飞机铝合金零件腐蚀机理与防护
第八章 飞机结构腐蚀与防护
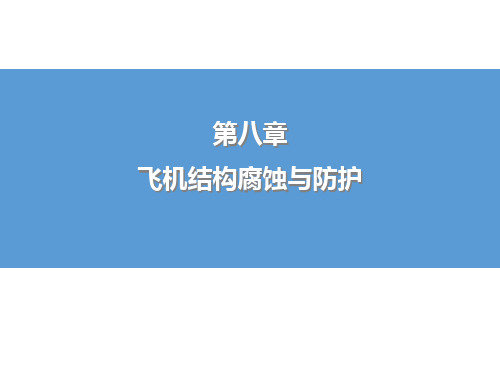
二、飞机结构的腐蚀
1.飞机常见腐蚀类型 (2)局部腐蚀——④缝隙腐蚀
形成原因: (1)飞机外部。由于未加涂层的铝件、紧固件表面受外界侵蚀而产生 腐蚀,因此大气污染起了主要作用。 (2)飞机内部。最易发生腐蚀的地方是厨房或洗手间,原因是液体的 凝积、溢出和泄露;还有弯管处,因该处液体排放常被堵塞。 应对措施:选择合适的材料或涂镀层、缓蚀剂和电化学保护等。
二、飞机结构的腐蚀
1.腐蚀防护基本方法
(1)改善金属的本质 (2)形成保护层
1)金属的磷化处理——钢铁制品去油、除锈后,放入特定组成的磷酸 盐溶液中浸泡,即可在金属表面形成一层不溶于水的磷酸盐薄膜。
2)金属的发蓝处理——将钢铁制品加到NaOH和NaNO2的混合溶液中, 加热处理,其表面即可形成一层厚度为0.5~1.5μm的蓝色氧化膜(主要成分 为Fe3O4),以达到钢铁防腐蚀的目的。
学习目标
➢ 素质目标 [1] 具备“敬仰航空、敬畏生命、敬重装备”精神;; [2] 具备良好的质量意识; [2] 具有较强的安全生产、环境保护意识。
பைடு நூலகம்
主要内容
一、腐蚀理论基础 二、飞机结构的腐蚀 三、飞机结构的防护
一、腐蚀理论基础
1.金属腐蚀定义
金属腐蚀是指金属材料受周围介质的作用而损坏。 腐蚀一般可按以下方式分类: 按腐蚀的机理,可分为化学腐蚀和电化学腐蚀; 按腐蚀的形式,可分为全面腐蚀和局部腐蚀; 按产生腐蚀的条件,可分为应力腐蚀、大气腐蚀、海水腐蚀和微 生物腐蚀等。
飞机结构件腐蚀的原因、预防和修理方法分析
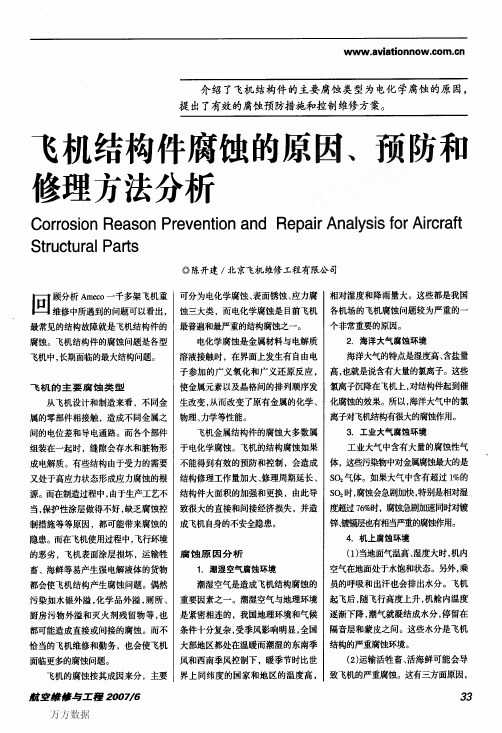
(7)加强对货物装卸过程的管理, 杜绝因野蛮装卸造成的飞机货舱地 板、侧壁板损坏,以避免腐蚀介质渗入 到飞机结构件上。
(8)在雨季、高温、潮湿季节中,应 缩短检查周期,加强防腐蚀措施。
(9)如果可能,深入研究腐蚀的起 因,制定相应的预防措施并在实施中 不断完善和提高。
飞机的腐蚀按其成因来分,主要
可分为电化学腐蚀、表面锈蚀、应力腐 蚀三大类,而电化学腐蚀是目前飞机 最普遍和最严重的结构腐蚀之一。
电化学腐蚀是金属材料与电解质 溶液接触时,在界面上发生有自由电 子参加的广义氧化和广义还原反应, 使金属元素以及晶格问的排列顺序发 生改变,从而改变了原有金属的化学、 物理、力学等性能。
(2)安装修理件的配合表面均应 涂密封胶隔绝,必要时紧固件也应涂 密封胶湿安装,所有止裂孔要涂底漆 并用软铆钉或密封胶堵住。
(3)修理件、孔壁、埋头窝等处,均 应做表面防护处理,并喷涂底漆。
(4)修理件材料尽量选取与相邻 结构相容的材料,电位相当;复合材料 与合金材料之间也要相容,碳纤维树 脂板与铝合金材料不能直接接触,必 要时可共固化一层玻璃纤维一环氧树
相对湿度和降雨量大。这些都是我国 各机场的飞机腐蚀问题较为严重的一 个非常重要的原因。
