模具开发技术要求
模具的技术要求

装配过程中零件不允许磕、碰、划伤和锈蚀。
螺钉、螺栓和螺母紧固时,严禁打击或使用不合适的旋具和扳手。紧固后螺钉槽、螺母和螺钉、螺栓头部不得损坏。
规定拧紧力矩要求的紧固件,必须采用力矩扳手,并按规定的拧紧力矩紧固。
同一零件用多件螺钉(螺栓)紧固时,各螺钉(螺栓)需交叉、对称、逐步、均匀拧紧。
补焊前必须将缺陷彻底清除,坡口面应修的平整圆滑,不得有尖角存在。
根据铸钢件缺陷情况,对补焊区缺陷可采用铲挖、磨削,炭弧气刨、气割或机械加工等方法清除。
补焊区及坡口周围20mm以内的粘砂、油、水、锈等脏物必须彻底清理。
在补焊的全过程中,铸钢件预热区的温度不得低于350°C。
在条件允许的情况下,尽可能在水平位置施焊。
补焊时,焊条不应做过大的横向摆动。
铸钢件表面堆焊接时,焊道间的重叠量不得小于焊道宽度的1/3。
10.锻件要求:
每个钢锭的水口、冒口应有足够的切除量,一以保证锻件无缩孔和严重的偏折。
锻件应在有足够能力的锻压机上锻造成形,以保证锻件内部充分锻透。
锻件不允许有肉眼可见的裂纹、折叠和其他影响使用的外观缺陷。局部缺陷可以清除,但清理深度不得超过加工余量的75%,锻件非加工表面上的缺陷应清理干净并圆滑过渡。
轴承外圈与开式轴承座及轴承盖的半圆孔不准有卡住现象。
轴承外圈与开式轴承座及轴承盖的半圆孔应接触良好,用涂色检查时,与轴承座在对称于中心线120°、与轴承盖在对称于中心线90°的范围内应均匀接触。在上述范围内用塞尺检查时,0.03mm的塞尺不得塞入外圈宽度的1/3。
轴承外圈装配后与定位端轴承盖端面应接触均匀。
模具技术要求
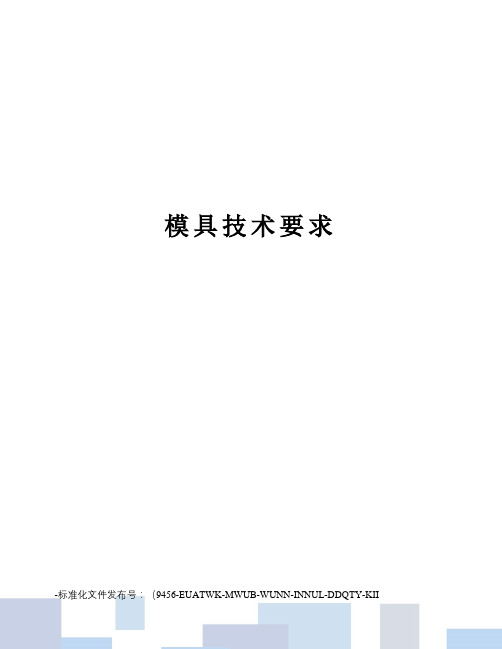
模具技术要求-标准化文件发布号:(9456-EUATWK-MWUB-WUNN-INNUL-DDQTY-KII模具技术要求一.模具材料及热处理要求1.拉延、成形类模具外板件拉延序凸模、凹模及压边圈使用GGG70L铸铁,淬火硬度HRC50-55;内板件凸模、凹摸及压边圈使用MoCr铸铁,淬火硬度HRC50-55。
特殊情况下须渗氮或TD处理(模具图纸会签时确认)。
变形剧烈及高强度钢板(抗拉强度≥350MPa)的制件应采用整体镶Cr12MoV;淬火硬度要达到HRC58—62。
基体采用HT300。
采用键槽与螺栓链接。
GGG70L铸件厂:天津虹岗或长城精工或经甲方认可的同等铸造品质铸造厂。
2.冲裁类模具普通板料零件料厚小于或等于1.2mm的刃口镶块可采用空冷钢(7CrSiMnMoV 或ICD-5),淬火硬度HRC55-60;料厚大于1.2mm的采用Cr12MoV材料,淬火硬度为HRC58~62。
料厚大于等于1.4mm的镶块采用波浪刃口。
高强度板的制件采用Cr12MoV材料,淬火硬度为HRC58~62。
所有凹模镶块、废料刀均采用背托,凹模采用镶块结构,凸模可采用整体结构。
模具基体采用HT300。
3.翻边、整形类模具中大型模具凹模镶块原则上应采用侧面固定式以便于调整;小型模具可采用整体式结构,料厚大于1.4mm的凹模采用镶块式。
零件料厚小于或等于1.2mm,材料可选用MoCr/7CrSiMnMoV;零件料厚大于1.2mm 的采用Cr12MoV或与之相当的材料(应取得甲方工艺认可,具体以会签为准)。
普通板料的制件凸模可采用合金铸铁,表面淬火硬度不低于HRC50;高强度板的制件采用Cr12MoV材料,淬火硬度为HRC58-62;如采用分体或镶块式基座(底板)可采用HT300的材料。
对于部分易拉毛部位,必要时需进行TD处理。
