焊缝磁粉检测工艺规程
磁粉检测工艺规程

磁粉检测工艺规程1. 0目的及适用范围1.1目的为保证磁粉检测的工作质量,提供准确可靠的检测数据,特制定本规程。
1.2适用范围1.1 本规程适用于铁磁性材料(磁导率≥1)制成的设备及其零部件之表面或近表面缺陷的检测和等级评定;1.2 本规程适用于连续电磁轭式磁粉检测和线圈磁化法的方法和要求。
2.0编制依据2.1本程序依据JB/T4730-2005.4《承压设备无损检测》编制;2.2本程序参照锅炉压力容器无损检测人员资格考核委员会编写的《磁粉检测》编制。
3.0检测设备和材料3.1 本工艺规程选定的设备为:3.1.1交流电磁轭式磁粉检测仪3.1.2线圈磁化法;3.2 为保证磁粉检测结果的可靠,磁粉探伤仪要进行定期校验,必要时可进行随机校验;3.3 磁轭提升力的校验:便携式交流磁轭式磁粉探伤仪(磁轭间距≤200mm),其提升力至少为45N(约4.5kg);3.4 磁粉及磁悬液3.4.1 磁粉应具有高导磁率和低剩磁性质,磁粉之间不应相互吸引,通常有Fe3O4和Fe2O3二种。
本公司采用喷罐式黑油磁悬液和湿式荧光磁粉;3.4.2 磁粉粒度应均匀,湿磁粉的平均粒度为2~10μm,最大粒度应不大于45μm。
本公司采用喷罐式黑油磁悬液、荧光磁粉;3.4.3 磁粉的颜色选定,是以工件表面与磁粉颜色形成有较高的对比度而定。
通常非荧光磁粉的颜色有:黑色、白色和红色几种,非荧光磁粉本公司采用黑色;3.4.4 当出现特殊情况下非荧光磁粉或采用荧光磁粉检测时采取现场自行配制,但必须满足如下要求:a). 湿式非荧光磁粉的配制:是以煤油做分散剂,另加适当的变压器油配制而成。
通常煤油和变压器比例各50%。
其磁悬液的浓度为每升磁悬液施加10~20g磁粉;b). 湿式荧光磁粉的配制:是以煤油做分散剂,另加适当的变压器油配制而成。
通常煤油和变压器比例各50%。
其磁悬液的浓度为每升磁悬液施加1~3g荧光磁粉;c).对配制的磁悬液须进行浓度测试,其方法为:以每100ml磁悬液盛入浓度测定管内,非荧光磁粉沉淀30min后观察磁粉沉淀体积为1.2~2.4ml为合格。
无损检测工艺规程(磁粉检验)
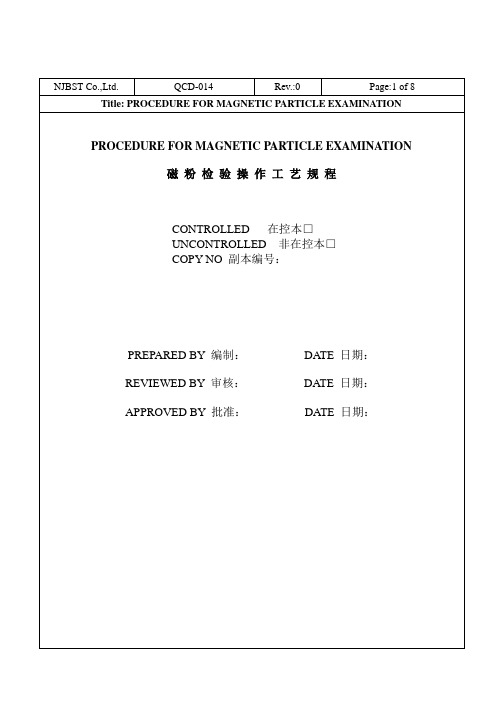
1. General
1.1 This procedure is applied to the magnetic particle examination of ferromagnetic materials and welds for ASME Code items.