2.海洋大气腐蚀环境 海洋大气的特点是湿度高、含盐量 高,也就是说含有大量的氯离子。这些 氯离子沉降在飞机上,对结构件起到催 化腐蚀的效果。所以,海洋大气中的氯 离子对飞机结构有很大的腐蚀作用。 3.工业大气腐蚀环境 工业大气中含有大量的腐蚀性气 体,这些污染物中对金属腐蚀最大的是 s02气体。如果大气中含有超过l%的 s02时,腐蚀会急剧加快,特别是相对湿
腐蚀的一般性修理原则
飞机上常用合金材料及其腐蚀防护探究
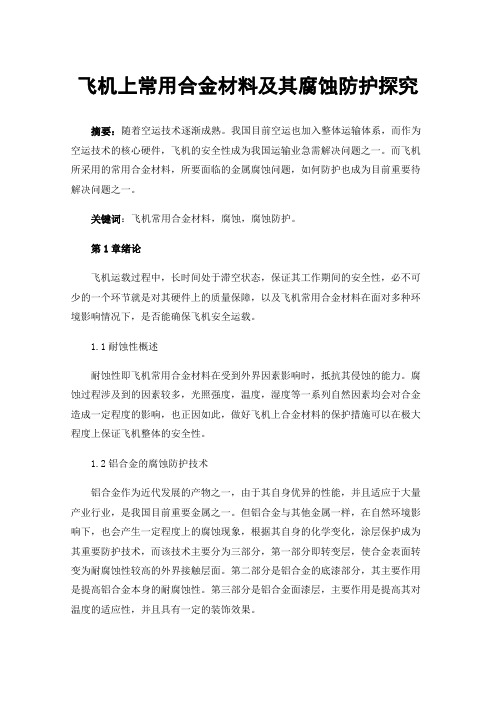
飞机上常用合金材料及其腐蚀防护探究摘要:随着空运技术逐渐成熟。
我国目前空运也加入整体运输体系,而作为空运技术的核心硬件,飞机的安全性成为我国运输业急需解决问题之一。
而飞机所采用的常用合金材料,所要面临的金属腐蚀问题,如何防护也成为目前重要待解决问题之一。
关键词:飞机常用合金材料,腐蚀,腐蚀防护。
第1章绪论飞机运载过程中,长时间处于滞空状态,保证其工作期间的安全性,必不可少的一个环节就是对其硬件上的质量保障,以及飞机常用合金材料在面对多种环境影响情况下,是否能确保飞机安全运载。
1.1耐蚀性概述耐蚀性即飞机常用合金材料在受到外界因素影响时,抵抗其侵蚀的能力。
腐蚀过程涉及到的因素较多,光照强度,温度,湿度等一系列自然因素均会对合金造成一定程度的影响,也正因如此,做好飞机上合金材料的保护措施可以在极大程度上保证飞机整体的安全性。
1.2铝合金的腐蚀防护技术铝合金作为近代发展的产物之一,由于其自身优异的性能,并且适应于大量产业行业,是我国目前重要金属之一。
但铝合金与其他金属一样,在自然环境影响下,也会产生一定程度上的腐蚀现象,根据其自身的化学变化,涂层保护成为其重要防护技术,而该技术主要分为三部分,第一部分即转变层,使合金表面转变为耐腐蚀性较高的外界接触层面。
第二部分是铝合金的底漆部分,其主要作用是提高铝合金本身的耐腐蚀性。
第三部分是铝合金面漆层,主要作用是提高其对温度的适应性,并且具有一定的装饰效果。
1.3飞机上常用合金的腐蚀现状及存在形式飞机主体构造多半采用合金材料,这其中包含了飞机骨架,蒙皮,以及大部分结构零件等多方面。
由此可见,合金腐蚀情况对于飞机而言,危害性极大。
一旦飞机主体出现问题,飞行安全隐患极大程度增加,甚至造成重大安全事故。
同时还会影响到飞机的正常使用以及维护。
1.4研究内容及目标通过比对合金材料耐腐蚀性,综合考虑飞机常用合金的安全性,其具体研究内容是:通过实验对比各种金属材料以及合金材料在相同环境下,耐腐蚀性程度。
飞机大修中常见腐蚀种类及防腐措施
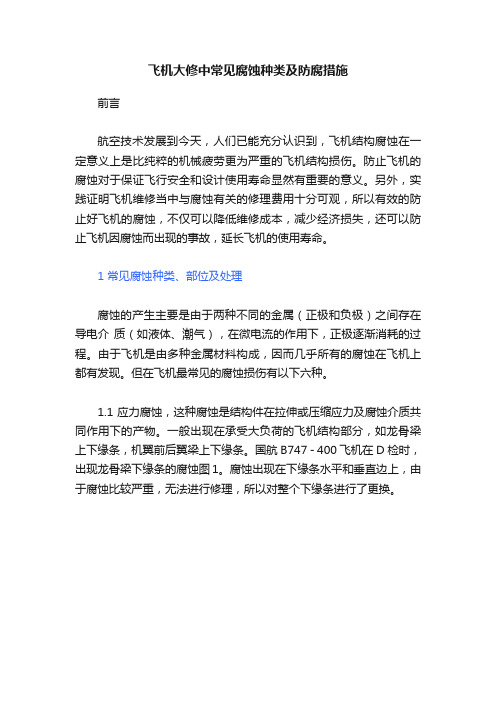
飞机大修中常见腐蚀种类及防腐措施前言航空技术发展到今天,人们已能充分认识到,飞机结构腐蚀在一定意义上是比纯粹的机械疲劳更为严重的飞机结构损伤。
防止飞机的腐蚀对于保证飞行安全和设计使用寿命显然有重要的意义。
