复合型疲劳裂纹研究的现状与展望
复合材料的疲劳裂纹扩展与评估

复合材料的疲劳裂纹扩展与评估在现代工程领域,复合材料凭借其优异的性能,如高强度、高刚度、良好的耐腐蚀性等,得到了广泛的应用。
然而,就像任何材料一样,复合材料在长期的使用过程中也会面临疲劳损伤的问题,其中疲劳裂纹的扩展是导致其性能下降甚至失效的重要原因之一。
因此,深入研究复合材料的疲劳裂纹扩展机制,并建立有效的评估方法,对于确保复合材料结构的可靠性和安全性具有至关重要的意义。
要理解复合材料的疲劳裂纹扩展,首先需要了解复合材料的基本组成和结构。
复合材料通常由两种或两种以上具有不同物理和化学性质的材料组成,其中一种作为基体,另一种或几种作为增强相。
常见的复合材料有纤维增强复合材料,如碳纤维增强复合材料和玻璃纤维增强复合材料,以及颗粒增强复合材料等。
在疲劳载荷作用下,复合材料中的裂纹起始和扩展过程与传统的单一材料有很大的不同。
对于单一材料,裂纹通常在材料的表面或内部缺陷处起始,并沿着特定的晶体学方向扩展。
而对于复合材料,由于其复杂的微观结构,裂纹的起始位置可能在基体、增强相或者基体与增强相的界面处。
而且,裂纹在扩展过程中会遇到不同的相和界面,其扩展路径也会变得更加复杂。
影响复合材料疲劳裂纹扩展的因素众多。
首先是材料的组分和微观结构。
增强相的类型、含量、分布以及与基体的结合强度都会对疲劳性能产生影响。
例如,碳纤维具有较高的强度和刚度,能够显著提高复合材料的疲劳性能;而增强相的分布不均匀可能导致局部应力集中,从而加速裂纹的起始和扩展。
其次,加载条件也是一个重要因素。
加载频率、应力比、加载波形等都会影响疲劳裂纹的扩展速率。
此外,环境因素如温度、湿度等也可能对复合材料的疲劳性能产生不利影响。
为了研究复合材料的疲劳裂纹扩展行为,科学家们采用了多种实验方法。
其中,最常用的是疲劳试验。
通过对试样施加循环载荷,监测裂纹的长度随循环次数的变化,从而得到疲劳裂纹扩展曲线。
在实验中,通常采用光学显微镜、扫描电子显微镜等设备来观察裂纹的形态和扩展路径。
复合材料的疲劳裂纹扩展研究

复合材料的疲劳裂纹扩展研究在现代工程领域,复合材料因其优异的性能而得到了广泛的应用。
然而,复合材料在长期承受循环载荷作用时,疲劳裂纹扩展问题成为了影响其可靠性和使用寿命的关键因素。
因此,对复合材料疲劳裂纹扩展的研究具有重要的理论意义和实际应用价值。
复合材料是由两种或两种以上不同性质的材料通过物理或化学方法组合而成的一种新型材料。
其具有比强度高、比刚度大、耐腐蚀、耐高温等优点,广泛应用于航空航天、汽车、船舶、体育器材等领域。
但是,由于复合材料的组织结构和性能的复杂性,其疲劳裂纹扩展行为与传统金属材料有很大的不同。
复合材料的疲劳裂纹扩展机制较为复杂。
在疲劳载荷作用下,复合材料内部会产生多种损伤形式,如纤维断裂、基体开裂、界面脱粘等。
这些损伤相互作用,共同影响着疲劳裂纹的扩展。
与金属材料的疲劳裂纹通常沿着晶界或滑移面扩展不同,复合材料中的疲劳裂纹可能会沿着纤维方向、基体内部或者纤维与基体的界面扩展,这取决于材料的组成、纤维的排布方式以及加载条件等因素。
影响复合材料疲劳裂纹扩展的因素众多。
首先是材料的组成和结构。
纤维和基体的性能、纤维的体积含量、纤维的排布方式等都会对疲劳裂纹扩展产生重要影响。
