模具各阶段要求
模具质量控制要点

模具质量控制要点引言概述:模具在工业生产中起着至关重要的作用,对于产品的质量和生产效率有着直接的影响。
为了确保模具的质量,需要进行有效的质量控制。
本文将从五个大点出发,详细阐述模具质量控制的要点。
正文内容:1. 模具设计阶段的质量控制要点1.1 模具结构设计:模具结构的合理性直接关系到模具的使用寿命和生产效率。
要点包括:合理的结构布局、适当的材料选择、充分考虑模具的易制造性等。
1.2 模具尺寸设计:模具尺寸的准确性对于产品的精度和一致性至关重要。
要点包括:合理的尺寸公差设定、考虑材料的收缩率和变形等因素、使用先进的设计软件进行模拟分析等。
1.3 模具表面处理:模具表面的处理对于产品的外观和质量有着直接的影响。
要点包括:选择合适的表面处理方法、考虑模具表面的耐磨性和耐腐蚀性、保证表面的光洁度和平整度等。
2. 模具加工制造阶段的质量控制要点2.1 材料采购和检验:模具的质量直接关系到材料的质量。
要点包括:选择合适的材料供应商、进行材料的化学成分和力学性能检验、保证材料的一致性和可靠性等。
2.2 加工设备和工艺控制:模具的加工质量与加工设备和工艺密切相关。
要点包括:选择先进的加工设备、制定合理的加工工艺流程、加强工艺控制和监测等。
2.3 模具装配和调试:模具的装配和调试对于模具的使用效果和寿命有着重要影响。
要点包括:严格按照装配图纸进行装配、进行合理的调试和测试、保证模具的运行稳定性和可靠性等。
3. 模具使用阶段的质量控制要点3.1 模具保养和维护:模具的保养和维护对于延长模具的使用寿命和保证产品质量至关重要。
要点包括:定期进行模具的清洁和润滑、进行模具的磨损检查和更换、及时处理模具的故障和问题等。
3.2 模具使用环境控制:模具的使用环境对于模具的稳定性和寿命有着直接影响。
要点包括:控制模具的使用温度和湿度、避免模具受到腐蚀和污染、保证模具的使用环境清洁和干燥等。
3.3 模具使用记录和反馈:模具的使用记录和反馈对于改进模具设计和加工工艺有着重要意义。
模具的生产流程

模具的生产流程
模具生产是工业制造中重要的环节之一,它主要涉及到从设计到
制造再到加工、修理、改造等方面的各个环节。
以下是模具的生产流程:
1、设计阶段:模具的制作始于设计,制作模具的设计师必须详细
地了解产品的使用要求、尺寸、形状等。
在设计过程中需要进行设计
评估,有利于确定所选的材料、加工技术和成型工艺等。
2、材料选择:在材料选择过程中,设计师必须考虑到模具材料的
机械性能、成本、精度等因素。
一般情况下,模具材料要求坚硬而不
易变形。
3、制造模具:制造模具的技术水平决定了模具的质量和精度,因此,制造模具的工作人员必须具备一定的专业知识。
4、加工模具:加工模具是需要反复校验和测试的,主要包括开槽、打孔、切割、抛光、磨削和刻蚀等。
在这个环节中,需要使用一些高
精度机床和其他装备,以确保各个部件的精度和质量。
5、测试和修理:在测试阶段,需要对模具进行加工测试,以检查
模具的质量和精度。
如果出现问题,需要对模具进行修理或修改。
6、维护和修理:模具在使用过程中会出现损坏、磨损、老化等
问题,需要及时进行维护和修理。
总之,模具生产是一个复杂的过程,需要多方面的专业技术和精湛的技艺。
只有经过严格的设计、制造、修理和维护,才能够确保模具的质量和使用寿命。
模具生产过程的六个阶段
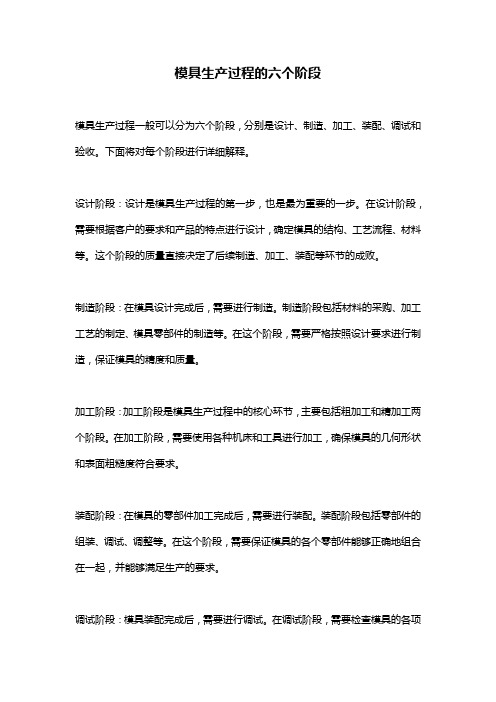
模具生产过程的六个阶段
