强度课实验——临界转速测试实验报告
整理后数据报告..2

转子实验报告(图)实验一:测量转子临界转速实验目的:探究使用转子转动的振幅-转速曲线、轴心轨迹、波形图等判断并找出转子临界转速。
实验仪器:1. INV1612 型多功能柔性转子实验台及各种振动传感器 2.INV1612U型采集分析系统实验原理:(1)转子转动角速度数值上与转轴横向弯曲振动固有频率相等。
(2)转子在临界转速附近转动时,转轴的振动明显变得剧烈,即处于“共振”状态,转速超过临界转速后的一段速度区间内,运转有趋于平稳。
所以通过观察转轴振动振幅-转速曲线可以测量临界转速。
(3)轴心轨迹再通过临界转速时,长短轴发生明显变化,所以通过观察轴心X-Y图中振幅-相位变化,可以判断临界转速。
测量和分析参数通道数: 11 ; 采样频率: 4091.91Hz ; dt: 0.244385ms数字跟踪滤波设置:基频1X 带通滤波通道参数:(1)为了排除转子在不同速度提升下对临界转速时轴心、波形,振幅等图形的影响,本次实验采用在不同提升速度状态下观察分析图形,然后由图形找出转子的临界速度。
(2)本次实验也要讨论分析转轴的负重位置对临界转速的影响,以下实验过程将对上述条件做分别讨论。
******负重盘在转轴的中间位置时《一》缓慢提升速度:(1)振幅-转速曲线:由图形及数据采集仪得到的数据(图形右侧)得当转速达到3100r/min时转子振幅达到最大值0.024um(即可以判断出转子的临界转速为3100r/min(2)临界速度轴心轨迹:由轴心轨迹再通过临界转速时转轴的水平和竖直位移发生明显变化,所以通过观察轴心X-Y图(上图)可以判断临界转速3098r/min(图形右侧标示栏)(3)临界速度前轴心轨迹:(4)临界速度后轴心轨迹:从上述(3)、(4)两幅图可以看出转轴在临界转速前后的轴心位置偏移明显比临界转速时的轴心轨迹要小。
(5)临界速度波形图:Ch2:转轴水平位移X(um)Ch3:转轴垂直位移Y(um)Ch4:实验台水平位移X(um)Ch5:实验台垂直位移Y(um)《二》快速提升速度:(1)振幅-转速曲线:观察快速提升速度时的转速-幅值曲线与缓慢提速时对应图形基本相同,本图所读出临界转速为3120r/min 。
试验回转转子临界转数测定

回转转子临界转数测定实验一、实验目的:1、感性的了解轴的转动及临界转速的现象,并仔细观察转轴通过临界转速时的情况。
2、实验带有单转子轴的临界转速以及轴长度的变化与临界转速的关系,并和理论计算值进行比较。
3、掌握临界转速的测试方法。
4、分析影响轴的临界转速的各种原因。
5、测试并绘出实验转子的一阶,二阶振型曲线,了解转子在临界速度时的变形情况。
二、基础原理:临界转速的理论基础是震动理论,因为任何体系都有其自振频率。
单转子的轴,当其参 数( 指轴的长度,转子重量等)固定后,它的自振频率也是个定值。