另外,实践证明飞机维修当中与腐蚀有关的修理费用十分可观,所以有效的防止好飞机的腐蚀,不仅可以降低维修成本,减少经济损失,还可以防止飞机因腐蚀而出现的事故,延长飞机的使用寿命。
1 常见腐蚀种类、部位及处理腐蚀的产生主要是由于两种不同的金属(正极和负极)之间存在导电介质(如液体、潮气),在微电流的作用下,正极逐渐消耗的过程。
由于飞机是由多种金属材料构成,因而几乎所有的腐蚀在飞机上都有发现。
但在飞机最常见的腐蚀损伤有以下六种。
1.1应力腐蚀,这种腐蚀是结构件在拉伸或压缩应力及腐蚀介质共同作用下的产物。
一般出现在承受大负荷的飞机结构部分,如龙骨梁上下缘条,机翼前后翼梁上下缘条。
国航B747 - 400飞机在D检时,出现龙骨梁下缘条的腐蚀图1。
腐蚀出现在下缘条水平和垂直边上,由于腐蚀比较严重,无法进行修理,所以对整个下缘条进行了更换。
图 1 747龙骨梁下缘条水平和垂直边的腐蚀1.2电化学腐蚀,这种腐蚀是两种不同的金属相互连接,在潮湿环境下形成的腐蚀典型。
主要特征是腐蚀主要发生在两种不同的金属或金属与非金属导体相互接触的边缘附近。
在飞机大修过程中,机翼上蒙皮经常会被发现有些紧固件周围有轻微腐蚀,如图2。
根据电化学腐蚀的机理,在制定结构修理方案时就必须按照以下原则。
修理材料与原材料不一致时,应做好两种材料的隔绝工作,如使用钢件修理铝件时,必须在钢件上涂至少两遍的底漆,并在两种材料的结合面涂封严胶。
图2与钢紧固件接触的2024铝合金1.3缝隙腐蚀,这类腐蚀是水分进人缝隙后,由于缝隙口边的水分含氧量与位于缝隙中间及底部的水分含氧量不同,形成电位差。
在含氧量高的缝隙口处,金属就成为正极面被腐蚀,如图3。
在结构中不可避免会出现缝隙,如螺母压紧面、铆钉头底面等。
飞机铝合金结构件的腐蚀机理与控制

在腐蚀微 电池 电场 力的 作用下 ,阳极区的 A 首 l 先发生溶解反应 , 不断形成 A ¨进入到溶液 中去 , l 并 释放 电子 , 电子迁移到 阴极 区 , 在腐蚀 电解 质的作用 下 ,阴极区发生吸氧反应生成 O 。 H。 在溶液 中 , 金属 A 的浓度随 着腐蚀反应 的进 行 l 不断增加 , 最终 与 O 。 H 离子发生水解反应 , 生成 白色
变形 、磨 损等 ,其 中腐蚀是最常 见的损伤形 式之 一 , 由于 腐蚀造成 的事 故 占飞机 全部 损伤事故 的 2 % , 0 这 个问题在老龄飞机上表现的尤为突 出。由于腐蚀问 题 的存在 , 往往缩短 飞机结构件 的使用寿命 , 甚至还 会危及飞行安全 。 ̄ 8年A 0a n 98 l 航空公司的波音7 7 1 h 3 飞机发生空 中事故 , 经过事故调查后认为:由于机身增 压舱纵向蒙皮搭接接头处一排铆钉孔 , 在服役的热带海 洋环境和循环增压载荷作用下, 引起 了不可检测的多条
结构 的应 力分布 , 引起局部应 力集 中, 从而形成腐蚀
疲 劳裂纹;剥蚀和缝隙腐蚀使蒙皮 、 桁条等构件的厚 度减 薄 , 大大降低材料的强度 , 增大应力 , 最终导致
