铬铁矿的还原焙烧过程
德国铬铁矿无钙焙烧概况
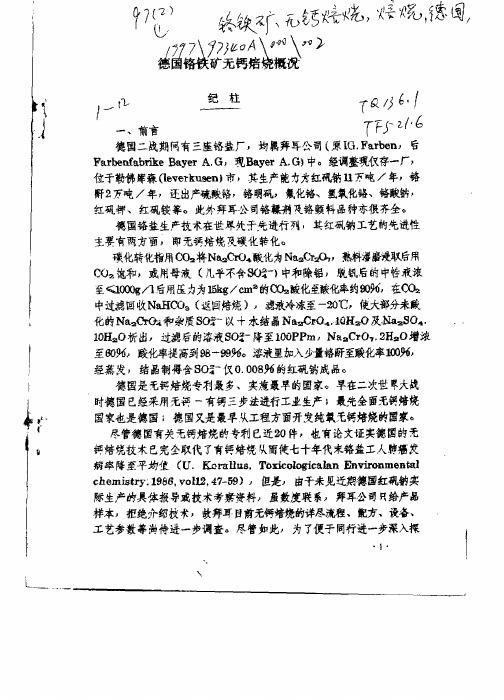
五、控制80 /A 。 。 i 。 l0 比的无钙培烧 有钙焙烧时,硅铝形成l点高、难溶于水的硅酸葛、铝酸钙等化 熔 合物。 无钙焙境对 硅铝 除生成熔点高、不术溶的的铝硅 酸盐 (a k O 或N  ̄ 盘毛 l N A  ̄ . aMg s 2)外 若铬矿中枣质S0 / 1 i 0 il A2 2 犀尔
D l4 6 用 10 E 2 3的 0 毋铬矿同8 份纯碱 、5 廿 4 6 返渣的麓合物于 90 5—
1 0 连续焙蛲。熟料逆流浸洗。选后的渣月水打成含固20 /l 1 0 0g 的 浆敢, 耿忉匿 扫 ( n 火气压 )送旋液分离器 为粗细两半。枉浆滤舌 烘干怍返渣循环陡用。细渣排敷。 矿I粗蜘渣组成见表2 ! 己 。
料喷Na H 溶液 )。 O
三、足碱_步晓成和浸渣旋l 离 二 液
德国大部分无镑培烧专利为足碱一步蛲麻泛 配碱率为理论量
10 。其填科一般用近渣 育的也用氧化 0 ̄ 或黄最矿蛲制碗酸后
的尾渣 ( 主要盛份为F 2 e0 ),为了 减少返渣P 硅、铝,使渣巾适于 作填料的键铁矿及未反应的铬铁矿富集 穗副爱 先栗用旋液分离o
故不会烧结,用螺旋输料机推入回转窑的反应带.安有喷嘴的糯碱管
’
4‘
.
从窑胁 至 ( 露尾约l 窑长的 )反应带 N O- Nac 8 /3 a I ̄ I 2 O 水溶液从
喷嗜 以细 蓦 . 吨洒在随窑运动着 的热粉料上 ,迅 即发生一 系列物理化学
变化 ( 蒸发,h H变Nac 。 2! ,升温、碱解、氧化… )形成小球粒一 O
发 <7m. C 6 7娜, F C 5 分C .5 用 e 解毒吉社减: 龃渣∞ 杜蹙 》1 U 鼬 , 含 z a 细渣的2 , 作返渣循环 。 从楹细渣含 O是 倍
高碳铬铁生产技术

高碳铬铁生产技术
高碳铬铁是一种重要的合金原料,广泛应用于钢铁行业。
高碳铬铁生产技术一般包括以下几个步骤:
1. 原料准备:选择合适的铬铁矿石和碳素材料,通常使用高质量的铬铁矿石和焦炭作为原料。
2. 矿石炼烧:将铬铁矿石进行炼烧,以消除矿石中的杂质,并使其达到一定的还原程度。
3. 原料混合:将炼烧后的铬铁矿石和碳素材料混合均匀,按照一定的配比要求,通常是铁矿和焦炭的比例为2:1。
4. 熔炼过程:将混合好的原料加入高温炉中进行熔炼,通常使用电弧炉或高炉进行熔炼。
在熔炼过程中,要控制好熔炼温度和炉内气氛,以确保合金的成分和质量。
5. 合金调整:根据需要调整合金的成分,并加入适量的合金添加剂,如硅、硫、锰等,以提高合金的性能。
6. 出炉和铸造:熔炼完成后,将熔融的高碳铬铁倒入模具中进行凝固和铸造,得到固态的高碳铬铁块。
7. 冷却和检验:将铸造好的高碳铬铁块进行冷却,然后进行质量检验,检查合金的成分和物理性能是否符合要求。
以上就是高碳铬铁生产技术的一般步骤,不同的生产厂家和工
艺可能会有一些差异,但总体上大致相同。
高碳铬铁的生产过程需要有一定的专业知识和技术,以确保合金的质量和性能。
铬铁合金生产过程

铬铁合金生产过程铬铁合金是一种由铬和铁混合而成的合金,主要用于生产高速钢和不锈钢等材料。
它具有耐蚀、高温稳定等优良性能,在现代工业中具有广泛应用。
以下是铬铁合金的生产过程。
1. 原料准备:铬铁合金的主要原料是铬铁矿和冶金焙烧石灰石。
