汽车工艺设计及验证
整车设计流程实验报告

整车设计流程实验报告1. 引言整车设计是汽车工程领域中的重要部分,它涵盖了各个方面,包括车身结构设计、动力系统设计、底盘系统设计等。
本实验旨在通过模拟整车设计流程,了解并学习汽车设计的基本原理和方法。
2. 实验目的1. 掌握整车设计的基本流程;2. 熟悉汽车设计中的关键点和参数;3. 学习使用相关设计软件进行汽车设计。
3. 实验流程3.1 需求调研与概念设计首先,我们对整车的市场需求和技术指标进行调研,了解用户的需求以及竞争对手的产品特点。
在此基础上,进行概念设计,确定整车的大致结构和零部件组成。
3.2 三维建模与总体设计根据概念设计的结果,使用三维建模软件对整车的外观和内部结构进行细化设计。
通过进行总体设计,确定车身尺寸、车轮布局、底盘结构等。
3.3 零部件设计与模拟分析在总体设计的基础上,开始对各个零部件进行详细设计。
使用CAD软件绘制零部件的结构图,并进行模拟分析,例如强度分析、流体仿真等。
3.4 配置参数的确定与优化根据各个零部件设计的结果,结合市场需求进行配置参数的确定与优化。
例如发动机的功率、车身的重量、悬挂系统的刚度等。
3.5 整车性能仿真与优化将各个零部件的设计参数整合到整车模型中,进行整车性能仿真与优化。
通过模拟不同工况和驾驶条件下的性能表现,并对设计进行调整和优化。
3.6 制造工艺设计与试制根据设计结果,进行制造工艺的设计与优化。
确定零部件的加工工艺和装配工艺,制定试制计划并进行试制。
3.7 试验验证与改进根据试制结果进行试验验证。
通过对整车的各项性能指标进行测试,发现问题并进行改进,直至满足设计要求。
4. 结果与讨论通过本实验,我们成功完成了整车设计流程的模拟。
在需求调研与概念设计阶段,我们充分了解了整车设计的市场需求和技术指标。
通过三维建模与总体设计,我们确定了整车的结构和零部件布局。
通过零部件设计与模拟分析,我们对各个零部件的强度和流体特性进行了分析。
在配置参数的确定与优化过程中,我们根据市场需求对整车进行了参数配置和优化。
工艺验证的内容和分类

工艺验证的内容和分类
工艺验证是通过对现有工艺的技术标准进行实际测试和确认,以提高工
艺质量水平、优化设计过程,以满足相关安全要求为目的的一种技术检验活动。
工艺验证分为安全性验证和可行性验证两大类:
一、安全性验证:安全性验证是指验证工艺设计是否符合国家、行业标
准和规范,以预防工艺搞错等问题,提高工艺质量水平。
二、可行性验证:可行性验证是指验证工艺设计的可实施性,包括原料、工人技能、仪器设备等,以及与安全要求、效率等对比,确认工艺设计是否
合理可行。
在工艺验证中,还应严格按照行业标准和国家MAP的规定来条例、调整、规划,保证工艺安全可靠、提高可行性,有效优化和促进生产经营。
从上述可以看出,工艺验证是保障工艺安全可靠、提高可行性的一项重
要活动,质量验证、成本分析、技术规定实施、安全性验证、可行性验证等
都是需要加以考虑的因素,必须按照国家、行业有关法律法规严格要求,不
