喷砂抛丸基本知识
抛丸、喷丸、喷砂等表面处理工艺简介.

抛丸、喷丸、喷砂等表面处理工艺简介抛丸(pāo wán) 英文名:shot blast抛丸是一种机械方面的表面处理工艺的名称,类似的工艺还有喷砂和喷丸。
抛丸的原理是用电动机带动叶轮体旋转(直接带动或用V型皮带传动),靠离心力的作用,将直径约在0.2~3.0的弹丸(有铸钢丸、钢丝切丸、不锈钢丸等不同类型)抛向工件的表面,使工件的表面达到一定的粗造度,使工件变得美观,或者改变工件的焊接拉应力为压应力,提高工件的使用寿命。
通过提高工件表面的粗糙度,也提高了工件后续喷漆的漆膜附着力。
抛丸这种工艺几乎用于机械的大多数领域,如修造船、汽车零部件、飞机部件、枪炮坦克表面、桥梁、钢结构、玻璃、钢板型材、管道内外壁防腐甚至道路表面等等行业。
原理抛丸的原理抛丸是靠叶轮高速旋转,将在叶轮中心的磨料,经过调流块(Regulator)及叶轮推动器(Impeller)预加速,送入叶片区再将磨料高速抛出,速度可超过100m/s,由于抛丸覆盖范围较大,所以不需利用气压,能源效益远高于喷枪。
叶轮是抛丸机的心脏,由电动马达直接或间接驱动,每家叶轮生产商均有独特的设计,主要分为单碟和双碟叶轮。
每片叶轮可装上4至8块叶片。
单碟叶轮较轻及设计成弧形叶片;双碟式叶轮较重,但较易装卸叶片及准确控制抛出磨料。
叶片的形状有直身或弧形设计,直身叶片设计简单,可独立装卸,虽然这种叶片设计可清理的范围(见下文)较小和抛出速度较低,但由于成本低,因此较为普遍。
弧形叶片较难装卸和成本较高,但可清理的范围较大及抛出速度较高。
另外,叶轮在抛丸室的摆放位置亦很重要,如覆盖范围、与工件距离、工件移动范围、受磨料二次反弹或其它叶轮的相互覆盖范围、保养更换的方便性等。
经验显示倾斜的叶轮对工件覆盖较好,而数个小功率叶轮较一个大功率叶轮在运作时会较灵活和效果更佳。
抛丸工艺损耗性很高,其中包括叶轮和内衬钢板等会较易磨损,因此它们的寿命对生产工序很重要。
高铬铸钢叶轮如使用48HRC硬度的钢砂,寿命约为800小时,钢丸则为1500小时。
抛丸和喷砂
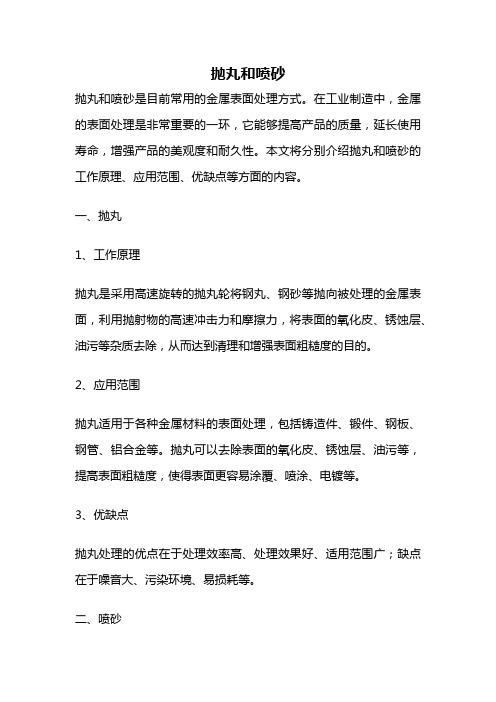
抛丸和喷砂
抛丸和喷砂是目前常用的金属表面处理方式。
在工业制造中,金属的表面处理是非常重要的一环,它能够提高产品的质量,延长使用寿命,增强产品的美观度和耐久性。
本文将分别介绍抛丸和喷砂的工作原理、应用范围、优缺点等方面的内容。
一、抛丸
1、工作原理
抛丸是采用高速旋转的抛丸轮将钢丸、钢砂等抛向被处理的金属表面,利用抛射物的高速冲击力和摩擦力,将表面的氧化皮、锈蚀层、油污等杂质去除,从而达到清理和增强表面粗糙度的目的。
2、应用范围
抛丸适用于各种金属材料的表面处理,包括铸造件、锻件、钢板、钢管、铝合金等。
抛丸可以去除表面的氧化皮、锈蚀层、油污等,提高表面粗糙度,使得表面更容易涂覆、喷涂、电镀等。
3、优缺点
抛丸处理的优点在于处理效率高、处理效果好、适用范围广;缺点在于噪音大、污染环境、易损耗等。
二、喷砂
1、工作原理
喷砂是利用压缩空气将磨料喷向被处理的金属表面,利用磨料的高速冲击力和摩擦力,将表面的氧化皮、锈蚀层、油污等杂质去除,从而达到清理和增强表面粗糙度的目的。