铬铁矿是一种含有铬和铁的矿石,一般含有60%以上的铬和20%以上的铁。
冶金焙烧石灰石是一种用于冶金生产的石灰石,主要成分是氧化钙和氧化镁。
2. 熔炼制备:将铬铁矿和焙烧石灰石按比例混合后送入高炉熔炼。
高炉是一种大型的冶金设备,用于熔化铁矿石及其他原料,生产熔铁和熔渣。
在高温下铁矿石和焙烧石灰石会相互作用,生成铁和熔渣,并逐步还原出铬铁合金。
3. 分离铬铁合金:熔铁与熔渣在高炉的底部分层,铬铁合金则随熔铁一起流出高炉。
铬铁合金在熔铁中的比例一般很少,需要进行进一步的分离。
一种常用的方法是将熔铁倒入钢包,通过真空蒸馏将铬铁合金和其他杂质分离。
经过多次蒸馏,铬铁合金的含量逐渐提高。
4. 淬火处理:铬铁合金具有较高的硬度和韧性,但通常需要进行淬火处理来提高其性能。
淬火是一种快速冷却的工艺,可以使合金组织变硬、细化,同时提高其耐磨性和强度。
淬火处理可以通过水淬、油淬或空气冷却等方式完成。
5. 精炼处理:经过分离和淬火处理后,铬铁合金中的杂质和其他不纯物质的含量仍然较高。
为了进一步提高其纯度和质量,需要进行精炼处理。
精炼处理可以通过真空吸氧、气体浮选、磁选等方式进行。
精炼处理之后的铬铁合金,其纯度和品质均得到了提升。
6. 包装出厂:经过精炼处理后的铬铁合金,需要进行包装和出厂。
一般将铬铁合金装入钢桶中,密封包装后运输至下游生产厂家,供其生产各种合金材料和产品。
以上就是铬铁合金的生产过程。
该合金生产过程复杂,需要严格掌控各个环节,以确保生产出高质量的合金产品。
铬铁矿的还原焙烧过程

铬铁矿的还原焙烧过程铬铁矿的还原焙烧过程1、焙烧温度对铬铁矿还原焙烧效果的影响图1铬铁矿经不同温度下焙烧120min后所得产物的SEM图像图1为铬铁矿在不同焙烧温度下还原120min后产物表观形貌的SEM图像。
从图中可以看出,当焙烧温度为950℃时,矿石颗粒表面存在明暗不同两相,但相互分离并不彻底,相界面难以辨别。
温度为1050℃时,明亮物相与相对较暗物相己能够明显分辨,且较950℃时体积有所增大。
当温度升至1150℃时,明亮物相由球状发展为棒条状。
通过EDS检测可知,明亮物相为还原析出相,其主要成分为金属铁、金属铬和少量的碳,较暗物相为铬铁矿基体相。
不考虑各析出相中的碳元素,排除相分离尚不充分的950℃还原产物,可将其他试样析出相中铁和铬的比例关系绘如图2。
由图2可知,在1050℃和1100℃时,析出相中主要成分为铁元素,而当温度升至1150℃时,铬元素成为析出相的主体元素。
由此可以得出在950-1100℃的范围内主要发生的是铬铁矿中铁的还原,铬仍存在于矿石基体中。
当焙烧温度达到如1150℃时,大量的铬被还原为金属态进入析出相,证明在此温度下部分含铬尖晶石相参与了还原反应。
实验所得结论与热力学分析结果一致。
图2 不同焙烧温度下还原120min后析出相金属元素组成图3为Factsage软件计算得出的1100℃和1150℃下Cr-Fe-C-O系优势区域图。
在1100℃时,常压线(由“+”组成)穿过了优势区域图中的灰色区域()和浅灰色区域(),意味着从热力学角度讲,当石墨增锅内气压为1 atm时Cr2O3和Fe(或Fe3C)可以作为还原产物共存。
当温度为1150℃时,常压线穿过了深灰色区域(Cr3C2+Fe),说明在此温度下铬会被大量还原为金属态,并以碳化物的形式存在。
此时,选择性还原铬铁矿中铁元素的目标难以实现。