4.压料(退料)顶出器可采用铸造结构,但应根据其强度要求,决定用铸铁或球铁或铸钢材料(工艺会签时,甲方根据具体结构决定)。
模具技术要求
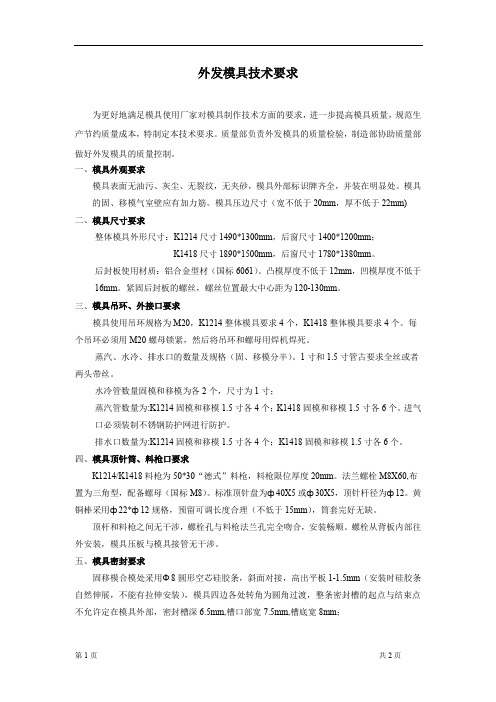
外发模具技术要求为更好地满足模具使用厂家对模具制作技术方面的要求,进一步提高模具质量,规范生产节约质量成本,特制定本技术要求。
质量部负责外发模具的质量检验,制造部协助质量部做好外发模具的质量控制。
一、模具外观要求模具表面无油污、灰尘、无裂纹,无夹砂,模具外部标识牌齐全,并装在明显处。
模具的固、移模气室壁应有加力筋。
模具压边尺寸(宽不低于20mm,厚不低于22mm) 二、模具尺寸要求整体模具外形尺寸:K1214尺寸1490*1300mm,后窗尺寸1400*1200mm;K1418尺寸1890*1500mm,后窗尺寸1780*1380mm。
后封板使用材质:铝合金型材(国标6061)。
凸模厚度不低于12mm,凹模厚度不低于16mm。
紧固后封板的螺丝,螺丝位置最大中心距为120-130mm。
三、模具吊环、外接口要求模具使用吊环规格为M20,K1214整体模具要求4个,K1418整体模具要求4个。
每个吊环必须用M20螺母锁紧,然后将吊环和螺母用焊机焊死。
蒸汽、水冷、排水口的数量及规格(固、移模分半)。
1寸和1.5寸管古要求全丝或者两头带丝。
水冷管数量固模和移模为各2个,尺寸为1寸;蒸汽管数量为:K1214固模和移模1.5寸各4个;K1418固模和移模1.5寸各6个。
进气口必须装制不锈钢防护网进行防护。
排水口数量为:K1214固模和移模1.5寸各4个;K1418固模和移模1.5寸各6个。
四、模具顶针筒、料枪口要求K1214/K1418料枪为50*30“德式”料枪,料枪限位厚度20mm。
法兰螺栓M8X60,布置为三角型,配备螺母(国标M8)。
标准顶针盘为ф40X5或ф30X5,顶针杆径为ф12。
黄铜棒采用ф22*ф12规格,预留可调长度合理(不低于15mm),筒套完好无缺。
顶杆和料枪之间无干涉,螺栓孔与料枪法兰孔完全吻合,安装畅顺。
螺栓从背板内部往外安装,模具压板与模具接管无干涉。
五、模具密封要求固移模合模处采用Φ8圆形空芯硅胶条,斜面对接,高出平板1-1.5mm(安装时硅胶条自然伸展,不能有拉伸安装),模具四边各处转角为圆角过渡,整条密封槽的起点与结束点不允许定在模具外部,密封槽深6.5mm,槽口部宽7.5mm,槽底宽8mm;六、模具其他要求1、后档板:K1214模具后挡板数量不少于三处,K1418不少于4处,避让宽度不小于80mm。
模具技术要求
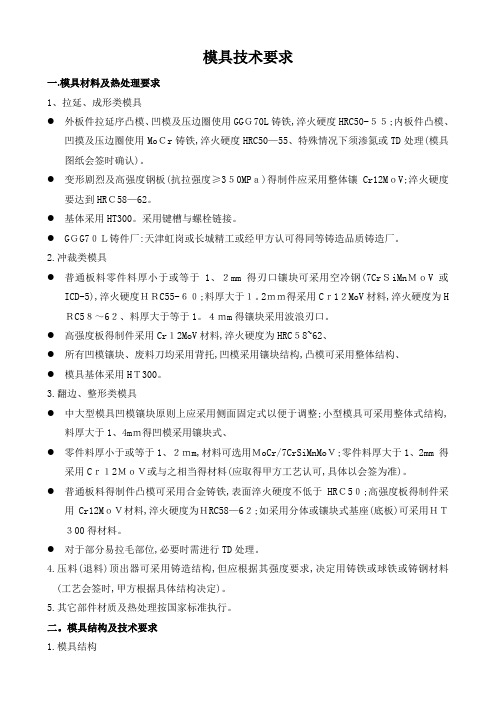
模具技术要求一.模具材料及热处理要求1、拉延、成形类模具●外板件拉延序凸模、凹模及压边圈使用GGG70L铸铁,淬火硬度HRC50-55;内板件凸模、凹摸及压边圈使用MoCr铸铁,淬火硬度HRC50—55、特殊情况下须渗氮或TD处理(模具图纸会签时确认)。
●变形剧烈及高强度钢板(抗拉强度≥350MPa)得制件应采用整体镶Cr12MoV;淬火硬度要达到HRC58—62。
●基体采用HT300。
采用键槽与螺栓链接。
●GGG70L铸件厂:天津虹岗或长城精工或经甲方认可得同等铸造品质铸造厂。
2.冲裁类模具●普通板料零件料厚小于或等于1、2mm得刃口镶块可采用空冷钢(7CrSiMnMoV 或ICD-5),淬火硬度HRC55-60;料厚大于1。
2mm得采用Cr12MoV材料,淬火硬度为H RC58~62、料厚大于等于1。
4mm得镶块采用波浪刃口。