2、应用范围
喷砂适用于各种金属材料的表面处理,包括铸造件、锻件、钢板、钢管、铝合金等。
喷砂可以去除表面的氧化皮、锈蚀层、油污等,提高表面粗糙度,使得表面更容易涂覆、喷涂、电镀等。
3、优缺点
喷砂处理的优点在于处理效果好、适用范围广、成本低;缺点在于处理效率低、易产生粉尘、对环境污染严重。
总的来说,抛丸和喷砂都是有效的金属表面处理方式,可以根据实际情况选择其中一种或两种方式进行表面处理。
在选择时,需要考虑到处理效率、处理效果、环境污染、成本等多个方面的因素,综合评估后选择最适合的表面处理方式。
抛丸、喷丸、喷砂等表面处理工艺简介

抛丸抛丸(pāo wán) 英文名:shot blast抛丸是一种机械方面的表面处理工艺的名称,类似的工艺还有喷砂和喷丸。
抛丸的原理是用电动机带动叶轮体旋转(直接带动或用V型皮带传动),靠离心力的作用,将直径约在0.2~3.0的弹丸(有铸钢丸、钢丝切丸、不锈钢丸等不同类型)抛向工件的表面,使工件的表面达到一定的粗造度,使工件变得美观,或者改变工件的焊接拉应力为压应力,提高工件的使用寿命。
通过提高工件表面的粗糙度,也提高了工件后续喷漆的漆膜附着力。
抛丸这种工艺几乎用于机械的大多数领域,如修造船、汽车零部件、飞机部件、枪炮坦克表面、桥梁、钢结构、玻璃、钢板型材、管道内外壁防腐甚至道路表面等等行业。
原理抛丸的原理抛丸是靠叶轮高速旋转,将在叶轮中心的磨料,经过调流块(Regulator)及叶轮推动器(Impeller)预加速,送入叶片区再将磨料高速抛出,速度可超过100m/s,由于抛丸覆盖范围较大,所以不需利用气压,能源效益远高于喷枪。
叶轮是抛丸机的心脏,由电动马达直接或间接驱动,每家叶轮生产商均有独特的设计,主要分为单碟和双碟叶轮。
每片叶轮可装上4至8块叶片。
单碟叶轮较轻及设计成弧形叶片;双碟式叶轮较重,但较易装卸叶片及准确控制抛出磨料。
叶片的形状有直身或弧形设计,直身叶片设计简单,可独立装卸,虽然这种叶片设计可清理的范围(见下文)较小和抛出速度较低,但由于成本低,因此较为普遍。
弧形叶片较难装卸和成本较高,但可清理的范围较大及抛出速度较高。
另外,叶轮在抛丸室的摆放位置亦很重要,如覆盖范围、与工件距离、工件移动范围、受磨料二次反弹或其它叶轮的相互覆盖范围、保养更换的方便性等。
经验显示倾斜的叶轮对工件覆盖较好,而数个小功率叶轮较一个大功率叶轮在运作时会较灵活和效果更佳。
抛丸工艺损耗性很高,其中包括叶轮和内衬钢板等会较易磨损,因此它们的寿命对生产工序很重要。
高铬铸钢叶轮如使用48HRC硬度的钢砂,寿命约为800小时,钢丸则为1500小时。
抛丸、喷砂、喷丸

3.阿尔门(Almen)试验
喷丸强度常用N试片(用于有色金属试验)、A试片(最常用)、C试片(更高强度)来进行测量, A试片和C试片之间关系为近似3倍关系。如用C试片测得强度为0.15-0.20C mm就相当于0.45-0.60A mm。图中厚的为C试片,薄的为A试片。
试验过程中,先测量试片原有变形,然后将卡好该试片的工装置于喷丸箱内,采用与工件相同的工艺进行喷射。喷丸结束,取下试片,测量变形拱高。
2.喷丸强度
