小轿车发动机缸体制造工艺(精)
发动机缸体生产过程

发动机缸体生产过程嘿,你知道发动机缸体是怎么生产出来的吗?这可真是个超级有趣的过程,就像一场精心编排的大型魔术表演,只不过这魔术的背后是严谨的科学和高超的工艺。
我有个朋友在发动机制造厂里工作,他叫小李。
有一次我有幸去参观了他们的工厂,亲眼目睹了发动机缸体生产的全过程,那场面,真叫一个震撼。
生产发动机缸体啊,首先得从原材料说起。
这些原材料就像是厨师做菜的食材一样重要。
缸体的主要材料通常是高强度的铸铁或者铝合金。
这就好比盖房子,你得先选好结实耐用的砖头。
铝合金材质的缸体就像是轻盈的舞者,重量轻,有助于提高发动机的燃油效率,就像舞者灵活的身姿可以快速移动一样。
而铸铁缸体呢,则像是一位强壮的大力士,具有更高的强度和耐热性,能够承受更大的压力。
接下来就是铸造的过程啦。
这个过程就像是雕塑家在创作一件伟大的作品。
工人们把原材料加热融化,然后倒入事先制作好的模具里。
这模具啊,就像是一个魔法盒,金属液体流进去之后,就会按照模具的形状成型。
我当时看到那红红的、滚烫的金属液体,像岩浆一样流淌进模具,心里想着,这要是不小心洒出来一点儿,那可不得了啊!旁边的老师傅笑着跟我说:“小伙子,这可都是有严格的操作流程的,不会出乱子的。
”我就好奇地问:“师傅,这就像把水倒进一个瓶子里一样,但是要困难多了吧?”老师傅哈哈笑着说:“那可不,这比倒水可复杂太多啦,温度、流速、模具的状况都得严格把控呢。
”铸造出来的缸体雏形可还不行,它就像一块未经雕琢的璞玉。
然后就是机械加工的环节了。
这时候各种大型的加工设备就像一群技艺精湛的工匠,开始对缸体进行精细的加工。
比如说,要在缸体上钻出活塞运动的气缸孔。
这钻孔的精度要求极高,就像在一根头发丝上雕刻花纹一样精细。
我看到那些机床在高速运转,发出嗡嗡的声音,小李告诉我:“你看,这些设备都是按照设定好的程序进行操作的,误差非常小。
要是这个孔钻歪了或者大小不合适,那这个缸体可就报废了。
”我不禁感叹:“哇,这可真是差之毫厘谬以千里啊!”在加工的过程中,还有一个很重要的步骤就是珩磨。
发动机缸体加工工艺
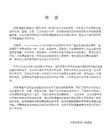
汽车发动机缸体加工工艺分析
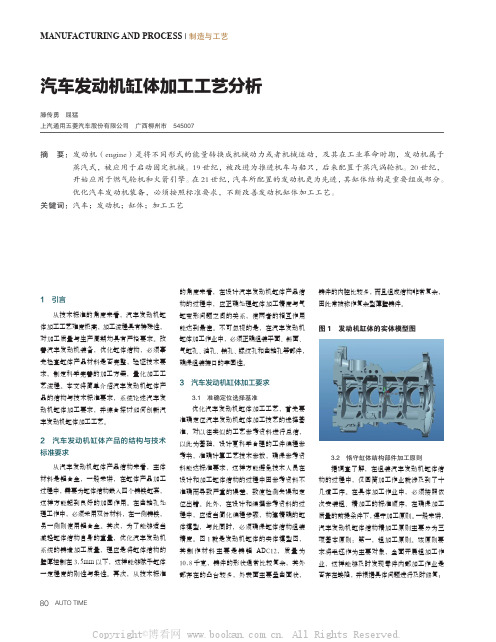
80AUTO TIMEMANUFACTURING AND PROCESS | 制造与工艺汽车发动机缸体加工工艺分析滕传勇 屈猛上汽通用五菱汽车股份有限公司 广西柳州市 545007摘 要: 发动机(engine)是将不同形式的能量转换成机械动力或者机械运动,及其在工业革命时期,发动机属于蒸汽式,被应用于启动固定机械。
19世纪,被改进为推进机车与船只,后来配置于蒸汽涡轮机。
20世纪,开始应用于燃气轮机和火箭引擎。
在21世纪,汽车所配置的发动机更为先进,其缸体结构是重要组成部分。
优化汽车发动机装备,必须按照标准要求,不断改善发动机缸体加工工艺。
关键词:汽车;发动机;缸体;加工工艺1 引言从技术标准的角度来看,汽车发动机缸体加工工艺难度极高,加工流程具有特殊性,对加工质量与生产周期均具有严格要求。
