龚举成:价值流程图解释共34页
《价值流程图》课件
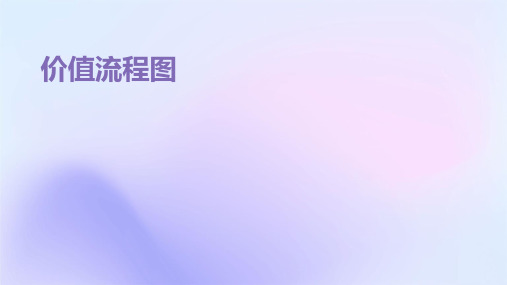
目录
• 价值流程图简介 • 如何绘制价值流程图 • 价值流程图分析 • 价值流程图实施与监控 • 价值流程图案例分析
01
价值流程图简介
定义与概念
价值流程图是一种可视化工具,用于描述一个产品或服务的生产过程,以及各个步骤之间的逻辑关系 。
它通过图形化的方式展示从原材料的采购到最终产品的交付过程中,各个工序的顺序、时间、资源等信 息。
优化与完善
分析流程图
通过分析流程图,找出流程中的瓶颈、浪费和不合理 之处。
提出改进措施
根据分析结果,提出具体的改进措施,如优化流程、 提高自动化程度等。
完善流程图
根据改进措施,对流程图进行修改和完善,使其更加 符合实际操作和管理需求。
03
价值流程图分析
识别瓶颈与问题
瓶颈识别
通过价值流程图分析,识别出生 产或服务流程中的瓶颈环节,如 设备故障、物料短缺、人力不足 等。
以落地。
监控改进过程
03
在改进实施过程中,通过价值流程图对关键指标进行
实时监控,确保改进工作按照预期方向推进。
持续优化与改进
分析改进结果
对改进结果进行分析,评估各项措施 的实施效果,识别改进带来的收益。
总结经验教训
总结改进过程中的经验教训,为后续 的持续优化提供参考。
调整改进计划
根据分析结果和经验总结,对改进计 划进行调整,持续优化价值流程,提
的业务流程。
价值流程图的应用范围
制造业 价值流程图广泛应用于制造业的 生产过程中,帮助企业识别和优 化生产流程,提高生产效率和产 品质量。
业务流程改进 价值流程图可以用于分析各种业 务流程,帮助企业识别和改进低 效、浪费的环节,提高业务流程 的效率和效益。
价值流程图概述

价值流程图(Value Stream Mapping ,简称VSM)价值流程图概述价值流程图(Value Stream Mapping )是()生产系统框架下的一种用来描述和的形象化工具。
它运用的工具和技术来帮助企业理解和精简生产。
价值流程图的目的是为了辨识和减少中的浪费。
浪费在这里被定义为不能够为提供增值的任何活动,并经常用于说明中所减少的浪费”总量。
VSM可以作为管理人员、工程师、生产制造人员、流程规划人员、以及发现浪费、寻找浪费根源的起点。
从这点来说,VSM还是一项工具。
但是,VSM往往被用作工具、工具。
VSM通过形象化地描述生产过程中的物流和信息流,来达到上述工具目的。
从购进的那一刻起,VSM就开始工作了,它贯穿于生产制造的所有流程、步骤,直到终端产品离开。
对生产制造过程中的周期时间、当机时间、、原材料流动、信息流动等情况进行描摹和记录,有助于形象化当前流程的活动状态,并有利于对生产流程进行指导,朝向理想化方向发展。
VSM通常包括对当前状态”和未来状态”两个状态的描摹,从而作为精益制造战略的基础。
价值流程图(VSM )分析的是两个流程:第一个是(情报)流程,即从市场部接到订单或市场部预测客户的开始,到使之变成和的过程;第二个是流程,即从供应商供应原材料入库开始,随后出库制造、入库、产品出库,直至产品送达客户手中的过程。
此外,实物流程中还包括产品的检验、停放等环节。
企业在进行价值流程图(VSM)分析时,首先要挑选岀典型的产品作为深入调查分析的对象,从而绘制岀信息(情报)流程和实物流程的现状图,然后将现状图与信息(情报)和实物流程的理想状况图相比较,发现当前生产过程中存在的问题点,进而针对问题点提出改进措施。
