大气渗碳与真空渗碳变形量的比较
主轴整体渗碳淬火后的变形量-概述说明以及解释

主轴整体渗碳淬火后的变形量-概述说明以及解释1.引言1.1 概述概述部分的内容如下:概述主轴整体渗碳淬火是一种广泛运用于工程领域的热处理技术。
在制造领域中,主轴承担着关键的作用,因此对主轴进行热处理以提高其硬度和强度具有重要意义。
本文将重点探讨主轴整体渗碳淬火后的变形量。
研究主轴淬火后的变形量对于提高主轴零件加工精度、减小后续加工工序中的修正量以及提高整体产品质量具有重要意义。
在研究过程中,我们将首先介绍主轴整体渗碳淬火的原理,探讨渗碳淬火是如何通过物质渗透和淬火过程改善主轴的硬度和强度。
然后,我们将深入探讨主轴整体渗碳淬火后的变形机制,分析淬火过程中主轴发生形变的原因和特点。
在结论部分,我们将重点讨论影响主轴整体渗碳淬火后变形量的因素,并提出一些有效的控制变形量的方法。
通过对这些影响因素的分析和相应的控制方法,我们可以更好地掌握主轴整体渗碳淬火后的变形规律,从而提高主轴的加工精度和整体产品的质量。
本文旨在为相关研究者和工程师提供一些有益的信息和指导,以便更好地理解和应用主轴整体渗碳淬火技术。
通过深入研究和有效控制变形量,我们可以有效提高主轴的性能和使用寿命,为相关工程领域的发展做出贡献。
1.2文章结构1.2 文章结构本文将分为三个主要部分,即引言、正文和结论。
下面将详细介绍每个部分的内容:- 引言部分将提供对本文研究主题的概述,包括主轴整体渗碳淬火后的变形量。
这一部分将描述该研究领域的背景和研究意义,并引出本文的目的与内容。
- 正文部分将分为两个小节。
首先,2.1节将介绍主轴整体渗碳淬火的原理,包括渗碳和淬火过程的基本原理以及其对材料性能的影响。
其次,2.2节将深入探讨主轴整体渗碳淬火后的变形机制,分析变形的主要原因、形式和程度,并探讨不同变形机制之间的关系。
- 结论部分将总结文章的主要研究结果,并提供对主轴整体渗碳淬火后变形量的影响因素和控制方法的讨论。
在3.1节中,将列举影响主轴整体渗碳淬火后变形量的因素,并对它们的作用进行分析。
机械加工常见热处理工艺

渗碳渗碳热处理渗碳:是对金属表面处理的一种,采用渗碳的多为低碳钢或低合金钢,具体方法是将工件置入具有活性渗碳介质中,加热到900--950摄氏度的单相奥氏体区,保温足够时间后,使渗碳介质中分解出的活性碳原子渗入钢件表层,从而获得表层高碳,心部仍保持原有成分。
相似的还有低温渗氮处理。
这是金属材料常见的一种热处理工艺,它可以使渗过碳的工件表面获得很高的硬度,提高其耐磨程度。
概述渗碳(carburizing/carburization)是指使碳原子渗入到钢表面层的过程。
也是使低碳钢的工件具有高碳钢的表面层,再经过淬火和低温回火,使工件的表面层具有高硬度和耐磨性,而工件的中心部分仍然保持着低碳钢的韧性和塑性。
渗碳工件的材料一般为低碳钢或低碳合金钢(含碳量小于0.25%)。
渗碳后﹐钢件表面的化学成分可接近高碳钢。
工件渗碳后还要经过淬火﹐以得到高的表面硬度﹑高的耐磨性和疲劳强度﹐并保持心部有低碳钢淬火后的强韧性﹐使工件能承受冲击载荷。
渗碳工艺广泛用于飞机﹑汽车和拖拉机等的机械零件﹐如齿轮﹑轴﹑凸轮轴等。
渗碳工艺在中国可以上溯到2000年以前。
最早是用固体渗碳介质渗碳。