改善汽车发动机装备,优化缸体结构,必须事先检查缸体产品材料是否完整,验证技术要求,制定科学完善的加工方案,量化加工工艺流程。
本文将简单介绍汽车发动机缸体产品的结构与技术标准要求,系统论述汽车发动机缸体加工要求,并综合探讨如何创新汽车发动机缸体加工工艺。
2 汽车发动机缸体产品的结构与技术标准要求从汽车发动机缸体产品结构来看,主体材料是铝合金,一般来讲,在缸体产品加工过程中,需要为缸体结构嵌入四个铸铁缸套,这样方能起到良好的加固作用。
在曲轴孔处理工作中,必须采用双份材料,在一侧铸铁,另一侧则使用铝合金。
其次,为了能够适当减轻缸体结构自身的重量,优化汽车发动机系统的铸造加工质量,理应是将缸体结构的壁厚控制在3.5mm 以下,这样能够赋予缸体一定程度的刚性与柔性。
再次,从技术标准的角度来看,在设计汽车发动机缸体产品结构的过程中,应正确处理缸体加工精度与气缸变形问题之间的关系,使两者的相互作用能达到最佳。
不可忽视的是,在汽车发动机缸体加工作业中,必须正确组装平面、斜面、气缸孔、油孔、销孔、螺纹孔和曲轴孔等部件,确保组装接口的牢固性。
汽车发动机缸体制造工艺
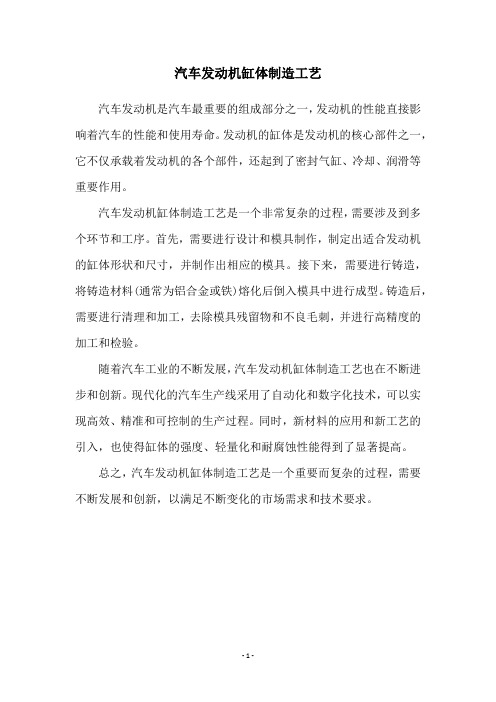
汽车发动机缸体制造工艺
汽车发动机是汽车最重要的组成部分之一,发动机的性能直接影响着汽车的性能和使用寿命。
发动机的缸体是发动机的核心部件之一,它不仅承载着发动机的各个部件,还起到了密封气缸、冷却、润滑等重要作用。
汽车发动机缸体制造工艺是一个非常复杂的过程,需要涉及到多个环节和工序。
首先,需要进行设计和模具制作,制定出适合发动机的缸体形状和尺寸,并制作出相应的模具。
接下来,需要进行铸造,将铸造材料(通常为铝合金或铁)熔化后倒入模具中进行成型。
铸造后,需要进行清理和加工,去除模具残留物和不良毛刺,并进行高精度的加工和检验。
随着汽车工业的不断发展,汽车发动机缸体制造工艺也在不断进步和创新。
现代化的汽车生产线采用了自动化和数字化技术,可以实现高效、精准和可控制的生产过程。
同时,新材料的应用和新工艺的引入,也使得缸体的强度、轻量化和耐腐蚀性能得到了显著提高。
总之,汽车发动机缸体制造工艺是一个重要而复杂的过程,需要不断发展和创新,以满足不断变化的市场需求和技术要求。
- 1 -。
论发动机缸体的加工工艺

环球市场/理论探讨-176-论发动机缸体的加工工艺朱广波 史晓龙上汽通用五菱汽车股份有限公司青岛分公摘要:汽车制造业作为国民经济的支柱产业,多年来为我国经济发展做出了非常突出的贡献。
然而,在经历了突飞猛进的高增长之后,我国汽车工业面临着越来越多的问题和压力。
如何在我国人口红利逐渐消失、企业竞争力日益下降的今天,进一步降低生产成本,同时不断提高产品质量,实现绿色制造,应对市场对产品提出的日新月异的需求尤其重要。
在此背景下本文将着重分析探讨发动机缸体的加工工艺要点,以期能为以后的实际工作起到一定的借鉴作用。
关键词:发动机;缸体;加工1、发动机缸体加工工艺性分析发动机缸体毛坯制作成坯后,上下缸体的6个面都需要采用金属切削加工的工艺方法最终加工成缸体成品,在加工过程中还要穿插气密检测、清洗、珩磨缸孔等工艺方法。
金属切削加工发动机缸体主要包括:铣面、铣孔、钻孔、镗孔、铰孔和攻丝等。