影响喷丸强度的工艺参数主要有:弹丸直径、弹流速度、弹丸流量、喷丸时间等。弹丸直径越大,速度越快,弹丸与工件碰撞的动量越大,喷丸的强度就越大。喷丸形成的残余压应力可以达到零件材料抗拉强度的60%,残余压应力层的深度通常可达0.25mm,最大极限值为1mm左右。喷丸强度需要一定的喷丸时间来保证,经过一定时间,喷丸强度达到饱和后,再延长喷丸时间,强度不再明显增加。在喷丸强度的阿尔门试验中,喷丸强度的表征为试片变形的拱高。
4.喷丸覆盖有人对喷丸覆盖率常这样认为:我的喷嘴1上1下喷工件2遍,不就可以满足200%的覆盖率了吗?乍一听觉得有道理,其实不是这样的。
覆盖率的测量是这样的:先在工件表面涂上一层彩釉或萤光釉,然后按工艺参数对工件进行喷丸,每喷表面一遍将工件取出,在显微镜(放大镜)下观察所残留的涂层在表面所占的比例,如还有20%残留,则覆盖率为80%。当残留只有2%,即覆盖率为98%时,可视为全部清除,即覆盖率为100%,此时就有一个时间。若达到400%的覆盖率,就是4倍的该时间。
5.覆盖率的影响因素
影响覆盖率的因素有零件材料硬度、弹丸直径、喷射角度和距离、喷丸时间等。在规定的喷丸强度条件下,零件的硬度低于或等于标准试片硬度时,覆盖率能达到100%;反之,覆盖率会下降。在相同的弹丸流量下,喷嘴与工件的距离越长、喷射的角度越小、弹丸直径越小,达到覆盖率要求的时间就越短。喷丸强化时,应选择大小合适的弹丸、喷射角度及距离,使喷丸强度和覆盖率同时达到要求值。
喷丸强化基础知识ballshotpeening

喷丸强化工艺技术简介1强化喷丸概念在了解喷丸强化技术之前,有必要将抛丸、喷砂、喷丸的三个容易混淆的概念解释一下。
这三个概念其实就四个字:喷、抛、丸、砂,其中,喷抛是工艺方法,丸砂是使用的材料。
喷,是用高压空气将丸、砂吹到工件的表面,抛是用高速旋转的叶片抛射到工件表面,丸用的是钢丸,砂用的是石英砂等。
喷丸过程就是将大量弹丸喷射到零件表面上的过程,有如无数小锤对表面锤击,因此,金属零件表面产生极为强烈的塑性形变,使零件表面产生一定厚度的冷作硬化层,称为表面强化层,此强化层会显著地提高零件的疲劳强度。
测评强化丸质量有三个基本参数:强度、覆盖率、表面粗糙度。
2喷丸强度影响喷丸强度的工艺参数主要有:弹丸直径、弹流速度、弹丸流量、喷丸时间等。
弹丸直径越大,速度越快,弹丸与工件碰撞的动量越大,喷丸的强度就越大。
喷丸形成的残余压应力可以达到零件材料抗拉强度的60%,残余压应力层的深度通常可达0. 25mm,最大极限值为1mm左右。
喷丸强度需要一定的喷丸时间来保证,经过一定时间,喷丸强度达到饱和后,再延长喷丸时间,强度不再明显增加。
在喷丸强度的阿尔门试验中,喷丸强度的表征为试片变形的拱高。
3阿尔门(Almen)试验喷丸强度常用N试片(用于有色金属试验)、A试片(最常用)、C试片(更高强度)来进行测量,A试片和C试片之间关系为近似3倍关系。
如用C试片测得强度为0. 15~0.20Cmm就相当于0.45~0.60Amm。
图中厚的为C试片,薄的为A试片。
试验过程中,先测量试片原有变形,然后将卡好该试片的工装置于喷丸箱内,采用与工件相同的工艺进行喷射。
喷丸结束,取下试片,测量变形拱高。