Value Stream 聞呂ppingFuture StateCurre门t State价值流程图的历史1980年代,的与率先运用去除的方法来获取,他们的主要岀发点是提高,而非提高。
之所以这么做,是因为他们认为生产效率的提高将有助于,从而能够暴露岀系统中的深层的浪费问题和问题。
价值流程图
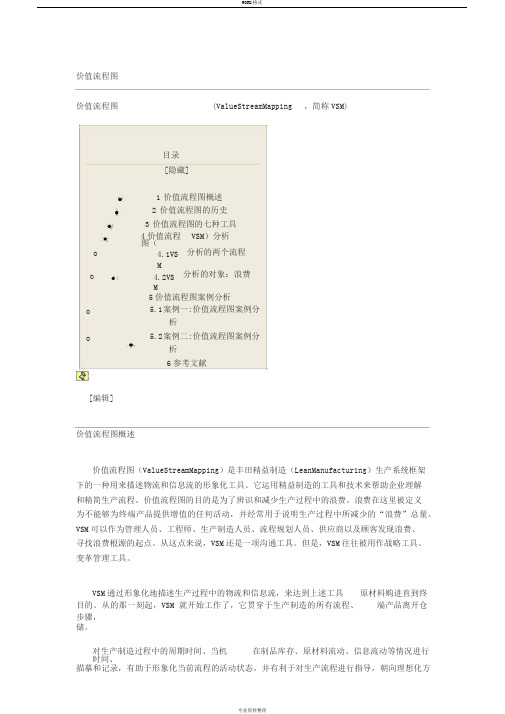
价值流程图价值流程图(ValueStreamMapping ,简称VSM)目录[隐藏]1价值流程图概述2价值流程图的历史3价值流程图的七种工具4价值流程图(VSM)分析o 4.1VSM分析的两个流程o 4.2VSM分析的对象:浪费5价值流程图案例分析o 5.1 案例一:价值流程图案例分析o 5.2 案例二:价值流程图案例分析6参考文献[编辑]价值流程图概述价值流程图(ValueStreamMapping)是丰田精益制造(LeanManufacturing)生产系统框架下的一种用来描述物流和信息流的形象化工具。
它运用精益制造的工具和技术来帮助企业理解和精简生产流程。
价值流程图的目的是为了辨识和减少生产过程中的浪费。
浪费在这里被定义为不能够为终端产品提供增值的任何活动,并经常用于说明生产过程中所减少的“浪费”总量。
VSM可以作为管理人员、工程师、生产制造人员、流程规划人员、供应商以及顾客发现浪费、寻找浪费根源的起点。
从这点来说,VSM还是一项沟通工具。
但是,VSM往往被用作战略工具、变革管理工具。
VSM通过形象化地描述生产过程中的物流和信息流,来达到上述工具目的。
从的那一刻起,VSM就开始工作了,它贯穿于生产制造的所有流程、步骤,原材料购进直到终端产品离开仓储。
对生产制造过程中的周期时间、当机时间、在制品库存、原材料流动、信息流动等情况进行描摹和记录,有助于形象化当前流程的活动状态,并有利于对生产流程进行指导,朝向理想化方向发展。
VSM通常包括对“当前状态”和“未来状态”两个状态的描摹,从而作为精益制造战略的基础。
价值流程图(VSM)分析的是两个流程:第一个是信息(情报)流程,即从市场部接到客户订单或市场部预测客户的需求开始,到使之变成采购计划和生产计划的过程;第二个是实物流程,即从供应商供应原材料入库开始,随后出库制造、成品入库、产品出库,直至产品送达客户手中的过程。
此外,实物流程中还包括产品的检验、停放等环节。
价值流程图介绍

增值的空间(Value Add Space) 产品运输距离(Product Travel)
班次(shifts) 前库存(Before) 后库存(After)
完整的价值流分析过程
客户需求
1. 基于距顾客最 近的下游过程的 有效工作时间, 节拍时间是什么? 2. 你是按顾客拉 动还是直接按发 送建立一个成品 超市?
认识价值流程图符号
物料流 符号
信息流 符号
认识关键性的指标
1 2 3 4 5 6 7 8 9 10 11 12
工人操作周期时间(OCT) 设备加工时间(Auto) 换线(或换型)(Changeover) 正常工作时间(%Up) 品质良率(e.g. FPY or RTY) 生产单元效率(Cell Productivity) 增值的时间(Value Add Time)
包括资源,时间,空间等。
客户决定了销售价格!