模具生产过程一般可以分为六个阶段,分别是设计、制造、加工、装配、调试和验收。
下面将对每个阶段进行详细解释。
设计阶段:设计是模具生产过程的第一步,也是最为重要的一步。
在设计阶段,需要根据客户的要求和产品的特点进行设计,确定模具的结构、工艺流程、材料等。
这个阶段的质量直接决定了后续制造、加工、装配等环节的成败。
制造阶段:在模具设计完成后,需要进行制造。
制造阶段包括材料的采购、加工工艺的制定、模具零部件的制造等。
在这个阶段,需要严格按照设计要求进行制造,保证模具的精度和质量。
加工阶段:加工阶段是模具生产过程中的核心环节,主要包括粗加工和精加工两个阶段。
在加工阶段,需要使用各种机床和工具进行加工,确保模具的几何形状和表面粗糙度符合要求。
装配阶段:在模具的零部件加工完成后,需要进行装配。
装配阶段包括零部件的组装、调试、调整等。
在这个阶段,需要保证模具的各个零部件能够正确地组合在一起,并能够满足生产的要求。
调试阶段:模具装配完成后,需要进行调试。
在调试阶段,需要检查模具的各项
功能,如开合力、抽芯、顶出等,确保模具可以满足生产的要求。
验收阶段:模具生产过程的最后一个阶段是验收。
在验收阶段,需要对模具进行全面的检查和测试,确保模具的各项指标符合要求,同时还要进行生产试验,验证模具的适用性和可靠性。
只有通过了验收,才能向客户交付模具。
模具质量控制要点

模具质量控制要点引言概述:模具是创造工业中的关键设备,对于产品的质量和生产效率具有重要影响。
因此,模具质量控制是创造企业必须重视的问题。
本文将从五个方面介绍模具质量控制的要点。
一、设计阶段的质量控制要点:1.1 确定模具的使用环境和工作条件,包括温度、压力、材料等因素,以便确定模具的材料选择和结构设计。
1.2 采用CAD/CAM技术进行模具设计和分析,确保模具的结构合理、功能完善,并能满足产品的要求。
1.3 进行模具的可靠性分析和寿命预测,以提前发现潜在的问题并采取相应的措施。
二、加工创造阶段的质量控制要点:2.1 选择优质的模具材料,并进行严格的质量检测,确保材料的性能符合要求。
2.2 采用先进的加工设备和工艺,保证模具的加工精度和表面质量。
2.3 进行模具的装配和调试,确保模具的各个部件能够正常工作,同时进行必要的试模和调整。
三、使用阶段的质量控制要点:3.1 定期对模具进行维护和保养,包括清洁、润滑、紧固等,以延长模具的使用寿命。
3.2 定期对模具进行检测和测试,包括尺寸测量、性能测试等,以及时发现和修复模具的问题。
3.3 建立模具使用档案,记录模具的使用情况、维修情况等,以便进行后续的分析和改进。
四、质量控制的关键要点:4.1 引入先进的质量管理体系,如ISO9001等,建立完善的质量控制流程和标准。
4.2 建立模具质量控制的指标体系,包括尺寸精度、表面质量、使用寿命等指标,并进行定期的评估和改进。
4.3 加强对模具质量的监控和追溯,及时发现和处理质量问题,避免扩大化。
五、持续改进的质量控制要点:5.1 建立模具质量改进的机制和团队,定期进行质量分析和评估,找出问题的根本原因,并采取相应的改进措施。
5.2 加强与供应商的合作,确保模具材料和零部件的质量可控。
5.3 建立模具质量培训计划,提高员工的技术水平和质量意识,为模具质量控制提供坚实的基础。
总结:模具质量控制是创造企业必须重视的问题,本文从设计阶段、加工创造阶段、使用阶段、质量控制的关键要点以及持续改进的要点五个方面介绍了模具质量控制的要点。