●高强度板得制件采用Cr12MoV材料,淬火硬度为HRC58~62、●所有凹模镶块、废料刀均采用背托,凹模采用镶块结构,凸模可采用整体结构、●模具基体采用HT300。
3.翻边、整形类模具●中大型模具凹模镶块原则上应采用侧面固定式以便于调整;小型模具可采用整体式结构,料厚大于1、4mm得凹模采用镶块式、●零件料厚小于或等于1、2mm,材料可选用MoCr/7CrSiMnMoV;零件料厚大于1、2mm 得采用Cr12MoV或与之相当得材料(应取得甲方工艺认可,具体以会签为准)。
●普通板料得制件凸模可采用合金铸铁,表面淬火硬度不低于HRC50;高强度板得制件采用Cr12MoV材料,淬火硬度为HRC58—62;如采用分体或镶块式基座(底板)可采用HT300得材料。
●对于部分易拉毛部位,必要时需进行TD处理。
4.压料(退料)顶出器可采用铸造结构,但应根据其强度要求,决定用铸铁或球铁或铸钢材料(工艺会签时,甲方根据具体结构决定)。
5.其它部件材质及热处理按国家标准执行。
二。
模具结构及技术要求1.模具结构1、1模具结构采用单动式,原则上按甲方认可得乙方提供得结构式样(模具需满足自动化线要求)。
模具设计的几个要求

模具设计的几个要求第一篇:模具设计的几个要求青岛海培德模具加工厂模具设计的几个要求1.冲压工艺性分析冲压工艺性是指零件冲压加工的难易程度。
在技术方面,主要分析该零件的形状特点、尺寸大小(最小孔边距、孔径、材料厚度、最大外形)、精度要求和材料性能等因素是否符合冲压工艺的要求。
如果发现冲压工艺性差,则需要对冲压件产品提出修改意见,经产品设计者同意后方可修改。
.搜集必要的资料设计冷冲模时,需搜集的资料包括产品图、样品、设计任务书和参考图等,并相应了解如下问题:)了解最大限度采用标准件的可能性,以缩短模具制造周期。
)了解制件的生产性质是试制还是批量或大量生产,以确定模具的结构性质。
)了解适用的压力机情况和有关技术规格,根据所选用的设备确定与之相适应的模具及有关参数,如模架大小、模柄尺寸、模具闭合高度和送料机构等。
)了解提供的产品视图是否完备,技术要求是否明确,有无特殊要求的地方。
5)了解模具制造的技术力量、设备条件和加工技巧,为确定模具结构提供依据。
)了解制件的材料性质(软、硬还是半硬)、尺寸和供应方式(如条料、卷料还是废料利用等),以便确定冲裁的合理间隙及冲压的送料方法。
.确定合理的冲压工艺方案确定方法如下:)最后从产品质量、生产效率、设备占用情况、模具制造的难易程度、模具寿命、工艺成本、操作方便和安全程度等方面进行综合分析、比较,在满足冲件质量要求的前提下,确定适合具体生产条件的最经济合理的冲压工艺方案,并填写冲压工艺过程卡片(内容包括工序名称、工序数目、工序草图(半成品形状和尺寸)、所用模具、所选设备、工序检验要求、板料规格和性能、毛坯形状和尺寸等):;)根据工艺计算,确定工序数目,如拉深次数等。
)根据各工序的变形特点、尺寸要求确定工序排列的顺序,例如,是先冲孔后弯曲还是先4)根据生产批量和条件,确定工序的组合,如复合冲压工序、连续冲压工序等。
)根据工件的形状、尺寸精度、表面质量要求进行工艺分析,确定基本工序的性质,即落料、冲孔、弯曲等基本工序。
模具技术要求及验收标准
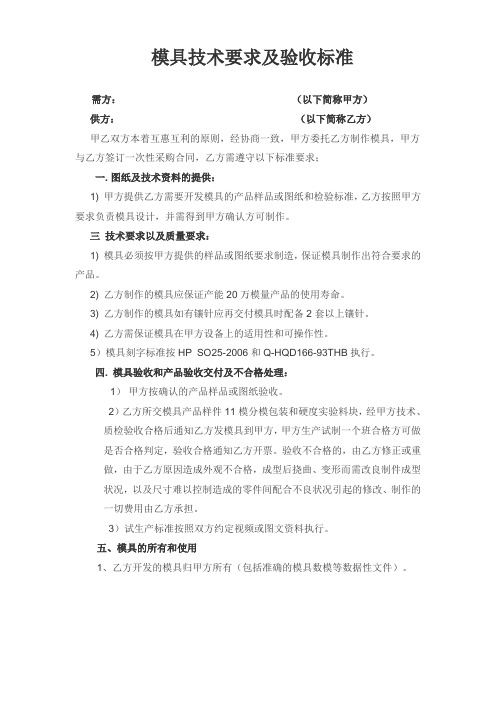
模具技术要求及验收标准
需方:(以下简称甲方)
供方:(以下简称乙方)
甲乙双方本着互惠互利的原则,经协商一致,甲方委托乙方制作模具,甲方与乙方签订一次性采购合同,乙方需遵守以下标准要求;
一. 图纸及技术资料的提供:
1) 甲方提供乙方需要开发模具的产品样品或图纸和检验标准,乙方按照甲方要求负责模具设计,并需得到甲方确认方可制作。
