注射模的工作原理与典型结构-4
注射模的典型结构.

1 单分型面注射模(二板式注射模) 单分型面注射模是注射模中最简单、最常见的一种结构形式,也 称二板式注射模。单分型面注射模只有一个分型面,其典型结构 如图5.1所示。单分型面注射模具根据结构需要,既可以设计成 单型腔注射模,也可以设计成多型腔注射模,应用十分广泛。。
1.工作原理 合模时,在导柱8和导套9的导向和定位作用下,注射机的合模系 统带动动模部分向前移动,使模具闭合,井提供足够的锁模力锁 紧模具。在注射液压缸的作用下,塑料熔体通过注射机喷嘴经模 具浇注系统进入型腔,待熔体充满型腔并经保压、补缩和冷却定 型后开模如图5.1a所示;开模时,注射机合模系统带动动模向后 移动,模具从动模和定模分型面分开,塑件包在凸模7上随动模一 起后移.同时拉料杆15将浇注系统主流道凝料从浇口套中拉出, 开模行程结束,注射机液压顶杆2l推动推板13,推出机构开始工作, 推杆18和拉料杆15分别将塑件及浇注系统凝料从凸模7和冷料穴中 推出,如图5.1b所示,至此完成一次注射过程。合模时,复位杆 使推出机构复位,模具准备下一次注射。
1.工作原理
开模时,动模部分向后移动,由于弹簧7的作用,模具首先 在A分型面分型,中间板(定模板) 12随动模一起后退,主流道 凝料从浇口套lo中随之拉出。当动模部分移动一定距离后, 固定在定模板12上的限位销6与定距拉板8左端接触,使中间 板停止移动,A分型面分型结束。动模继续后移,B分型面分 型。因塑件包紧在型芯9上,这时浇注系统凝料在浇口处拉 断,然后在B分型面之推板16时,推出机构开始工
作,椎件板4在推杆14的推动下将塑件从型芯9上推出,塑件 在B分型面自行落下。
2.设计注意事项 (1)浇口的形式 三板式点浇口注射模具的点浇口截面积较小,直径 只有0.5~1.5 mm。 (2)导柱的设置 三板式点浇口注射模具,在定模一侧—定要设置导 柱,用于对中间板的导向和支承,加长该导柱的长度,也可以对 动模部分进行导向,因此动模部分就可以不设置导柱。如果是推 件板推出机构,动模部分也一定要设置导柱。
注射模的典型结构

NO 31
7.定模板(凹模固定板)
用于固定凹模镶件的板状零件;
NO 32
8.浇口套
直接与注射机喷嘴反复接触,带有主流道通道的衬套类零件;
NO 33
9.定位圈
使注射机喷嘴与模具浇口套对中,决定模具在注射机上安装位置的定 位零件;
NO 34
10.定模座板
使定模固定在注射机定模安装板上的板件;
NO 35
NO 23
常见的侧抽芯机构是斜导柱滑块侧抽芯机构,其原理如下图:
NO 24
斜导柱侧向分型与抽芯注射模
斜导 柱 滑块 滑块锁
导滑板
NO 25
注射模具主要零部件名称及定义
1.动模座板 动模固定在注射机的移动工作板上的板件;
NO 26
2.垫块
调节模具闭合高度,形成推出机构所需的推出空间的块状零件;
NO 11
浇口套 定模座板 定模板 推杆固定板 动模板 支承板 推板 垫块 动模座板 推杆 复位杆
NO 12
导柱
(b) 塑件和浇注系统凝料
(a) 二板模注射模典型结构 NO 13
单分型面注射模
NO 14
典型单分型面注射模具工作原理
NO 15
典型单分型面注射模具工作原理
NO 16
NO 17
NO 10
单分型面注射模具剖切图:
各部分名称如下: 1-动模座板 3-支承板 5-型芯 7-定模板 9-定位圈 11-螺钉 13-塑件 15-螺钉 17-推板 19-推杆 21-弹簧 2-垫块 4-动模板 6-导套 8-浇口套 10-定模座板 12-型腔 14-导柱 16-推杆固定板 18-拉料杆 20-复位杆
NO 39
15.推杆
用于推出塑件或浇注系统凝料的杆件;
第四章 注射成型工艺-2010.

