乙炔真空渗碳的现状
真空渗碳技术国内外发展现状

真空渗碳技术国内外发展现状真空渗碳技术数十年的发展受到了热处理领域的广泛重视,取得了一系列进展。
1 国外研究现状法国ECM公司的分级气淬(Stop GQ)技术,在180~200℃之间等温停留工件自回火,可节省回火工序;低压真空碳氮共渗,加热温度在800~900℃之间,处理后工件表面含碳量和含氮量分别约为0.6%~0.8%和0.15%~0.30%,渗层深度在0.25~0.50mm范围,所用气体为氨气和乙炔。
日本Inata采用乙炔为富化气,在汽车零部件、机械和模具等工件上实现真空高浓度渗碳,其优点主要在于在渗碳层上析出尺寸细小的球状碳化物,进而提高工件综合性能;在温度范围为1000~1050℃下对不锈钢进行真空渗碳,工件表面可获得较高的硬度从而提高其耐磨性,此外真空渗碳还用于先进材料的热处理,比如航空航天材料,要求在300~500℃或者更高温度能保持其力学性能。
波兰的Piotr Kula等通过对厚度为0.45mm的工业纯铁进行低压真空碳氮共渗处理,结果表明在温度高于700℃时添加氨气导致加热室内造成碳的沉积,为达到在高温真空渗碳过程中易于控制奥氏体晶粒长大添加氨气应在550~700℃之间进行。
波兰的Emilia Wolowiec等通过对18CrNi8钢真空渗碳过程中“渗碳/扩散”周期的数量和时间上进行优化发现在不考虑渗碳温度的情况下,两段式(1个渗碳阶段+1个扩散阶段)真空渗碳会导致真空渗碳处理过程时间增长,工艺总时间和渗碳的效率取决于在扩散阶段18CrNi8钢表面获得的瞬时最低碳浓度值。
2 国内研究现状北京南口机车车辆机械厂樊玉福等人通过对27SiMnMoV钢制针阀体在型号为PFV500×600的真空渗碳炉经真空渗碳、气淬、冷处理和回火后进行研究,发现尽管针阀体存在近似盲孔结构但经真空渗碳处理后渗碳层性能良好且变形量较小。
北京航空材料研究院孙枫等人为解决Cr17Ni2不锈钢因存在钝化膜和渗碳温度高等难题,通过研究淬火温度不同和冰冷处理工艺不同对Cr17Ni2不锈钢真空渗碳后心部金相组织和硬度后发现表面硬度≥750HV10,渗层深度在0.5mm时为Cr17Ni2不锈钢理想的显微组织和硬度,其微观组织为弥散且尺寸较小的分布于马氏体中的碳化物和δ铁素体组成。
热处理技术发展和前景发展趋势(最新整理)
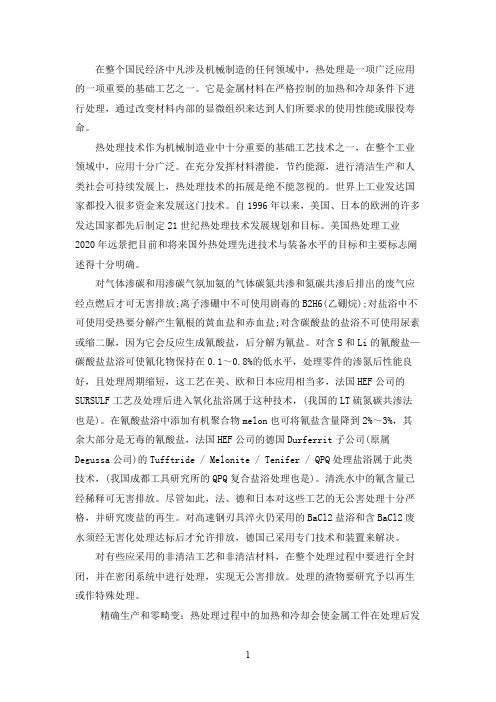
在整个国民经济中凡涉及机械制造的任何领域中,热处理是一项广泛应用的一项重要的基础工艺之一。
它是金属材料在严格控制的加热和冷却条件下进行处理,通过改变材料内部的显微组织来达到人们所要求的使用性能或服役寿命。
热处理技术作为机械制造业中十分重要的基础工艺技术之一,在整个工业领域中,应用十分广泛。
在充分发挥材料潜能,节约能源,进行清洁生产和人类社会可持续发展上,热处理技术的拓展是绝不能忽视的。
世界上工业发达国家都投入很多资金来发展这门技术。
自1996年以来,美国、日本的欧洲的许多发达国家都先后制定21世纪热处理技术发展规划和目标。
美国热处理工业2020年远景把目前和将来国外热处理先进技术与装备水平的目标和主要标志阐述得十分明确。
对气体渗碳和用渗碳气氛加氨的气体碳氮共渗和氮碳共渗后排出的废气应经点燃后才可无害排放;离子渗硼中不可使用剧毒的B2H6(乙硼烷);对盐浴中不可使用受热要分解产生氰根的黄血盐和赤血盐;对含碳酸盐的盐浴不可使用尿素或缩二脲,因为它会反应生成氰酸盐,后分解为氰盐。