断加强安全可靠性保障,始终坚持严格执行质量标准,保证工艺验证质量。
汽修工艺管理制度
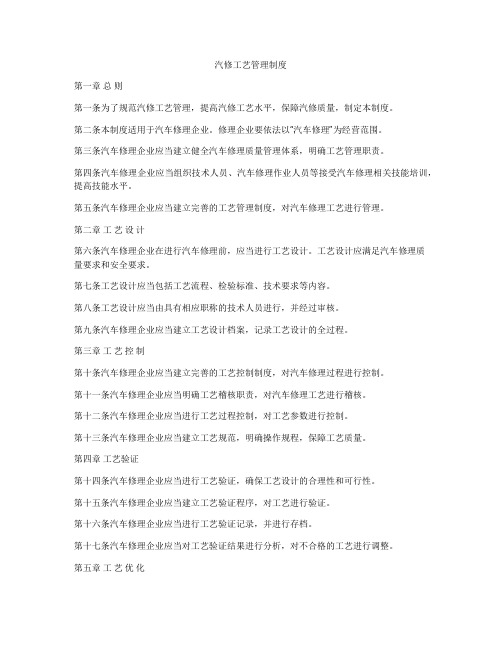
汽修工艺管理制度第一章总则第一条为了规范汽修工艺管理,提高汽修工艺水平,保障汽修质量,制定本制度。
第二条本制度适用于汽车修理企业。
修理企业要依法以“汽车修理”为经营范围。
第三条汽车修理企业应当建立健全汽车修理质量管理体系,明确工艺管理职责。
第四条汽车修理企业应当组织技术人员、汽车修理作业人员等接受汽车修理相关技能培训,提高技能水平。
第五条汽车修理企业应当建立完善的工艺管理制度,对汽车修理工艺进行管理。
第二章工艺设计第六条汽车修理企业在进行汽车修理前,应当进行工艺设计。
工艺设计应满足汽车修理质量要求和安全要求。
第七条工艺设计应当包括工艺流程、检验标准、技术要求等内容。
第八条工艺设计应当由具有相应职称的技术人员进行,并经过审核。
第九条汽车修理企业应当建立工艺设计档案,记录工艺设计的全过程。
第三章工艺控制第十条汽车修理企业应当建立完善的工艺控制制度,对汽车修理过程进行控制。
第十一条汽车修理企业应当明确工艺稽核职责,对汽车修理工艺进行稽核。
第十二条汽车修理企业应当进行工艺过程控制,对工艺参数进行控制。
第十三条汽车修理企业应当建立工艺规范,明确操作规程,保障工艺质量。
第四章工艺验证第十四条汽车修理企业应当进行工艺验证,确保工艺设计的合理性和可行性。
第十五条汽车修理企业应当建立工艺验证程序,对工艺进行验证。
第十六条汽车修理企业应当进行工艺验证记录,并进行存档。
第十七条汽车修理企业应当对工艺验证结果进行分析,对不合格的工艺进行调整。
第五章工艺优化第十八条汽车修理企业应当对工艺进行优化,提高工艺水平。
第十九条汽车修理企业应当建立工艺改进制度,对工艺进行改进。
第二十条汽车修理企业应当对工艺进行持续改进,提高汽车修理质量。
第六章工艺管理第二十一条汽车修理企业应当建立工艺管理制度,明确工艺管理职责。
第二十二条汽车修理企业应当进行工艺管理,制定工艺管理程序。
第二十三条汽车修理企业应当建立完善的工艺管理档案,记录工艺管理的全过程。
工艺验证报告

□焊装专用、通用工辅具配备不齐全,不满足生产需求,详见[焊装生产用工具明细表]。
□涂装专用、通用工辅具配备齐全,满足生产需求。
□涂装专用、通用工辅具配备不齐全,不满足生产需求,详见[涂装生产用工具明细表]。
□总装专用、通用工辅具配备齐全,满足生产需求。
□总装专用、通用工辅具配备不齐全,不满足生产需求,详见[总装生产用工具明细表]。
□总装线不存在通过受制约问题,通过性满足产品要求。
□总装线存在通过受制约问题,通过性不满足产品要求,具体问题为等工位,其中可以改造后满足要求的有个工位,无法改造的有个工位,详见[总装通过性验证记录表]。
(五)、生产节拍验证:
本次验证冲压模具共套,单批压制件以上达到稳定状态的有套,仍不能达到稳定状态的有套,需改进后再次验证,详见[冲压模具验证记录表]。
□总装生产线节拍达不到工艺设计要求,不能满足批量生产,瓶颈工位为,需进行改进或调整。