例如,高强度的纤维可以提高复合材料的疲劳性能,而纤维与基体之间良好的界面结合则有助于阻止裂纹的扩展。
其次,加载条件也是一个关键因素。
加载频率、应力比、最大应力等都会改变疲劳裂纹的扩展速率。
此外,环境因素如温度、湿度等也会对复合材料的疲劳性能产生不可忽视的影响。
为了研究复合材料的疲劳裂纹扩展,实验研究是必不可少的手段。
常见的实验方法包括恒幅疲劳实验、变幅疲劳实验和疲劳裂纹扩展实验等。
在这些实验中,可以通过测量裂纹长度随循环次数的变化来获得疲劳裂纹扩展速率。
同时,借助先进的检测技术,如 X 射线衍射、电子显微镜等,可以对疲劳损伤的微观机制进行深入分析。
在理论研究方面,已经建立了一些模型来描述复合材料的疲劳裂纹扩展行为。
疲劳裂纹扩展的健康监测技术研究进展(二)2024

疲劳裂纹扩展的健康监测技术研究进展(二)引言概述:疲劳裂纹扩展是金属材料在长期受力作用下产生的一种破坏形式,对工程结构的安全性和可靠性具有重要影响。
因此,开展疲劳裂纹扩展的健康监测技术研究,对于提高工程结构的安全性和可维护性具有重要意义。
本文着重探讨疲劳裂纹扩展的健康监测技术研究进展,并从以下五个大点进行阐述。
一、无损检测技术在疲劳裂纹监测中的应用1. 超声波检测技术2. 磁控传感器技术3. 红外热成像技术4. 振动传感器技术5. X射线检测技术二、微小裂纹监测技术的研究进展1. 微小裂纹检测的难点与要求2. 光纤光栅传感器监测技术3. 微纳传感器监测技术4. 萤石磷光体监测技术5. 声发射技术在微小裂纹监测中的应用三、结构健康监测技术在疲劳裂纹扩展中的应用1. 动态应变测试技术2. 激光干涉技术3. 无线传感器网络技术4. 智能监测系统技术5. 基于云计算的健康监测技术四、机器学习在疲劳裂纹监测中的应用1. 数据采集与处理2. 特征提取和选择3. 分类算法与模型训练4. 监督学习和无监督学习方法5. 集成学习与深度学习技术五、新兴技术在疲劳裂纹健康监测中的前景和挑战1. 纳米技术在疲劳裂纹监测中的应用2. 多尺度监测技术的研究前景3. 多模态监测技术的发展趋势4. 生物启发式监测技术的潜力5. 疲劳裂纹健康监测中的可持续性及环保问题总结:疲劳裂纹扩展的健康监测技术研究正在不断取得突破,无损检测技术、微小裂纹监测技术、结构健康监测技术、机器学习技术和新兴技术的应用为疲劳裂纹的及时发现和有效监控提供了更先进的手段和方法。
然而,仍然存在一些挑战,如数据处理和算法优化等。
未来的研究重点应放在新兴技术的应用和发展趋势上,以提高疲劳裂纹健康监测的准确性、可靠性和可持续性。
复合材料疲劳裂纹扩展行为研究

复合材料疲劳裂纹扩展行为研究在现代工程领域,复合材料因其优异的性能而得到广泛应用。
然而,疲劳裂纹扩展行为是影响复合材料使用寿命和可靠性的关键因素之一。
对复合材料疲劳裂纹扩展行为的深入研究,对于保障结构的安全性和耐久性具有重要意义。
复合材料是由两种或两种以上不同性质的材料通过物理或化学方法组合而成的。
与传统单一材料相比,复合材料具有高强度、高刚度、良好的耐腐蚀性等优点。
但正是由于其复杂的成分和结构,使得疲劳裂纹的扩展行为更为复杂。
疲劳裂纹的产生通常源于材料内部的微观缺陷、制造过程中的残余应力或者在使用过程中的外部载荷作用。
在复合材料中,这些因素的相互作用使得裂纹的萌生和扩展机制变得多样化。