对含S和Li的氰酸盐—碳酸盐盐浴可使氰化物保持在0.1~0.8%的低水平,处理零件的渗氮后性能良好,且处理周期缩短,这工艺在美、欧和日本应用相当多,法国HEF公司的SURSULF工艺及处理后进入氧化盐浴属于这种技术,(我国的LT硫氮碳共渗法也是)。
在氰酸盐浴中添加有机聚合物melon也可将氰盐含量降到2%~3%,其余大部分是无毒的氰酸盐,法国HEF公司的德国Durferrit子公司(原属Degussa公司)的Tufftride / Melonite / Tenifer / QPQ处理盐浴属于此类技术,(我国成都工具研究所的QPQ复合盐浴处理也是)。
清洗水中的氰含量已经稀释可无害排放。
尽管如此,法、德和日本对这些工艺的无公害处理十分严格,并研究废盐的再生。
对高速钢刃具淬火仍采用的BaCl2盐浴和含BaCl2废水须经无害化处理达标后才允许排放,德国已采用专门技术和装置来解决。
真空渗碳工艺

真空渗碳工艺一、概述真空渗碳是一种高效的表面硬化处理方法,其主要作用是提高金属材料的抗磨损性能、耐腐蚀性能和疲劳寿命。
该工艺通过在真空环境中将金属样件暴露在碳源气体中,使得碳原子在样件表面形成一层均匀的硬质化合物层,从而提高材料的表面硬度和耐磨性。
二、工艺流程1. 预处理首先需要对待处理的金属样件进行清洗和除油处理,以保证样件表面干净无油污。
常用的清洗方法包括机械清洗、化学清洗和电解清洗等。
2. 装夹将经过预处理的金属样件装夹在真空渗碳设备中。
装夹时应保证样件间距适当,不得过于密集或过于疏松。
3. 真空排气启动真空泵进行排气,将渗碳设备内部压力降至目标值以下。
排气时间视设备大小和压力要求而定,通常需要数小时到数十小时不等。
4. 加热升温在排气结束后,开始进行加热升温。
加热速率应根据样件材质和要求的渗碳深度等因素进行调整,通常为10℃/min到50℃/min不等。
当样件温度达到目标温度时,保持一段时间以使其达到均匀的温度分布。
5. 渗碳在样件达到目标温度并保持一定时间后,开始注入碳源气体进行渗碳处理。
常用的碳源气体包括乙炔、甲烷、丙烷等。
渗碳时间视要求的硬化层厚度而定,通常需要数小时到数十小时不等。
6. 降温在完成渗碳处理后,开始进行降温。
降温速率应根据样件材质和硬化层深度等因素进行调整,通常为10℃/min到50℃/min不等。
当样件表面温度降至室温以下时,可以停止降温。
7. 后处理完成真空渗碳处理后,需要对金属样件进行清洗和除油处理,并对其表面进行抛光和喷涂等后处理工艺。
三、注意事项1. 清洗和除油处理应彻底,以保证样件表面干净无油污。
2. 装夹时应保证样件间距适当,不得过于密集或过于疏松。
3. 加热升温和降温速率应根据样件材质和硬化层深度等因素进行调整,过快或过慢都会影响硬化层的质量。
4. 渗碳时间应根据要求的硬化层厚度进行调整,过长或过短都会影响硬化层的质量。
5. 后处理工艺应细致,以保证金属样件表面光滑无划痕。
双室低压真空渗碳炉与单室低压真空渗碳炉性能特点比较