迥转机械由于设计、制造和安装的欠妥,致使转子的重心与其转轴的中心不从合(即是有一微小的偏心),若此轴以角速度ω 旋转时,由于转子产生附加给轴的离心力(周期性变化的干扰力),而产生强迫振动,当强迫振动的频率正好与其轴的自振频率相等,系统的振动显得十分剧烈,此时产生共振现象。
由振动理论知道,机器振动的振幅(值)随转速的升高而加大,当达到临界转速时,振幅将变为最大,在理论上振幅达到无穷大,但事实上迥转系统存在阻尼(如轴承油膜阻尼以及转子与周围空气摩擦等),故即使在到达临界转速这一瞬间时,振幅亦不可能达到无穷大,只能为某一数值较大的振幅值。
这种现象在工程上称为共振,在机器发生共振时的转速,称为临界转速。
轴的临界转速,可以根据理论公式求出。
对于简支的单转子而且转子在其轴中间时,临界转速可按下式计算:(1)两端简支结构形式: 22)(3a L ma EJL k -=ω式中:E :轴的弹性模量(210GPa )J :轴惯性矩644d J π=m :转子的质量(千克) 轴的临界转速为πωkk n 30= (rpm )(2)一端悬臂结构形式:2)(3a a L m EJ k +=ω式中:E :轴的弹性模量(E=210GPa )J :轴的惯性矩644d J π=m :转子的质量(千克) 轴的临界转速为πωk K n 30=(rpm )三、实验装置本实验装置参见图轴安装在装有含油的滑动轴承支架上,在轴端安装一转子。
单圆盘转子的临界转速测定
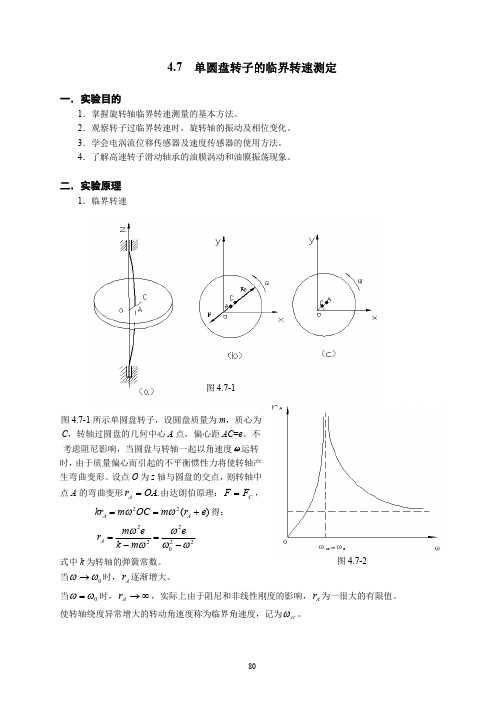
4.7 单圆盘转子的临界转速测定一.实验目的1.掌握旋转轴临界转速测量的基本方法。
2.观察转子过临界转速时,旋转轴的振动及相位变化。
3.学会电涡流位移传感器及速度传感器的使用方法。
4.了解高速转子滑动轴承的油膜涡动和油膜振荡现象。
二.实验原理1.临界转速图4.7-1所示单圆盘转子,设圆盘质量为m ,质心为C ,转轴过圆盘的几何中心A 点,偏心距AC =e 。
不考虑阻尼影响,当圆盘与转轴一起以角速度ω运转时,由于质量偏心而引起的不平衡惯性力将使转轴产生弯曲变形。
设点O 为z 轴与圆盘的交点,则转轴中点A 的弯曲变形.OA r A =由达朗伯原理:C F F =,)(22e r m OC m kr A A +==ωω得: 220222ωωωωω-=-=em k e m r A (4.7-1) 式中k 为转轴的弹簧常数。
当0ωω→时,A r 逐渐增大。
当0ωω=时,∞→A r ,实际上由于阻尼和非线性刚度的影响,A r 为一很大的有限值。
使转轴绕度异常增大的转动角速度称为临界角速度,记为cr ω。
图 4.7-2图4.7-1。
mk cr ==0ωω (4.7-2)即它等于系统的固有频率。
此时转速称为临界转速,记为cr n 。
当cr ωω>时,实践证明,质心C 位于OA 之间,如图(4.7-1)(c )所示:这时e r OC A -=,A A kr e r m =-)(2ω,所以:202222ωωωωω-=-=ek m e m r A (4.7-3)↓↑A r ,ω。
