
最后一个原则是要防止再发生,这就像是给品质城堡修个坚固的城墙。
不能让那些问题小怪兽再次入侵,要是不做好防范,就像补了东墙西墙又破了,永远在救火,忙得晕头转向。
品质管理的三现五原则啊,其实就是一场和品质问题斗智斗勇的有趣游戏。
我们得像勇敢的探险家一样,在现场这个神秘的世界里,通过现物这个神奇的媒介,找到现实中的答案,再挥舞着五原则这五把宝剑,把品质管理得妥妥当当。
8D报告三现五原则

通过充分掌握实时情况环节,查明异常变化点,确定要因,确定真因,查明真因
为下个环节做准备 b.查明真正原因的步骤:
4M目的:通过4M分析 找出变化点
5W目的:在4M分析处 变化方向后,找出变化 点,深入挖掘问题真相
4M+1M+1E 人(MAN) 机(MACHINE) 材料(MATERIAL) 制造方法(METHOD) 测量(MEASUREMENT) 环境(ENVIROMEN)
4、可以容易地评价针对每一 步所采取的行动是否是最妥 切的。
5、将为解决问题所开展的活 动内容作为技术诀窍记录下 来,不断地积累技术经验。同 时,便于向领导汇报,向相
关部门传达。
6、减少问题再次发生的次数
一、三现五原则定义
“五原则”是指从“三现主义”(现场、现物、现 实)出发,分五个步骤解决问题。
三.三现五原则注意事项
1.无科学根据的数据之解析对策
疑 问 点:常发生的直觉判断 ~ 焊接强度不足对策:焊道加长2mm.正确吗? ~ 模温不足变形对策:模温提高10℃.没问题吗?
思 考:加长2mm、提高10℃如何得到的? 直觉+经验≠事实 100个直觉或经验不如1个数据
分析方法:科学的根据=实验数据 ~ 有实验的数据才能决定新的标准。 ~ 要去试验出焊道加长2mm及模温提高10℃是作业最好的条件。
质量管理三现五原则

2-B 查明原因(发生的途径、问题再现试验WHY WHY分析)
3 采取)适当的对策 (对策内容、效果预测PPA) 4确认(对策)效果(效果实绩) 5对(问题)源头的反馈(需落实到体制、组织的内容)
15、案例
右腕受伤
1- A 发生状况(现象、申诉内容、发生次数、5W1H处置内容)
1、发生场所:汽缸压铸NO.2生产线。 2、 发生状况:请参照右手腕受伤素描图
检验: 为何会检测不出来。
10、五层分析
意义:为什么之五层分析是一个形容 词,代表追根究底的意思,其目 的在寻求真正的原因,并不是一 次要作五次为什么分析,可以比 五次少,也可以比五次多,只要 能寻求出真正的原因。
10、五层分析
实例说明: 不良现象:踩刹车时有上、下作动感觉。
1
2
3
4
5
目视检查
为什 Drum内 未检查
3、五层分析是三现五原则单之中 心思想及布局。
11、要因 对策案例练习
1.要因:人为疏忽 对策:教育训练加强
2.要因:XX治具磨损 对策:更换新治具
3.要因:遗漏焊接 对策:后工程实施全检以确保
4.要因:半成品因台车太小不慎流入后工程 对策:台车修改加大
5.要因:修护车辆,等待时间长 对策:等待时间提供杂志阅读
1、把握现况 - 5W2H
WHERE 何地 – 记入问题发生的场所。 WHY 为什么 – 具体的内容 HOW 怎么样 – 问题是怎样发生的 HOW MANY 什么程度 – 问题发生量,
程度。
1、把握现况的填写方法
1、问题点的概要(信息的收集、整 理)。例:针对部品或工程。
2、问题再现试验的结果 3、现行品(现在生产)的品质状况 4、发生的对象范围
三现五原则

Drum内 未检验 为何 径黑皮
铸造时
热不均匀 (500↑℃)
之五 产生 层分 析
Drum内径 Drum加热 尺寸NG 变形
模具与
模具磨损
Drum间隙
过大
6
无温度 控制 (180200℃)
无原则 要求
10、五层分析
1、五层分析是三现五原则原因解 析之浓缩要点内容。
2、五层分析是同说故事一样,故 事必须连贯。
11、要因 对策案例练习
6. 要因:涂装后之成品受落尘污染 对策:将成品以防尘套保护
7. 要因:锁付之螺丝易松动 对策:螺丝追加LOCKTITE涂布
8. 要因:宿舍被单送洗频度高易破损 对策:送洗频度由15天/1次→30天/1次
9. 要因:检验疏忽 对策:首末件检验→全检
10.要因:焊接后H方向尺寸NG 对策:焊接治具H方向调整
3、五层分析是三现五原则单之中 心思想及布局。
11、要因 对策案例练习
1.要因:人为疏忽 对策:教育训练加强
2.要因:XX治具磨损 对策:更换新治具
3.要因:漏掉焊接 对策:后工程实施全检以确保
4.要因:半成品因台车太小不慎流入后工程 对策:台车修改加大
5.要因:修护车辆,等待时间长 对策:等待时间提供杂志阅读
制程变异应从制程面去改善
5、变化点分析不清楚
疑 问 点:此前为何不会发生不良,目前才发生? 一定是哪里有变更,变化点在哪里?