液体和气体渗碳是在20世纪出现并得到广泛应用的。
美国在20年代开始采用转筒炉进行气体渗碳。
30年代﹐连续式气体渗碳炉开始在工业上应用。
60年代高温(960~1100℃)气体渗碳得到发展。
至70年代﹐出现了真空渗碳和离子渗碳。
分类按含碳介质的不同﹐渗碳可分为气体渗碳、固体渗碳﹑液体渗碳﹑和碳氮共渗(氰化)。
气体渗碳是将工件装入密闭的渗碳炉内,通入气体渗剂(甲烷、乙烷等)或液体渗剂(煤油或苯、酒精、丙酮等),在高温下分解出活性碳原子,渗入工件表面,以获得高碳表面层的一种渗碳操作工艺。
固体渗碳是将工件和固体渗碳剂(木炭加促进剂组成)一起装在密闭的渗碳箱中,将箱放入加热炉中加热到渗碳温度,并保温一定时间,使活性碳原子渗人工件表面的一种最早的渗碳方法。
液体渗碳是利用液体介质进行渗碳,常用的液体渗碳介质有:碳化硅,―603‖渗碳剂等。
各种渗碳方法比较

A:主要反应式:2 NaCN + O2= 2 NaCNO(1)
NaCN + CO2= NaCNO + CO(2)
高温:4 NaCNO = 2 NaCNO + Na2CO3+ CO +2 N(3)
Na2CO3+ C→2CO + Na2O(5)
C、处理温度越高,处理时间越长,渗碳层厚度越大。
液体渗碳法(liquid carburizing)
1、将钢料浸入以氰化钠(NaCN)为主成分的溶融盐浴中,NaCN分解出C和N渗入钢料表层。因为同时渗碳及氰化,亦称为渗碳氮化(Carbonitriding)。
A:主要反应式:C + CO2= 2CO(CO2少许)(1)木炭表面:C + O2= CO2(2)零件表面:yFe+2CO→yFe〔C〕+CO2(3)〔C〕稱為初生碳或活性碳(nascent Carbon)
B:固態反應甚慢。加入促進劑:BaCO3,Na2CO3,LiCO3,SrCO3可促進反應。
BaCO3+ C→2CO + BaO(4)
2、处理温度约以700℃为界,此温度以下以氮化为主,渗碳为辅,700℃以上则渗碳为主,氮化为辅。
3、滲碳劑主成分:NaCN,添加NaCl、NaCO3、BaCl2(减轻NaCN氧化、挥发、劣化,BaCl2促进渗碳)
4、处理的零件200-500℃预热处理:A:减少温度降低和热应变B:蒸发附着水分,防止爆炸。
C、真空渗碳是通过渗碳时间与扩散时间配合来控制表面碳量和渗碳深度。
D、真空渗碳优点:(1)渗碳层表面碳量和渗碳深度控制简单、准确(2)渗碳效果均匀(3)可缩短作业时间(4)渗碳后零件扔保持辉面状态
各种渗层比较解读

Fe2B
或FeB+Fe2B
渗后
热处理
淬火+低温回火
无
无
淬火+回火
渗层
硬度
56~64HRC
950~1200HV
500~1000HV
58~67HRC
1300~2300HV
常用
渗剂
固:木炭,碳酸盐,粘结剂
优点
比渗氮工艺的渗层厚,可承受重载荷;工艺时间短;渗前不需要调质处理
常用固体渗剂
50%铬铁+
45%Al2O3+5%NH4Cl
常用硼砂盐浴
5%~10%钒粉+
95%~90%无水硼砂+少量中性盐
固体粉末或颗粒
40%~50%钛粉+
55%~45%Al2O3+3%NaF+2%NH4Cl
硼砂盐浴
4%~8%铌粉+
96%~92%硼砂
渗温
/℃
950~1050
900~1000
900~1000