构件 裂纹 ,甚至断裂 。
下面我们以飞机结构件最常 见的铝合金L 2 Z Y1C 硬 铝 为 例 ,讨 论 一 下 铝 合金 腐蚀 的 电化 学 原 理 。 L 2 Z属于 A - uMg系硬铝合金 ,在其保护 层遭 Y1C 1 — C 到破坏 以后 ,大 气环境 中由于工业污 染含大量 c 。 l 、 S 2 2 ,这 些成分溶于水 ,造成水的 p O 、H S H值偏小 ,
pa tditi to a r di g t e o i a e i lo s m m a z da e e al ri n e s r sa ans r i g a ep e e ed Th s r, srbui n nde o n yp n ar n sas u pl i r e nds v r tne tm a u e g i te o n r r s nt . i e p d
飞机上常用合金材料及其腐蚀防护

飞机上常用合金材料及其腐蚀防护【摘要】本论文主要阐述了新型合金材料在飞机结构上的应用及其腐蚀防护系统,首先从新型合金材料及其在飞机结构中的应用开始,主要介绍了铝合金、镁合金、钛合金和超高强度钢;其次详细介绍了飞机的使用环境对主要结构部位的腐蚀特性;最后引申到几种常见合金材料的腐蚀与腐蚀防护。
关键词:常用合金材料、铝合金、镁合金、钛合金、超高强度钢、飞行环境、腐蚀、防护目录绪论 (3)1.常用合金材料及其在飞机结构中的应用 (4)1.1铝合金 (4)1.1.1硬铝合金 (4)1.1.2超硬铝合金 (4)1.1.3锻铝合金 (4)1.1.4防锈铝合金 (5)1.1.5高纯高韧铝合金 (5)1.1.6铝锂合金 (6)1.2.镁合金 (6)1.3钛合金 (6)1.4超高强度钢 (7)2.飞机的使用环境对主要结构部位的腐蚀特性 (9)2.1飞机的使用环境概述 (9)2.1.1环境因素复杂 (9)2.1.2环境因素是随机变量 (9)2.2飞机主要结构部位的腐蚀特性 (9)2.2.1机身部分 (9)2.2.2机翼部分 (10)2.2.3尾翼部分 (10)2.2.4起落架部分 (10)2.2.5发动机区域 (11)2.2.6发动机主要部件 (11)3.新型合金材料的腐蚀防护 (13)3.1铝合金的腐蚀防护 (13)3.1.1常用铝合金的腐蚀特性 (13)3.1.2常用铝合金的防护系统 (13)3.2镁合金的腐蚀防护 (14)3.2.1常用镁合金的腐蚀特性 (14)3.2.2常用镁合金的防护系统 (14)3.3钛合金的腐蚀防护 (15)3.3.1常用钛合金的腐蚀特性 (15)3.3.2钛合金的表面防护系统 (15)3.4超高强度钢的腐蚀防护 (15)3.4.1常用超高强度钢的腐蚀特性 (15)3.4.2超高强度钢的表面防护系统 (16)结束语 (17)谢辞 (18)文献 (19)绪论高性能飞机结构材料对降低飞机结构质量和提高飞机的结构效率、服役可靠性及延长寿命具有极为重要的作用,是飞机结构材料的主要发展趋势。
飞机腐蚀与防护.