当0ωω>>时,e r A ≈。
这时质心C 与轴心点O 趋于重合,即圆盘绕质心C 转动,这种现象称为自动定心现象。
2.相位突变转子在升速运行时,当转速达到临界装速时,转轴的振动位移与激励力之间的相位角会发生突变,此时轴心轨迹的李萨育图(椭圆)会达到最大并突然转向。
3.滑动轴承的油膜涡动和油膜振荡高速转子在临界转速以上工作时,由于滑动轴承中油膜的作用,使转轴在某特定转速下产生回旋,引起轴承和转子系统的强烈振动,称为油膜振荡。
旋转机械转速,角速度及转轴横向位移测量实验报告

旋转机械转速,角速度及转轴横向位移测量实验报告(文章一):振动位移转速在旋转机械中的测量振动位移转速在旋转机械中的测量(一)、振动位移的测量原理(1)、传感器原理机器的振动、位移总是伴随着机器的运转,即使是机器在最佳的运动状态,由于很微小的缺陷,也将产生某些振动。
在工作中我们常用的振动位移监测仪是由电涡流传感器、前置器、延伸电缆、监测仪转换器组成,其构成原理如图所示。
探头线圈接受前置器振荡电路来的高频电流,在其周围产生高频磁场,该磁场穿过靠近它的转轴金属表面,在其中产生一个电涡流,该电涡流产生的磁场方向和线圈磁场方向相反,改变了原线圈的感抗,该感抗的变化随探头顶部金属表面的间隙变化而变化。
前置器检测电路检测探头线圈的感抗变化。
再经放大电路将感抗变化量变换放大成相应电压变化信号输出。
经监测仪进行信号转换并显示,转换成4~20mA,1~5V的标准信号送入DCS或PLC中,在测量中,前置器放大输出的直流电压信号用做机械位移的测量,交流电压信号用做振动的测量。
(2)、机械量测量原理由于机械物体振动量的大小可以用振动的基本参量——位移、速度、加速度来表述。
对于简谐振动来说,用如下数学表达式来确定各参量之间的关系:X=XmSin(ωt+φ) 式中X——位移,即物体振动时相对于基准位置的位置变化(其最大的位置变化称为振幅,即式中的Xm,单位为μm);t——时间;ω——圆频率;φ——初始相角,根据上图的机械实际变化量,电涡流传感器能够真实地把它反映到输出电压变化上,并根据量值对振动进行指示。
如传感器特性为7.87V/mm,V峰-峰=78.7mv则此时振动值应为10μm,但在实际工作时我们用万用表测量的交流电压是有效值,必须进行换算,就有如下公式:振动值=交流毫伏值x2.828/7.87(此式在处理故障时非常实用)对实际测量产生的振动量,转换前进行计算,确定量值,比对转换器输出。
机械位移主要是指轴的轴向移动量,根据电涡流传感器的工作原理,感抗的变化随探头与顶部金属表面的间隙变化而变化,正是利用这点,我们对轴位移量进行测量。
结构强度与振动试验报告
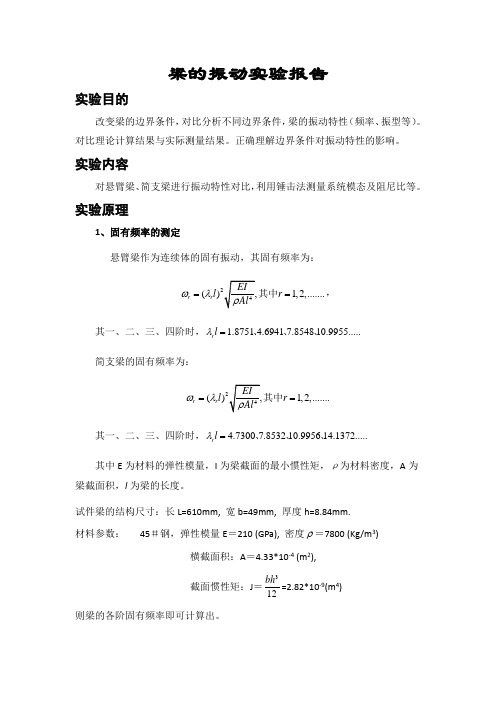