另外,从图中还可得出,当体系中二氧化碳分压很低时(如反应的初始阶段Cr3C2会与Fe3C共存于析出相。
工业上以铬铁矿为原料冶炼铬的流程

工业上以铬铁矿为原料冶炼铬的流程
以铬铁矿为原料冶炼铬的流程一般包括以下几个步骤:
铬铁矿矿石选矿:铬铁矿矿石经过进料筛、自动倾斜筛、磁选机等设备进行选矿,去除杂质,得到经过选矿的矿石。
矿石烧结:将选好的矿石放入烧结炉中,加入适量的烧结剂,经过高温烧结,使矿石中的铬氧化物转化为铬酸钾。
铬酸钾提炼:将烧结好的铬酸钾与氢氧化钾混合,加入碱溶液进行提炼,得到浓缩的铬酸溶液。
铬酸溶液还原:将浓缩的铬酸溶液经过还原剂还原,得到纯铬。
纯铬熔炼:将得到的纯铬加入熔炼炉中,经过高温熔炼,得到铬块
铬块加工:将得到的铬块经过加工设备进行切割、拉伸、冷却等工序,得到各种规格的铬板、铬线、铬棒等。
铬板、铬线、铬棒等加工:将得到的铬板、铬线、铬棒等经过冷却、切割、拉伸、热处理等工序,得到各种规格的铬件。
铬件使用:铬件可用于制造各种铬合金零件,如汽车零件、航空零件、医疗器械等,也可用于制造铬涂层,如铬涂层铸件、铬涂层管道等。
铬铁矿氧化焙烧动力学

铬铁矿氧化焙烧动力学李小斌;齐天贵;彭志宏;刘桂华;周秋生【摘要】用于铬盐生产的传统无钙焙烧过程存在铬氧化率低的问题,严重影响铬的生产效率和回收率.为强化铬铁矿氧化焙烧过程,对铬氧化过程的动力学规律及其氧化反应机理进行了研究.结果表明:铬铁矿氧化焙烧过程,铬的氧化反应分为初期和后期两个阶段,初期铬氧化速率快,后期铬氧化速率慢,在优化条件下,铬(Ⅲ)的氧化率可达99%以上;两个阶段铬的氧化反应均符合收缩未反应核动力学模型且受表面化学反应控制,铬氧化反应初期和后期的表观反应活化能分别为68.7和231.8 kJ/mol;反应初期是铬铁矿直接与碳酸钠和氧气发生反应生成铬酸钠,而后期则是铬铁矿与反应初期生成的铁酸钠和氧气发生反应生成铬酸钠.【期刊名称】《中国有色金属学报》【年(卷),期】2010(020)009【总页数】7页(P1822-1828)【关键词】铬铁矿;铬酸钠;氧化焙烧;动力学【作者】李小斌;齐天贵;彭志宏;刘桂华;周秋生【作者单位】中南大学,冶金科学与工程学院,长沙,410083;中南大学,冶金科学与工程学院,长沙,410083;中南大学,冶金科学与工程学院,长沙,410083;中南大学,冶金科学与工程学院,长沙,410083;中南大学,冶金科学与工程学院,长沙,410083【正文语种】中文【中图分类】TF111Abstract:The traditional lime-free roasting process used for manufacturing chromate from chromite ore has low oxidation rate which impact the chromate production efficiency and chromium recovery rate seriously. To intensify the oxidation roasting process of chromite ore, the oxidation kinetics and its mechanism were studied. The results show that there are two stages for the oxidation roasting process of