1.2 The magnetic particle examination method is suitable for detecting cracks and other discontinuities on or near the surface in ferromagneticபைடு நூலகம்materials.
1.4 This procedure shall be demonstrated to the satisfaction of the AI prior to implementation.
2. Personnel
2.1 The NDE personnel who engage in magnetic particle examination shall be qualified and certified according to NJBST Co.,Ltd.’s “Written Practice for NDE Personnel Training, Examination, Qualification & Certification”(No.:QCD-011).
磁粉检测工艺规程
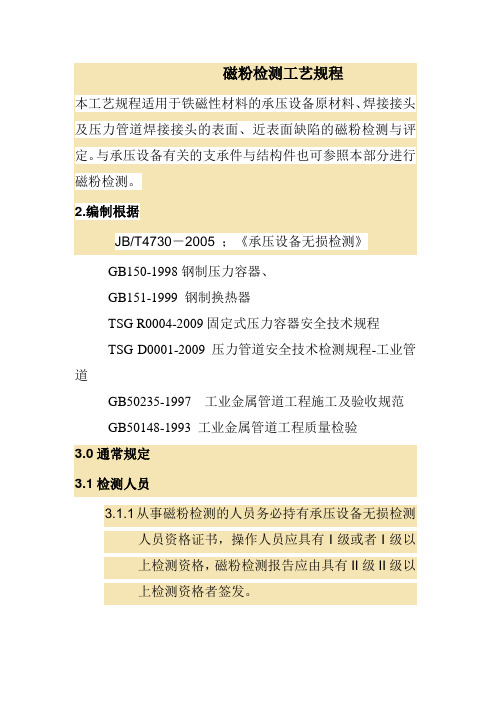
磁粉检测工艺规程本工艺规程适用于铁磁性材料的承压设备原材料、焊接接头及压力管道焊接接头的表面、近表面缺陷的磁粉检测与评定。
与承压设备有关的支承件与结构件也可参照本部分进行磁粉检测。
2.编制根据JB/T4730-2005 ;《承压设备无损检测》GB150-1998钢制压力容器、GB151-1999 钢制换热器TSG R0004-2009固定式压力容器安全技术规程TSG D0001-2009 压力管道安全技术检测规程-工业管道GB50235-1997 工业金属管道工程施工及验收规范GB50148-1993 工业金属管道工程质量检验3.0通常规定3.1检测人员3.1.1从事磁粉检测的人员务必持有承压设备无损检测人员资格证书,操作人员应具有I级或者I级以上检测资格,磁粉检测报告应由具有II级II级以上检测资格者签发。
3.1.2色盲、色弱及矫正视力低于1.0者不得从事磁分检测工作。
3.2检测设备与材料3.2.1检测设备3.2.1.1磁粉检测设备应经检定合格并在检定有效期内使用。
3.2.1.2磁粉检测作业前,检测设备应经调试合格。
当磁轭式检测设备磁轭间距为最大时,交流电磁轭至少应有45N的提升力;直流电磁轭至少应有177N的提升力;交叉磁轭至少应有118N的提升力(磁极与试件表面间隙为0.5mm)3.2.1.3使用剩磁法检测时,交流探伤机应配备断电相位操纵器。
3.2.1.4黑光辐照度及波长当使用荧光磁粉检测时,使用黑光灯在工件表面的黑光辐照度应大于或者等于1000μW/cm2,黑光的波长约为320nm~400nm,中心波长约365nm 。
黑光源应符合GB/T16673的规定。
3.2.1.5退磁装置应能保证工件退磁后表面剩磁小于或者等于0.3mT(240A/m) 。
3.2.1.6磁场强度计、标准试片、磁场指示器、黑光灯等辅助器材应满足磁粉检测的需要。
3.2.2检测材料3.2.2.1磁粉检测材料应有产品合格证或者质量证明书,并应符合下列要求:3.2.2.2磁粉应具有高导磁率、低矫顽力与低剩磁,磁粉之间不应相互吸引;3.2.2.3磁粉粒度均匀,颜色与检测工件应有较高的对比度。