第二篇注射成型工艺及模具第四章注射成型工艺第一节热塑性塑料的工艺性能第二节注射机的基本结构及规格第三节注射成型原理及其工艺过程第四节注射成型工艺条件的选择与控制第五节几种常用塑料的注射成型特点第六节典型注射制件的工艺条件与各种塑料的注射工艺参数注射成型特点: (1 成型周期短,能一次成型形状复杂、尺寸精确、带有金属嵌件或非金属嵌件的塑料制件; (2 生产率高,易实现自动化生产; (3 除氟塑料以外,热塑性塑料都可以采用注射成型; (4 模具结构复杂,生产成本高,不适合单件生产。
主要技术任务如何根据设备条件和塑料原料,正确制定注射成型工艺规程以及合理设计注射模具,以保证生产能够正常进行,并具有较低的生产成本和较高的经济效益。
第一节热塑性塑料的工艺性能一塑料的成型收缩塑料制件从模具中取出发生尺寸收缩的特性称为塑料的收缩性。
a−b × 100% S 实= b a: 成型温度时制件尺寸,b:常温时制件尺寸 S 表示塑件的实际收缩率实由于成型温度时的制件尺寸无法测量,因此常用常温时的型腔尺寸取代。
c−b S 计= × 100% b C: 常温时型腔尺寸。
S计:塑件的计算收缩率 C=b(1+ S计)S计见表4-1,4-2具体分析时对于收缩率范围较小的塑料,取中间值,称平均收缩率对于收缩率范围较大的塑料,应根据制件的形状,特别时制件厚度来选,壁厚者选大值,壁薄者选小值。
制件各部分尺寸的收缩率不尽相同,应根据实际情况加以选择。
二塑料的流动性相对分子量小,熔融指数高,螺旋线长度长,表观粘度小,流动比好(流动长度/ 制品厚度)则流动性好。
流动性好的有:尼龙,聚乙烯,聚苯乙烯,聚丙烯,醋酸纤维流动性一般的有: ABS ,有机玻璃,聚甲醛,聚氯醚流动性差的有:聚碳酸酯,硬聚氯乙稀,聚苯醚,聚砜,氟塑料等。
①②③熔融指数的含义在规定条件下,一定时间内挤出的热塑性物料的量,也即熔体每 10min通过标准口模毛细管的质量,用 MFR 表示,单位为 g/10min 。
注射模的基本结构及特点
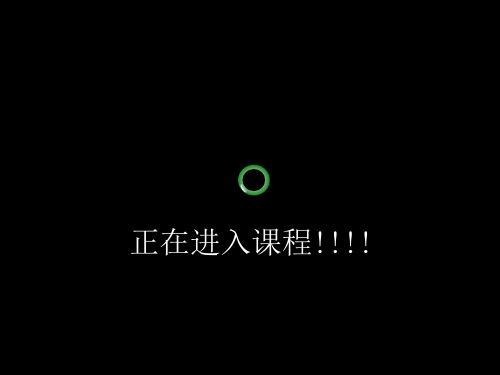
(6) 加热和冷却系统: 为了满足注
塑工艺对模具的温度要求,必须对模具温度 进行控制。
(7) 排气系统:
当中的热废气。
用来排出模具型腔
排气系统 产生的缺 陷
总结:
本次课主要对塑料模具的 基本组成和各组成的特点进行 学习,同时了解注射机的类型 特点。
课后练习:
1、对模具的基本组成进行记忆
指出下面的图形所指位置的名称
重、难点:
重点:注射模具的典型结构 难点:各类典型结构的特点
学习目标:
了解注射机的分类和工作原理,掌握注 射模的典型结构。
一、注射机工作过程
注射机结构图
提问:注射机是 如何工作呢
注射机主要工作 部分
注射机的工艺过程:
塑件 保压 冷却 固化 充模 加热 熔融 注射机 料筒 颗粒、粉 状塑料
注射机工作原理
注射机是如何工作呢注射机结构图颗粒粉状塑料注射机加热熔融冷却固化注射机工作原理主要作用加热熔融塑料成粘流态在一定压力和速度下将塑料注入型腔注射结束进行保压与补缩1卧式注射机注射装置与合模装置轴线呈一线与水平方向平行flash展立式注射机工作原理示意图注射装置与合模装置轴线呈一线与水平方向垂直排列2立式注射机注射装置与合模装置的轴线相互垂直排列3直角式注射机图84直角式注射机锁模装置
浇注系统平面图
手机实物举例
(3)导向机构:
主要有导柱和导套 构成。起到合模定 位的作用。
(4)脱模机构:
用于开模时将塑件 从模具中脱出的装 置,又称顶出机构。
Flash 展示