chromite ore. The oxidation reaction is very rapid in the initial stage but quite slow in the later stage. The oxidation rate of chromium(Ⅲ) in chromite ore can reach more than 99%under the optimized conditions. The whole oxidation process of chromite ore follows the shrinking unreacted core model,andthe surface chemical reaction is the controlling step. The apparent activation energies of the initial and later stages are 68.7 and 231.8 kJ/mol, respectively. And the sodium chromate is produced by the reaction of chromite with sodium carbonate and oxygen in the initial stage, whereas sodium chromate is formed by the reaction of chromite with sodium ferrite formed in the initial stage and oxygen in the latter stage.Key words:chromite ore; sodium chromate; oxidation roasting; kinetics铬铁矿氧化焙烧法几乎是铬盐生产的唯一方法,其中分为有钙焙烧法和无钙焙烧法,它们都是将铬铁矿与纯碱在高温氧化条件下进行焙烧,使矿石中的铬转化为水溶性的铬酸钠经浸出等后续处理获得铬盐产品[1−3]。
冶炼铬铁生产实践报告(2篇)
第1篇一、引言铬铁是一种重要的合金材料,广泛应用于不锈钢、高速钢、模具钢、耐热钢等合金钢的生产中。
铬铁的生产工艺主要包括铬铁矿石的选矿、熔炼和精炼等环节。
本报告以我国某铬铁生产企业为例,对冶炼铬铁的生产实践进行详细分析,以期为铬铁生产提供参考。
二、生产流程1. 铬铁矿石的选矿(1)原料准备:将铬铁矿石破碎至一定粒度,以满足后续选矿工艺的要求。
(2)选矿工艺:采用浮选法进行选矿,将铬铁矿石中的有益成分与有害成分分离。
(3)精矿制备:通过磁选、重选等方法,进一步富集铬铁精矿。
2. 铬铁熔炼(1)原料准备:将选矿得到的铬铁精矿与适量的焦炭、石灰石等熔剂混合。
(2)熔炼工艺:采用电炉熔炼,将混合原料加热至熔化状态,进行熔炼。
(3)炉前操作:根据生产要求,对熔炼过程进行调节,确保铬铁质量。
3. 铬铁精炼(1)原料准备:将熔炼得到的铬铁熔体进行浇铸,得到初炼铬铁。
(2)精炼工艺:采用真空精炼、脱硫、脱磷等方法,提高铬铁的纯度。
(3)炉后操作:对精炼后的铬铁进行检验,确保其质量符合标准。
三、生产实践分析1. 生产设备(1)选矿设备:主要包括颚式破碎机、球磨机、浮选机等。
(2)熔炼设备:主要包括电炉、配料系统、炉前操作设备等。
(3)精炼设备:主要包括真空精炼炉、脱硫设备、脱磷设备等。