2.全天候飞行的要求:小飞机的高 度比较低。因此受天气影响比较大;大飞 机飞行的高度一般在平流层底部,会遇到 的冰粒、雨水等。
3.飞行性能的提高,采用大量的新 工艺新材料。
4.工业污染:废气、废液、废渣等 会造成飞机表面或一些暴露在外表的金属 结构产生腐蚀。
二、腐蚀的原因
1.腐蚀:是指金属及其制品在生产和使用过程中,在 周围环境因素的作用下,发生破坏变质,造成原有 的化学、物理、机械等性质的改变。
2.金属的抗腐蚀能力取决于:金属本身的特性(化学 稳定性),环境,表面保护层好坏。
三、腐蚀的机理:
1.化学腐蚀:金属与环境介质直接发 生化学作用而产生的破坏。腐蚀过程的特 点是无电流产生,腐蚀产物直接产生并覆 盖在腐蚀处,化学腐蚀往往是在高温干燥 的环境中产生。
Fillet seal: 缝隙处填胶
发现腐蚀的去除与修理
• 打磨 – 必须彻底去除腐蚀产物,露 出金属本色
• 切割 – 把结构件出现腐蚀的部分彻 底割除
• 加强 – 对打磨超标或切割的区域进 行加强修理
• 更换 – 对腐蚀的结构件进行更换新 件
日常维护中的腐蚀预防措施
定期清洁飞机容易污染的 区域,特别是容易受液压油、 强腐蚀介质、电解质污染的 区域或结构件,并重新喷涂 防腐蚀抑制剂。
—— 金材 102 赵红昌 100601206
飞机腐蚀引起的事
故
飞机的腐蚀是一种灾难性 的腐蚀,不仅会造成直接 或间接的经济损失,而且 会造成重大的飞行事故。 1985年8月12日一架波音 747客机,因应力腐蚀断 裂而坠毁,死亡500多人; 2002年5月华航空难造成 225人死亡原因也是飞机 尾部有裂纹引起。
飞机铝合金结构件的腐蚀机理与控制措施
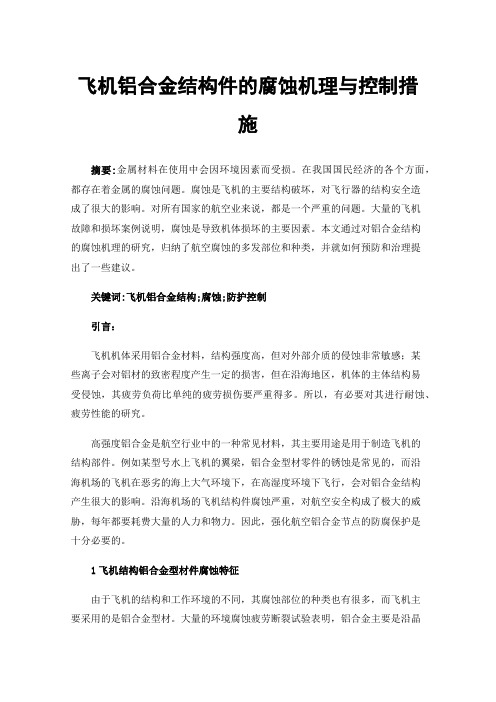
飞机铝合金结构件的腐蚀机理与控制措施摘要:金属材料在使用中会因环境因素而受损。
在我国国民经济的各个方面,都存在着金属的腐蚀问题。
腐蚀是飞机的主要结构破坏,对飞行器的结构安全造成了很大的影响。
对所有国家的航空业来说,都是一个严重的问题。
大量的飞机故障和损坏案例说明,腐蚀是导致机体损坏的主要因素。
本文通过对铝合金结构的腐蚀机理的研究,归纳了航空腐蚀的多发部位和种类,并就如何预防和治理提出了一些建议。
关键词:飞机铝合金结构;腐蚀;防护控制引言:飞机机体采用铝合金材料,结构强度高,但对外部介质的侵蚀非常敏感;某些离子会对铝材的致密程度产生一定的损害,但在沿海地区,机体的主体结构易受侵蚀,其疲劳负荷比单纯的疲劳损伤要严重得多。
所以,有必要对其进行耐蚀、疲劳性能的研究。
高强度铝合金是航空行业中的一种常见材料,其主要用途是用于制造飞机的结构部件。
例如某型号水上飞机的翼梁,铝合金型材零件的锈蚀是常见的,而沿海机场的飞机在恶劣的海上大气环境下,在高湿度环境下飞行,会对铝合金结构产生很大的影响。
沿海机场的飞机结构件腐蚀严重,对航空安全构成了极大的威胁,每年都要耗费大量的人力和物力。
因此,强化航空铝合金节点的防腐保护是十分必要的。
1飞机结构铝合金型材件腐蚀特征由于飞机的结构和工作环境的不同,其腐蚀部位的种类也有很多,而飞机主要采用的是铝合金型材。
大量的环境腐蚀疲劳断裂试验表明,铝合金主要是沿晶剥落,首先是在保护层的划痕部位出现点蚀,然后由于超出容限而失效。
铝合金基体在长时间的侵蚀下,出现了大量的凸起,主要表现为星层状的剥落,大部分的裂纹都是平行的。
航空结构的腐蚀破坏是一项综合性的多学科综合工程,它涵盖了材料学等多个方面,其影响范围很大,而飞机铝合金构件的局部腐蚀剥蚀是一种较为普遍的简单腐蚀破坏。