例如,纤维增强复合材料中的纤维与基体之间的界面性能、纤维的分布和取向等都会对疲劳裂纹的扩展产生显著影响。
研究复合材料疲劳裂纹扩展行为的方法多种多样。
实验研究是其中最直接和有效的手段之一。
通过对标准试样进行疲劳加载实验,可以获得裂纹扩展速率与应力强度因子范围之间的关系曲线。
在实验中,需要精确控制加载条件、测量裂纹长度的变化,并记录相关的数据。
同时,借助先进的观测技术,如电子显微镜、X 射线衍射等,可以对裂纹扩展过程中的微观结构变化进行详细分析。
除了实验研究,数值模拟方法也在复合材料疲劳裂纹扩展研究中发挥着重要作用。
有限元方法、边界元方法等可以建立复合材料的微观或宏观模型,模拟疲劳裂纹的扩展过程,并预测其寿命。
这些数值方法能够考虑材料的非均匀性、各向异性等特性,为深入理解裂纹扩展机制提供了有力的工具。
在研究复合材料疲劳裂纹扩展行为时,还需要考虑环境因素的影响。
例如,温度、湿度等环境条件会改变材料的性能,从而影响疲劳裂纹的扩展速率。
此外,加载频率、加载波形等加载条件也会对裂纹扩展行为产生不同程度的影响。
对于不同类型的复合材料,其疲劳裂纹扩展行为也存在差异。
例如,碳纤维增强复合材料和玻璃纤维增强复合材料在纤维类型、强度和刚度等方面有所不同,导致它们在疲劳性能上表现出各自的特点。
复合材料结构疲劳损伤特性分析及维修技术研究

复合材料结构疲劳损伤特性分析及维修技术研究近年来,随着科技的不断发展和人们对材料的需求不断增加,复合材料的应用范围已经扩展到了航空、汽车、建筑等多个领域。
复合材料具有轻质、高强、高刚性等优点,但同时也存在一些缺陷,其中最重要的就是疲劳问题。
复合材料在使用过程中,会面临着不断的载荷变化和温度变化,这些都会对材料属性产生不同程度的影响。
而长时间的使用后,多次复合载荷会产生疲劳问题,不仅会降低复合材料的强度和刚度,还可能导致材料出现裂纹、层间剥离等损伤,进而影响整个结构的安全性和可靠性。
因此,分析复合材料结构疲劳损伤特性及其维修技术已经成为了研究的热点。
一、复合材料结构疲劳损伤特性的分析方法1. 宏观损伤评估方法宏观损伤评估方法是将复合材料结构划分为不同的单元,通过分析各个单位材料的应变和声发射等参数,来评估结构的损伤程度。
遇到复合材料损伤事故时,这种方法的优点在于可以定位和判断损伤区域,对后续的维修方案设计有指导作用。
2. 微观损伤评估方法微观损伤评估方法是将复合材料结构放大到材料的微观尺度,通过观察材料和显微镜下的形状和颜色,来寻找材料中的裂纹和损伤。
然后,通过一系列的试验和数据分析,来评估复合材料在不同载荷和温度下的疲劳性能。
二、复合材料结构的维修技术研究1. 干式结构修复技术干式结构修复技术是利用环氧粘结剂对复合材料结构进行修复的方法。
这种技术具有修复效果好,方便实施、成本低等优点,但是对环氧粘结剂的成分和使用方法要求极高,一旦操作失误就会导致修复失效。
2. 液态材料注射修复技术液态材料注射修复技术是利用没有固化的液态复合材料注射到损伤部位进行修复的方法,这种方法具有精准度高、修复效果稳定等优点。
但是,该方法的局限是要求损伤部位比较容易接近和注射材料的质量较为重要。
3. 微波技术修复技术微波技术修复技术是利用微波高频能量对复合材料结构进行修复的方法,这种技术具有损伤面积小、立即修复等优点。