发动机缸体的加工一般情况下可划分为两个阶段,一是分体加工阶段,二是组件加工阶段。
分体加工阶段主要是将上下缸体上的精度要求不太高的一般结构特征、组合后不便加工的结构特征及关系到合缸的结构特征加工到位或去除大部余量,主要包括合缸面、合缸定位销孔、进排气两侧的安装面与孔系、止推面及轴瓦槽等特征。
发动机缸体的重要结构特征,如曲轴孔、气缸孔、缸盖面、前后端的定位销孔等必须安排在发动机缸体合缸后进行精加工。
发动机缸体试制加工的工艺流程安排可视企业设备现状进行合理安排,一般来讲,采用立式加工中心进行加工,装夹较为方便,但工序会相对分散,需要投入的工艺装备较多,会加大试制的加工成本。
采用卧式加工中心进行加工,可以使工序相对集中,投入的工装较少,可降低试制加工成本。
2、发动机缸体加工工艺要点2.1 缸体加工自动线汽车缸体加工自动线是汽车制造行业中的一种高效设备。
自动线又分为刚性自动线和柔性自动线。
在我国,加工缸体最多的当属组合机床自动线,其输送形式有棘爪输送、摆杆式输送和抬起步伐输送等,都属于刚性自动线。
汽车缸体铸造工艺

一、缸体材料车用发动机缸体缸盖的材质主要有灰铸铁,铝合金,蠕墨铸铁等。
传统的发动机无论是缸体还是缸盖都是采用铸铁的,但是铸铁有着许多先天的不足,例如重量大、散热性差、摩擦系数高等等。
所以,许多发动机厂商都在寻找更适合的材料制造发动机的构成部件,比如密度小的铝。
铝的比重轻,单位体积的铝结构强度要小于铸铁,所以铝缸体通常体积反而大些。
但铝容易和燃烧时产生的水发生化学作用,耐腐蚀性不及铸铁缸体,尤其对温度压强都更高的增压引擎更是如此。
铸铁缸体和铝缸体各有其优缺点,所以所以高增压的引擎很多都采用铸铁缸体,小型车的缸体则更多向铝缸体发展。
金属中的元素组成会对金属材料的性能产生较大的影响,就钢铁而言,钢中含碳量增加,屈服点和抗拉强度升高,但塑性和冲击性降低,当碳量0.23%超过时,钢的焊接性能变坏,因此用于焊接的低合金结构钢,含碳量一般不超过0.20%。
碳量高还会降低钢的耐大气腐蚀能力,在露天料场的高碳钢就易锈蚀;此外,碳能增加钢的冷脆性和时效敏感性。
不同的缸体元素配比也是有差别的。
合肥江淮铸造有限责任公司缸体化学成分要求化学成分(%)C Si Mn P S Cr Cu Ti Sn Pb下限 3.25 1.95 0.60 0.00 0.06 0.25 0.30 0.00 0.06 0.00 0上限 3.40 2.10 0.90 0.06 0.10 0.35 0.50 0.03 0.09 0.00 4二、原材料熔炼熔炼设备选用:中频感应保温电炉:生产效率10t/h,外水冷长炉龄大排距冲天炉:生产效率7t/h。
1、原材料原材料一般为回炉料,废钢和生铁。
回炉料是厂家的常备材料,在使用时必须注意其本身的干净程度。
回炉料的加入量必须严格按一定比例,否则会导致铁水的Si、S含量不易控制。
江淮生产的缸体铸件回炉料使用量一般不超过20%。
在江淮的缸体生产中,废钢的使用量超过50%。
这是由于生铁本身含有粗大石墨,而石墨熔点较高,在2000℃以上,在熔炼中不能熔尽,使得结晶过程中石墨变得粗大。
汽车发动机缸体的铸造工艺
汽车发动机缸体的铸造工艺汽车发动机的发展离不开发动机铸造工艺的进步,而发动机铸造的核心在于汽车发动机缸体的铸造工艺。