(5)侧向分型与抽芯机构:
侧向抽芯机构是斜导柱、侧型芯滑块、锁紧 块和侧型芯滑块的定位装置组成。
带侧向抽芯的注射模
Flash讲解
注射机结构分析及工作原理

(一)注塑机结构分析及其工作原理一、注塑机的工作原理注塑成型机简称注塑机。
注塑成型是利用塑料的热物理性质,把物料从料斗加入料筒中,料筒外由加热圈加热,使物料熔融,在料筒内装有在外动力马达作用下驱动旋转的螺杆,物料在螺杆的作用下,沿着螺槽向前输送并压实,物料在外加热和螺杆剪切的双重作用下逐渐地塑化,熔融和均化,当螺杆旋转时,物料在螺槽摩擦力及剪切力的作用下,把已熔融的物料推到螺杆的头部,与此同时,螺杆在物料的反作用下后退,使螺杆头部形成储料空间,完成塑化过程,然后,螺杆在注射油缸的活塞推力的作用下,以高速、高压,将储料室内的熔融料通过喷嘴注射到模具的型腔中,型腔中的熔料经过保压、冷却、固化定型后,模具在合模机构的作用下,开启模具,并通过顶出装置把定型好的制品从模具顶出落下。
注塑机作业循环流程如图1所示。
图1 注塑机工作程序框图二、注塑机的分类按合模部件与注射部件配置的型式有卧式、立式、角式三种(1)卧式注塑机:卧式注塑机是最常用的类型。
其特点是注射总成的中心线与合模总成的中心线同心或一致,并平行于安装地面。
它的优点是重心低、工作平稳、模具安装、操作及维修均较方便,模具开档大,占用空间高度小;但占地面积大,大、中、小型机均有广泛应用。
(2)立式注塑机:其特点是合模装置与注射装置的轴线呈一线排列而且与地面垂直。
具有占地面积小,模具装拆方便,嵌件安装容易,自料斗落入物料能较均匀地进行塑化,易实现自动化及多台机自动线管理等优点。
缺点是顶出制品不易自动脱落,常需人工或其它方法取出,不易实现全自动化操作和大型制品注射;机身高,加料、维修不便。
(3)角式注塑机:注射装置和合模装置的轴线互成垂直排列。
根据注射总成中心线与安装基面的相对位置有卧立式、立卧式、平卧式之分:①卧立式,注射总成线与基面平行,而合模总成中心线与基面垂直;②立卧式,注射总成中心线与基面垂直,而合模总成中心线与基面平行。
角式注射机的优点是兼备有卧式与立式注射机的优点,特别适用于开设侧浇口非对称几何形状制品的模具。
注射模具的工作原理
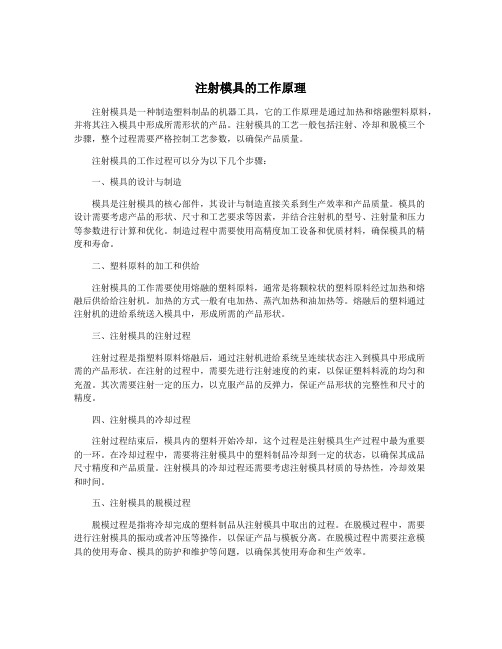
注射模具的工作原理注射模具是一种制造塑料制品的机器工具,它的工作原理是通过加热和熔融塑料原料,并将其注入模具中形成所需形状的产品。
注射模具的工艺一般包括注射、冷却和脱模三个步骤,整个过程需要严格控制工艺参数,以确保产品质量。
注射模具的工作过程可以分为以下几个步骤:一、模具的设计与制造模具是注射模具的核心部件,其设计与制造直接关系到生产效率和产品质量。
模具的设计需要考虑产品的形状、尺寸和工艺要求等因素,并结合注射机的型号、注射量和压力等参数进行计算和优化。
制造过程中需要使用高精度加工设备和优质材料,确保模具的精度和寿命。
二、塑料原料的加工和供给注射模具的工作需要使用熔融的塑料原料,通常是将颗粒状的塑料原料经过加热和熔融后供给给注射机。
加热的方式一般有电加热、蒸汽加热和油加热等。
熔融后的塑料通过注射机的进给系统送入模具中,形成所需的产品形状。
三、注射模具的注射过程注射过程是指塑料原料熔融后,通过注射机进给系统呈连续状态注入到模具中形成所需的产品形状。
在注射的过程中,需要先进行注射速度的约束,以保证塑料料流的均匀和充盈。
其次需要注射一定的压力,以克服产品的反弹力,保证产品形状的完整性和尺寸的精度。