磁粉检测工艺规程和工艺卡
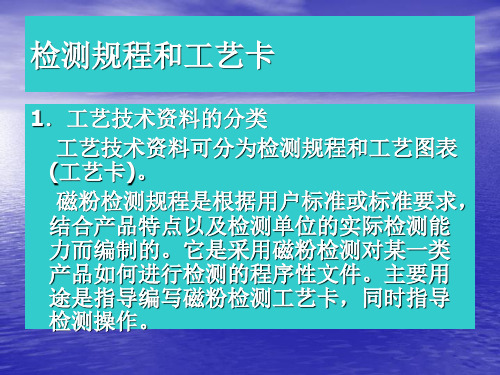
• 〔11〕光线及环境 使用荧光磁粉检测时,
暗区的“环境光照度应小于20lx 〞,“黑 光辐照度应不小于1000μW/cm2 〞。使用 非荧光磁粉检测时,“可见光照度应大于或 等于1000 lx〞。当现场采用便携式设备检 测,由于条件所限无法满足时,可见光照度 可适当降低,但“不得低于500lx 〞。
• 磁粉检测规程应纳入检测单位的工艺文件
管理系统严格管理(编号管理和版次管理);
• 磁粉检测工艺规程的更改应按检测单位相
关文件规定的更改程序进行,执行与编制 相同的审核和批准程序。未按规定的更改 程序进行的更改是无效的。
• 应保持检测工艺规程和工艺卡的严肃性
与整洁性,严禁在检测工艺规程和工艺卡 上涂抹或添加内容。
需要,可以直接采用相关行业的磁粉检测标准, 甚至可以采用国家标准、国家军用标准等。一般 应根据所检测的产品和企业的设施、人员的具体 情况编制适合自己企业的检测规程或标准。
• 磁粉检测工艺规程编制时应参考表1所列工程进
行编写。其选取原那么可参考JB/T4730.42005相关标准。
• 2.2.2工艺卡
• 2)对于受压加工部件和材料可填写“不允许存在
任何裂纹和白点〞,紧固件和轴类零件填写“不 允许任何横向缺陷显示〞。如对于Ⅲ级受压加工 部件和材料可填写“线性缺陷磁长度l≤6.0mm〞 〞圆形缺陷磁痕(评定框尺寸为2500mm2,其中 一条矩形边长最大为150mm),长径,且在评定 框内不多于4个“。
(4) 其它条件确实定:
• 根据使用电流的种类、大小,检验批量,
及检测单位实际条件确定探伤设备和器材; 并按检测和观察要求,选择磁粉(干粉或湿 粉)和磁悬液(荧光磁粉或非荧光磁粉)。对 形状复杂或有要求的制件,应采用辅助磁 化的工装。对采用半自动化检查的设备, 应检查确定整个检测系统的适用性。对检 测场地、观察环境都应满足检测要求。
磁粉检验工艺规程

磁粉检测工艺规程JHD/GC03-2011编制:审核:批准:山东宏达科技集团有限公司一、目的用于规范被检产品磁粉探伤操作,确保探伤过程和结果符合相关国家标准和行业标准的要求。
二、引用标准RCCM-MC5000RCCM-MC8000三、适用范围本工艺适用于用RCCM-MC5000中规定的连续法技术对被检工件的焊缝进行的磁粉检验。
四、探伤人员、探伤设备及系统要求1、人员要求磁粉检验应有按MC8000的规定取得资格证书的人员进行。
2、检测设备及器材2.1 磁粉检验设备的选择2.1.1 根据被检工件的形状特点,预测可能出现的缺陷的特点选择磁化装置。
2.1.2 磁粉检验设备一般有通电磁化装置、通磁磁化装置和固定式磁粉检验装置。
2.1.3 装置的校验或标定2.1.3.1 磁化装置的校验磁化装置,尤其是电流表,应按书面文件规定的要求,每6个月校验一次。
2.1.3.2测量装置的标定测量装置(照度计、辐射计、磁场指示器)应按书面文件规定的要求,每12个月标定一次。
3. 探伤前工件表面的准备3.1 按《无损检测控制程序》的规定进行表面检验前的确认与委托,被检区域和检验范围,按ACCM-MC5142要求确定。
3.2 被检件表面应干净,受检区域及附近不小于25mm宽度范围内应清洁干燥,无油脂、涂料、铁锈、氧化皮及其它妨碍缺陷显示的各种覆盖物。
在正常光照检验和磁化前,可以在工件表面喷施极细的亮光颜色涂料或涂层以增加对比度。