室炉在进行气淬时,冷却气体带走的热量不仅仅是工件的热量,在冷却工件的 同时,还要带走加热元件,隔热层,,等带有的热量,因此,他的气淬效率也 相对于双室炉低很多,经过测算,单室炉 10bar 的冷却能力,基本上与双室炉 6bar 的冷却能力相当。一般认为,对于 20bar 的氮气淬火,其淬火能力略逊于 静止的油淬,因此单室气淬炉的淬火能力之低,是可以想见的。 4, 更长的使用寿命和更低的保养成本: 由于单室炉,每次上下料都要开外炉门,使热区接触大气,因此在排气过程中, 难免会有部分氧化现象出现。使热区组件寿命降低。另外对于真空泵组来说, 频繁的从大气状态抽空到真空,并反复进行,也是不利于真空泵的使用寿命的。
2,
本。而对于双室炉,热区一直保持在真空和高温状态,在冷工件进入热室时, 炉温基本上降到 750 摄氏度,在此温度下进行真空加热,热量的传递,主要靠 辐射传热,因此,双室炉不需要安装低温对流加热装置即可达到快速加热。, 基于上述原因,双室真空炉相对单室真空炉有更快的加热速率和更高的生产效 率。
3, 更高的淬火效率: 由于单室炉设计的原因,其加热渗碳和淬火都在一个室内进行,在淬火时,高 压气体在冷却风扇的带动下高速流动,此时的高压气体冲击力很强,由于单室 炉的隔热层和加热元件为石墨构成,对高压气体的冲击承受能力有限,因此, 一般情况下,单室气淬炉的淬火压力仅为 10bar 左右,过高,会大大降低热区 构件的使用寿命。而对于双室炉,其加热室为在真空下连续加热,而淬火室内 结构基本由钢构成,不存在高压气体的冲击问题,因此,一般双室真空炉淬火 压力可达 20bar,这意味着,双室炉对于不同材料有更宽的适用范围。另外,单
ECM ICBP 966TG 双室渗碳炉技术特 公司的双室低压渗碳炉,与相应其他厂家的双室炉型比较,最明显的技术 优势是其可扩展性。 ECM 方案中提供的 ICBP966TG 在气淬室和加热渗碳室 中间有一个转移通道室(见图),该转移室在客户产能需要扩大时,可以将中 间转移室横向加长成通道罐,每一段通道罐,带有 2 个标准接口,可以连接 2 个新的加热渗碳室,如有需要,还可以加装一个淬火油槽(由于气淬的淬火能 力的局限性,如加装淬火油槽,该设备将可对任何牌号材料进行渗碳淬火处理, 增加该设备的通用性。)这就是 ECM 专利的模块化设计优势。这样,在今后的 生产中, 该设备将显示出更高的生产灵活性---- 对产能扩大的要求和对不同材料 淬火工艺的选择。并且,由于该设备在扩展时,其真空系统,控制系统,淬火 系统等都可以与之前的加热室公用,避免了重复采购,其单位生产能力的扩展 成本将大大低于购置新设备的成本。 另外,由于双室炉普遍采用横向滑动门,而单室渗碳炉一般炉门采用拉开式设 计,因此,采用双室炉设计,将便于设备的自动化联线,ECM 的 ICBP 设备的 控制系统可以与附属设备通讯,并控制其工作,这样,只要在附属设备和 ICBP 炉门前安装自动外部上料机构,就可以实现渗碳,回火,清洗等工艺的连续自 动生产,如 ECM 公司在上海汽车齿轮厂项目。 因此,模块化设计的 ICBP 设备,具有空前的灵活性,满足客户的不同需要。 生产的高效率: 由于 ECM 低压渗碳技术,及乙炔渗碳技术的采用,ICBP 设备具有很高的生产 效率,特别是和传统的单室低压渗碳炉比较,这表现在: 1, 节省加热时间: ECM 的 ICBP 设备,由于其双室设计,加热室由隔热气密门与传送室分隔,故 加热室始终处在热态(900 摄氏度左右的等待状态),因此冷工件进入热室时的 升温速率相应比较高,而传统的单室渗碳气淬炉需要从室温开始加热,因此双 室炉节省了加热时间,提高生产效率。 2 , 节省抽空时间: 单室渗碳气淬炉,由于其结构特点决定,在每次进料和出料时必须打开炉门, 使整个热区暴露在大气中。