2. 生产工艺(1)选矿工艺:采用浮选法进行选矿,具有较高的选矿效率。
(2)熔炼工艺:采用电炉熔炼,具有较高的熔炼效率。
(3)精炼工艺:采用真空精炼、脱硫、脱磷等方法,确保铬铁质量。
3. 生产管理(1)人员管理:加强员工培训,提高员工操作技能和安全生产意识。
(2)设备管理:定期对生产设备进行维护保养,确保设备正常运行。
(3)质量管理:严格执行生产工艺和质量标准,确保产品质量。
四、存在问题及改进措施1. 存在问题(1)选矿效率有待提高:部分选矿设备老化,影响选矿效率。
(2)熔炼过程能耗较高:电炉熔炼过程中,能耗较高。
(3)精炼过程存在污染:真空精炼过程中,可能产生有害气体。
铬铁矿还原焙烧预处理工艺
铬铁矿还原焙烧预处理工艺铬铁矿还原焙烧工艺在冶金领域中应用广泛,是生产铬铁和含铬合金的主要方法。
此工艺是将铬铁矿粉与碳质还原剂进行混合,在1000℃以上的高温炉中进行碳热还原反应,从而使稳定的尖晶石结构得到完全破坏。
本研究在传统还原焙烧工艺的基础上,以热力学计算为指导,对不同焙烧条件的还原产物进行综合分析,探索是否存在铁氧化物选择性还原,铬元素富集的可能。
此外,本研究还重点分析了预处理工艺对于铬铁矿中尖晶石结构转变行为的影响规律。
1热力学分析传统的还原焙烧工艺是将铬铁矿的尖晶石结构彻底破坏,令所有的金属元素在高温炉中还原为金属态。
本研究为确定各类尖晶石结构在还原焙烧过程中的稳定性进行了如下热力学分析。
由于Boudouard反应的存在,铬铁矿的还原焙烧往往受固体碳单质和气体一氧化碳的共同作用,通过数据查阅和计算整理,得出相关反应的热力学参数列于表1和表2,并绘制了关系图,如图1和2所示。
其中,在2000℃以下不与固体碳和一氧化碳发生还原反应,是铬铁矿中最为稳定的尖晶石结构。
表1 固体碳还原铬铁矿相关反应及其热力学参数表2 一氧化碳还原铬铁矿相关反应及其热力学参数由表1、表2、图1和图2可知,铬铁矿还原焙烧过程中,各物相的稳定性顺序为。
高温有利于尖晶石结构的破坏,(以℃计)在600℃左右即可发生还原反应,当温度升至1400℃时除外其他尖晶石相均可分解。
经分析还可发现,铬铁矿中含铁物相稳定性较含铬物相低,909℃时可出现金属态铁,但温度需达到1105℃才会出现金属态铬,并以碳化物的形式存在。
由此说明,从热力学角度讲,对尖晶石纯物质而言,通过控制还原焙烧温度,存在选择性破坏含铁尖晶石相,分离其中铁元素的可能。
此种预处理方式。
一方面能够起到铬铁预分离的效果,提高铬铁矿的m(Cr)/m(Fe),实现铬铁矿资源的综合利用,另一方面也会对铬铁矿中的铬元素适度富集。
图 1 铬铁矿尖晶石相焙烧反应关系图图2 铬铁矿还原所得氧化物和金属相焙烧反应关系图2实验方法2.1实验原料南非是铬铁矿资源储备的第一大国,也是中国最大的铬铁矿进口国,因此本实验选取南非铬铁矿为原料,其成分如表3所示。
铬铁冶炼工艺
铬铁冶炼工艺铬铁是一种重要的合金材料,广泛应用于不锈钢、合金钢等领域。
铬铁冶炼工艺是将铬矿石和铁矿石经过一系列的冶炼过程,将铬和铁合金化合成铬铁合金的过程。
这一工艺的发展历史悠久,经过不断的技术创新和改进,现代铬铁冶炼工艺已经相当成熟。
铬铁冶炼工艺的第一步是选矿,即从矿石中提取出含铬和含铁的矿石。
常见的铬矿石有菱铬矿、绿铬矿等,而铁矿石则有赤铁矿、磁铁矿等。
选矿的目的是通过物理或化学方法,将有用的矿石和杂质分离开来,以便后续的冶炼过程。