从顾客的角度看,大部分公司非增值活动的总量大约为95%!什么是客户愿意支付的?
采矿
一个可乐罐的价值流
------这是发达公司运营的很现代的价值流
熔炼 热轧 冷轧
加工时间:3小时 存储和运输时间:11小时 累计报废:24%
再熔 炼
回收
制罐
消费 者
存储 罐装 存储 超市 库存
Lead Time,即整个整 个生产过程时间。包括 了,人的操作时间,设 备的运行时间,以及库 存的消耗时间。 库存的消耗时间=当前 流程段的库存数量/客 户每天的消耗需求量。
现状价值流程图绘制
Step#8增加原料供应
将供应商端的原料供应 添加进来,形成从供应 商到客户端的完整供应 链。
现状价值流程图绘制
价值流程图解释
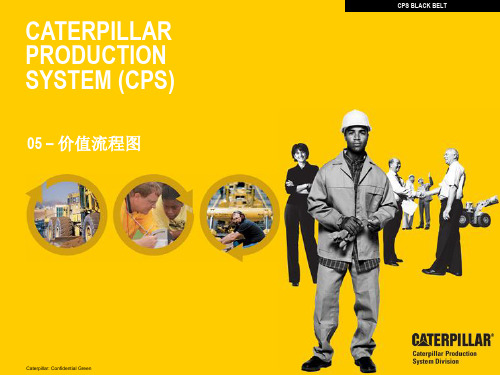
05 – 价值流程图
Caterpillar: Confidential Green
CPS BLACK BELT
IT’S OUR TURN…
目的
本章结束时,你将能够:
▪定义价值流和价值流程图 ▪识别价值流程图的4个区域 ▪认识主要的图标 ▪计算节拍时间 ▪列举建立价值流程图的10个步骤
价值流程图 - CPS 指导原 则
CPS BLACK BELT
▪ “消除浪费” – 有助于识别浪费和浪费的根源 ▪ “价值流管理” - 能清楚的显示可以改进的区域
▪ “从客户的角度出发” - 提供从前后贯穿的视角(产品,服务或业 务过程),始于客户,终于客户。
▪ “可视化管理”- 提供一个形象的图形来建立共同的景象。
Caterpillar: Confidential Green
CPS BLACK BELT
9
IT’S OUR TURN…
第四步:收集库存数据
计算价值流中的库存数量: ▪ From dock to dock (start to end) 门到门 ▪ 过程之间 ▪ 在返工和维修区域 ▪ 包括标准库(维持流的仓库) ▪ 包括未运输的成品
信息流
供应商
生产控制
浪费
过程
物料流
▪ 将不连续的流重点标记出来 ▪找出物料流和信息流交互的地方 ▪将浪费和有改进机会的区域重点标记出来
Caterpillar: Confidential Green
CPS BLACK BELT
客户
浪费
6
IT’S OUR TURN…
关键步骤
选择一个产品 族
绘制当前的情 景
价值流程图培训讲义课件

价值流程图培训讲义课件•价值流程图基本概念与原理•识别浪费与改善机会•流程优化策略与技巧•跨部门协作与沟通在价值流图中应用目录•数据收集、整理和分析在价值流图中应用•价值流程图持续改进方向探讨01价值流程图基本概念与原理价值流程图定义及作用价值流程图定义价值流程图作用价值流图绘制方法与步骤确定范围和目标分析浪费收集数据设计未来图绘制现状图制定实施计划价值流浪费增值活动非增值活动关键术语解析02识别浪费与改善机会过度生产浪费等待浪费运输浪费不合理加工浪费库存浪费030201动作浪费缺陷浪费产品不良、返工、报废等造成的质量成本和时间浪费。
浪费类型及识别方法现场观察数据分析员工反馈价值流分析精益工具应用效益评估对提出的改善措施进行效益评估,包括成本节约、时间缩短、质量提升等方面。
可行性分析对改善措施进行可行性分析,考虑技术可行性、经济可行性和组织可行性等因素。
风险评估对改善措施可能带来的风险进行评估,制定相应的应对措施。
案例分析:某企业浪费识别及改善实践案例背景某制造企业存在生产效率低下、质量不稳定等问题,需要进行价值流分析和改善。
浪费识别通过现场观察和数据分析,发现该企业存在过度生产、等待、运输等多种浪费现象。
03流程优化策略与技巧流程优化目标与原则目标原则关键流程优化策略探讨自动化与智能化流程再造引入先进技术和工具,实现流程自动化和智能化,提高效率和准确性。
标准化与规范化实用技巧分享:如何提高流程效率01020304消除浪费简化流程强化沟通协作持续改进04跨部门协作与沟通在价值流图中应用提升整体效率通过协同合作,避免资源浪费和重复劳动,提高整体工作效率。