由于热区中的部件多数为石墨材料,具有很高的吸 气率(石墨的吸附特性),所以每次上料之后,在加热和抽空过程中,工作真 空度的建立需要相对长的时间( 在抽空的过程中,吸附在石墨材料上的气体会 随着真空度和温度的提高缓慢排出,在真空上技术上,叫做“真空排气”)。 另外,由于在低温状态下(低于 600 摄氏度)进行真空加热,其热传导主要靠 对流传递,因此单室真空炉,必须装有低温对流加热风扇并向炉内充氮气 (2bar),以提高低温段的加热速度。这样既使结构复杂化,也增加了生产成
渗碳常用工艺
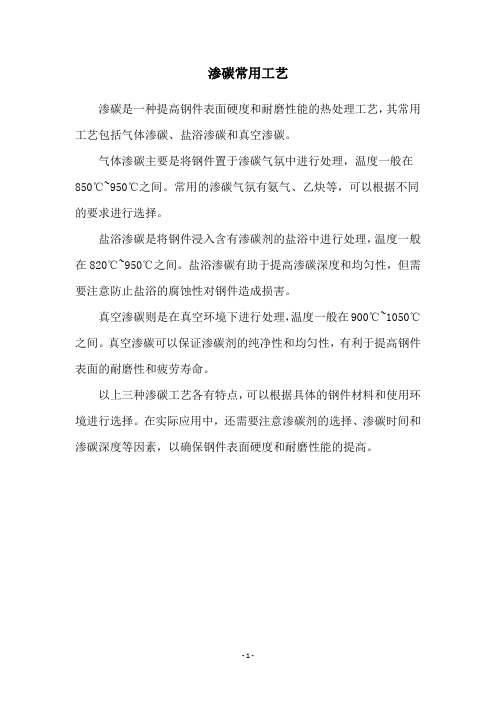
渗碳常用工艺
渗碳是一种提高钢件表面硬度和耐磨性能的热处理工艺,其常用工艺包括气体渗碳、盐浴渗碳和真空渗碳。
气体渗碳主要是将钢件置于渗碳气氛中进行处理,温度一般在850℃~950℃之间。
常用的渗碳气氛有氨气、乙炔等,可以根据不同的要求进行选择。
盐浴渗碳是将钢件浸入含有渗碳剂的盐浴中进行处理,温度一般在820℃~950℃之间。
盐浴渗碳有助于提高渗碳深度和均匀性,但需要注意防止盐浴的腐蚀性对钢件造成损害。
真空渗碳则是在真空环境下进行处理,温度一般在900℃~1050℃之间。
真空渗碳可以保证渗碳剂的纯净性和均匀性,有利于提高钢件表面的耐磨性和疲劳寿命。
以上三种渗碳工艺各有特点,可以根据具体的钢件材料和使用环境进行选择。
在实际应用中,还需要注意渗碳剂的选择、渗碳时间和渗碳深度等因素,以确保钢件表面硬度和耐磨性能的提高。
- 1 -。
浅谈低压真空渗碳热处理技术

203中国设备工程 2020.07 (上)中国设备工程C h i n a P l a n t E n g i n e e r i ng为了提高航空产品渗碳类零件工艺控制水平,于2010年从法国引进了一台低压真空渗碳炉,采用低压真空脉冲渗碳。
由于低压真空渗碳与我厂以往可控气氛渗碳相异之处较大,为充分发挥其优越性,必须熟悉低压真空渗碳工作原理,编制出合理的工艺程序,才能充分展现该设备的先进性。
本文对脉冲渗碳过程进行了初步探讨,通过多次试验,编制多种不同材料、不同技术要求的渗碳工艺程序。
1 低压真空渗碳1.1 渗碳概述不管是可控气氛渗碳还是低压真空渗碳,不外乎以下三个阶段:(1)渗碳介质的分解;(2)碳原子的浅谈低压真空渗碳热处理技术吴平(长沙中传航空传动有限公司,湖南 长沙 410200)摘要:本文探讨了低压真空渗碳原理及炉气成分,以及低压真空渗碳的优势与不足,影响零件表面碳浓度的相关因素。
结合实际应用情况,确定了几种典型齿轮渗碳工艺程序,为航空产品研制生产作好了技术准备。
关键词:低压真空;脉冲渗碳;饱和含碳量;工艺程序 中图分类号:TG156.9 文献标识码:A 文章编号:1671-0711(2020)07(上)-0203-03吸收;(3)碳原子的扩散。
1.2 真空脉冲渗碳原理(1)原理及过程:低压真空渗碳热处理实际上是在低压真空状态下,通过多个强渗(通人渗碳介质)+扩散(通入保护气体)与一个集中的扩散过程,达到满足图纸要求渗层深度的工艺过程,如图1所示。
其控制方法为“饱和值调整法”,即在强渗期使奥氏体固溶碳并饱和,在扩散期使固溶了的碳向内部扩散达到目标要求值,通过调整渗碳、扩散时间比,达到控制表面碳浓度和渗层深度的目的。
T1:第一步乙炔时间(零件表面碳浓度达到1.18所需要的时间)。