三技术要求以及质量要求:
1) 模具必须按甲方提供的样品或图纸要求制造,保证模具制作出符合要求的产品。
2) 乙方制作的模具应保证产能20万模量产品的使用寿命。
3) 乙方制作的模具如有镶针应再交付模具时配备2套以上镶针。
4) 乙方需保证模具在甲方设备上的适用性和可操作性。
5)模具刻字标准按HP SO25-2006和Q-HQD166-93THB执行。
四. 模具验收和产品验收交付及不合格处理:
1)甲方按确认的产品样品或图纸验收。
2)乙方所交模具产品样件11模分模包装和硬度实验料块,经甲方技术、质检验收合格后通知乙方发模具到甲方,甲方生产试制一个班合格方可做是否合格判定,验收合格通知乙方开票。
验收不合格的,由乙方修正或重做,由于乙方原因造成外观不合格,成型后挠曲、变形而需改良制件成型状况,以及尺寸难以控制造成的零件间配合不良状况引起的修改、制作的一切费用由乙方承担。
3)试生产标准按照双方约定视频或图文资料执行。
五、模具的所有和使用
1、乙方开发的模具归甲方所有(包括准确的模具数模等数据性文件)。
模具开发技术要求
模具技术要求1.1 模具总体要求1.1.1 模具寿命:模具使用寿命不少于30万冲次。
(在正常使用和定期维护保养前提下以 5000 冲次为不修模的期限)。
1.1.2 各个阶段的冲压件尺寸合格率:开发阶段OTS1 OTS2 PPV PP SOP 备注关键尺寸合格率100% 100% 100% 100% 100%全尺寸合格率85% 90% 95% 100% 100%1.2 设计制造要求1.2.1 在模具从设计到验收的过程中,应以零件为单位建立模具档案,至少包括但不局限于以下内容:缺陷风险分析记录、模具设计会签记录、会议纪要、更改记录、模具制造计划以及实际进度记录、试模记录、模具铸件质保书、冲压零件检测记录、模具刃口材料及硬度、模具焊接图、模具检查记录等。
1.2.2 模具所使用的材料及其加工、供货、调试和移交须符合订货技术要求,以及国家现行的模具技术标准和规范,劳动安全保护,环保及公认的常识性机械、模具知识及买方的相关规定。
1.2.3 预验收保证零件(拉延的凹模、凸模、压边圈,成型块、切刀等)技术工艺可靠并且无堆焊。
模具卖方因零件修改或模具缺陷而进行的堆焊(包括使用的电焊条)须经过买方认可。
买方决定是否允许堆焊,以何种方式堆焊。
1.2.4 起重装置:对于大型模具(模具长度大于等于1800mm),采用插销式吊耳(PIN TYPE HOOK),插销式吊耳应配有自锁功能起重棒。
每套模具配起重棒4根;对于中小型模具(模具长度小于1800mm),采用4根铸入式起重棒;考虑到模具的叠放,吊耳、起重棒要满足承受两倍模具自重的要求。
1.2.5 在设计上必须考虑铸造工艺性、加工工艺性和维修方便性。
模具铸件本体为实型铸造(特别说明,铸造实型要求为整体数控铣,必须选择密度较大的泡沫,数控完成后必须手工打磨表面平整,不允许出现泡沫颗粒,保证铸件外观质量,手工粘贴泡沫模型时,同样保证铸件的外观质量)。
所有铸件必须经过退火处理,不允许有疏松,气孔,夹渣等等铸造缺陷,外表清砂良好。
模具工程师岗位职责、要求以及未来可以发展的方向
模具工程师岗位职责、要求以及未来可以发展的方
向
模具工程师是指从事模具设计、制造和管理工作的专业人才,
其主要职责包括:制定模具设计和加工方案、协助生产车间解决加
工难题、跟进模具制造进度、对现有模具进行改进以提高生产效率等。
一名优秀的模具工程师需要具备以下要求:
1.专业技能:具备扎实的工程基础知识,掌握CAD、CAE、CAM