汽车发动机缸体作为发动机的核心部件,除了承载发动机部件外,还需具有良好的散热和密封性能。
因此,发动机缸体的铸造工艺对发动机整体性能和稳定性有着至关重要的作用。
本文将从铸造材料、铸造工艺、铸造缺陷、铸造后处理等方面对汽车发动机缸体的铸造工艺进行详细探讨。
一、铸造材料发动机缸体通常采用铸铁材料,主要分为灰铸铁和球墨铸铁。
灰铸铁通常用于较低功率和低转速的汽车发动机,而球墨铸铁则适用于高性能、高功率、高转速的汽车发动机。
球墨铸铁在强度、塑性、耐磨性等方面均优于灰铸铁,且在重量、散热、强度均有更好的表现。
同时,球墨铸铁具有更好的冲击吸能性能,能够有效地防止发动机在碰撞时的损坏。
二、铸造工艺1. 铸型制作铸型制作是铸造过程中的重要环节,它直接影响到铸体的质量和缺陷率。
一般采用砂型铸造,其制作包括砂型模板制作、芯制作、脱模、修型等步骤。
对于汽车发动机缸体的铸造,为了保证制品的精度和质量,通常采用分型铸造法,即把模型分成几个部分分别制作再组装成模型,以保证铸体的准确度。
2. 熔炼与倒铸铸型制作完成后,便进入了熔炼与倒铸环节。
熔炼时,为了保证铸体的质量,一般采用先熔化高温点低融点的材料,然后在熔化过程中加入低温点高融点的材料,并在熔融过程中进行剧烈搅拌,以使铸材充分混合。
倒铸时,应尽量减小流型和鼓包缺陷的产生,避免气孔、夹渣等缺陷产生。
3. 铸后处理铸造完成后,需要进行铸后处理,以进一步提高铸体的性能与质量。
铸后处理主要包括清除毛边、磨光、修整、冷却采取等环节。
其中,清除毛边和磨光是保证表面光洁度的必要环节,而修整和冷却采取是保证铸体的准确度和性能的关键环节。
三、铸造缺陷由于铸造工艺的复杂性和铸造材料的不均匀性等原因,汽车发动机缸体在铸造过程中通常会出现各种类型的缺陷,如气孔、夹渣、热裂、鼓包、孔眼等。
发动机缸体铸件的精整工艺与装备
( i doS nu c i r nfcuigC . t, i d oS ad n 6 2 , hn ) Qn a a ri hn yMa u tr o, d Qn a hn og2 2 8 C ia g Ma e a n L g 6
摘 要: 以发动机缸 体铸件 为例介 绍 了铸件精 整工 艺与 装备 , 包括铸件 的落砂 、 浇 冒1 、 处理 、 击除 去 2 :热 振
芯、 一次粗抛 、 铸件表面磨 削、 工精整 、 人 二次精抛 、 检验及铸件涂装等 。介绍如何 选择合理 的铸 件清理工 艺和 高
端的清理生产装备 , 实现铸件清理的连续 、 以 自动化生产 , 从而从真正 意义上实现铸造 生产从 传统的手 工、 半机
2 1 年第 5 01 期
21 年 01
・
铸
造Hale Waihona Puke 设备与 工
艺
1 O月
F U D Y E UP N N E H O O Y O N R Q IME TA D T C N L G
铸 造设 备 ・
发 动机缸体 铸件 的精整 工艺与装备
王德 志 。 田永 恒
( 青岛三锐机械制造有限公 司, 山东 青岛 2 62 ) 6 2 8
1 发 动机 缸体 铸件 精 整
21 落 砂 、 芯 单 元 . 除
211 单元 功 能 ..