T2:第一步扩散时间(零件表面碳浓度达扩散至0.95所需要的时间)。
长焰煤30%比例比长焰煤10%比例高2.7℃/1.5℃,说明长焰煤30%比例的火焰中心是相对偏上的。
热处理技术装备发展趋势与市场前景

热处理技术装备发展趋势与市场前景1少无氧化加热技术与装备依然是行业发展的大趋势(1)真空热处理设备真空热处理技术具有无氧化、无脱碳和小畸变的优越性,也是当代热处理技术先进性的主要标志之一,在航空航天、兵器军工、电子特别是模具等行业的应用越来越广泛,每年的热处理炉产量约500台。
一方面,真空热处理设备市场很大;另一方面,设备供应商家也多。
市场竞争激烈促使商家进一步提高产品质量,加强服务意识。
参加本次展览的真空炉厂家共计20家,海外制造商和国内企业基本上各占一半。
易普森工业炉(上海)有限公司、德国iva(益发)工业炉有限公司、日本jh(japanhayes)corporation、ald真空工业股份公司、德国schmetz公司、德国pva公司、法国bmi、ecm公司、康萨克公司等都带来自己的最新技术和最新设备。
如jh(japanhayes)公司展示了乙炔真空渗碳技术,法国ecm公司介绍了低压真空渗碳技术,德国schmetz公司产品以高压气淬炉和双向冷却系统、深度冷却系统为特长,主要用于工模具行业;ald真空工业股份公司也是一家老牌的真空炉厂家,主要产品有单双室、模块化真空高压渗碳气淬炉等;德国pva公司的主要产品有高温真空炉和钎焊炉,法国bmi主要产品有高压气淬、油淬真空炉和低压渗碳、渗氮炉,康萨克公司现隶属应达集团公司,主要生产各种真空热处理炉,其炉温控制精度高,主要用于航空航天工业,新近在国内无锡建厂。
国内真空热处理设备技术发展很快,以质量上乘、价格优势和良好服务赢得了市场。
北京机电研究所、中国电子科技集团公司第二研究所、北京七星华创电子股份有限公司工业炉公司、北京华翔电炉技术有限责任公司、北京市华海中谊真空工业炉制造有限公司、北京易西姆工业炉科技发展有限公司、汉中汉江工具赛普机电设备有限公司、爱发科中北真空(沈阳)有限公司、沈阳恒进真空科技有限公司、沈阳佳誉真空科技有限公司等参加展览,其中北京机电研究所在设备质量和成套工艺技术服务方面表现突出,汉中汉江工具赛普机电设备有限公司在制造设备的同时,又有热处理加工服务。
真空渗碳及碳氮共渗技术近况和应用
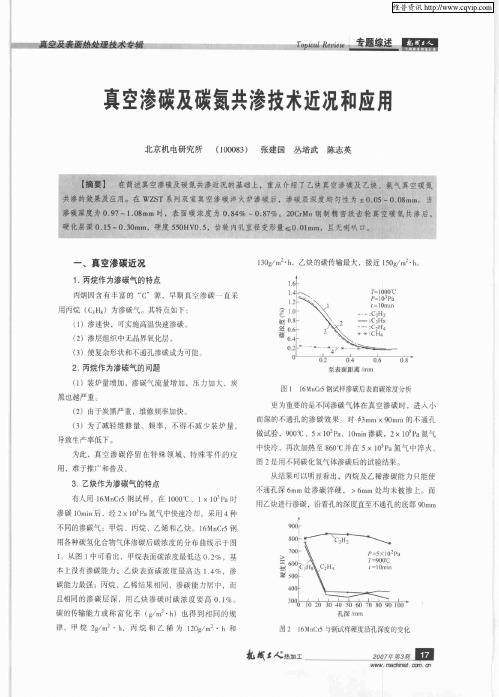
维普资讯
长, 效率提高,装炉量逐渐加大到 30 70g炉。 0 ~ 0k /
0 9 0 2 2. 8 6 3 4 3 O. 0. 0 0. 3 O. 2 0. 0 4l 4 4 4 4 0 9 0 2 1 5 4 4 4 4 O. 2 7 3 8 . O 0. 5 O. _ 0. 4 0. 3 4 4 0 9 0 2 1 1 4 4 4 4 0. 4 8 3 8 . O 0. 6 0. 5 0. 3 O. 3 4 0 9 0 2 10 4 4 3 3 3 9 3 5 . 7 0. 0 0. 0 O. 7 O. 9 O. 8
更为重要的是不同渗碳气 体在真空渗碳时 ,进^小
而深的不通孔的渗碳效 果: :对 3 l x9 m 的不通孔 mn 硼 0
()为了减轻维修 量 、频率 ,不 得不减 少装炉量 , 3 导致生产率低下 为此,真空渗 碳停 留在特 殊领 域 、特殊 零 件的应
用 .难于推广和普及