3.3 表面处理方法以钢丝刷、砂轮、或纱布打磨,有机溶剂清洗为宜。
4. 磁粉探伤工艺4.1. 磁化方法的选择根据被检件的几何形状、质量、状态和钢种及假设的不连续缺陷的取向和深度等,选择磁化方法。
当检验材料裂纹的情况下,只能采用通磁磁化法。
4.2.根据被检件施工的实际情况,推荐使用羊角式电磁轭和交叉式电磁轭,且必须满足MC-5000的要求,通交流电应能提升4.5Kg的铁磁体;通直流电、且磁极间距为最大时,可以提升18Kg的铁磁体。
焊缝的磁粉检测技术

1.3 磁粉检测的优缺点
1.3.1 磁粉检测的优点 (1) 能直观的显示出缺陷的位置、形状和大小; (2) 可检测出铁磁性材料表面和近表面的缺陷; (3) 检测速度快、工艺简单、成本低、污染少; (4) 灵敏度高,可检测微米级宽的缺陷。 1.3.2 磁粉检测的缺点 (1) 不能检测非铁磁性材料; (2) 不能检测埋藏较深的缺陷; (3) 不容易发现与工件表面夹角极小的缺陷; (4) 直接通电法和触头法因为易产生电弧烧伤工件 而不适用于对表面质量要求较高的工件进行检测; (5) 不能通过对磁痕的分析直接判断缺陷本身的深
141 141
Mining & Processing Equipment
第 35 卷 2007 年第 10 期 缺陷,检测效率很低,因此磁轭法尤其是便携式磁轭 在现场检测时一般只是作为一种辅助磁粉检测方法。
焊缝的磁粉检测技术
2.2 磁化电流的选择
为了在工件上产生磁场而采用的电流称为磁化电 流。磁粉检测采用的磁化电流有交流电、整流电 (单相 半波整流电、单相全波整流电、三相半波整流电和三 相全波整流电)、直流电和冲击电流。其中最常用的磁 化电流有交流电、单相半波整流电和三相全波整流 电,它们在磁粉检测时具有不同特点,应根据不同情 况进行选取。 用交流电磁化时,由于交流电具有趋肤效应,对 于表面微小缺陷检测灵敏度高,但当缺陷在工件表面 2 mm 以下时一般无法检测。由于交流电在生产和生活 中使用最为广泛,在现场易于找到交流电源,因此在 压力容器检验时常用交流电作为磁化电流。另外,用 交流电不但易于退磁,而且两次磁化的工序间可以不 退磁。 整流电能检测近表面较深的缺陷 (最深可达 4 mm),同时因为其含有交流成分,因此对表面缺陷也 有较高的检测灵敏度。在条件具备的情况下应尽量采 用整流电。 直流电可检测到的缺陷深度最大,可检测出 6 mm 深的缺陷,但几乎检测不到表面缺陷,因此有很大的 局限性。
磁粉检测工艺规程(ASME)
Magnetic Particle Examination Procedure 磁粉检测工艺规程CERTIFICATION演示证实声明This is certified that this procedure has been demonstrated to the satisfaction of the Authorized Inspector in accordance with the requirements of T-150 of Section V.本规程已按ASME规范第Ⅴ卷T-150的要求,在带缺陷试板上进行了演示。
演示结果得到了AI的认可。