不过,该技术还处于研究阶段,需要更多实验和数据来验证其可行性。
复合型疲劳裂纹扩展门槛值的研究
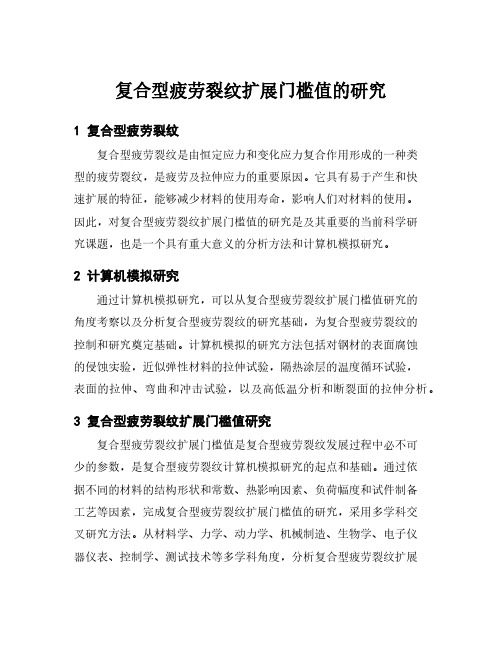
复合型疲劳裂纹扩展门槛值的研究1 复合型疲劳裂纹复合型疲劳裂纹是由恒定应力和变化应力复合作用形成的一种类型的疲劳裂纹,是疲劳及拉伸应力的重要原因。
它具有易于产生和快速扩展的特征,能够减少材料的使用寿命,影响人们对材料的使用。
因此,对复合型疲劳裂纹扩展门槛值的研究是及其重要的当前科学研究课题,也是一个具有重大意义的分析方法和计算机模拟研究。
2 计算机模拟研究通过计算机模拟研究,可以从复合型疲劳裂纹扩展门槛值研究的角度考察以及分析复合型疲劳裂纹的研究基础,为复合型疲劳裂纹的控制和研究奠定基础。
计算机模拟的研究方法包括对钢材的表面腐蚀的侵蚀实验,近似弹性材料的拉伸试验,隔热涂层的温度循环试验,表面的拉伸、弯曲和冲击试验,以及高低温分析和断裂面的拉伸分析。
3 复合型疲劳裂纹扩展门槛值研究复合型疲劳裂纹扩展门槛值是复合型疲劳裂纹发展过程中必不可少的参数,是复合型疲劳裂纹计算机模拟研究的起点和基础。
通过依据不同的材料的结构形状和常数、热影响因素、负荷幅度和试件制备工艺等因素,完成复合型疲劳裂纹扩展门槛值的研究,采用多学科交叉研究方法。
从材料学、力学、动力学、机械制造、生物学、电子仪器仪表、控制学、测试技术等多学科角度,分析复合型疲劳裂纹扩展门槛值研究,分析复合型疲劳裂纹多体问题,并从计算机科学角度结合系统理论和复合型疲劳裂纹的多重情况,进行研究和实践。
4 结论复合型疲劳裂纹的研究对于钢材的使用寿命和强度具有重要意义,因此复合型疲劳裂纹扩展门槛值的研究成为了当前科学研究的重点,需要多学科的综合研究,从而为加固材料结构拓展出新的设计理念,改善材料的使用寿命和强度能够提供准确可靠的参考。
疲劳裂纹扩展的健康监测技术研究进展(一)2024

疲劳裂纹扩展的健康监测技术研究进展(一)引言概述:疲劳裂纹扩展是一种常见的结构损伤模式,对工程结构的安全性和可靠性具有重要影响。
近年来,随着健康监测技术的不断发展,疲劳裂纹扩展的健康监测技术也得到了快速进展。
本文将就疲劳裂纹扩展的健康监测技术研究进展进行详细介绍。
正文:1. 无损检测技术1.1 超声波检测技术1.2 热红外成像技术1.3 激光检测技术1.4 射线检测技术1.5 声发射检测技术2. 电化学监测技术2.1 电化学阻抗谱技术2.2 电化学噪声技术2.3 电化学腐蚀技术2.4 电化学传感器技术2.5 微流控技术3. 结构响应监测技术3.1 动态应变测量技术3.2 振动响应测量技术3.3 结构声发射监测技术3.4 变形监测技术3.5 特征参数提取技术4. 健康评估与预警技术4.1 数据处理与分析技术4.2 模型预测与诊断技术4.3 扩展寿命预测与评估技术4.4 基于机器学习的健康监测技术4.5 蓝牙无线传输技术5. 系统集成与管理技术5.1 分布式监测系统5.2 多传感器网络技术5.3 实时监测与远程控制技术5.4 数据存储与共享技术5.5 监测与报警系统的可视化展示技术总结:疲劳裂纹扩展的健康监测技术研究取得了显著进展,主要包括无损检测技术、电化学监测技术、结构响应监测技术、健康评估与预警技术以及系统集成与管理技术等方面。