(六)、制造装配一致性、零部件一致性验证:
焊装生产线本项目产品共用个冲压件,其中件一致性有保证,车身焊接稳定,一致性好,件一致性没有保证,焊接后需人工修整,影响焊接质量和节拍,详见[焊装冲压件验证记录表]。
□涂装用车身表面质量稳定,一致性好,满足涂装线生产要求。
总装共需 种,本次验证 种,合格满足使用要求的 种,需进行改进的 种,详见[总装工位器具验证记录表]。
5、检具:
冲压件检具共 套,本次本次验证 套,合格满足使用要求的 套,需进行改进的 套,详见[冲压件检具验证记录表]。
焊装共需检具 套,本次验证 套,合格满足使用要求的 套,需进行改进的 套,详见[焊装检具验证记录表]。
□焊装生产线节拍达到工艺设计要求,可以满足批量生产。
汽车SOP量产-工艺验证报告(参考)
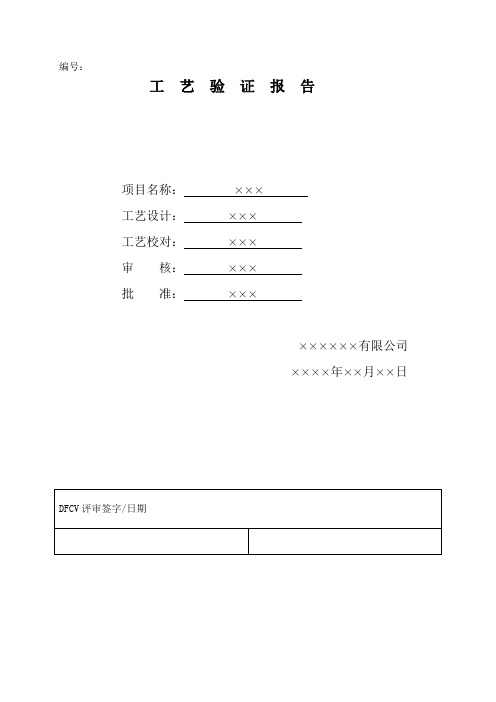
规格
数量
实际数量
备注(是否符合)
1
××
××
××
××
××
2
××
××
××
××
××
3
××
××××Biblioteka ××××4
××
××
××
××
××
5
××
××
××
××
××
6
××
××
××
××
××
7
××
××
××
××
××
8
××
××
××
××
××
9
××
××
××
××
××
10
××
××
××
××
××
11
××
××
××
××
××
12
….
….
….
….
编号:
工 艺 验 证报 告
项目名称:×××
工艺设计:×××
工艺校对:×××
审 核:×××
批 准:×××
××××××有限公司
××××年××月××日
DFCV评审签字/日期
项目名称
×××工艺验证
产品名称
××××
工序名称
××××
工艺验证内容及结论
1、产品质量:
工艺完成后产品要求及检测结果如下:
检测项目
检测要求
5、工装夹具验证情况:
工装夹具验证结果满足产品加工要求。
6、××个零件试装数据报告:
检测项目
检测要求
实际次数
实测结果合格率
不合格数
备注
汽车制造工程管理规范解读

汽车制造工程管理规范解读在汽车制造领域,为了保持生产过程高效、质量稳定,确保汽车制造符合行业标准和客户需求,制定了一系列的管理规范。
本文将对其中的几项重点规范进行详细解读,包括质量管理规范、工程管理规范和安全管理规范。
一、质量管理规范汽车制造的核心目标是提供高质量的汽车产品。
质量管理规范旨在确保整个生产过程的可控性和稳定性,以减少缺陷率、提高产品质量。
以下是几项质量管理规范的要点解读:1.1质量控制计划(QCP):质量控制计划是针对汽车制造过程中的关键质量特性和控制点制定的一份文件,它包括了质量目标、控制点和控制措施等内容。
制定QCP的目的是建立起一套科学的质量控制措施,确保每个制造过程都能达到既定的质量标准。
1.2质量检验标准(QIS):质量检验标准是制定产品检验流程及标准的指导文件。
通过制定详细的检验标准,包括外观缺陷、功能性测试等方面,可以确保每个生产步骤得到正确执行,从而提高产品质量的一致性。