等相关软件技术,熟悉模具工艺流程及制造工艺。
2.沟通协调:具备良好的沟通能力和团队协作精神,能与生产
部门有效沟通,解决设计与加工中的问题。
3.质量控制:熟悉常规的质量管理体系和相关标准要求,能够
对制造过程中的质量、效率和成本做出合理的控制管理。
4.创新能力:具备敏锐的市场洞察力和提升企业竞争力的意识,能够对模具进行改进提高生产效率、降低成本等。
模具工程师未来可以发展的方向:
1.技术研发:通过开发新材料、新技术以及新工艺来提高模具
设计和制造的技术含量,打造高附加值模具。
2.技术管理:协同方案制订、质量控制、制造进度跟踪,规范
管理制度,为企业提供更好的生产效率和管理水平。
3.新产品研发:在新产品的研发中发挥重要作用,通过模具的
革新和提高模具的精度就可以提高产品的精度和效率。
4.工程管理:管理整个制造流程,包括设计、生产、组装、实
验等,并建立一套完整的管理体系,将整个生产过程集中管理,不
断优化生产效率。
综上所述,模具工程师的职责涵盖了制定模具设计方案到协助生产车间解决加工难题的全过程。
在未来,模具工程师可以通过技术研发、技术管理、新产品研发、工程管理等方面的发展,为企业提供更丰富的价值。
(701字)。
模具技术要求【范本模板】
模具技术要求一.模具材料及热处理要求1.拉延、成形类模具●外板件拉延序凸模、凹模及压边圈使用GGG70L铸铁,淬火硬度HRC50—55;内板件凸模、凹摸及压边圈使用MoCr铸铁,淬火硬度HRC50-55.特殊情况下须渗氮或TD处理(模具图纸会签时确认).●变形剧烈及高强度钢板(抗拉强度≥350MPa)的制件应采用整体镶Cr12MoV;淬火硬度要达到HRC58—62。
●基体采用HT300。
采用键槽与螺栓链接。
●GGG70L铸件厂:天津虹岗或长城精工或经甲方认可的同等铸造品质铸造厂。
2.冲裁类模具●普通板料零件料厚小于或等于1。
2mm的刃口镶块可采用空冷钢(7CrSiMnMoV 或ICD-5),淬火硬度HRC55—60;料厚大于1.2mm的采用Cr12MoV材料,淬火硬度为HRC58~62。
料厚大于等于1。
4mm的镶块采用波浪刃口。
●高强度板的制件采用Cr12MoV材料,淬火硬度为HRC58~62。
●所有凹模镶块、废料刀均采用背托,凹模采用镶块结构,凸模可采用整体结构。
●模具基体采用HT300.3.翻边、整形类模具●中大型模具凹模镶块原则上应采用侧面固定式以便于调整;小型模具可采用整体式结构,料厚大于1.4mm的凹模采用镶块式。
●零件料厚小于或等于1.2mm,材料可选用MoCr/7CrSiMnMoV;零件料厚大于1.2mm 的采用Cr12MoV或与之相当的材料(应取得甲方工艺认可,具体以会签为准)。
●普通板料的制件凸模可采用合金铸铁,表面淬火硬度不低于HRC50;高强度板的制件采用Cr12MoV材料,淬火硬度为HRC58—62;如采用分体或镶块式基座(底板)可采用HT300的材料。
●对于部分易拉毛部位,必要时需进行TD处理。
4.压料(退料)顶出器可采用铸造结构,但应根据其强度要求,决定用铸铁或球铁或铸钢材料(工艺会签时,甲方根据具体结构决定)。
5.其它部件材质及热处理按国家标准执行。
二.模具结构及技术要求1.模具结构1。
模具设计技术要求
模具设计技术要求
以下是 6 条模具设计技术要求及例子:
1. 模具的精度那可是超级重要的呀!就好比建房子,根基不稳怎么行呢?想象一下,要是模具精度不够,生产出来的东西尺寸都不对,那不是浪费大家的时间和精力嘛!比如说制造一个手机壳的模具,如果精度出问题,那生产出来的手机壳还怎么能完美贴合手机呢?我们可得把精度牢牢把控住呀!