做试验 . 0T、5 2a O i 90 1 P 、lmn渗碳 .2x1 a x 0 0P 氮气 中快冷 , 次加热 至 80E并在 5×1 a 气中淬 火 再 6 ̄ 0P 氨 图 2是再不同碳 化氢气体渗碳后的试验结果 .
( 质量分数 , %)
0∞ .
三、真空渗碳的应用
1 齿轮类零件的应用 .
图 4 2C M 齿 轮类零 件真空 渗碳后外 观 ,渗层 为 0r o
- 1、下载文档前请自行甄别文档内容的完整性,平台不提供额外的编辑、内容补充、找答案等附加服务。
- 2、"仅部分预览"的文档,不可在线预览部分如存在完整性等问题,可反馈申请退款(可完整预览的文档不适用该条件!)。
- 3、如文档侵犯您的权益,请联系客服反馈,我们会尽快为您处理(人工客服工作时间:9:00-18:30)。
乙炔真空渗碳的现状
[ 日本] 岩田均
摘 要: 介绍了乙炔真空渗碳新工艺的特点、发展现状、工艺流程, 阐述了该工艺的实 际应用以及今后有待解决的课题。
关键词: 乙炔真空渗碳; 工艺; 应用
中图分类号: TG156. 8+ 1
文献标识码: B
引言
乙炔真空渗 碳技术自 公布以 来已历 时 7 a 左 右, 由于其优异的渗碳质量、渗碳再现性以及解决碳 黑问题, 从而有较好的热处理效果, 目前正在应用于 各个领域。乙炔真空渗碳实现了产品质量的改进和 作业环境的改善, 显示了热处理技术的一个发展方 向。并且, 它具有气体渗碳中所没有的下述特征:
料 载气 CO
工艺参数
粉 末 材料
温度
进料
反应 升华 蒸发 速度 直径/
器中 器中 器中 L/h
喷涂质量
浓度 g/ cm2
150 / 60 60 40~ 140 0. 5~ 1. 8
CO 120 / 20 40 50~ 200 0. 6~ 2. 2
CO, N 400 50 / 30 50~ 80 0. 6~ 1. 2
第4期
乙炔真空渗碳的现状
31
表 3 批量内表面含碳量的差异
区段
F侧
R侧
4
0. 79
0. 81
3
0. 79
0. 78
2
0. 79
0. 78
1 平均
0. 83
0. 85
0. 803
差异范围 0. 78% ~ 0. 85% C 范围 0. 07% C ( 质量分数 C)
处理工件: SCM420H 齿数
3 复合热处理的发展
3. 1 高碳真空渗碳 可析出微细碳化物的高碳真空渗碳处理, 采用
5 结束语
使用不饱和碳化氢气体 ∃ ∃ ∃ 乙炔的乙炔真空渗 碳技术进入市场已历时 7 a 了。从根本上解决了采 用丙烷进行真空渗碳固有的碳黑问题, 目前。该工 艺设备作为批量生产用设备, 在各领域中推广应用。 今后, 将研究进一步提高渗碳气体的效率、利用高温
渗碳以缩短渗碳时间等课题, 而且, 要积极推动向连
表面硬度 758 768 ∀ 749 72 757 34 2. 4 2. 3
渗碳深度 0. 64 0. 69 ∀ 0. 72 0. 87 0. 7 0. 1 3. 2 1. 9
( 注: 汽车零件材质 SUM 22, 渗碳硬化层 0. 7 mm, 批 的数量 3 600 个, 悬挂方式处理)
表 3 表示对汽车油压零件实施真空渗碳处理 时, 得到的表面含碳量离散的结果。其表面含碳量 的离散在批内幅度为 0. 1% 以内 ( # 0. 05% 以内) , 如采用乙炔真空渗碳, 则在批内、批与批之间、单件 内的渗碳均匀性均无问题, 该工艺完全可用于批量 产品的处理。