4喷丸覆盖率覆盖率是指工件上每一个点被钢丸打到的次数,有人对喷丸覆盖率常这样认为:我的喷嘴1上1下喷工件2遍,不就可以满足200%的覆盖率了吗?乍一听觉得有道理,其实不是这样的。
覆盖率的测量是这样的:先在工件表面涂上一层彩釉或萤光釉,然后按工艺参数对工件进行喷丸,每喷表面一遍将工件取出,在显微镜(放大镜)下观察所残留的涂层在表面所占的比例,如还有20%残留,则覆盖率为80%。
喷砂,抛丸,喷丸的区别
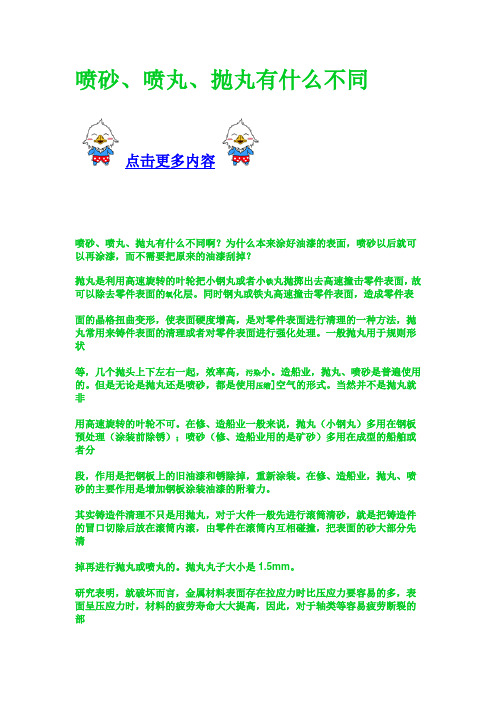
喷砂、喷丸、抛丸有什么不同点击更多内容喷砂、喷丸、抛丸有什么不同啊?为什么本来涂好油漆的表面,喷砂以后就可以再涂漆,而不需要把原来的油漆刮掉?抛丸是利用高速旋转的叶轮把小钢丸或者小铁丸抛掷出去高速撞击零件表面,故可以除去零件表面的氧化层。
同时钢丸或铁丸高速撞击零件表面,造成零件表面的晶格扭曲变形,使表面硬度增高,是对零件表面进行清理的一种方法,抛丸常用来铸件表面的清理或者对零件表面进行强化处理。
一般抛丸用于规则形状等,几个抛头上下左右一起,效率高,污染小。
造船业,抛丸、喷砂是普遍使用的。
但是无论是抛丸还是喷砂,都是使用压缩]空气的形式。
当然并不是抛丸就非用高速旋转的叶轮不可。
在修、造船业一般来说,抛丸(小钢丸)多用在钢板预处理(涂装前除锈);喷砂(修、造船业用的是矿砂)多用在成型的船舶或者分段,作用是把钢板上的旧油漆和锈除掉,重新涂装。
在修、造船业,抛丸、喷砂的主要作用是增加钢板涂装油漆的附着力。
其实铸造件清理不只是用抛丸,对于大件一般先进行滚筒清砂,就是把铸造件的冒口切除后放在滚筒内滚,由零件在滚筒内互相碰撞,把表面的砂大部分先清掉再进行抛丸或喷丸的。
抛丸丸子大小是1.5mm。
研究表明,就破坏而言,金属材料表面存在拉应力时比压应力要容易的多,表面呈压应力时,材料的疲劳寿命大大提高,因此,对于轴类等容易疲劳断裂的部件通常采用喷丸形成表面压应力,提高产品寿命,此外,金属金属材料对拉伸很敏感,这就是材料的拉伸强度比压缩强度低的多的原因,这也是金属材料一般用拉伸强度(屈服,抗拉)表示材料性能的原因。
我们日常乘坐的汽车的钢板的工作面就是用喷丸来强化的,可以显著的提高材料的抗疲劳强度。
抛丸是用电机带动叶轮体旋转,靠离心力的作用,将直径在0.2~3.0的丸子(有铸丸\切丸\不锈钢丸等)抛向工件的表面,使工件的表面达到一定的粗造度,使工件变的美观,或着改变工件的焊接拉应力为压应力,提高工件的使用寿命.几乎用于机械的大多数领域,修造船\汽车零部件\飞机部件\枪炮坦克表面\桥梁\钢结构\玻璃\钢板\管道\等等.喷砂(丸)是用压缩空气作为动力将直径在40~120目的砂或0.1~2.0左右的丸喷向工件的表面,使工件达到同样的效果.丸粒的大小不同,达到的处理效果就不一样.重点提出:喷丸同样能起到强化的作用.现在国内的设备走进了一个误区,认为只有抛丸才能达到强化的目的.美国\日本的企业用于强化的是抛喷丸并用的!各有各的优势.比如象齿轮这样的工件,抛丸的出丸角度无法改变,只能用变频改变初速度.但它处理的量大,速度快,而喷丸则正好于之相反,抛丸的效果就没有喷丸的效果好。
抛丸、喷丸、喷砂等表面处理工艺简介.