发动机缸体铸件精整是指 , 缸体铸件浇注成 型 后从落砂开始至铸件进行精加工之前 的一系列铸 件清理工序 的总称。
它包括铸件落砂 、 除芯 单 元 ; 次 粗 抛 清 理 单 一
该单元 的 目的是 除去工件表面 的面砂和型腔 内 的芯 砂 , 面砂 和 芯 砂 分 离 , 别 进 入 不 同 的 旧砂 分
汽车发动机缸体模具设计及低压铸造工艺
汽车发动机缸体模具设计及低压铸造工艺摘要:目前,对于汽车铝合金发动机缸体采用压力铸造的方法较为广泛。
因此,压铸造工艺在汽车发动机缸体铸造中的应用过程,通过缸体模型合理的设计,调整与优化相关工艺参数,可以达到提高合格率的目的。
关键词:汽车发动机;模具设计;低压铸造工艺引言下缸体是汽车发动机上的重要零件,其上部与气缸体、下部与油底壳相连;气缸体与下缸体之间安装有曲轴。
下缸体在发动机工作过程中的特点是:处于高温状态下工作,承受较大的热冲击作用和承受较大的力,工作条件较为恶劣。
下缸体对气密性要求较高。
另外,此铸件在缸体的螺栓孔处及水泵孔凸台处较为厚大,极易产生铸造缺陷。
选择低压铸造工艺方法,采用合理的工艺参数、模具结构及局部快冷生产此铸件,不仅能解决铸件上厚大部位铸造缺陷的问题,同时也能满足此铸件组织致密性的要求。
1汽车发动机缸体结构本次研究以GM-L850发动机下缸体为例,铸件重为10.3 kg,轮廓尺寸为471 mm,371 mm和91mm,壁厚平均为4.0 mm。
材质是铝合金,这种材料具有力学性能好以及铸造工艺性能好的特点,因此,在汽车发动机铸造中应用比较广泛。
为了满足具体的工艺条件,在结构设计中进行的主要措施有两个:①在曲轴孔半圆处对工艺余量增加,以能够在下部形成一个厚大部位;②为了能够对模具结构简化,可以不铸出产品机械加工斜孔。
发动机铸件结构如图1。
2发动机缸体铸造模具设计铸造模具设计中所采用的是UG软件CAD模块,依照具体的工艺和产品毛坯三维模型,实施分型拆模,从而得到模具型芯、型腔、滑块以及镶块等,之后将这些模具分型与标准或者是非标准零件结合实施装配,经过一系列干涉检查、成型分析等流程之后,也就能够获取模具。
在进行模具三维设计中,重点是要表而形成分模成型特征,其他特征则较易实现。
汽车发动机缸体模具工作流程如图2.3模具设计3.1模具结构形式为了顺利开模,模具分型要采用多分型面,模具有6个方向开模,分别是:底模、顶模、右模、左模、前模及后模(具体模具结构见图3)。
汽车发动机汽缸体缸孔双轴精镗加工工艺
i n d e x .E v e n t u a l l y , t h i s p r o j e c t w a s p u t i n t o o p e r a t i o n i n a n e n t e r p i r s e .