影响结构腐蚀的主要因素有:制造工艺水平、结构防腐设计水平和材料的耐蚀性能。
在不同的飞机使用区域,在污染较重的区域,会出现较大的腐蚀。
- 1、下载文档前请自行甄别文档内容的完整性,平台不提供额外的编辑、内容补充、找答案等附加服务。
- 2、"仅部分预览"的文档,不可在线预览部分如存在完整性等问题,可反馈申请退款(可完整预览的文档不适用该条件!)。
- 3、如文档侵犯您的权益,请联系客服反馈,我们会尽快为您处理(人工客服工作时间:9:00-18:30)。
据统计,铝和铝合金要占一架飞机总重量的70%,而飞机的结构件大部分是由铝合金材料构成。
铝合金构件的损伤形式有多种,如疲劳断裂、裂纹、变形、磨损等,其中腐蚀是最常见的损伤形式之一。
由于腐蚀造成的事故占飞机全部损伤事故的20%,这个问题在老龄飞机上变现的尤为突出。
由于腐蚀问题的存在,往往缩短飞机结构件的使用寿命,甚至还危及飞行安全。
如1988年Aloha航空公司的波音737飞机发生空中事故,经过事故调查后认为:由于机身增压舱纵向蒙皮搭接接头处一排铆钉孔,在服役的热带海洋环境和循环增压载荷作用下,引起了不可检测的多条腐蚀疲劳裂纹,从而引起事故。
因此,腐蚀问题不容忽视,这就需要我们在航空维修过程中加强检查与控制。
飞机结构件的腐蚀是飞机在使用环境中随着时间推移而发生的化学累积性损伤。
作为电化学反应,必须同时具备三个条件才能发生,即活性金属、腐蚀环境(介质)和导电通路。
同时,它又作为与时间有关的损伤,需要一定时间的累积才能发生,并且要求在一定的损失范围之内就进行维护和修理。
一般民航和军航的飞机维修规定:腐蚀损失深度不超过蒙皮厚度的10%。
腐蚀的种类很多,通过对飞机铝合金材料构件腐蚀情况的统计和分析得知,点蚀、剥蚀缝隙腐蚀这三类是腐蚀的主要表现形式。
其中,点蚀改变飞机结构的应力分布,引起局部应力集中,从而形成腐蚀疲劳裂纹;剥蚀和缝隙腐蚀使蒙皮、桁条等构件的厚度减薄,大大降低材料的强度,增大应力,最终导致构件裂纹,甚至断裂。
在飞机结构修理中,构件中存在应力腐蚀裂纹是一个常遇到的实际问题。
例如,1L-18飞机上翼面处的大量B94铝合金铆钉产生了应力腐蚀裂纹。
应力腐蚀裂纹通常都很小,宽度较窄,没有引起人们注意的特征,又因常被腐蚀产物覆盖,所以很难发现,有时需要采用无损探伤技术进行检查。
构件发生应力腐蚀断裂时,常常是在事先没有明显预兆的情况下突然发生,因此对飞机的飞行安全危害较大。
一般来说,腐蚀坑洞是应力腐蚀裂纹的主要萌生源。
通常情况下,存在应力腐蚀裂纹构件的表面,常有不同程度的腐蚀痕迹。
当然,由交变应力引起的疲劳裂纹以及焊接裂纹、热处理裂纹也可转化为应力腐蚀裂纹。
应力腐蚀裂纹具有较多的二次裂纹,这种现象在铝合金、镁合金、高强度钢及钛合金中都可看到。
主裂纹的扩展方向垂直于最大正应力的方向。
从宏观看应力腐蚀断裂的断口一般有三个区:1.开裂源区。
该区的断口腐蚀较为严重,开裂源的根部往往有蚀坑。
2.应力腐蚀裂纹的扩展区。
这是应力腐蚀裂纹缓慢扩展过程中所形成区域,;裂纹扩展过程是材料的组织与应力及介质相互作用的过程。
从宏观上来看,这个过程的特性是呈脆性的,即使是具有高塑形的Cr-Ni奥氏体不锈钢也如此。
由于裂纹是沿着材料的某一结晶学方向(如解理面),所以断口的粗糙不平的。
而这种不平度是随着材料的组织与晶粒度而变化的。
由于腐蚀产物的存在,在应力腐蚀断口上,可以明显看到,裂纹缓慢扩展区和因为构件的有效载面不能承受静应力而断裂的区域是截然不同的。
3.最后一个区域就是快速拉断或撕裂区。