1.3不合格品控制程序(NQP):不合格品控制程序规定了对于发现的不合格品的处理流程。
它涉及到对不合格品的分类、处理和纠正措施等,以确保不合格品不会流入市场并影响消费者的使用体验。
二、工程管理规范工程管理规范针对的是制造过程中的工程活动,包括工艺设计、设备管理、产品验证等方面。
通过执行工程管理规范,可以有效控制生产进度、保证产品质量,并提高制造过程的效率。
以下是几项工程管理规范的重点解读:2.1工艺设计规范:工艺设计规范是针对汽车制造中的工艺流程和工艺参数制定的一份指导文件。
它包括了产品加工流程、设备选型、工艺控制等方面,以确保产品能够按照既定的质量标准进行生产。
2.2设备管理规范:设备管理规范涉及到汽车制造中使用的设备的管理和维护。
通过制定设备的保养计划、定期检查设备状况以及培训设备操作人员,可以确保设备的可靠性和稳定性,提高生产效率和产品质量。
2.3产品验证规范:产品验证规范是指对于汽车产品的性能、可靠性和安全性进行验证的活动。
整车工业化工艺设计评审标准
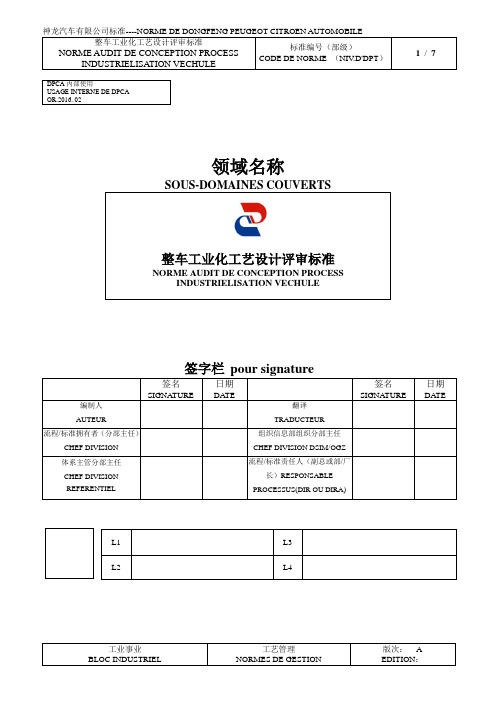
DPCA内部使用USAGE INTERNE DE DPCAOR.2016. 02领域名称SOUS-DOMAINES COUVERTS整车工业化工艺设计评审标准NORME AUDIT DE CONCEPTION PROCESSINDUSTRIELISATION VECHULE签字栏pour signature签名SIGNATURE 日期DATE签名SIGNATURE日期DATE编制人AUTEUR翻译TRADUCTEUR流程/标准拥有者(分部主任)CHEF DIVISION组织信息部组织分部主任CHEF DIVISION DSIM/OGZ体系主管分部主任CHEF DIVISION REFERENTIEL 流程/标准责任人(副总或部/厂长)RESPONSABLE PROCESSUS(DIR OU DIRA)L1 L3 L2 L45.4.2.技术任务书规定的技术要求的符合性审核。
5.4.3.技术方案的3D数字化设计与模拟的审核。
5.4.4.必要的设计说明书、CAE计算与分析的审核。
5.4.5.设备的土建施工设计指导图、动能及流体耗量的审核。
5.4.6.项目上下游的技术接口方案(如物流与输送、自动化生产信息处置等技术)的审核。
5.5.评审程序6相关文件 6 Documents referentiels《工艺设计与更改控制程序》《Procedure de la maitrise de modification et conceptionde process》7 保存记录7 enregistrement archivage记录名称Nom d’enregistrements 保存期限dureed’ archivage移交责任人Responsable delivraison保存责任人responsable deconservation归档时间Tempsd’archvage保存场所Lieu deconservation到期处理方式mode de traitement àecheance《整车工业化工艺设计评审记录》5年授权专家DPPC/DTP Apres audit DPPC/DTP 碎纸机销毁Detruire labrise-papier8 附件8 Annexe。