四、注射模具的冷却过程注射过程结束后,模具内的塑料开始冷却,这个过程是注射模具生产过程中最为重要的一环。
在冷却过程中,需要将注射模具中的塑料制品冷却到一定的状态,以确保其成品尺寸精度和产品质量。
注射模具的冷却过程还需要考虑注射模具材质的导热性,冷却效果和时间。
五、注射模具的脱模过程脱模过程是指将冷却完成的塑料制品从注射模具中取出的过程。
在脱模过程中,需要进行注射模具的振动或者冲压等操作,以保证产品与模板分离。
在脱模过程中需要注意模具的使用寿命、模具的防护和维护等问题,以确保其使用寿命和生产效率。
注射模具是一项非常重要的生产技术,它涉及到材料科学、加工技术和机械设备的多个领域。
注射模具生产工艺需要由严格的工艺控制和操作规范,从而确保产品精度、质量和生产效率。
注塑模具基本结构(图解)

应用范围:
主要用于当塑件侧面凹槽或孔较 浅,所需抽拔距不大,但成型面积 较大的场合。
特点:抽芯距较短,抽芯力较大。
2011年12月27日
5.带活动镶件注射模
动画文件夹\注射模分 类讲解\带活动镶嵌件 注射模.swf
模具上设有活动的 型芯、螺纹型芯。
2011年12月27日
Байду номын сангаас 带活动镶件注射模
有些塑件有更特殊的要求,如模具上需要设置螺纹型芯或螺 纹型环等时,在型腔的局部设置活动镶件。 开模时,这些活动镶件不能简单地沿开模方向与塑件分 离,而是必须在塑件脱模时连同塑件一起移出模外,然后通 过手工或专门的工具将它与塑件分离,在下一次合模注射之 前,再重新将其放入模内。
合模时,推出机构靠复位杆并准备下一次注射。
2011年12月27日
(2)单分型面注射模的特点
动画文件 夹\单分型 面注射模\ 单分型面 注射模工 作视频.rm
1)注射模结构简单,成型塑件的适应性强;
2)塑件连同凝料在一起,需手工切除;
3)单分型面注射模应用广泛,据统计,单分型面 的注射模占总注射模的70%。
2011年12月27日
开模时,动模部分向后移 动,开模力通过斜导柱驱 动侧型芯滑块,迫使其在 动模板的导滑槽内向外滑 动,直至滑块与塑件完全 脱开,完成侧向抽芯动作。
这时塑件包在型芯上随动 模继续后移,直到注射机 顶杆与模具推板接触,推 出机构开始工作,推杆将 塑件从型芯上推出。
合模时,复位杆使推出机 构复位,斜导柱使侧型芯 滑块向内移动复位,最后 由楔紧块锁紧。
3.浇注系统
将塑料由注射机喷嘴引向型腔的流道称为浇注系统, 浇注系统分主流道、分流道、浇口、冷料穴四个部 分,是由浇口套、拉料杆和定模板上的流道组成。
塑料成型工艺与模具结构单元四 双分型面注射模结构

第三节 双分型面注射模典型结构
弹簧-滚柱式定距分型机构
图4-11 弹簧-滚柱式定距分型机构(一) 1—支座 2—弹簧座 3—弹簧 4—滚柱 5—拉杆 6—定模座板 7—定模板 8—定距螺钉 9—动模板
第三节 双分型面注射模典型结构
弹簧-滚柱式定距分型机构
图4-12 弹簧-滚柱式定距分型机构(二) 1—拉杆 2—支座 3—拉杆固定座 4—定模座板 5—滚柱 6—定模板 7—动模板 8—弹
第一节 双分型面注射模概述
4)推出装置,包括推杆13、推杆固定板3、推板2和推件板6。 5)定距分型部分,包括定距拉杆7及其端部的螺母、弹簧8。 6)结构零部件,包括模脚1、支承板4、型芯固定板5、流道板9和定 模板10等。
第一节 双分型面注射模概述
图4-2 弹簧分型拉杆定距式双分型面注射模 1—模脚 2—推板 3—推杆固定板 4—支承板
第一节 双分型面注射模概述