Certified by DateⅢ级证明人:日期:Satisfied by Date授权检验师:日期:1 Scope范围1.1 This procedure is applied to the magnetic particle examination of ferromagnetic materials and welds for ASME Code Items.本规程适用于ASME规范产品铁磁性材料和焊缝的磁粉检验。
1.2 The magnetic particle examination method is suitable for detecting cracks and other discontinuities on or near the surface in ferromagnetic materials. Shapes or sizes to be examined and extent of the examination shall be in accordance with the reference requirement detailed in the approved drawings 磁粉探伤方法适用于检测铁磁性材料表面或近表面裂纹及其它不连续性。
磁粉工艺规程
1、适用范围1.1 本规程按NB/T47013-2015的要求编写,适用于阀门上的原材料、零部件和焊接接头表面、近表面缺陷的检测;对于Ⅰ、Ⅱ类焊缝进行100%磁粉检测,对Ⅲ类焊缝不要求作磁粉检验,但当外观检验有怀疑时,应补充进行磁粉检验。
1.2 公司一般采用磁轭式磁粉探伤仪进行磁粉检测。
1.3 本规程适用于非荧光和荧光湿磁粉的连续磁化法。
公司一般采用非荧光磁粉检测。
2、引用标准、法规NB/T47013-2015 《承压设备无损检测》GB11533-1989 《标准对数视力表》JB/T6003-1992 《磁粉探伤用磁粉》JB/T6005-2004 《无损检测磁粉检测用试片》JB/T8290-1998 《磁粉探伤机》3、检测人员3.1 检测人员必须经过培训取得国家有关部门颁布的,并与其工作相适应的资格证书。
3.2 检测人员每年应检查一次身体,未经矫正或矫正的近(距)视力和远(距)视力应不低于5.0,不得有色盲。
4、设备、工具和材料磁粉探伤设备必须符合JB/T8290的规定。
4.1 磁化设备及校验4.1.1 磁化设备采用磁轭式的磁粉探伤机,可以是使用交流电的,也可以使用直流电的。
4.1.2 提升力的校验,至少每年或损坏后修复时校验一次,长期停用首次使用前也应校验,应使用磁轭最大间距时,交流至少用45N的提升力;直流至少应有177N的提升力。
4.1.3 紫外线灯:当采用荧光法检测时,所使用的紫外线灯在工作表面的紫外线强度应不低于1000μW/㎝2,紫外线的波长应在320nm~400nm范围内。
4.2 灵敏度试片4.2.1 A型灵敏度试片用于被检测工件表面有效磁场强度和方向、有效检测区以1-30/100型标准试片,适及磁化方法是否正确的测定,公司磁粉检测一般选用A1用于连续磁化法。
4.2.2 灵敏度试片的使用将试片无人工缺陷的面朝上,使试片与被检面接触良好,必要时可用透明胶带将其整体贴在被检面上,但人工缺陷处不得贴覆,试验时边磁化边施加磁悬液,以人工缺陷清晰显示来确定磁化规范。
磁粉检测工艺规程
1. 适用范围1.1本规程适用于铁磁性材料制成的承压设备原材料、零部件和焊接对接接头、T 型接头和角接接头表面、近表面缺陷的检测和缺陷等级评定。
不适用于非铁磁性材料的检测。
1.2本规程规定了在磁粉检测过程中,为获得正确的检测结果所必须遵循的程序和要求。