1) 可实现高温下的短时间处理; 2) 不会产生晶界氧化, 不易形成表面的不完全 淬火层; 3) 渗碳层的控制较简单; 4) 对有细孔、非贯通孔等复杂形状的工件, 具有 良好的渗碳性。 丙烷真空渗碳炉的最大问题是, 随着碳黑的产 生而带来了各种弊端。而这种碳黑问题得到解决的 根本原因, 是因为在超低压 下( 在 1 kPa 以下, 为通 常真空热处理的作业水平) 将乙炔 用作渗碳气体。 关于采用乙炔真空渗碳工艺所得到的产品质量、经 济性以及安全性等在热处理协会杂志等文献上作了 报道。目前, 已有乙炔真空渗碳炉作为批量生产用 真空渗碳炉正在运行, 本文将以渗碳质量为中心, 介 绍用乙炔真空渗碳炉进行批量生产处理的现状。
传统的丙烷真空渗碳工艺, 存在着操作中产生碳黑 的问题, 因而不太使用该方法。如果采用乙炔真空 渗碳, 就较容易实现高碳真空渗碳。在质量方面, 渗 碳层中的碳化物大小、形状和析出层都能满足要求, 有利于提高工件耐磨性和改善疲劳强度。该工艺在 砂土磨耗严重的 磁砖金属模具( SKD11) 、机床的主 轴、喷丸机的叶轮等的应用中取得一定的成果, 从而 过渡到了批量产品的应用阶段。 3. 2 真空碳氮共渗与喷丸强化处理
续真空渗碳炉发展的研究工作。
%
译自日本&热处理∋2005, ! 3, 125~ 127
彭惠民 译 金祥林 校
收稿日期: 2006- 02- 23
( 上接第 28 页)
表 1 金属化工艺规范及金属复合粉末材料的性能
原
涂层
Fe( CO) 5 Ni( CO) 4 Cr( CO) 6 Mo( CO ) 6 W( CO) 6 Cr( C6H6) 2
采用乙炔气体, 在各种温度下, 对 SCM415 的试 件实施了不同时间的渗碳, 根据所得到的渗碳层的 碳分析, 在总渗碳时间下, 求得的 K 值及有效渗碳 深度达到 0. 3% C 及 0. 4% C 时, 求出的 K 值的结果 见表 1。并且, 总渗碳深度、渗碳及扩散的各个时间 设定也列于表 1 中。另外, 除了 SCM415 钢材外, 对 Si5C 与 SNCM420 也进行 了同样的 试验, 求出了 K 值。虽材质不同, K 值几乎无变化。合金元素产生 的影响, 与其说是对渗碳难易程度的控制, 不如说是 对淬透性产生较大的影响。
图 5 用 V - MALS 连续高空渗碳炉的操作图表
图 4 不锈钢的真空渗碳硬度分布曲线
4 连续真空渗碳炉的现状
作为最新尝试的多个加热室 V- MALS 连续真 空渗碳炉已投入使用了。本设备是适应于多品种生 产及少品种大批量生产的连续真空渗碳炉。图 5 为 使用 V- MALS 连续真空渗碳炉的代表性的热处理 曲线。由该图可知, 如硬化层为 0. 7 mm 左右, 则生 产线的生产节拍可定为 75~ 90 min。
图 1 批量产品处理中炉内压力与硬度的关系
图 2 批量产品处理中炉内压力与变形量的关系
此外, 对于淬透性好的合金钢小工件而言, 渗碳 后的气体冷却是有效措施, 无需淬火后的表面清洗, 而且, 淬火变形小, 可以做到高质量的渗碳淬火。该 工艺在欧洲国家已相当普及了。 2 批量生产应用中的渗碳均匀性
乙炔真空渗碳中的渗碳均匀性, 在批量与批量 之间、批量内都得到了稳定的结果。
表 1 K 值、R 值与渗碳温度
渗碳温度 900 930 980 1 040
应用实例
8% 表面含碳量
总渗碳深度 0. 62 0. 71 1. 14 1. 24 低碳钢、表面硬化钢