m e n t s 。 t h i s p r o j e c t c o m p a r e d t h e d e v e l o p m e n t o f t h e c y l i n d e r h o l e b o r i n g ma c h i n i n g c e n t e r a n d s p e c i a l
Ab s t r a c t :Ai mi n g t o a n a u t o mo bi l e e n g i n e c y l i n d e r b l o c k c y l i n d e r bo r e p r o c e s s i n g e q u i p me n t a n d p r o c e s s r e q u i r e -
( K e y L a b o r a t o y o f Ma n u f a c t u r e a n d T e s t T e c h n i q u e s f o r A u t o mo b i l e P a R s ,Mi n i s t y r o f E d u c a t i o n , C h o n g q i n g U n i v e r s i t y o f T e c h n o l o g y ,C h o n g q i n g 4 0 0 0 5 4, C H N)
关 键词 : 发 动机汽 缸体 中图分 类号 : T K 2 6 3 . 1 缸子 L 专用镗 床 文献标 识 码 : A 精镗 工艺
- 1、下载文档前请自行甄别文档内容的完整性,平台不提供额外的编辑、内容补充、找答案等附加服务。
- 2、"仅部分预览"的文档,不可在线预览部分如存在完整性等问题,可反馈申请退款(可完整预览的文档不适用该条件!)。
- 3、如文档侵犯您的权益,请联系客服反馈,我们会尽快为您处理(人工客服工作时间:9:00-18:30)。
小轿车发动机缸体制造工艺 - 1 -小轿车发动机缸体制造工艺缸体是汽车发动机乃至汽车中的最重要的零件之一,它的加工质量直接影响发动机的质量,进而影响到汽车整体的质量,因此发动机缸体的制造加工长期以来一直受到国内外汽车生产企业的高度重视。
1缸体的简单介绍:发动机缸体是发动机的基础零件和骨架,同时又是发动机总装配时的基础零件。
缸体的作用是支承和保证活塞、连杆、曲轴等运动部件工作时的准确位置;保证发动机的换气、冷却和润滑;提供各种辅助系统、部件及发动机的安装。
汽车发动机的缸体和上曲轴箱常铸成一体,称为缸体——曲轴箱。
缸体上部的圆柱形空腔称为气缸,下半部为支承曲轴的曲轴箱,其内腔为曲轴运动的空间。
在缸体内部铸有许多加强筋,冷却水套和润滑油道等。
根据缸体与油底壳安装平面的位置不同,通常把缸体分为以下三种形式。
(1) 一般式缸体:其特点是油底壳安装平面和曲轴旋转中心在同一高度。
这种缸体的优点是机体高度小,重量轻,结构紧凑,便于加工,曲轴拆装方便;但其缺点是刚度和强度较差(2) 龙门式缸体:其特点是油底壳安装平面低于曲轴的旋转中心。
它的优点是强度和刚度较好,能承受较大的机械负荷;但其缺点是工艺性较差,结构笨重,加工较困难。
(3) 隧道式缸体:这种形式的缸体曲轴的主轴承孔为整体式,采用滚动轴承,主轴承孔较大,曲轴从缸体后部装入。
其优点是结构紧凑、刚度和强度好,但其缺点是加工精度要求高,工艺性较差,曲轴拆装不方便。
为了能够使缸体内表面在高温下正常工作,必须对缸体和缸盖进行适当地冷却。
冷却方法有两种,一种是水冷,另一种是风冷。
水冷发动机的缸体周围和缸盖中都加工有冷却水套,并且缸体和缸盖冷却水套相通,冷却水在水套内不断循环,带走部分热量,对缸体和缸盖起冷却作用。
现代汽车上基本都采用水冷多缸发动机,对于多缸发动机,气缸的排列形式决定了发动机外型尺寸和结构特点,对发动机机体的刚度和强度也有影响,并关系到汽车的总体布置。
按照气缸的排列方式不同,缸体还可以分成单列式、V型和对置式三种。