动模继续后移,B—B分型面分型,塑件包紧在型芯11上留在动模一 侧,浇注系统凝料在浇口处自行拉断,然后在A—A分型面之间自行 脱落或人工取出。动模继续后移,当注射机的顶杆接触推板2时,推 出机构开始工作,在推杆13和推件板6的推动下将塑件从型芯11上推 出,在B—B分型面之间自行落下。
第一节 双分型面注射模概述
一、双分型面注射模结构特点 双分型面注射模泛指浇源自系统凝料和塑件由不同分型面取出的注
射模,也称为三板式注射模。 1.双分型面注射模的组成
如图4⁃2所示,双分型面注射模由以下几部分组成: 1)成型零部件,包括型芯11、流道板9。 2)浇注系统,包括浇口套12、流道板9、定模板10。 3)导向部分,包括导柱14、定距拉杆7和流道板9上的导向孔。
- 1、下载文档前请自行甄别文档内容的完整性,平台不提供额外的编辑、内容补充、找答案等附加服务。
- 2、"仅部分预览"的文档,不可在线预览部分如存在完整性等问题,可反馈申请退款(可完整预览的文档不适用该条件!)。
- 3、如文档侵犯您的权益,请联系客服反馈,我们会尽快为您处理(人工客服工作时间:9:00-18:30)。
二、相关知识
(一)注射模具的分类及组成 2.注射模具的组成
(1)成型零件:构成模具型腔的零件 (2)浇注系统:将熔融塑料由注射机喷嘴引向型腔的流道,一般由主流道, 分流道,浇口,冷料穴组成。 (3)导向机构:是指保证动、定模合模时正确对合和推出机构运动的平稳性。 (4)侧向分型与抽芯机构 :塑件上的侧向如有凹凸形状、孔或凸台,这就需要 有侧向的凸模或成型块来成型。
图7-10 热流道注射模 1—动模座板 2、13—垫块 3—推板 4—推杆固定板 5—推杆 6—支承板 7—导套8—动模板 9—凸模 10—导柱 11—定模板 12—凹模 14—喷嘴 15—热流道板 16—加热器孔道 17—定模座板 18—绝热层9—浇口套 20—定位圈 21—注射机喷嘴
(4 ) 按成型技术可分为:
低发泡注射模、精密注射模、气辅成型注射模、双色注射模、多色注射模
2.注射模具的结构 9 10 11 12 13 14 15
8 7
6 5 4
3
2
1
1-定位圈 2-定模座板 3-浇口套 4-定模板 5-动模板 6-支承板 7-推杆固定板 8-推板 9-支架 10-推杆 11-拉料杆 12-导柱 13-型芯 14-凹模 15-冷却水道
(1) 按注射模的总体结构特征对其进行分类,可分为以下几种:
单分型面注射模、双分型面注射模、带侧向分型与抽芯机构的注射模、单 型腔注射模 、多型腔注射模、自动卸螺纹注射模 、无流道注射模等
(2 )按浇注系统结构形式可分:
普通浇注系统注射模、热流道浇注系统注射模
(3) 按塑料性质可分为:
热塑性塑料注射模具、热固性塑料注射模具
二、相关知识
(二)典型注射模具结构 2.双分型面注射模
二、相关知识
(二)典型注射模具结构 2.双分型面注射模
( l)浇口的形式 点浇口直径 0.5 ~1.5mm。 (2)导柱的设置 通常设置在动模一侧或凸模较高的一侧
二、相关知识
(二)典型注射模具结构 3.侧向分型与抽芯注射模 当塑件侧壁有孔、凹槽或 凸起时,其成型零件必须制
(5)推出机构: 推出机构是指模具分型后将塑件从模具中推出的装置。
(6)温度调节系统 :控制模具的温度 (7)排气系统:注射时,将型腔内德气体排出 (8)支承零部件:用来安装固定或支承前述的各部分机构的零部件均称为支承 零部件。
二、相关知识
(二)典型注射模具结构 1.单分型面注射模
也叫二板模,既可设计成单型腔注射模, 也可设计成多型腔注射模, 应用十分广泛。