这些技术的不断发展和应用,为工程结构的安全性和可靠性提供了有力的支持。
然而,仍然存在一些挑战和问题需要进一步研究和解决,如数据处理与分析的优化、模型预测与诊断的准确性提升、系统集成与管理的完善等。
相信随着技术的不断创新和完善,疲劳裂纹扩展的健康监测技术将会得到更广泛的应用和推广。
复合材料的疲劳性能与性能研究

复合材料的疲劳性能与性能研究在现代工程领域中,复合材料凭借其卓越的性能表现,已经成为众多关键应用中的首选材料。
然而,要充分发挥复合材料的优势,深入理解其疲劳性能和其他相关性能至关重要。
复合材料是由两种或两种以上具有不同物理和化学性质的材料组合而成。
常见的复合材料包括纤维增强复合材料(如碳纤维增强复合材料、玻璃纤维增强复合材料)和层合复合材料等。
这些材料通常具有高强度、高刚度、良好的耐腐蚀性和轻质等优点,使其在航空航天、汽车、船舶、体育用品等领域得到了广泛应用。
疲劳性能是评估材料在循环载荷作用下抵抗破坏能力的重要指标。
对于复合材料而言,其疲劳行为较为复杂,受到多种因素的影响。
首先,复合材料的组成成分,如增强纤维和基体材料的性质,对疲劳性能起着关键作用。
一般来说,高强度的纤维能够提供更好的抗疲劳能力,而基体材料的韧性和粘结性能则影响着纤维与基体之间的载荷传递效率。
其次,复合材料的制造工艺也会显著影响其疲劳性能。
例如,纤维的排列方向和分布均匀性、制造过程中的孔隙率和缺陷等,都会在疲劳过程中成为裂纹萌生和扩展的源头。
此外,加载条件,包括载荷的大小、频率、波形以及环境因素(如温度、湿度、化学介质等),也会对复合材料的疲劳寿命产生重要影响。
在研究复合材料的疲劳性能时,常用的实验方法包括疲劳试验和疲劳寿命预测模型。
疲劳试验通常在专门的试验机上进行,通过施加循环载荷来观察材料的失效行为,并记录疲劳寿命数据。
为了更准确地评估复合材料在实际使用条件下的疲劳性能,还会进行模拟实际工况的复杂加载和环境条件下的试验。
疲劳寿命预测模型则是基于实验数据和理论分析,试图建立起材料性能、载荷条件和疲劳寿命之间的定量关系。
常见的预测模型包括基于应力寿命(SN)曲线的方法、基于损伤力学的方法以及基于概率统计的方法等。
这些模型在一定程度上能够帮助工程师在设计阶段预估复合材料结构的疲劳寿命,从而优化设计,提高结构的可靠性。
除了疲劳性能,复合材料的其他性能也同样值得关注。
- 1、下载文档前请自行甄别文档内容的完整性,平台不提供额外的编辑、内容补充、找答案等附加服务。
- 2、"仅部分预览"的文档,不可在线预览部分如存在完整性等问题,可反馈申请退款(可完整预览的文档不适用该条件!)。
- 3、如文档侵犯您的权益,请联系客服反馈,我们会尽快为您处理(人工客服工作时间:9:00-18:30)。
鞍钢技术复合型疲劳裂纹研究的现状与展望田常海(鞍钢技术中心)摘要 介绍了国内外有关学者对复合型疲劳裂纹扩展的研究情况及试验结果,并对他们的理论加以详细论述,同时提出了今后这一领域的研究方向。