梁的振动实验报告实验目的改变梁的边界条件,对比分析不同边界条件,梁的振动特性(频率、振型等)。
对比理论计算结果与实际测量结果。
正确理解边界条件对振动特性的影响。
实验内容对悬臂梁、简支梁进行振动特性对比,利用锤击法测量系统模态及阻尼比等。
实验原理1、固有频率的测定悬臂梁作为连续体的固有振动,其固有频率为:()1,2,.......r r l r ωλ==其中, 其一、二、三、四阶时, 1.87514.69417.854810.9955.....r l λ=、、、 简支梁的固有频率为:()1,2,.......r r l r ωλ==其中 其一、二、三、四阶时, 4.73007.853210.995614.1372.....r l λ=、、、 其中E 为材料的弹性模量,I 为梁截面的最小惯性矩,ρ为材料密度,A 为梁截面积,l 为梁的长度。
试件梁的结构尺寸:长L=610mm, 宽b=49mm, 厚度h=8.84mm. 材料参数: 45#钢,弹性模量E =210 (GPa), 密度ρ=7800 (Kg/m 3)横截面积:A =4.33*10-4 (m 2),截面惯性矩:J =312bh =2.82*10-9(m 4)则梁的各阶固有频率即可计算出。
2、实验简图图1 悬臂梁实验简图图2简支梁实验简图实验仪器本次实验主要采用力锤、加速度传感器、YE6251数据采集仪、计算机等。
图3和图4分别为悬臂梁和简支梁的实验装置图。
图5为YE6251数据采集仪。
图3 悬臂梁实验装置图图4 简支梁实验简图图5 YE6251数据采集分析系统实验步骤1:"在教学装置选择"中,选择结构类型为"悬臂梁",如果选择等份数为17,将需要测量17个测点。
2:本试验可采用多点激励,单点响应的方式,如果是划分为17等份,请将拾振点放在第5点。
3:请将力锤的锤头换成尼龙头,并将力通道的低通滤波器设置为1KHz,将拾振的加速度通道的低通滤波器设置为2KHz。
临界浓度测定实验报告

一、实验目的1. 理解临界浓度(CMC)的概念及其在表面活性剂溶液中的重要性;2. 掌握测定表面活性剂溶液临界浓度的实验原理和方法;3. 通过实验,学会使用表面张力法和电导法测定表面活性剂溶液的临界浓度。
二、实验原理临界浓度(CMC)是指表面活性剂溶液中,表面活性剂分子开始形成胶束的最低浓度。
在CMC以下,表面活性剂分子主要分散在溶液中,而当浓度超过CMC时,表面活性剂分子会自相缔合形成胶束。
胶束的形成会导致溶液性质发生显著变化,如表面张力、溶解度、电导率等。
表面张力法:通过测定溶液表面张力随浓度变化的关系,找到曲线的转折点,即可确定CMC。
电导法:通过测定溶液电导率随浓度变化的关系,找到曲线的转折点,即可确定CMC。
三、实验仪器与试剂1. 仪器:表面张力仪、电导率仪、超级恒温槽、移液管、容量瓶、滴定管等。
2. 试剂:表面活性剂(如十二烷基硫酸钠、十二烷基苯磺酸钠等)、蒸馏水、氯化钠等。