工艺设计验证方法
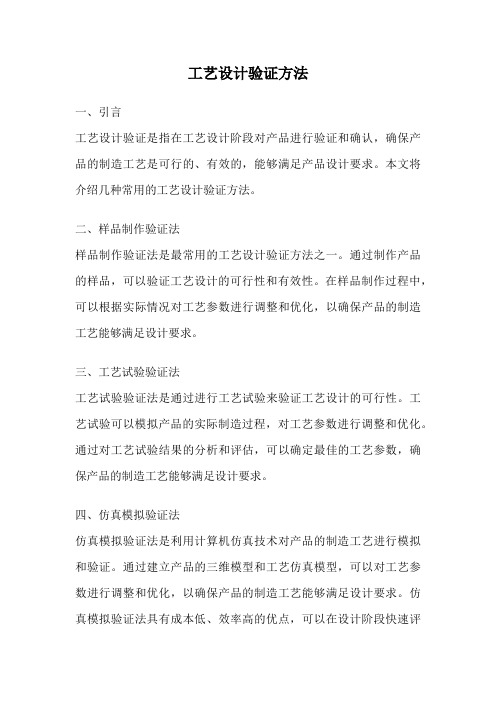
工艺设计验证方法一、引言工艺设计验证是指在工艺设计阶段对产品进行验证和确认,确保产品的制造工艺是可行的、有效的,能够满足产品设计要求。
本文将介绍几种常用的工艺设计验证方法。
二、样品制作验证法样品制作验证法是最常用的工艺设计验证方法之一。
通过制作产品的样品,可以验证工艺设计的可行性和有效性。
在样品制作过程中,可以根据实际情况对工艺参数进行调整和优化,以确保产品的制造工艺能够满足设计要求。
三、工艺试验验证法工艺试验验证法是通过进行工艺试验来验证工艺设计的可行性。
工艺试验可以模拟产品的实际制造过程,对工艺参数进行调整和优化。
通过对工艺试验结果的分析和评估,可以确定最佳的工艺参数,确保产品的制造工艺能够满足设计要求。
四、仿真模拟验证法仿真模拟验证法是利用计算机仿真技术对产品的制造工艺进行模拟和验证。
通过建立产品的三维模型和工艺仿真模型,可以对工艺参数进行调整和优化,以确保产品的制造工艺能够满足设计要求。
仿真模拟验证法具有成本低、效率高的优点,可以在设计阶段快速评估多种工艺方案。
五、统计分析验证法统计分析验证法是通过对大量数据进行统计和分析,评估工艺设计的可行性和有效性。
通过对数据的分析,可以确定工艺参数的合理范围,确保产品的制造工艺能够满足设计要求。
统计分析验证法可以帮助工程师更好地理解和控制工艺过程,提高产品的制造质量。
六、质量控制验证法质量控制验证法是通过对产品的质量进行监控和控制,评估工艺设计的可行性和有效性。
通过建立合理的质量控制系统,可以及时发现和纠正工艺过程中的问题,保证产品的制造工艺能够满足设计要求。
质量控制验证法可以帮助企业提高产品的制造质量和市场竞争力。
七、结论工艺设计验证是确保产品制造工艺可行性的重要环节。
本文介绍了几种常用的工艺设计验证方法,包括样品制作验证法、工艺试验验证法、仿真模拟验证法、统计分析验证法和质量控制验证法。
通过合理选择和应用这些方法,可以有效地验证和确认产品的制造工艺,提高产品的制造质量和市场竞争力。
- 1、下载文档前请自行甄别文档内容的完整性,平台不提供额外的编辑、内容补充、找答案等附加服务。
- 2、"仅部分预览"的文档,不可在线预览部分如存在完整性等问题,可反馈申请退款(可完整预览的文档不适用该条件!)。
- 3、如文档侵犯您的权益,请联系客服反馈,我们会尽快为您处理(人工客服工作时间:9:00-18:30)。
•同步工程的宗旨: •将汽车实际生产中可能会发生的问题提前到产品设计阶段解决。
第二部分 同步工艺分析 2.开展SE活动的目的
•2.2 优化工艺,降低制造风险
产品设 计
•能否制造?
•能否制造合格?
•能否批量生产?