模具的生产过程包括五个阶段

模具的生产过程包括五个阶段模具是现代工业制造中必不可少的重要部件,它可以用于制造各种金属或非金属零部件。
模具的生产过程可以分为五个阶段,包括设计、制造、检测、使用和维护。
一、设计阶段在模具的生产过程中,设计阶段是极为关键的一环。
设计师需要充分了解客户的需求和要求,明确模具的用途和制造条件。
随之设计师需要根据产品的形状、尺寸和材质等方面因素进行合理的设计。
在设计过程中,设计师需要采用专业的设计软件,模拟制作过程,进行虚拟试验。
只有通过科学的设计,才能为后面的制造打下坚实的基础。
二、制造阶段在确认了模具的设计方案之后,制造阶段便开始了。
在制造过程中,需要进行材料的选择和加工。
不同类型的模具材料有不同的特点,需要根据设计师的要求进行选择。
一般来说,模具材料应该具有高强度、高硬度、耐磨、耐热、耐腐蚀等特点。
加工过程中,需要采用各种先进的工艺设备,如电火花机、钻床、铣床等。
此外,制造人员需要严格按照设计要求进行制造,保证最终的制品具有高精度和高质量。
三、检测阶段在制造完成之后,需要进行模具的检测。
在检测过程中,需要采用各种测量仪器和检测设备,如三坐标测量机、显微镜、硬度计等。
通过对模具的精度、形状、尺寸等方面进行检测,确定制品是否合格。
只有合格的模具才能进行下一步的使用。
四、使用阶段模具的使用一般需要进行大量的生产实践。
制造人员需要进行必要的调试,使其性能达到最优状态。
同时,在实际使用中,需要根据生产规模和模具的磨损情况等因素进行必要的调整和维护,以延长其使用寿命。
五、维护阶段模具使用过程中,需要进行必要的保养和维护。
在使用模具之前,需要进行必要的清洁和检查。
如发现模具有磨损和损坏现象,需要及时进行维修或更换。
此外,在不使用模具之前,需要妥善存放,避免存放在潮湿、高温、阳光直接照射或易受冲击的地方。
总结:以上就是模具的生产过程中的五个阶段,每一个阶段都十分关键。
其中,设计阶段是决定模具质量的关键一环。
制造阶段是将设计制品变成现实制品的重要过程。
模具设计的标准

模具设计的标准1. 引言模具设计在工业制造中起着至关重要的作用,它们被广泛应用于金属加工、塑料注塑、汽车制造以及电子设备等领域。
一个优质的模具设计对于产品质量和生产效率有着重要的影响。
因此,制定模具设计的标准是必要的,可以确保设计师们具备相同的设计要求和目标。
2. 模具设计的基本原则模具设计的标准旨在优化设计过程、提高生产效率、确保模具质量和保证产品规格的一致性。
以下是模具设计的基本原则:2.1 简化设计模具设计应该尽量简化模具的结构和零件数量,以减少制造成本和加工时间。
简化的设计可以降低模具的重量,提高使用寿命,并且方便清洁和维护。
2.2 提高精度和可靠性模具应该具备高精度的加工能力,以确保产品的质量和准确性。
此外,模具设计还应考虑到材料的可靠性和耐用性,以便长时间使用而不损坏。
2.3 考虑制造和加工要求模具设计应充分考虑制造和加工过程中的要求,例如模具的可加工性、装配性和调试性等。
合理的设计可以减少制造过程中的错误和延误。
3. 模具设计的标准要素为了确保模具设计的一致性和可比性,以下标准要素应该包括在模具设计中:3.1 尺寸和公差模具设计中应明确规定产品的尺寸和公差要求。
尺寸和公差的标准化可以确保不同批次生产的产品具有相同的质量和功能。
3.2 材料选择在模具设计中,应根据产品的特性和使用环境选择合适的材料。
考虑因素包括高温、高压、腐蚀性和耐磨性等要求。