工件质量验收等级应按设计技术条件和有关施工规范确定,并应符合图样规定。
1.3磁粉检测的一般要求还应符合NB/T47013.1及NB/T47013.4的有关规定。
2. 引用标准、法规NB/T4730.1-2015 《承压设备无损检测》第一部分:通用要求NB/T4730.4-2015 《承压设备无损检测》第四部分:磁粉检测TSG Z8001-2013 特种设备无损检测人员资格考核与监督管理规则GB/T 11533 标准对数视力表GB/T 23907 无损检测磁粉检测用试片TSG G0001-2012 锅炉安全技术监察规程GB/T 16507-2013 锅壳锅炉GB/T 16508-2013 水管锅炉TSG 21-2016 固定式压力容器安全技术监察规程TSG D0001-2009《压力管道安全技术监察规程》3.名词术语3.1 公称厚度:检测对象名义厚度,不考虑材料制造偏差或加工减薄。
3.2 相关显示:磁粉检测时由缺陷产生的漏磁场吸附磁粉而形成的磁痕显示,一般也称为缺陷显示。
3.3 非相关显示:磁粉检测时由截面变化或材料磁导率改变等产生的漏磁场吸附磁粉而形成的磁痕显示。
3.4 伪显示:不是由漏场吸附磁粉形成的磁痕显示。
3.5 纵、横向缺陷:缺陷磁痕长轴与工件(轴类或管类)轴线或母线的夹角大于或等于30°时,按横向缺陷处理;其他按纵向缺陷处理。
4.检测人员资格4.1检测人员应按照TSG Z8001-2013《特种设备无损检测人员考核规则》进行考核,取得MT资格证书,方能承担检测工作,无证人员只可在持证人员的指导下从事辅助工作。
不同技术等级人员,只能从事与该等级相应的无损检测工作,并负相应的技术责任。
磁粉检测通用工艺规程
1总则本规程规定了磁粉检测的人员、设备检测方法及缺陷的评定。
适用于本单位对铁磁性材料和焊接接头近表面和表面缺陷采用非荧光湿式磁粉连续磁化法的检测及评定。
2 引用标准GB150 压力容器GB151 管壳式换热器JB/T4730—2005 承压设备无损检测JB/T6065 磁粉检测用试片JB/T6063 磁粉探伤用磁粉技术条件TSG R0004-2009 固定式压力容器安全技术监察规程3 检测人员3.1 检测人员必须经过培训,并取得相应的资格。
3.2 检测人员未经矫正或矫正视力应不低于5.0,并每年检查一次。
3.3 检测人员不得有色盲。
4 磁粉检测设备及器材4.1 磁粉检测设备4.1.1 本单位设备及性能见表14.1.2 电磁扼的提升力每半年校验一次。
在磁扼损伤修复后应重新校验。
4.2 磁粉检测用标准试片4.2.1 磁粉检测标准试片有A1型和C型,主要用于检验磁粉检测设备、磁粉和磁悬液的综合性能,了解被检工件表面有效磁场强度和方向、有效检测区及磁化方法是否正确。
4.2.2 磁粉检测时一般应选用A1—30/100型标准试片,当检测坡口等狭小部位,A1试片使用不便时,一般选用C—15/50型标准试片。
具体见表2。
表2 标准试片的类型、规格和图形4.2.3 连续法检测时将试片无人工缺陷的面朝外。
为了使试片与被检面接触良好,可用透明胶带将试片平整的粘贴在被检面上,胶带不能覆盖试片上人工缺陷。
4.2.4 试片表面有锈蚀、摺折或磁特性发生改变时不得继续使用。
4.3 磁粉(磁膏)和磁悬液4.3.1 一般用磁膏配制磁悬液(磁悬液浓度见表3),磁膏选用上海宏达。
4.3.2 磁悬液一般用水做载液,将磁膏均匀挤出100mm左右,加入1L水搅拌均匀即达到10-25g/L的要求。