思 考:不良隐藏於变化点中。
分析措施:4M1D里寻找真因 人[Man]:人员有否更换,有否依原则作业、人员之 士气等。 机[Machine]:机器设备、镆、治、检、工具有否调 整、变更等。 料[Material]:材料有否变化、前工程流入件不良事 等。 措施[Method]: 原则有否要求?原则是否明确? 设计[Design]: 是否设计变更等。
- 1、下载文档前请自行甄别文档内容的完整性,平台不提供额外的编辑、内容补充、找答案等附加服务。
- 2、"仅部分预览"的文档,不可在线预览部分如存在完整性等问题,可反馈申请退款(可完整预览的文档不适用该条件!)。
- 3、如文档侵犯您的权益,请联系客服反馈,我们会尽快为您处理(人工客服工作时间:9:00-18:30)。
为了使在调查过程中不要遗漏有用的信息和重要事实,要 多听、多看(严禁带有成见)在确认过程中尽可能地使用(3 现实主义),在进行原因分析时,要最大限度使用“特性要素 图”
现状把握举例:
1、 3、 4、 6、 机种、型号 2、 发生状况:(市场、公司内) 问题发生时的现象或(当事人的)申诉 发生年月日 5、 发生件数 对发生问题机种或是零部件的处置结果。
五原则三----对策实施
临 时 对 策 适 当 对 策 (防止恶化扩大) 永 久 对 策 (避免再发) •已流入市场处理 •库存成品处理 •半成品处理 •不良品处理 •制造面、流出 面之治本对策 •水平展开对策 •工程作业者 •进料检验者 •市场服务者 (品质通报)
对策情报传达
适当的对策(对策内容、效果预测PPA)
為什 麼之 飾條素材 五層 產生縮水 分析
2
目視檢查時 未檢查
3
無檢查基準
4
加熱不均 勻 模具損壞
5
溫度控 制損壞 未按規 定檢查
射出時素材加熱 飾條素材表 變形 面NG 模具與飾條間隙 過大
1、五層分析是三現五原則原因解析之濃縮重點內容。 2、五層分析是同說故事一樣,故事必須連貫。 3、五層分析是三現五原則單之中心思想及佈局。
不良实物
不良发生的状况, 包括使用状况 不良品发生的原 地、环境因素
五原则一--------现状把握
现状把握目的 针对问题,全盘调查事实掌握变异(机遇/非机遇原因)归纳可 疑方向 对事实的把握(现在生产的该零部件的品质状况、现象、问题 内容、发生次数、5W2H处置内容)
现状把握内容
1、问题点的概要(信息的收集、整理)例,针对部品或工程。 2、问题再现试验的结果 3、现行品的品质状况 4、发生的对象范围 5、利用绘图、图表、柱状图使问题明确化。 6、将可能想到的原因、内容,详尽的进行整理,在记录上明 确的记载。
1 2 3 4 无检查基准 铸造时Drum 加热变形 模具与Drum 间隙过大 5 温度过高加 热不均匀 (500↑℃) 模具磨损 6 无温度 控制 (180200℃) 无标准 规定
目视检查 为什 Drum内 未检查 么之 径黑皮 Drum内径 五层 产生 尺寸NG 分析
Байду номын сангаас
實例說明: 不良現象:車門板上、下作動異音 1
9、制造面、流出面未检讨
疑 问 点:1.为何会流出?为何会制造出?为何设备检不出? 2.流出面之解析对策经常被疏忽。 思 考:顾客所反应之问题必定制造面、流出面共同发生, 仅对策制造或流出面并未能彻底解决问题。 分析方法:1.制造面→分析4M之变化点→真因对策。 2.流出面→a.分析制程中之流程→作业环境、作 业检验工程标准。 b.分析检验之流出→出货检验标准、 限度样品、自动检测、防呆装置。 PS: 为何会检测不出来。
Ψ.這種人姓“賴”,什麼事都敢推開,所
有的不良品全都不關自己的事,推脫理由多得讓 人
難以置信.要麼是自己從來沒學過;要麼是前輩
沒教好;要麼同事“坑”了自己……總能打出一 個冠冕堂皇的理由.