3.3 模具标准件模具设计中应尽量使用标准件,以减少设计和制造的复杂性。
标准件的使用可以降低制造成本和提高模具的可维护性。
3.4 塑料模具特殊要求在塑料模具设计中,考虑到流道设计、冷却系统、顶针和脱模机构等特殊要求。
这些要求对产品质量和生产效率的影响非常重要。
4. 模具设计的流程为了确保模具设计的一致性和规范性,一个典型的模具设计流程应包括以下步骤:4.1 分析和定义在模具设计之前,应进行产品的分析和定义。
了解产品的功能、样式和尺寸要求是设计一个合适的模具的基础。
汽车零件模具质量控制要点

汽车零件模具质量控制要点在汽车零件制造过程中,模具好坏直接决定零件质量情况,如何提高模具的质量,最重要的是确定模具的质量控制点,通过质量控制点控制的控制,能够将模具零件控制在一个较好的水平,下面是一些经常会涉及到的汽车零件模具质量控制要点:1. 模具设计阶段1.1 材料选择在模具设计阶段,选择适当的材料是确保模具质量的关键。
以下是一些材料选择的要点:- 材料强度:模具需要具备足够的强度和刚度,以承受高压和高温的作用。
因此,在选择材料时,需要考虑其强度和刚度特性,以确保模具在使用过程中不会变形或损坏。
- 耐磨性:模具在使用过程中会与工件接触,因此需要具备良好的耐磨性能。
选择具有良好耐磨性的材料可以延长模具的使用寿命,并减少维修和更换的次数。
- 耐腐蚀性:某些工件的加工过程中会产生腐蚀性介质,因此模具材料需要具备良好的耐腐蚀性。
选择耐腐蚀性较好的材料可以防止模具表面的腐蚀和损坏。
- 加工性能:模具的制造过程需要进行切削、冲压、铣削等加工操作,因此选择具有良好加工性能的材料可以提高制造效率和降低制造成本。
- 成本:材料的选择还需要考虑成本因素。
一方面,材料成本应该合理,以控制制造成本;另一方面,考虑到模具的使用寿命和维护成本,选择质量较好的材料也是非常重要的。
综上所述,模具设计阶段的材料选择是确保模具质量的重要环节。
需要综合考虑材料的强度、耐磨性、耐腐蚀性、加工性能和成本等因素,以选择合适的材料,从而保证模具的质量和使用寿命。
1.2 结构设计在模具设计的结构设计阶段,需要考虑以下几个要点:1. 模具结构的合理性:模具的结构设计应该符合零件的形状和尺寸要求,能够保证零件的加工精度和质量。
同时,模具的结构应该尽量简单,易于加工和维修。
2. 模具的刚度和稳定性:模具在加工过程中需要承受较大的压力和振动,因此模具的结构应具有足够的刚度和稳定性,以避免变形和振动对零件加工质量的影响。
3. 模具的导向和定位:模具的导向和定位是保证零件加工精度的重要因素。
模具管理办法:模具生命周期管理

模具管理办法模具生命周期管理1. 引言在制造业中,模具是非常重要的生产工具,直接影响产品的质量和生产效率。
模具的管理对于企业的发展具有重要意义。
本文将介绍模具管理办法中的一个关键方面,即模具生命周期管理。
通过合理的模具生命周期管理,企业能够最大程度地延长模具的寿命,提高生产效率,降低生产成本。
2. 模具生命周期管理的定义模具生命周期管理是指从模具的引进、设计、制造、使用到报废的全过程进行规划、组织、控制和监督的管理活动。
模具生命周期管理的目标是确保模具在整个生命周期内能够以最佳状态进行工作,并提高模具的使用寿命和生产效率。
3. 模具生命周期管理的主要内容3.1 模具的选型和引进在模具生命周期的第一阶段,企业需要根据产品的特点和需求进行模具的选型和引进。
合理的选型可以保证模具能够满足产品的要求,并降低制造成本。