从应力腐蚀开裂的方式来看,它的微观开裂途径通常有三种类型,即穿晶型、沿晶型和混合型。
一般说来,应力腐蚀的微观开裂途径与材料的晶体结构、合金成分、热处理状态以及构件所处的介质环境与应力状态有关。
铝合金的应力腐蚀开裂途径几乎总是沿着晶界的。
这是因为铝合金沿晶界沉淀物或紧靠晶界有一层薄层富合金元素或贫合金元素区,从而晶界与晶粒基体有很大的电位差,使晶界成为铝合金应力腐蚀敏感的区域。
腐蚀疲劳是指构件在交变应力和腐蚀介质联合作用下发生的疲劳破坏。
交变应力和腐蚀介质联合作用要比期中一个单独作用更加有害。
严格来说,除了在真空和惰性介质中工作的构件外,所有的疲劳破坏都是腐蚀疲劳破坏。
特别是对于铝合金来说,潮湿空气就是一种严重的腐蚀环境。
因此,飞机长期服役后,某些铝合金构件就可能发生腐蚀疲劳破坏,尤其是Al-Zn-Mg,铝合金对潮湿空气更加敏感,更容易发生腐蚀疲劳破坏。
腐蚀疲劳的S-N曲线具有明显的特征。
腐蚀环境与交变载荷同时作用,会使长寿命的疲劳强度降低很多,在干燥空气中可能出现比较平缓的长寿命S-N特性,但在腐蚀疲劳条件下就不会出现。
这也是说腐蚀疲劳曲线没有水平段。
由于潮湿空气就是铝合金的严重腐蚀环境,所以在一般湿度条件测得的铝合金S-N曲线,没有明显的水平段,即没有明显的疲劳极限。
通常,腐蚀疲劳裂纹往往萌生在腐蚀坑洞处,例如,An-24机机翼油箱上壁板的边缘裂纹就萌生在面板边缘表面的蚀坑处。
构件在交变载荷作用下产生的表面滑移,会使金属表面膜发生反复破裂,从而在构件表面上出现许多活性区域,进而形成腐蚀坑洞。
因此,在腐蚀环境下,构建表面可形成多个疲劳源。
构件表面的腐蚀疲劳裂纹可多条同时存。
这也就是说,在一条腐蚀疲劳裂纹附近,有可能形成许多条表面次裂纹,并扩展到比较深的深度,这些次裂纹彼此大体上相互平行地向内扩展,在达到一定长度之后,便停止扩展,只有主裂纹继续扩展,并导致构件断裂。
因此,主裂纹附近出现多条次裂纹的现象,是腐蚀疲劳断裂的表面特征之一。
一般来说,腐蚀疲劳的表面裂纹比机械疲劳裂纹宽些。
但是,在表面以下,逐渐变细,貌似常见的疲劳裂纹。
这表明,当裂纹前缘远离表面时,腐蚀环境的影响会明显降低。
应当指出,某些合金的应力腐蚀裂纹只能在特定腐蚀环境下才会发生,但是,腐蚀疲劳裂纹则可发生在差不多所有易于遭到一般性腐蚀介质的材料上。
腐蚀疲劳裂纹多半是穿晶的,但也有沿晶的,这主要取决于材料的特性和工作条件。
铝合金在低频和大应力幅下,其腐蚀疲劳裂纹可能是沿晶的,不过这种情况多发生在材料的短横向。
在多数情况下,单纯的机械疲劳与腐蚀疲劳的鉴别可用断口是否有腐蚀产物覆盖作为鉴别依据。
利用扫描电镜、电子控针以及其他化学分析方法,对断口表面的腐蚀产物进行成分分析,鉴别腐蚀介质的成分,这是腐蚀疲劳断裂分析工作的常用分析方法。
但是,腐蚀疲劳断口上的腐蚀产物往往也给分析工作带来极大的不便。
在一些情况下,由于断口腐蚀严重,以致使断口的宏观和微观形貌特征遭到破坏,给确定构件断裂性质带来一定困难。
在腐蚀产物的下面仍然保留着疲劳特征的情况下,应采取适当的清洗剂仔细清洗断口,将覆盖于断口上面的腐蚀产物清洗干净之后,再观察断口的疲劳特征。
目前,应力腐蚀开裂机理还不完全明白。
因此,其防止方法还只是一般性的或经验性德。
通常,可采用下列一种或几种方法来减轻或防止应力腐蚀开裂:1.铝锌合金(例如LC4),不锈钢(例如Cr-Ni 奥氏体不锈钢和高强度结构钢(例如30crMnSiA)对应力腐蚀具有较高的敏感性。
因此,在飞机结构设计过程中,应成分考虑到这一点。