Ψ.其實質是能力不足,不願承擔自己的責任.讓
這種人解決不良品,不良品還沒動一根“毛”, 內部責任追究的“戰火”早已熊熊燃起,結果只 會導致各部門內戰不休,分散了團體的力量,事 情越辦越亂. C.孤芳自賞型. 孤芳自賞
制程变异应从制程面去改善
5、变化点分析不清楚
疑 问 点:以前为何不会发生不良,现在才发生? 一定是哪里有变更,变化点在哪里? 思 考:不良隐藏於变化点中。
分析方法:4M1D里寻找真因 人[Man]:人员有否更换,有否依标准作业、人员之 士气等。 机[Machine]:机器设备、镆、治、检、工具有否调 整、变更等。 材[Material]:材料有否改变、前工程流入件不良等。 方法[Method]: 标准有否规定?标准是否明确? 设计[Design]: 是否设计变更等。
6、无回馈标准
疑问点:如何保证以后不会再发?或这样对策就不会再发吗? 欠了什么。 思 考:1.作业者不知道、不清楚、则不良问题仍然会再发生, 所以让作业者明白如何才能做良品是非常重要的。 2. 标准回馈 作业者知道 明确 如何去做
3.作业标准四项重点:内容、手顺、时间、结果。 4.重要之标准类:作业标准、图面、零件检验标准、 QC工程表、试验规范、规章、标 准样品。 5.保证不会再发: 真因 对策 回馈标准 是不二法门。
在把握事实的基础上,利用5W2H法对需要的信息 进行调查并使之明确化。 WHO 谁 – 类型、种类、受影响的部分。 WHAT 什么 – 问题的症状,尽可能使用图表, 将问题表达清楚。 WHEN 何时 – 记入问题发生的日期。 WHERE 何地 – 记入问题发生的场所。 WHY 为什么 – 具体的内容 HOW 怎么样 – 问题是怎样发生的 HOW MUCH 什么程度 – 问题发生的量,程度。
A.自我放棄型. 自我放棄 這種人一旦遇上不良品,第一句話就是 “算了吧!做不到!不可能!”對不良品惟恐避之 而不及,對不良品的解決方法想都不想,一把將 不良品推開老遠. 其實質是自信不足,害怕不良品,怕承擔風 險,責任.讓這種人去處理不良品,只會越處理越 多,小則辦壞一件事,大則拖垮一個部門. B.歸咎他責型. 咎他責
三、三现五原则手法
为找到问题的根本原因,系统的解决问题,我们需要一 个解决品质问题的标准作业手法,以下将介绍一种用于解决 生产现场品质问题的解决手法------三现五原则 何谓“三现五原则”: 三现: 现场、现状、现物 五原则: 把握现状、原因分析、对策实施、效果确认、回馈标准
三
现
现物 三现 现状 现场
8、无三现
疑 问 点:有至现场去看吗?有否实车确认、实物、 实地确认? 说 明:1.杂志与资讯:未三现,可能会得到错误之 讯息,或疏略重点资讯。 2.选择性事实:三现的目的,在於针对问题, 全盘掌握事实,而未三现,可能仅知道部份 事实。 3.有三现,才能相信自己,说服别人。
解析对策必须遵守三现主义
三现五原则手法讲解
---提高品质问题的解析能 力
目
一、不良品的对应
1、不良品定义 2、对待不良品的四种态度
录
6、无回馈标准 7、再现试验证明 8、无三现 9、制造面、流出面未检讨
二、处理不良的错误观念
1、无科学根据DATA 2、以偏概全 3、增加不必要成本 4、以变更设计改善制程变异 5、变化点分析不清楚
3、增加不必要成本
疑 问 点:利润很高吗?增加成本没关系吗? 说 明:1.利润=售价-成本 成本UP,自然利润降低。 2.解析对策成本面结果有三种: a.成本UP:需有UP的合理原因,需检讨合理与不合理 b.成本不变动 c.成本下降:GOOD 3.成本UP部份由厂商吸收,虽然不影响SY,但对总体 成本仍是上升的,亦非好之对策。
♣ 開拓進取的態度是作為優秀的管理人員
必備的條件之一.