第 - 1 - 页共 7 页小轿车发动机缸体制造工艺 - 2 -2缸体的工作条件:缸体通常工作在高温、高载荷、磨损剧烈的条件下,承受较大的压力,受力复杂,同时工作在汽油的沉浸下,工作环境潮湿。
3缸体的使用性能要求:缸体的工作条件决定了缸体必须具有高强度、高刚度、高硬度、高耐磨性以及良好的散热性,同时要有很好的密封性、防漏性、减振性等。
4缸体毛坯材料的选择:发动机缸体采用的材料一般是灰铸铁HT150、HT200、HT250,也有采用铸铝或铸钢的。
采用灰铸铁可以满足高强度、高刚度以及高耐磨性的要求,而且工艺性能、减振性、切削加工性能优良,同时成本较低,但是会增加缸体的重量,增加发动机的负担;采用铸钢材料,可以使缸体承受更大的冲击载荷;采用铝合金材料最大的好处是可以减轻缸体的重量,顺应了汽车轻量化的趋势,因此最近采用铸铝材料的缸体越来越多。
每种材料都有自身的特点,优劣共存,我们需要根据不同缸体产品的不同质量要求来确定相应的生产材料。
5毛坯制造方法的选择:铸造、锻压、焊接、粉末冶金和非金属材料成形等方法都可以作为机械零件毛坯的制造方法,但它们的制造成本、生产条件等都有差异,再加上实际生产中零件毛坯生产批量的不同,我们对制造方法的选择必然也会不同,正确的方法是:结合生产实际,综合考虑毛坯的使用要求、生产经济性要求,同时兼顾环境保护,最终达到制造方法与实际生产条件相适应。
对于缸体这种形状复杂、尺寸较大、有不规则的外形和内腔、壁厚不均的箱体类零件,通常采用铸造(砂型铸造)的方法,采用铸造的方法不但可以满足缸体的使用性能要求,而且生产成本较低。
砂型铸造流程:准备炉料→熔炼金属→浇注→凝固冷却→落砂清理→检验→合格铸件缸体毛坯的技术要求:对非加工面不允许有裂纹、冷隔、疏松、气孔、砂眼等铸造缺陷。
缸体毛坯质量对加工的影响:加工余量过大,会增加机床的负荷,影响机床和刀具的使用寿命,成本变高;飞边过大,直接影响刀具使用寿命;由于冷热加工基准不统一,毛坯各部分相互间的偏移会造成机械加工时余量不均匀。
6缸体零件结构简图(部分):第 - 2 - 页共 7 页小轿车发动机缸体制造工艺- 3 -第 - 3 - 页共 7 页小轿车发动机缸体制造工艺 - 4 -第 - 4 - 页共 7 页小轿车发动机缸体制造工艺- 5 -7缸体制造工艺:7.1工艺特点如图所示,此缸体为一整体铸造结构,其上部有4个缸套安装孔;缸体的水平隔板将缸体分成上下两个部分;缸体的前端面从前到后排列有三个同轴线的凸轮轴安装孔和惰轮轴孔。
缸体的工艺特点是:结构、形状复杂;加工的平面、孔多;壁厚不均;加工精度要求高,属于典型的箱体类加工零件。
加工平面一般采第 - 5 - 页共 7 页小轿车发动机缸体制造工艺 - 6 -用刨、铣削等方法加工,加工孔主要采用镗削,加工小孔多用钻削。
由于缸体结构复杂,因此如何保证各表面的相对位置精度是加工中的一个重要问题。
7.2工艺基准选择合理的加工工艺基准,直接关系到能否保证零件的加工质量。
一般来说,工艺基准可分为粗基准和精基准。
(1)粗基准对于上线的毛坯,其粗基准的选择尤为重要,粗基准选择不合理会造成加工余量分布不均匀,加工面偏移,产生废品。
在缸体的生产中,我们一般采用侧面为粗基准。
(2)精基准对于发动机缸体这种箱体零件来说,一般采用“一面两销”为全线的统一基准。
对于较长的自动生产线系统,由于定位销孔在使用过程中的磨损造成定位不准确,因此,将定位销孔分为2~3段使用。
在缸体定位销孔的加工中,我们采用以侧面、底面和主轴孔定位,在加工中心上加工。
7.3加工阶段的划分缸体需要加工的表面许多,不同表面的加工精度也不同。
因此,在拟定工艺顺序时,要抓住“加工精度高的表面”这个主要矛盾,合理安排工序。
安排工艺顺序的原则是:先粗后精,先面后孔,先基准后其它。
1)粗加工阶段在发动机缸体的机械加工过程中,安排粗加工工序,对毛坯全面进行粗加工,切去大部分余量,以保证生产效率。
2)半精加工阶段在发动机缸体的机械加工中,为了保证一些重要表面的加工精度,安排一些半精加工工序,将精度和表面粗糙度要求中等的一些表面加工完成,而对要求较高的表面进行半精加工,为以后的精加工做准备。