抛丸、喷丸、喷砂等表面处理工艺简介抛丸(pāo wán) 英文名:shot blast抛丸是一种机械方面的表面处理工艺的名称,类似的工艺还有喷砂和喷丸。
抛丸的原理是用电动机带动叶轮体旋转(直接带动或用V型皮带传动),靠离心力的作用,将直径约在0.2~3.0的弹丸(有铸钢丸、钢丝切丸、不锈钢丸等不同类型)抛向工件的表面,使工件的表面达到一定的粗造度,使工件变得美观,或者改变工件的焊接拉应力为压应力,提高工件的使用寿命。
通过提高工件表面的粗糙度,也提高了工件后续喷漆的漆膜附着力。
抛丸这种工艺几乎用于机械的大多数领域,如修造船、汽车零部件、飞机部件、枪炮坦克表面、桥梁、钢结构、玻璃、钢板型材、管道内外壁防腐甚至道路表面等等行业。
原理抛丸的原理抛丸是靠叶轮高速旋转,将在叶轮中心的磨料,经过调流块(Regulator)及叶轮推动器(Impeller)预加速,送入叶片区再将磨料高速抛出,速度可超过100m/s,由于抛丸覆盖范围较大,所以不需利用气压,能源效益远高于喷枪。
叶轮是抛丸机的心脏,由电动马达直接或间接驱动,每家叶轮生产商均有独特的设计,主要分为单碟和双碟叶轮。
每片叶轮可装上4至8块叶片。
单碟叶轮较轻及设计成弧形叶片;双碟式叶轮较重,但较易装卸叶片及准确控制抛出磨料。
叶片的形状有直身或弧形设计,直身叶片设计简单,可独立装卸,虽然这种叶片设计可清理的范围(见下文)较小和抛出速度较低,但由于成本低,因此较为普遍。
弧形叶片较难装卸和成本较高,但可清理的范围较大及抛出速度较高。
另外,叶轮在抛丸室的摆放位置亦很重要,如覆盖范围、与工件距离、工件移动范围、受磨料二次反弹或其它叶轮的相互覆盖范围、保养更换的方便性等。
经验显示倾斜的叶轮对工件覆盖较好,而数个小功率叶轮较一个大功率叶轮在运作时会较灵活和效果更佳。
抛丸工艺损耗性很高,其中包括叶轮和内衬钢板等会较易磨损,因此它们的寿命对生产工序很重要。
高铬铸钢叶轮如使用48HRC硬度的钢砂,寿命约为800小时,钢丸则为1500小时。
工艺讲解抛丸、喷丸、喷砂

⼯艺讲解抛丸、喷丸、喷砂丸与砂:丸⼀般是球形⼀类没有棱⾓的颗粒.如钢丝切丸等; 砂是指有棱⾓的砂粒,如棕刚⽟、⽩刚⽟、河砂等。
喷与抛:喷是以压缩空⽓作为动⼒将砂料或丸料喷到材料表⾯,达到清除和⼀定的粗糙度。
抛是将丸料以⾼速旋转时产⽣的离⼼⼒的⽅法,冲击材料表⾯,达到清除和⼀定的粗糙度。
其实看到这,我想⼤家都已经彻彻底底地将喷丸,抛丸,喷砂分清楚了,有⼩伙伴问,那有没有抛砂啊?我说,有!在建筑⼯地上,⼯⼈⽤铁锹和泥的时候可能会抛砂,⼯业上没有!呵呵呵下⾯咱们就针对每个概念再深⼊地聊聊吧...喷丸:使⽤丸粒轰击⼯件表⾯并植⼊残余压应⼒,提升⼯件疲劳强度的冷加⼯⼯艺。
喷丸处理是⼯⼚⼴泛采⽤的⼀种表⾯强化⼯艺,其设备简单、成本低廉,不受⼯件形状和位置限制,操作⽅便,但⼯作环境较差。
喷丸⼴泛⽤于提⾼零件机械强度以及耐磨性、抗疲劳和耐腐蚀性等。
还可⽤于表⾯消光、去氧化⽪和消除铸、锻、焊件的残余应⼒等。
清理特点:1、可以任意使⽤⾦属或⾮⾦属弹丸,以适应清理⼯件表⾯的不同要求;2、清理的灵活性⼤,容易清理复杂⼯件的内、外表⾯和管件的内壁,并且不受场地限制,可将设备安置在特⼤型⼯件附近;3、设备结构较简单,整机投资少,易损件少,维修费⽤低;4、必须配备⼤功率的空压站,在清理效果相同的条件下,消耗的能量较⼤;5、清理表⾯易有湿⽓,容易再⽣锈;6、清理效率低,操作⼈员多,劳动强度⼤。
抛丸:抛丸是⼀个冷处理过程,分为抛丸清理和抛丸强化,抛丸清理顾名思义是为了去除表⾯氧化⽪等杂质提⾼外观质量,抛丸强化就是利⽤⾼速运动的弹丸(60-110m/s)流连续冲击被强化⼯件表⾯,迫使靶材表⾯和表层(0.10-0.85mm)在循环性变形过程中发⽣以下变化:1.显微组织结构发⽣改性;2.⾮均匀的塑变外表层引⼊残余压应⼒,内表层⽣产残余拉应⼒;3.外表⾯粗糙度发⽣变化(Ra Rz)。