K
有效渗碳深度 To 0. 3% C
0. 44
0. 54
0. 78
1. 04 表面硬化钢
有效渗碳深度 To 0. 4% C
业已证实: 如采用乙炔真空渗碳, 则没有温度上 的制约, 对不锈钢的渗碳处理, 能提高耐磨性。图 3 表示在柴油发动机汽车零件上进行乙炔真空渗碳得 到的组织照片( 工件状态) ; 图 4 表示其硬度分布。
30
国外机车车辆工艺
2006 年 7 月
图 3 不锈钢工件真空渗碳的组织照片( 汽车零件 SUS304)
0. 37
0. 46
0. 69
0. 94 低碳钢
R 扩散时间 T d 渗碳时间 T c 1. 3
1. 5
2. 2
3. 5 低碳钢
1. 3 淬火 渗碳与扩散结束之后, 用氮气将压力恢复到 20
kPa~ 80 kPa 左右, 再进行油淬。通过选择适当地恢
第4期
乙炔真空渗碳的现状
29
复压力设定值, 可改变淬火油的冷却特性, 能减少淬 火变形。但是, 油面压力过低, 淬火油的冷却能力就 不足, 就不能淬硬。图 1 表示工业车辆用齿轮的批 量处理中的炉内压力与淬火硬度的关系; 图 2 为批 量产品热处理中炉内压力与工件变形量的关系。该 齿轮( 渗碳用表面硬化钢) 得到的处理结果是: 只要 在一定的炉内压力范围内, 经过减压, 淬火硬度就会 提高, 变形量也减少( 绝对值) 。由此可知, 在真空渗 碳炉中, 为了减小工件变形量, 油淬时的油面压力是 抑制变形的一个重要因素。
炉体结构, 基本上与普通的真空炉相同, 其结构可承 受 1 100 以上的温度, 可以任意地选择高于普通渗 碳温度的温度。当需要特别深的渗碳层时, 可以采 用高温渗碳, 大幅度地缩短渗碳时间。 1. 2 渗碳时间与扩散时间的设定
在真空气氛中, 当升温及各部位均匀加热结束 后, 就立刻引入渗碳气体( 乙炔气体) 。在几秒钟后 炉内达到规定压力, 工件表面各部位就会均匀地处 在减压下的渗碳气氛中, 并立即开始渗碳。在规定 时间渗碳后, 再排出渗碳气体, 然后再恢复到原来的 真空度进行扩散。
图 2 用等离子喷涂法对零件表面喷涂金属化粉末材料的强化涂层
实际使用的结果表明, 用金属有机镍化合物金
属化的氧化铝( 含镍 20% ) 强化的零件, 其使用寿命
比原部件提高了 3. 5~ 4 倍。
%
译自俄罗斯& !∀#∃%&∃∋ (#∃)∗!∃+,−!∃∋
胥金荣 译 宋忠明 校
收稿日期: 2006- 03- 17
为改善工件的高温疲劳强度和耐热胶着性能, 人们正在对真空渗碳工艺中再加入氮化处理的碳氮 共渗( 高碳) 工艺作详细研讨。据报道, 真空碳氮共 渗或者在真空碳氮共渗( 高碳) 后再通过实施喷丸强 化处理, 可获得良好的表面强化效果。今后, 期待该 工艺在需要高温强度的零部件上得到应用。 3. 3 不锈钢的渗碳
CO 600 70 / 30 60~ 120 0. 6~ 1. 2
CO, N 750 80 / 30 40~ 120 1. 0~ 1. 5
Co. N 320 / 40 40 600~ 100 0. 5~ 1. 0
离子喷涂法在 65 号钢制成的 试样表面进行 喷涂 ( 见图 2a) , 以及在中耕机工作爪的工作面上进行喷 涂( 见图 2b) 。台架试验的结果表明, 用镍金属化的 三氧化二铝强化涂层( 含镍 10% ~ 30% ) 的试件, 其 耐磨性比 65 钢试样本身提高 1. 5~ 3. 0 倍以上。