表3 磁悬液浓度磁粉类型配制浓度,g/L 沉淀浓度(含固体量),ml/100ml非荧光磁粉10~25 1.2~2.4荧光磁粉0.5~3.0 0.1~0.44.4 其他器材4.4.1 反差增强剂在检测较粗糙的表面时采用,一般为购买成品。
- 1、下载文档前请自行甄别文档内容的完整性,平台不提供额外的编辑、内容补充、找答案等附加服务。
- 2、"仅部分预览"的文档,不可在线预览部分如存在完整性等问题,可反馈申请退款(可完整预览的文档不适用该条件!)。
- 3、如文档侵犯您的权益,请联系客服反馈,我们会尽快为您处理(人工客服工作时间:9:00-18:30)。
焊缝磁粉检测工艺规程
一、适用范围
1.1该工艺规程适用于图号A、B、C、D类焊缝(包括热影响区)以及向外宽展至少25mm范围内的表面及近表面缺欠的磁粉检测技术及验收等级。
1.2 本工艺规程适用于非荧光湿磁粉的连续法磁化技术。
检测工艺卡内容是本工艺规程的补充(由II级探伤资格人员按本工艺规程等要求编写),其参数规定的更具体。
二、引用标准和法规
本工艺规程按JB/T4730.5-2005和所给图纸技术要求(图号)编写,要求焊缝检验等级为级,其合格级别为级。
其他引用标准如下:
GB/T9445—2008 无损检测人员资格鉴定与认证
JB/T6061—2007 无损检测焊缝磁粉检测
JB/T6063 无损检测磁粉检测用材料
JB/T6065 无损检测磁粉检测用试片
JB/T5097—2005 无损检测渗透检测和磁粉检测观察条件
JB/T8290 无损检测磁粉探伤机
三、人员资格
3.1焊缝的磁粉检测及最终验收结果的评定由具有中国无损检测学会(执行GB/T9445-2008/ISO9712-2005)相应方法和工业门类的II级资格的磁粉检测资格人员来完成。
焊缝的磁粉检测的评定报告的审核和批准有Ⅲ级(相应方法和工业门类)资格的磁粉检测资格人员来完成。
3.2 从事焊缝的磁粉检测人员,应具有一定的金属材料、热处理和焊接方面基础知识和焊缝磁粉检测经验。
3.3 检测人员未经矫正或经矫正的近(距)视力和远(距)视力应不低于5.0(小数记录值1.0),每年应检查一次,不得有色盲。
四、设备、器材、材料和辅助材料
磁粉检测设备应符合JB/T8290的规定。
磁粉粒度和性能的其他要求应符合JB/T6063的规定。
至少半年校验一次,在磁轭损伤修复后应重新校验。
当使用磁轭最大间距时,交流电磁轭至少应有45N的提升力。
4.3试片
-30/100, C-15/50型标准试片。
磁粉检测时一般应选用A
1
4.4 磁悬液
使用中日合资美柯达探伤器材(苏州-上海)有限公司生产的黑水悬浮液(类型:
MT—BW)。
磁悬液的浓度的测定采用磁悬液的浓度测定管进行。
一般浓度应控制在10-25g/L的范围内或按制造厂的推荐。
4.5反差剂
使用使用中日合资美柯达探伤器材(苏州-上海)有限公司生产的FA-5型号的反差剂。
五、被探工件表面制备要求
被检表面应无氧化皮、油脂、焊缝飞溅、表面沟槽、污物等任何能影响检测灵敏度的污物。
必要时,可用砂纸或局部打磨来改善表面状况,以便准备解释显示。
任何清理或表面准备都不应影响磁粉显示的形成。
六、探伤时机
焊接接头的磁粉应在焊后进行;有延迟裂纹倾向的材料,应在焊后至少24小时后进行。
七、检测工艺和检测技术
7.1预处理
预处理的清除和打磨见上第五节。
在工件表面先喷涂上一层薄而均匀反差增强剂,干燥后再磁化工件焊缝.