关键词 疲劳裂纹 扩展Now aday Sit uation and Perspective ofthe Invest igation of Composite Fatig ue CrackTian Changhai(AISC Technolog y Center)Abstract T his a rticle intr oduces t he situation of the study on co mposite fatigue cr ack spread-ing by the fo reign ex per ts and the ex per iment results,gives t he detail discussion o n their theo ry, and point s o ut the direction of t he study in t his f ield as w ell.Key Words fatig ue crack spr ead1 引 言疲劳裂纹的扩展取决于部件所用的材料性质、几何形状及受载情况等,过去对于疲劳裂纹扩展的描述在工程上一般都基于Paris 公式,它对描述纯Ⅰ型疲劳裂纹扩展是成功的。
但是,实际工程中的大多数情况并非是纯Ⅰ型的,而往往是复合型受载,在复合型加载条件下,含有Ⅱ型裂纹的复合型裂纹往往改变原裂纹的扩展方向,含有Ⅲ型裂纹的复合田常海 工学博士 鞍钢技术中心金检室 邮编 114001型裂纹往往发生裂纹面的扭转,对这一情况, Paris公式便无能为力。
于是一些学者进行了Ⅰ-Ⅱ、Ⅰ-Ⅲ复合型裂纹扩展试验,提出了描述复合型裂纹扩展的理论。
2 Ⅰ-Ⅱ复合型疲劳裂纹的扩展2.1 Ⅰ-Ⅱ复合型疲劳裂纹门槛值试验Qao H ua〔1〕等人利用单边缺口试样(受非对称的四点弯曲循环加载和含倾斜裂纹板试样承受循环双轴拉伸)进行了大量的铁合金和有色合金疲劳裂纹门槛值试验,获得了Ⅰ-Ⅱ复合型裂纹门槛值分布图,如图1所示。
图1中的实线表示下限门槛值,低于此值时,在载荷比R =0.2以及加载频率f =15~80Hz 的情况下,探测不到疲劳裂纹的扩展。
虚线代表门槛值上限,在上限之外的区域,裂纹在垂直于裂纹尖端最大拉应力(R Q )max 的平面上以Ⅰ型扩展为主。
两线之间的区域,裂纹扩展强烈地依赖于裂纹面间的摩擦。
上限曲线的位置(对于Ⅰ型裂纹扩展的起始点)依赖于断口凸凹面相互闭锁和氧化物形成所导致的裂纹闭合,这种闭合还引起两曲线包围区内裂纹扩展的停止。
随着循环拉伸应力比的增大,裂纹闭合量下降,此时,上限曲线(虚线)开始向下限曲线(实线)靠近,当用切口裂纹代替尖锐疲劳裂纹承受复合型疲劳加载时,上限曲线和下限曲线相重合,这些结果表明了裂纹面的摩擦滑动对复合型疲劳裂纹扩展有重大影响。
图1 Ⅰ-Ⅱ复合型疲劳裂纹门槛值分布图2.2 Ⅰ-Ⅱ复合型疲劳裂纹扩展的描述如果由裂纹面接触而引起的摩擦对疲劳裂纹影响不显著的话,根据几种判据可以预测Ⅰ-Ⅱ复合型加载或Ⅱ型加载条件下的疲劳裂纹扩展路径,为了定量处理不同Ⅰ-Ⅱ复合型加载参数下的疲劳裂纹扩展路径,引入了裂纹尖端的类型复合度W m 的概念。
W m =arctg K 2K 1(1)He and Hutchinson〔2〕给出了根据最大应变能释放率理论和最大周向应力理论及裂纹沿K 2=0方向扩展这一判据所预测的裂纹开裂角随断裂类型复合度的变化曲线。
Sih 〔3〕以应变能密度因子为理论基础,提出了以最小应变能密度因子幅值作为主要参量描述复合型裂纹扩展速率,即d A /d N =8($S min )X(2)式中S min 为Ⅰ、Ⅱ、Ⅲ型应力强度因子及极角H 的函数,8、X 为材料常数。