2. 模具的材料选择可不能马虎哟!这就跟选食材做饭一样,得挑好的呀!要是选个差劲的材料,它能经得住反复使用吗?就像做蛋糕的模具,要是材料不好,用几次就变形了,那不是糟糕透顶啦!所以咱得精心挑选合适的材料,确保它耐用又可靠呀!
3. 模具的结构设计得合理呀!这可关系到整个生产过程顺不顺畅哦!它就像一部机器的运转系统,不合理的话不就卡壳啦?比如说设计一个汽车零部件的模具,结构不合理,脱模都困难,还怎么高效生产呢?咱们得好好琢磨琢磨这结构设计呢!
4. 模具的冷却系统也是关键呀!这就像人在大热天需要降温一样。
没有好的冷却系统,生产速度能快得起来吗?好比注塑模具,冷却不行的话,成型时间长,效率多低呀!我们一定得重视这个冷却系统呀,让它发挥最大作用!
5. 模具的维护保养可不能忘啊!这就像爱护自己的宝贝一样。
不保养它,它能一直好用吗?你想啊,一个长期不保养的模具,各种问题都会冒出来,那不是给自己找麻烦嘛!所以呀,要定期给模具做个检查、保养护理啥的,让它一直健健康康的呀!
6. 模具的设计创新多重要呀!这就像给自己的生活加点新花样一样。
一直守着老一套,能有进步吗?看看人家那些厉害的模具设计,多么有创意呀!咱也不能落后呀,要大胆去尝试新的设计思路,说不定就能做出让人惊艳的模具呢!
总之,模具设计技术要求可多了去了,每一条都得认真对待,这样才能做出好的模具,生产出高质量的产品呀!。
- 1、下载文档前请自行甄别文档内容的完整性,平台不提供额外的编辑、内容补充、找答案等附加服务。
- 2、"仅部分预览"的文档,不可在线预览部分如存在完整性等问题,可反馈申请退款(可完整预览的文档不适用该条件!)。
- 3、如文档侵犯您的权益,请联系客服反馈,我们会尽快为您处理(人工客服工作时间:9:00-18:30)。
模具开发技术要求1 方案、图纸确认要求1.1 模具制造厂家在收到我司确认的产品三维图(小型1天、中型2 天、大型3 天)内将分型线、结构简图等技术问题与我司确认。
模具制造厂家的模具结构图纸在设计完成后应提交我司确认,特别是浇口设置、分型面设置等影响到外观质量的设计,以及镶拼方法、结构运动等重要问题,必须在我司认可后执行;模具制造厂家在模具加工过程中发现结构出现问题,需及时通知我司,新的结构必须在得到我司确认后实施;否则出现的问题由模具制造厂家负责。
1.2 模具制造厂家在模具加工过程中,如果出现质量事故,应及时向我司通报,同时模具的修补方案应得到我司的认可,并更改模具结构图纸;如需烧焊修补,模具修补区域、烧焊工艺必须得到我司项目工程师的书面确认,并在图纸上明确标明实际烧焊区域以及影响区域;1.3模具分型面上必须设计合理的排气槽。
模具分型面设计应合理,并且保证足够的强度。
定模固定板与注射机固定板间要增加隔热板,防止定模固定板和注射机固定板扩大,导致拉杆错位使模具咬死。
电器盒安装在模具顶部,冷却系统接头设计在模具底部,排水槽出口在分流板安装板底部。
2 模具材质要求2.1 模具成型零件材质要求。
具体材料由模具制造厂家按照我司指定品牌自行采购;2.2 模具制造厂家提供模具使用钢材的材质报告,并保证钢材质量,如在模具规定寿命期限内因钢材质量问题而引起的模具故障,模具制造厂家应承揽由此而造成的一切我司损失,并应立即按我司要求修复模具或更换模具;3 模具各个系统要求3.1 浇注系统要求3.1.1 主流道均采用浇口套标准件,并确保与设备配套。
三板模分流道出在前模板背面的部分截面必须为梯形,主流道抛光至表面粗糙度Ra3.2 以上,三板模点浇口分流道抛光至表面粗糙度Ra1.6以上,无倒扣;3.1.2 三板模倒锥形拉料杆必须可靠固定,可以用沉头螺丝固定,也可以用压板压住,但不能在模具运输或装卸时掉出。