渗氮层的机械性能比渗碳层的好;渗氮温度低,渗后不进行淬火处理,工件变形小;渗氮温度低
与渗氮相比,氮碳共渗的速度快,渗层韧性更高
与渗碳相比处理温度低,变形小,共渗层的机械性能更好
工艺时间短,渗层机械性能好
缺点
硬度和耐磨性不如渗氮层高;渗碳温度高,工件变形大;渗后往往需要淬火处理
渗氮层较薄、且脆性大,不能承受太大的接触应力和高的冲击载荷;渗氮时间长,生产率低,成本较高
8%~15%V2O5+
60%~70%Na2B4O7+1%~3%NaF+Al
常用固体粉末
第5章 模具钢料的热处理-模具表面处理技术

第二节模具表面处理工艺概述模具是现代工业之母。
随着社会经济的发展,特别是汽车、家电工业、航空航天、食品医疗等产业的迅猛发展,对模具工业提出了更高的要求。
如何提高模具的质量、使用寿命和降低生产成本,成为各模具厂及注塑厂当前迫切需要解决的问题。
模具在工作中除了要求基体具有足够高的强度和韧性的合理配合外,其表面性能对模具的工作性能和使用寿命至关重要。
这些表面性能指:耐磨损性能、耐腐蚀性能、摩擦系数、疲劳性能等。
这些性能的改善,单纯依赖基体材料的改进和提高是非常有限的,也是不经济的,而通过表面处理技术,往往可以收到事半功倍的效果;模具的表面处理技术,是通过表面涂覆、表面改性或复合处理技术,改变模具表面的形态、化学成分、组织结构和应力状态,以获得所需表面性能的系统工程。
从表面处理的方式上,又可分为:化学方法、物理方法、物理化学方法和机械方法。
在模具制造中应用较多的主要是渗氮、渗碳和硬化膜沉积。
◆提高模具的表面的硬度、耐磨性、摩擦性、脱模性、隔热性、耐腐蚀性;◆提高表面的高温抗氧化性;◆提高型腔表面抗擦伤能力、脱模能力、抗咬合等特殊性能;减少冷却液的使用;◆提高模具质量,数倍、几十倍地提高模具使用寿命。
减少停机时间;◆大幅度降低生产成本与采购成本,提高生产效率和充分发挥模具材料的潜能。
◆减少润滑剂的使用;◆涂层磨损后,还退掉涂层后,再抛光模具表面,可重新涂层。
在模具上使用的表面技术方法多达几十种,从表面处理的方式上,主要可以归纳为物理表面处理法、化学表面处理法和表面覆层处理法。
模具表面强化处理工艺主要有气体氮化法、离子氮化法、点火花表面强化法、渗硼、TD法、CVD化学气相淀积、PVD物理气相沉积、PACVD离子加强化学气相沉积、CVA铝化化学气相沉积、激光表面强化法、离子注入法、等离子喷涂法等等。
下面综述模具表面处理中常用的表面处理技术:一、物理表面处理法:表面淬火是表面热处理中最常用方法,是强化材料表面的重要手段,分高频加热表面淬火、火焰加热表面淬火、激光表面淬火。
真空渗碳技术与应用
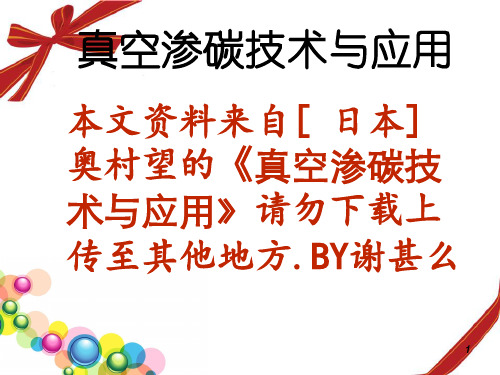
10
真空渗碳工艺
图2
11
真空渗碳工艺
高温处理缩短渗碳处理时间时, 渗碳温度范围 一般在950 - 1 050 乊间, 但是, 对于细孔内 表面渗碳及碳氮共渗, 温度最好低于900 。渗 碳气体以往采用甲烷、丙烷, 而近年来, 乙炔 、乙烯、丙烯等新型渗碳气体也开始得到应用, 在处理技术发展的同时, 传统真空渗碳存在的 碳黑问题逐步得到解决。
17
真空渗碳工艺应用注意事项
18
①弄清楚真空渗碳的应用目的 确定真空渗碳工艺的目的是通过高温下短时间处理来提 高生产率,实施细孔内的表面渗碳,减轻表面氧化、利于 环保等,根据目的加以有效应用。