影响:可提⾼材料/零件疲劳断裂抗⼒,防⽌疲劳失效,塑性变形与脆断,提⾼疲劳寿命。
- 1、下载文档前请自行甄别文档内容的完整性,平台不提供额外的编辑、内容补充、找答案等附加服务。
- 2、"仅部分预览"的文档,不可在线预览部分如存在完整性等问题,可反馈申请退款(可完整预览的文档不适用该条件!)。
- 3、如文档侵犯您的权益,请联系客服反馈,我们会尽快为您处理(人工客服工作时间:9:00-18:30)。
一.喷砂行业常用英语shot blast 喷砂;喷丸清理;喷砂清理;喷净法shot-blast 喷丸加工;喷砂加工;喷丸加工sand blast machine 喷砂机sand blast rubber hose 喷沙胶管Sandblasting equipment 喷砂设备sand blasting 喷砂处理sand blasting cleaner 喷砂清理机sand blasting machine 喷砂机sand blasting nozzle 喷砂嘴sand blowing 喷砂打光sand blast rubber hose 喷砂橡胶管shot blast chamber 喷丸清理室shot blast cleaning 喷丸清理shot blast shop 喷丸除锈车间shot hanger blast 悬链式连续抛丸清理机;连续喷丸清砂;悬链式连续抛丸清理机shot-blast cabinet 喷丸室shot-blast chamber 喷丸室shot-blast cleaning barrel 抛丸清理滚筒shot-blast room 喷丸室shot-blast Shove out! 撑开!shot-blast unit 喷丸装置air shot blast machine 喷丸清理机combined shot-blast shakeout cleaning chamber 抛喷丸落砂清理室blast 阵风;气浪;炸毁;炸药shot 装子弹;注塑量;注料量;注射SHOT =Society for the History of Technology 技术史学会[美]blast furnace blast 高炉鼓风shot after shot 一枪接一枪shot-by-shot deconvolution 逐炮反褶积二.喷砂清理与抛丸清理区别抛丸是利用高速旋转的叶轮把小钢丸或者小铁丸抛掷出去高速撞击零件表面,故可以除去零件表面的氧化层。
同时钢丸或铁丸高速撞击零件表面,造成零件表面的晶格扭曲变形,使表面硬度增高,是对零件表面进行清理的一种方法,抛丸常用来铸件表面的清理或者对零件表面进行强化处理。
一般抛丸用于规则形状等,几个抛头上下左右一起,效率高,污染小。
造船业,抛丸、喷砂是普遍使用的。
但是无论是抛丸还是喷砂,都是使用压缩空气的形式。
当然并不是抛丸就非用高速旋转的叶轮不可。
在修、造船业一般来说,抛丸(小钢丸)多用在钢板预处理(涂装前除锈);喷砂(修、造船业用的是矿砂)多用在成型的船舶或者分段,作用是把钢板上的旧油漆和锈除掉,重新涂装。
在修、造船业,抛丸、喷砂的主要作用是增加钢板涂装油漆的附着力。
其实铸造件清理不只是用抛丸,对于大件一般先进行滚筒清砂,就是把铸造件的冒口切除后放在滚筒内滚,由零件在滚筒内互相碰撞,把表面的砂大部分先清掉再进行抛丸或喷丸的。
抛丸丸子大小是1.5mm。