风 险
•工装投入
第二部分 同步工艺分析
2.开展SE活动的目的
•2.3 降低开发成本
产品设 计
•输送设备(专用):电动葫芦、往复式输送系统、滚床/滑橇输送系统、Pickup、升
降机等。
•生产工具或辅具(专用):气动焊钳、助力机械手、电动磨头、风动扳手、零件盛具等
。
•冲压件
•悬挂式点焊机
•螺母焊机
•焊接夹具
•MIG焊机
•螺柱焊机
第三部分 生产线/工装 4. 焊接生产线
•4.3 焊接生产线现状
生产线的组成
•操作者 工具 工装 工艺设备 输送设备 检测工具/设备
第三部分 生产线/工装
1.生产线的概念
生产线的节拍
• W X D X T X 3600 X δ1 X δ2
•(分钟/台
•设计产能 X[1+〔1-合格率〕]车)
•W——年工作日,标准设定为251天。 •D——每天生产班次,在扩初设计时的一般取为2班制。 •T——每班工作时长,2班时为8小时,3班制时一般为7小时。 •δ1 ——开工率,按长安公司现有管理水平,设定为93%。 •δ2 ——作业能率,一般设定为95%。
第二部分 同步工艺分析 4. SE分析输出
•工艺虚拟验证
第二部分 同步工艺分析 4. SE分析输出
第三部分 生产线/工装 1.生产线的概念
生产线的概念
• 按工艺需求,配备生产某种产品(零、部件)所需要 的各种工艺装备、设备及各工种的工人,负责完成某种产 品(零、部件)的全部制造工作,对相同的劳动对象进行 不同工艺加工的一系列组合。
•工程化SE分析 •SE总结
第二部分 同步工艺分C
•O D
•ST
•PT
•D R
•C P
•D C
•C •L •L C RS
•J1
•F S
•参考车分析
•样车制作
• 参考车分析 •模型及主断面分析
参考车材料分析 特殊工艺分析 大型覆盖件草图 制造资源分析 初步生产线方案 新工艺新材料应用 分析
工焊艺接流及程总验装证工艺验证
SE总结
车身分块分析 冲压成形性分析 外观间隙公差分析 装配断面分析 典型断面涂装性分析 工艺难点分析
工程化SE分析
车身零件冲压成形性分析
定位基准的确定
生产线适应性分析
CAE分析(关重/复杂零件)
与设计人员进行沟通对接 SE问题的清理、追踪 SE问题的闭环管理
第二部分 同步工艺分析 4. SE分析输出
第三部分 生产线/工装
7. 与奇端对标
•7.1 冲压
•奇 瑞
冲压车间 生产线 设备生 工序 产厂家
设备代号
•长 安
冲压一车间 1线 (车间面积
约
12000 2线 平方 米)
3线
4线
冲压二车间 1-2线
(车间面积 约
3线
18000 4线 平方 米) 5线
济南第二 6序 机床厂
J47-600/400-4000-2200 X 1(台) J39-630A-3800-2000 X 5(台)
翼子板及门盖类等中大 型覆盖件
大梁前段、中段、后段 、前、后碰撞横梁等中 大型结构件
前罩内板、前壁板 、前壁板侧板、前 、中、后立柱、
E 500 手工
一般结 构件
F 500 手工
一般结构 件
最大生 产能力 (3班制)
500万件/年
540万件/年
540万件/年
第三部分 生产线/工装
4. 焊接生产线
•4.1 焊接的一般工艺流程
第三部分 生产线/工装 2.生产线规划/设计/建设流程
•初步制造方案
•生产线工艺方案
•生产线招标
•生产线安装
•试生产
•生产线调试
•生产线设备制造 •工艺设备制造
•生产线 •扩初设计
•生产线施工建设
•工程施工设计
第三部分 生产线/工装
3. 冲压生产线
•3.1 冲压的一般工艺流程
•落料及堆 垛
•拉延成 形
•SI
•S C
•O D
•ST
•PT
•D R
•C P
•D C
•C •L •L C RS
•J1
•F S
•参考车分析
•样车制作
• 参考车分析 •模型及主断面分析
参考车车身材料
大型覆盖件草图
制造资源分析
初步制造方案
新工艺新材料应用
分析
模型及主断面分
析
•工程化SE分析 •SE总结
样车制作
车身零件冲压成形性验证
车检测线等。
•生产工装(专用):分装夹具、发动机托盘等。 •输送设备(专用):悬链输送系统、板链输送系统、滚床/滑橇输送系统、AGV小车、
升降机等。
•生产工具或辅具(通用):风扳枪、扭力扳手、拉铆枪、电池枪、零件盛具等。
•冷媒加注设 备
•AGV输送小车
第三部分 生产线/工装
6. 总装生产线
•6.3 总装生产线现 状
•串行工程
•市场分 析
•产品设 计
•制造过 程
•市场分 析
•并行工程
•市场分 析
•产品设 计
•制造过 程
•市场分 析
第二部分 同步工艺分析
2.开展SE活动的目的
•2.1 缩短开发周期
市场 分析
产品 设计
工艺 设计
销售 服务
制造 运行
•环节间存在内在的联系
? •存在的问题贯穿项目始终
•什么时候解决问题 •投入小、收效大?