四、实验步骤1. 准备溶液:按照实验要求,配制一系列不同浓度的表面活性剂溶液。
2. 表面张力法测定CMC:(1)使用表面张力仪测定不同浓度溶液的表面张力;(2)以表面张力为纵坐标,以浓度为横坐标,绘制曲线;(3)找到曲线的转折点,即为CMC。
3. 电导法测定CMC:(1)使用电导率仪测定不同浓度溶液的电导率;(2)以电导率为纵坐标,以浓度为横坐标,绘制曲线;(3)找到曲线的转折点,即为CMC。
4. 结果分析:比较两种方法得到的CMC值,分析误差来源。
五、实验结果与分析1. 表面张力法测定的CMC:以十二烷基硫酸钠溶液为例,实验得到的CMC为0.002 mol/L。
2. 电导法测定的CMC:以十二烷基硫酸钠溶液为例,实验得到的CMC为0.003mol/L。
两种方法得到的CMC值存在一定差异,可能是由于实验条件、试剂纯度等因素的影响。
六、实验总结1. 通过本实验,掌握了表面活性剂溶液临界浓度的测定方法,了解了CMC在表面活性剂溶液中的重要性。
临界比例度实验报告
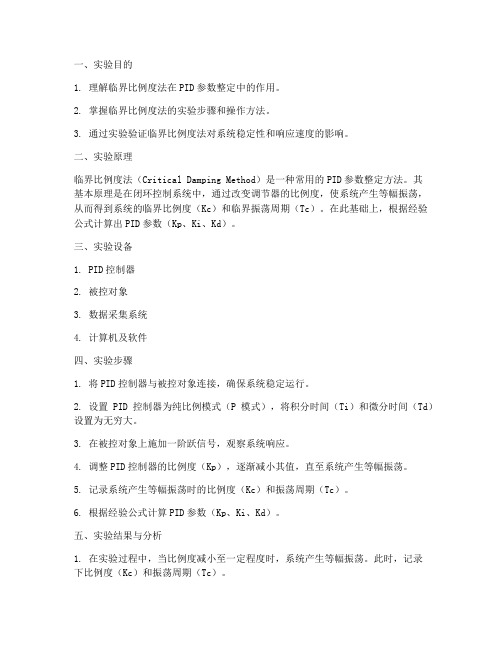
一、实验目的1. 理解临界比例度法在PID参数整定中的作用。
2. 掌握临界比例度法的实验步骤和操作方法。
3. 通过实验验证临界比例度法对系统稳定性和响应速度的影响。
二、实验原理临界比例度法(Critical Damping Method)是一种常用的PID参数整定方法。
其基本原理是在闭环控制系统中,通过改变调节器的比例度,使系统产生等幅振荡,从而得到系统的临界比例度(Kc)和临界振荡周期(Tc)。
在此基础上,根据经验公式计算出PID参数(Kp、Ki、Kd)。
三、实验设备1. PID控制器2. 被控对象3. 数据采集系统4. 计算机及软件四、实验步骤1. 将PID控制器与被控对象连接,确保系统稳定运行。
2. 设置PID控制器为纯比例模式(P模式),将积分时间(Ti)和微分时间(Td)设置为无穷大。
3. 在被控对象上施加一阶跃信号,观察系统响应。
4. 调整PID控制器的比例度(Kp),逐渐减小其值,直至系统产生等幅振荡。
5. 记录系统产生等幅振荡时的比例度(Kc)和振荡周期(Tc)。
6. 根据经验公式计算PID参数(Kp、Ki、Kd)。
五、实验结果与分析1. 在实验过程中,当比例度减小至一定程度时,系统产生等幅振荡。
此时,记录下比例度(Kc)和振荡周期(Tc)。
2. 根据经验公式计算PID参数(Kp、Ki、Kd):- Kp = Kc 0.6- Ki = Kc 0.5 Tc- Kd = Kc 0.1 Tc^23. 将计算得到的PID参数输入PID控制器,观察系统响应。
4. 分析实验结果,验证临界比例度法对系统稳定性和响应速度的影响。
六、实验结论1. 临界比例度法是一种有效的PID参数整定方法,能够快速、准确地得到系统稳定的PID参数。
2. 临界比例度法对系统稳定性和响应速度有显著影响,通过调整PID参数,可以优化系统性能。