同时,引进过程中需要与模具供应商进行充分的沟通和交流,确保模具的质量和交货时间符合要求。
3.2 模具的设计和制造模具的设计和制造是模具生命周期的关键环节。
在设计阶段,需要充分考虑产品的特点和生产工艺,确保模具的结构和尺寸满足要求。
在制造过程中,需要严格控制材料的选择和加工工艺,确保模具的质量和精度。
同时,还需要对模具进行试模,以验证模具的性能和稳定性。
3.3 模具的使用和维护模具的使用和维护是模具生命周期管理的重要环节。
在使用过程中,需要注意合理安排生产计划,避免过度使用和疲劳损坏。
同时,还要定期进行模具的保养和维护,包括清洁、润滑和检修等工作,以保证模具的正常工作和延长使用寿命。
3.4 模具的修复和改造随着模具的使用,可能会出现磨损、断裂或其他故障。
在这种情况下,需要及时进行模具的修复和改造。
修复工作包括修复模具的表面,修复模具的结构和尺寸等。
改造工作包括对模具进行功能的改进和升级,以适应产品的变化和生产工艺的改变。
3.5 模具的报废和淘汰当模具的使用寿命达到一定阶段或发生严重故障时,就需要对模具进行报废和淘汰。
- 1、下载文档前请自行甄别文档内容的完整性,平台不提供额外的编辑、内容补充、找答案等附加服务。
- 2、"仅部分预览"的文档,不可在线预览部分如存在完整性等问题,可反馈申请退款(可完整预览的文档不适用该条件!)。
- 3、如文档侵犯您的权益,请联系客服反馈,我们会尽快为您处理(人工客服工作时间:9:00-18:30)。
恒 邦 模 具 制 品 厂
产品与模具各阶段要求
T1阶段(模具) 1、 第一次试模省模要求:所有能看到的位置,不能有刀纹(火花纹可接受);表面光洁度需省到统一。
2、 其它类试模省模要求:PA 、POM 胶件如涉及到外形的,按硬胶料标准省模,只涉及到装配的,只要能出模即可,可不省模。
3、 透明类产品要求:达到透明要求。
4、 直径小于2mm 及长度超过200mm 的顶针或司筒要做托针。
5、有关模具的制做要求:按《模具质量对照手册》当中的第7、10、11、12、13、15、1
6、19、22、23、24、25、26、28、29、30、31、33、34、35、36、3
7、3
8、3
9、41、42、44、45、47、48、52、53、54、55、56、58、60、62、63、67、68、70、71、72、78、80、81、82、83、84、86要求做。
6、 第一次试模时应做斜边,如果没有做应由工模部主管及工程部主管签名确认才可以试模。
(应留意放行的次数)
7、 工模部在试模时应将模具清洗干净才可以试模。
8、 啤机组在试模后应要用纸板粘走水板给有关部门。
(啤机组T1~TN 都需要粘走水板) T2阶段模具
12、省模要求:所有能看到的位置省400#砂纸以上,后模省顺到出模,如涉及到外表及表面能看到 的地方,则省到与前模一致(注意:不能有火花纹)。
13、有关模具的制做要求:按《模具质量对照手册》当中的第43、61、64、65、66、73、85要求 做。
TN 阶段(模具)
1、 TN 板要求:前模省800#砂纸,如产品面积较大,则需省1000#砂纸;后模省顺到出模(省400#砂纸)。
2、 流道要省320#油石。
3、 有关模具的制做要求:按《模具质量对照手册》当中的第1、2、3、
4、
5、
6、8、14、1
7、1
8、20、46、4
9、50、51、57、77、79、81、要求做。
~ ~ ~ 完 ~ ~ ~
编写人:
审核人:
版本:00。