研究表明,就破坏而言,金属材料表面存在拉应力时比压应力要容易的多,表面呈压应力时,材料的疲劳寿命大大提高,因此,对于轴类等容易疲劳断裂的部件通常采用喷丸形成表面压应力,提高产品寿命,此外,金属金属材料对拉伸很敏感,这就是材料的拉伸强度比压缩强度低的多的原因,这也是金属材料一般用拉伸强度(屈服,抗拉)表示材料性能的原因。
我们日常乘坐的汽车的钢板的工作面就是用喷丸来强化的,可以显著的提高材料的抗疲劳强度。
抛丸是用电机带动叶轮体旋转,靠离心力的作用,将直径在0.2~3.0的丸子(有铸丸\切丸\不锈钢丸等)抛向工件的表面,使工件的表面达到一定的粗造度,使工件变的美观,或着改变工件的焊接拉应力为压应力,提高工件的使用寿命.几乎用于机械的大多数领域,修造船\汽车零部件\飞机部件\枪炮坦克表面\桥梁\钢结构\玻璃\钢板\管道\等等.喷砂(丸)是用压缩空气作为动力将直径在40~120目的砂或0.1~2.0左右的丸喷向工件的表面,使工件达到同样的效果.丸粒的大小不同,达到的处理效果就不一样.重点提出:喷丸同样能起到强化的作用.现在国内的设备走进了一个误区,认为只有抛丸才能达到强化的目的.美国\日本的企业用于强化的是抛喷丸并用的!各有各的优势.比如象齿轮这样的工件,抛丸的出丸角度无法改变,只能用变频改变初速度.但它处理的量大,速度快,而喷丸则正好于之相反,抛丸的效果就没有喷丸的效果好。
喷砂是利用压缩空气把石英砂高速吹出去对零件表面进行清理的一种方法。
工厂里也叫吹砂,不仅去锈,还可以顺带除油,对涂装来说非常有用。
常用于零件表面除锈;对零件表面修饰(市场卖的小型的湿式喷砂机就是这个用途,砂粒通常是刚玉,介质是水);在钢结构中,应用高强螺栓进行联接是一种比较先进的方法,由于高强联接是利用结合面之间的摩擦来传力的,所以对结合表面的质量要求很高,这时必须用喷砂对结合表面进行处理。
喷沙用于形状复杂,易于用手工除锈,效率不高,现场环境不好,除锈不均匀。
一般的喷砂机都有各种规格的喷砂枪,只要不是特别小的箱体,都可以把枪放进去打干净。
压力容器的配套产品—封头采用喷砂方式清除工件表面的氧化皮,石英砂的直径为 1.5mm~3.5mm.有一种加工就是利用水作载体,带动金刚砂来加工零件的,就是一种喷砂。
喷砂是采用压缩空气为动力,以形成高速喷射束将喷料高速喷射到被需处理工件表面,使工件表面的外表面的外表或形状发生变化,由于磨料对工件表面的冲击和切削作用,使工件的表面获得一定的清洁度和不同的粗糙度,使工件表面的机械性能得到改善,因此提高了工件的抗疲劳性,增加了它和涂层之间的附着力,延长了涂膜的耐久性,也有利于涂料的流平和装饰。
喷砂工艺与其它清理工艺相比有以下特点:一、喷砂处理是最彻底、最通用、最迅速、效率最高的清理方法。
二、喷砂处理可以在不同粗糙度之间任意选择,而其它工艺是没办法实现这一点的。
手工打磨可以打出毛面但速度太慢,化学溶剂清理则清理表面过于光滑不利于涂层粘接。
喷砂作为一种常规的磨料射流技术经过不断的发展、提高和完善,以其独特的加工机理和广泛的加工、应用范围,使其在当今的表面处理行业中越来越受到青睐,已广泛地应用于机械制造、仪器仪表、医疗器械、电子电器、纺织机械、印染机械、化工机械、食品机械、工具、刃具、量具、模具、玻璃、陶瓷、工艺品、机械修理等等众多领域。
三.喷砂工艺研究一、前处理对于工件在被喷涂、喷镀保护层(油漆或其它防腐物料)之前,工件表面均应进行认真的处理,称之为前处理。
前处理质量好坏,影响着涂层的附着力、外观、涂层的耐潮湿及耐腐蚀等方面,因最好的涂膜(层)都是粘附到被认真清理的表面。
前处理工作做的不好,锈蚀仍会在涂层下继续蔓延,使涂层成片脱落。
经过认真清理的表面和一般简单(手工用砂纸或刷子)清理的工件,用暴晒法进行涂层比较,寿命可相差4-5倍。
表面清理的方法很多,但被接受最普遍的方法是:A.溶剂清理 B.酸洗 C.手动工具 D.动力工具。