选矿完成后,接下来是炼铬炼铁。
炼铬通常采用炼铬炉,将铬矿石和还原剂(如焦炭)放入炼铬炉中,通过高温熔炼,使铬和铁相互还原生成铬铁合金。
而炼铁则是将铁矿石和燃料(如焦炭)放入高炉中,通过高温熔炼,将铁矿石中的氧化铁还原为金属铁。
炼铬炼铁完成后,将铬铁合金和铁合金按照一定的比例混合,得到所需的铬铁合金。
这一过程涉及到严格的配料和混炼工艺,以确保最终产品的质量符合要求。
铬铁冶炼工艺中的关键技术包括炼炉设计、还原剂选择、炉温控制等方面。
炼炉设计直接影响到冶炼效率和炼铬炼铁的质量,而还原剂的选择则关系到反应的还原性能和产物的纯度。
炉温控制是冶炼过程中非常重要的环节,过高或过低的温度都会影响到反应的进行。
随着科技的发展,铬铁冶炼工艺也在不断进步。
新型的炼炉设备、先进的自动化控制系统、高效的能源利用技术等都为铬铁冶炼带来了新的发展机遇。
同时,环保要求也促使铬铁冶炼企业不断优化工艺,减少废气、废水和固体废物的排放。
总的来说,铬铁冶炼工艺是一个复杂而精密的工程,需要多个环节的配合和协调。
只有不断进行技术改进和创新,才能使铬铁冶炼工艺达到更高的效率和质量,为不锈钢、合金钢等行业提供更好的原材料。
铬铁矿无钙焙烧的反应机理
铬铁矿无钙焙烧的反应机理纪柱(天津化工研究院,天津300131) 摘要 研究了铬铁矿无钙焙烧反应机理,得出配碱量高低及有无填料对氧化速度、硅铝的副反应均有显著影响;少碱和足碱焙烧的活化能分别为50.3及73.2kJ/K.mo l。
关键词 铬铁矿 铬酸钠 固相反应 反应动力学 活化能 铬矿无钙(不用白云石、石灰石等钙质填料)焙烧制取铬酸钠及其物相变化已有报导〔1、2〕,现将过程的反应机理作如下探讨。
实验用含Cr2O349.31%的铬铁矿(M g,FeⅡ)(Cr、Al、FeⅢ)2O4(可简写成M g Cr2O4及FeCr2O4),主要杂质为Mg、Fe、Si、Al。
使用含Na2CO399.88%的试剂纯碱。
所用填料为M gO及Fe2O31200℃合成的镁铁矿。
1 配碱率的影响1.1 主要反应铬铁矿无钙焙烧的主要反应有:M gCr2O4+2Na2CO3+32O22Na2C rO4+M gO+2C O2(1)…2FeCr2O4+4Na2CO3+72O24Na2C rO4+Fe2O3+4CO2……(2)…………………………………………………………………SiO2+Na2CO3Na2S iO3+CO2(3)………………………………Al2O3+Na2C O32NaAlO2+C O2(4)…………………………… 生成的Na2SiO3、NaAlO2作为Na原料还将进一步反应(式11~16),M gO及Fe2O3则生成镁铁矿M gFe2O4。
式(1,2)表明,每kg铬(以Cr2O3计)所需纯碱理论量为1.395kg。
实际配碱量与理论量之比称为配碱率,配碱率≤50%称少碱焙烧,>80%称足碱焙烧。
生成铬酸钠的碱与实际配碱量之比称为碱利用率。
1.2 无填料焙烧不用任何填料,铬矿仅与纯碱混合焙烧,其氧化率及碱利用率同配碱率的关系见图1。
熟料水溶Al2O3及可熔盐(焙烧温度下的熔液)同配碱率关系见图2。
氧化率曲线在配碱<50%时斜率大,>50%后斜率变小;碱利用率曲线在配碱(40~50)%处呈现极大值。
- 1、下载文档前请自行甄别文档内容的完整性,平台不提供额外的编辑、内容补充、找答案等附加服务。