3. 实验过程中,应严格控制实验条件,确保实验结果的准确性。
七、实验改进1. 可以尝试不同类型的被控对象,验证临界比例度法的适用范围。
临界转速测量
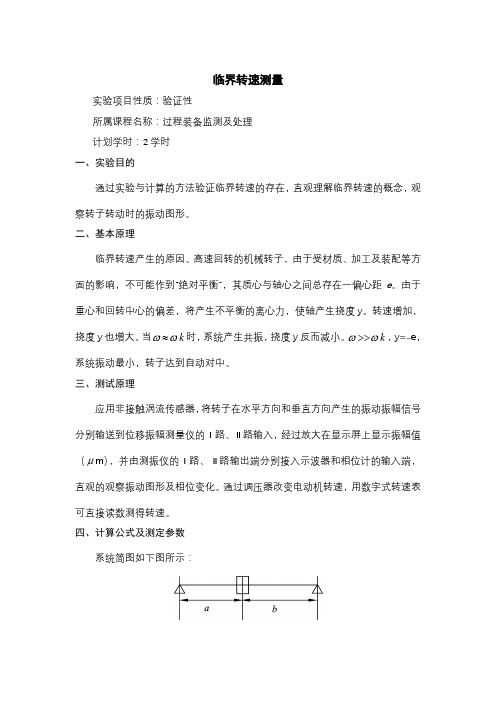
临界转速测量实验项目性质:验证性所属课程名称:过程装备监测及处理 计划学时:2学时 一、实验目的通过实验与计算的方法验证临界转速的存在,直观理解临界转速的概念,观察转子转动时的振动图形。
二、基本原理临界转速产生的原因。
高速回转的机械转子,由于受材质、加工及装配等方面的影响,不可能作到“绝对平衡”,其质心与轴心之间总存在一偏心距e 。
由于重心和回转中心的偏差,将产生不平衡的离心力,使轴产生挠度y 。
转速增加,挠度y 也增大。
当k ωω≈时,系统产生共振,挠度y 反而减小。
k ωω>>,y=-e ,系统振动最小,转子达到自动对中。
三、测试原理应用非接触涡流传感器,将转子在水平方向和垂直方向产生的振动振幅信号分别输送到位移振幅测量仪的Ⅰ路、Ⅱ路输入,经过放大在显示屏上显示振幅值(μm ),并由测振仪的Ⅰ路、Ⅱ路输出端分别接入示波器和相位计的输入端,直观的观察振动图形及相位变化。
通过调压器改变电动机转速,用数字式转速表可直接读数测得转速。
四、计算公式及测定参数系统简图如下图所示:轴的临界转速为:min /30r mkn e π=其中:223 EJLK a b =N/m 式中:E —轴材料的弹性摸量 72.110E =⨯N/cm 2 J —轴的惯性矩 ()44cm 64取平均值d d J π=1.测量结果:d = cm b = cm m = Kg L =a +b cm2.计算结果:J = cm 4 K = N/m N e= r/min五、实验装置图3 实验装置示意图实验装置:由调压器、试验台底座、电机、含油轴承支座、接油盘、传感器支座、圆盘、轴、传感器、位移测量仪、示波器等组成。
六、实验步骤1.临界转速测定(1)装好转轴及圆盘,并检查各螺钉,特别要注意联轴器的顶丝和圆盘的顶丝要顶紧轴,两圆盘的顶丝应错开90°,防止发生事故。
检查并调整传感器端面与轴间的距离为1mm左右,将各仪表按图3所示接线。
- 1、下载文档前请自行甄别文档内容的完整性,平台不提供额外的编辑、内容补充、找答案等附加服务。
- 2、"仅部分预览"的文档,不可在线预览部分如存在完整性等问题,可反馈申请退款(可完整预览的文档不适用该条件!)。
- 3、如文档侵犯您的权益,请联系客服反馈,我们会尽快为您处理(人工客服工作时间:9:00-18:30)。
实验三转子临界转速测量实验
一. 实验目的
1. 观察转子在亚临界、临界及超临界的工作情况。
2. 计算转子的理论临界转速,并与实测值作比较
3. 分析研究在实验中产生的各种物理现象,了解影响转子临界转速
的各种因素。
4. 熟悉实验设备及其操作方法;熟悉软件应用。
二.