7.2磁化技术
采用连续磁化方法。
在通电磁化的同时,施加磁悬液,持续磁化时间为1-3秒,停施磁悬液至少1秒后才可停止磁化。
为保证磁化效果应至少反复磁化二次,7.3磁化方向
7.3.1采用纵向磁化(磁轭法)被检工件的每一被检区至少进行两次独立的检测,两次检测的磁力线方向应大致相互垂直。
7.3.2焊缝检测时,宜使用相同的磁化方向及磁场覆盖。
被检材料中电流路径的宽度应大于或等于焊缝及热影响区要加上50mm,且在任何情况下焊缝及热影响区应处于有效区域内,应规定相对于焊缝方位的确切方向,磁化区域每次应有不少于15mm的重叠。
磁轭的磁极间距应控制在75mm~200mm之间。
7.4检测介质的施加
采用黑水磁悬液,应确认整个检测面被磁悬液湿润后,磁悬液的施加可采用喷方法。
同时不应使检测面上磁悬液的流速过快。
7.5综合性能测试
采用试片时系统灵敏度进行综合性能测试。
7.5.1试片的选用:对接接头选用A型试片;T型接头或角焊缝选用C型
7.5.2将试片向人工槽的一面与工件被检表面贴实(间隙小于0.1mm),用粘胶纸贴住试片四角。
7.5.3对试片及其相贴实的被检工件表面按本规程进行磁粉检测,对试片施加磁粉检测时,采用连续法。
7.5.4根据试片上人工槽的显示状况与程度,来评定所验证的磁粉检测综合性(系统灵敏度)是否符合要求。
若试片上的人工缺陷能清晰显示,则符合,否则不符合。
7.6缺陷磁痕的观察
7.6.1观察条件按JB/T5097
7.6.2缺陷磁痕的观察应在磁痕形成后立即进行。
7.6.3缺陷磁痕的评定应在可见光下进行,工件被检处可见光照度应不小于1000lx。
7.6.4当辩认细小磁痕时,应用2-10倍放大镜进行观察。
7.6.5显示的记录
缺陷磁痕的显示记录采用数码照片方式记录,应把钢皮尺放在缺陷磁痕旁边一起照相,同时用草图标注。
7.7退磁:
本图纸要求磁粉检测的焊缝一般不要求做退磁处理,若要求作金属加工工艺其退磁的剩磁H≤0.3Mt(240A/m)。
八、缺陷评定和质量分级
8.1磁痕显示分为相关显示、非相关显示和伪显示。
8.2伪显示:凡怀疑存在掩盖时,宜修整检测表面或使用替代的检测方法。
8.3长宽比大于3的缺陷磁痕,按条状磁痕处理;长宽比小于等于3的缺陷磁痕,按圆形磁痕处理。
8.4缺陷磁痕的长轴方向与工件轴线或母线的夹角大于等于30度时,作为横向缺陷处理,其他按纵向处理。
8.5两条或两条以上缺陷磁痕在同一直线上且间距小于等于2mm时,按一条磁痕处理,其长度为两条缺陷磁痕之和加间距。
8.6长度小于0.5mm的磁痕不计。
8.7 磁粉检测质量分级按JB/T4730.4-2005表6.
8.8综合评级
在圆形缺陷评定区内同时存在多种缺陷时,应进行综合评级。
对各类缺陷分别评定级别,取质量级别最低的级别作为综合评级的级别;当各类缺陷的级别相同时,则降低一级作为综合评级的级别。
九、对超标缺陷的处理
9.1 不可接受的显示的缺陷必须清除。
9.2 检测人员必须在焊缝上标记需清除缺陷的数量、位置和长度。
9.3可通过定点打磨或电弧气刨方法把缺陷清除干净,检测确认没有缺陷后,再进行补焊。
9.4 补焊时可采用控制电流和局部加热等方法,以免产生新的焊接缺陷。
9.5 对于裂纹类缺陷,也可在焊缝上打止裂孔来控制补焊引起的裂纹扩展。
9.6 补焊完成目视检验合格后,应对修补区域使用相同磁粉系统和技术重新检测和评定。
十、检测报告
10.1应出具检测报告,至少应包括:
a)委托单位;
b)被检工件:名称、编号、规格、材质、坡口型式、焊接方法和热处理状况; c)检测设备: 名称、型号;
d)检测规范:磁化方法及磁粉规范、磁粉种类及磁悬液浓度和施加磁粉的方法,
检测灵敏度校验及标准试片;
e)磁痕记录及工件草图(或示意图);
f)检测结果及质量分级、检测标准名称和验收等级;
g)检测人员、审核人员、批准人员相应的资格和签名;
h)检测日期。
10.2.资料保存
10.2.1磁粉检测记录
磁粉检测现场原始记录及检测位置图由Ⅱ级检测人员按规定填写并签字认可。
10.2.2磁粉检测报告
磁粉检测报告应准确、完整,并经Ⅱ级以上审核、批准签字认可。
10.2.3磁粉检测报告及其他检测资料(现场原始记录及检测位置图)一起交档案室存档,保存时间不少于7年,7年后,若用户需要可转交用户保管。
编制(资格):审核(资格):批准(资格):
日期日期日期。