图7-5 带有活动镶块的注射模 1—定模座板(兼凹模) 2—导柱 3—活动镶块 4—型芯 5—动模板 6—支承板 7—动模座(模脚) 8—弹簧 9—推杆 10—推杆固定板 11—推板
二、相关知识
(二)典型注射模具结构 5.角式注射模用注射模
主流道、分流道开设在分型面上,而且主流道截面的形状一般为圆形或扁圆形, 注射方向与合模方向垂直,特别适合于一模多腔、塑件尺寸较小的注射模具
1—模脚 2—支承板 3—成型镶块 4、6—螺钉 5—动模板 7—推件板 8—拉板 9—定模板 10—定模座板 11—型芯 12—导柱
二、相关知识
(二)典型注射模具结构 7.热流道注射模
它包括用于热塑性塑料的热流道或绝 热流道注射模和用于热固性塑料的温流 道注射模等,是一种成型后只需取出塑 件而无流道凝料的注射模。在成型过程 中,模具浇注系统中的塑料始终保持熔 融状态。 节省了塑料用量,提高了生产效率, 有利于实现自动化生产,保证塑件质量。 但无流道凝料注射模结构复杂,造价高, 模温控制要求严格,对塑件形状和塑料 品种也有一定限制,因此仅适用于大批 量生产。
项目5 注射模具的分类及组成
1.注射模
概念
通过注射机的螺杆或活
塞,使料筒内塑化熔融的塑
料经喷嘴与浇注系统注入型
腔,并固化成型所用的模具,
称为塑料注射模具,简称注
射模。
二、相关知识
(一)注射模具的分类及组成
1.注射模的工作原理
动画3-2
二、相关知识
(一)注射模具的分类及组成 1.注射模具的分类
18-定模座板
二、相关知识
(二)典型注射模具结构 4.带有活动镶块的注射模
有的塑料制品带有内侧凸、凹槽 或螺纹等,为简化模具结构,需要在 模具上设置活动镶件:活动型芯、 螺纹型芯、型环等。 应注意: 1. 活动镶件在模具中应有 可靠的定位和正确的配合; H8/f8 配合5 ~ 10 mm,其余 长度3˚~5˚的斜面; 2. 推杆先复位,否则活动 镶件将无法放人安装孔内。
9-推模固定板 10-支承板 11-动模板 12-推件板 13-中间板 14-定模板
二、相关知识
(二)典型注射模具结构 2.双分型面注射模
A-A分型面取出浇注系统凝料; B-B分型面取出塑件 双分型面增加一块中间板(浇道板), 所以也叫三板式注射模(动模板、浇道板、定模板)。 常用于点浇口进料的单腔或多腔模具。
二、相关知识
(二)典型注射模具结构 5.自动卸螺纹的注射模
二、相关知识
(二)典型注射模具结构 6.定模设置推出机构的注射模
因推出机构一般设在
动模一侧,所以注射模开模 后,塑件应留在动模一侧。
但有时因塑件的特殊要求或 受塑件形状的限制,开模后, 塑件留在定模上(或有可能 留在定模上),则应在定模 一侧设置推出机构。
( 1 )分流道开设在分型面上 ( 2 )塑件应尽量留在动模一侧。 ( 3 )动模一侧必须设有拉料杆 ( 4 )合模导柱既可设置在动模一侧也可设置在定模一侧, 标准模架的导柱一般都设置在动模一侧。 ( 5 )常用的复位机构有复位杆复位和弹簧复位两种。
2.双分型面注射模
1-浇口套 2-限位钉 3-弹簧 4-导柱 5-推杆 6-型芯 7-推板 8-支架
成可侧向移动的,否则塑件
无法脱模。 带动侧向成型零件进行侧 向移动的整个机构称为侧向 分型与抽芯机构。
3.侧向分型与抽芯注射模
1-定位圈 2-浇口套
3-锁紧块 4-斜导柱
5-滑块拉杆 6-螺母
7-推件板 8-推杆 9-推杆固定板 10-推板 11-支架 12-垫块 13-支撑板 14-动模板 15-型芯 16-侧型芯滑块 17-定模板