二、处理不良的错误观念
1、无科学根据DATA
疑 问 点:常发生的直觉判断 ~ 焊接强度不足对策:焊道加长2mm.正确吗? ~ 模温不足变形对策:模温提高10℃.没问题吗? 思 考:加长2mm、提高10℃如何得到的?
直觉+经验≠事实
100个直觉或经验不如1个数据 分析方法:科学的根据=实验数据 ~ 有实验的数据才能决定新的标准。 ~ 要去试验出焊道加长2mm及模温提高10℃是作业最好的条件。
7、再现试验证明
疑 问 点:你如何知道解析不良原因是正确的吗? 思 考:科学的实验是最好的证明→再现试验。 分析方法:正向再现与反向再现。 1.正向:将不良要因排除(不良条件修正)后会制造 出良品。 2.反向:以不良条件生产会制造出不良品。 若上述二向再现结果与假设违背,则肯定 所解析出之不良原因必定有偏差。 3.不良品再现。
三、三现五原则手法
1、三现 2、五原则 3、案例讲解
一、不良品發生先別慌
不良品是指: 1、不良品是指: 不能滿足规格要求的產品. . 消除不良品,原本就是管理工作的一部份, 經歷的越多,經驗越能得到積累;管理能力越能 得到提升.
2、不良品是萬嚴之首.管理的歷史可以說就是一部 與不良品作斗爭的歷史,只要有生產活動存在,就有 不良品的存在.不良品是測試管理人員合不合格的 最好“考題”之一,誰也躲不開.但是,面對同樣一 種不良,卻有四種不同的態度.
Q&A是5原则的关键: 1、在进行Q&A时,最重要的是提出正确的问题。 2、如果错误的提问,就会得出错误的答案,无法掌 握真因。在进行Q&A时经验会成为帮助,而重要的 还是理解Q&A的做法。 3、即使是经验少的人,如果能正确实行Q&A,也能 够发现真因。
实例说明: 不良现象:踩刹车时Brake Pedal有上、下作 动感觉。
五原则二-----原因分析
用特性要因图,利用Q&A (提问和回答)的”WHY WHY”分析;再现试验,抓 住真正的原因 查明原因 4M分析 5W分析法 特性要因图 查明原因 再现试验 NG再现 OK再现 不良再现 不良原因 查明原因 流出原因 问题 要因 真因 (流出面) (制造面)
原因分析之再现试验: (1).模擬法.將生產相同組合的生產要素,確認能 否導致同一不良現象. (2).配對法.將生產要素按一定的條件進行組合, 確認哪種組合出現相同不良. (3).排除法.將生產要素逐個進行替換,當替換到 不良消失時,多半是該生產要素引發的不良. (4).對比法.將良品與不良品進行比較,找出其中 差別之處,這種差別很可能就是造成不良的原因.
原因分析之WHY WHY分析: 意义:为什么之五层分析是一个形容词,代表追根 究底的意思,其目的在寻求真正的原因,并不是 一次要作五次为什么分析,可以比五次少,也可 以比五次多,只要能寻求出真正的原因。 1、五层分析是三现五原则原因解析之浓缩重点内容。 2、五层分析是同说故事一样,故事必须连贯。 3、五层分析是三现五原则单之中心思想及布局。 4、WHY、WHY的分析要从问题发生的原因(或叫硬件方 面的原因)和流出原因(又叫软件方面的原因)两 方面进行。 5、WHY、WHY分析的信息来源,基本上是以特性要因 图为基础。 6、为了说明真因,可以加入插图。