•工艺规划
•工艺设计
•工艺完善
•工装 样车制
作 •试生 产
•小批 量
•工艺验证
第二部分 同步工艺分析
1.同步工艺分析定义
• SE(Simultaneous Engineering),即同步开发工程,是一种对产 品及相关过程进行并行、一体化设计的系统工作模式。 即工艺技术人员协同 其他部门人员一起,从产品开发初期就考虑到产品开发全周期中的一切工艺因 素,包括品质、成本、材料、加工、进度计划等,通过与设计部门人员的良好 协作及信息的及时交流,从而达到优化产品设计、降低开发成本并缩短开发周 期的目的。
•SE输出文 件
产品设计优化
•)ECR(设计变更请求 •特殊公差分析 •工艺流程初步规划 •工艺路线初步规划
供应商支持
•设备规划/需求 •工装规划 •划车身件工序规 •算车身件坯料估
先期工艺设计
•生产工艺流程 •生产工艺路线 •生产线规划/方案 •工装规划/方案 •投资估算 •工艺规程编制
第二部分 同步工艺分析 4. SE分析输出
•切边冲 孔
•入 库
•整 形 •检 查
第三部分 生产线/工装
3. 冲压生产线
•3.2 冲压设备及工装
•生产设备(通用):机械式压力机或液压式压力机;机械式压力机效率高但投资
大,液压式压力机效率较低但拉延成形性好,投资较少。
•生产工装(专用):冲压模具、检具。 •输送设备(通用) :机器人、机械手、输送带。 •生产工具或辅具(专用):端拾器(自动化生产需要)、风动磨头、零件盛具等
•前壁板总 成
•后地板总 成
•前地板总 成
•发动机仓总 成
•车架总 成
•左侧围总 成
•右侧围总 成
•白车体总 成
•白车调整线
•门、盖生产线
第三部分 生产线/工装
4. 焊接生产线
•4.2 焊接设备及工装
•生产设备(通用):电阻式点焊机、CO2焊机、螺柱焊机、机器人焊接系统/涂胶系统
等。
•生产工装(专用):焊接夹具、门盖装具等。
• 在传统的机械制造行业,工艺设计主要是指工艺规程和
工艺装备设计的总称, 而在大规模的现代制造企业中,工艺设 计就不仅仅包含了依据产品设计要求制定产品制造过程的方法 、工装/设备规划、物流规划、操作规范、标准等内容,同时 还融入包含了对产品的先期可行性分析工作内容。
•工艺设计是产品设计到产品制造的桥梁
•K O
•SI
•S C
•O D
•ST
•PT
•D R
•C P
•D C
•C •L •L C RS
•J1
•F S
•参考车分析
•样车制作
• 参考车分析
参考车材料分析 特殊工艺分析 大型覆盖件草图 制造资源分析 初步生产线方案 投资估算
•模型及主断面分析
模型及主断面分 析
车身分块分析 冲压成形性分析 外观间隙公差分析 装配断面分析 典型断面涂装性分析 工艺难点分析
•形状能否简化
•工序能否减少
•材料的多选性
•?
第二部分 同步工艺分析 3. SE分析阶段/内容
•K O
•SI
•S C
•参考车分 析
•O D
•ST
•PT
•D R
•C P
•D C
•C •L •L C RS
•J1
•F S
•样车制 作
•模型及主断面分析
•工程化SE分析 •SE总结
第二部分 同步工艺分析 3. SE分析阶段/内容
漆机器人系统等。
•生产工装(专用):各类卡具等。
•输送设备(专用):电动葫芦、悬链系统、滚床/滑橇输送系统、叉转系统、升降机等
。
•生产工具或辅具(通用):手动喷枪、打磨机、抛光机、注腊枪、挤胶枪等。