Sih 〔3〕用这种方法对Ⅰ-Ⅱ复合型裂纹拐弯扩展阶段裂纹尖端的分析时,是用曲折成Z 字形的裂纹尖端的连线表示假想直线斜裂纹代替原来的Z 字形折线裂纹,8、X 取式2在纯Ⅰ型裂纹下得到的8、X 值,预测了Ⅰ-Ⅱ复合型裂纹扩展路径及循环次数。
还有采用投影法、广义J 积分法、最大应变法对Ⅰ-Ⅱ复合裂纹扩展速率进行研究的,得到的结果与Sih 〔3〕的结果基本相同,即Ⅰ-Ⅱ复合型疲劳裂纹的扩展方向基本满足于静载失稳情况提出的几种准则。
然而,由于Ⅰ-Ⅱ复合型疲劳裂纹扩展后裂纹面摩擦的严重影响,预测循环次数与试验结果相差较大。
到目前为止,已进行的Ⅰ-Ⅱ复合型疲劳裂纹扩展试验可以得到如下结果:(1)如果疲劳裂纹受纯Ⅱ型位移的作用,裂纹侧面总处于接触状态,因此,Ⅱ型共面裂纹的扩展最终必定停止(如图1所示两曲线之间的区域)。
试验表明,受Ⅱ型疲劳裂纹作用的试样断口上易形成磨损碎片。
由于纯Ⅱ型摩擦接触,断裂也能够通过发展Ⅰ型分叉裂纹而进行。
只有叠加拉伸载荷,闭合效应才能减少或完全消失。
(2)由于Ⅰ-Ⅱ复合型疲劳裂纹扩展受裂纹面摩擦的严重影响,裂纹扩展速率是其自身裂纹长度的函数,具有不同长度的裂纹将表现出不同的疲劳裂纹扩展特征。
如果试样含有切口而不是疲劳裂纹,那么在复合型疲劳作用下常可观察到较低的门槛值。
(3)在结构钢Ⅱ型疲劳裂纹扩展研究中,裂纹扩展的衰减来自两个因素:裂纹前缘的残余应力;断口凸凹区的相互闭锁和凸凹交错引起的严重塑性变形。
3 Ⅰ-Ⅲ复合型疲劳裂纹的扩展3.1 Ⅰ-Ⅲ复合型疲劳裂纹扩展的特征和描述电站及传动系统中的涡轮机轴及汽车的一些构件经常发生循环扭转疲劳破坏,循环扭转破坏可能沿纵向剪切面以反平面剪切(Ⅲ型方式),或者沿最大主拉应力面(与轴成±45°),以Ⅰ型方式出现。
在低应力循环时(一般小于70%屈服应力),局部Ⅰ型扩展控制着整个Ⅲ型断裂过程。
因此,以扭转断裂或者以螺旋状断口的宏观拉伸方式,即45°分叉裂纹的微观拉伸方式的发生,这导致断口上出现所谓的“工厂屋顶”形貌,在高幅循环扭转作用下,发生纯扭转裂纹扩展(沿径向),它可导致平面断口。
在低幅应力循环扭转载荷下,由于曲线裂纹路径及裂纹面间附加的摩擦接触、闭锁,使Ⅲ型或Ⅰ-Ⅲ复合型疲劳裂纹扩展的表征成为一件困难的工作。
即$K3的名义值不能唯一地表征Ⅲ型或Ⅰ-Ⅲ复合型疲劳裂纹扩展,疲劳裂纹扩展的任何名义驱动力与产生循环断裂的有效驱动力有明显的差异。
因裂纹顶端的循环位移范围的名义值($CT D)3定义简单,而常用来描述扭转疲劳特性。
所有三种类型(Ⅰ、Ⅱ、Ⅲ型)的裂纹扩展速率都可在共同尺度上进行对比。
利用循环塑性应变强度参量$#3描述了Ⅲ型疲劳裂纹扩展特性。
从本质上说,这一方法与CT D方法相同,对于线弹性脆性材料,用循环塑性应变强度参量$ 3描述Ⅲ型疲劳裂纹扩展的方法与用Ⅲ型应力强度因子K3描述疲劳裂纹扩展的方法相同。
3.2 Ⅰ-Ⅲ复合型疲劳裂纹扩展阻力的估计为了回避裂纹的闭合效应对Ⅲ型疲劳裂纹扩展的影响,通常采用两种试验方法估计Ⅲ型裂纹真实扩展速率。
T echgg〔4〕提出的第一种方法是在不同的名义“驱动力”即$K3或($CTD)3下,测量Ⅲ型裂纹扩展速率d A/ d N随裂纹长度A(或c)的变化曲线,每条曲线代表一个固定的远场循环加载水平,将它们外推到零裂纹长度,便得到了没有任何断口干扰的裂纹扩展速率。