(中国喷砂机械网 )在这几种方式中,每种方式都有各自的适用范围,但在所有表面清理方法中,喷砂方法是最彻底、最通用、最广泛的方式,原因是:A、喷砂比其它方式对工件表面清理的速度和彻底最佳。
B、没有其它哪种工艺方法允许你在四种公认的、普遍接受二、喷砂是采用压缩空气为动力形成高速喷射束,将喷料(铜矿砂、石英砂、铁砂、海砂、金刚砂等)等高速喷射到需处理工件表面,使工件外表面的外表发生变化,由于磨料对工件表面的冲击和切削作用,使工件表面获得一定的清洁度和不同的粗糙度,使工件表面的机械性能得到改善,因此提高了工件的搞疲劳性,增加了它和涂层之间的附着力,延长了涂膜的耐久性,也有利于涂料的流平和装饰。
三、与其它前处理工艺(如酸洗、工具清理)对比1) 喷砂处理是最彻底、最通用、最迅速、效率最高的清理方法。
2) 喷砂处理可以在不同粗糙度之间任意选择,而其它工艺是没办法实现这一点的,手工打磨可以打出毛面但速度太慢动作,化学溶剂清理则清理表面过于光滑不利于涂层粘接。
的清洁度之间进行任意选择。
喷砂应用(一)工件涂镀、工件粘接前处理喷砂能把工件表面的锈皮等一切污物清除,并在工件表面建立起十分重要的基础图式(即通常所谓的毛面),而且可以通过调换不同粒度的磨料,达到不同程度的粗糙度,大大提高工件与涂料、镀料的结合力。
或使粘接件粘接更牢固,质量更好。
(二)铸锻件毛面、热处理后工件的清理与抛光喷砂能清理铸锻件、热处理后工件表面的一切污物(如氧化皮、油污等残留物),并将工件表面抛光提高工件的光洁度,起到美化工件的作用。
喷砂清理能使工件露出均匀一致的金属本色,使工件外表更美观,达到美化装饰的作用。
(三)机加工件毛刺清理与表面美化喷砂能清理工件表面的微小毛刺,并使工件表面更加平整,消除了毛刺的危害,提高了工件的档次。
并且喷砂能在工件表面交界处打出很小的圆角,使工件显得更加美观、更加精密。
(四)改善零件的机械性能机械零件经喷砂后,能在零件表面产生均匀细微的凹凸面(基础图式),使润滑油得到存储,从而使润滑条件改善,并减少噪声提高机械使用寿命。
(五)光饰作用1、对各种工件表面抛光,使工件表面更美观。
2、使工件达到光滑又不反光要求。
对于某些特殊用途工件,喷砂可随意实现不同的反光或亚光。
如不锈钢工件、木制家具表面亚光化,磨砂玻璃表面的花纹图案,以及布料表面的毛化加工等。
(六)消除应力及表面强化通过砂丸敲击工件表面,消除应力,增加工件表面强度,如弹簧、机加工刀具和飞机叶片等工件的表面处理。
清理等级也即清洁度,代表性国际标准有两种:一种是美国85年制订“SSPC-”;第二种是瑞典76年制订的“Sa-”,它分为四个等级分别为Sa1、Sa2、Sa2.5、Sa3,为国际惯常通用标准,详细介绍如下:Sa1级——相当于美国SSPC—SP7级。
采用一般简单的手工刷除、砂布打磨方法,这是四种清洁度中度最低的一级,对涂层的保护仅仅略好于未采用处理的工件。
Sa1级处理的技术标准:工件表面应不可见油污、油脂、残留氧化皮、锈斑、和残留油漆等污物。
Sa1级也叫做手工刷除清理级。
(或清扫级)Sa2级——相当于美国SSPC—SP6级。
采用喷砂清理方法,这是喷砂处理中最低的一级,即一般的要求,但对于涂层的保护要比手工刷除清理要提高许多。
Sa2级处理的技术标准:工件表面应不可见油腻、污垢、氧化皮、锈皮、油漆、氧化物、腐蚀物、和其它外来物质(疵点除外),但疵点限定为不超过每平方米表面的33%,可包括轻微阴影;少量因疵点、锈蚀引起的轻微脱色;氧化皮及油漆疵点。
如果工件原表面有凹痕,则轻微的锈蚀和油漆还会残留在凹痕底部。
Sa2级也叫商品清理级(或工业级)。
Sa2.5级——是工业上普遍使用的并可以作为验收技术要求及标准的级别。
Sa2.5级也叫近白清理级(近白级或出白级)。