- 2、"仅部分预览"的文档,不可在线预览部分如存在完整性等问题,可反馈申请退款(可完整预览的文档不适用该条件!)。
- 3、如文档侵犯您的权益,请联系客服反馈,我们会尽快为您处理(人工客服工作时间:9:00-18:30)。
铬铁矿的还原焙烧过程
1、焙烧温度对铬铁矿还原焙烧效果的影响
图1铬铁矿经不同温度下焙烧120min后所得产物的SEM图像图1为铬铁矿在不同焙烧温度下还原120min后产物表观形貌的SEM图像。
从图中可以看出,当焙烧温度为950℃时,矿石颗粒表面存在明暗不同两相,但相互分离并不彻底,相界面难以辨别。
温度为1050℃时,明亮物相与相对较暗物相己能够明显分辨,且较950℃时体积有所增大。
当温度升至1150℃时,明亮物相由球状发展为棒条状。
通过EDS检测可知,明亮物相为还原析出相,其主要成分为金属铁、金属铬和少量的碳,较暗物相为铬铁矿基体相。
不考虑各析出相中的碳元素,排除相分离尚不充分的950℃还原产物,可将其他试样析出相中铁和铬的比例关系绘如图2。
由图2可知,在1050℃和1100℃时,析出相中主要成分为铁元素,而当温度升至1150℃时,铬元素成为析出相的主体元素。
由此可以得出在950-1100℃的范围内主要发生的是铬铁矿中铁的还原,铬仍存在于矿石基体中。
当焙烧温度达到如1150℃时,大量的铬被还原为金属态进入析出相,证明在此温度下部分含铬尖晶石相参与了还原反应。
实验所得结论与热力学分析结果一致。
图2 不同焙烧温度下还原120min后析出相金属元素组成图3为Factsage软件计算得出的1100℃和1150℃下Cr-Fe-C-O系优势区域图。
在1100℃
时,常压线(由“+”组成)穿过了优势区域图中的灰色区域()和浅灰色区域(),意味着从热力学角度讲,当石墨增锅内气压为1 atm时Cr2O3和Fe(或Fe3C)
可以作为还原产物共存。
当温度为1150℃时,常压线穿过了深灰色区域(Cr3C2+Fe),说明在此温度下铬会被大量还原为金属态,并以碳化物的形式存在。
此时,选择性还原铬铁矿中铁元素的目标难以实现。
另外,从图中还可得出,当体系中二氧化碳分压很低时(如反应的初始阶段Cr3C2会与Fe3C共存于析出相。
所得结论进一步证实了上文所得分析与实验结果。
图3 不同温度下Cr-Fe-C-O系优势区域图
图4不同温度焙烧产物XRD谱图以及标准衍卡片
图4给出了铬铁矿原矿、1100℃和1150℃时还原产物的XRD谱图。
结合分析可知,在1100℃时,尖晶石相衍射峰由于铁元素的还原而被削弱,同时出现了还原金属相。
当温度升至1150℃时,含铬尖晶石相参与还原反应,尖晶石结构遭到破坏,此时尖晶石相衍射峰峰值已降低到较低水平,而金属及其碳化物相成为此时产物的主要成分。
值得注意的是,所有的焙烧产物中均未发现铬氧化物的衍射峰,证明在本实验条件下所得还原产物中,铬元素仍主要赋存于尖晶石相中。
为进一步研究1100℃下类质同象尖晶石结构在还原焙烧过程中的
转变行为,图4还给出了国际衍射数据中心(ICDD)提供的标准衍射卡片。
将其与原矿和1100℃还原产物的XRD谱图进行对比可知,原矿中的尖晶石相衍射峰与纯物质近似,而随着其中铁元素还原析出,的衍射峰不但没有降低反而有所增强,30度左右的衍射峰下降幅度较大,的衍射峰下降幅度较小,尖晶石相衍
射峰整体向MgO·Cr203的标准峰转变。
由以上结果可以得出,在还原焙烧温度为1100℃时,尖晶石相中的铁元素逐渐脱离晶格,但并未导致尖晶石结构完全破坏,而是使尖晶石相由以