主流道拉料杆处,冷料穴一般为锥形,以便拉出冷料,便于取件。
3.1.3 模具料道应设计合理,冷料要易于去除,制品外观面应无浇口痕迹,浇口尺寸和浇口高度要一致,偏差不大于0.05mm,浇口无注塑缺陷(喷痕、流纹等),制品有装配处不应有残余冷料。
3.2 冷却系统的要求3.2.1 冷却水路的设计必须充分均匀,一个系统的各个浇口要有专门且条件完全相同的冷却水,一系列浇口的冷却回路不能串联使用。
模具正常生产时,必须满足合同规定的注塑生产周期要求,并且模具成型部位前后模温差要求在±5C以内;3.2.2 冷却水路必须畅通,无铁屑污物等,无漏水和渗水现象;3.2.3 所有冷却系统要求使用标准配件,如:水嘴、水管、堵头、密封圈等均采用我司指定的标准件标准设计;3.3 顶出机构要求3.3.1 所有顶杆、扁顶、推杆均选用盘起公司和三住公司标准零件供应商的产品;顶杆杯头端面齐平,无打磨痕迹,若顶杆上加倒钩,要求倒钩的方向必须保持一致或均匀并不能影响制品取出;严禁更改顶杆胚头尺寸,包括直径和厚度,推板与顶杆胚头要求互相匹配,不准加垫片;3.3.2 顶块的固定必须牢固,四周非成型部分应加工3-5度的斜度,下部周边应倒角;方顶杆必须设置油槽;复位弹簧选用指定标准件,两端不能打磨、割断,复位弹簧安装孔底面必须为平底;3.3.3 对于顶面非平面的顶杆,都应有止转定位,顶出复位顺畅、无卡滞、窜动现象。
3.3.4 顶出板复位必须到底,顶块等顶出机构与滑块等有干涉的模具应增加强制复位;3.3.5 模具液压系统驱动的顶出复位,在装配后和试模前应检查,保证动作可靠。
所有液压驱动零件必须设计行程开关控制动作。
3.4 斜顶和滑块机构的要求3.4.1 斜顶机构的运动应顺畅,无卡滞、起刺、复位不良等缺陷,斜顶的抽芯角度一般情况下不得大于15度;3.4.2 滑块抽芯一般使用斜导柱驱动,斜导柱与开模方向夹角应比滑块锁紧面与开模方向夹角小2-3度。
也可采用液压等其它可靠方式驱动;3.4.3 滑块滑动底面与模板之间、锁紧面应设计耐磨板;3.5 热流道的要求3.5.1 热流道电源线插座必须固定在定模板上。
3.5.2 热电偶的型号必须明确,并与温控表对应,热电偶布置位置合理,控温可靠,每一组加热元件都应有热电偶控制,温控表设计温度与实际显示温度误差不能大于±5℃,控温应灵敏;3.5.3 喷嘴与加热圈应紧密接触,喷嘴上下两端的避空段、封胶段、定位段尺寸符合图纸要求。
3.5.4 分流板加热器可选用加热棒、加热丝等元件。
加热棒应接触良好,加热棒与集流板应有 0.1mm的配合间隙(h7/g6),便于更换、维修; 3.5.5 模具上安装热流道走线部分的槽位必须是圆角过渡;且圆角不得小于R3,热流道接线应捆扎,用压板盖住,以免装配时压断电线,装配完成后,使用万用表进行检查,避免有接地现象;3.5.6 所有的热流道模具必须有热流道标识牌,标识牌的内容必须保证与实际接线一致;4 模具生产设备和生产效率及模具吊装的要求4.1 模具与设备的接口要求4.1.1 模具的设计必须完全适合选定的注塑机参数。
(有关注塑机参数由我司提供或模具制造厂家到我司测量)特别是顶出孔的大小及其位置确定,必须与所提供的注塑机相配;4.1.2 定位圈选用我司的标准件。
如有特别要求,请按照单套模具具体要求执行;4.1.3 顶板、底板的孔位与所提供设备相符;4.1.4 浇口套球径和入口直径应大于注塑机喷嘴球R和入口直径;4.2 模具的吊装要求4.2.1 模具配件不能影响模具的吊装和存放,如安装时下方有外漏的油缸、预复位机构等,应有支撑腿保护,支撑腿应高于模具配件;如安装时上方有外漏的油缸、预复位机构等,可以更改吊环孔位置,但必须保证模具吊装平衡;4.2.2 每个重量超过10KG 的模具零部件都必须有适合的吊环孔,其它零件也需有相应措施保证零部件拆卸安装方便;4.2.3 吊环必须能旋到底,吊装必须平衡,5-16T模具起吊时最大偏移量不能超过3mm,16T以上不能超过5mm;4.3 模具生产节拍的要求:满足成型机节拍要求(一个循环的时间):1800T:75秒。