3)精加工阶段对精度和表面粗糙度要求高的表面进行加工。
4)次要小表面的加工一些表面(如螺纹孔表面)可以在精加工主要表面后进行,一方面加工时对工件变形影响不大,同时废品率也会降低;另外,如果表面加工出现差错时,那么这些小表面也就不必加工了,这样即避免了人力、物力、资金的浪费。
但是要注意的是,如果小表面的加工容易造成主要表面损伤的话,那么就应该将小表面加工放在主要表面的精加工之前。
5)妥善安排辅助工序这类工序(如检验工序)在零件粗加工阶段之后、关键工序加工前后、零件全部加工完毕后,都要适当安排。
对加工阶段进行划分的优点是:一是可以在粗加工之后采取措施消除工件内应力,保证精度;二是将精加工放在后面可以避免在运输过程中损坏工件已加工好的表面;三是先粗加工各表面可以及时发现毛坯缺陷并及时处理,以免工时不必要的浪费。
需要注意的是,在粗加工和精加工之前应分别加上预备热处理和最终热处理的工序。
7.4工艺路线安排(热处理另作阐述)工序00: 毛坯上线工序10:粗铣上下平面工序20:粗铣底面、铣安装面、钻Ø11U7孔底孔Ø10.7、铰孔Ø11U7、钻10—M10X1.25 螺纹底孔Ø8.7、攻螺纹10—M10X1.25、钻2—Ø16U8 底孔Ø15.7、2—Ø16U 孔口倒角450铰孔2—Ø16U8工序30:粗铣前后端面工序40:铣缸体瓦槽工序50:半精镗缸孔、缸孔倒角1X450第 - 6 - 页共 7 页小轿车发动机缸体制造工艺 - 7 -工序60:去毛刺检验工序70:精铣顶面、钻18—M14X1.5 螺纹底孔Ø12.5/14.5、铰孔2—Ø18、攻螺纹18—M14X1.5(以上工序采用底面“一面两销“定位)工序80:钻孔、攻螺纹18—M14X1.5—5H、钻底孔18—Ø12.5(采用顶面“一面两销“定位)工序90:去毛刺、清洗、吹净工序100:工作台转1800 粗铣曲轴孔座2—Ø84、粗镗孔Ø61~62、工作台转1800、粗镗孔Ø61~62、镗孔Ø65~64.6、半精镗孔Ø61.6、工作台转1800 半精镗孔Ø61.6、精镗孔Ø65、铣瓦槽、工作台转1800 铣另一处瓦槽、粗镗孔Ø35~34.6 粗镗孔Ø30~29.6、转1800 精镗Ø30、钻Ø12孔、钻2—Ø10孔、钻6—M10螺纹底孔Ø9、攻螺纹M8工序110:粗铣小平面、精铣小平面、转1800铣小平面、精铣缸体一端面、精铣另一端面、按尺寸要求钻孔及攻螺纹工序120:铣凸平面、精铣凸平面、转向复合钻孔、孔加工、转向铣平面工序130:去毛刺、清洗(以上工序采用底面“一面两销“定位)工序140:底孔加工、逆时针转动工作台钻中心孔、顺时针转动工作台钻引导孔、攻螺纹工序150:清洗(以上工序以端面“一面两销“定位)工序160:精镗曲轴孔、钻底孔、铰孔工序170:精铣分离面、钻孔、钻底孔、钻螺纹底孔、铰孔、攻螺纹(以上工序以侧面“一面两销“定位)工序180:空气吹尽、粗珩气缸孔、精珩气缸孔、各面曲轴孔去毛刺工序190:最终清洗、成品检验分组打印工序200:涂油、成品下线8热处理8.1热处理的作用对材料进行热处理是改善金属材料性能的一种常见的方法,它能够使材料的组织结构发生变化,从而达到改善加工工艺性能和强化力学性能的目的。
对于缸体这种力学性能要求较高的零件,合理安排热处理工序非常重要。
8.2热处理工序对于铸铁材料的缸体而言,通常的热处理工艺为:预备热处理(去应力退火+正火+去应力退火)→最终热处理(淬火+高温回火,又称调质处理+表面淬火)预备热处理安排在粗加工阶段之前,其目的是:消除残余内应力,防止工件变形、开裂;改善组织,细化晶粒;调整硬度,改善切削性能。
退火工艺规范为:加热温度500~550℃,加热速度60~120℃/h,经一定时间保温后,炉冷到150~220℃出炉空冷。
正火工艺规范:将铸件加热到880~920℃,保温1~3h,然后出炉空冷。
正火后,为了消除正火时铸件产生的内应力,通常还要进行去应力退火。
最终热处理安排在精加工阶段之前,其目的是:使材料具有使用时的所有力学性能。
调质处理的工艺规范为:将工件加热至860~900℃,保温后油淬,然后在550~600℃回火2~4h。