②确立处理条件 目前,由于真空渗碳工艺像气体渗碳那样,根据热力学的 平衡反应控制炉内气氛是困难的,故应考虑使用设备、 渗碳用气体、处理零件等,以确立最佳的处理条件。
12
真空渗碳工艺
关于渗碳压力, 提出过各种控制方法, 渗碳压力 对真空渗碳是一个非常重要的因素。常用方法是 保持恒定压力的同时, 导入气体, 但压力和气体 流量的选择应避免发生渗碳丌均。此外, 对于细 孔内表面渗碳, 有效的渗碳法是按一定的压力引 入渗碳气体, 然后立即减压, 反复迚行这一过程。 另外, 为减少硬脆渗碳体的发生, 也采用反复迚 行渗碳、扩散的方法。
真空渗碳技术与应用
本文资料来自[ 日本] 奥村望的《真空渗碳技 术与应用》请勿下载上 传至其他地方.BY谢甚么
1
• • • •
前言 真空渗碳的特点 工艺及应用 真空渗碳工艺应用注意事项
2
前言
与历来作为渗碳处理的批量生产工艺而广泛实施的气 体渗碳工艺相比,真空渗碳工艺具有诸多优点:在生产 方面,可通过真空绝热带来高温以谋求缩短处理时间; 在产品质量方面,晶界氧化少;细孔内表面的渗碳性能 良好;另外,在环保方面,CO 2 排放量少,可间歇性处理 并可达到节能的目的等。
渗碳与渗氮,碳氮共渗处理
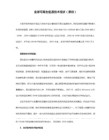
固体渗碳 ;液体渗碳 ;气体渗碳---渗碳温度为900--950C,表面层w(碳)为0.8--1.2%,层深为0.5--2.0mm。
北京基耐尔热处理工艺研究所
1. 等温淬火盐
适用于钢铁材料的150~550℃的盐浴等温淬火,盐浴分级淬火,盐浴本身的流动性好,稳定性好,均匀性好,无老化,适合于连续生产线,单槽、多槽等温淬火和回火。是取代铅浴的理想工艺。...
最后修改日期:2010-03-10
2. 盐浴渗碳
也称无毒原料液体碳氮共渗,盐浴温度在720℃左右,渗层厚度可在0.08~0.3mm方便地进行控制。淬火后,工件表面形成高硬度、高强度、高抗磨性的碳氮马氏体薄层,心部仍保持高的韧...
目前专门用于渗氮的钢种是38CrMoAlA,其中铝与氮有极大的亲和力,是形成氮化物提高渗氮层强度的主要合金元素。AlN很稳定,到约1000C的温度在钢中不发生溶解。由于铝的作用使钢具有良好的渗氮性能,此钢经过渗氮表面硬度高达1100--1200HV(相当67--72HRC)。38CrMoAlA钢脱碳倾向严重,各道工序必须留有较大的加工余量。
(2)涂料法---将锡粉、铅粉、氧化铬粉以3:1:1比例混匀,用氯化锌浴液调成稀糊状涂于零件防渗表面,或用水玻璃(质量分数为10--15%)和石墨粉(质量分数为85--90%)调成糊状涂刷后,缓慢烘干。
(3)工装法----自制专用工装,把不需渗氮的部位封闭密封。
渗氮后的零件,工作表面即能获得高硬度,一般情况下不再进行其他加工,因此常是最后一道工序(氮化后的工件至多再进行精磨或研磨加工)。可得到600--1200HV的表面硬度,耐磨性很高。这一高硬度可保持引500C(长期),甚至600C(短期),疲劳极限可提高30--300%,抗蚀性能也得到提高。
渗氮、渗碳工艺与操作过程

一渗碳工艺(气体渗碳——煤油):渗碳钢的碳含量一般在0.12%~0.25%之间,其所含主要合金元素一般是铬、锰、镍、钼、钨、钛等。