实验装置及测试框图
三. 实验原理
电涡流位移传感器盘
支承支承
轴
联轴器
光电转速传感器电动机底座
图1
图1为临界转速实验装置示意图,其结构为单盘转子以简支形式支承在滑动轴承上。
实验圆盘安装在轴的跨度中间。
整个转子由变速电动机带动旋转,电动机的转速通过调压变压器控制,可无级变速。
转速测量:本实验系统采用的是光电转速传感器,在转轴上贴有反光条,转轴每转动一周光电转速传感器感应一个脉冲。
此脉冲就是键相位,反光条所在的位置就是振动相位零角度对应的实际位置。
同时,转速脉冲信号输入测量系统的转速输入通道用于转速测量。
转速的测量可以通过计数器测量单位时间内键相位脉冲的个数得到(计数法),可以测量2个键相位脉冲之间的时间T得到(测周期法)。
振动传感器:旋转机械的振动测量有多种传感器,其中电涡流传感器为非接触式,用于直接测量旋转轴的振动位移。
振动测量模块可以给电涡流振动位移传感器提供工作电源、对反馈的振动信号进行测量、分析。
等角度数据采集:不同于一般数据采集系统的是旋转机械的振动数据采集必须保证等角度,即:在转子的每个转动周期T内采集Kph 个数据,称之为等角度采样或称整周期采样。
轴心轨迹:旋转机械振动实验的一个突出特点。
在旋转轴的水平、
垂直两个方向分别安装
两只互相垂直的位移传
感器,两路信号分别输入
示波器的X、Y轴,可以
合成显示转轴轴心的运
转轨迹。
实验中采用软件中的重采样时间波形,即可看到转子轴心轨迹。
四.实验步骤
1.测量参数设置
分析模式:瞬态
阶次上限:64X
阶次分辨率:0.125X
转速控制:通过转速控制数据采集的进行
起始转速:1000rpm
结束转速:6000rpm(应大于临界转速)
转速间隔:50rpm
显示阶次:1X (显示工频振动)
测量通道参数设置
测量通道各参数见下图
信号选择
见下图的信号选择对话框,选择需要显示的信号类型。
调出Bode 图的相频曲线首先建立显示Bode
图的幅频曲线窗口
在Bode 图窗口中点
击鼠标右键,选择“图
形属性”弹出右边的对
话框。
进入“坐标”,在右下“Y轴”选项下拉菜单
中选择“相频”
显示转速
由主菜单“显示”中选择“转速显示”,调出转速显示框,显示框大小、位置可调整。
测试
由主菜单“控制”中选择“启动采样”,进入数据采集。
下右图所示的测试界面分别显示了重采样波形、阶次谱、Bode 相频
曲线、Bode 幅频曲线
五. 数据处理
原始数据:m 盘=800g ,d=(9.4+9.5+9.6)/3=9.5mm ,l=24.0cm 1.
无盘有重轴的临界转速轴cr ω
4
64d J π
=4)3-9.5x1064
(π
==3.998x10-10m 4
2
d
A π=4=7.09x10-5 m 2
ρπωA EJ l 22
=
轴cr 7800
)5
-(7.09x1010
-x3.998x109210x100.242
2X π=
=2111.24rad/s
2.
单盘无重轴的临界转速盘cr ω
3
l 48EJ
c =
3
(0.24)
)
10
-0)x(3.998x19-48x(210x10=
=2.915x105 N/m 2
盘
盘m c
=
cr ω0.8
5
2.915x10
=
=603.65 rad/s
3.
单盘均质轴转子的临界转速cr ω
2
cr 2cr 2cr
1
1
1
盘轴
ωωω+
=
2
22
cr
5.66031
4.2211111
+
=
ω
w cr =580.4 rad/s
cr cr n ωπ
30
=
rpm .35542=
六. 实验数据记录表和实验曲线
转
速 3500 4000 4500 4700 4900 5000 5100 5300 5500 扰
度
351 543 1032 1721 3098 2580 1268 412 289
七.误差产生的原因及实验中的异常现象。
1、根据顿克公式计算的值本应该低于精确值,而本实验的计算值
却高于实际测得的值,可能的原因是装置放置导致该系统本身
的刚性降低,使得实际测得值降低。
2、数据采集的软件做得不精确,数据采集不精准,使得测得的数
值偏小。
3、计算数值的原始数据获得过程有很大的误差,使得计算数值偏
高。
4、系统本身存在缺陷,在实验过程中,输出电流过大,电动机承
载过大,使得实际测到的临界转速上不去,所以测得的值偏小。
5、设施设备使用次数太多,造成材料本身存在缺陷,这样实验的
误差就更大了。