这种方法的主要缺点是:需要在几种不同的恒定的“驱动力”即$K3或($CTD)3下分别在不同的裂纹长度下测量裂纹的扩展速率。
才能外推出远场恒定加载水平下真实扩展速率的单一值,需要的试样多,但是这种方法能明显地表明扭转疲劳断裂中裂纹扩展是如何随裂纹面干扰的加剧而降低的。
用该方法得到的Ⅲ型真实裂纹扩展速率稍高于同等CTD范围下的Ⅰ型疲劳裂纹扩展速率。
这一结果隐含着:Ⅲ型疲劳裂纹较Ⅰ型有明显高的阻力来自裂纹的闭合、自锁、摩擦效应,然而,由于没有考虑到裂纹曲折路径对Ⅲ型裂纹顶端应力场的影响以及闭合对Ⅰ型裂纹扩展速率的影响,该推断未得到充分的试验证实。
T scheg g和Suresh 曾经运用这种外推法得到的真实断裂阻力来估计摩擦滑动对4340钢(200℃回火)Ⅲ型裂纹断裂韧性的影响,发现环形缺口圆柱试样(直径19m m)的疲劳预制裂纹深度从0.2mm增到1.2m m,其Ⅲ型裂纹断裂韧性约增加1倍。
第二种方法的目的是降低扭转疲劳中断裂表面干扰的复杂性,它的循环扭转载荷上叠加一静拉伸载荷,以便将闭锁的凸凹断口分离。
T schegg〔4〕进行了纯Ⅲ型裂纹加载和在Ⅲ型裂纹加载上叠加一静拉伸载荷(K1=6~11M Pa・m1/2)的扩展速率对比试验,表明:利用这一技术,在某些条件下,即便施加小的静拉伸载荷,也会因降低闭合程度而使Ⅲ型疲劳裂纹扩展速率明显增加。
使断口完全分离的拉伸载荷是材料性能、循环扭转载荷幅和裂纹扩展微观机制的函数,对于高强度材料,需要相当大的拉伸载荷来消除裂纹面的接触。
然而叠加如此大的拉伸载荷来消除裂纹面的接触,会导致裂纹顶端处于强烈的复合型状态,目前,还没有能够唯一表征复合型裂纹扩展的可靠方法,虽然在Ⅲ型疲劳裂纹加载上施加即使很小的静拉伸载荷,就可以减小Ⅲ型疲劳裂纹的闭合效应,而使Ⅲ型疲劳裂纹扩展速率明显增加,然而其增加的速度却明显低于纯Ⅲ型疲劳裂纹扩展速率的增加速度。
4 复合型裂纹的脆性断裂准则现有的复合型裂纹断裂准则可分为两大类:一是以裂纹尖端的应力-应变场为基础;二是基于能量平衡观点的能量理论,以裂纹尖端的应力-应变场为基础的断裂准则,又可分为以裂纹尖端应力为参量的复合型裂纹断裂准则和以裂纹尖端应变为参量的断裂准则。
所有的这些准则都假定裂纹开裂扩展将沿着以裂纹尖端为中心的射线方向,并且在此方向的某个函数存在着一个极值,当此极值达到临界值时,裂纹开始失稳扩展。
4.1 复合型裂纹脆性断裂的应力准则以应力为参量的断裂准则主要为最大周向应力准则〔R H〕max准则。
60年代Erdogan和Sih继承了历史上宏观最大正应力理论思想,提出了复合型裂纹的最大周向应力准则:裂纹沿R H最大的方向扩展;当R H在此方向上取得极值时,裂纹开裂。
此准则的缺点在于: (1)R H具有奇异性,当r→0时,R H→∞;(2)该准则没有综合考虑其它应力分量的作用;(3)不能将平面应力和平面应变问题区分开来。
薛大为〔5〕建议考虑裂纹尖端附近等S r H线上取最大周向应力点,裂纹将由其尖端沿指向此点的方向开裂,开裂条件为:沿此方向的周向应力达到某临界值。
也有人建议将裂纹尖端附近等应变密度线上的R H作为参量,假定裂纹沿等应变能密度线上最大周向应力的方向开裂,则在此方向上取得极值作为开裂条件。