FeO·Cr203为主的晶体结构逐渐转变为以为主的品体结构。
由以上分析可推测,在焙烧温度达到含铁尖晶石相还原温度时(如本实验中的1100℃),铬铁矿颗粒表层首先进行还原反应。
晶格中的Fe( II)和Fe(III)结合还原剂提供的电子转变为金属态并向表面富集,内部的铁离子由于浓度梯度的作用向外部迁移,而外部的其他金属离子为保证矿石颗粒的电荷平衡则向内部移动,使还原反应持续进行,也造成了尖晶石晶格中金属离子的重新分配。
与此同时,单质碳和一氧化碳与矿石表明富铁尖晶石结构中的骨架氧结合,形成一氧化碳和二氧化碳气体脱离体系,导致部分尖晶石结构被破坏。
反应进行到一定程度,当浓度梯度所产生的驱动力不足以使核心处的铁离子克服阻力继续向外扩散时,还原反应趋于停止,最终少量铁元素残留于矿石中。
在此过程中,大部分铬元素并未参与还原反应,依然存在于尖晶石结构内。
当焙烧温度满足富铬尖晶石相还原温度时(如本实验中的1150℃),尖晶石结构进一步分解,铬被还原为金属态以单质或碳化物的形式脱离基体,与铁共同形成析出相。
因此,1100℃为本实验所得铬铁矿还原焙烧预处理的适宜温度,在此温度下能够实现铬铁矿初步除铁和铬元素适当富集的目的。
2、焙烧时间对铬铁矿还原焙烧效果的影响
图5为铬铁矿在1100℃下还原焙烧不同时间后所得产物的SEM图像。
由图可知,析出相在还原焙烧20min后即以点状形式均匀出现在矿石颗粒表面,并随着焙烧时间的延长而不断长大、聚集。
经EDS检测,得知析出相的主体元素始终为铁元素。
图6为铁还原率随焙烧时间的变化规律。
由图6可知,还原焙烧进行到120min后,71.3%的铁元素从尖晶石相中还原析出,继续延长焙烧时间对除铁效果的促进作用并不明显。
图5 铬铁矿在1100℃下还原焙烧不同时间所得产物的SEM图像
图6 1100℃下焙烧时间对除铁率的影响
3、还原焙烧产物分析
还原焙烧产物经球磨一磁选或酸浸操作后可令富铁析出相与铬铁矿分离。
对实验中所得试样进行多点EDS分析,选取特征结果。
图7为南非铬铁矿原矿和其经1100℃还原焙烧2h 并经室温盐酸浸出处理后的SEM图像和尖晶石相EDS图谱。
由图7中SEM图像可知,尖晶石相在预处理后表面出现大量孔洞,这是铁元素的析出和溶解造成的。
对预处理前后的铬铁
矿进行BET检测,发现比表面积由1.44升至7.07。
对比还原焙烧处理前后尖晶石相EDS谱图可知,尖晶石相中铁元素含量大幅降低,类质同象尖晶石由富铁尖晶石结构转变为热稳定性更强的以和为主的尖晶石结构。
此外,研究还发现铬元
素主要赋存于尖晶石相中,少量铬以碳化物的形式残留在孔洞周围。
由于在常温下铬的碳化物几乎不溶于盐酸,因此在还原焙烧过程中析出的金属态铬可经盐酸浸出处理后与金属态铁分离,避免造成严重的铬损失。
在本实验中,南非铬铁矿经预处理后,Cr2O3质量分数由45%升高到52%, m(Cr)/m(Fe)由1.7提高至5.8,满足了I级冶炼精矿的质量要求,实现了铬元素的适度富集和铬铁矿应用领域的拓展。
图7 还原焙烧预处理前后铬铁矿的SEM图像和尖晶石相EDS图谱对处理后的南非铬铁矿进行硫酸浸出实验,发现铬元素浸出速率大幅提升,但酸耗量和氧化剂用量并没有明显变化。
分析可知,铬铁矿经还原焙烧预处理后,增大了矿石颗粒比表面积,从而使矿石的分解效率得以提高。
然而,铬元素仍存在于稳定的尖晶石结构中,矿石的分解条件并没有明显改变。