促进创新不同部门间的知识、技能和经验交流有助于激发创新思维,产生更好的解决方案。
•强化团队凝聚力:跨部门协作有助于打破部门壁垒,增强团队之间的信任和合作。
沟通不畅部门间沟通不足或沟通方式不当,可能导致信息传递失真或延误。
目标不一致不同部门可能有不同的目标和KPI ,导致协作困难。
价值流程图介绍ppt课件

分析资源消耗对流程成本 的影响
优化资源利用,降低流程 成本
03
价值流程图的绘制方法
确定目标与范围
明确价值流程图的目标
确定要解决的问题或改进的方向,例如提高生产效率、降低成 本等。
确定价值流程图的范围
明确要分析的业务流程范围,包括涉及的部门、岗位、时间等。
收集数据与资料
收集业务流程相关数据
包括流程中的时间、成本、质量等方面的数据。
制定战略目标
通过平衡计分卡明确企业的战略 目标,将目标分解为可操作的价
值流程图指标。
绩效评估与改进
结合平衡计分卡的绩效评估结果, 对价值流程图进行持续改进和优
化。
员工激励与培训
将平衡计分卡的绩效目标与员工 激励和培训相结合,提高员工对 价值流程图的认同度和执行力。
06
价值流程图实施过程中的挑战与 对策
目标不一致
各部门目标可能存在差异,难以形成统一的价值 观和行动准则。
资源分配不均
资源在各部门间的分配可能不均衡,影响跨部门 协作的效果。
员工培训与技能提升问题
培训内容与需求不匹配
培训内容可能过于理论化或与员工实际需求不符,导致培训效果 不佳。
培训方式单一
传统的培训方式可能缺乏互动性和趣味性,使员工失去学习兴趣。
01
02
03
完善流程图细节
对流程图中的各个环节进 行细化,添加必要的说明 和注释,使流程图更加清 晰易懂。
优化流程图结构
对流程图中的不合理之处 进行优化,如合并重复环 节、简化流程等,以提高 流程效率。
验证流程图准确性
与相关人员进行沟通,验 证流程图的准确性,确保 流程图与实际业务流程相 符。
龚举成:价值流 (1)
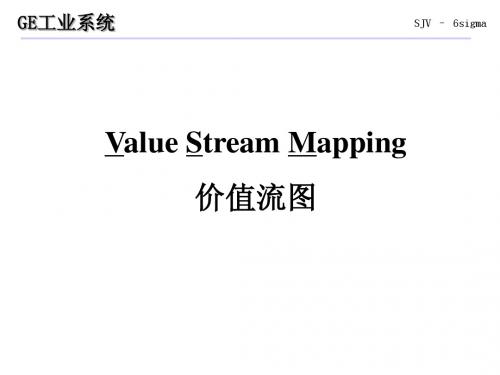
SJV – 6sigma
Travel to Machine finishing
全面生产维护 减少安装调试时间 TPM set up reduction
Machine R. turn/grind Finish
拉动系统 pull system 小单元生产 Cellular mfg..
一件流 1 piece flow
卡车工厂
=
价值流图是一个反映该过程的简单图表. A Value Stream Map is simply a graphical depiction of these actions
GE工业系统 价值流图是一种战略工具 Value Stream Map is a Strategic Tool
管理层
画出当前的状态
• 一个人/小组画出整个流程One person/team draw entire process • 手画草图Draw in pencil by hand • 在基层收集所有的数据Collect all data on the shop floor • 从最靠近客户和上道工序出开始 Begin closest to the customer and work upstream • 浏览整个流程以便理解Walk the process quickly to understand flow • 参观流程, 收集数据Walk again and collect data • 指出当前流程中的浪费Identify waste in the current state • 理解被指定为浪费的原因Understand the reason for identified waste • 在当前的流程图上表明可以改进的地方 Draw improvement idea directly on current state VSM • 考虑设备/资金/时间的限制 Consider equipment/financial/time constraints