2.当某一种材料处在特定的腐蚀环境中时,应力腐蚀开裂速率是受应力强度因子控制的。
对于某些合金材料,例如钛合金,当应力强度因子低于某特定值时,材料或构件就不会发生应力腐蚀破坏,这一特定值就是应力腐蚀临界应力强度因子,或称门槛应力强度因子。
但是,对铝合金来说,它们没有确定的值,一般来说,采用过时效或分级时效的材料,尽管静强度稍有下降,但抗应力腐蚀性能显著提高。
3.在构件成型、冷加工、焊接等一系列公益过程中,若可能带来明显的残余盈利的话,则一般应加进消除残余拉应力的热处理工艺。
4.采用喷丸、滚压等表面强化处理措施或采用超声波、振动等方法,可降低残余拉应力或引入压应力,从而提高零构件的抗应力腐蚀性能。
试验结果表明,喷丸能够相当显著地提高合金材料抗应力腐蚀破坏的能力。
5.采用表面渗碳、渗氮、氰化、渗金属或合金等工艺措施,也可提高合金材料抗应力腐蚀开裂的能力。
这种方法不仅直接提高了表面层的强度,而且由于强化层的存在,也提高了合金的抗蚀性,改变了表面内应力分布,产生表面压应力,因此提高了抗应力腐蚀开裂的能力。
6.紧固件孔的过大径向干涉量不仅导致疲劳寿命降低,而且对于7075-T6这样的铝合金干涉量超过3.2%时,材料对应力腐蚀敏感性增加。
考虑到国产铝合金材料的化学成分,热处理和加工规范等因素,在铆接结构中干涉量可去3%。
7.热处理至抗拉强度高于1370Mpa的钢对应力腐蚀的敏感性非常明显。
因此,对构件热处理、表面处理的工艺过程应严格控制。
对于高强度,不合理地提高材料的抗拉强度是非常危险的。
在控制热处理温度时,应当控制使其抗拉强度达到技术条件的中、下限。
由30CrMnSiA高强度钢制成的米格-15比斯飞机主起落架轮叉的应力腐蚀破坏,就是由于热处理不当,抗拉强度高于技术条件的上限所造成的。
8.应力集中是产生应力腐蚀的主要原因。
表面缺陷和亚表面缺陷,偶然的机械划伤,构件的几何形状改变等都会引起应力集中。
因此,在飞机结构设计中,应采用避免或减缓应力集中的措施。
抗腐蚀疲劳的基本措施:1.能够减轻腐蚀疲劳的主要方法,是选择一种能在使用环境中显示低腐蚀性的材料来获得较好的抗腐蚀疲劳性能。
因为铝铜合金耐应力腐蚀和腐蚀疲劳的性能优于铝锌合金,所以进行飞机结构设计时,尽可能选用铝铜合金设计结构件。
2.金属构件表面的拉应力是腐蚀疲劳破坏的嘴主要因素。
因此,讲金属构件表面置于压应力下,是延长金属构件疲劳寿命的嘴普遍采用的方法。
显然,对金属构件表面采用喷丸、滚压、渗碳、渗氮等表面强化处理工艺,使表面产生残余压应力,就可明显地提高构件的腐蚀疲劳强度。
3.在腐蚀环境中工作的零构件,采用表面镀层的方法可隔开腐蚀环境,使它不与零构件表面直接接触。
通常,阳极镀层是有利的;而阴极镀层是有害的。
锌和镉的镀层对钢来说属于阳极镀层,因而能改善抗腐蚀疲劳性能。
锌镀层的改善效果更好。
铬和镍的镀层对钢来说属于阴极镀层,用这些金属进行电镀后会产生有害的拉伸残余应力和表面毛细裂纹,还可能造成氢脆。
4.氧化性涂层可隔开腐蚀介质,有利于提高抗腐蚀疲劳性能。
例如,讲高强度铝合金包一层纯铝表层(包铝),能大大提高铝合金的抗腐蚀疲劳性能。
如果喷丸处理与氧化性涂料结合使用,能更加提高抗腐蚀疲劳性能。
5.应力集中也还是腐蚀疲劳破坏的主要原因。
因此,在进行飞机结构设计时,应尽量避免和减少应力集中,;在生产和使用过程中,应避免发生机械损伤。
6.疲劳试验和使用实践表明,构件的纵向抗腐蚀疲劳性能最好,而短横向抗腐蚀疲劳性能最差。
所以,在进行飞机结构设计时,应充分考虑到沿材料的纵向和长横向方向受力,避免构件的短横向受较大的拉应力。