5 模具外观与模具标识以及模具使用寿命要求5.1 所有的模具型腔数量超过一个以上者必须有型腔标记;型腔标记必须清楚,表面不得产生缩水等缺陷;5.2 所有模具的水路、油路必须有进出标识;水的进出标记为“IN”“OUT”油的进出标识为“OIN”“OOUT”;5.3 在正常情况下,模具的使用寿命要求不得低于30万次。
6 模具备件和技术资料要求6.1 模具备件要求6.1.1 在买方终验收合格之日起,在质保期内,卖方按技术协议规定的生产节拍为买方连续正常生产免费提供备品、备件及服务。
6.1.2 质保期满后,卖方承诺持续不断的为买方提供优惠价格的备件及技术支援。
保证模具交付一年内(或正常生产2万件以上)的备品、备件提供和一年内的免费模具维修(供方模具本身问题),如需方使用不当造成模具损坏,供方有义务协助需方进行维修。
6.1.4 所提供的模具备件应随模具运输至我司指定的地点,备件清单应传真我司技术开发部。
6.1.5 热流道系统、液压系统应根据合同要求或单套模具要求提供相应部件的备件及所购标准件的供货商名称、联系方式和产品详细型号等;6.2 技术资料要求6.2.1 模具交付时,模具制造厂家向我司提供全套最终版本的模具技术资料:1)、模具的3D、2D数据 1套 光盘形式2)、完整的模具图纸 3套3)、模具标准件资料 1套4)、模具使用说明书 1套5)、全部模具的易损件、备品、备件清单 1套备注:完整的模具图纸包含模具明细表、装配图、动模图、定模图、重要零件图、水路循环图、热流道图。
6.2.2 模具使用的工艺参数。
7 模具验收标准7.1 模具出厂检验要求7.1.1 模具制造厂家应按照合同规定时间首试,模具首试后,模具制造厂家应将样品连同样品尺寸和外观自检单及注塑工艺记录表一起送我司检验并装配验证;7.1.2 模具出厂前,模具制造厂家应按本技术协议和合同要求对模具进行自检,自检合格后填写由我司提供的自检表。
我司将按此对模具进行检验,如有不实,模具制造厂家应承担相应的处罚。
此项作为中期款付款依据;7.1.3 模具在最终交付我司前应进行试模验证,对在试模中出现的问题及时进行调整,模具交到我司后不允许出现制品难成型、制品取件困难以及使用脱模剂等严重缺陷;7.2 验收分为两部分:塑料件验收和模具验收7.2.1 塑料件的外观和尺寸必须完全符合图纸要求和装配要求,达到我司质检部门的验收标准;7.2.2 模具的验收以“技术要求和合同为准,必须全部符合要求,模具制造厂家在模具交付时,需提供模具自检报告,模具运到塑料公司进行全面检验包括试模和验证。
7.2.3 如我司检验结果与模具制造厂家自检不符,模具制造厂家应承担相应违约责任。
如模具不符合以上技术要求,存在严重缺陷,模具制造厂家除按合同要求重新开模外,还应按合同要求承担违约责任7.2.4 模具制造厂家制作的模具在我司工厂,在正常工艺下生产三轮,每轮连续生产500件模具无故障和零件合格率、外观合格率、涂装合格率、尺寸合格率必须达到招标文件中所规定的质量目标,且效率符合我司要求,模具方可验收。
8 外观要求8.1 模具外表面需涂银灰色防锈漆、在操作面要用印有明显黄色字体的模具名称。
同时在操作面的右下角要镶有名牌。
名牌要有如下内容:1)模具名称和型号2)模具制造厂家3)模具制造厂家地址4)模具生产制造日期5)模具型腔、型芯材料及生产厂家6)模架、热流道等主要件生产制造单位。