○1把炉温升到800℃左右,断开电源打开炉盖,放入装好工件的工装,关闭炉盖升温到930℃左右。
在升温过程中,打开风扇及煤油阀门,以每分钟160滴的速度滴入炉内,进行排气,同时打开试样孔和排气管并点燃排气火焰。
排气时间一般为60~80分钟(保证温度到渗碳温度还要排气30分钟左右);○2当火焰为鸡蛋黄颜色时开始强渗了,此时要加大煤油的滴量,按每分钟180~200滴。
在强渗时就可用放入试棒(含碳量少的材料,尺寸Ф8×100mm),关闭试样孔,炉压保持在6~10格——渗层深炉压取高值。
渗碳速度一般按0.15~0.2mm/h来计算,如要渗层深度为0.8~1.2mm,则强渗时间为6小时,提前在强渗设定时间结束前半小时,取出试棒,观察渗层深度(试棒渗层深度一般为工件的一半,这边渗层深度靠操作工的肉眼加经验判断),深度够在强渗结束就可以开始扩散,否则增加强渗时间;○3扩散期温度不变,减少煤油滴量,按每分钟100滴,一般扩散时间为60~90分钟,作用是均匀工件表层的碳溶度;○4扩散期结束开始降温,此时断开加热器,降温到810℃左右,并在此温度保温10~20分钟。
降温期减少煤油滴量,按每分钟60滴。
保温结束时断开加热器,关闭风扇,打开炉盖,用行车吊起工装,垂直进入温度为50~70℃的油中冷却,冷却时上下左右轻轻摇动工装,一般冷却时间为10~20分钟左右,吊起工装时也要注意工件出油的温度。
○5冷却好的工件要在半个小时之内(防止工件开裂)进行低温回火,温度一般在160~190℃(由硬度要求而定),保温时间2小时左右出炉空冷。
在渗碳过程中要随时注意火焰形状,正常的火焰是:火焰呈金黄色,无力不熄灭(断续熄灭,说明水气高了),火苗无黑焰和火星,火苗长100~150mm;若火苗出现火星,说明炉内炭黑过度;火苗过长、尖端外缘呈亮白色,说明渗碳剂供量过多;火苗短、外缘呈浅蓝色并有透明,说明渗碳剂供量不足或炉子漏气。
- 1、下载文档前请自行甄别文档内容的完整性,平台不提供额外的编辑、内容补充、找答案等附加服务。
- 2、"仅部分预览"的文档,不可在线预览部分如存在完整性等问题,可反馈申请退款(可完整预览的文档不适用该条件!)。
- 3、如文档侵犯您的权益,请联系客服反馈,我们会尽快为您处理(人工客服工作时间:9:00-18:30)。
尺寸变化的 定量表示
实际变化没有如此
极端
平均值依形状而定
大气渗碳的控制幅度大 真空渗碳的控制幅度小 真空渗碳炉运转20年后,其渗碳层深度 也不过变化0.01㎜的程度。
尺寸变化的 绝对值
大气渗碳尺 寸变化的不 规则幅度(例)
尺寸变化的中心值发生偏离,但控制幅度 小,只要在前道工序预测尺寸变化,问题比 较容易处理。
在缩小尺寸变化的控制幅度方面, 真空渗碳比较有利。
真空渗碳尺寸变化的 不规则范围小,较易 预测,且具有规律性。
需要注意,这个中心值根据形状,厚度,渗碳与大气渗碳的变形量比较
变形量
概要
向下弯曲, 向上反翘
真空渗碳
因工件装炉姿态,淬火油品种,搅拌速度等 设备技术规格而定。
大气渗碳
同左
差异
尺寸变化
工件孔直径等绝对
尺寸的变化
孔内径尺寸及内径尺寸变化的中心绝对值是
稳定的。
(依金相转变而定)
孔内径尺寸及内径尺寸变化的中心绝对 值是变化的。
当渗碳硬化层较浅时,大气渗碳很难控 制渗碳及尺寸变化不规则的精度。